蒸发器的设计计算
mvr蒸发器设计计算

mvr蒸发器设计计算蒸发器是一种用于将液体转化为气体的设备,它在各行各业的生产过程中起着重要作用。
气体的蒸发可以实现物质的分离和浓缩,因此有准确的设计和计算蒸发器十分重要。
在蒸发器的设计过程中,MVR (Mechanical Vapor Recompression,机械蒸汽压缩)技术是一种高效能的选择。
MVR蒸发器设计计算主要包括以下几个关键步骤:确定需求、计算传热量、确定蒸发器类型、计算换热面积、确定处理量与浓缩率。
在这篇文章中,我们将详细介绍每个步骤,并给出适用的计算公式和实例。
1. 确定需求在设计MVR蒸发器之前,我们需要明确所需要的蒸发量、物料浓度、产品温度等基本需求。
这些数据将决定我们后续的设计和计算。
2. 计算传热量在MVR蒸发器中,传热是实现蒸发的关键。
传热量的计算可以采用传热方程,根据传热介质和物料的性质来确定。
例如,对于常见的水蒸气传热,我们可以采用传热系数和换热面积来计算所需的传热量。
3. 确定蒸发器类型MVR蒸发器有多种类型,包括单效式、多效式和热泵式等。
根据需求和物料特性,选择适合的蒸发器类型是十分重要的。
不同类型的蒸发器在能耗、蒸发效率和操作成本等方面存在差异,因此需综合考虑各个因素进行选择。
4. 计算换热面积换热面积是蒸发器设计中的重要参数,它决定了传热效果和设备的尺寸。
根据物料的热传导性质、蒸发器类型和其他因素,我们可以采用不同的换热计算方法。
例如,对于扁平管蒸发器,可以使用换热系数和有效传热面积来计算所需的换热面积。
5. 确定处理量与浓缩率根据实际需求,确定处理量和浓缩率是设计MVR蒸发器的重要考虑因素。
处理量指的是单位时间内处理的物料量,而浓缩率则是指在蒸发过程中物料的浓度变化。
处理量和浓缩率之间存在着一定的关系,需要综合考虑。
综上所述,MVR蒸发器设计计算涉及多个关键步骤,包括确定需求、计算传热量、确定蒸发器类型、计算换热面积以及确定处理量与浓缩率。
通过合理的设计和计算,可以实现蒸发过程的高效能和低能耗。
蒸发器的设计计算

蒸发器设计计算已知条件:工质为R22,制冷量kW 3,蒸发温度C t ︒=70,进口空气的干球温度为C t a ︒=211,湿球温度为C t b ︒=5.151,相对湿度为34.56=φ%;出口空气的干球温度为C t a ︒=132,湿球温度为C t b ︒=1.112,相对湿度为80=φ%;当地大气压力Pa P b 101325=。
(1)蒸发器结构参数选择选用mm mm 7.010⨯φ紫铜管,翅片厚度mm f 2.0=δ的铝套片,肋片间距mm s f 5.2=,管排方式采用正三角排列,垂直于气流方向管间距mm s 251=,沿气流方向的管排数4=L n ,迎面风速取s m w f /3=。
(2)计算几何参数翅片为平直套片,考虑套片后的管外径为沿气流方向的管间距为沿气流方向套片的长度为设计结果为 mm s L 95.892565.2132532=+⨯=+=每米管长翅片表面积:每米管长翅片间管子表面积:每米管长总外表面积:每米管长管内面积:每米管长的外表面积:肋化系数:每米管长平均直径的表面积:(3)计算空气侧的干表面传热系数①空气的物性空气的平均温度为空气在下C ︒17的物性参数②最窄截面处空气流速③干表面传热系数干表面传热系数用小型制冷装置设计指导式(4-8)计算(4)确定空气在蒸发器内的变化过程根据给定的进出口温度由湿空气的焓湿图可得kg g d kg g d kg kJ h kg kJ h 443.7,723.8,924.31,364.432121====。
