注塑模具设计方法
注塑模具设计步骤

注塑模具设计步骤注塑模具的设计须按照以下几个步骤进行:(1)塑件分析1.明确塑件设计要求仔细阅读塑件制品零件图,从制品的塑料品种,塑件形状,尺寸精度,表面粗糙度等各方面考虑注塑成型工艺的可行性和经济性,必要时,要与产品设计者探讨塑件的材料种类与结构修改的可能性。
2.明确塑件的生产批量小批量生产时,为降低成本,模具尽可能简单;在大批量生产时,应保证塑件质量前提条件下,尽量采用一模多腔或高速自动化生产,以缩短生产周期,提高生产率,因此对模具的推出机构,塑件和流道凝料的自动脱模机构提出严格要求。
3.计算塑件的体积和质量计算塑件的体积和质量是为了选用注塑机,提高设备利用率,确定模具型腔数。
(2)注塑机选用根据塑件的体积或重量大致确定模具的结构,初步确定注塑机型号,了解所使用的注塑机与设计模具有关的技术参数,如:注塑机定位圈的直径,喷嘴前端孔径及球面半径,注塑机最大注塑量,锁模力,注塑压力,固定模板和移动模板面积大小及安装螺孔位置,注塑机拉杆的间距,闭合厚度,开模行程,顶出行程等。
(3)模具设计的有关计算1.凹,凸模零件工作尺寸的计算;2.型腔壁厚,底板厚度的确定;3.模具加热,冷却系统的确定。
(4)模具结构设计1.塑件成型位置及分型面选择;2.模具型腔数的确定,型腔的排列和流道布局以及浇口位置设置;3.模具工作零件的结构设计;4.侧分型与抽芯机构的设计;5.顶出机构设计;6.拉料杆的形式选择;7.排气方式设计。
(5)模具总体尺寸的确定,选购模架模架已逐渐标准化,根据生产厂家提供的模架图册,选定模架,在以上模具零部件设计基础上初步绘出模具的完整结构图。
(6)注塑机参数的校核1.最大注塑量的校核;2.注塑压力的校核;3.锁模力的校核;4.模具与注塑机安装部分相关尺寸校核,包括闭合高度,开模行程,模座安装尺寸等几方面的相关尺寸校核。
(7)模具结构总装图和零件工作图的绘制模具总图绘制必须符合机械制图国家标准,其画法与一般机械图画法原则上没有区别,只是为了更清楚地表达模具中成型制品的形状,浇口位置的设置,在模具总图的俯视图上,可将定模拿掉,而只画动模部分的俯视图。
注塑模具设计
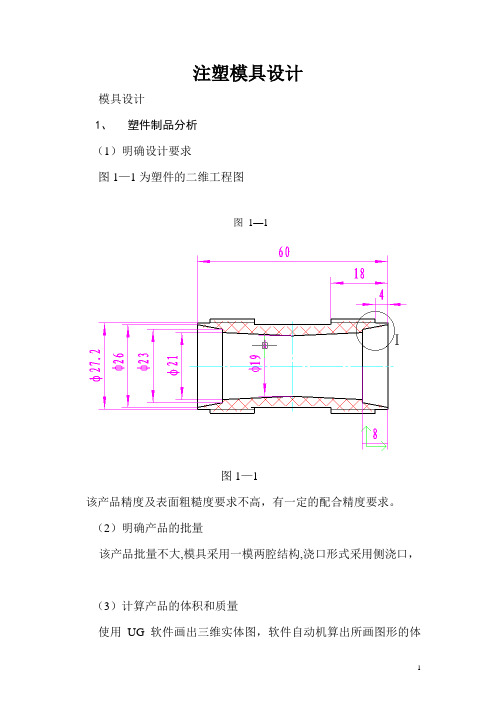
注塑模具设计模具设计1、塑件制品分析(1)明确设计要求图1—1为塑件的二维工程图图1—1图1—1该产品精度及表面粗糙度要求不高,有一定的配合精度要求。
(2)明确产品的批量该产品批量不大,模具采用一模两腔结构,浇口形式采用侧浇口,(3)计算产品的体积和质量使用UG软件画出三维实体图,软件自动机算出所画图形的体积。
通过计算得塑件的体积V塑=13.85cm3塑件的质量M塑=ρV塑=1.04×13.85=14.4g式中ρ---塑料的密度,g/cm3.流道凝料的质量m2还是个未知数,可按塑件质量的0.6倍来估算。
浇注系统的质量M浇=ρV浇=8.6g浇注系统的体积V浇=8.30cm3.故V总= 2×V塑+V浇= 2×13.85cm3 +8.30cm3.= 36cm3 M总=2×M塑+M浇=2×14.4g+8.6g= 43g2.注塑机的确定选择注射机型号 XS—ZY—250主要技术规格如下:螺杆直径:65mm注射容量:250cm3注射压力:1300MPa锁模力:1800kN最大注射面积:500cm3模具厚度:最大350mm最小250mm模板行程:350mm喷嘴:球半径 18mm孔直径4m定位孔直径:125mm顶出:两侧孔径 40mm两侧孔距 280mm3.浇注系统的设计(1)主流道形式浇注系统是指模具从接触注射机喷嘴开始到型腔未知的塑料流动通道,起作用是使塑料熔体平稳且有顺序的填充到型腔中,并在填充和凝固过程中把注射压力充分传递到各个部位,已获得组织机密、外形清晰地塑件。
