精益生产培训教材(PPT 41页)
合集下载
《精益生产培训》ppt课件精品模板分享(带动画)
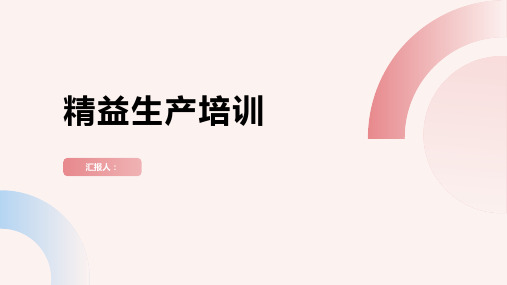
结论:美的集团 的精益生产成功 案例表明,通过 科学管理和创新 技术手段,企业 可以提高生产效 率和产品质量, 降低成本和缩短 交货期,增强市 场竞争力。
如何推广精益生产文化
第六章
提高员工意识
培训:定期组织精益生产培训,让员工了解精益生产理念、方法和工具。
宣传:通过内部宣传、精益文化墙等方式,宣传精益生产的重要性和优势, 增强员工的认同感和归属感。
建立示范点
选择具有代表性的生产现场作为示范点 制定具体的实施方案和计划 安排专业的技术人员进行指导和监督 总结经验教训,不断完善和优化实施方案
激励和奖励机制
建立精益生产知识竞赛,鼓励员工 参与
设立精益生产优秀员工奖,激励员 工积极参与
添加标题
添加标题
添加标题
添加标题
针对实施精益生产的部门或团队进 行奖励
增强客户满意 度
提高产品性能 和质量
提升企业品牌 形象和竞争力
增强企业竞争力
提高生产效率
降低成本
优化资源配置
提升产品质量
创新产品研发
增强市场竞争力
精益生产的核心工具
第三章
价值流分析
定义:识别和追踪产品或服务在生产过程中的所有活动 目的:找出浪费和不增值的环节 方法:绘制价值流图,包括生产流程、时间、人力、物力等 作用:为精益生产提供分析和改进的依据
添加标题
添加标题
它通过消除浪费、提高效率、减少 成本来最大化价值
浪费是指任何消耗了资源而不增加 价值的活动
精益生产的起源
目的:消除浪费,提高效率
起源:20世纪50年代,日本 丰田汽车公司
方法:采用生产流程分析和 改进工具,如价值流图、流
程图等
结果:提高了生产效率和质 量,降低了成本,增强了竞
精益生产培训课件(PPT 72页)
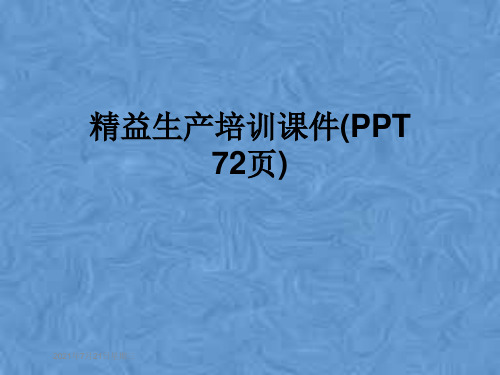
视5S工作。
素养
• 定义:人人依规矩行事,工作的每 分钟、每个环节都具备良好的思维 方式。
• 目的:提升人的品质,使每个人都 成为对任何工作都持认真态度 的 优秀管理者和员工。
5S活动开展原则
• 1、自我管理 • 2、持之以恒 • 3、小处着眼
• 实例
返回
推行精益重在坚持
维持
改 善
改善和维持 循环
整顿
• 定义:要的东 西依规矩定位, 摆放整齐,并 明确表明。
• 目的:不浪费 时间寻找需要 的物品
整顿
是对整理后的东西的整顿。
• 定位摆放
物各有位,物在其位
• 定量摆放
过目知数,控制库
• 目视管理
标识清晰,一目了然
• 取用方便
提高效率,保证质量
整顿推行要点
• 1、将整理后的货架、场所空间进行重新规 划使用。
库存的浪费
• 后果: 1、过多的库存,使资金都积压在原材料, 企业的利润有相当一部分被货款利息吃掉了。 2、库存过多,会产生锈蚀变质, 3、增加人去清点、整理
库存的浪费
后果
增加利息负担 占用场地厂房 管理人员增加 入出库的搬运 处锈等工作浪费 长时间失效的浪费
最大的问题: 完全掩盖了工 厂里的问题。
• 精益生产的基本思想 • 2.1 一大目标:低成本、高效率、高
