起重机钢轨的焊接
重型起重机钢轨的手工电弧焊接

第 2 卷 第 5期 3 20 07年 1 O月
有
色
矿
冶
Vo . 123. 5 № Oco e 0 t b r20 7
NON— F ERROUS M I NG NI AND ET M ALLURGY
文章 编 号 :07—9 7 2 0 ) 5 0 6 3 10 6 X(0 7 0 —0 4 —0
3 焊 接 工 艺
3 1 选择 焊 接材料 .
c c + 十 + 鹎 + + 字 … =
按碳 当量公式计算得 : 30S 0 钢轨的碳当 E 6 (t ) 7
量为 08 %, 见该 钢 轨 的焊 接性 很 差 , 裂 纹 的 .0 可 冷 敏感 性大 , 接时 容 易产生 硬脆 的高 碳马 氏体 . 加 焊 增
保证 接头 两侧 部位 的温度 均匀 。
3 4 施焊过 程 .
将钢 轨的焊 接截 面镗 出 , 面 附近 3 以 内 截 0mm 要 清理干 净铁锈 、 油污 、 水分 等 杂质 , 出金属光 泽 。 露
放 好 轨道 接 头 垫板 并 达 到焊 接 温度 后 , 焊接 顺
序由下而上, 按照轨底一 轨腹一轨道上部截面顺序
・ 收稿 日期 :07—0 一儿 20 5
作者简介 : 郭春风(9 9 )女 , 17 一 , 工学学士 , 助理工程师, 主要从事焊接工艺工作。
维普资讯
第 5期
郭 春风 等 : 型 起 重 机 钢轨 的 手工 电弧 焊 接 重
4 7
置焊 接 。表面采 用 D N 5 5E 1 I 8 5 一UM 一3 0 03 2 0 、 . mm 耐磨堆 焊 焊 条 , 度 为 3HR , 有 较 好 的 耐 硬 0 C具 磨性 。 3 2 焊前准 备 .
钢轨焊接工艺

钢轨焊接工艺在起重机的制造工艺中,常将箱形主梁上铺设的钢轨采用对接形式焊接成一根无缝隙的长钢轨。
现将实际工作中钢轨对接焊接工艺的案例总结如下。
一、根据钢轨的材质和表面硬度要求选择焊材1. 钢轨起重机的小车轨道有三种:⑴起重机钢轨如QU70 QU80等。
(2) P型钢轨女口P24 P38 P43等。
(3) 方钢如:30mnr K 40mm 40mr K 40mm等。
前两种钢轨的顶部做成凸状,底部是具有一定宽度的平板,可增大与基础的接触面。
钢轨的截面为工字形,具有良好的抗弯强度,其含碳量、含锰量较高,w=0.5,,0.8, ,w=CMn0.6,,1.5,。
而方钢的材料为Q275顶部平直,对车轮磨损较大,这里暂不讨沦。
2. 焊条钢轨的对接焊缝要求不进行处理就能达到钢轨的表面硬度。
如下图所示,在轨道头部以下,用E5016焊条;在轨道头部用堆焊焊条D322(铬钨钼钒冷冲模焊条)。
这样既经济又实用,不但可保证对接焊缝质量和强度,而且可使堆焊层硬度(焊后空冷)?55HRC。
上述两种焊接条都是交、直流两用,直径均为5mm焊接电流均为180,240A,电弧电压均为36,24V。
二、对接焊工艺1. 工具、材料及焊接准备电焊机1,2台,焊炬2,3把0,300?温度计一只,氧气、乙炔气。
焊前将焊条放在350,400?烘箱内烘焙1h以后,把对接的钢轨平放在水泥地面上支好,对接焊缝间隙20mm 校直、校平,钢轨对接表面除油、除污、打磨及擦洗干净。
2. 焊接操作由于钢轨焊接性能较差,因此焊接工艺较为繁琐,要把0,300?的温度计固定在钢轨上,在距离焊缝两边100mm长的位置,用2,3把焊炬同时对钢轨预热。