在空气的焓湿图上连接空气的进出口状态点1和点2,并延长与饱和气线()0.1=ϕ相交于点w ,该点的参数是C t kg g d kg kJ h w w w ︒===8,6.6,25。
在蒸发器中空气的平均比焓值 由焓湿图查得kg g d C t m m 8,2.16=︒=析湿系数(5)循环空气量的计算进口状态下干空气的比体积循环空气的体积流量(6)空气侧当量表面传热系数的计算对于正三角形排列的平直套片管束,翅片效率f η小型制冷装置设计指导式(4-13)计算,叉排时翅片可视为六角形,且此时翅片的长对边距离和短对边距离之比4.24.1025d B ,1b m ===ρ且B A 肋折合高度为凝露工况下翅片效率为当量表面传热系数(7)管内R22蒸发时的表面传热系数R22在C t ︒=70时的物性参数为:饱和液体密度 33.1257m kg l =ρ饱和蒸气密度 343.26m kg g =ρ液体粘度 s Pa l ⋅⨯=-6102.202μ气体粘度 s Pa g ⋅⨯=-610815.11μ汽化热 kg kJ 56.1990=γ液体热导率 K m W l ⋅⨯=-/102.133λ蒸气热导率 K m W g ⋅⨯=-/1093.93λ液体普朗特数 62.2=rl P蒸气普朗特数 92.0=rg PR22在管内蒸发的表面传热系数由小型制冷装置设计与指导式(4-5)计算。
多效蒸发器设计计算
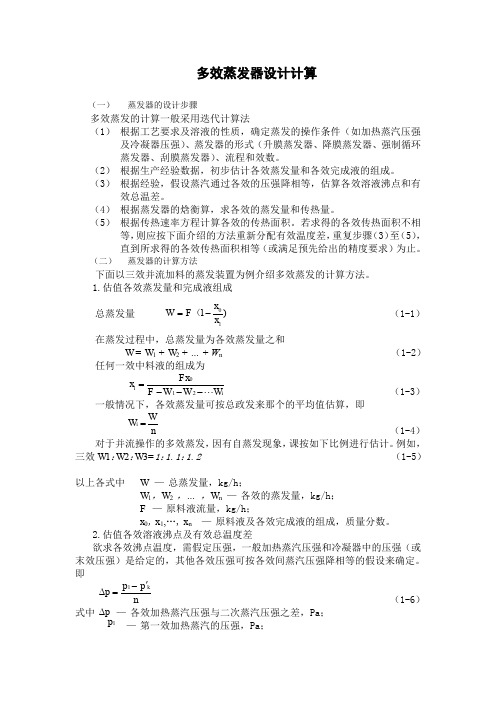
多效蒸发器设计计算(一) 蒸发器的设计步骤多效蒸发的计算一般采用迭代计算法(1) 根据工艺要求及溶液的性质,确定蒸发的操作条件(如加热蒸汽压强及冷凝器压强)、蒸发器的形式(升膜蒸发器、降膜蒸发器、强制循环蒸发器、刮膜蒸发器)、流程和效数。
(2) 根据生产经验数据,初步估计各效蒸发量和各效完成液的组成。
(3) 根据经验,假设蒸汽通过各效的压强降相等,估算各效溶液沸点和有效总温差。
(4) 根据蒸发器的焓衡算,求各效的蒸发量和传热量。
(5) 根据传热速率方程计算各效的传热面积。
若求得的各效传热面积不相等,则应按下面介绍的方法重新分配有效温度差,重复步骤(3)至(5),直到所求得的各效传热面积相等(或满足预先给出的精度要求)为止。
(二) 蒸发器的计算方法下面以三效并流加料的蒸发装置为例介绍多效蒸发的计算方法。
1.估值各效蒸发量和完成液组成总蒸发量 (1-1)在蒸发过程中,总蒸发量为各效蒸发量之和W = W 1 + W 2 + … + W n (1-2) 任何一效中料液的组成为(1-3) 一般情况下,各效蒸发量可按总政发来那个的平均值估算,即(1-4)对于并流操作的多效蒸发,因有自蒸发现象,课按如下比例进行估计。
例如,三效W1:W2:W3=1:1.1:1.2 (1-5)以上各式中 W — 总蒸发量,kg/h ;W 1,W 2 ,… ,W n — 各效的蒸发量,kg/h ;F — 原料液流量,kg/h ;x 0, x 1,…, x n — 原料液及各效完成液的组成,质量分数。
2.估值各效溶液沸点及有效总温度差欲求各效沸点温度,需假定压强,一般加热蒸汽压强和冷凝器中的压强(或末效压强)是给定的,其他各效压强可按各效间蒸汽压强降相等的假设来确定。
