金属基复合材料界面表征及其进展
颗粒增强金属基复合材料的研究现状及展望

第20卷第1期V o l.20N o.1 硬 质 合 金CE M EN T ED CA RB I D E2003年3月M ar.2003综合评述颗粒增强金属基复合材料的研究现状及展望王基才Ξ 尤显卿 郑玉春 程娟文(合肥工业大学材料学院,合肥,230009)摘 要 从材料的选择、制备技术和性能等方面对颗粒增强金属基复合材料的研究现状进行综合评述。
分析了颗粒增强金属基复合材料发展过程中存在的一些问题及改进措施,指出了颗粒增强金属基复合材料的几个重要发展方向:制备技术的改进、应用范围向特色应用领域的拓宽和再生回收的重视。
关键词 复合材料 碳化物粒子 制备技术 性能 生产应用1 引 言自1965年A Kelly,G J davies和D C ratch ley 等[1]首先总结和提出了金属基复合材料(M etal M atrix Com po sites,简称MM C s)的资料以来, MM C s就以其高的比强度、比刚度及良好的热稳定性、耐磨性、尺寸稳定性及成分可设等优点[2-4]吸引了各国学者和科研人员的关注,成为材料研究和开发的热点。
按增强体的形式MM C s可分为连续纤维增强、短纤维或晶须增强、颗粒增强等。
由于连续纤维增强的MM C s必须先制成复合丝,工艺成本高而复杂,因此其应用范围有很大的局限性,只应用于少数有特殊性能要求的零件。
颗粒增强金属基复合材料(Particu late R einfo rced M etal M atrix Com po sites,简称PRMM C)是将陶瓷颗粒增强相外加或自生进入金属基体中得到兼有金属优点(韧性和塑性)和增强颗粒优点(高硬度和高模量)的复合材料。
PRMM C具有增强体成本低,微观结构均匀,材料各向同性,可采用热压、热轧等传统金属加工工艺进行加工等优点[5-8],因而与纤维增强、晶须增强金属基复合材料相比倍受关注[9-10]。
2 PRMM C材料的选择基体材料是MM C s的主要组成部分,起着固结增强相、传递和承受各种载荷(力、热、电)的作用。
金属基复合材料界面

金属基复合材料界面金属基复合材料界面是指由金属基体和其他材料相互作用形成的界面。
金属基复合材料是一种重要的结构材料,在航天、航空、汽车制造等领域发挥着重要作用。
而界面则是金属基复合材料性能的关键因素之一,影响着材料的力学性能、热学性能、电学性能等。
金属基复合材料界面的特点主要包括界面强度、界面形态以及界面反应等。
首先,界面强度是指金属基复合材料界面的抗剪强度,决定了材料的强度和韧性。
界面形态则是指金属基复合材料界面的结构形貌,包括界面的平整度、均匀度等。
最后,界面反应是指金属基复合材料界面处发生的化学反应,影响着材料的稳定性和使用寿命。
金属基复合材料界面的研究主要包括界面强度的测试方法以及界面的表征技术。
一般来说,界面强度可以通过剪切测试、拉伸测试等方法进行测量。
剪切测试是将金属基复合材料的界面置于剪切载荷下,通过测量界面之间的滑动距离和加载力来计算界面的剪切强度。
拉伸测试则是将金属基复合材料的界面置于拉伸载荷下,通过测量界面的断裂强度和断裂面积来计算界面的拉伸强度。
界面的表征技术主要包括电子显微镜观察和X射线衍射分析等。
电子显微镜观察可用于观察金属基复合材料界面的形貌和结构特征,如界面的平整度、均匀度以及异质相等。
X射线衍射分析则可以用于分析界面处的晶体结构和相变行为,从而揭示界面反应的机制和影响因素。
金属基复合材料界面的性能调控主要包括三个方面,即界面结构调控、界面化学调控以及界面力学调控。
界面结构调控主要是通过改变复合材料的结构和工艺参数来调控界面的形貌和结构特征,从而改善界面的强度和稳定性。
界面化学调控则是通过引入中间相或质量扩散来调控界面的化学反应,从而提高界面的稳定性和抗氧化性能。
