金属基复合材料界面
金属基复合材料的界面类型
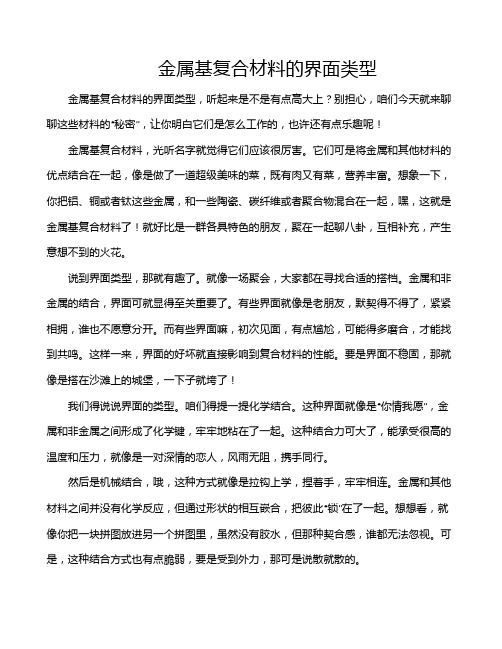
金属基复合材料的界面类型金属基复合材料的界面类型,听起来是不是有点高大上?别担心,咱们今天就来聊聊这些材料的“秘密”,让你明白它们是怎么工作的,也许还有点乐趣呢!金属基复合材料,光听名字就觉得它们应该很厉害。
它们可是将金属和其他材料的优点结合在一起,像是做了一道超级美味的菜,既有肉又有菜,营养丰富。
想象一下,你把铝、铜或者钛这些金属,和一些陶瓷、碳纤维或者聚合物混合在一起,嘿,这就是金属基复合材料了!就好比是一群各具特色的朋友,聚在一起聊八卦,互相补充,产生意想不到的火花。
说到界面类型,那就有趣了。
就像一场聚会,大家都在寻找合适的搭档。
金属和非金属的结合,界面可就显得至关重要了。
有些界面就像是老朋友,默契得不得了,紧紧相拥,谁也不愿意分开。
而有些界面嘛,初次见面,有点尴尬,可能得多磨合,才能找到共鸣。
这样一来,界面的好坏就直接影响到复合材料的性能。
要是界面不稳固,那就像是搭在沙滩上的城堡,一下子就垮了!我们得说说界面的类型。
咱们得提一提化学结合。
这种界面就像是“你情我愿”,金属和非金属之间形成了化学键,牢牢地粘在了一起。
这种结合力可大了,能承受很高的温度和压力,就像是一对深情的恋人,风雨无阻,携手同行。
然后是机械结合,哦,这种方式就像是拉钩上学,捏着手,牢牢相连。
金属和其他材料之间并没有化学反应,但通过形状的相互嵌合,把彼此“锁”在了一起。
想想看,就像你把一块拼图放进另一个拼图里,虽然没有胶水,但那种契合感,谁都无法忽视。
可是,这种结合方式也有点脆弱,要是受到外力,那可是说散就散的。
再来说说电磁结合,这种界面就像是超级英雄的联手。
金属和非金属通过电磁力相互作用,形成了稳固的结合。
它们之间的相互吸引,就像是你看到喜欢的人,心里怦怦直跳。
电磁结合在高温条件下表现也不错,简直就是材料界的“超级明星”。
咱们得提一提界面缺陷的问题。
这就有点像人际关系中的小矛盾了。
即使是最好的朋友,偶尔也会因为一些小事产生误会。
金属基复合材料界面

金属基复合材料界面金属基复合材料界面是指由金属基体和其他材料相互作用形成的界面。
金属基复合材料是一种重要的结构材料,在航天、航空、汽车制造等领域发挥着重要作用。
而界面则是金属基复合材料性能的关键因素之一,影响着材料的力学性能、热学性能、电学性能等。
金属基复合材料界面的特点主要包括界面强度、界面形态以及界面反应等。
首先,界面强度是指金属基复合材料界面的抗剪强度,决定了材料的强度和韧性。
界面形态则是指金属基复合材料界面的结构形貌,包括界面的平整度、均匀度等。
最后,界面反应是指金属基复合材料界面处发生的化学反应,影响着材料的稳定性和使用寿命。
金属基复合材料界面的研究主要包括界面强度的测试方法以及界面的表征技术。
一般来说,界面强度可以通过剪切测试、拉伸测试等方法进行测量。
剪切测试是将金属基复合材料的界面置于剪切载荷下,通过测量界面之间的滑动距离和加载力来计算界面的剪切强度。
拉伸测试则是将金属基复合材料的界面置于拉伸载荷下,通过测量界面的断裂强度和断裂面积来计算界面的拉伸强度。
界面的表征技术主要包括电子显微镜观察和X射线衍射分析等。
电子显微镜观察可用于观察金属基复合材料界面的形貌和结构特征,如界面的平整度、均匀度以及异质相等。
X射线衍射分析则可以用于分析界面处的晶体结构和相变行为,从而揭示界面反应的机制和影响因素。
金属基复合材料界面的性能调控主要包括三个方面,即界面结构调控、界面化学调控以及界面力学调控。
界面结构调控主要是通过改变复合材料的结构和工艺参数来调控界面的形貌和结构特征,从而改善界面的强度和稳定性。
界面化学调控则是通过引入中间相或质量扩散来调控界面的化学反应,从而提高界面的稳定性和抗氧化性能。
界面力学调控主要是通过改变金属基复合材料的力学性能来调控界面的剪切强度和散射行为,从而提高界面的强度和韧性。
总之,金属基复合材料界面是一种关键的材料界面,影响着金属基复合材料的力学和热学性能。
了解金属基复合材料界面的特点和性能调控方法,对于开发高性能金属基复合材料具有重要意义。
金属基复合材料的界面结合性能研究

金属基复合材料的界面结合性能研究随着科技进步和工业发展,金属基复合材料在各个领域得到了广泛应用。
金属基复合材料由金属基体和增强相组成,通过界面结合强化材料和基体的相互作用,增强了材料的性能。
然而,界面结合性能对于金属基复合材料的整体性能有着重要影响。
本文将探讨金属基复合材料的界面结合性能以及相关研究进展。
首先,界面结合性能是金属基复合材料的重要性能之一。
金属基复合材料的界面结合强度和界面结合能力决定了材料的力学性能、疲劳性能和耐蚀性能等。