浇注系统可分为普通浇注系统和无流道凝料系统。
考虑浇注系统设计的基本原则:适应塑料的成型工艺性、利于型腔内气体的排出、尽量减少塑料熔体的热量和压力损失、避免熔料直冲细小型芯、便于修正和不影响塑件外观质量、便于减少塑料损失和减小模具尺寸等。
根据模具主流道与喷嘴的关系: R 2= R 1+(1~2)㎜ D=d+(0.5~1)㎜. 取主流道球面半径R=20㎜, 取主流道小端直径D =Φ5㎜, 球面配合高度h=3-5mm 取h=4 mm主流道长度 有标准模架结合该模具的结构,取L=85mm为了便于将凝料从主流道中拔出,将主流道设计成圆锥形,其斜度为1°~3°d—喷嘴直径 1~5.00+=d d 40=d 5=d2o=α R=10(2)分流道的设计分流道在多型腔模具中是必不可少的,它起连接主浇道和浇口的作用。
注塑模具设计步骤(经典)

设计者:农文生
步骤2
【1】设计区域(之 后修补零件再分型)
【2】创建曲面补片 【3】编辑分型线段 【4】创建分型面 【5】创建型芯、型 腔 【6】型腔布局
步骤3
设计者:农文生
创建定位圈、 浇口套、流道 等
步骤4
说明:由于本塑造成品存在倒扣 现象故应设计滑块和斜顶机构
【滑块与顶料装置】
1创建滑块 2创建斜顶
设计者:农文生
பைடு நூலகம்
步骤5
【标准件管理】【顶杆】
1创建顶出系统
【冷却】
2创建冷却系统
(水嘴、冷却道、喉塞等)
设计者:农文生
整体效果 及 学习心得
细心+耐心+独 立思考+合作
设计者:农文生
谢
呼~呼、、完成任务、爬上去、嘻嘻!
谢 欣 赏
设计者:农文生
注射模具设计流程介绍
1总体设计思路分享 2基本设计步骤介绍 3整体效果及学习心得
设计者:农文生
总体设计思路分享
首先分析零件结构、分型、创建型芯型 腔,接着调用LKM-SG模架,然后创建定位 圈、浇口套、滑块、斜顶机构、顶出系统、 冷却系统等
设计者:农文生
基本设计步骤1
• 项目初始化、工件 • 在【注射模向导】工具条 中单击【项目初始化】按 钮,打开部件文件设置参 数及选项;调整WCS坐标 系,设计模具坐标 • 在【注射模向导】工具条 中单击【工件】在弹出的 【工件尺寸】对话框中设 置工件的参数及选项
注塑模具的设计及制造

注塑模具的设计及制造注塑模具是用于注塑成型的模具,它的设计和制造直接关系到产品质量和生产效率。
本文将从设计和制造两个方面介绍注塑模具的相关知识。
一、注塑模具的设计1.产品设计分析:在进行注塑模具设计之前,首先要对即将生产的产品进行分析。
了解产品的形态尺寸、材料特性、注塑工艺和生产要求等,为模具设计提供依据。
2.模具结构设计:根据产品要求和注塑工艺,设计模具的结构。
包括模具的开合方式、定位方式、注塑道设计和冷却系统设计等。
合理的结构设计可以提高模具使用寿命和生产效率。
3.模具零件设计:根据模具结构设计,对各个零件进行详细设计。
比如模具芯、模具腔、滑块、顶出机构、定位销和定位套等。
零件设计要考虑到材料选择、加工工艺和装配要求等。
4.模具标准件选用:在模具设计过程中,可以选用一些标准件,如模具基础板、导向套和注塑嘴等。
合理选用标准件不仅可以减少设计工作量,还可以提高模具加工精度和降低成本。
5.注塑模具的通气设计:在注塑过程中,模具内会产生大量的气体,如果不能有效排出,会导致产品缺陷。
所以,在模具设计中要合理设置通气孔和排气槽,以确保注塑过程的质量。