界面力学调控主要是通过改变金属基复合材料的力学性能来调控界面的剪切强度和散射行为,从而提高界面的强度和韧性。
总之,金属基复合材料界面是一种关键的材料界面,影响着金属基复合材料的力学和热学性能。
了解金属基复合材料界面的特点和性能调控方法,对于开发高性能金属基复合材料具有重要意义。
第六章复合材料表界面的分析表征

41
不同处理碳纤维增强复合材料冲击 载荷与冲击时间的对应关系
A. 接枝聚丙烯酰胺碳纤维; B. 接枝聚丙烯 酸碳纤维; C. 氧等离子处理碳纤维; D. 未 处理碳纤维
氧等离子处理(曲线C)碳纤维 复合丝试样的冲击载荷曲线主 要弹性承载能U1差不多比未处 理者增加近3倍,表明基体变形 更大,也有更多的纤维发生形 变。相反塑性承载能U2却小到 可略视的地步,几乎没有什么 纤维拔出和与基体的脱粘,充 分表明了强结合的界面特征。
25
碳纤维表面官能团的分析
还原剂,消除自由基,证明等 离子处理产生的大部分是游离
基,不是酚羟基
图6-25 等离子处理时间对自由基浓度的影响
在等离子处理初期,自由基浓度迅速增加,处 理5分钟后,自由基浓度增加渐趋平缓。
27
图6-26 UHMWPE纤维表面活性的衰减
经等离子处理后的UHMWPE纤维暴露在空气中,表 面自由基的浓度随时间而衰减,表面活性在逐渐减小
36
6.4.2 复合材料界面的动态力学分析
a-接枝玻纤 b-未接枝玻纤 涂敷聚苯乙烯树脂的玻璃纤维辫子的动态
力学扭辫曲线
曲线b在92℃处出现一个 尖锐的聚苯乙烯玻璃化转变 损耗峰,而曲线a上,在聚 苯乙烯玻璃化转变损耗峰高 温一侧还有一个小峰,一般 称为α’峰,也叫做界面峰。
界面粘结强,则试样承 受周期负荷时界面的能力损 耗大,α’峰越明显。
复合材料界面受到因 热膨胀系数不同引起 的热残余应力。热残 余应力的大小正比于 两者的热膨胀系数之 差Δα和温差ΔT, 也与基体和纤维的模 量有关。
29
❖ 6.4 界面力学性能的分析表征
难熔金属基复合材料的研究进展

难熔金属基复合材料的研究进展难熔金属基复合材料是一种具有卓越性能和广泛应用潜力的材料。
它由高熔点金属基体和分散相组成,具有高温强度、耐腐蚀性、耐磨损性和导电性等优点。
难熔金属基复合材料的研究已经取得了显著的进展,并在航空航天、能源、汽车和冶金等领域得到广泛应用。
难熔金属基复合材料的研究主要涉及材料的制备技术、性能优化和应用研究。
目前,常用的制备技术包括粉末冶金、熔融混合、机械合金化和表面改性等方法。
其中,粉末冶金是一种常用的制备难熔金属基复合材料的方法。
通过粉末冶金技术可以得到具有均匀分散相的复合材料,从而提高材料的力学性能和耐热性能。
难熔金属基复合材料的性能优化主要通过合金化和微结构控制实现。
通过合金化可以改变金属基体的组成,调整材料的力学性能和导热性能。
通过微结构控制可以调控分散相的尺寸、形状和分布,进一步提高材料的力学性能和耐热性能。
此外,难熔金属基复合材料的表面改性也是一种常用的性能优化手段。
通过在金属基体的表面引入功能性涂层,可以提高材料的表面硬度、耐磨损性和耐腐蚀性。
难熔金属基复合材料在航空航天领域具有广泛的应用前景。
在航空发动机中,难熔金属基复合材料可以作为高温结构材料使用,用于制造涡轮叶片、燃烧室和燃气轮机等部件。
难熔金属基复合材料具有出色的高温强度和耐热性能,可以提高发动机的工作效率和可靠性。
此外,在航天航空热保护系统中,难熔金属基复合材料也可以作为热隔断材料使用,有效减少空气动力热、压力热和辐射热对航天器的影响。
在能源领域,难熔金属基复合材料可以用于制造高温燃料电池和核能反应堆等设备。
难熔金属基复合材料具有优异的导电性能和耐腐蚀性,可以提高燃料电池和核能反应堆的运行效率和安全性。
此外,难熔金属基复合材料还可以用于制造高温储能设备,用于储存太阳能和风能等可再生能源。