好的界面结合性能可以增强材料的强度和韧性,提高材料的负荷承受能力。
因此,研究金属基复合材料的界面结合性能对于提高材料的性能至关重要。
其次,当前金属基复合材料的界面结合性能研究主要集中在几个方面。
首先是材料选择。
在金属基复合材料的界面结合性能研究中,选择合适的金属基体和增强相材料非常重要。
科学家通过研究不同材料的界面结合性能,选择最佳的组合,以提高金属基复合材料的性能。
其次是界面处理。
通过表面处理、化学修饰等方式改善金属基复合材料的界面结合性能,使得界面结合更加牢固。
最后是界面结合机理研究。
通过实验和模拟方法,科学家们深入研究了金属基复合材料界面结合机理的基本原理,为材料的设计和改进提供了理论指导。
此外,金属基复合材料的界面结合性能研究还有一些挑战和难点。
首先是实验方法的选择。
由于界面结合性能的研究需要对界面进行精确的测试和分析,科学家们需要选择合适的实验方法和设备以获得可靠的数据。
其次是界面结合性能与材料性能的相互影响。
界面结合性能的改变可能会影响材料的力学性能、疲劳性能等,因此需要综合考虑界面结合性能和材料性能之间的关系。
最后是界面结合性能的模拟和预测。
由于金属基复合材料的界面结合机理复杂,准确地预测和模拟界面结合性能仍然是一个挑战。
综上所述,金属基复合材料的界面结合性能研究是一个重要而有挑战性的领域。
通过选择合适的材料、优化界面处理方法以及深入研究界面结合机理,可以提高金属基复合材料的性能。
金属基复合材料制备中有害界面反应控制和润湿性增强探讨

摘
要 : 现 阶 段 , 属 陶 瓷 复 合 材 料 研 究 的 重 点 在 于 开 发 新 的 金 属 陶 瓷 体 系 、 善 金 属 陶 瓷 的 界 面 结 构 及 提 高 材 料 在 金 改
的 综 合 性 能 。 而 这 一 切 都 是 以金 属 陶 瓷 的 润 湿 性 及 界 面性 质 为 基 础 的 , 一 直 是 材 料 科 学 工 作 者 全 力探 讨 的 难 点 与 热 点 这 问题 。 在 金 属 陶 瓷 摩 擦 材 料 中 , 属 和 陶 瓷 相 间 的 结 合 强 度 不 足 是 导 致 材 料 磨 损 失 效 的 重 要 原 因 。 金 关 键 词 : 属 基 复 合 材 料 ; 面 处 理 ; 湿 过 程 金 表 润
中图分类 号 : TB 文 献标识码 : A 文 章 编 号 : 6 2 3 9 ( 0 0 1 — 3 10 1 7— 1 8 2 1 ) 50 7 —2
括 物 理 气 相 沉 积 ( VD) 化 学 气 相 沉 积 ( VD) 物 理 化 学 气 P 、 C 、 相 沉 积 ( C ) 表 面 涂 覆 处 理 、 理 化 学 清 洗 ( 某 些 盐 如 P VD 、 物 用 1 1 改 善 陶 瓷 粒 子 的 表 面 状 况 . 氟 W e te研 究 了 固 体 表 面 粗 糙 度 对 润 湿 性 的 影 响 , 碳 酸 钠 、 锆 酸 钾 等 对 陶 瓷 颗 粒 进 行 处 理 去 除 颗 粒 表 面 得 nzl 氧 化 膜 和 污 染 物 , 改 善 陶 瓷 与 金 属 液 的 润 湿 性 ) 可 。 W e te 方 程 为 : nzl R( s d g— o 1 一 o g o O 一 Rc s s) lcs1 oO 1 3 使 金 属 基 合 金 化 . 这 是 目前 使 用 最 广 泛 和 最 有 效 的 方 法 之 一 , 属 基 通 金 式 中 R 粗 糙度 因子 ; ~ 过 添 加 合 金 元 素 来 降 低 熔 融 金 属 的 表 面 张 力 及 其 固 液 界 面 e一 接 触 角 。 1 甚 由式 可 知 : 糙 表 面 的 接 触 角 余 弦 函 数 的 绝 对 值 总 是 能 , 至 通 过 添 加 的 合 金 元 素 在 固 液 界 面 参 加 界 面 反 应 来 粗 比 平 滑 表 面 大 , :> 9。 , 面 粗 化 使 O值 变 大 ; 当 0 即 0 0时 表 而 < 减 小 接 触 角 。 9 。 , 面 粗 化 使 0 变 小 。这 说 明 对 于 可 以 润 湿 的 体 系 , 1 4 提 高 润 湿 过 程 中 的 温 度 O时 表 值 . 固体 表 面粗 化 时 体 系 的 润 湿 性 更 好 。 通 常 情 况 下 升 高 温 度 对 固体 的 表 面 能 没 什 么 影 响 , 但 1 2 对 陶 瓷 粒 子 进 行 表 面 处 理 . 可 以 降 低 熔 融 金 属 的 表 面 能 , 到 改 善 润 湿 性 的 目的 。 另 达 由 Yo n u g氏方 程 得 : 大 a g可 以 减 小 接 触 角 , 对 陶 外 , 高 温 度 还 可 以 破 坏 熔 融 金 属 表 面 的 氧 化 层 , 金 属 与 增 s 可 升 使 瓷 粒 子 进 行 表 面 处 理 , 过 物 理 化 学 的 方 法 来 增 大 og 包 陶 瓷 充 分 接 触 以 促 进 润 湿 。此 外 , 有 提 高 液 相 压 力 , 加 通 s, 还 如
