烧结配料的计算调整
烧结配料计算第一步

烧结配料计算第一步估算烧结矿预想成分范围值一、初步范围值:想要估算烧结矿预想成分必须以炼铁对烧结矿的总体要求和含铁原料库存状况入手。
根据炼铁对烧结矿全铁含量、二元碱度和氧化镁等成分的要求下制定最大范围的烧结矿成分含量,然后分析含铁物料组合是否能满足炼铁要求。
注意原料中的总体全铁含量必须高于烧结矿要求的全铁含量,其他原料满足烧结矿其他成分和质量指标。
二、精确范围值:根据优先定硅原则,进一步预算烧结矿成分范围值。
优先定硅原则:计算烧结矿配比时从确定烧结矿二氧化硅含量开始,以二氧化硅为中心进行配料计算,得到预想烧结矿的具体成分范围值。
据高硅低碱、低硅高碱和二元碱度的要求确定烧结矿中二氧化硅含量,高碱度烧结矿的二氧化硅含量 4.7-5.7(4.5-6)为最佳范围值(高碱度烧结矿的二氧化硅含量不宜超过5.5、超高碱度烧结矿的二氧化硅含量不宜超过 5.2、2.5以上碱度的烧结矿二氧化硅含量不宜超过5);氧化钙根据二元碱度和二氧化硅范围求得;三氧化二铝不超过二氧化硅量的一半;氧化镁的配入量需要使烧结矿的二元碱度与四元碱度的比值为1.1-1.2之间,其他金属(轻金属:比铁轻的金属,相对密度小于5)、重金属(比铁重的金属,相对密度大于5)和碱金属(能与氧气直接发生反应的金属)及脉石成分≤1%;其余成分为铁的氧化物(三氧化二铁、氧化亚铁、四氧化三铁)三、验算验算烧结预想成分的合理性1、烧结矿全量:全铁/0.7-0.11氧化亚铁+二氧化硅+氧化钙+氧化镁+三氧化二铝+0.5~1(杂质和残碳)=100(杂质的量根据配加原料的成分做具体分析;残碳结合烧结过程确定,范围值0.1-0.3)2、验算原料亚铁值:结合烧结原料成分校对后数据,有亚铁的物料成分乘以各自配比然后求和,求和值除以总残存既得出烧结矿中的原料带入亚铁值。
这是在没有氧化还原反应时烧结矿理论含亚铁量,应是烧结矿中亚铁含量的1~1.1倍。
它是确定烧结矿亚铁含量的数据标量,也是烧结总体过程是否为弱氧化反应的衡量点。
烧结计算公式

烧结计算公式产量台时台时=利用系数=作业时间 210作业时间作业率=%(取参数报表中时间)日历时间作业时间扣外作业率=%(取参数报表中时间、影响因素)日历时间-外因时间产量成品率=%(返矿取配料配比变更)产量+返矿某物料干料量干料量=该原料湿料量×(1-H2O%)单耗=×1000 (kg)产量铁料原料消耗(单耗)=1吨消耗多少公斤该物料。
匀矿×印粉配加百分比×(1-H2O%)例:印粉=━━━━━━━━━━━━━━━━━×1000 (kg)烧结矿产量一次配料:某料下料量=某料的百分比×总下料量∕100 (t)某料总配比表中配比一次配料某物料配比=━━━━━━━━━━━━━━━━━一次配料物料在总配比表配比之和某物料下料量=某物料下料量(吨/小时)×运行时间段产量返矿出矿率=%返矿率=%混合料总量×0.92 