当钢轨温度达到230,250?时,先用E5016焊条从钢轨底部边加热边堆焊,堆焊至轨道头部时,在用D322焊条边加热边堆焊。
焊接要间断进行,尽量减少焊接部位的热量,使焊接过程中始终保持轨道温度230,250?。
全部焊接完成后,还要继续加热到250?,再将钢轨在空气中经过?0.5h时间缓慢冷却到室外温度(30?左右),以防止裂纹产生。
起重机钢轨接长焊接工艺

起重机钢轨接长焊接工艺起重机钢轨接长焊接是一项高精度的操作,它的质量直接关系到起重机的安全性和使用寿命。
因此,这项工艺必须予以充分重视,并采取合理有效的措施来保证和保障。
起重机钢轨接长焊接一般需要使用激光焊接、电弧焊接和熔接三种方法,其中激光焊接技术最为常用,工艺在激光熔接机上实现,其操作要求高,对所采用的激光焊接机的选择和配置要求较为严格。
激光焊接使用激光束,在金属表面上形成液态熔融层,形成固态焊缝,极大地提高了接长焊接的质量。
在起重机钢轨接长焊接过程中,激光焊接机参数调整要求较高,焊接速度、焊接深度、焊接温度和焊接功率均要进行调整,确保钢轨接头处焊接熔接层的质量,以保证起重机钢轨的质量和使用寿命。
焊接时,应严格控制焊接温度,焊接温度过高、焊接温度过低均会影响焊接质量,甚至导致焊接失败,长期使用起重机钢轨遭受损伤而寿命缩短。
此外,起重机钢轨接长焊接过程中应注意工艺技术的控制,工艺技术的控制是保证接长焊接质量的关键。
除了激光焊接机的参数调整以外,在焊接前还应清除钢轨表面的杂质,焊接过程中还应控制焊接时间以减少焊接温度的变化,以保证接头处的熔接层的质量和外观效果。
此外,起重机钢轨接长焊接还应加强安全措施。
激光焊接技术在起重机钢轨接长焊接过程中非常常见,因此,应采取必要的安全措施,以防止可能发生的意外。
焊接前应检查是否有有火花飞出的情况,以及眼部防护是否良好,而且激光焊接的环境应保持良好的通风和照明技术,以防止原料,污染物或灰尘等有害物质污染焊接操作环境。
以上就是起重机钢轨接长焊接工艺的主要内容,也是起重机钢轨接长焊接工艺的必备知识。
起重机钢轨接长焊接是一项质量要求较高的工艺,必须按照有效的章程,按照正确的操作程序,遵守安全操作规则,确保操作质量,保证产品的质量和使用寿命,以达到综合效益的最大化。
起重机轨道安装技术要求

起重机轨道安装技术要求1、起重机轨道的安装方式用于安装轨道的轨道梁常用的有2种:一种是钢结构梁,一种是混凝土预制梁。
混凝土预制梁必须留有预埋孔,以备安装时穿螺栓,或者在混凝土预制梁中预埋螺栓。
起重机轨道的安装方法有用压板固定法、钩形螺杆固定、焊接和螺栓联用固定等。
为了进行水平方向的调整,轨道压板上的孔通常做成长孔,垂直方向的调整可在钢轨下加垫。
轨道压板在设计时,要具有足够的刚性,每块压板,根据受力的大小可以制成单孔的或双孔的。
只有轨道与轨道梁或者轨道梁上固定的钢垫板采用焊接方式连接时,车档方可焊接在轨道上。
2、轨道铺设前对轨道梁的安装要求2.1 对混凝土轨道梁的要求(1)轨道梁制作时必须保证沿梁横向及纵向的预留螺栓孔位置偏差≤5 mm,螺栓孔直径比螺栓直径大2~7 mm,梁顶面要求平整,但不得抹压光滑。
(2)轨道梁的安装偏差必须满足下列要求,否则要调整好轨道梁后才允许用混凝土找平。
①梁中心位置对设计定位轴线的偏差≤5 mm。
②梁顶面标高对设计标高的偏差+ 10 mm-5 mm。
③梁上预留螺栓孔及预留螺栓对梁中心的位移偏差≤5 mm。
(3)混凝土找平层的施工要求①混凝土找平层强度等级为C30,厚度为30~50 mm。