质量地进行生产,消除生产中的一切浪 費 • 2.2两大支柱:准时化、自働化 • 2.3一大基础:改善活動
精益的5项原则
• 1 价值观(Value) 2 价值流(Value Stream) 3 流动(Flow) 4 拉动(Pull) 5 尽善尽美(Perfection)
动作的浪费
• 根源:
素养
• 定义:人人依规矩行事,工作的每 分钟、每个环节都具备良好的思维 方式。
• 目的:提升人的品质,使每个人都 成为对任何工作都持认真态度 的 优秀管理者和员工。
5S活动开展原则
• 1、自我管理 • 2、持之以恒 • 3、小处着眼
• 实例
返回
推行精益重在坚持
维持
改 善
改善和维持 循环
整顿
• 定义:要的东 西依规矩定位, 摆放整齐,并 明确表明。
• 目的:不浪费 时间寻找需要 的物品
整顿
是对整理后的东西的整顿。
• 定位摆放
物各有位,物在其位
• 定量摆放
过目知数,控制库
• 目视管理
标识清晰,一目了然
• 取用方便
提高效率,保证质量
整顿推行要点
• 1、将整理后的货架、场所空间进行重新规 划使用。
库存的浪费
• 后果: 1、过多的库存,使资金都积压在原材料, 企业的利润有相当一部分被货款利息吃掉了。 2、库存过多,会产生锈蚀变质, 3、增加人去清点、整理
库存的浪费
后果
增加利息负担 占用场地厂房 管理人员增加 入出库的搬运 处锈等工作浪费 长时间失效的浪费
最大的问题: 完全掩盖了工 厂里的问题。
• 精益生产的基本思想 • 2.1 一大目标:低成本、高效率、高
质量地进行生产,消除生产中的一切浪 費 • 2.2两大支柱:准时化、自働化 • 2.3一大基础:改善活動
精益的5项原则
• 1 价值观(Value) 2 价值流(Value Stream) 3 流动(Flow) 4 拉动(Pull) 5 尽善尽美(Perfection)
动作的浪费
• 根源:
精益生产知识培训演示课件(29张)

利润是如何产生的?
获得利润的两大手法: 手法一:降低成本(节流) 手法二:提高效率(开源) 通过改善消除浪费,提高附加价值 实现
成本中心型 售价=成本+利润
以计算或实际成本为中心,加上预先设定的利润,得出为产品的售价。
售价中心型
利润=售价-成本
以售价为中心,当市场售价变动时,利润随着变动。
利润中心型
板
保
证
保 全
· 安 全
产
目视管理
推进顺序2
步骤1:意识改革
步骤2:5S
步骤2:流动生产
舍弃陈旧的想法,采用JIT思想。
JIT
JIT改善的基础是整理、整顿、 清扫、清洁、教养等5S
步骤5:标准作业
停止大批制造,让每一项工程 都遵循顺序来制造。
步骤4:平准化
JIT
好不容易所完成的物品流程, 不可弄乱,要牢记在心。
精益生产知识培训
目
录
一、什么是精益生产 二、为什么要进行精益生产 三、精益生产的七大浪费 四、如何做精益生产
一、什么是精益生产
企业的基本经营概念
●为股东创造利润—维系企业生存 ●向社会提供好的产品——占领市场空间 ●企业和员工共同的发展
企业经营的真正目的在于制造利润,因此在企业的 整个经营过程中如何获得最大的利润是企业的头等 大事!