产量+返矿反推产量=高返×0.97+落地量-上落地量+高炉入炉烧结矿量其它计算公式黑料合量公式(FeO×0.777-TFe)×1.43-FeO-SiO2-CaO-MgO=98-99白料合量公式CaO×1.784+MgO×2.09+SiO2=96-99有效CaO石=CaO石-SiO2石×R基(R烧-R基)×SiO2石∕有效CaO石=需加减灰石量(混合料SiO2总-SiO2石)×R基-(混合料CaO总-CaO石)=R基需要CaOR基需要CaO灰石湿配比=÷(1-H2O%)有效CaO石CaOR=SiO2反推产量=高炉入炉烧结矿+高返×0.97+落地量-上落地量铺底料使用量计算公式:铺底料用量=台车宽度×铺底料厚度×烧结矿堆比重×机速×运行时间例:3.5×0.04×1.7×720×1.05(机速)=180T残存=干料*(1-烧损%)各物料残留成份计算:TFe=干料×TFe%SiO2=干料×SiO2% CaO=干料×CaO%MgO=干料×MgO% Al2O3=干料×Al2O3%烧结矿成份计算:TFe=各物料残留TFe之和×100∕各物料残存之和SiO2=各物料残留SiO2之和×100∕各物料残存之和CaO=各物料残留CaO之和×100∕各物料残存之和MgO=各物料残留MgO之和×100∕各物料残存之和Al2O3=各物料残留Al2O3之和×100∕各物料残存之和。
烧结配料计算第五步

烧结配料计算第五步确定配比值一、查看预想成分和既定少烧结矿成分要求的相符程度。
查看烧结矿预想成分与既定的烧结矿各项指标是否匹配,全铁值应控制在在±0.5%之内,其他成分波动值在±0.2%之内,1、预想烧结矿全铁成分>既定成分0.5%以上,绝大部分的情况是因为预算时的烧成量过小引起的;预想烧结矿全铁成分<既定成分0.5%以上,绝大部分情况是因为计算时的烧成量过大引起的。
两种情况都需要重新计算各种物料的烧损值。
如果各种物料的烧损值没有问题,则需要重新用全量公式验算各种物料的全铁含量,尤其是铁矿粉的全铁含量。
2、预想烧结矿中二元碱度、氧化镁和三氧化二铝的含量应控制在既定成分的±0.2%之内。
如果不在此范围内应首先查找烧损原因,其次查找各种物料的这几种成分含量是否准确无误。
二、验算烧结矿预想成分全量是否在99-100%之间。
用烧结矿全量公式:全铁/0.7-0.11氧化亚铁+二氧化硅+氧化钙+氧化镁+三氧化二铝+0.5~1(残炭和杂质)=100验算烧结矿预想成分全量是否在99-100%之间。
1预想烧结矿全量<99%,说明一种或几种物料全量不足90%,需要检查后重新计算预想烧结矿成分。
2、预想烧结矿全量>100%,说明一种或几种物料全量超过100%或计算时有错误存在,必须重新检查物料全量及重新计算预想烧结矿成分。
三、检查烧结原料带入亚铁总量和既定烧结矿亚铁含量的比值高碱度原料带入亚铁总量是否为烧结矿亚铁含量的1.0-1.1倍。
原料带入的总亚铁量低于烧结矿的亚铁量,烧结焙烧过程总体就是还原反应;带入的总亚铁量高于烧结矿的亚铁量时,烧结的焙烧过程总体就是就是氧化反应。
而高碱度烧结矿的焙烧过程总体为弱氧化性是高碱度烧结矿的主要特性之一。
注:此三条都吻合时,就可基本确定计算烧结配比的准确性。
但是配比的优化程度还需要烧结过程的实际情况来检验。
所以计算出配比只是配料师工作完成的其中一部分,接下来还需要配料师到现场观测、指导烧结手法、修正烧结过程参数和优化配比。
烧结配料计算第三步

烧结配料计算第三步确立配料原则一、一次配料原则及补充说明一)一次配料的原则1、粒度混匀矿最佳的粒度组成应该是:0mm~3mm占20~40%;3mm~5mm占40~60%;5mm~8mm<15%;8mm以上<5%[2]。
2、水份混匀矿综合水份5~6.5%[3];结晶水≤3%[4]。
3、烧损混匀矿综合烧损控制在8~10%为宜。
(烧结配料的基本标准。
