烧结配料
烧结配料模型公式

2.配料2.1概述烧结配料是按烧结矿的质量指标要求和原料成分,将各种原料(含铁料、溶剂、燃料等)按一定的比例配合在一起的工艺过程,适宜的原料配比可以生产出数量足够的性能良好的液相,适宜的燃料用量可以获得强度高还原性好的烧结矿。
对配料的基本要求是准确。
即按照计算所确定的配比,连续稳定配料,把实际下料量的波动值控制在允许的范围内,不发生大的偏差。
实践表明,当配料发生偏差,会影响烧结过程的进行和烧结矿的质量。
生产中,当烧结机所需的上料量发生变化时,须按配比准确计算各种料在每米皮带或单位时间内的下料量;当料种或原料成分发生变化时,则应按规定要求,重新计算配比,并准确预计烧结矿的化学成分。
2.2配料方法——质量配料法此法是按原料的质量进行配料的一种方法。
其主要装置是皮带电子称——自动控制调节系统——调速圆盘给料机,配料时,每个料仓配料圆盘下的皮带电子称发出瞬时送料量信号,此信号输入调速圆盘自动调节系统,调节部分即根据给定值信号与电子皮带秤测量值信号的偏差,自动调节圆盘转速,达到所要求的给料量,质量配料系统如图1所示质量配料法可实现配料的自动化,便于电子计算机集中控制与管理,配料的动态精度可高达0.5%-1%,为稳定烧结作业和产品成分创造了良好条件,也是劳动条件得到改善。
2.3配料室(本厂)配料室采用单列布置,15个矿槽,混匀矿槽上采用移动B=1000卸料车向各配料槽给料;无烟煤、焦粉、冷返矿矿槽上采用B=650固定可逆胶带机向各配料槽给料。
生石灰用外设压缩空气将汽车罐车送来的生石灰送至配料槽。
混匀矿采用¢2500圆盘给料机排料,配料电子称称重;燃料和溶剂及冷返矿直接用配料电子称拖出;生石灰的排料、称量及消化通过叶轮给料机、电子称及消化器完成。
以上几种原料按设定比例经称量后给到混合料的B=800胶带机上。
料槽侧壁安装振动电机,防止料槽闭塞。
调速圆盘自动调节系统 给定值 控制量偏差 调节部分 调节量 操作部分(圆盘) 操作量控制部分 (圆盘给料机)检出部分 (电子皮带秤) 图1 质量配料系统2.3.1配料主要设备A圆盘给料机a特点:给料粒度范围大(0-50mm),给料均匀准确,调整容易、运转平稳可靠,管理方便。
烧结配料计算第五步

烧结配料计算第五步确定配比值一、查看预想成分和既定少烧结矿成分要求的相符程度。
查看烧结矿预想成分与既定的烧结矿各项指标是否匹配,全铁值应控制在在±0.5%之内,其他成分波动值在±0.2%之内,1、预想烧结矿全铁成分>既定成分0.5%以上,绝大部分的情况是因为预算时的烧成量过小引起的;预想烧结矿全铁成分<既定成分0.5%以上,绝大部分情况是因为计算时的烧成量过大引起的。
两种情况都需要重新计算各种物料的烧损值。
如果各种物料的烧损值没有问题,则需要重新用全量公式验算各种物料的全铁含量,尤其是铁矿粉的全铁含量。
2、预想烧结矿中二元碱度、氧化镁和三氧化二铝的含量应控制在既定成分的±0.2%之内。
如果不在此范围内应首先查找烧损原因,其次查找各种物料的这几种成分含量是否准确无误。
二、验算烧结矿预想成分全量是否在99-100%之间。
用烧结矿全量公式:全铁/0.7-0.11氧化亚铁+二氧化硅+氧化钙+氧化镁+三氧化二铝+0.5~1(残炭和杂质)=100验算烧结矿预想成分全量是否在99-100%之间。
1预想烧结矿全量<99%,说明一种或几种物料全量不足90%,需要检查后重新计算预想烧结矿成分。
2、预想烧结矿全量>100%,说明一种或几种物料全量超过100%或计算时有错误存在,必须重新检查物料全量及重新计算预想烧结矿成分。