《金属基复合材料》第二章,界面及相容性
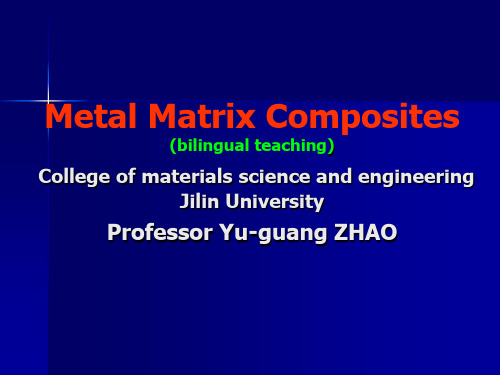
2.2 Definition of interface (界面的定义)
It is a micro-region between matrix and reinforcements where the chemical composition is changed markedly and load can be transferred. It is a new phase which has a certain thickness and structure of which has obvious difference as compared to reinforcement or matrix. So called interfacial phases.
Type of interfacial binding force:(界面结合力有三类) 1) Mechanical combining force —— Friction,
(机械结合——摩擦力)
2) Physical combining force —— Vanderwaals force and hydrogen bond,(物理结合——范德华力和氢键)
metal matrix composite materials cannot be considered in isolation, they are mutually related. Chemical interactions and reactions between the matrix and the reinforcement component determine the interface adhesion, modify the characteristics of the composite components and affect the mechanical characteristics significantly. In high temperature use of MMCs the microstructure has to remain stable for long service periods. Thermal stability and failure is determined by changes in the microstructure and at the interfaces, e.g. reaction and precipitation processes. Thermal stress of MMCs can take place both isothermally and cyclically. The effects show differences. During a cyclic load of monolithic materials, especially at high temperature gradients and cycle speeds, a high probability of failure by thermal fatigue is to be expected, e.g. short-fiber reinforced aluminum alloys possess good thermal shock stability. The formation of the interface between the matrix and the reinforcing phase has a substantial influence on the production and characteristics of the metallic composite materials. The adhesion between both phases is usually determined by the interaction between them. During the production of the molten matrix e.g. by infiltration, wettability becomes significant.