)4、氧化镁含量混匀矿中氧化镁含量一般应调至其三氧化二铝含量的 1.3~1.5倍,一般值为:2~3%。
这不仅关系到烧结矿的矿相组成,而且直接关系到高炉冶炼的顺行。
(烧结配料的基本标准。
)5、碱度混匀矿二元碱度一般控制在1.1~1.2[5]。
(烧结配料的基本标准。
)二)补充说明矿粉比例:铁矿粉的具体配入量需按混合料粒度组成、亚铁含量、矿相组成和成本的要求计算获得。
如果原料条件达不到最佳配比状态,可按粒度要求进行铁料搭配。
粒度:没有海沙、镍矿等特殊物料配入时可按此粒度组成进行配料。
水分:结晶水越少越好。
烧损:混匀矿烧损不越小烧结矿相对产量越高,一般情况下不低于5%。
氧化镁含量:这个比例不仅关系到四元碱度与二元碱度的匹配,而且在一定程度上决定烧结矿相组成的合理性。
碱度:在一定程度上决定烧结矿相组成的合理性。
配料计算:湿基值代入计算以确保配料的准确性,同时保证原料不亏库。
二、燃料配加要求固定碳、灰分、挥发分的要求焦粉:固定碳≥80%,灰分<18%;挥发分<1%;灰分:其中二氧化硅占60%左右,三氧化二铝占30%左右,其他占10%左右(焦粉全量拆分参照值)。
白煤(无烟煤):固定碳≥75%;灰分<25%;挥发分<1.5%;灰分:其中二氧化硅占60%,三氧化二铝占30%左右,其他占10%(白煤全量拆分参照值)。
粒度水分要求焦粉粒度:0-3mm≥75%;3mm-5mm≤20%;5mm-8mm<3%,焦粉水分<10。
白煤粒度:0-3mm≥65%;3mm-5mm≤30%;5mm-8mm<5%,白煤水分<10。
烧结工艺

品位=Tfe总量 ÷ 残存总量×100%
CaO =CaO总量 ÷ 残存总量×100%
MgO =MgO总量 ÷ 残存总量×100%
SiO2 =SiO2总量 ÷ 残存总量×100%
TiO2 =TiO2总量 ÷ 残存总量×100%
V2O5 =V2O5总量 ÷ 残存总量×100%
带入Tfe=配比×TFe含量=71.5%×64.11%≈45.84%
带入CaO=配比×CaO含量=71.5%×64.11%≈0.915%
带入SiO2=配比×SiO2含量=71.5%×64.11%≈2.881%
带入MgO=配比×MgO含量=71.5%×64.11%≈0.858%
球团返矿 2 61 1.2 5.3 1 2.1 0.4 0 1.22 0.024 0.106 0.020 0.042 0.007 2
瓦斯灰 0.9 30 5 7 1 0.2 45 0.26 0.043 0.060 0.000 0.009 0.001 0.4675
白灰粉 7.7 76 4 6 15 0.00 5.814 0.306 0.459 0.000 0.000 6.5025
残存总量为所有物料烧成量的和。Tfe总量为所有物料带入铁量的总和;CaO为所有物料带入CaO的总和;SiO2为所有物料带入SiO2的总和;MgO为所有物料带入MgO的总和;TiO2为所有物料带入TiO2的总和;V2O5为所有物料带入V2O5的总和。
(4)、计算烧结矿碱度、品位、CaO、MgO、SiO2、TiO2、V2O5
轻烧白云石粉 4 45 2.5 30 11 0.00 1.800 0.100 1.200 0.000 0.000 3.56
烧结原理及配料计算
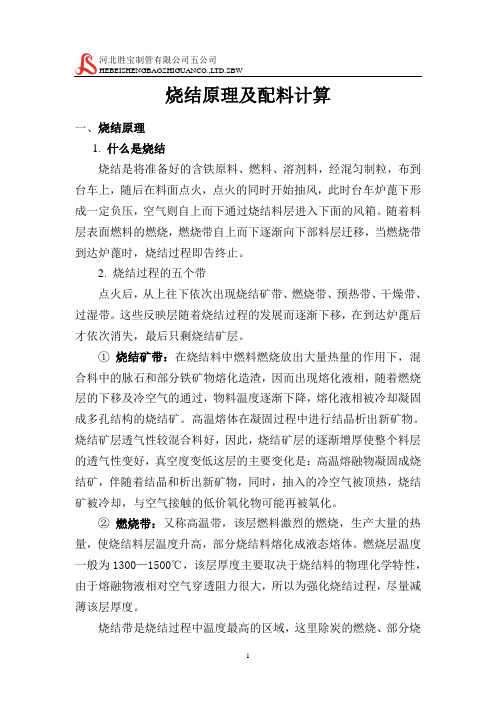