②混凝土找平层施工前应按要求检查轨道梁的安装偏差,如不符合要求,则应调整轨道梁。
③根据轨道梁面的实测标高,确定一个合适的混凝土找平层顶面控制标高,在轨道梁上每隔2.4~3.0 m设置一个控制标高的基准点。
④用仪器测量,调整好基准点的标高,定出找平层顶面标高的基准线,然后安装模板,清除轨道梁顶面和螺栓孔内的杂物,并将螺栓孔上口堵住,洒水湿润后即可浇筑混凝土。
⑤找平层顶面必须找平压光,不得有石子外露和凹不平现象,不允许采用在表面另铺水泥砂浆的方法找平。
⑥施工中要随时用仪器测量检查,找平层顶面必须满足下列要求:螺栓处400 mm宽度范围内顶面不水平度≤5 mm;任意6.0 m长度内螺栓处顶面标高差±3 mm;沿全长各螺栓处顶面标高差±5m。
43公斤道轨安装规范

43公斤道轨安装规范起重机轨道安装1.轨道安装流程:根据上道工序(结构安装)的工序交接资料,对轨道梁进行复测验收。
轨道梁安装的各项技术指标应控制在《钢结构工程施工质量验收规范》GB50205-2001附录E.0.2的允许偏差之内。
合格后方可进行轨道的安装。
3.天车轨道放线:根据工序交接给定轨道梁中心点,用经纬仪在轨道梁上打点。
然后放出一条安装基准线,用钢盘尺测出轨道的跨度,在另一个轨道梁上放出轨道安装的另一条基准线。
4.压板选用及焊接根据图纸要求,选用焊接型轨道固定件,底座、压板及调整板为Q235或Q345钢铸件,螺栓为8.8级;固定件底座与吊车梁焊接,焊条型号选用与连接件材质相适应。
如选用Q235或Q345钢时分别采用E4315、E7015型焊条。
安装轨道前,根据安装基准线在轨道的两侧布置压板,压板间距按照《吊车轨道联结及车挡》05GJ25要求间距600mm进行底板定位,然后焊接;要求为中级工作制吊车采用两侧焊缝,重级工作制吊车采用三面围焊缝,焊缝质量应符合三级焊缝外观质量标准。
5.轨道吊装:轨道吊装可根据吊装环境、地点、重量选用汽吊进行到场吊装,卸车时垫以枕木,使轨道立放,避免存放变形。
a、起吊重量=每根轨道重+钩重+钢丝绳重量b、起吊高度=轨道标高+1.5米所有的轨道都必须从厂房内侧吊装。
6、轨道调整用千斤顶或撬棍先两端后中间调整到要求数值后固定,再用盘尺按照轨距数值调整另一侧轨道,方法相同。
轨道找正后应把紧所有连接螺栓并无松动现象。
7、轨道焊接接头施工工艺按照业主要求,轨道接头焊接接头,要求轨道布置时同一车间内对应轨道接缝位置应错开,其错开的距离不应等于天车前后车轮的基距。
7.1钢轨焊接变形的控制在施焊过程中钢轨接头将向下弯曲变形,预先采用赤铜板和钢垫板将钢轨端头垫起40-60mm,利用已制作好的螺栓和压板等连接件拧紧螺母使钢轨固定在吊车梁上,每一条钢轨接头附近应至少设置4处固定点。
当焊完轨底部分以后,松开压板,将钢轨端头的垫起高度降低到10mm,再拧紧压板螺母。
轨道焊接工艺规程
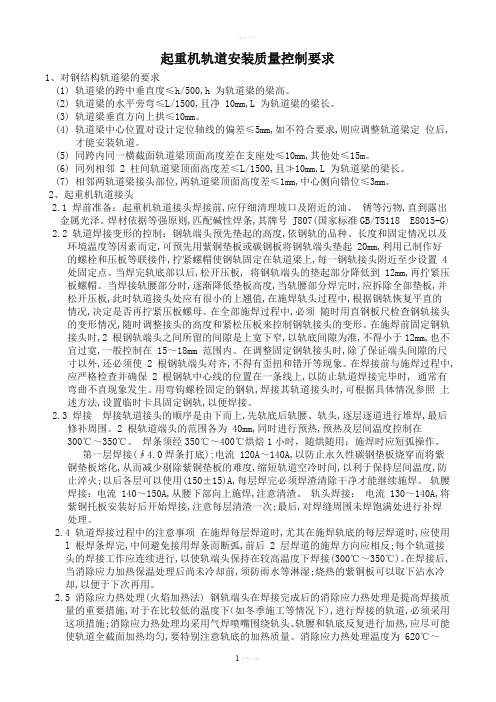
起重机轨道安装质量控制要求1、对钢结构轨道梁的要求(1) 轨道梁的跨中垂直度≤h/500,h 为轨道梁的梁高。
(2) 轨道梁的水平旁弯≤L/1500,且净 10mm,L 为轨道梁的梁长。
(3) 轨道梁垂直方向上拱≤10mm。
(4) 轨道梁中心位置对设计定位轴线的偏差≤5mm,如不符合要求,则应调整轨道梁定位后,才能安装轨道。
(5) 同跨内同一横截面轨道梁顶面高度差在支座处≤10mm,其他处≤15m。