• 基本思想就是消灭包括库存再内的一切无效的劳 动与浪费,达到降低成本,提高产品质量来增强 企业的竞争优势的目的。精,即是不投入任何多 余的生产要素,只在适当的时间生产必要的产品; 益,即所有经营活动均应有益有效。
二、为什么要进行精益生产
成本的构成 成本一般有以下要素组成: 材料、人工、制造费用、消耗品、管理费用、设备、工资… …等
精益生产培训课件(PPT 41页)
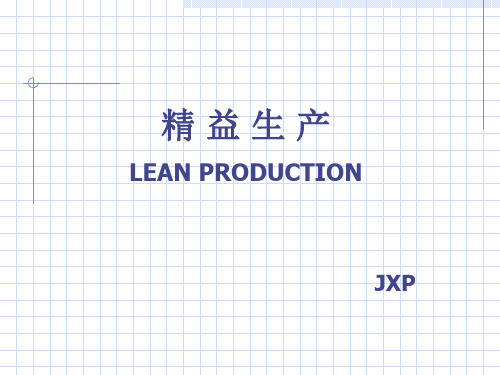
按Tact Time组织生产,产成品库存会降
低到最低限度
如何改进生产活动
改善生产活动来配合生产流程的改善 在没有或很少库存的情况下,生产过程 的可靠性尤其重要。要保证生产的连续 性,必须通过减少生产准备时间、机器 检修、待料停工时间和减少废品的产生 来实现
减少生产准备时间
一般做法是:
1. 列举生产准备程序的每一项要素和步骤 2. 辨别内在因素和外在因素 3. 尽可能变内在因素为外在因素 4. 精简影响生产准备的内外因素
计算如下:
60m / h 60s / h 21.2units / h 170s / unit 80units / h 3.8
21.2units / h
(取4个工作台,尚有生产能力剩余)
规划精益生产单元的布置。
实际设计生产精益生产单元时,可以考 虑设置两个铣、钻、磨加工区,每个加 工区由两个工作台组成,每个工作台配 备一个工人
精益生产
LEAN PRODUCTION
JXP
精益生产是什么?
精益生产是一种以最大限度地减少运营
成本为主要目标的生产方式
精——少而精,不投入多余生产要素,
只在适当时间生产必要的产品
益——所有经营活动有益有效,具有经
济性
特点
•消除一切浪费 •追求精益求精和不断改善 •去掉一切不增值的岗位
核心:精简
组产品,需要经过铣、钻、磨、装配和 打包等六道工序,每周生产3200件,所 有这些产品的加工过程相似,需要的工 人相同。该企业每周工作5天,每天工作 8小时。
生产指定产品每道工序的单位加工时间:
现对其进行精益化改造
经调查: 1.铣、钻、磨床尚有剩余生产能力,因
此在不影响其它生产条件下,可进行 适当调整 2.所有装配线和包装依靠手工完成,只 需提供工作台和工具
低到最低限度
如何改进生产活动
改善生产活动来配合生产流程的改善 在没有或很少库存的情况下,生产过程 的可靠性尤其重要。要保证生产的连续 性,必须通过减少生产准备时间、机器 检修、待料停工时间和减少废品的产生 来实现
减少生产准备时间
一般做法是:
1. 列举生产准备程序的每一项要素和步骤 2. 辨别内在因素和外在因素 3. 尽可能变内在因素为外在因素 4. 精简影响生产准备的内外因素
计算如下:
60m / h 60s / h 21.2units / h 170s / unit 80units / h 3.8
21.2units / h
(取4个工作台,尚有生产能力剩余)
规划精益生产单元的布置。
实际设计生产精益生产单元时,可以考 虑设置两个铣、钻、磨加工区,每个加 工区由两个工作台组成,每个工作台配 备一个工人
精益生产
LEAN PRODUCTION
JXP
精益生产是什么?