三、检查烧结原料带入亚铁总量和既定烧结矿亚铁含量的比值高碱度原料带入亚铁总量是否为烧结矿亚铁含量的1.0-1.1倍。
原料带入的总亚铁量低于烧结矿的亚铁量,烧结焙烧过程总体就是还原反应;带入的总亚铁量高于烧结矿的亚铁量时,烧结的焙烧过程总体就是就是氧化反应。
而高碱度烧结矿的焙烧过程总体为弱氧化性是高碱度烧结矿的主要特性之一。
注:此三条都吻合时,就可基本确定计算烧结配比的准确性。
但是配比的优化程度还需要烧结过程的实际情况来检验。
所以计算出配比只是配料师工作完成的其中一部分,接下来还需要配料师到现场观测、指导烧结手法、修正烧结过程参数和优化配比。
项目三 烧结配料
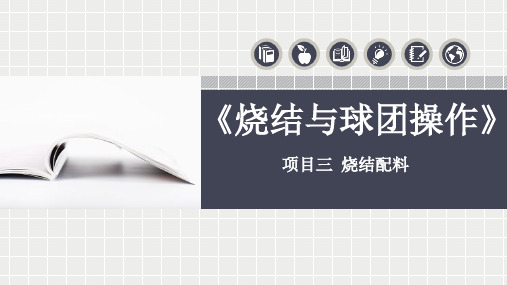
用熔剂、返矿粉等配料,但不适用水分含量较大的精矿粉;
1— 电 动 机 ;2— 减
直筒式套筒采用刮刀排料,堵料现象较蜗牛式套筒轻,但
速器;3—圆盘;4—
下料量波动大。故当精矿或粉矿用量较大时,宜用带活动
套筒;5—闸门
刮刀的套筒;当熔剂或燃料用量少,而且要求精确性高时,
宜用闸门式套筒。
相关知识
一、配料设备
设混合矿减重ax =0.084%×0.9+1.06%=1.14%;
石灰石减重a =42.25%;
炉尘减重a尘
=10.87%+0.102%×0.9=10.96%;
焦粉减重a焦 =80.9%+0.8%×0.9+2.17%=83.7%;
总减重a=Xax +Ya +8a尘 +8a焦 =0.0114X+0.4225Y+0.88+6.7=0.0114X+0.4225Y+7.58
偏大,因此,应根据干料量的变化来进行必要的调整。
4.同一品种原料下料量过大时,最好用两台给料机给料,可减少下料量的波动。
5.应十分注意下料量少的物料品种的下料量。由于影响下料量的因素较多,在人工操作
时要严格配料操作,班与班统一操作,要勤称量勤校正。铁料每15min校正一次,根据
具体情况规定各种下料量的波动范围。
掌握影响配料准确的因素,熟悉实际烧结矿成分与配料计算值发生偏差
的原因及调整措施。
任务
描述
配料操作是根据配料单准确配料,使用圆盘给料机给料,电子皮带秤称
量依次按配比加入混匀矿、返矿、熔剂、燃料等原料,通过皮带运输到烧结
混匀系统。配料必须按配料单准确配料,使配合料的化学成分合乎规定;配碳
烧结配料计算第三步

烧结配料计算第三步确立配料原则一、一次配料原则及补充说明一)一次配料的原则1、粒度混匀矿最佳的粒度组成应该是:0mm~3mm占20~40%;3mm~5mm占40~60%;5mm~8mm<15%;8mm以上<5%[2]。
2、水份混匀矿综合水份5~6.5%[3];结晶水≤3%[4]。
3、烧损混匀矿综合烧损控制在8~10%为宜。
(烧结配料的基本标准。
)4、氧化镁含量混匀矿中氧化镁含量一般应调至其三氧化二铝含量的 1.3~1.5倍,一般值为:2~3%。
这不仅关系到烧结矿的矿相组成,而且直接关系到高炉冶炼的顺行。
(烧结配料的基本标准。
)5、碱度混匀矿二元碱度一般控制在1.1~1.2[5]。
(烧结配料的基本标准。
)二)补充说明矿粉比例:铁矿粉的具体配入量需按混合料粒度组成、亚铁含量、矿相组成和成本的要求计算获得。
如果原料条件达不到最佳配比状态,可按粒度要求进行铁料搭配。
粒度:没有海沙、镍矿等特殊物料配入时可按此粒度组成进行配料。
水分:结晶水越少越好。
烧损:混匀矿烧损不越小烧结矿相对产量越高,一般情况下不低于5%。
氧化镁含量:这个比例不仅关系到四元碱度与二元碱度的匹配,而且在一定程度上决定烧结矿相组成的合理性。
碱度:在一定程度上决定烧结矿相组成的合理性。