(6) 同列相邻 2 柱间轨道梁顶面高度差≤L/1500,且≯10mm,L 为轨道梁的梁长。
(7) 相邻两轨道梁接头部位,两轨道梁顶面高度差≤1mm,中心侧向错位≤3mm。
2、起重机轨道接头2.1 焊前准备:起重机轨道接头焊接前,应仔细清理坡口及附近的油、锈等污物,直到露出金属光泽。
焊材依据等强原则,匹配碱性焊条,其牌号 J807(国家标准GB/T5118 E8015-G) 2.2 轨道焊接变形的控制:钢轨端头预先垫起的高度,依钢轨的品种、长度和固定情况以及环境温度等因素而定,可预先用紫铜垫板或碳钢板将钢轨端头垫起 20mm,利用已制作好的螺栓和压板等联接件,拧紧螺帽使钢轨固定在轨道梁上,每一钢轨接头附近至少设置 4 处固定点。
当焊完轨底部以后,松开压板, 将钢轨端头的垫起部分降低到 12mm,再拧紧压板螺帽。
当焊接轨腰部分时,逐渐降低垫板高度,当轨腰部分焊完时,应拆除全部垫板,并松开压板,此时轨道接头处应有很小的上翘值,在施焊轨头过程中,根据钢轨恢复平直的情况,决定是否再拧紧压板螺母。
在全部施焊过程中,必须随时用直钢板尺检查钢轨接头的变形情况,随时调整接头的高度和紧松压板来控制钢轨接头的变形。
在施焊前固定钢轨接头时,2 根钢轨端头之间所留的间隙是上宽下窄,以轨底间隙为准,不得小于12mm,也不宜过宽,一般控制在 15~18mm 范围内。
在调整固定钢轨接头时,除了保证端头间隙的尺寸以外,还必须使 2 根钢轨端头对齐,不得有歪扭和错开等现象。
行车钢轨铝热焊接技术的应用

QU 8 0 Q UI O 0 Q u1 2 o O . 4 0  ̄ 0 . 7 1 5 ~ 2 O 2 6  ̄ 2
5 9 l 2 3 5 0 0
I
( 6 ) 浇 注
3 . 钢轨铝热焊接技术标准
焊 接 接 头 质 量 标 准 执 行 T B 1 0 4 1 3 -2 0 0 3 { 铁路轨道工程质量验
F e 2 O3 + 2 AI = 2 F e + A 1 2 O3 + 8 2 9 . 9 k J
3 F e 2 0 + 8 A l = 9 F e + 4 Al 2 03 + 3 2 3 6 . 3 k J
( 1 )
2 . 铝热焊剂技术要求 ( 表2 )
表 2 铝 热剂 焊 剂 主 要 化 学 成 分 %
正常磨损外 , 还会发生一系列其他现象 。 因车轮对接 口的冲击 、振动而导致接 口处出现不同程 度的
钒、 铬、 锰、 钨 等 从 其 氧 化 物 中
还 原 出来 , 同 时 放 出大量 热 , 温
标准值/ ( m m / m)
O ~ + O . 5
内侧工作面
O . 5
度可达 2 0 0 0 ~ 3 0 0 0  ̄ C , 从而使这些金属成为液态 。 铝热化学反应是氧化还原反应 ,主要 反应 产物为液态铝热
I
2 ) 钢轨 端头 处理 及 对 n : 连接 处原采用 电焊 ( 5 0 6焊 条 ) 焊 接方 (
3 . 铝热焊剂 焊接工艺参数 ( 表3 )
表 3 铝 热 焊剂 焊接 工艺 参 数
项目
I
( 3 ) 砂模 准 备
裂的情况 , 决定采用 Q u 1 2 o和 Q UI O 0
起重机轨道安装技术要求
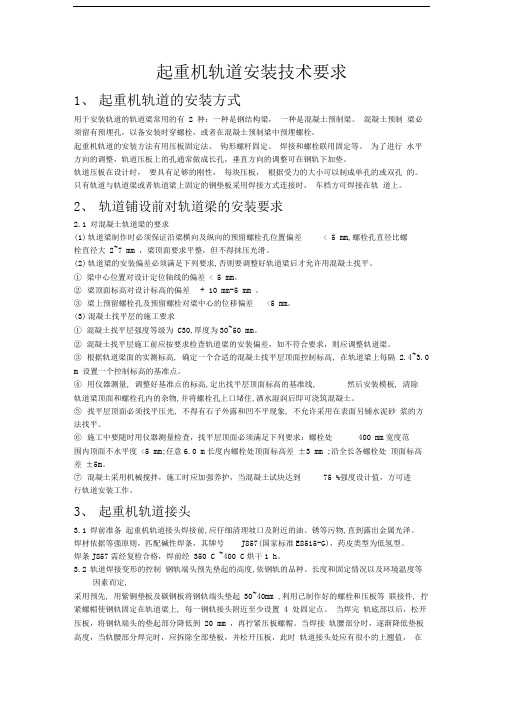
起重机轨道安装技术要求1、起重机轨道的安装方式用于安装轨道的轨道梁常用的有2 种:一种是钢结构梁,一种是混凝土预制梁。
混凝土预制梁必须留有预埋孔,以备安装时穿螺栓,或者在混凝土预制梁中预埋螺栓。
