挤出成型工艺介绍设备
挤出机和挤出成型工艺

挤出成型工艺和挤出机1.挤出成型工艺1.1 挤出成型工艺:在挤出机中通过加热、加压而使物料以流动状态持续通过口模(即机头)成型的方式称挤出成型或挤塑。
是塑料重要的成型方式之一。
1.2 挤出成型的特点:①设备本钱低,制造容易,投资少,上马快。
②生产效率高,挤出机的单机产量较高,产率一般在几千克~5吨/小时。
③持续化生产。
能制造任意长度的薄膜、管、片、板、棒、单丝、异型材和塑料与其他材料的复合制品等。
④生产操作简单,工艺控制容易,易于实现自动化。
占地面积小,生产环境清洁,污染少。
⑤能够一机多用。
挤出机也能进行混合、造粒。
1.3 挤出成型可分为两个阶段:第一阶段是使固态塑料变成粘性流体(即塑化),并在加压情形下,使其通过特殊形状的口模,而成为截面与口模形状相仿的持续体。
第二阶段则是用适当的处置方式使挤出的持续体失去塑性状态而变成固体,即取得所需制品。
1.4 挤出成型工艺分类:干法(熔融法)—通过加热使塑料熔融成型①塑化方式湿法(溶剂法)—用溶剂将塑料充分软化成型(CN、CA及纺丝)持续式:螺杆式挤出机,借助螺杆旋转产生的压力和剪切力,使物料充分塑化和均匀混合,通过口模而成型,可进行连续生产。
②加压方式间歇式:柱塞式挤出机,借助柱塞压力,将事先塑化好的物料挤出口模而成型。
仅用于粘度特别大,流动性极差的塑料。
如:PTFE,成型温度下,粘度为1010~1014泊(一般熔融塑料的粘度范围为102~108泊);HUMWPE等。
柱塞可提供很大的压力,但形状不能太复杂,不能加分流梭。
间歇式生产。
2. 挤出设备塑料的挤出,绝大多数都是热塑性塑料,而且又是采用持续操作和干法塑化的。
故在设备方面多用螺杆式挤出机。
螺杆式挤出机有单、双(或多螺杆)之分。
大部份用单螺杆挤出机,只是粉料,RPVC 95%以上都用双螺杆挤出机。
2.1 单螺杆挤出机2.1.1 单螺杆挤出机的组成:由传动系统、加料系统、挤压系统、机头和口模和加热与冷却系统等组成。
不同的材料及成型工艺的主要设备及其作用

不同的材料及成型工艺的主要设备及其作用一、概述在制造业中,材料和成型工艺是产品制造的关键因素。
随着科技的不断进步,越来越多的材料和成型工艺被应用于生产过程中。
为了实现高效、高质的制造,主要设备也经历了不断的改进和发展。
本文将对不同的材料及成型工艺的主要设备及其作用进行详细的介绍。
二、材料分类及对应设备1.金属材料金属材料在制造业中占有重要地位,常用的金属材料包括钢铁、铜、铝等。
针对这些金属材料的加工,主要设备包括:熔炼炉、轧机、冲压机、焊接机等。
这些设备的作用是熔炼金属、轧制金属板材、冲压金属零件以及焊接金属部件等。
2.塑料材料塑料材料因其轻便、耐腐蚀等特性广泛应用于各个领域。
针对塑料材料的加工,主要设备包括:注塑机、挤出机、热压成型机等。