HEBEISHENGBAOZHIGUANCO.,LTD.SBW烧结原理及配料计算一、烧结原理1. 什么是烧结烧结是将准备好的含铁原料、燃料、溶剂料,经混匀制粒,布到台车上,随后在料面点火,点火的同时开始抽风,此时台车炉蓖下形成一定负压,空气则自上而下通过烧结料层进入下面的风箱。
随着料层表面燃料的燃烧,燃烧带自上而下逐渐向下部料层迁移,当燃烧带到达炉蓖时,烧结过程即告终止。
2. 烧结过程的五个带点火后,从上往下依次出现烧结矿带、燃烧带、预热带、干燥带、过湿带。
这些反映层随着烧结过程的发展而逐渐下移,在到达炉蓖后才依次消失,最后只剩烧结矿层。
①烧结矿带:在烧结料中燃料燃烧放出大量热量的作用下,混合料中的脉石和部分铁矿物熔化造渣,因而出现熔化液相,随着燃烧层的下移及冷空气的通过,物料温度逐渐下降,熔化液相被冷却凝固成多孔结构的烧结矿。
高温熔体在凝固过程中进行结晶析出新矿物。
烧结矿层透气性较混合料好,因此,烧结矿层的逐渐增厚使整个料层的透气性变好,真空度变低这层的主要变化是:高温熔融物凝固成烧结矿,伴随着结晶和析出新矿物,同时,抽入的冷空气被顶热,烧结矿被冷却,与空气接触的低价氧化物可能再被氧化。
②燃烧带:又称高温带,该层燃料激烈的燃烧,生产大量的热量,使烧结料层温度升高,部分烧结料熔化成液态熔体。
燃烧层温度一般为1300—1500℃,该层厚度主要取决于烧结料的物理化学特性,由于熔融物液相对空气穿透阻力很大,所以为强化烧结过程,尽量减薄该层厚度。
烧结带是烧结过程中温度最高的区域,这里除炭的燃烧、部分烧结料融化外,还伴随着碳酸盐的分解,硫酸盐的分解、硫化物和磁化矿的氧化,部分赤铁矿的热分解、还原等。
总之,这一带的物理化学变化异常复杂。
③预热带:空气通过燃烧带参加反映后,即携带一部分热量进入下部为预热带。
预热带厚度较薄,与燃烧带紧密相连,温度一般为400℃—800℃,在预热带,烧结料中的结晶水分解,部分碳酸盐,硫酸盐也开始分解,磁铁矿局部被氧化及组分间的固相反应等。
烧结配料计算实战案例解析一
烧结配料计算实战案例解析一一步步讲解配比计算的思路与具体方法步骤,希望大家能有举一反三的能力,尽快把实战案例中的配料方法应用到日常工作中去。
一、原料成分分析原料成分时首先观察和分辨各种原料名称、化学组成、物理结构和冶金性能。
如果遇到不认识的原料应及时弄清楚物料性质、查询产地、分析化学成分、判断其所有性能及应用方法。
对于铁料的不同叫法也应有一定的了解,不应在叫法不同时产生对物料的误判断。
其次对于各种物料成分的观察应有侧重点,铁料重点是全铁、二氧化硅和烧损(铁矿粉的烧损由结晶水的析出和氧化还原反应两部分组成,其中化验的烧损为结晶水烧损,两部分的量均可用全量公式求得);熔剂重点是二氧化硅、氧化钙、氧化镁和烧损(熔剂的烧损由结晶水的析出和碳酸盐分解两部分组成,化验烧损为两部分之和。
碳酸盐分解由化学方程式带入分子量求得,烧损剩余部分为结晶水);燃料的重点是烧损、二氧化硅和三氧化二铝。
(燃料的烧损由碳的气化、结晶水的析出和挥发分三部分组成,化验烧损一般为三项之和。
焦粉一般不含结晶水,挥发分含量也很少);辅料应全面分析(辅料的烧损由炭的气化、结晶水的析出两部分组成,化验烧损为两部分之和)。
二、上级下达或炼铁需要指标每个公司、厂矿下达的烧结矿指标都不尽相同,各有侧重点。
作为配料技师来讲,应把烧结矿的所有物化指标都优化到极致作为工作目标。