复合材料-第四章复合材料界面

(1)物理因素
例1 粉末冶金制备的W丝/Ni,钨在镍中有很大的固溶度,在1100℃左右使用50小时后,钨丝发生溶解,造成钨丝直径仅为原来的60%,大大影响钨丝的增强作用,如不采取措施,将产生严重后果。为此,可采用钨丝涂覆阻挡层或在镍基合金中添加少量合金元素,如钛和铝,可以起到一定的防止钨丝溶入镍基合金的作用。
如何防止碳在镍中先溶解后析出的问题,就成为获得性能稳定的Cf / Ni的关键。
例2 碳纤维增强镍基复合材料。在800℃高温下,在界面碳先溶入镍,而后又析出,析出的碳是石墨结构,密度增大而在界面留下空隙,给镍提供了渗入碳纤维扩散聚集的位置。而且随温度的提高镍渗入量增加,在碳纤维表层产生镍环,严重损伤了碳纤维,使其强度严重下降。
4.2.1 聚合物基复合材料的界面
1.界面的形成 聚合物基复合材料界面的形成可以分成两个阶段: ①基体与增强纤维的接触与浸润过程; 增强纤维优先吸附能较多降低其表面能的组分,因此界面聚合物在结构上与聚合物基体是不同的。 ②聚合物的固化阶段。聚合物通过物理的或化学的变化而固化,形成固定的界面层。
1
2
复合材料中的界面并不是一个单纯的几何面,而是一个多层结构的过渡区域,这一区域由五个亚层组成。
界面是复合材料的特征,可将界面的机能归为以下几种效应。……P61
复合材料界面设计的原则(总的原则)
界面粘结强度要保证所受的力由基体通过界面传递给增强物,但界面粘结强度过高或过弱都会降低复合材料的强度。
第6章-2 金属基复合材料的界面及其表征
6.2.6.2 界面对金属基复合材料力学性能的影响
界面结合强度对复合材料 的冲击性能影响较大。纤维 从基体中拔出,纤维与基体 脱粘后,不同位移造成的相 对摩擦都会吸收冲击能量, 并且界面结合还影响纤维和 基体的变形能力。
三种复合材料的典型冲击载荷- 时间关系曲线
1-弱界面结合 2-适中界面结合 3-强界面结合
1
界面组成及成分变化
2
界面区的位错分布
3
界面强度的表征
4
界面残余应力的测定
5 界面结构的高分辨观察及其原子模拟
10
6.3.1 界面组成及成分变化
确定界面上有无新相形成是界面表征的主要内容之一。新相可能是 增强体与基体通过扩散反应而在界面处形成的新相, 也可能是基体组 元与相界处杂质元素反应在界面处优先形核而成为新相。 一般情况下常用明场像或暗场像对界面附近区域形貌进行观察, 通 过选区衍射和X射线能谱进行微区结构和成分分析。 当析出物十分细小时, 可采用微衍射和电子能量损失谱来分析其结 构和成分, 电子能量损失谱尤其适合于对C、O等轻元素的分析。可 以准确判知界面析出物的结构、成分和形貌特征。
1、金属基复合材料界面可分成哪些类型?请分别举 例说明不同类型界面的特征。 2、金属基复合材料的界面结合有哪几种?什么样的 界面结合对力学性能更有利?