配料计算:湿基值代入计算以确保配料的准确性,同时保证原料不亏库。
二、燃料配加要求固定碳、灰分、挥发分的要求焦粉:固定碳≥80%,灰分<18%;挥发分<1%;灰分:其中二氧化硅占60%左右,三氧化二铝占30%左右,其他占10%左右(焦粉全量拆分参照值)。
白煤(无烟煤):固定碳≥75%;灰分<25%;挥发分<1.5%;灰分:其中二氧化硅占60%,三氧化二铝占30%左右,其他占10%(白煤全量拆分参照值)。
粒度水分要求焦粉粒度:0-3mm≥75%;3mm-5mm≤20%;5mm-8mm<3%,焦粉水分<10。
白煤粒度:0-3mm≥65%;3mm-5mm≤30%;5mm-8mm<5%,白煤水分<10。
烧结矿的配料
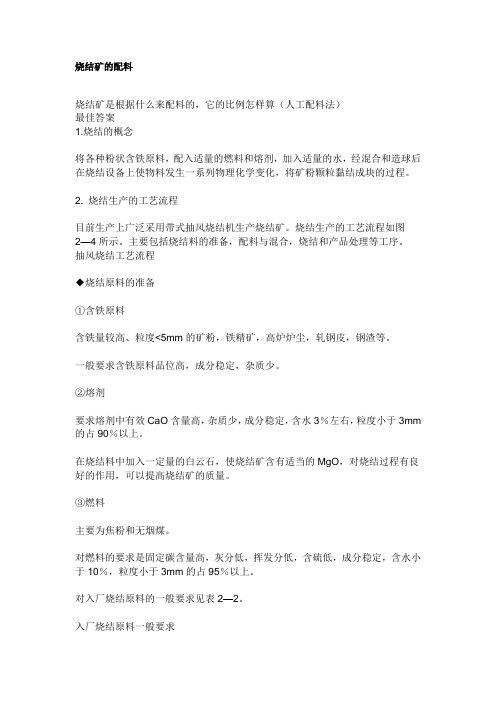
烧结矿的配料烧结矿是根据什么来配料的,它的比例怎样算(人工配料法)最佳答案1.烧结的概念将各种粉状含铁原料,配入适量的燃料和熔剂,加入适量的水,经混合和造球后在烧结设备上使物料发生一系列物理化学变化,将矿粉颗粒黏结成块的过程。
2. 烧结生产的工艺流程目前生产上广泛采用带式抽风烧结机生产烧结矿。
烧结生产的工艺流程如图2—4所示。
主要包括烧结料的准备,配料与混合,烧结和产品处理等工序。
抽风烧结工艺流程◆烧结原料的准备①含铁原料含铁量较高、粒度<5mm的矿粉,铁精矿,高炉炉尘,轧钢皮,钢渣等。
一般要求含铁原料品位高,成分稳定,杂质少。
②熔剂要求熔剂中有效CaO含量高,杂质少,成分稳定,含水3%左右,粒度小于3mm 的占90%以上。
在烧结料中加入一定量的白云石,使烧结矿含有适当的MgO,对烧结过程有良好的作用,可以提高烧结矿的质量。
③燃料主要为焦粉和无烟煤。
对燃料的要求是固定碳含量高,灰分低,挥发分低,含硫低,成分稳定,含水小于10%,粒度小于3mm的占95%以上。
对入厂烧结原料的一般要求见表2—2。
入厂烧结原料一般要求◆配料与混合①配料配料目的:获得化学成分和物理性质稳定的烧结矿,满足高炉冶炼的要求。
常用的配料方法:容积配料法和质量配料法。
容积配料法是基于物料堆积密度不变,原料的质量与体积成比例这一条件进行的。
准确性较差。
质量配料法是按原料的质量配料。
比容积法准确,便于实现自动化。
②混合混合目的:使烧结料的成分均匀,水分合适,易于造球,从而获得粒度组成良好的烧结混合料,以保证烧结矿的质量和提高产量。
混合作业:加水润湿、混匀和造球。
根据原料性质不同,可采用一次混合或二次混合两种流程。
一次混合的目的:润湿与混匀,当加热返矿时还可使物料预热。
二次混合的目的:继续混匀,造球,以改善烧结料层透气性。
用粒度10~Omm的富矿粉烧结时,因其粒度已经达到造球需要,采用一次混合,混合时间约50s。
使用细磨精矿粉烧结时,因粒度过细,料层透气性差,为改善透气性,必须在混合过程中造球,所以采用二次混合,混合时间一般不少于2.5~3min。
简述烧结配料方法

简述烧结配料方法
烧结配料方法是指将粉状或颗粒状原料进行配料混合,并通过一定的工艺和设备进行烧结成型的过程。
烧结配料方法主要包括以下几个步骤:
1. 原料准备:将所需的原料按照一定比例进行准备,这些原料包括粉状或颗粒状的金属粉末、粘结剂、助熔剂等。
2. 配料混合:将所准备的原料添加到混合机中进行混合,确保各种原料能够均匀分布,以保证成品的均匀性和稳定性。
3. 来料检测:对混合好的配料进行化学成分、粒度分布、流动性等方面的检测,以确保配料的质量和稳定性。
4. 烧结过程:将混合好的配料装填入烧结装置,通过一定的温度和压力条件下进行烧结成型。