精益生产是一种以最大限度地减少运营
成本为主要目标的生产方式
精——少而精,不投入多余生产要素,
只在适当时间生产必要的产品
益——所有经营活动有益有效,具有经
济性
特点
•消除一切浪费 •追求精益求精和不断改善 •去掉一切不增值的岗位
核心:精简
组产品,需要经过铣、钻、磨、装配和 打包等六道工序,每周生产3200件,所 有这些产品的加工过程相似,需要的工 人相同。该企业每周工作5天,每天工作 8小时。
生产指定产品每道工序的单位加工时间:
现对其进行精益化改造
经调查: 1.铣、钻、磨床尚有剩余生产能力,因
此在不影响其它生产条件下,可进行 适当调整 2.所有装配线和包装依靠手工完成,只 需提供工作台和工具
精益生产培训课件(PPT68页).pptx

“美国的生产体制还有改进的可能”。
2、精益生产由来
丰田公司丰田英二和大野耐一等人根据自身面临需求不 足、技术落后、资金短缺等严重困难的特点,同时结合日本 独特的文化背景,提出了一系列改进生产的方法:及时制生 产、全面质量管理、并行工程。经近30年创立了一种全新的 多品种、小批量、高效益和低消耗的生产方式,即丰田生产 方式。改生产方式的发展与应用,使日本汽车工业突飞猛进, 1980年产量达到1100万辆,出口250万,超过美国成为第一。 1973年因为石油危机行业萧条下,丰田盈利备受瞩目。 从那时起丰田生产方式开始被人关注。1978年大野耐一著书 《丰田生产方式》, 国内,1986年一汽变速器率先实施精益,东风、跃进
2、精益生产由来
上世纪中期,即二战后,日本经济百废待举, 日本政府制定了“国民收入倍增计划”,把汽车 工业作为重点发展的战略性产业。那个时候美国 的汽车工业处于发展的顶峰。为提高工业生产效 率、为寻求日本汽车发展道路,1950年春组织 包括丰田公司在内业界人员出国考察福特汽车。。 考察完毕,日本人深受启发,得出大批量生产模 式不适合日本、 丰田人在报告中还指出
TPS 丰田生产方式
(日本)
LP 精益生产 (国际)
3、为何要精益生产
从企业存在的价值说起。
生产产品、服务社会、最终 目的是为获取利润。 企业需要生产经营维持 激烈竞争的市场经济下、 买方市场下、多品种小批量 生产特点下,企业要不寻常 的生产经营 什么是不同寻常的生产经 精益化生产现场管理及班组建设
第一章 精益生产概论
1、什么是精益生产
精益生产( Lean Production ),是美国麻省 理工学院研究小组对日本汽车工业生产管理方 式(以丰田汽车公司TPS为代表)进行调研后, 对这种生产方式赋予的名称。
2、精益生产由来
丰田公司丰田英二和大野耐一等人根据自身面临需求不 足、技术落后、资金短缺等严重困难的特点,同时结合日本 独特的文化背景,提出了一系列改进生产的方法:及时制生 产、全面质量管理、并行工程。经近30年创立了一种全新的 多品种、小批量、高效益和低消耗的生产方式,即丰田生产 方式。改生产方式的发展与应用,使日本汽车工业突飞猛进, 1980年产量达到1100万辆,出口250万,超过美国成为第一。 1973年因为石油危机行业萧条下,丰田盈利备受瞩目。 从那时起丰田生产方式开始被人关注。1978年大野耐一著书 《丰田生产方式》, 国内,1986年一汽变速器率先实施精益,东风、跃进
2、精益生产由来
上世纪中期,即二战后,日本经济百废待举, 日本政府制定了“国民收入倍增计划”,把汽车 工业作为重点发展的战略性产业。那个时候美国 的汽车工业处于发展的顶峰。为提高工业生产效 率、为寻求日本汽车发展道路,1950年春组织 包括丰田公司在内业界人员出国考察福特汽车。。 考察完毕,日本人深受启发,得出大批量生产模 式不适合日本、 丰田人在报告中还指出
TPS 丰田生产方式
(日本)
LP 精益生产 (国际)
3、为何要精益生产
从企业存在的价值说起。
生产产品、服务社会、最终 目的是为获取利润。 企业需要生产经营维持 激烈竞争的市场经济下、 买方市场下、多品种小批量 生产特点下,企业要不寻常 的生产经营 什么是不同寻常的生产经 精益化生产现场管理及班组建设
第一章 精益生产概论
1、什么是精益生产
精益生产( Lean Production ),是美国麻省 理工学院研究小组对日本汽车工业生产管理方 式(以丰田汽车公司TPS为代表)进行调研后, 对这种生产方式赋予的名称。
精益生产培训教材(PPT 41页)
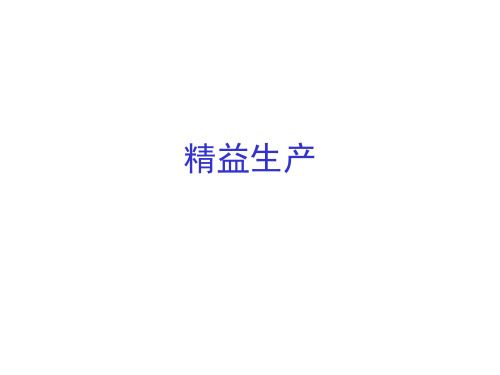
The Job
工 作
Time Fluctuation 时间波动
Job Element Sheet 工作要素单
Element 1 要素 1
Job Element Sheet 工作要素单
Element 2 要素 2
Job Element Sheet 工作要素单
Element 3 要素 3
Job Element Sheet 工作要素单
TIME FLUCTUATION WORKSHEET 时间波开工作单 JOB ELEMENT SHEET 工作要素单 TIME MEASUREMENT SHEET 时间测量单
STANDARDISED OPERATIC THEET 标准作业单
Quality Process Sheet
Department/ Welding 05
精益生产
课程内容
• 定义 • 产生与开展 • 特点与优越性 • 核心内容与生产要素 • 标准化介绍 • 最终目的
什么是精益生产?