在汽车领域,难熔金属基复合材料可以用于制造发动机和制动系统等关键部件。
难熔金属基复合材料具有出色的耐磨损性和耐高温性能,可以提高发动机和制动系统的性能和寿命。
金属基复合材料的发展趋势
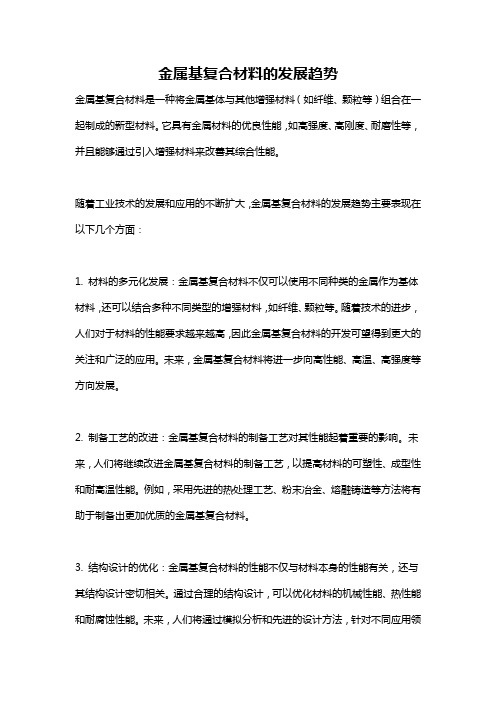
金属基复合材料的发展趋势金属基复合材料是一种将金属基体与其他增强材料(如纤维、颗粒等)组合在一起制成的新型材料。
它具有金属材料的优良性能,如高强度、高刚度、耐磨性等,并且能够通过引入增强材料来改善其综合性能。
随着工业技术的发展和应用的不断扩大,金属基复合材料的发展趋势主要表现在以下几个方面:1. 材料的多元化发展:金属基复合材料不仅可以使用不同种类的金属作为基体材料,还可以结合多种不同类型的增强材料,如纤维、颗粒等。
随着技术的进步,人们对于材料的性能要求越来越高,因此金属基复合材料的开发可望得到更大的关注和广泛的应用。
未来,金属基复合材料将进一步向高性能、高温、高强度等方向发展。
2. 制备工艺的改进:金属基复合材料的制备工艺对其性能起着重要的影响。
未来,人们将继续改进金属基复合材料的制备工艺,以提高材料的可塑性、成型性和耐高温性能。
例如,采用先进的热处理工艺、粉末冶金、熔融铸造等方法将有助于制备出更加优质的金属基复合材料。
3. 结构设计的优化:金属基复合材料的性能不仅与材料本身的性能有关,还与其结构设计密切相关。
通过合理的结构设计,可以优化材料的机械性能、热性能和耐腐蚀性能。
未来,人们将通过模拟分析和先进的设计方法,针对不同应用领域开发出更加优化的金属基复合材料结构。
4. 新型增强材料的研究:金属基复合材料在增强材料的选择上有很大的灵活性。
未来,人们将继续寻找新型的增强材料,并研究其与金属基体的相容性和增强效果。
例如,纳米材料、陶瓷颗粒等新型增强材料的引入,将进一步提高金属基复合材料的性能。
5. 应用领域的扩大:金属基复合材料由于其优异的性能,在航空航天、汽车制造、机械制造等领域得到了广泛应用。
未来,随着技术的发展和应用需求的不断增加,金属基复合材料将在更多领域得到应用。
尤其是在新能源、环保、生物医学等领域,金属基复合材料的应用前景将更加广阔。
总之,随着工业技术的不断发展,金属基复合材料将继续取得重大进展。
石墨烯增强铝基复合材料的研究进展
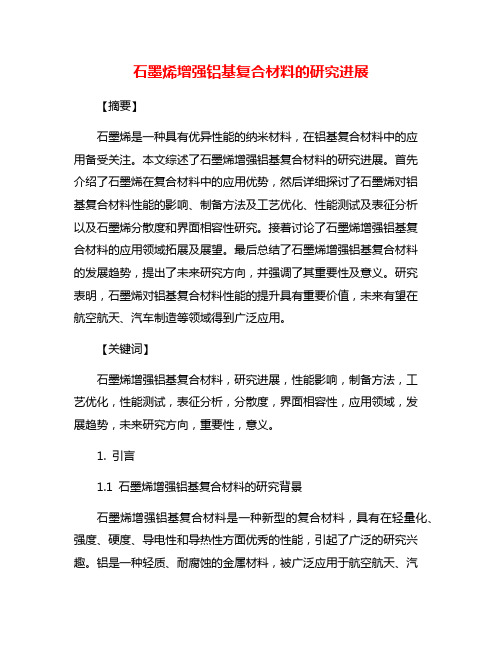
石墨烯增强铝基复合材料的研究进展【摘要】石墨烯是一种具有优异性能的纳米材料,在铝基复合材料中的应用备受关注。
本文综述了石墨烯增强铝基复合材料的研究进展。
首先介绍了石墨烯在复合材料中的应用优势,然后详细探讨了石墨烯对铝基复合材料性能的影响、制备方法及工艺优化、性能测试及表征分析以及石墨烯分散度和界面相容性研究。
接着讨论了石墨烯增强铝基复合材料的应用领域拓展及展望。
最后总结了石墨烯增强铝基复合材料的发展趋势,提出了未来研究方向,并强调了其重要性及意义。
研究表明,石墨烯对铝基复合材料性能的提升具有重要价值,未来有望在航空航天、汽车制造等领域得到广泛应用。
【关键词】石墨烯增强铝基复合材料,研究进展,性能影响,制备方法,工艺优化,性能测试,表征分析,分散度,界面相容性,应用领域,发展趋势,未来研究方向,重要性,意义。
1. 引言1.1 石墨烯增强铝基复合材料的研究背景石墨烯增强铝基复合材料是一种新型的复合材料,具有在轻量化、强度、硬度、导电性和导热性方面优秀的性能,引起了广泛的研究兴趣。
铝是一种轻质、耐腐蚀的金属材料,被广泛应用于航空航天、汽车制造、电子设备等领域。
铝的力学性能相对较低,容易发生塑性变形和疲劳破坏,限制了其应用范围。
1.2 石墨烯在复合材料中的应用优势1. 高强度:石墨烯具有出色的机械性能,是世界上最强硬的材料之一,比钢强度还高。