3
6.2.6 界面对性能的影响
不同类型和用途的金属基复合材料界面的作用和最佳界面结构 性能有很大差别。
纤维增强脆性基体复合材料的微观断裂模型 (a)纤维“桥接” (b)裂纹穿过纤维造成脆断
11
挤压铸造Al18B4O33w /Al-2.5%Mg 复合材料界面 TEM 照片
4Al18B4O33+33Mg = 33MgAl2O4+6Al+16B
第4章复合材料的界面
4
第四页,编辑于星期六:二十一点 三十四分。
界面通常包含以下几个部分:
化学因素:与界面化学作用有关
连续界面反应;纤维侧、基体侧
交换式界面反应;元素交换(基体中至少两种元素)
暂稳态界面反应;氧化层,不稳定
25
第二十五页,编辑于星期六:二十一点 三十四 分。
3、残余应力
物理相容性,主要是热膨胀系数匹配
此外,金属基体要有足够的韧性和强度。
有关金属基复合材料的界面控制研究主要有以下两方面:
如:表面的几何形状、分布状况、纹理结构; 表面吸附气体和蒸气程度;表面吸水情况,杂质存在;
8
第八页,编辑于星期六:二十一点 三十四分。
由于界面区相对于整体材料所占比重甚微,欲单独对某一性能 进行度量有很大困难。
因此常借于整体材料的力学性能来表征界面性能,如层间剪切
强度(ILSS)就是研究界面粘结的良好办法; 再配合断裂形貌分析等即可对界面的其他性能进行研究。
(2)阻断效应 结合适当的界面有阻止裂纹扩展、中断材料破坏 、减缓应力集中的作用。
(3)不连续效应 在界面上产生物理性能的不连续性和界面摩擦 出现的现象,如抗电性、电感应性、磁性、耐热性等。
(4)散射和吸收效应 光波、声波、热弹性波、冲击波等在界 面产生散射和吸收。
(5)诱导效应 一种物质(通常是增强物)的表面结构使另一种(通 常是聚合物基体)与之接触的物质的结构由于诱导作用而发生改变 ,由此产生一些现象,如强的弹性、低的膨胀性、耐冲击性7和耐
金属基复合材料界面特征与力学性能
工业技术96 2015年35期金属基复合材料界面特征与力学性能肖伟利山东核电设备制造有限公司,山东烟台 265118摘要:随着金属基复合材料应用要求的不断提高,研究其界面特征与力学性能凸显出重要意义。
本文首先对相关内容做了概述,分析了复合材料微结构拓扑优化,并结合相关实践经验,研究了MMC的制备工艺和制备方法,提出了个人看法。
关键词:金属基复合材料;界面特征;力学性能中图分类号:TB333 文献标识码:A 文章编号:1671-5810(2015)35-0096-011 前言作为金属基复合材料应用中的重要工作,对其界面特征与力学性能的研究在近期得到了广泛关注。
该项课题的研究,将会更好地提升对其界面特征与力学性能的掌控水平,从而有效优化金属基复合材料在实际应用中的整体效果。
2 概述金属基复合材料界面,乃至所有复合材料界面都是外载荷从复合材料基体传递给增强体的主要媒介。
复合材料界面的性质在很大程度上决定复合材料的性能。
对金属基复合材料来说,其增强体常为陶瓷粒子或金属间化合物相吸各种纤维,所以其界面的原子结构、化学成分和原子键结合类型不同于界面两侧的材料,且在界面上更容易发生化学反应。
尽管在界面上产生一个反应层是增强体与基体牢固结合所需要的,但反应层过量生长将直接影响复合材料的力学性能。
实际上,金属基复合材料的屈服;断裂、疲劳强度以及裂纹扩展行为等均与界面反应层厚度有关系,再者,其使用条件的选择,使用寿命如何也均主要依赖界面特性。
所以,只有深入了解金属基复合材料的界面微结构、界面反应和界面稳定性等界面特性,建立界面结构特性因素与力学性能指标之间的数学模型,才能在深层、次层上阐明界面特征与力学性能间的关系,以达到利用“界面工程”发展新型高性能复合材料的目的。
3 复合材料微结构拓扑优化研究结构拓扑优化是结构形状优化的发展,是布局优化的一个方面。
当形状优化逐渐成熟后,结构拓扑优化这一新的概念就开始发展,现在拓扑优化正成为国际结构优化领域一个最新的热点。
金属基复合材料的界面微观结构与力学性能研究
金属基复合材料的界面微观结构与力学性能研究金属基复合材料由金属基体和强化相组成,具有优异的力学性能和良好的工程应用前景。
在金属基复合材料的力学性能中,复合界面的微观结构起着关键作用。