即(1-6) 式中 — 各效加热蒸汽压强与二次蒸汽压强之差,Pa ;— 第一效加热蒸汽的压强,Pa ; )110x x F W -=(n W W i =ii W W W F Fx x ---=210n p p p k '-=∆1p ∆1p— 末效冷凝器中的二次蒸汽的压强,Pa 。
蒸发器的设计计算

蒸发器的设计计算蒸发器是一种用于蒸发液体的设备,广泛应用于化工、制药、食品等行业。
它通过提供适当的温度和压力条件,将液体转化为气体,并将其中的溶质分离出来。
蒸发器的设计计算是确保蒸发器能够有效地工作并达到预期性能的重要一环。
1.蒸发器的传热计算:蒸发过程是通过传热实现的,因此需要计算蒸发器的传热表面积和传热系数。
传热表面积的确定涉及到物料的传热需求以及蒸发器的设计参数,例如液体和气体的温度差,气体速度等。
传热系数的计算可以通过经验公式或者通过实验测定得到。
2.蒸发器的蒸汽消耗计算:蒸发过程需要提供适当的蒸汽量来提供传热热量,因此需要计算蒸汽的需求量。
蒸汽消耗的计算涉及到蒸发器的传热效率、物料的传热需求以及蒸汽的热量等因素。
3.蒸发器的液体供给计算:蒸发器是通过液体供给来进行蒸发的,因此需要计算液体的供给量。
液体供给的计算涉及到物料的蒸发速率、液体的流量以及液体的浓度等因素。
4.蒸发器的驱动力计算:蒸发器需要提供适当的驱动力来推动蒸发过程,因此需要计算驱动力的大小。
驱动力的计算涉及到物料的浓度差、压力差以及温度差等因素。
除了以上几个方面,蒸发器的设计还需要考虑到其他因素,例如材料的选择、操作条件的确定以及设备的尺寸等。
蒸发器的设计计算需要综合考虑这些因素,并根据实际情况进行优化。
总结起来,蒸发器的设计计算是一个复杂的过程,需要综合考虑传热、蒸汽消耗、液体供给以及驱动力等因素。
这些计算是确保蒸发器能够有效地工作并达到预期性能的关键。
通过合理的设计计算,可以提高蒸发器的效率,提高生产能力,降低能源消耗,并确保产品质量的稳定性。
各种蒸发器冷凝器计算

各种蒸发器冷凝器计算蒸发器和冷凝器是热力工程中常见的设备,用于蒸发和冷凝流体。
本文将介绍各种蒸发器和冷凝器的计算方法。
一、蒸发器蒸发器是将液体转化为蒸汽的设备。
根据蒸发器的类型有多种不同的计算方法。
1.蒸发器内换热面积计算蒸发器的内换热面积可以通过以下公式计算:A=Q/(U×ΔTm)其中,A为内换热面积,Q为传热量,U为换热系数,ΔTm为平均温差。
2.各种蒸发器的计算常见蒸发器种类有多效蒸发器、喷雾式蒸发器、蒸镜式蒸发器等。
这些蒸发器的计算方法略有不同。
多效蒸发器的换热器内换热面积计算可以使用以下公式:A = Q / (Ud × ΔTmd)其中,A为内换热面积,Q为传热量,Ud为蒸气侧的换热系数,ΔTmd为蒸汽的平均温差。
喷雾式蒸发器的蒸发速率计算可以使用以下公式:W = (G × H) / (λ × (hlg - hgf))量蒸发潜热,hlg为蒸汽的焓值,hgf为液体的焓值。
蒸镜式蒸发器的换热面积和蒸发速率计算方法类似多效蒸发器。
二、冷凝器冷凝器是将蒸汽或气体转变为液体的设备。
根据冷凝器的类型有多种不同的计算方法。
1.冷凝器的内换热面积计算冷凝器的内换热面积可以通过以下公式计算:A=Q/(U×ΔTm)其中,A为内换热面积,Q为传热量,U为换热系数,ΔTm为平均温差。
2.各种冷凝器的计算常见冷凝器种类有冷却管束冷凝器、冷凝器冷凝管束冷凝器等。
这些冷凝器的计算方法略有不同。
冷却管束冷凝器的换热面积计算可以使用以下公式:A = Q / (Ud × ΔTmd)其中,A为内换热面积,Q为传热量,Ud为冷却侧的换热系数,ΔTmd为冷却水的平均温差。