将其添加到铝基复合材料中可以显著提高复合材料的强度和硬度。
2. 轻质:石墨烯的密度极低,仅为铝的0.77%,因此可以有效降低复合材料的密度,使其更轻便。
3. 良好的导热性和导电性:石墨烯具有优异的导热和导电性能,可以改善复合材料的导热和导电性能,提高其传热和传电效率。
4. 耐腐蚀性:石墨烯具有优秀的耐腐蚀性,可以有效延长复合材料的使用寿命。
综合以上优势,石墨烯在铝基复合材料中的应用具有巨大的潜力,可以为各个领域提供更高性能的材料解决方案。
2. 正文2.1 石墨烯对铝基复合材料性能的影响石墨烯具有优异的导热性和导电性,能够有效提高铝基复合材料的导热性和导电性能。
金属基复合材料的界面结合性能研究
金属基复合材料的界面结合性能研究随着科技进步和工业发展,金属基复合材料在各个领域得到了广泛应用。
金属基复合材料由金属基体和增强相组成,通过界面结合强化材料和基体的相互作用,增强了材料的性能。
然而,界面结合性能对于金属基复合材料的整体性能有着重要影响。
本文将探讨金属基复合材料的界面结合性能以及相关研究进展。
首先,界面结合性能是金属基复合材料的重要性能之一。
金属基复合材料的界面结合强度和界面结合能力决定了材料的力学性能、疲劳性能和耐蚀性能等。
好的界面结合性能可以增强材料的强度和韧性,提高材料的负荷承受能力。
因此,研究金属基复合材料的界面结合性能对于提高材料的性能至关重要。
其次,当前金属基复合材料的界面结合性能研究主要集中在几个方面。
首先是材料选择。
在金属基复合材料的界面结合性能研究中,选择合适的金属基体和增强相材料非常重要。
科学家通过研究不同材料的界面结合性能,选择最佳的组合,以提高金属基复合材料的性能。
其次是界面处理。
通过表面处理、化学修饰等方式改善金属基复合材料的界面结合性能,使得界面结合更加牢固。
最后是界面结合机理研究。
通过实验和模拟方法,科学家们深入研究了金属基复合材料界面结合机理的基本原理,为材料的设计和改进提供了理论指导。
此外,金属基复合材料的界面结合性能研究还有一些挑战和难点。
首先是实验方法的选择。
由于界面结合性能的研究需要对界面进行精确的测试和分析,科学家们需要选择合适的实验方法和设备以获得可靠的数据。
其次是界面结合性能与材料性能的相互影响。
界面结合性能的改变可能会影响材料的力学性能、疲劳性能等,因此需要综合考虑界面结合性能和材料性能之间的关系。
最后是界面结合性能的模拟和预测。
由于金属基复合材料的界面结合机理复杂,准确地预测和模拟界面结合性能仍然是一个挑战。
综上所述,金属基复合材料的界面结合性能研究是一个重要而有挑战性的领域。
通过选择合适的材料、优化界面处理方法以及深入研究界面结合机理,可以提高金属基复合材料的性能。
MMC4-复合材料的界面
交换反应结合 混合结合
上述几种结合方式的组合
动力学相容 —— 界面反应动力学
增强物与基体相互作用的数量、速度、反应产物的数量和形态 扩散是界面反应动力学中的主要现象和速度控制过程。
1. 基体与增强物之间不生成化合物,只生成固溶体
这种情况并不导致复合材料性能的急剧降低,主要的危险是 增强物的溶解消耗。
凝固技术国家重点实验室
第四讲 金属基复合材料的界面
界面的基本概念 界面的物理化学特性 界面反应 界面力学与变形、断裂 界面表征
2006-8-2
MMC的重点
一、界面的基本概念
复合材料是由两种或两种以上物理和化学性能不同的材料成的 新型材料,那么必然存在异种材料的接触面——界面。 在金属基复合材料中往往由于基体与增强物发生相互作用、生 成化合物,基体与增强物的互扩散、形成扩散层,增强物的表 面预处理涂层,使界面的形状、尺寸、成分、结构等变得非常 复杂。
SiC纤维沿深度方向元素分布
SiC中的C SiC中的Si 氧 游离的C
主元素C和Si在表面层含量 较少,而杂质富集