在烧结过程中,粘结剂和助熔剂将起到使原料颗粒粘结在一起,并形成所需形状和结构的作用。
5. 冷却处理:烧结完成后,需要对成品进行冷却处理,使其达到适宜的温度后进行取出,以保证成品的质量和稳定性。
烧结配料方法广泛应用于金属材料、陶瓷材料、高温合金、复合材料等行业和领域,是一种重要的制造工艺。
这种方法可通过调节原料配比、烧结温度等参数,实现对产品的性能、形状和结构的控制和调整。
烧结配料计算实战案例解析一
烧结配料计算实战案例解析一一步步讲解配比计算的思路与具体方法步骤,希望大家能有举一反三的能力,尽快把实战案例中的配料方法应用到日常工作中去。
一、原料成分分析原料成分时首先观察和分辨各种原料名称、化学组成、物理结构和冶金性能。
如果遇到不认识的原料应及时弄清楚物料性质、查询产地、分析化学成分、判断其所有性能及应用方法。
对于铁料的不同叫法也应有一定的了解,不应在叫法不同时产生对物料的误判断。
其次对于各种物料成分的观察应有侧重点,铁料重点是全铁、二氧化硅和烧损(铁矿粉的烧损由结晶水的析出和氧化还原反应两部分组成,其中化验的烧损为结晶水烧损,两部分的量均可用全量公式求得);熔剂重点是二氧化硅、氧化钙、氧化镁和烧损(熔剂的烧损由结晶水的析出和碳酸盐分解两部分组成,化验烧损为两部分之和。
碳酸盐分解由化学方程式带入分子量求得,烧损剩余部分为结晶水);燃料的重点是烧损、二氧化硅和三氧化二铝。
(燃料的烧损由碳的气化、结晶水的析出和挥发分三部分组成,化验烧损一般为三项之和。
焦粉一般不含结晶水,挥发分含量也很少);辅料应全面分析(辅料的烧损由炭的气化、结晶水的析出两部分组成,化验烧损为两部分之和)。
二、上级下达或炼铁需要指标每个公司、厂矿下达的烧结矿指标都不尽相同,各有侧重点。
作为配料技师来讲,应把烧结矿的所有物化指标都优化到极致作为工作目标。
所以在完成既定指标和任务的同时也应以不断提升烧结矿其他性能为职责,尤其烧结矿对高炉冶炼过程影响的控制应作为配料技师工作的重中之重。
三、步骤第一步估算烧结矿预想成分首先根据优先定硅原则和现场物料状况预算烧结矿成分范围值。
然后预测的范围值根据炼铁部的要求,运用全量公式,进一步缩小范围。
经过一定验算经验和现场生产经验的积累就可以达到把烧结矿的预想成分确定在很小的范围。
第二步校准化验成分校准化验成分时的注意事项1、由于物料中的微量元素无法全部测量,所以一般情况下全量值不会超过100%。
2、全量验算出现偏差较大时,必须根据现场具体情况找出原因,判断准确后进行校准。
烧结配料个人工作总结
烧结配料个人工作总结烧结配料是炼钢过程中非常重要的一环,它直接关系到炼钢产品的质量和成本。
作为烧结配料部门的一名员工,我经过一段时间的工作,现在对自己的工作进行总结如下:首先,我在工作中时刻保持着高度的责任感和紧迫感,严格按照工艺要求和生产计划,做好烧结配料的准备工作。
在原料的选择上,我始终遵循经济、环保和质量相结合的原则,不断寻求更好的原料选择和配比方案,以降低生产成本,提高产品质量。
其次,我在工作中注重团队合作,积极与其他部门进行沟通与协调。
特别是在生产过程中出现问题时,我会主动与烧结工艺、设备维护等部门进行沟通,共同解决问题,确保生产顺利进行。
同时,我也会和采购部门保持密切联系,及时了解原料市场变化,确保原料供应充足稳定。
另外,我也不断学习和提升自己的专业知识和技能,关注行业动态和新技术,努力将先进的科学技术用于烧结配料生产中,提高生产效率和产品质量。
总的来说,我在烧结配料部门的工作中不断努力,始终保持着高度的责任感和团队合作精神,不断提升自身的专业知识和技能,为企业的发展做出了积极的贡献。