所以在完成既定指标和任务的同时也应以不断提升烧结矿其他性能为职责,尤其烧结矿对高炉冶炼过程影响的控制应作为配料技师工作的重中之重。
三、步骤第一步估算烧结矿预想成分首先根据优先定硅原则和现场物料状况预算烧结矿成分范围值。
然后预测的范围值根据炼铁部的要求,运用全量公式,进一步缩小范围。
经过一定验算经验和现场生产经验的积累就可以达到把烧结矿的预想成分确定在很小的范围。
第二步校准化验成分校准化验成分时的注意事项1、由于物料中的微量元素无法全部测量,所以一般情况下全量值不会超过100%。
2、全量验算出现偏差较大时,必须根据现场具体情况找出原因,判断准确后进行校准。
烧结配料碱度现场快速调整法
烧结配料碱度现场快速调整法:(1)两种物料配比发生变化:生石灰配比差(%)=配比调整值×(ΣSiO2差值×R2-ΣCaO差值)÷CaO有效生石灰(2)碱度变化调整:生石灰配比差(%)=(新R2×SiO2矿-CaO 矿)÷CaO有效新(3)生石灰成分变化:生石灰配比差(%)=原配比×CaO有效原÷CaO有效新-原配比例1:已知铁精粉SiO2为5.5%、CaO为0%,配比为20%,高返SiO2为5.3%、CaO为9.01%,配比为12%,原烧结矿碱度为1.9倍,生石灰中有效钙74%,现将铁精粉配比上调3%,高返配比下调3%,如碱度不变情况下,生石灰应调整多少?解:根据公式推出:生石灰配比差(%)=3×{(5.5-5.3)×1.9+(9.01-0)}÷74=0.38则在碱度不变情况下,生石灰配比应上调0.38%,给定物料配比找齐。
例2:已知原烧结矿碱度为2.0倍,SiO2为5.5%、CaO为11%,生石灰成分SiO2为2.5%、CaO为78%,根据生产需求现将碱度上调到2.1倍,问生石灰应调整多少?解:根据公式推出:生石灰配比差(%)=(2.1×5.5-11)÷(78-2.1×2.5)=0.75%则在碱度不变情况下,生石灰配比应上调0.38%,给定物料配比找齐。
则碱度上调到2.1倍后,生石灰配比应上调0.75%,给定物料配比找齐。
例3:已知原烧结矿碱度为2.0倍,生石灰成分SiO2为2.5%、CaO为78%,配比7%,外购生石灰成分SiO2为1.5%、CaO为85%,问碱度不变情况下,生石灰应调整多少?解:根据公式推出:生石灰配比差(%)={7×(78-2.0×2.5)÷(85-2.0×1.5)}-7=-0.76%则在碱度不变情况下,生石灰配比应下调0.69%,给定物料配比找齐。
烧结配料计算实战案例解析二
烧结配料计算实战案例解析二案例2主要讲述如何实现优化和优化可以达到的效果,以及各种原则为何能成为烧结顺行和配比优化的保障。
某钢铁公司90平米步进式烧结机原料条件(校对后)公司下达的烧结矿指标烧结矿品位TFe:≥54;二元碱度:1.85±0.1,合格率90%;亚铁:8-10%;转股强度≥75%;高返矿率≤15%。
大家从对烧结矿下达的指标可以看出,每个企业对烧结矿指标的要求大相径庭。
但作为烧结配料技师来讲必须把配料过程控制的精细和准确,以追求最优化的配比为目标,为了整个钢铁长流程的高效、低耗的生产打好坚实的基础。
对比说明:①优化前原配比把燃料配比不计入烧结配比100%内,造成烧结矿烧损计算不准确、烧结物料成分带入量不准确,计算矿相组成和实际矿相组成偏差较大,最终导致烧结矿整体预想成分不准确;实际烧成量比计算出的烧成量小,造成烧结生产概念性错误,同时造成配入量不准确,导致所有的产量、原料消耗和库存量不准确,成本难以核算。