注塑机的作用是将熔融状态的塑料注入模具中,冷却后得到所需形状的塑料零件;挤出机则是通过螺杆旋转产生的压力,将熔融状态的塑料挤出成连续的型材;热压成型机则是利用热压工艺将塑料片材热压成所需形状的制品。
3.复合材料复合材料是由两种或两种以上材料组成的新型材料,具有优异的性能。
针对复合材料的加工,主要设备包括:预浸料设备、热压罐、缠绕机等。
预浸料设备的作用是将树脂与纤维预先混合,制成预浸料;热压罐的作用是将复合材料在高温高压下固化成型;缠绕机则是通过将纤维缠绕在芯模上,制成所需形状的复合材料制品。
三、成型工艺与设备的作用1.注塑成型工艺与注塑机注塑成型工艺是一种常见的塑料加工工艺,主要设备为注塑机。
注塑机的作用是将熔融状态的塑料注入模具中,经过冷却固化后开模取出塑料制品。
注塑成型工艺的特点是生产效率高、适用范围广,可以生产各种形状和尺寸的塑料制品。
2.挤出成型工艺与挤出机挤出成型工艺是一种常见的塑料加工工艺,主要设备为挤出机。
挤出机的作用是将塑料原料加热熔融,通过螺杆将熔融状态的塑料推挤出模头,冷却后形成连续的型材或管材。
挤出成型工艺的特点是连续生产、生产效率高,可以生产各种规格的型材和管材。
挤出成型设备介绍和特性曲线

挤出成型过程可分为如下三个阶段:
• 1、塑化阶段 在挤出机上进行塑料的加热和混炼, 使固态原料变为均匀的粘性流体。
• 2、成型阶段 在挤出机螺杆的作用下,熔融塑料 以一定的压力和速度连续通过装在挤出机上的成型 机头,获得一定的断面形状。
• 3、定形阶段 通过冷却等方法使熔融塑料已获取 的形状固定下来,成为固态制件。
• 定型装置:将从机头中挤出的塑料的既定形状稳 定下来.并对其进行精整,从而得到更为精确的 截面形状、尺寸和光亮的表面。通常采用冷却和 加压的方法达到这一目的。
• 冷却装置:由定型装置出来的塑料在此得到充分 的冷却,获得最终的形状和尺寸。
• 牵引装置:其作用为均匀地牵引制品。并对制品 的截面尺寸进行控制,使挤出过程稳定地ቤተ መጻሕፍቲ ባይዱ行。
• 经历的形态:玻璃态----粘流态----高弹态----玻璃态
3、控制系统
• 挤出机的控制系统:它由各种电器、仪表和执行机 构组成。根据自动化水平的高低,可控制挤出机的 主机、辅机的拖动电机、驱动油泵、油(汽)缸和 其它各种执行机构按所需的功率、速度和轨迹运行, 以及检测、控制主辅机的温度、压力、流量,最终 实现对整个挤出机组的自动控制和对产品质量的控 制。
挤出成型设备介绍和特性曲线
动画演示
§4-1 概 述
1.定义:挤出成型又称挤塑(挤压模塑),在挤出机的 螺杆或柱塞的挤压作用下,使高聚物的熔体(或粘 流体),通过一定形状的口模,而成为具有恒定截 面的连续型材的一种成型方法。