同时,我也清楚的意识到自己在工作中还有许多不足之处,会继续努力充实自己,为企业的发展做出更大的贡献。
烧结配料的工作总结:在烧结配料部门的工作中,我不仅仅是一个执行者,更是一个思考者和决策者。
我时刻关注着整个烧结配料生产过程中的各个环节,努力寻求各种改进和优化的途径,以提高生产效率和产品质量。
首先,我对原料的质量和供应情况进行了深入的了解和研究。
我与供应商保持密切的合作关系,了解原料市场的动态,以及原料的质量和价格变化情况。
通过与供应商深入交流,我不仅学到了更多的原料知识,也为企业节约了采购成本,确保了原料的供应和质量。
其次,我积极参与生产工艺的改进和优化工作。
我和烧结工艺师、设备维护人员共同讨论,寻求各种可以优化和提高生产效率的方案。
我们不断尝试新的工艺和设备,以及调整烧结配料的配比方案,以提高产品的均匀度和结晶度,确保产品质量。
烧结配料计算方法及公式
烧结配料计算方法及公式
以下是一个烧结时使用钢铁厂原料进行配料计算的例子:
1.确定所需烧结矿中每种元素的含量要求,如Fe、SiO2、Al2O3、CaO、MgO等。
2.根据矿石的化学成分及质量,计算出每种原料中所含的各个元素的
质量。
例如,铁矿石中的Fe含量为60%,则铁矿石中Fe的质量为铁矿石
的质量乘以0.6
3. 计算出各个原料的配料量。
根据质量平衡,可以得到配料方程组,通过求解方程组,可以计算出每种原料的配料量。
例如,假设需要配
1000kg的烧结矿,通过方程组求解可以得到铁矿石的配料量为500kg。
4.检查配料计算结果的准确性。
计算得到的配料量应符合质量平衡和
材料平衡的要求,各种元素的含量也应符合烧结矿的要求。
需要注意的是,烧结配料计算中的公式和方法可以根据具体情况进行
适当的调整和改变。
不同的烧结工艺和原料要求会对配料计算的方法和公
式产生影响。
总结起来,烧结配料计算是通过质量平衡和材料平衡方法,根据烧结
矿的要求,计算出每种原料的配料量。
配料计算的准确性对于确保烧结过
程中原料的合理利用及烧结矿的质量稳定具有重要作用。
烧结配料专业知识
烧结配料专业知识
烧结是一种重要的冶金工艺,通过将粉状或颗粒状原料在高温
下烧结成块状,形成强度较高的烧结矿。
烧结配料的选择和搭配对
烧结过程和烧结品质具有重要影响。
以下是烧结配料的一些专业知识。
初烧配料
初烧配料是指矿石和焦炭等原料。
高品位的矿石通常具有较高
的烧结活性和烧结强度,对于提高烧结矿的质量至关重要。
焦炭作
为还原剂和燃料,有助于提供高温条件并促进烧结反应的进行。
配矿比例
配矿比例是指各种原料在烧结过程中所占的比重。
合理的配矿
比例能够达到均衡的化学组成和物理性能,从而提高烧结矿的质量。
配矿比例应根据不同矿石的质量、含量和烧结性能进行调整。
黏结剂
黏结剂是为了提高烧结矿的结合力和强度而添加的物质。
常用的黏结剂包括焦炭灰、煤焦油和助剂等。
黏结剂的种类和添加量应根据矿石的性质和烧结目标来确定。
硅酸盐
硅酸盐是烧结过程中常见的添加剂,能够提高烧结矿的冷热强度和耐久性。
常用的硅酸盐包括石灰石和硅石等。
硅酸盐的添加量应根据矿石的含量和质量进行调整,以避免对烧结过程产生负面影响。
燃料选择
烧结过程中需要提供足够的热能来保持高温条件。
为了满足这一需求,可以选择高热值的燃料,如焦炭、煤粉等。
燃料选择应综合考虑价格、可获得性和热值等因素。
以上是烧结配料的一些专业知识。
在实际生产中,需要根据矿石的质量和特性以及生产要求来调整烧结配料的选择和搭配,以达到提高烧结矿质量和生产效益的目标。