二、注塑模具的制造1.模具材料选择:注塑模具常用的材料有优质合金钢和工具钢,比如P20、718、2738等。
材料的选择要根据产品要求、生产批量和制造成本等因素综合考虑。
2.模具加工工艺:注塑模具的加工工艺包括铣削、镗削、磨削、电火花和线切割等。
不同的加工工艺需要选用不同的设备和工装,操作人员要熟悉模具加工过程和技术要求。
3.模具热处理:模具在使用过程中需要经过热处理,以提高材料的硬度和耐磨性。
常见的热处理方法有淬火、回火和表面处理等,要根据模具材料和要求选择适当的热处理方法。
4.模具组装和调试:在模具制造完成后,需要对各个零部件进行组装和调试。
确保模具各部件的精度和配合度,在注塑生产前进行试模和修正,以保证产品质量。
总之,注塑模具的设计和制造对于提高注塑产品的质量和生产效率至关重要。
注塑模具设计操作流程
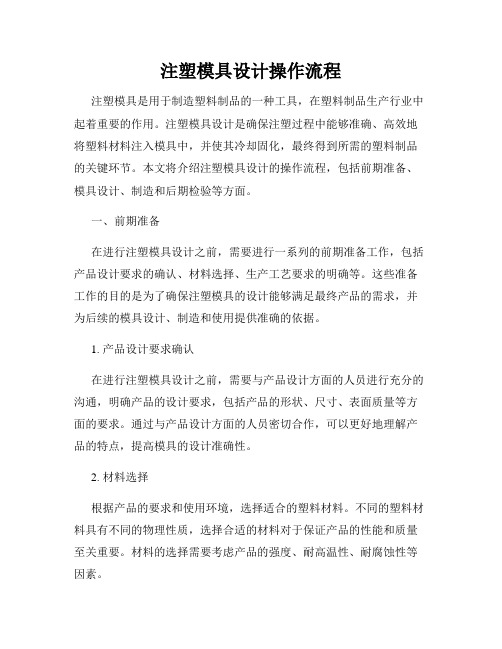
注塑模具设计操作流程注塑模具是用于制造塑料制品的一种工具,在塑料制品生产行业中起着重要的作用。
注塑模具设计是确保注塑过程中能够准确、高效地将塑料材料注入模具中,并使其冷却固化,最终得到所需的塑料制品的关键环节。
本文将介绍注塑模具设计的操作流程,包括前期准备、模具设计、制造和后期检验等方面。
一、前期准备在进行注塑模具设计之前,需要进行一系列的前期准备工作,包括产品设计要求的确认、材料选择、生产工艺要求的明确等。
这些准备工作的目的是为了确保注塑模具的设计能够满足最终产品的需求,并为后续的模具设计、制造和使用提供准确的依据。
1. 产品设计要求确认在进行注塑模具设计之前,需要与产品设计方面的人员进行充分的沟通,明确产品的设计要求,包括产品的形状、尺寸、表面质量等方面的要求。
通过与产品设计方面的人员密切合作,可以更好地理解产品的特点,提高模具的设计准确性。
2. 材料选择根据产品的要求和使用环境,选择适合的塑料材料。
不同的塑料材料具有不同的物理性质,选择合适的材料对于保证产品的性能和质量至关重要。
材料的选择需要考虑产品的强度、耐高温性、耐腐蚀性等因素。
3. 生产工艺要求明确在确定了产品的设计要求和材料选择之后,需要明确生产工艺要求。
生产工艺要求涉及到注塑过程中的各个环节,包括注塑机的选择、注塑温度的控制、注塑时间的控制等。
明确生产工艺要求可以帮助设计师更好地进行模具的设计。
二、模具设计模具设计是注塑模具设计操作流程中的核心环节,包括模具结构设计和模腔设计。
1. 模具结构设计模具结构设计是根据产品的形状和要求,确定模具的结构,包括模具的分模方式、模具的开合方式、配件的布置等。
模具结构设计需要考虑到产品的复杂性、生产效率等因素,确保模具能够满足生产需求。
2. 模腔设计模腔设计是模具设计的关键环节之一,是根据产品的形状和尺寸来确定模腔的形状和尺寸。
模腔的设计需要考虑到产品的收缩率、表面质量等因素,通过合理的模腔设计可以提高产品的成型质量。
什么是DFM注塑模具的设计DFM要点(一)2024

什么是DFM注塑模具的设计DFM要点(一)引言概述:DFM(Design for Manufacturing)是一种注塑模具设计的方法,旨在提高生产效率、降低成本、提升产品质量。
本文将围绕DFM注塑模具设计的要点展开探讨,帮助读者更好地理解和应用DFM设计原则。
正文内容:一、材料选择1. 根据产品特性选择合适的材料,考虑其熔融温度、流动性、收缩率等因素。
2. 增加材料的可再生性和可回收性,符合环保和可持续发展的要求。