冷凝器冷凝管束冷凝器的冷凝速率计算可以使用以下公式:W = (G × H) / (λ × (hgf - hfg))量冷凝潜热,hgf为蒸汽的焓值,hfg为液体的焓值。
以上就是各种蒸发器和冷凝器的计算方法。
刮板式蒸发器设计计算内容有
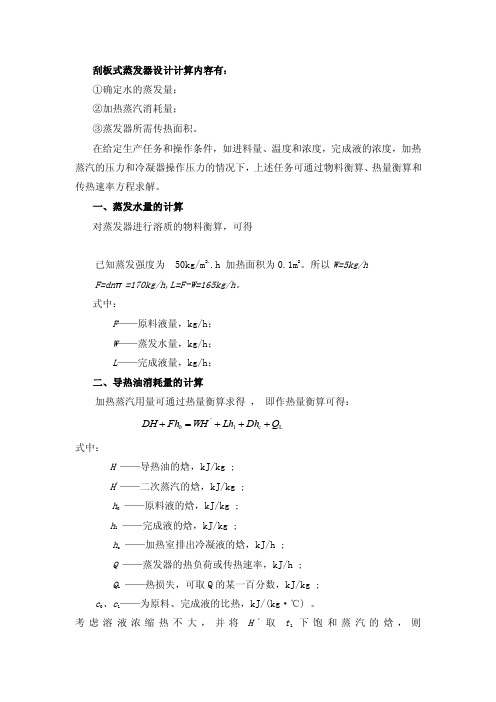
刮板式蒸发器设计计算内容有:①确定水的蒸发量;②加热蒸汽消耗量;③蒸发器所需传热面积。
在给定生产任务和操作条件,如进料量、温度和浓度,完成液的浓度,加热蒸汽的压力和冷凝器操作压力的情况下,上述任务可通过物料衡算、热量衡算和传热速率方程求解。
一、蒸发水量的计算对蒸发器进行溶质的物料衡算,可得已知蒸发强度为 50kg/m 2..h 加热面积为0.1m 2。
所以W=5kg/hF=dn π=170kg/h,L=F-W=165kg/h 。
式中:F ——原料液量,kg/h ;W ——蒸发水量,kg/h ;L ——完成液量,kg/h ;二、导热油消耗量的计算加热蒸汽用量可通过热量衡算求得 , 即作热量衡算可得:L c 10Q Dh Lh W H Fh DH +++=+‘式中:H ——导热油的焓,kJ/kg ;H ´——二次蒸汽的焓,kJ/kg ;h 0 ——原料液的焓,kJ/kg ;h 1 ——完成液的焓,kJ/kg ;h c ——加热室排出冷凝液的焓,kJ/h ;Q ——蒸发器的热负荷或传热速率,kJ/h ;Q L ——热损失,可取Q 的某一百分数,kJ/kg ;c 0、c 1——为原料、完成液的比热,kJ/(kg ·℃) 。
考虑溶液浓缩热不大,并将H ´取t 1下饱和蒸汽的焓,则L c 10Q Dh Lh W H Fh DH +++=+‘式可写成: rQ Wr t t FC D L 010')(++-= 式中: r 、r ´——分别为加热蒸汽和二次蒸汽的汽化潜热,kJ/kg 。
又已知原料由预热器加热至沸点后进料(沸点进料),即t 0=t 1,并不计热损失,则rQ Wr t t FC D L 010')(++-=可写为r Wr D '=由于蒸汽的汽化潜热随压力变化不大,故 r = r ´。
D /W =1,即蒸发一千克水需要约一千克加热蒸汽,实际操作中由于存在热损失等原因,D /W ≈1,即D ≈W=5kg 。
蒸发器的设计计算
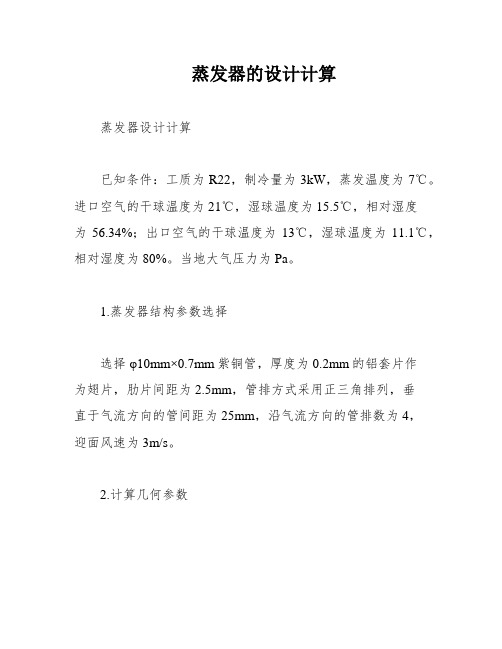
蒸发器的设计计算蒸发器设计计算已知条件:工质为R22,制冷量为3kW,蒸发温度为7℃。
进口空气的干球温度为21℃,湿球温度为15.5℃,相对湿度为56.34%;出口空气的干球温度为13℃,湿球温度为11.1℃,相对湿度为80%。
当地大气压力为Pa。
1.蒸发器结构参数选择选择φ10mm×0.7mm紫铜管,厚度为0.2mm的铝套片作为翅片,肋片间距为2.5mm,管排方式采用正三角排列,垂直于气流方向的管间距为25mm,沿气流方向的管排数为4,迎面风速为3m/s。
2.计算几何参数翅片为平直套片,考虑套片后的管外径为10.4mm,沿气流方向的管间距为21.65mm,沿气流方向套片的长度为86.6mm。
设计结果为每米管长翅片表面积为0.3651m²/m。
每米管长翅片间管子表面积为0.03m²/m。
每米管长总外表面积为0.3951m²/m。
每米管长管内面积为0.027m²/m。
每米管长的外表面积为0.m²/m。