• 精益生产是 通过系统结构、人员组织、运行方式和市 场供求等方面的变革,使生产系统能很快适应用户需 求不断变化,并能使生产过程中一切无用、多余的东 西被精简,最终到达包括市场供销在内的生产的各方 面最好的结果。
Worksheet
#
5-140
Opr
WGL
Page__1__ of__1__
Sup
Maint
Eng
3302246
QC QUICK
CHANGE OVER
VISUAL FACTORY
FORD Total Prod.T
F
M
Maint.
P
ERROR PROOFING D
精益生产培训教材(共 38张PPT)
柏拉图
柏拉图
28
• 改善效果之确认
(元)
25000
改善前
(%)
100 75
(元)
25000
改善後 效果
支 出 金 額
20000 15000 10000 5000 0
累 計 比 率
支 出 金 額
20000 15000 10000 5000 0
50 25 0
伙 零 水 教 交 其 食 用 電 育 際 他 費 錢 瓦 費 費 斯 費
经过取消、合并、重排后的必要工序,应 采用最简单的方法或设备替代,以节省人
作业改善压缩
分割转移
作 业 时 间
作 業 改 善
作 业 时 间
工序
1
2
3
4
5
工序
2
3
并行作业,增加人员
拆解去除
1人 作业 作 业 时 间 作 业 时 间
2人 作业
工序
1
2
3
4
5
工序
1
2
3
作业改善后合并
重排
作 业 时 间
作 业 时 间
伙 零 水 教 交 食 用 電 育 際 費 錢 瓦 費 費 斯 費
29 柏拉图
• 效果确认的柏拉图制作要决
1. 2. 3. 4. 必须两个柏拉图并排,分为改善前与改善后。 收集数据的期间和对象必须一致。 季节性的变化应列入考虑。 对於改善项目以外的要因也要加以注意。
3.多能工培养
多能工是指掌握多个岗位作业技
21
QC手法——鱼骨图
开车人数增加
交通事故多
道路施工
收入提高 生活品质提高 虛榮心作祟休闲增加 休息日多 活动地点多 货车任意卸貨 购物商圈 停车位少 等候停车对伍长 收費速度慢
精选精益生产培训教材PPT144页
满足小批量、交期短、品种多的特点。
丰田生产方式硬环境 整合
5S
看板管理 均衡化 一个流
作业切换
JIT 品质保证 标准作业
多能工
目视管理 设备保养 柔性化
少人化
日本企业的精益生产状况
1950年起,电子行业:独创项目管理与短产品周期——仅仅有三菱公司实验过。 大部分企业——美国过去的:统计质量控制概念、QC手法、PDCA、QCC、QFD等。 ——1960年,日产公司获得“戴明奖” ——丰田采用TQM,1965年获得“戴明奖” (丰田生产模式与TQM结合,是丰田的优势) ——1973年能源危机,大部分企业亏损,而丰田盈利。三菱全面实施丰田模式,马自达、
I
C /T = C /O = U p tim e = L o t S iz e =
注:
C/T -周期时间 C/O -换型调整时间 Uptime -工时利用率 Qty -数量 Lot Size -批量
LT -- 交货周期 MCT -制造周期
VA -增加价值的时间
In s p . L a b e l
Pow er Assy
学习提纲
生产方式的变革 精益思想的基本原则 精益生产的工具运用与选择 导入精益生产的程序与步骤 精益生产与流程再造
第一章 生产方式的变革
手工生产
低产量 个性化
大规模生产同步生产精益 Nhomakorabea产组织大批量少品种 工序式生产 设备大难组合
消除浪费 不断改进 员工参与
在同步生产的基础 上,强调缩短生产 周期提高资源利用 率需求驱动
内部工艺工程
XYZ Corporation
外部资源
C/T = 45 sec C/O = 30 mins 3 Shifts 2% Scrap
丰田生产方式硬环境 整合
5S
看板管理 均衡化 一个流
作业切换