3. 考虑材料的成本和可供应性,避免因材料不稳定导致生产问题。
二、模具结构设计1. 合理设计模具的冷却系统,确保产品快速冷却,提高生产效率。
2. 避免模具过于复杂,减少制造成本和模具维护成本。
3. 确保模具的刚度足够,避免因模具变形而导致产品变形或尺寸偏差。
三、产品结构设计1. 设计符合注塑工艺要求的产品结构,避免过于复杂的形状和壁厚不均匀等问题。
2. 考虑产品的装配性和模具的脱模性,减少脱模力和装配难度。
3. 考虑产品的设计可靠性和强度,避免产品在使用过程中出现断裂或变形等问题。
四、工艺参数设定1. 合理选择注塑机的射出速度、压力和温度等参数,确保产品质量。
2. 设计合理的料斗和喂料系统,确保材料供给平稳、无堵塞。
3. 考虑模具的填充、冷却和脱模过程,优化工艺参数,提高生产效率和产品质量。
五、模具维护和改进1. 建立定期维护计划,保证模具的正常运行和寿命。
2. 收集和分析模具运行数据,及时发现并解决潜在问题,改进模具设计。
3. 与模具制造商和生产工厂建立良好的沟通渠道,共同解决技术问题和改进模具性能。
总结:DFM注塑模具设计要点包括材料选择、模具结构设计、产品结构设计、工艺参数设定和模具维护与改进等方面。
合理应用DFM设计原则可以提高注塑模具的生产效率、降低成本并提升产品质量,对于企业的持续发展具有重要意义。
注塑模具设计教程
注塑模具设计教程
注塑模具设计是一门复杂而重要的技术,它是注塑加工过程中最关键的环节。
下面我将为大家简单介绍一下注塑模具设计的基本步骤和注意事项。
注塑模具设计的基本步骤主要包括产品设计、模具结构设计和模具零件设计。
首先,产品设计是整个模具设计的起点,要根据产品的功能和外观要求确定产品的形状、尺寸等参数,这对后续的模具设计非常重要。
其次,模具结构设计是指模具的整体结构,包括模具的开合方式、冷却系统、排气系统等,要根据产品的形状和工艺要求来确定模具结构,以保证产品的质量和生产效率。
最后,模具零件设计是指模具的各个零部件,如模具芯、模具腔、导向机构等,这些零部件要满足产品的形状和工艺要求,并能在生产过程中正常运行。
在注塑模具设计过程中,还需要注意以下几点。
首先,要考虑产品的特点和所用材料的性质,如产品的壁厚、缩水率、线收缩率等,以及材料的熔点、流动性等,这些因素会影响到模具的结构设计和零件设计。
其次,要合理选择模具材料,一般情况下,模具材料应具有高硬度、高强度和耐磨损等特点,以提高模具的寿命和使用效果。
再次,要注意模具的冷却系统设计,合理设置冷却水道,以提高产品的质量和生产效率。
最后,要考虑模具的制造工艺,合理划分工序和加工方法,以确保模具的加工精度和质量。
总之,注塑模具设计是一门复杂而重要的技术,它直接关系到产品的质量和生产效率。
通过合理的产品设计、模具结构设计
和模具零件设计,可以提高产品的质量和生产效率,降低成本,为企业带来更大的利益。
同时,在注塑模具设计过程中还要考虑产品特点、材料性质、模具材料选择、冷却系统设计和制造工艺。
希望以上内容可以对注塑模具设计有所帮助。
注塑模具设计与制造教程
03
注塑模具结构设计
分型面设计技巧及注意事项
分型面选择原则
确保产品顺利脱模,减少溢料和 飞边,简化模具结构。
分型面设计要点
分型面应位于产品断面轮廓最大 的地方,便于脱模;避免在分型 面上设计小孔或凹槽,防止溢料 和飞边;分型面的设计应便于模
具的加工和装配。
注意事项
分型面的选择应避免影响产品的 外观和性能;对于复杂的产品, 可能需要采用多个分型面进行脱
性能要求
模具材料应具有良好的切削加工性、热处理稳定 性、耐磨性、耐腐蚀性和抗疲劳性等性能。