- 1、下载文档前请自行甄别文档内容的完整性,平台不提供额外的编辑、内容补充、找答案等附加服务。
- 2、"仅部分预览"的文档,不可在线预览部分如存在完整性等问题,可反馈申请退款(可完整预览的文档不适用该条件!)。
- 3、如文档侵犯您的权益,请联系客服反馈,我们会尽快为您处理(人工客服工作时间:9:00-18:30)。
2.配料2.1概述烧结配料是按烧结矿的质量指标要求和原料成分,将各种原料(含铁料、溶剂、燃料等)按一定的比例配合在一起的工艺过程,适宜的原料配比可以生产出数量足够的性能良好的液相,适宜的燃料用量可以获得强度高还原性好的烧结矿。
对配料的基本要求是准确。
即按照计算所确定的配比,连续稳定配料,把实际下料量的波动值控制在允许的范围内,不发生大的偏差。
实践表明,当配料发生偏差,会影响烧结过程的进行和烧结矿的质量。
生产中,当烧结机所需的上料量发生变化时,须按配比准确计算各种料在每米皮带或单位时间内的下料量;当料种或原料成分发生变化时,则应按规定要求,重新计算配比,并准确预计烧结矿的化学成分。
2.2配料方法——质量配料法此法是按原料的质量进行配料的一种方法。
其主要装置是皮带电子称——自动控制调节系统——调速圆盘给料机,配料时,每个料仓配料圆盘下的皮带电子称发出瞬时送料量信号,此信号输入调速圆盘自动调节系统,调节部分即根据给定值信号与电子皮带秤测量值信号的偏差,自动调节圆盘转速,达到所要求的给料量,质量配料系统如图1所示质量配料法可实现配料的自动化,便于电子计算机集中控制与管理,配料的动态精度可高达0.5%-1%,为稳定烧结作业和产品成分创造了良好条件,也是劳动条件得到改善。
2.3配料室(本厂)配料室采用单列布置,15个矿槽,混匀矿槽上采用移动B=1000卸料车向各配料槽给料;无烟煤、焦粉、冷返矿矿槽上采用B=650固定可逆胶带机向各配料槽给料。
生石灰用外设压缩空气将汽车罐车送来的生石灰送至配料槽。
混匀矿采用¢2500圆盘给料机排料,配料电子称称重;燃料和溶剂及冷返矿直接用配料电子称拖出;生石灰的排料、称量及消化通过叶轮给料机、电子称及消化器完成。
以上几种原料按设定比例经称量后给到混合料的B=800胶带机上。
料槽侧壁安装振动电机,防止料槽闭塞。
调速圆盘自动调节系统 给定值 控制量偏差 调节部分 调节量 操作部分(圆盘) 操作量控制部分 (圆盘给料机)检出部分 (电子皮带秤) 图1 质量配料系统2.3.1配料主要设备A圆盘给料机a特点:给料粒度范围大(0-50mm),给料均匀准确,调整容易、运转平稳可靠,管理方便。
b圆盘给料机的结构它由传动机构、圆盘、套筒和调节排料量的闸门或刮刀组成。
电动机经联轴节通过减速机来带动圆盘。
圆盘转动时,料仓内的物料随着圆盘一起移动,并向出料口的一方移动,经闸门或刮刀排出物料。
排出量的大小可用刮刀装置或闸门来调节。
C圆盘给料机给料量波动的原因(1)圆盘和料槽不同心。
(2)盘面不水平。
(3)盘面衬极磨损程度不同。
(4)原料水分变化(5)物料粒度变化。
(6)矿槽内料位变化。
料位一般60%-80%。
B电子皮带秤a特点电子皮带秤用于皮带运输机输送固定散粒性物料的计量上,可直接指示皮带运输机的瞬时送料量,也可累计某段时间内的物料总量,与自动调节口配合还可进行输料量的自动调节,实现定量自动给料。
B结构电子皮带秤由称框、传感器、测速头及仪表组成。
称框用以决定物料的有效称量,传感器用以测量重量并转换成电量信号输出,测量头用以测量皮带轮传动速度并转换成频率信号,仪表由测速、放大、显示、积分、分频、计数、电源等单元组成,用以对物料重量进行直接显示及总量的累计,并输出物料重量的电流信号作调节口的输入信号。