2.应用: 塑料挤出成型:管材、板材、片材、薄膜、挤出吹 塑。主要是热塑性塑料的挤出,现也有热固性。
§4-2-2 挤出成型基本原理
挤出成型: 是将物料送入加热的机筒与旋转着的螺杆之间进
塑料挤出成型设备有哪些种类
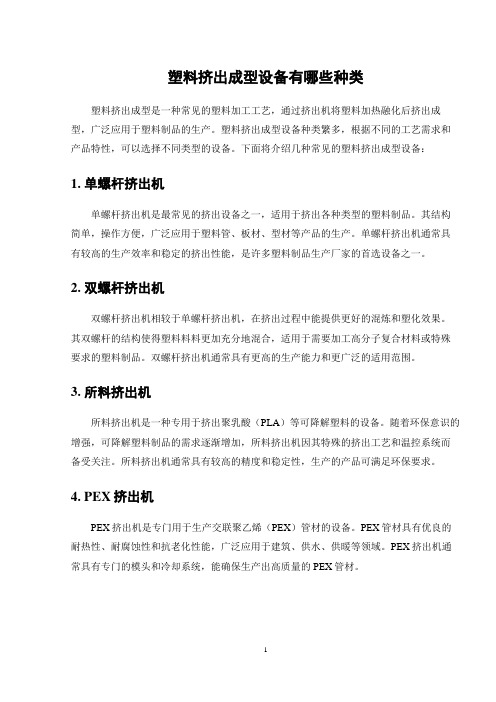
塑料挤出成型设备有哪些种类塑料挤出成型是一种常见的塑料加工工艺,通过挤出机将塑料加热融化后挤出成型,广泛应用于塑料制品的生产。
塑料挤出成型设备种类繁多,根据不同的工艺需求和产品特性,可以选择不同类型的设备。
下面将介绍几种常见的塑料挤出成型设备:1. 单螺杆挤出机单螺杆挤出机是最常见的挤出设备之一,适用于挤出各种类型的塑料制品。
其结构简单,操作方便,广泛应用于塑料管、板材、型材等产品的生产。
单螺杆挤出机通常具有较高的生产效率和稳定的挤出性能,是许多塑料制品生产厂家的首选设备之一。
2. 双螺杆挤出机双螺杆挤出机相较于单螺杆挤出机,在挤出过程中能提供更好的混炼和塑化效果。
其双螺杆的结构使得塑料料料更加充分地混合,适用于需要加工高分子复合材料或特殊要求的塑料制品。
双螺杆挤出机通常具有更高的生产能力和更广泛的适用范围。
3. 所料挤出机所料挤出机是一种专用于挤出聚乳酸(PLA)等可降解塑料的设备。
随着环保意识的增强,可降解塑料制品的需求逐渐增加,所料挤出机因其特殊的挤出工艺和温控系统而备受关注。
所料挤出机通常具有较高的精度和稳定性,生产的产品可满足环保要求。
4. PEX挤出机PEX挤出机是专门用于生产交联聚乙烯(PEX)管材的设备。
PEX管材具有优良的耐热性、耐腐蚀性和抗老化性能,广泛应用于建筑、供水、供暖等领域。
PEX挤出机通常具有专门的模头和冷却系统,能确保生产出高质量的PEX管材。
结语以上介绍的仅是几种常见的塑料挤出成型设备,随着科技的发展和工艺的创新,挤出设备的类型和性能也在不断提升。
根据生产需求和产品特性,选择合适的挤出设备至关重要,只有选择适合的设备才能更好地满足生产需求,提高生产效率,降低成本,生产出更优质的塑料制品。
混凝土挤出成型方法
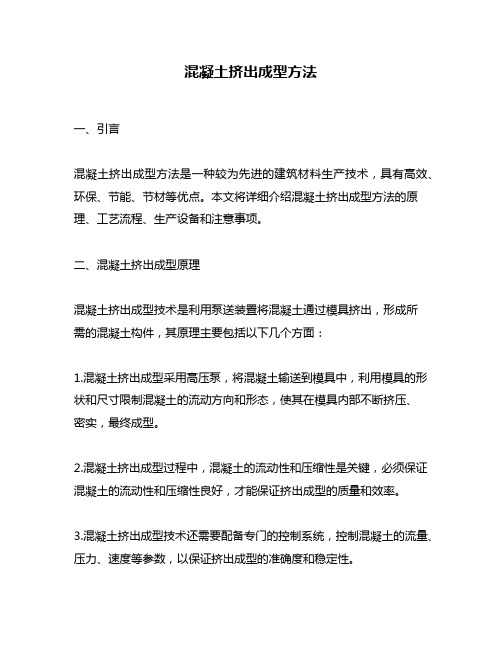
混凝土挤出成型方法一、引言混凝土挤出成型方法是一种较为先进的建筑材料生产技术,具有高效、环保、节能、节材等优点。
本文将详细介绍混凝土挤出成型方法的原理、工艺流程、生产设备和注意事项。
二、混凝土挤出成型原理混凝土挤出成型技术是利用泵送装置将混凝土通过模具挤出,形成所需的混凝土构件,其原理主要包括以下几个方面:1.混凝土挤出成型采用高压泵,将混凝土输送到模具中,利用模具的形状和尺寸限制混凝土的流动方向和形态,使其在模具内部不断挤压、密实,最终成型。
2.混凝土挤出成型过程中,混凝土的流动性和压缩性是关键,必须保证混凝土的流动性和压缩性良好,才能保证挤出成型的质量和效率。