精度与表面质量要求
精度要求
根据产品精度要求,确定模具的制造 精度和装配精度,保证产品的尺寸精 度和形位公差。
表面质量要求
模具表面应平整、光滑,无裂纹、毛 刺等缺陷;分型面、型腔等重要表面 应达到一定的粗糙度要求,以保证产 品的外观质量和脱模顺畅。
分类
根据模具的结构和使用特点,注塑模具可分为单分型面 注塑模、双分型面注塑模、带有侧向分型与抽芯机构的 注塑模以及热流道注塑模等。
注塑模具结构组成
导向部件
浇注系统
由主流道、分流道、浇口和冷料 穴等组成,用于将熔融的塑料从 注塑机喷嘴引入模具型腔。
包括导柱、导套等,用于保证动 模和定模在合模时的相对位置精 度。
压力调整技巧及常见问题解决方案
压力调整技巧
注射压力、保压压力和背压是注塑成型过程中的关键压力参数。 根据产品的结构、壁厚和塑料的流动性,合理调整这些压力参 数,以确保塑料充分填充模具并补偿收缩。
常见问题解决方案
针对飞边、短射、缩水等常见问题,通过调整注射速度、保压 时间和压力分布等参数,可以有效改善产品质量。
加工工艺流程梳理与规范操作指南
注塑模具设计
这一原则很重要,修改塑件产品图时,必须根据图 纸尺寸公差要求,修改为中间尺寸。尺寸及公差的几种 情况如表2-2所示。 表2-2 尺寸及公差的几种情况
2.2 侧抽芯机构
塑件的侧面常带有孔或凹槽,如图2-9所示。 在这种情况下,必须采用侧向成型芯才能满足塑 件成型上的要求。但是,这种成型芯必须制成活 动件,能在塑件脱模前将其抽出。完成这种活动 成型芯的抽出和复位机构叫抽芯机构。
图2-23 锁紧楔的形式
图2-24 锁紧楔的角度
6) 抽芯时的干涉现象 斜导柱在定模、滑块在动模的该结构形式设计时应注意, 滑块与推杆在合模复位过程中不能发生“干涉”现象,所谓 干涉现象是指滑块的复位先于推杆的复位致使活动型芯与推 杆相碰撞,造成活动型芯或推杆损坏,如图2-25所示。为了 避免上述干涉现象发生,在塑件结构允许的情况下,尽量避 免将推杆设计在活动型芯的水平投影面相重合处,否则,必 须满足条件,如图2-26所示,才能避免干涉现象。
④ 直导套常应用于简单模具或模板较薄的模具;I型带头导 套主要应用于复杂模具或大、中型模具的动定模导向中;II 型带头导套主要用于推出机构的导向中。为有利于减小摩擦, 在导套上也可开设储油槽,或采用自润滑型导套(在钢质导 套的环形槽内设 MoS2、在高强黄铜导套的侧壁孔内设固体 石墨)。 ⑤ 为了确保合模后分型面良好贴合,导柱与导套在分型面处 应设置承屑槽:一般都是削去一个面,或在导套的孔口倒角, 如图2-28所示。 ⑥ 导柱工作部分的长度应比型芯端面高出6-8mm ,如图229所示。
4、斜导柱倾斜角a 倾斜角的大小关系到斜导柱所承受的弯曲 力和实际达到的抽拨力,也关系到斜导柱的工 作长度、抽芯距和开模行程。为保证一定的抽 拔力及斜导柱的强度,取a小于25°,一般在 12°~25°范围内选取。 5、斜导柱直径 根据材料力学可以推导出斜导柱直径计算 公式:
最全注塑模具设计步骤以及注意事项的讲解
控铣削等加工方法,确保型芯、型腔的加工精度和表面质量。
02
浇口套、定位圈等关键零件加工工艺
采用高精度磨削、研磨等加工方法,保证零件的尺寸精度和形位公差。
03
导柱、导套等导向零件加工工艺
采用无心磨床、外圆磨床等高精度磨削设备,确保导向零件的精度和耐
磨性。
装配顺序和调试方法论述
装配顺序
遵循先下后上、先内后外的原则,先进行模架等支撑零件的装配,再进行型芯、型腔等成型零件的装配,最后进 行浇口套、定位圈等关键零件的装配。