②优化前白云石用量少,碳酸盐配加量不够,氧化镁和三氧化二铝比值为0.8,二元碱度和四元碱度的比值为1.24,这样情况下导致焙烧过程料面收缩不够,烧结矿结矿困难,烧结矿机械强度差,粉化率提高,返矿增加,产量降低,成本升高。
③优化前生石灰配加量大,在有粒度很好的镍矿配入、烧结焙烧过程料面透气性好的情况下配入大量生石灰只会降低烧结矿结矿强度,增加返矿,增加成本。
④优化前由于杨迪粉二氧化硅波动大,配加量大造成烧结矿中二氧化硅量波动大,二元碱度波动大,碱度合格率低。
优化后用全量公式核算各种铁粉历次化验成分,确定杨迪粉二氧化硅含量在4-5.6%之间波动较大,减少杨迪粉配加量,增加了印粉配加量,大幅度提高了碱度合格率。
很多情况下:铁料的全铁比较稳定,二氧化硅和结晶水互补性波动。
⑤优化前由于矿相结构、物料组成不合理返矿产生和配入量较大;优化后返矿减少,产量提高,成本降低。
⑥优化前实际生产数值:烧结矿碱度合格率/月=85%;烧结矿转股系数/月=73~75;烧结综合返矿率20~23;烧结机利用系数:1.35。
烧结配料计算方法及公式
烧结配料计算的方法烧结过程是一个非常复杂的氧化还原过程,氧的得失很难确定,原料成分的波动和水分的大小均会对最终结果产生影响,而要精确进行烧结配料的理论计算,在烧结生产中显得尤为麻烦,并且要占用大量的时间,所以,现场配料计算一般多采用简易计算方法,即:反推算法。
所谓反推算法是先假定一个配料比,并根据各种原料的水分、烧损、化学成分等原始数据,计算出烧结矿的化学成分,当计算结果符合生产要求,即可按此料比进行组织生产,如果不否,再重新进行调整计算,直至满足生产要求为止。
如果在实际生产中,所计算的配比和实际有误差,可分析其产生误差的原因,并再次进行调整计算。
生产中如何确定配料比,也是大家所关心的一个问题,实际上配料比的确定常常是根据炼铁生产对烧结矿的质量指标的要求和原料供应状况以及原料成分等,并结合生产成本进行合理的搭配,反复计算,得出最终使用的配料比。
一、在进行反推算法计算时,首先要了解有关配料方面需要掌握的一些术语。
1、烧损:物料的烧损是指(干料)在烧结状态的高温下(1200—1400摄氏度)灼烧后失去重量对于物料试样重量的百分比。
2、烧残:物料的残存量即物料经过烧结,排出水分和烧损后的残存物量。
3、水分:烧结原料的水分含量是指原料中物理水含量的百分数,即一定的原料(100g— 200g)加热至150摄氏度,恒温1h,已蒸发的水分重量占试样重量的百分比。
4、化学成分:原料的化学成分是指某元素或化合物含量占该种干原料试样重量的百分比。
二、具体计算公式1、烧残量二干料配比X(1—烧损)2、进入配合料中的TFe=该种原料含TFe量X该种原料配比3、进入配合料中的SiO2=该种原料含SiO2量X该种原料配比4、进入配合料中的CaO=该种原料含CaC Mx该种原料配比5、进入配合料中的MgO=该种原料含MgO tx该种原料配比6 进入配合料中的Mr^该种原料含Mn量X该种原料配比7、烧结矿的化学成分烧结矿TFe=各种原料带入的TFe之和十总的烧残量烧结矿SiO2=各种原料带入的SiO2之和十总的烧残量烧结矿Ca8各种原料带入的CaO之和十总的烧残量烧结矿Mg®各种原料带入的MgO 之和十总的烧残量烧结矿Mn^各种原料带入的Mn之和十总的烧残量如果还有其他指标要求,其计算公式同上。