本文将探讨金属基复合材料的界面微观结构与力学性能的研究。
1. 金属基复合材料的界面结构金属基复合材料的界面结构是指金属基体与强化相之间的结构特征。
界面的微观结构决定了力学性能的优劣。
其中,界面的结晶度、化学成分均会影响力学性能。
以铝基复合材料为例,硅化物在金属基体中的分布方式、界面的结晶度以及界面的塑性变形等因素均对力学性能有着重要影响。
2. 界面结构与材料强度的关系界面结构对材料的强度具有重要影响。
研究表明,界面结晶度高、接触面积大的复合材料具有更高的强度。
这是因为结晶度高的界面可以有效抑制裂纹扩展,提高材料的抗拉强度。
另外,界面的接触面积大可以增加原子间的相互作用力,从而增加材料的韧性。
3. 界面结构与材料的塑性变形能力除了影响材料的强度外,界面结构还会对材料的塑性变形能力产生影响。
界面能够阻止晶体滑移,从而抑制材料的塑性变形。
如果界面结晶度低,会导致界面的塑性变形更易发生,从而影响材料的韧性和延展性。
因此,界面的结晶度对于金属基复合材料的塑性变形能力具有重要意义。
4. 界面结构与疲劳性能的关系疲劳性能是金属基复合材料工程应用中需要考虑的重要因素。
界面结构对材料的疲劳性能影响较大。
较为均匀的界面分布可以有效地抑制裂纹扩展,提高材料的疲劳寿命。
此外,良好的界面结晶度有助于维持材料的结构完整性,从而提高疲劳性能。
综上所述,金属基复合材料的界面微观结构与力学性能有着密切的关系。
界面结构的优化可以提高材料的强度、塑性变形能力和疲劳性能。
在今后的研究中,应重点关注界面结构的调控与优化,以进一步提高金属基复合材料的力学性能。
- 1、下载文档前请自行甄别文档内容的完整性,平台不提供额外的编辑、内容补充、找答案等附加服务。
- 2、"仅部分预览"的文档,不可在线预览部分如存在完整性等问题,可反馈申请退款(可完整预览的文档不适用该条件!)。
- 3、如文档侵犯您的权益,请联系客服反馈,我们会尽快为您处理(人工客服工作时间:9:00-18:30)。
华东理工大学2012-2013学年第二学期《金属基复合材料》课程论文2013.6班级复材101 学号10103638 温乐斐开课学院材料学院任课教师麒成绩浅谈金属基复合材料界面特点、形成原理及控制方法摘要金属基复合材料都要在基体合金熔点附近的高温下制备,在制备过程中纤维、晶须、颗粒等增强体与基体将发生程度不同的相互作用和界面反应,形成各种结构的界面。
界面结构和性能对金属基复合材料的性能起着决定性作用。
深入研究和掌握界面反应和界面影响性能的规律,有效地控制界面的结构和性能,是获得高性能金属基复合材料的关键。
本文简单讨论一下金属基复合材料的界面反应、界面对性能的影响以及控制界面反应和优化界面结构的有效途径等问题。
前言由高性能纤维、晶须、颗粒与金属组成的金属基复合材料具有高比强度、高比模量、低热膨胀、耐热耐磨、导电导热等优异的综合性能有广阔的应用前景,是一类正在发展的重要高技术新材料。
随着金属基复合材料要求的使用性能和制备技术的发展,界面问题仍然是金属基复合材料研究发展中的重要研究方向。
特别是界面精细结构及性质、界面优化设计、界面反应的控制以及界面对性能的影响规律等,尚需结合材料类型、使用性能要求深入研究。
金属基复合材料的基体一般是金属、合金和金属间化合物,其既含有不同化学性质的组成元素和不同的相,同时又具有较高的熔化温度。
因此,此种复合材料的制备需在接近或超过金属基体熔点的高温下进行。
金属基体与增强体在高温复合时易发生不同程度的界面反应;金属基体在冷凝、凝固、热处理过程中还会发生元素偏聚、扩散、固溶、相变等。
这些均使金属基复合材料界面区的结构十分复杂,界面区的结构及组成明显不同于基体和增强体,其受到金属基体成分、增强体类型、复合上艺参数等多种因素的影响。
在金属基复合材料界上出现材料物理性质(如弹性模量、线胀系数、热导率、热力学参数)和化学性质等的不连续性,使增强体与基体金属形成了热力学不平衡的体系。
因此,界面的结构和性能对金属基复合材料中的应力和应变的分布、导热和导电、热膨胀性能、载荷传递及断裂过程都起着决定性作用。
针对不同类型的金属基复合材料,深入研究界面精细结构、界面结构和性能优化与控制途径,以及界面结构性能的稳定性等,是金属基复合材料发展中的重要容。