JIT 品质保证 标准作业
多能工
目视管理 设备保养 柔性化
少人化
日本企业的精益生产状况
1950年起,电子行业:独创项目管理与短产品周期——仅仅有三菱公司实验过。 大部分企业——美国过去的:统计质量控制概念、QC手法、PDCA、QCC、QFD等。 ——1960年,日产公司获得“戴明奖” ——丰田采用TQM,1965年获得“戴明奖” (丰田生产模式与TQM结合,是丰田的优势) ——1973年能源危机,大部分企业亏损,而丰田盈利。三菱全面实施丰田模式,马自达、
I
C /T = C /O = U p tim e = L o t S iz e =
注:
C/T -周期时间 C/O -换型调整时间 Uptime -工时利用率 Qty -数量 Lot Size -批量
LT -- 交货周期 MCT -制造周期
VA -增加价值的时间
In s p . L a b e l
Pow er Assy
学习提纲
生产方式的变革 精益思想的基本原则 精益生产的工具运用与选择 导入精益生产的程序与步骤 精益生产与流程再造
第一章 生产方式的变革
手工生产
低产量 个性化
大规模生产同步生产精益 Nhomakorabea产组织大批量少品种 工序式生产 设备大难组合
消除浪费 不断改进 员工参与
在同步生产的基础 上,强调缩短生产 周期提高资源利用 率需求驱动
内部工艺工程
XYZ Corporation
外部资源
C/T = 45 sec C/O = 30 mins 3 Shifts 2% Scrap
精益生产培训管理课程(PPT 92张)
► (2)比规定的时间提前完成了任务。
► 实际上,是生产的速度大于销售的速度,供大于求,
必然产生库存。而库存被精益认为是万恶之源。 ► 精益追求的目标是二者的速度恰好相等。
2、等待
► ► ►
►
► ► ►
生产线品种切换。 工作量忽高忽低。 缺料导致机器和人员闲置。 上道工序故障。 设备故障。 生产线能力不均衡。 监视的浪费:两手抱袖、目光呆滞、无所事 事。
三、学习精益管理应具备的态度:
► 1、承认这是一种成熟、有效的管理技术。 ► 2、承认我们当前的生产模式不是最好的,我
们的现行管理中一定还存在问题: ► (1)效率并不是最高,成本还不是最低,效 益也不是最大。 ► (2)我们永远没有达到尽善尽美的水平,于 是管理中永远存在改进的余地。
三、学习精益管理应具备的态度:
► ►
基础越好的企业,越不容易见效;反之,基 础越差的企业,越容易见效(曲线)。 千万不要讲“我们的基础太差不适合搞精 益”——基础越差越适合搞精益。
9、要有信心
►
► ► ►
丰田公司平均30秒钟一辆车,3万多种零件, 潮水般地涌向生产线,每辆车都不同,设备 还不是最先进的(但是保养良好、最可靠 的)。 从供应商管理、设备管理、生产组织等等方 面想想,难吧?人家就这么干出来了。 我们的现场管理有这么难吗? 不能畏难,应该有十足的信心。
初步应用
► 应用这种思想,丰田产品成本大大下降。 ► 卖到美国被告倾销。 ► 但调查之后,全世界大吃一惊。
► 成本如此低下,价格如此低廉,而利润却如
此丰厚。
精益管理逐步流行
► 后来,美国人潜入丰田,潜心研究学习,回
去后著书立说,反过来推广到欧美和世界各 地,被称为LEAN PRODUCTION。 ► 经过近半个世纪的发展,精益模式在生产中 不断完善,至今天已经形成一套比较成熟、 可靠的生产运营模式而在全世界范围内备受 推崇、广为应用。 ► 近十年间在中国逐渐流行,被称为精益生产 管理。
精益生产培训教材81张幻灯片课件
跑冒滴漏 想些办法防止物品变脏
2024/8/3
43
3-S:清扫
清扫:
清除各场所内的脏污,并防止污染的发生。
目的:清除污染源,保持各场所干净整洁,是品质管理的
基础。
清扫厉行“三扫”原则:
扫漏:针对溢出物;
扫黑:针对角落之物;(即看不到的地方)
扫怪:针对怪异之处。
44 44