肋化系数为14.63.3.计算空气侧的干表面传热系数1)空气的物性空气的平均温度为17℃。
空气在下17℃时的物性参数为:密度为1.215kg/m³,比热容为1005kJ/(kg·K)。
2)空气侧传热系数根据空气侧传热系数的计算公式,计算得到空气侧的干表面传热系数为12.5W/(m²·K)。
根据给定的数据,蒸发器的尺寸为252.5mm×1mm×10.4mm。
空气在最窄截面处的流速为5.58m/s,干表面传热系数可以用小型制冷装置设计指导式(4-8)计算得到,计算结果为68.2W/m2·K。
在确定空气在蒸发器内的变化过程时,根据进出口温度和焓湿图,可以得到空气的进出口状态点1和点2的参数,连接这两个点并延长与饱和气线相交的点w的参数为hw25kJ/kg。
dw6.6g/kg。
tw8℃。
多效蒸发器设计计算

多效蒸发器设计计算Company Document number:WUUT-WUUY-WBBGB-BWYTT-1982GT多效蒸发器设计计算(一)蒸发器的设计步骤多效蒸发的计算一般采用迭代计算法(1)根据工艺要求及溶液的性质,确定蒸发的操作条件(如加热蒸汽压强及冷凝器压强)、蒸发器的形式(升膜蒸发器、降膜蒸发器、强制循环蒸发器、刮膜蒸发器)、流程和效数。
(2)根据生产经验数据,初步估计各效蒸发量和各效完成液的组成。
(3)根据经验,假设蒸汽通过各效的压强降相等,估算各效溶液沸点和有效总温差。
(4)根据蒸发器的焓衡算,求各效的蒸发量和传热量。
(5)根据传热速率方程计算各效的传热面积。
若求得的各效传热面积不相等,则应按下面介绍的方法重新分配有效温度差,重复步骤(3)至(5),直到所求得的各效传热面积相等(或满足预先给出的精度要求)为止。
(二)蒸发器的计算方法下面以三效并流加料的蒸发装置为例介绍多效蒸发的计算方法。
1.估值各效蒸发量和完成液组成总蒸发量(1-1)在蒸发过程中,总蒸发量为各效蒸发量之和W = W1 + W2 + … + W n (1-2)任何一效中料液的组成为(1-3)一般情况下,各效蒸发量可按总政发来那个的平均值估算,即(1-4)对于并流操作的多效蒸发,因有自蒸发现象,课按如下比例进行估计。
例如,三效W1:W2:W3=1:: (1-5)以上各式中 W — 总蒸发量,kg/h ;W 1,W 2 ,… ,W n — 各效的蒸发量,kg/h ;F — 原料液流量,kg/h ;x 0, x 1,…, x n — 原料液及各效完成液的组成,质量分数。
2.估值各效溶液沸点及有效总温度差 欲求各效沸点温度,需假定压强,一般加热蒸汽压强和冷凝器中的压强(或末效压强)是给定的,其他各效压强可按各效间蒸汽压强降相等的假设来确定。
即(1-6)式中 — 各效加热蒸汽压强与二次蒸汽压强之差,Pa ;— 第一效加热蒸汽的压强,Pa ;— 末效冷凝器中的二次蒸汽的压强,Pa 。
- 1、下载文档前请自行甄别文档内容的完整性,平台不提供额外的编辑、内容补充、找答案等附加服务。
- 2、"仅部分预览"的文档,不可在线预览部分如存在完整性等问题,可反馈申请退款(可完整预览的文档不适用该条件!)。
- 3、如文档侵犯您的权益,请联系客服反馈,我们会尽快为您处理(人工客服工作时间:9:00-18:30)。
蒸发器设计计算已知条件:工质为R22,制冷量kW 3,蒸发温度C t ︒=70,进口空气的干球温度为C t a ︒=211,湿球温度为C t b ︒=5.151,相对湿度为34.56=φ%;出口空气的干球温度为C t a ︒=132,湿球温度为C t b ︒=1.112,相对湿度为80=φ%;当地大气压力Pa P b 101325=。