CVD法沉积C层的SiC纤维
SiO2中的Si
SiC中的C SiC中的Si 氧 SiO2中的Si 溅射了Mo的SiC纤维 游离的C
由于基体和增强物的膨胀系数的不匹配、弹性性能的差别,金 属基复合材料在制造和加工过程中,在界面上产生残余应力, 此残余应力往往超过、甚至大大超过基体的屈服强度,致使界 面附近的基体的微观结构及性能发生明显变化,对复合材料的 宏观力学性能产生严重影响。
或
界面反应的控制
界面反应不足或过量都不利,反应不足材料强度低,过量则脆化
1. 增进结合
—— 控制
石墨纤维及氧化物作增强材料时,因与多数基体不能很好润湿,界 面结合强度低,很难完成传递载荷的任务。因此必须在不损伤纤维 的条件下改善基体对它们的润湿性,使得发生反应形成界面,并保 证界面的结合强度。改进润湿的主要方法是涂层。 在石墨纤维上用真空喷涂法涂上一层铝,再进行退火处理。低于 500°C时,Al与C几乎不起作用; 600°C形成少量Al4C3,强度 开始提高。
金属基复合材料简介及研究现状
3D打印技术
02
利用3D打印技术,实现金属基复合材料的定制化、高效制造
。
多尺度复合技术
03
发展多尺度复合技术,实现金属基复合材料的多层次结构设计
。
05
结论与展望
研究成果总结
金属基复合材料的制备技术得到改进,包括粉末冶金法、喷射沉积法、机械合金 化法等复合材料的应用领域不断扩大,涉及到能源、环保、医疗、航空航天等领 域,且在各个领域中都有显著的应用成果。
02
金属基复合材料的性能与 特点
力学性能
01
02
03
强度与硬度
金属基复合材料具有较高 的强度和硬度,能够承受 较大的应力和压力。
韧性
金属基复合材料的韧性比 金属单质更强,能够吸收 更多的能量,抵抗冲击和 振动。
疲劳性能
金属基复合材料的疲劳性 能较好,能够在反复应力 作用下保持稳定的性能。
物理性能
由于金属基复合材料具有高强度、高刚性和 轻质等优点,因此在航空航天领域得到广泛 应用,如飞机结构件、卫星部件等。
金属基复合材料在汽车工业中也有广泛应用 ,如汽车发动机部件、变速器齿轮等。
能源领域
生物医学领域
金属基复合材料在能源领域也有广泛应用, 如太阳能电池板支架、核反应堆结构件等。
金属基复合材料在生物医学领域也有广泛应 用,如人工关节、牙科种植体等。
扩散法
将增强体和金属基体在高温下进行扩散处理,使两者相互 渗透、结合,形成复合材料。该方法适用于制备连续或非 连续增强金属基复合材料。
喷射沉积法
将增强体和金属熔体通过喷射、雾化等方法制备成复合材 料。该方法适用于制备连续或非连续增强金属基复合材料 。
金属基复合材料的应用领域
第6章-2 金属基复合材料的界面及其表征
6.2.6.2 界面对金属基复合材料力学性能的影响
界面结合强度对复合材料 的冲击性能影响较大。纤维 从基体中拔出,纤维与基体 脱粘后,不同位移造成的相 对摩擦都会吸收冲击能量, 并且界面结合还影响纤维和 基体的变形能力。
三种复合材料的典型冲击载荷- 时间关系曲线
1-弱界面结合 2-适中界面结合 3-强界面结合
1
界面组成及成分变化
2
界面区的位错分布
3
界面强度的表征
4
界面残余应力的测定
5 界面结构的高分辨观察及其原子模拟
10
6.3.1 界面组成及成分变化
确定界面上有无新相形成是界面表征的主要内容之一。新相可能是 增强体与基体通过扩散反应而在界面处形成的新相, 也可能是基体组 元与相界处杂质元素反应在界面处优先形核而成为新相。 一般情况下常用明场像或暗场像对界面附近区域形貌进行观察, 通 过选区衍射和X射线能谱进行微区结构和成分分析。 当析出物十分细小时, 可采用微衍射和电子能量损失谱来分析其结 构和成分, 电子能量损失谱尤其适合于对C、O等轻元素的分析。可 以准确判知界面析出物的结构、成分和形貌特征。