2.3.2配料矿仓贮存能力配料矿仓贮存力表物料名称单仓有效容积(m3)矿仓数量(个)物料质量(t) 储存时间(h)混合料 115 5 1260 7.7生石灰 83 2 182 36石灰石 90 2 484 15燃料 90 2 180 14内返矿 90 2 322 5.3高炉返矿 130 1 234 10.5除尘灰 83 1 166 332.4配料操作与配料调整加强配料操作,及时地进行配料和给料量的调整,可以稳定生产,减少误差,使产品质量满足规定要求。
2.4.1配料工艺技术操作要点即使配料计算准确无误,如果没有精心操作,烧结矿的化学成分也难以保证。
生产上,配料工艺操作要点如下:(1)正常操作1)严格按配料单准确配料,圆盘给料机闸门开口度要适度,闸门开口的高度要保持稳定,保持下料稳定,下料量允许波动范围铁矿粉小于±0.3kg/m,溶剂与燃料小于±0.2kg/m,其他原料小于±0.1kg/m,使配合料的化学成分合乎规定标准。
2)配碳量要达到最佳值,保证烧结燃耗低,烧结矿中FeO含量低。
3)密切注意各种原料的配比量,发现短缺等异常情况时应及时查明原因并处理。
4)在成分、水分波动较大时,根据实际情况短时间作出调整。
5)同一种原料的配料仓必须轮流使用,以防堵料、水分波动等现象发生。
6)做好上料情况与变料情况的原始记录。
(2)异常操作1)在电子称不准确、误差超过规定范围时,可采用人工跑盘称料,增加称料频次。
2)在微机不能自动控制时,应采用手动操作。
3)当出现紧急情况,采用应急操作后,要马上通知有关部门立即处理。
应急操作不可长时间使用,岗位工人应该做好记录,在交接班时要核算出各种物料的使用量、参数,并计入原始记录。
2.4.2配料操作的注意事项(1)随时检查下料量是否符合要求,根据原料粒度、水分及时调查。
(2)运转中随时注意圆盘料槽的粘料、卡料情况,保障下料畅通、均匀。
(3)及时向备料组反映各种原料的水分、粒度杂物等的变化。
(4)运转中应经常注意设备声音,如有不正常音响及时停机检查、处理。
(5)注意电机轴承温度,不得超过55℃。
(6)圆盘在运转中突然停止,应详细检查,确无问题或故障排除后,方可重新启动,如再次启动不了,不得继续启动,应查出原因后进行处理。
2.4.3配料调整应注意的问题(1)滞后现象:配料比或给料量调整后有滞后现象,取样时要做到第二、第三个样才能反映出来。
例如烧结矿要求TFe=(50±1)%,第一次的化验样TR=49.2%,偏低。
调整时有两种措施,一是把配料的计算铁调至50%,当第二次的化验铁升高至49.5%时,说明铁品位已调至正常。
第二种措施是把配料的计算铁调至50.8%,但时间要严格控制在从配料到成品烧成的时间的2/3,随后就恢复到按铁50%的计算进行正常操作。
(2)兼顾其他成分的变化:调整铁分时,要注意R等的变化。
如铁分正常,碱度低时,调整时除增加石灰石用量外,还要适当调高铁分,又如烧结矿的碱度和铁分偏高时,可以用低铁原料置换高铁原料。
因为低铁原料的SiO2含量高,故可以不增加或少增加溶剂的用量。
(3)除尘器放灰的影响:除尘器收集的灰土,一般都直接卸到混合料皮带上,作为烧结原料。
这些灰含SiO2较高,CaO较低,因此放灰时,必然会使烧结矿碱度降低。
应适当增加熔剂配比。
2.5配料计算配料计算是为了掌握烧结矿含铁品位及化学成分提供需要处理的物料量,计算矿仓容积及确定运输系统能力。
2.5.1 配料计算的一般项目及公式A 烧结矿碱度烧结矿碱度一般只计算二元碱度,即R=CaO/SiO2式中R—烧结矿碱度,可由炼铁厂与烧结厂商定;CaO,SiO2——烧结矿中氧化钙,二氧化硅含量,%。