图1:制备关系图正文部分1.金属基复合材料界面特点与形成原因由于金属基复合材料必须在高温下制备,基体与增强体之间的界面反应:溶解、扩散、元素偏聚等很难避免,界面反应及作用的程度与基体、增强体的类型、化学、物理性质及制备工艺参数密切相关。
集体和增强体一旦选定,制备过程就决定界面结构和性能,特别是制备时的温度和高温下暴露的时间(保温及冷却过程)。
温度越高,停留时间越长,界面反应及作用越严重。
比较好的金属基复合材料界面应该是起到良好地粘结基体与增强材料但是又不能过分发生反应,不能产生大量的化合物、气泡以及出现应力集中等不良状况。
界面的结构和性能对复合材料中应力、应变分布、导热、导电、热膨胀性能、载荷的有效传递、断裂过程均起着决定性的作用。
金属基复合材料界面除了机械结合、溶解与润湿结合、反应结合、交换反应结合和混合结合外,还有氧化物结合。
(1)机械结合:基体与增强体之间仅仅依靠纯粹的粗糙表面相互嵌入(互锁)作用进行连接,成为机械结合或机械互锁。
纤维的表面粗糙度有助于基体的嵌合,基体的收缩有助于对纤维箍紧。
事实上,纯粹的机械结合(即无任何化学作用)是不存在的。
基体与增强体之间总会有弱的德华力存在,故机械结合更确切地将是机械结合占优势的一种结合而大多情况下是机械结合与反应结合并存的一种混合结合。
另外,机械结合只有当平行于界面施加作用力时候,其传递载荷才是有效的。
瓷基复合材料中的界面,大多以机械结合为主。
机械结合的特点:1.界面粗糙度对结合力起决定作用,因此表面刻蚀的增强体比光滑表面构成的复合材料强度大2-3倍;2.载荷平行于界面时承担的应力大,而垂直与界面时承担的应力非常小。
(2)溶解与润湿结合:在复合材料制造的过程中基体与增强体之间首先发生润湿,然后相互溶解,所形成的结合方式称为溶解与润湿结合。
润湿作用通常是主要的,而溶解是次要的,因为在高温下原子的扩散时间很短。
在这种情况下,组分之间的相互作用出现在电子等级上,即短程围,这意味着这些组分将进入原子尺度的接触。
溶解与润湿结合的特点:作用力短,只有几个原子距离;增强体存在氧化物膜,使得增强体与基体不润湿,需要破坏氧化层才能使增强体与基体润湿并产生一定的结合力;在增强体表面能很小时,采用表面镀膜层处理(如CVD)使两相之间的接触角小于90°,产生润湿,产生一定的结合作用力。
(3)反应结合:基体与纤维间发生化学反应,在界面上形成一种新的化合物而产生的结合称为反应结合。
这是一种最复杂、最重要的结合方式。
反应结合受扩散控制,能够发生反应的两种元素或化合物,只有通过相互接触和相互扩散才能发生某种化学反应。
扩散包括反应物质在组分物质中的扩散(反应初期)和在反应物质中的扩散(反应后期)。
不能笼统认为基体与纤维产生的反应都会产生反应结合,只有当反应后能产生界面结合的体系才能算是反应结合,如果反应后界面产生大量脆性化合物,造成界面弱化,这不仅不能称为反应结合,反而应称为反应阻碍结合。
要实现良好的反应结合,必须选择最佳的制造工艺参数(温度、压力、时间、气氛等)来控制界面反应的程度。
(4)交换反应结合:当增强体或基体成分含有两种或两种以上元素时,除发生界面反应外,在增强体、基体与反应产物之间还会发生元素交换。
所产生的结合称为交换反应结合。
交换反应结合的典型例子是硼纤维/钛合金复合材料系。
(5)混合结合:当由增强体和基体金属组成复合材料时,某些金属基体表面存在致密的氧化膜。
此氧化膜常常逐渐被某种工艺因素或化学反应破坏,使增强体与基体之间的界面从非化学结合向化学结合过渡,在过渡过程中,界面既存在机械结合又存在化学结合,成为混合结合。
混合结合的典型例子是硼纤维增强铝合金(6061)复合材料[B f(25%)Al]系。
该复合材料一般采用热压扩散结合方式制造,制造温度约为550℃。
在此温度和压力下,硼纤维与铝纤维基体的接触时间约为0.5h。
经过研究发现,将B f/Al 复合材料在550℃加热0.5h、5h、12h和165h后,拉伸强度分别为593MPa、524MPa、442MPa和317MPa。
以上结果表明,拉伸强度随着时间增加而减少;这是因为随着时间延续,铝的氧化膜逐渐破坏,B与Al之间出现机械结合过渡到机械结合与反应结合并存;B与Al之间的化学反应导致硼纤维的强度降低,从而引起复合材料性能下降。