1、金属基复合材料界面可分成哪些类型?请分别举 例说明不同类型界面的特征。 2、金属基复合材料的界面结合有哪几种?什么样的 界面结合对力学性能更有利?
3
6.2.6 界面对性能的影响
不同类型和用途的金属基复合材料界面的作用和最佳界面结构 性能有很大差别。
纤维增强脆性基体复合材料的微观断裂模型 (a)纤维“桥接” (b)裂纹穿过纤维造成脆断
11
挤压铸造Al18B4O33w /Al-2.5%Mg 复合材料界面 TEM 照片
4Al18B4O33+33Mg = 33MgAl2O4+6Al+16B
- 1、下载文档前请自行甄别文档内容的完整性,平台不提供额外的编辑、内容补充、找答案等附加服务。
- 2、"仅部分预览"的文档,不可在线预览部分如存在完整性等问题,可反馈申请退款(可完整预览的文档不适用该条件!)。
- 3、如文档侵犯您的权益,请联系客服反馈,我们会尽快为您处理(人工客服工作时间:9:00-18:30)。
第14卷第3期V o l.14N o.3材 料 科 学 与 工 程M aterials Science&Engineering总第55期Sep t.1996金属基复合材料界面表征及其进展梅 志 顾明元 吴人洁上海交通大学 上海 200030【摘 要】 界面是复合材料极其重要的组成部分,全面而确切地表征界面是控制和改善复合材料的最重要基础之一。
本文从界面组成及成分变化、界面区的位错分布、界面残余应力的测定和界面结构的高分辨观察及其原子模拟等四个方面综述了金属基复合材料界面表征的方法及其最新进展。
【关键词】 金属基复合材料 界面表征Character ization of M etal M atr ix Com posite I n terfaceand Its AdvancesM e i Zh i Gu M i ngyuan W u Ren j ieShangha i J i ao-tong Un iversity,Shangha i 200030【Abstract】 A s interface is very i m po rtant in compo site m aterial,characterizing interface all2 sidedly and exactly is one of the mo st i m po rtant bases of contro lling and i m p roving compo site m a2terials.In th is paper the m ethods and its latest developm ents of the characterizati on ofM M C′s in2terface are review ed.there are four m ain m ethods to characterize the interface;(1)to analysephase structure、compo siti on of interface;(2)to deter m ine dislocati on distributi on in the interfaceregi o;(3)to m easure interface residual stress;(4)to m anifest the interfacial structure w ith h ighreso luti on observati on and w ith atom ic si m ulati on of interface structure.T hey are introduced in o r2der.【Key words】 M etal m atrix compo site,Interface characterizati on.一、引 言界面是复合材料特有的而且是极其重要的组成部分,复合材料的性能与界面性质密切相关。