(1)蒸发器结构参数选择选用mm mm 7.010⨯φ紫铜管,翅片厚度mm f 2.0=δ的铝套片,肋片间距mm s f 5.2=,管排方式采用正三角排列,垂直于气流方向管间距mm s 251=,沿气流方向的管排数4=L n ,迎面风速取s m w f /3=。
(2)计算几何参数翅片为平直套片,考虑套片后的管外径为mm d d f o b 4.102.02102=⨯+=+=δ沿气流方向的管间距为mm s s 65.21866.02530cos 12=⨯=︒=沿气流方向套片的长度为mm s L 6.8665.21442=⨯==设计结果为 mm s L 95.892565.2132532=+⨯=+= 每米管长翅片表面积:f b f s d s s a 100042221⨯⎪⎭⎫ ⎝⎛-⋅=π ()5.210004.10414.365.212522⨯⎪⎭⎫ ⎝⎛⨯-⨯⨯= m 23651.0=每米管长翅片间管子表面积:ff f b b s s d a )(δπ-=()5.210002.05.24.1014.3⨯-⨯⨯= m m 203.0=每米管长总外表面积:m m a a a b f of 23951.003.03651.0=+=+=每米管长管面积:m m d a i i 2027.0)20007.001.0(14.3=⨯-⨯==π每米管长的外表面积:m m d a b b 2003267.00104.014.3=⨯==π肋化系数:63.14027.03951.0===iof a a β每米管长平均直径的表面积:m m d a m m 202983.020086.00104.014.3=⎪⎭⎫ ⎝⎛+⨯==π(3)计算空气侧的干表面传热系数 ①空气的物性 空气的平均温度为C t t t a a f ︒=+=+=1721321221 空气在下C ︒17的物性参数3215.1m kg f =ρ()K kg kJ c pf ⋅=1005704.0=rf Ps m v f 61048.14-⨯=②最窄截面处空气流速()()()()s m s s s s w w f f f d fb 58.52.05.25.24.102525311max =--⨯=--=δ③干表面传热系数干表面传热系数用小型制冷装置设计指导式(4-8)计算15.04.00max 42618.00014.0--⎪⎪⎭⎫⎝⎛⎪⎪⎭⎫⎝⎛+=bo of f a a v d w α15.04.0603267.03951.01048.140104.058.52168.00014.0---⎪⎭⎫ ⎝⎛⎪⎭⎫⎝⎛⨯⨯+=00792.0=()()()km W P c w r pff ⋅=⨯⨯⨯==23232max 402.68704.0100558.5215.100792.0ραα(4)确定空气在蒸发器的变化过程根据给定的进出口温度由湿空气的焓湿图可得kg g d kg g d kg kJ h kg kJ h 443.7,723.8,924.31,364.432121====。
在空气的焓湿图上连接空气的进出口状态点1和点2,并延长与饱和气线()0.1=ϕ相交于点w ,该点的参数是C t kg g d kg kJ h w w w ︒===8,6.6,25。