碱度设定后,通过下式计算原、燃料的配用量。
R=( CaO矿x+ CaO熔y+ CaO燃z)/ (SiO2矿x+ SiO2熔y+ SiO2燃z)x+y+z=1000,kg式中,x——1t混合料中铁精矿(粉矿)的用量,kgy——1t混合料中熔剂的用量,kgz——1t混合料中燃料的用量,kgCaO矿——铁精矿(粉矿)中CaO含量SiO2矿——铁精矿(粉矿)中SiO2含量CaO熔——熔剂中的CaO含量SiO2熔——熔剂中的SiO2含量CaO燃——燃料中的CaO含量SiO2燃——燃料中的SiO2含量B 燃料用量燃料用量可用三种不同基准进行计算。
(1)以单位铁原料为计算基准Q燃=q燃∑Q铁式中Q燃——燃料用量,t;q燃——每吨铁原料(干料)的燃料用量,可按7%~9%或通过试验确定∑Q铁——各种含铁原料的用量之和,t(2)以单位混合料为计算基准Q燃=q1燃Q混q1燃=C/C1式中q1燃——每吨混合料中燃料的用量,%Q燃——燃料用量,t;Q混——混合料量,t;C——混合料中固定碳的含量,一般C=3%~5%;C1——燃料中固定碳的含量,%(3)以单位烧结矿为计算基准Q燃=q2燃Q烧式中Q燃——燃料用量,t;Q烧——烧结矿的产量,t;q2燃——每吨烧结矿燃料用量,一般为烧结矿的5.5%~8%以上三种方法可根据实际情况任选一种,其中q燃q1燃q2燃都需要通过烧结试验或参照类似烧结厂的实际数据来确定,一般厚料层烧结时其值较低。
C 熔剂用量熔剂用量用下式计算:Q熔=∑Q原CaO1原/CaO1熔CaO1熔=CaO熔-RSiO2熔CaO1原= RSiO2原-CaO原式中Q熔——熔剂用量,t;Q原——某种原料的用量,t;SiO2原CaO原——某种原料中二氧化硅和氧化钙的含量,%CaO1原——为获得烧结矿碱度为R,某种原料的单位原料量所需氧化钙含量,%CaO1熔——熔剂中氧化钙的有效含量,%D 混合料量混合料用量用下式计算Q混=∑Q/(1-q水–q返)式中Q混——混合料用量,t;q水——混合料的含水量,%;q返——混合料中返矿比例Q——各种铁原料,熔剂和燃料的用量,t;q水,q返一般根据试验或类似烧结厂的经验数据预先确定。
E 返矿量返矿量按下式计算:Q返=Qq返式中Q返=循环量,t。
根据实际生产测定,每吨烧结矿产生返矿量400~600kg,一般取500kg,冷热返矿的比例一般为热:冷=40:60F 混合料用水量混合料用水量用下式计算:Q 水=Q 混q 水- ∑(Qq/1-q)式中Q ——各种含铁原料、熔剂和燃料的用量,t ;q ——相应的某种原料的含水量,%Q 水——混合料的用水量(未考虑水分的蒸发量),t ;Q 混——混合料用量,t ; q 水——每吨混合料的用水量,t 。
G 烧结矿产量烧结矿产量计算方法有 两种:一种简易法,不考虑在烧结过程中氧化亚铁的变化;另一种是考虑烧结过程中氧化亚铁引起的变化。
计算方法如下:不考虑烧结过程中氧化亚铁的变化引起的氧的增减时,按下式计算:Q 烧=∑Q (1−Ig −0.9S )式中 Q 烧——烧结矿产量,t ;Q ——各种含铁原料、熔剂及燃料的用量,t ;Ig ——相应的各种含铁原料、熔剂及燃料的烧损率,%;S ——相应的各种含铁原料、熔剂及燃料的含硫量,%;0.9——烧结脱硫率(一般按85%−90%计,指硫化物0)。
考虑烧结过程中氧化亚铁数量的变化引起氧的增减时,按下式计算: ∑Q [9(1−Ig −0.9s )+FeO]式中, FeO ——相应的各种铁原料、熔剂以及燃料中氧化亚铁的含量,%; FeO 烧——烧结矿中(根据试验或假定)氧化亚铁的平均含量,%。