5S---STANDARDIZE 标准化
No carrying 不需负重
No crawling 不需俯地
2024/8/3
No accumulating 不需累积
No stacking 不需堆积
No walking 不需走动
No stopping 没有停顿
49
发现浪费方法之 4
VSM 价值流 Gemba 去现场 5S 整理整顿 Visual Control 可视化管理 Layout 布局 Standard Work 标准作业
等料 等人 等机器 等指令 等检验 等……
2024/8/3
11
Waiting 等待
3#
2#
1#
2024/8/3
12
七大浪费之 5:过量生产 OVER
PRODUCTION
生产过多,(局部超产,超额) 生产过早,(局部提早) 超计划生产,(总量超出) 超出客户的需求
2024/8/3
13
Over Production 超额生产
我们所做的就是: 从顾客下定单直到我们收到钱为止。 哪些活动不增加价值。
Order 下定单
Cash 收到钱
2024/8/3
Simple, very clear focus简单,清楚
28
VSM 当前状态
2024/8/3
43
3-S:清扫
清扫:
清除各场所内的脏污,并防止污染的发生。
目的:清除污染源,保持各场所干净整洁,是品质管理的
基础。
清扫厉行“三扫”原则:
扫漏:针对溢出物;
扫黑:针对角落之物;(即看不到的地方)
扫怪:针对怪异之处。
44 44
5S---STANDARDIZE 标准化
No carrying 不需负重
No crawling 不需俯地
2024/8/3
No accumulating 不需累积
No stacking 不需堆积
No walking 不需走动
No stopping 没有停顿
49
发现浪费方法之 4
VSM 价值流 Gemba 去现场 5S 整理整顿 Visual Control 可视化管理 Layout 布局 Standard Work 标准作业
等料 等人 等机器 等指令 等检验 等……
2024/8/3
11
Waiting 等待
3#
2#
1#
2024/8/3
12
七大浪费之 5:过量生产 OVER
PRODUCTION
生产过多,(局部超产,超额) 生产过早,(局部提早) 超计划生产,(总量超出) 超出客户的需求
2024/8/3
13
Over Production 超额生产
我们所做的就是: 从顾客下定单直到我们收到钱为止。 哪些活动不增加价值。
Order 下定单
Cash 收到钱
2024/8/3
Simple, very clear focus简单,清楚
28
VSM 当前状态
- 1、下载文档前请自行甄别文档内容的完整性,平台不提供额外的编辑、内容补充、找答案等附加服务。
- 2、"仅部分预览"的文档,不可在线预览部分如存在完整性等问题,可反馈申请退款(可完整预览的文档不适用该条件!)。
- 3、如文档侵犯您的权益,请联系客服反馈,我们会尽快为您处理(人工客服工作时间:9:00-18:30)。
精益生产的核心内容
Standardized 标准化 Operations 操作
Error 防错 Proofing
Zero Stock 零库存
Smart Card 看板管理
U Style Cell U型制造单元
连续流
SPF 一物流
5S 5S
TEM 预防性维修
Lean Organization
精益组织
标准化作业--精益生产的运行准则
• 标准化工作(作业标准)是成文的、目前最好的、安 全及有效完成工作的方法。并达到必要的质量水准。
• 标准化是改进的基线。标准化工作则是标准化和稳定 性的基本方法。 没有标准化,我们不可能取得不断的 改进。
• 任何重复性的工作都有标准方法,工厂中主要集中于 生产操作、维修操作、更换工模具、物料供给。
精益生产的核心
浪费 消灭一切
!