根据模具结构确定加热装置的安装位置, 确保加热均匀且不影响模具其他功能。
油温机/水温机:适用于大型模具,加热 均匀,稳定性好。
03
06
考虑加热装置与冷却系统的协调,避免相 互干扰。
温度控制精度要求及实现途径
01
温度控制精度要求
02
根据制品要求确定温度控制精度,一般要求在±2℃ 以内。
03
对于高精度制品,温度控制精度要求更高,可达 ±1℃以内。
03
04
加强与客户和同行的沟 通和合作,不断提升服 务水平和市场竞争力。
培养高素质的人才队伍 ,为公司的可持续发展 提供有力保障。
感谢观看
THANKS
常见故障排查技巧和经验分享
常见故障排查技巧
介绍常见的注塑模具故障排查技巧,如检查模具磨损、清洗模具等。
经验分享
分享行业专家在注塑模具故障排除方面的经验和案例,提高读者解决问题的能力。
预防性维护策略推广
预防性维护策略
阐述预防性维护在注塑模具管理中的重要性 ,提出定期维护、保养和检查等策略。
推广实施
调试方法
在装配过程中,采用试装、试模等方法进行调试,确保模具各部件的配合精度和动作顺畅。对于复杂模具,还需 进行多次试模和调整,以达到最佳状态。
- 1、下载文档前请自行甄别文档内容的完整性,平台不提供额外的编辑、内容补充、找答案等附加服务。
- 2、"仅部分预览"的文档,不可在线预览部分如存在完整性等问题,可反馈申请退款(可完整预览的文档不适用该条件!)。
- 3、如文档侵犯您的权益,请联系客服反馈,我们会尽快为您处理(人工客服工作时间:9:00-18:30)。
1.3.3 动定模板大小、最大最小容模距、开模行程。
动定模板大小限制模具的长度和宽度尺寸,最大最小容模距限 制了模具高度,而开模行程限制了产品的最大顶出高度。
合模
开模
1.4 模腔数及其排列
1.4.1 确定模腔数的原则是什么? 1.4.2 多型腔的排列方式有哪些?
1.4.1 确定模腔数的原则是什么?
1.3 了解注塑机参数
1.3.1 最大注射量是多少? 1.3.2 最大注射速度和注射压力是多少? 1.3.3 动定模板大小、最大最小容模距、开模行程。
1.3.1 最大注射量是多少?
注塑机最大注射量是指螺杆在回退到最远行程后一次注射的塑 料重量,通常是以PS作为计量标准的。
模具设计者要了解将用于注塑的机器的最大注射量,并且所需 注射量最好不要超过最大注射量的80%。
双内抽芯机构
4.3 常见抽芯机构(十一)
拨块抽芯机构
4.3 常见抽芯机构(十二)
连杆抽芯机构
4.3 常见抽芯机构(十三)
哈夫块抽芯机构
4.3 常见抽芯机构(十四)
注塑模具设计方法
内容纲要
1 模具设计的准备工作 2 浇口与流道的设计 3 分型面设计 4 抽芯设计 5 顶出设计 6 排气设计 7 温度调节系统设计 8 热流道模具 9 模具材料 10 注塑不良对策
1 模具设计的准备工作
1.1 合格的产品图 1.2 了解注塑材料 1.3 了解注塑机参数 1.4 模具型腔数及其排列 1.5 模胚类型的选择 1.6 基本脱模方法 1.7 设定缩水率 1.8 设定成型尺寸
四型腔
1.4.2 多型腔排列的方式有哪些?(四)
六型腔
1.4.2 多型腔排列的方式有哪些?(五)
八型腔
1.5 模胚类型的选择
1.5.1 大水口模胚 1.5.2 小水口模胚
1.5.1 大水口模胚
1.5.2 小水口模胚
1.6 基本脱模方法
确定基本脱模方法,例如推杆顶出、推管顶出、推板顶出、气 动顶出、手动取出等。
注意:英制国家使用盎司作单位,一盎司约等于28克。
1.3.2 最大注射速度和注射压力是多少?