在蒸发器中空气的平均比焓值kg kJ n h h h h nh h h h ww w m /73.3625924.3125364.431924.31364.432512121=---+=---+=由焓湿图查得kg g d C t m m 8,2.16=︒= 析湿系数42.182.166.6846.2146.21=--+=--+=w m w m t t d d ξ(5)循环空气量的计算h kg h h Q q da m 06.944924.31364.4336003210,=-⨯=-=进口状态下干空气的比体积()ba P d T R v 1110016.01+=()()101325723.80016.012115.2734.287⨯++⨯=kg m 3846.0= 循环空气的体积流量h m v q q da m a v /67.798846.006.94431,,=⨯==(6)空气侧当量表面传热系数的计算⎪⎪⎭⎫⎝⎛++=b f b f f j a a a a ηξαα0 对于正三角形排列的平直套片管束,翅片效率f η小型制冷装置设计指导式(4-13)计算,叉排时翅片可视为六角形,且此时翅片的长对边距离和短对边距离之比4.24.1025d B ,1b m ===ρ且B A 3.027.1-='BAmρρ 3.014.227.1-⨯⨯= 55.2= 肋折合高度为()()()()mm d h b7.1055.2ln 35.01155.224.10ln 35.0112=⨯+-='+-'='ρρ mm ff 106.643102.023642.12.68220=-⨯⨯⨯⨯==δλξα凝露工况下翅片效率为()8683.0107.1006.64107.1006.64)(33=⨯⨯⨯⨯=''=--th h m h m th f η 当量表面传热系数⎪⎪⎭⎫⎝⎛++=b f b f f j a a a a ηξαα0 ⎪⎭⎫⎝⎛+⨯⨯⨯=3951.003.0365.08683.02.6842.1)/(06.852K m W ⋅= (7)管R22蒸发时的表面传热系数 R22在C t ︒=70时的物性参数为: 饱和液体密度 33.1257m kg l =ρ 饱和蒸气密度 343.26m kg g =ρ 液体粘度 s Pa l ⋅⨯=-6102.202μ 气体粘度 s Pa g ⋅⨯=-610815.11μ 汽化热 kg kJ 56.1990=γ 液体热导率 K m W l ⋅⨯=-/102.133λ 蒸气热导率 K m W g ⋅⨯=-/1093.93λ 液体普朗特数 62.2=rl P 蒸气普朗特数 92.0=rg PR22在管蒸发的表面传热系数由小型制冷装置设计与指导式(4-5)计算。
计算查的R22进入蒸发器时的干度25.01=x ,出口干度0.12=x 。
则R22的总质量流量为()()h kg x x Q q m 16.7225.0156.1993600336001200=-⨯⨯=-⨯=γ作为迭代计算的初值,取27200m W q i =,R22在管的质量流速()s m kg g i ⋅=2'160。