精益生产目标
浪费
0 库存
缺陷
通过消除浪费、降低成本、 提高质量、缩短制造周期,获得利润。
精益生产的体系构成
• 基础:计算机网络支持、以小组方式工 作的工作方式
• 三大支柱:
– 全面质量管理 – 准时生产和零库存 – 成组技术
精益生产的优越性
• 发现问题随时修改 • 供货环节 • 新产品开发 • 品种和数量 • 与顾客的关系
• 标准化工作进程:周期时间观察、工作要素确定、时 间测量、制作SOS。
• 组员和组长自己动手制定、维护标准化工作。 • 支持人员参与记录最安全、最符合人机工程学的工作
顺序。支持组员的培训及工作灵活性。 • 标准落实于作业区。
1.标准化工作(作业标准)是成文的、目前最好的、安全及有效 完成工作的方法。并达到必要的质量水准。
Planned 计划 Maintenance维护
In Time Supply 及时供货
JIT 准时化生产
More Variety多品种,小 Small Batch批量生产
DTD 门到门时间
Visual Controls 直观控制与管理
Zero Defect 零缺陷
eigonomics 人机工程
Production 生产 Office 办公室 Layout 布局
Quick Set-up 快速换模
Lead Time 缩短制 Reduction 造周期
Pull Systems 拉动式生产
Customer Requirement Rate
客户需求率
准时化生产是什么? (Just In Time)
✓ Right Material ✓ Right Time ✓ Right Quantity ✓ Right Quality ✓ Right Place
准确的材料和零件 在准确的时间 以准确的数量 与必要的质量 送至准确的地点
精益生产的要素
• 生产系统布局-- 精益生产的硬件基础 • 物流输送平衡-- 精益生产的主要对象 • U 型工作单元-- 精益生产的广阔舞台 • 标 准 化 作 业-- 精益生产的运行准则 • 灵捷工模设备-- 精益生产的支持保证 • 推行直观工厂-- 精益生产的信息展现 • FPS 监测指标-- 精益生产的效益量化 • TEAM工作法 --精益生产的开展方法
Section
Date:
4-10-96
Plant
Name Target
Time Cycle Time
KEY:
INPROCESS STOCK
53 sec.
43 sec .
KEY SAFETY/ ERGO
Process
Part
Name Part
#
DELTA CRITICAL
C
QUALITY CHECK
rear panel
TIME FLUCTUATION WORKSHEET 时间波动工作单 JOB ELEMENT SHEET 工作要素单 TIME MEASUREMENT SHEET 时间测量单
STANDARDISED OPERATIC THEET 标准作业单
Quality Process Sheet
Department/ Welding 05
Worksheet
#
5-140
Opr
WGL
Page__1__ of__1__
Sup
Maint
Eng
3302246
QC QUICK
CHANGE OVER
VISUAL FACTORY
FORD Total Prod.T
F
M
Maint.
P
面最好的结果。
• 精益生产是及时制造,消灭故障,消除一切浪费,向 零缺陷、零库存进军。
背景
• 市场需求变化
单品种、大批量
• 日本国情
经济萧条、缺少资金 社会文化背景
多品种、小批量
制造企业的生产制造策略--不同的生产模式
精益生产的产生
日本丰田汽车公司
精益生产的发展历史
精益生产的历史发展过程
• 丰田生产方式形成与完善阶段
精益生产
课程内容
• 定义 • 产生与发展 • 特点与优越性 • 核心内容与生产要素 • 标准化介绍 • 最终目的
什么是精益生产?
• 精益生产是 通过系统结构、人员组织、运行方式和市 场供求等方面的变革,使生产系统能很快适应用户需 求不断变化,并能使生产过程中一切无用、多余的东 西被精简,最终达到包括市场供销在内的生产的各方
大批大量生产方式 尽可能好 宝塔式 分工,专门化 数量很大的标准化产品 大库存缓冲 检验部门事后把关 很大 刚性自动化 组织机构庞大 串行模式 相互封闭 以用户为上帝,但产品少变 互不信任,无长期打算 可随时解雇,工作无保障
精益生产的特征
• 以用户为上帝 • 以“人”为中心 • 以“精简”为手段 • Team Work和并行设计 • JIT供货方式 • “零缺陷”工作目标
• 丰田生产方式的系统化阶段(即精益生 产方式的提出)
• 精益生产方式的革新阶段(对以前的方 法理论进行再思考,提出新的见解 )
精益生产与大批量生产的比较
比较项目 生产目标 管理方式 工作方式 产品特征 供货方式 产品质量 返修率 自动化 生产组织 设计方式 工作关系 用户关系 供应商 雇员关系
精益生产方式 追求尽善尽美 权力下放 集成,多能,综合工作组 面向用户、生产周期短 JIT方式,零库存 由工人保证,质量高,零缺陷 几乎为零 柔性自动化,但尽量精简 精简一切多余环节 并行方式 集体主义精神 以用户为上帝,产品面向用户 同舟共济、生死与共 终身雇佣,以企业为家