对于一些制品来说,必须有足够的注射压力和速度,才能够保 证充胶完整或者不出现明显的熔接痕。例如薄壁制品的注射要使用 高速才能充满。
注意:很多注塑机是用相对压力和速度来表征的,这 时要知道绝对数值就要查注塑机的说明书了。
2.3 潜水口(一)
潜伏式浇口是一种广为使用的浇口,开模时,制品和水口被强 制剥离,便于自动化生产,较脆的塑料不适合于潜水口。
使用潜伏式浇口,注意浇口前端要加工成圆台形,以便于制品 与水口剥离彻底。
2.3 潜水口(二)
这是另一种潜伏式浇口,用于较软的塑料。
2.4 点浇口
点浇口是指入水方式是从制品顶面垂直进入,同时,水口料和 制品从不同的分型面取出。模具使用小水口模胚,也叫三板模。一 些较脆的塑料不适合使用小水口。
1.1 合格的产品图
1.1.1 良好的产品结构。 1.1.2 尺寸合理。 1.1.3 公差合理。 1.1.4 表面要求合理。 1.1.5 明确的注塑材料。
1.1.1 良好的产品结构(一)
产品设计要尽量避免不必要的侧凹,避免出现模具抽芯,从而 简化模具结构。
1.1.1 良好的产品结构(二)
塑料产品要具有合适的壁厚及均匀的壁厚变化。 壁厚过小会造成流动阻力过大,发生缺胶现象。壁厚过大会造 成原料浪费并且缩水严重。 壁厚发生突变的地方,会产生应力集中,引起变形。因此产品 设计时尽量壁厚一致或者变化要均匀圆滑。
产品上10±0.1的孔位,模具设计时 的目标尺寸可确定为10.05,因为模芯越 磨损越小。
产品上10±0.1的胶位,模具设计时 的目标尺寸可确定为9.95,因为模腔越磨 损越大。
2 浇口与流道设计
2.1 浇口位置的选择 2.2 平水口 2.3 潜水口 2.4 点浇口 2.5 流道的形状和尺寸
2.1 浇口位置的选择
抽芯保险机构
4.3 常见抽芯机构(四)
内缩机构
4.3 常见抽芯机构(五)
前模斜滑块机构
4.3 常见抽芯机构(六)
异向多滑块机构
4.3 常见抽芯机构(七)
后模斜滑块机构
4.3 常见抽芯机构(八)
内滑块机构
4.3 常见抽芯机构(九)
液压抽芯机构,抽芯距离大,动作时间灵活。
4.3 常见抽芯机构(十)
3.4 常见分型面设计(八)
斜面柱位分模面
3.4 常见分型面设计(九)
侧面方位分模面
4 抽芯设计
4.1 什么是抽芯机构? 4.2 抽芯的计算 4.3 常见的抽芯机构 4.4 斜导柱的固定方式 4.5 压块的固定方式 4.6 滑块的固定方式 4.7 滑块与型芯的连接方式 4.8 滑块的导滑方式
4.1 什么是抽芯机构?
α≦25°(α为斜导柱倾 斜角度)
L=1.5D (L为配合长度) S=T+2~3mm(S为滑块需 要水平运动距离,T为成品倒 勾) δ为斜导柱与滑块间的 间隙,一般为0.5MM 斜导柱全长可以由CAD软 件测量得到
4.3 常见抽芯机构(一)
普通抽芯机构
4.3 常见抽芯机构(二)
前模抽芯机构
4.3 常见抽芯机构(三)
到底要以哪个
尺
尺寸为准啊?
寸
封
闭
!
1.1.3 公差合理
过于严格的公差会导致模具设计难度的增加和模具成本的增加。 因此,产品尺寸公差的制定应作仔细分析。
这个尺寸不重要, 还是放宽一点吧!