由于界面的原子结构、化学成分和原子键合不同于界面两侧的增强体和基体,界面的性质与界面两侧有很大的差别,而且在界面上更容易发生化学反应,所以界面对复合材料的性能起着极其重要的作用,有时甚至能起控制作用。
因此,只有深入了解界面的几何特征、化学键合、界面结构、界面的化学缺陷与结构缺陷、界面稳定性与界面反应及其影响因素,才能在更深的层次上理解界面与材料性能之间的关系,进一步达到利用“界面工程”发展新型高性能复合材料的目的。
与此同时,界面研究的成果不仅会给复合机理的研究带来促进作用,而且这项工作的深入开展还关系到研究物质表面结构与性能的现代新技术和新仪器的进展。
界面结构的研究是当前材料科学的前沿课题,人们对界面的相组成和结构、界面区的成分及其分布、近界面基体一侧的位错密度及其分布等以及它们与材料总体性能之间的关系进行了广泛研究。
然而,过去由于实验手段的限制,以往的研究工作大部分停留在微米尺度,而大量的精细结构被掩盖。
近年来,随着高分辨电子显微术(HR E M)及分析电子显微术(如EEL S、A P2F I M等)的发展,使得在原子尺度研究界面结构、界面化学及界面缺陷成为可能,再配合以其它微区形貌、结构和成分分析的手段,并加以综合应用,相互补充,使得对界面结构有了更深入的了解,取得了一些令人鼓舞的进展。
下面将从四个方面加以介绍。
二、界面层相组成及成分变化确定界面上有无新相形成是界面表征的主要内容之一。
这种析出物可能是增强体与基体通过扩散反应而在界面处形成的新相,也可能是基体组元与相界处杂质元素反应在界面处优先形核而成为新相。
一般情况下常用明场像或暗场像对界面附近区域形貌进行观察,通过选区衍射和X射线能谱进行微区结构和成分分析。
当析出物十分细小时,可采用微衍射和电子能量损失谱来分析其结构和成分,电子能量损失谱尤其适合于对C、O等轻元素的分析。
这种综合分析可以准确判知界面析出物的结构、成分和形貌特征,如文献[1]中就用X射线能谱、电子能量损失谱和微衍射等分析手段确认界面上存在细小M gO相,就是一个很好的实例。
界面上析出相不可避免地会对复合材料性能产生影响,有时甚至直接影响到材料性能的高低。
例如文献[2]在研究A l Si Cw界面组织与复合材料力学性能关系时,运用修正的混合规则(ROM)来研究拉伸强度的计算值与实验值的对比符合情况,结果发现对A l2Cu基体两者符合很好,而对A l2Cu2M g基体两者有较大偏差。
经显微组织观察,发现该偏差是由于界面上形成氧化物和尖晶石而造成晶须强度下降所致。
因此应用混合规则时必须考虑界面相对复合材料强度的影响,从而为今后复合材料基体合金的设计提供参考。
除此之外,增强体的加入也会影响到复合材料基体合金中固溶原子的分布,从而也会对复合材料性能产生影响,例如,用液体金属浸渗法制造纤维增强复合材料时,由于纤维排列对金属凝固的限制,导致基体中合金成分变化,甚至有未预料到的第二相形成在纤维 基体界面上,结果基体中合金元素浓度降低。
而起硬化作用析出物的形成,又要求有一活泼合金元素的临界值,所以以上成分变化会显著改变基体合金的时效硬化响应[3]。
大量报导证明,陶瓷增强体的存在会影响A l合金中固溶原子的分布,Strangw ood等[4]在研究Si C2A l合金界面上的固溶偏析时发现,在欠时效15V o l%Si C-2XXXA l(1.45at%Cu, 1.67at%M g,0.12at%Zr,0.1at%M n)的Si C 基体界面上的固溶偏析可达4.5at%M g和9at%Cu,而M g和Cu偏析都可降低界面区域附近A l基体的局部熔点,因此,尽管当温度似乎仍处于2124A l的固态范围时,固溶偏析可能严重到引起Si C2A l界面局部熔化的程度,从而可以解释该材料在高应变速率超塑性试验中的一些令人困惑的现象[4]。