起重机轨道的安装方法有用压板固定法、钩形螺杆固定、焊接和螺栓联用固定等。
为了进行水平方向的调整,轨道压板上的孔通常做成长孔,垂直方向的调整可在钢轨下加垫。
轨道压板在设计时,要具有足够的刚性,每块压板,根据受力的大小可以制成单孔的或双孔的。
只有轨道与轨道梁或者轨道梁上固定的钢垫板采用焊接方式连接时,车档方可焊接在轨道上。
2、轨道铺设前对轨道梁的安装要求2.1对混凝土轨道梁的要求(1)轨道梁制作时必须保证沿梁横向及纵向的预留螺栓孔位置偏差< 5 mm,螺栓孔直径比螺栓直径大2~7 mm ,梁顶面要求平整,但不得抹压光滑。
(2)轨道梁的安装偏差必须满足下列要求,否则要调整好轨道梁后才允许用混凝土找平。
①梁中心位置对设计定位轴线的偏差 < 5 mm。
②梁顶面标高对设计标高的偏差+ 10 mm-5 mm 。
③梁上预留螺栓孔及预留螺栓对梁中心的位移偏差<5 mm。
(3)混凝土找平层的施工要求①混凝土找平层强度等级为C30,厚度为30~50 mm。
②混凝土找平层施工前应按要求检查轨道梁的安装偏差,如不符合要求,则应调整轨道梁。
③根据轨道梁面的实测标高, 确定一个合适的混凝土找平层顶面控制标高, 在轨道梁上每隔2.4~3.0 m 设置一个控制标高的基准点。
④用仪器测量, 调整好基准点的标高,定出找平层顶面标高的基准线, 然后安装模板, 清除轨道梁顶面和螺栓孔内的杂物,并将螺栓孔上口堵住,洒水湿润后即可浇筑混凝土。
⑤找平层顶面必须找平压光, 不得有石子外露和凹不平现象, 不允许采用在表面另铺水泥砂浆的方法找平。
⑥施工中要随时用仪器测量检查,找平层顶面必须满足下列要求:螺栓处400 mm宽度范围内顶面不水平度 <5 mm;任意6.0 m长度内螺栓处顶面标高差±3 mm ;沿全长各螺栓处顶面标高差±5m。
- 1、下载文档前请自行甄别文档内容的完整性,平台不提供额外的编辑、内容补充、找答案等附加服务。
- 2、"仅部分预览"的文档,不可在线预览部分如存在完整性等问题,可反馈申请退款(可完整预览的文档不适用该条件!)。
- 3、如文档侵犯您的权益,请联系客服反馈,我们会尽快为您处理(人工客服工作时间:9:00-18:30)。
起重机钢轨的焊接
一、钢轨材料U71Mn的焊接性分析
1、该材料属于高碳钢,焊接性很差,必须采取高预热和缓冷措施。
2、无论从力学性能还是焊接工艺性考虑,均应采用“里软外硬”
的方案(即内部焊材应低匹配,使焊缝内部有较高的韧性,而
轨面应耐磨,以适应起重机的需要)。
3、焊接时应采取措施防止角变形。
高碳钢轨的矫正是十分困难
的。
坡口设计应使焊缝尽可能窄,以减少焊接工作量,减少变
形。
二、焊接工艺
1、焊接材料
距轨面15㎜起用D112焊条堆焊耐磨层,其余层均用低匹配的J507焊条施焊。
2、坡口形式
采用窄间隙直坡口。
留15~20㎜间隙以利于排渣和减少角变形。
3、预置反变形
反变形垫块的设计,应使焊后恰好使轨道面齐平。
4、预热和缓冷
接头两侧各200~300㎜范围内焊前预热到300~350℃并保持一段时间,焊后再将接头区加热到300℃并缓冷(用石棉粉覆盖)。
5、铜模强迫成形
钢轨接头装配后,先焊底部Ⅰ层焊缝,然后装配两侧铜夹板以强
迫Ⅱ层焊缝成形。
铜夹板与焊件间留4~6mm间隙以排渣。
底部焊缝用砂轮清根后再焊补,焊后接头表面和两侧再用砂轮修磨到位。
6、焊接工艺参数
盖面层和底部 I=160~180A,中间层I=200~210A。