1.1.4 表面要求合理
过高的表面要求会增大模具加工的成本,一定的蚀纹深度对应 一定的拔模斜度,太大的蚀纹深度会导致产品出模拉花。
浇口位置选择的原则有: • 保证模具充模完整。 • 有利于排气。 • 减少熔接痕的数量和降低熔接痕的影响。 • 分子取向的影响。
2.2 平水口(一)
平水口是指浇口位置处于主分模面上的浇口,根据浇口形状的 不同,又分为矩形浇口、扇形浇口、平缝式浇口等。
浇口高度和宽度可以按照经验或下表确定:
制品质量(g) 0~5 5~40
通过分型面的选择,尽量避免侧抽芯机构 。
左图产品需要抽 芯吗?
3.3.1 模具结构考虑(四)
若塑件有侧孔时,应尽可能将抽芯设在公模部份,避免母模抽 芯,应为母模抽芯会比公模抽芯困难很多。
大家看看左图产 品的分型面。
3.3.1 模具结构考虑(五)
由于斜滑块合模时锁紧力较小,对于投影面积较大的大型塑件, 可将塑件投影面积大的分型面放在公母模合模的主平面上,而将投 影面积较小的分型面作为侧向分模面,否则斜滑块的锁紧机构必须 做得很庞大,或由于锁不紧而溢边。
原来用电火花 加工就可以了
现在还要抛光!
1.1.5 明确的注塑材料
产品图上应标明使用的注塑材料,模具设计者应根据客户提供 的材料确定收缩率和判断该材料的加工工艺性,以便有针对性的设 计模具。
同一套模具使用不同的注塑材料并不能保证注塑件的尺寸稳定 性和外观质量。
1.2 了解注塑材料
1.2.1 要了解注塑材料的什么性能? 1.2.2 塑料是否有掺杂?
2.5 流道的形状和尺寸
① 圆形:比表面积最小,热量 不易散失,阻力小。但要同 时开在前后模上,故加工困 难。直径φ5~φ10。
② U形:加工易,效果好,常 采用。
③ 梯形:加工易,效果不错, 也常采用。
④ 半圆形:比表面积大,不常 采用。
⑤ 矩形:比表面积最大,很少 采用。
3 分型面设计
3.1 什么是分型面? 3.2 封胶方式 3.3 分型面的选择原则
1.1.1 良好的产品结构(三)
塑料件的一些地方应设计成圆角,避免了模具加工的清角问题, 同时也增加了模具的坚固性。
与此同时,塑料件的另一些地方例如分型面或型芯与型腔配合 处则不宜设计成圆角。否则会造成分模困难,使模具复杂化。
1.1.2 尺寸合理
产品图尺寸要完备,并且不多不少。缺少尺寸会使模具设计者 无所适从,而多余的尺寸有可能造成关键尺寸的失控。
用CAD检查脱模方向的倒勾Analysis。
3.3.1 模具结构考虑(二)
为便于塑件脱模,应使塑件在开模时尽可能留在公模,只要使 塑件与公模的结合力大于塑件与母模的结合力即可。
达到塑件与公模的结合力大于塑件与母模的结合力的方法有很 多种。
塑料件留在母模的后果是压模!直接 导致生产事故!
3.3.1 模具结构考虑(三)
3.2 封胶方式(三)
前模镶件和后模镶件相配合时,配合面与运动方向不垂直。
模具设计时,应尽量避免分模面与运 动方向平行的靠破!
3.3 分型面的选择原则
3.3.1 模具结构考虑 3.3.2 制品质量考虑 3.3.3 模具制造难易性考虑
3.3.1 模具结构考虑(一)
分型面选择的最重要的原则是:必须开设在制品断面轮廓最大 的地方。否则,制品只能强脱。
3.4 常见分型面设计(一)
高低分模面
3.4 常见分型面设计(二)
斜分模面
3.4 常见分型面设计(三)
曲面分模面
3.4 常见分型面设计(四)
侧面穿孔分模面的靠破和枕出
3.4 常见分型面设计(五)
侧面穿孔分模面
3.4 常见分型面设计(六)
平面穿孔分模面
3.4 常见分型面设计(七)
斜面方孔分模面
1.2.2 塑料是否有掺杂?
很多塑料为提高强度和韧度,会加入玻璃纤维或者碳纤维,加 入了这些不同的组分后,塑料的收缩率和流动特性会发生很大的改 变。通常加入的玻纤从15%到40%不等。
也有一些塑料加入另一种塑料以取得两种塑料折中的性能。例 如常用的ABS+PC。
PBT+30%GF是很多电子 产品的设计材料。
3.1 什么是分型面?