- 1、下载文档前请自行甄别文档内容的完整性,平台不提供额外的编辑、内容补充、找答案等附加服务。
- 2、"仅部分预览"的文档,不可在线预览部分如存在完整性等问题,可反馈申请退款(可完整预览的文档不适用该条件!)。
- 3、如文档侵犯您的权益,请联系客服反馈,我们会尽快为您处理(人工客服工作时间:9:00-18:30)。
烧结配料的计算调整
一、现场简易计算调整
1、干料配比=湿料配比×(100-水分)%
2、残存量=干料配比×(100-烧损)%
3、焦粉残存=焦粉干料配比×(100-烧损)%
=焦粉干料配比×灰分
4、烧结矿残存率=(总残存量÷总干料量)×%
5、进入配合料中TFe=原料含铁量×干料配比
SiO2=原料SiO2含量×干料配比
CaO=原料CaO含量×干料配比
6、烧结矿碱度R的工业计算
R2=(CaO矿×矿石量+ CaO灰×灰石量) ÷(SiO2矿×矿石量+ SiO2灰×灰石量﹍+S(0.5-1.5))
7、配合料及烧结矿的化学成分
TFe料=各种物料带入TFe之和÷各种干原料之和
TFe矿=各种物料带入TFe之和÷总残存量
SiO2料=各种物料带入SiO2之和÷各种干原料之和
SiO2矿=各种物料带入SiO2之和÷总残存量
CaO料=各种物料带入CaO之和÷各种干原料之和
CaO矿=各种物料带入CaO之和÷总残存量
二、配用石灰石的计算公式(阿尔希波夫公式)
100×(k×a-b)/【k×(a-c)+(d-b)】=加入量%
K----规定的碱度
a----料中SiO2+AI2O3的含量(石灰石中的除外)b----料中CaO+MgO的含量(石灰石中的除外)
c----石灰石中SiO2+AI2O3的含量%
d----石灰石中CaO+MgO的含量%
三、燃料配用量和配比的计算公式
Q燃=C混×(Q配+Q返)-C返×Q返/C煤kg B燃=Q燃÷Q配%
式中:Q燃、Q配、Q返分别为燃料配用量、配料室总流量、返矿流量
C混、C返、C煤----分别为混合料固定碳、返矿残碳、煤粉固定碳%
B燃----为燃料配比%
四、白云石配加量(干)的简易计算公式
白云石配比=(MgO A- MgO A‵)%×A/(1-H2O白%) ×MgO白%
式中:MgO A----烧结矿要求的MgO A%
MgO A‵--未加白云石烧结矿的MgO A%
H2O白----白云石中含H2O%
五、已知高炉渣中MgO含量,求烧结矿MgO含量。
计算公式
MgO矿=A*MgO渣*Fe矿/ Fe铁
式中:MgO矿---烧结矿的MgO%
A---渣铁比一般为0.4--0.7
MgO渣---渣中MgO含量一般为6%--8%,最高不超2%
Fe铁---生铁中的含量一般为94%
Fe矿---烧结矿中的铁一般为50%--56%
六、烧成量(残存量)计算(各原料残存量之和)
∑残存量=∑干料量*(100-Ig-S*ŋs)
Ig---烧损%
Ŋs---烧结托流率%
S----原料含硫量
七、CaO与CaF2间的换算公式(Ca、O、F的原子量分别为40,16,19)
CaO与CaF2间的换算系数=CaO的分子量/ F2的分子量
=(40+16)/(19*2)=1.47
八、搭配返矿的计算公式
加(或减)石灰石配比=返矿配比*返矿有效CaO/灰石有效CaO 返矿配比=返矿皮带上的返矿量*(混矿皮带速度/皮带速度)/料批