(6)氧化物结合:氧化物结合是指当采用的增强体是某种氧化物时,其与基体间发生反应生成另一种氧化物,所产生的结合。
具有氧化物结合的体系有Al2O3f/Ni、Al2O3f/Cu、SiO2f/Al等。
氧化物增强体与基体反应与否,取决于形成基体氧化物的自由能,同时,还要看气氛中氧的来源情况。
一般情况下,金属基复合材料是以界面化学结合为主,有时也会有两种或两种以上界面结合方式并存的现象。
另外,即使对于相同的组分、相同的工艺制备的复合材料,对应于不同的部位其界面结构也有较大差别。
通常将金属基复合材料界面分成Ⅰ、Ⅱ、Ⅲ三种类型:Ⅰ型界面代表增强体与基体金属既不溶解也不反应(包括机械结合和氧化物结合);Ⅱ型界面代表增强体与基体金属之间可以溶解;但不反应(即溶解与润湿结合);Ⅲ型界面表示增强体与基体之间发生反应并形成化合物(包括交换反应结合和混合结合)见表1所示:表1 金属基复合材料体系的界面类型①表示伪Ⅰ型界面。
②该体系在低温时生成Ni4V。
③当两组元溶解度极低时划为Ⅰ型。
表1中伪Ⅰ型界面的含义是:按热力学分析该种体系的增强体与基体之间应该发生化学反应,但基体金属的氧化膜阻止反应的进行,反应能否进行,取决于氧化膜的完整程度。
当氧化膜尚完整时,属于Ⅰ型界面;当工艺过程中温度过高或保温时间过长而使机体氧化膜破坏时,组分之间将发生化学反应,变为Ⅲ型界面。
具有伪Ⅰ型界面特征的复合材料系在工艺上宜采用固态法(加热法、粉末冶金、扩散结合),而不宜采用液态浸渗法,以免变为Ⅲ型界面而损伤增强体。
2. 金属基复合材料界面微观结构金属基复合材料界面是指金属基体与增强体之间的化学成分和物理、化学性质明显不同,构成彼此结合并能起传递载荷作用的微小区域。
界面微区的厚度可以从一个原子层到几个微米。
由于金属基体与增强体的类型、组分、晶体结构、化学物理性质有很大差别,以及在高温制备过程中有元素的扩散、偏聚、相互反应等,从而形成复杂的界面结构。
界面区包括了基体与增强体的接触连接面、基体与增强体相互作用生成的反应产物与接触连接面、基体与增强体相互作用生成的反应产物和析出相、增强体的表面涂层作用区、元素的扩散和偏聚区、近界面的高密度位错区等。
金属基复合材料中的典型结构主要有以下几种:(1)有界面反应产物的界面微结构:多数金属基复合材料在制备过程中发生不同程度的界面反应。
轻微的界面反应能有效地改善金属基体与增强体的浸润和结合,是十分有利的;严重界面反应将造成增强体的损伤和形成脆性界面相等,十分有害;界面反应通常是在局部区域中发生的,形成颗粒、棒状、片状的反应产物,而不是同时在增强体和基体相接触的界面上发生层状物。
只有严重的界面反应才可能形成界面反应层。
碳(石墨)/铝复合材料是研究发展最早的性能优异的复合材料之一。
碳(石墨)纤维的密度小(1.8~2.1g/cm3)、强度高(3500~7000MPa)、模量高(250~910GPa)、导热性好、线膨胀系数接近于零。
用它来增强铝、镁组成的复合材料,综合性能优异。
但是碳(石墨)纤维与铝基体在500℃以上会发生界面反应。
有效地控制界面反应十分重要。
当制备工艺参数控制合适时,界面反应轻微,界面形成少量细小的Al4C3。
制备温度过高、冷却速度过慢将会发生严重的界面反应,形成大量条状的Al4C3。
碳(石墨)/铝、碳(石墨)/镁、氧化铝/镁、硼/铝、碳化硅/铝、碳化硅/钛、硼酸铝/铝等一些主要类型的金属基复合材料,都存在界面反应的问题。
它们的界面结构中一般都有界面反应产物。
(2)有元素偏聚和析出相的界面微结构:金属基复合材料的基体选用金属合金,很少选用纯金属。
基体合金中含有各种金属化合物析出相,如铝合金中加入铜、镁、锌等元素会生成细小的Al2Cu、Al2CuMg、Al2MgZn等时效强化相。
由于增强体表面吸附作用,基体金属中合金元素在增强体的表面富集,为在界面区生成析出相创造了有利条件。
在碳纤维增强铝或镁复合材料中均可发现界面上有Al2Cu、Mg17Al12化合物析出相存在。
(3)增强体与集体直接进行原子结合的界面结构:增强体与基体直接进行原子结合,形成清洁、平直界面,界面上既无反应产物也无析出相。