则总流通面积为24'1025.1360016016.723600m q q A i m -⨯=⨯=⨯=每根管子的有效流通截面积2522108.540086.014.34m d A i i -⨯=⨯==π蒸发器的分路数16.2108.51025.154=⨯⨯==--i A A Z结合分液器的实际产品现状,取分路数为 Z=2 每一分路中R22的质量流量为h kg Z q g m m 08.36216.72===每一分路中R22在管的实际质量流速为()s m kg A g g i m i ⋅=⨯⨯=⨯=-258.172108.5360008.363600 于是40101.256.1998.1722.7-⨯=⨯==r g q B i i 09634.03.125743.26625.0625.0115.08.05.08.00=⎪⎭⎫ ⎝⎛⎪⎭⎫ ⎝⎛-=⎪⎪⎭⎫ ⎝⎛⎪⎭⎫ ⎝⎛-=lg x x C ρρ()()224.00086.08.93.12578.1722222=⨯⨯==i l i rl gd g F ρ ()()08.2756102.2020086.0625.018.1721Re 6=⨯⨯-⨯=-=-l i l d x i g μ()()ilrl l l d P λα4.08.0Re 023.0=()()0086.00932.062.208.2756023.04.08.0⨯=11.207=()()()⎥⎦⎤⎢⎣⎡+=fl c c rl cl i F B C F C C 452030125αα()()()[]2.2101.22.667224.02509634.0136.111.2077.043.09.0⨯⨯⨯+⨯⨯⨯=--)K m W ⋅=235.4050(8)传热温差的初步计算C t t t t t t a a a a m ︒=---=---=44.9713721ln 1321ln20121θ(9)传热系数的计算管污垢热阻i r 可以忽略,接触热阻以及导热热阻之和取为()K m W r ⋅=200048.0()K m W r a a k jii of⋅=++⨯=++=2006.4906.8510048.0027.035.40503951.0111αα(10)核算假设的i q 值202.46844.96.49m W k q m o =⨯==θ268512.468027.03951.0m W q a a q o iof i =⨯==计算表明,假设的27200m W q i =初值与核算的值26851m W 较接近,故假设有效,可用。
(11)蒸发器结构尺寸的确定 蒸发器所需的表面传热面积20'417.072003000m q Q A i i ===20'0408.62.4683000m q Q A o ===蒸发器所需传热管总长m a A l of t21.163951.0408.6'0'===迎风面积 2,074.03600367.798m w q A fa v f =⨯==取蒸发器的宽度mm B 350=,高mm H 300=。
实际迎风面积为2105.03.035.0m A f =⨯=。
已选定垂直于气流方向的管间距为mm s 251=,故垂直于气流方向的每排管子数为122530011===s H n 深度方向为4排,共布置48根传热管,故传热管的实际总长为m l t 8.164835.0=⨯=传热管的实际表面传热面积为2454.042.00086.014.34835.048m d A i i =⨯⨯⨯=⨯⨯=π09.1417.0454.0'==i i A A 04.121.168.16'==t t l l 下面计算蒸发器的实际外表面积 48根m 35.0长的管其翅片间管子表面积2505.00002.05.235035.00104.014.348m =⎪⎭⎫⎝⎛⨯-⨯⨯⨯管子左右两边都要伸出一定距离,分别取为mm 10,mm 3;U 型管需要用弯头相接,取弯头半径为mm R 5.12=。