加(或减)石灰石配比=返矿量*(混矿皮带速度/皮带速度*返矿有效CaO)/料批*石灰石有效CaO
九、生石灰置换成石灰石系数
生石灰有效CaO/石灰石有效CaO≈2.2
十、快速配料调整的计算公式
1、原料配比波动±1%、影响烧结矿T Fe的计算公式
△T Fe=[∑T Fe i外+(P i±1)T Fe i(1-W i)]/
[∑残存i外+(P i±1)(1-W i)(1-Ig i)]- T Fe0
式中:△T Fe----烧结矿T Fe波动值%
∑T Fe i外----除i种原料外各种矿粉带入铁量之和
P i------------i种原料湿配比%
T Fe i---------i种原料的含铁量%
W i------------i种原料的水分%
∑残存i外---除i种原料外各种原料的残存量之和%
Ig i-----i种原料的烧损%
T Fe o-----计算的烧结矿T Fe含量%
2、原料配比波动±1%、影响烧结矿碱度R的计算公式
△R2=[∑CaO i外+(P i±1)CaO i(1-W i)]/
[∑SiO2i外+(P i±1)SiO2i(1-W i)]- R0
式中:△R----烧结矿R波动值%
∑CaO i外、∑SiO2i外--除i种原料外各种原料带入CaO、SiO2之和P i------------i种原料湿配比%
CaO i、SiO2i ---------i种原料含CaO、SiO2量%
W i------------i种原料的水分%
R o-----计算的烧结矿R值
3、铁料含铁波动±1%、影响烧结矿T Fe的计算公式
△T Fe=[∑T Fe i外+P i((1-W i)(T Fe i±1)]/
[∑残存i外+P i(1-W i)(1-Ig i)]- T Fe0
式中:△T Fe----烧结矿T Fe波动值%
∑T Fe i外----除i种原料外各种矿粉带入铁量之和(干基)
P i------------i种原料湿配比%
T Fe i---------i种原料的含铁量%
W i------------i种原料的水分%
∑残存i外---除i种原料外各种原料的残存量之和%
Ig i-----i种原料的烧损%
T Fe o-----计算的烧结矿T Fe含量%
4、原料SiO2波动±1%、影响烧结矿碱度R的计算公式
△R2=∑CaO/ [∑SiO2i外+P i(SiO2±1)(1-W i)]- R0
式中:△R----烧结矿R波动值倍
∑CaO—各种原料含CaO之和(干基)%
∑SiO2i外---除i种原料外各种原料含SiO2之和(干基)%
P i------------i种原料湿配比%
SiO2i ---------i种原料含SiO2量%
W i------------i种原料的水分%
R o----------- 计算的烧结矿R值倍
5、原料CaO波动±1%、影响烧结矿碱度R的计算公式
△R= [∑CaO i外+P i(CaO i±1)(1-W i)]/ ∑SiO2- R0
式中:△R----烧结矿R波动值倍
∑SiO2—各种原料含SiO2之和(干基)%
∑CaO i外---除i种原料外各种原料含CaO之和(干基)%
P i------------i种原料湿配比%
CaO i---------i种原料CaO含量%
W i------------i种原料的水分%
R o----------- 计算的烧结矿R值
十一、用分析法计算含铁原料的公式。