我校金属基复合材料国家重点实验室利用电子能量损失谱仪,研究了T i C粒子强化I M I2 829T i合金,结果发现T i C粒子表面存在一明显的碳浓度梯度,贫碳区厚度与材料制备工艺和热处理过程有关,结合C2T i相图分析,提出基体和增强体之间C和T i的互相扩散,形成一理想的溶解型结合是该复合材料性能良好的原因[5]。
三、界面区的位错分布界面区近基体侧的位错分布是界面表征的又一重点,它有助于了解复合材料的强化机制。
经验表明,为了能更清晰地显示出位错分布的特征并便于定量测定位错密度,采用弱束成象效果较好。
过去,人们一直认为复合材料强度提高(实验强度值高于理论预测值)是由于位错使基体强化所致,并且在许多实验中也确实观察到了增强体周围较高的位错密度。
虽然后来发现,基体中亚晶尺寸减小也是复合材料强化的一个重要原因,但位错强化仍然是复合材料强化的重要机制之一。
采用高压电镜对A l Si Cw复合材料界面的原位观测证明:由于两种异质材料热膨胀系数不同,在复合制备冷却中界面处形成的位错,在加热到一定温度后会自行消失,但在重新冷却下来时又会再次产生。
这种复合材料中,位错密度可高达1013~1014m-2,是造成这类复合材料高强度的重要原因之一[6]。
近来,有人[7]对不连续碳化硅增强A l合金屈服应力增加的原因进行了定量研究,发现屈服应力增加幅度明显与Si C体积分数和颗粒大小有关。
实验结果表明,位错密度随Si C体积分数增加而增加、随粒子尺寸增加而减少。
亚晶尺寸随碳化硅体积分数和颗粒尺寸变化的趋势正好与位错密度相反。
林君山等[8]在研究铸造Si Cp 2024合金材料微观结构与强化机制时认为,由增强相导致的应力集中和基体形变的高约束度,是控制Si Cp 2024复合材料形变与强化的两个主要因素。
可以预料,今后对界面区位错分布的观察重点将转到研究位错产生、发展的影响因素上来,并有从定性发展到定量研究的趋势,并在可能的条件下,尽量采用高压电镜来观察较厚的薄膜试样,以尽可能真实地反映位错密度大小。
另外,对复合材料强化机制的研究也开始注意全面考察基体中组织变化带来的变化,而不再只考虑位错密度变化所造成的强化,表明人们对复合材料的强化机制有了一个更深刻的认识。
四、界面残余应力的测定复合材料的界面结合与该处的残余应力密切相关。
对界面处内应力的测量,除了我们所熟知的沿用非破坏性测量材料残余应力的X射线方法外,还有用中子衍射测残余应力的方法,近年来又发展了用会聚束电子衍射及同步辐射连续X射线测残余应变的方法。
目前对金属基复合材料来说,残余应力的测定主要还是采用单一波长的特征X射线的sin2Ω法[9]。
它所测出的是界面两侧一定厚度范围内的平均残余应力,而要确知在界面处的应力仍较困难,尤其是对增强体附近急剧变化的应变场的测量无能为力。
中子衍射[10]则利用中子对材料的高穿透性来测量残余应力。
这种方法虽能测量材料内部的应变,但它所测的是体积平均应力,所以它也不能解决增强体周围急剧变化应力的测量问题。
为解决这个问题,Todd等[11]采用高强度的同步辐射连续X射线,利用其能量色散衍射同时兼有较好穿透性(例如可穿透钛数毫米)和对残余应变梯度具有的高空间分辨率,测定了金属基复合材料内部连续增强体附近的残余应变梯度,其精度可达10-3到10-4,取得了满意的效果。
但这种方法的致命缺点是成本太高。
另外一些研究者则试图用会聚束电子衍射的方法来测定界面残余应力,并取得了可喜的进展。
如王仁卉[12]利用大角度会聚束电子衍射(LA CB ED)研究了A l A l2O3复合材料界面应力场,发现由于界面处存在应力场,引起界面附近的高阶劳厄线(HOL Z线)发生明显的弯曲和分裂并变得模糊,目前作者正通过对LA CB ED花样的动力学模拟来对界面处的应力场作进一步的研究。