3.混凝土挤出成型技术还需要配备专门的控制系统,控制混凝土的流量、压力、速度等参数,以保证挤出成型的准确度和稳定性。
三、混凝土挤出成型工艺流程混凝土挤出成型的工艺流程主要包括原料准备、混凝土配制、模具设计、挤出成型和后处理等环节。
1.原料准备:混凝土挤出成型所用原料主要包括水泥、砂、石子、添加剂等,需要进行准确的称量和混合,以确保混凝土的配合比例和质量。
2.混凝土配制:将混凝土原料按照一定比例混合,加水搅拌成糊状物,保证混凝土的均匀性和流动性。
3.模具设计:根据工程需要和混凝土特性,设计合适的模具形状和尺寸,以实现所需的混凝土构件。
4.挤出成型:利用高压泵将混凝土输送到模具中,通过模具的形状和尺寸限制混凝土的流动方向和形态,使其在模具内部不断挤压、密实,最终成型。
5.后处理:将挤出成型的混凝土构件进行表面处理、养护等,确保其质量和使用寿命。
四、混凝土挤出成型生产设备混凝土挤出成型生产设备主要包括高压泵、模具、控制系统等。
1.高压泵:高压泵是混凝土挤出成型的核心设备,其作用是将混凝土输送到模具中,保证混凝土的流量、压力、速度等参数,以实现挤出成型。
2.模具:模具是混凝土挤出成型的重要组成部分,其作用是限制混凝土的流动方向和形态,使其在模具内部不断挤压、密实,最终成型。
塑料挤出成型技术
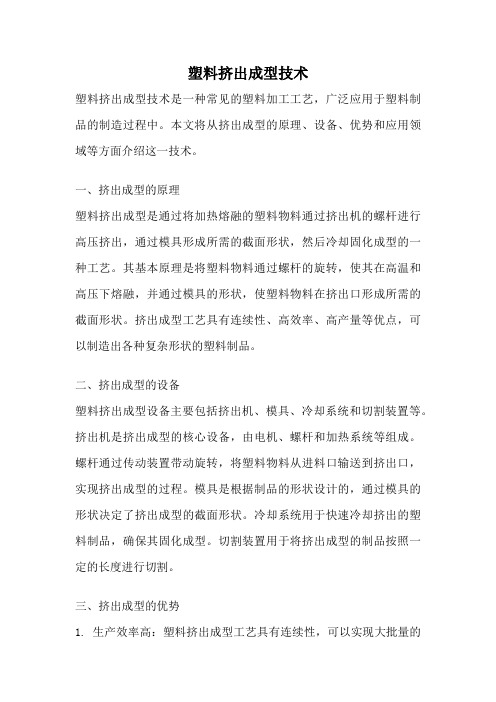
塑料挤出成型技术塑料挤出成型技术是一种常见的塑料加工工艺,广泛应用于塑料制品的制造过程中。
本文将从挤出成型的原理、设备、优势和应用领域等方面介绍这一技术。
一、挤出成型的原理塑料挤出成型是通过将加热熔融的塑料物料通过挤出机的螺杆进行高压挤出,通过模具形成所需的截面形状,然后冷却固化成型的一种工艺。
其基本原理是将塑料物料通过螺杆的旋转,使其在高温和高压下熔融,并通过模具的形状,使塑料物料在挤出口形成所需的截面形状。
挤出成型工艺具有连续性、高效率、高产量等优点,可以制造出各种复杂形状的塑料制品。
二、挤出成型的设备塑料挤出成型设备主要包括挤出机、模具、冷却系统和切割装置等。
挤出机是挤出成型的核心设备,由电机、螺杆和加热系统等组成。
螺杆通过传动装置带动旋转,将塑料物料从进料口输送到挤出口,实现挤出成型的过程。
模具是根据制品的形状设计的,通过模具的形状决定了挤出成型的截面形状。
冷却系统用于快速冷却挤出的塑料制品,确保其固化成型。
切割装置用于将挤出成型的制品按照一定的长度进行切割。
三、挤出成型的优势1. 生产效率高:塑料挤出成型工艺具有连续性,可以实现大批量的生产,提高生产效率。
2. 制品质量稳定:挤出成型的制品形状稳定,尺寸精确,质量可靠。
3. 适用范围广:挤出成型工艺适用于各种塑料,可以制造出各种形状的制品,如管材、板材、型材等。
4. 设备投资少:相对于其他塑料加工工艺,挤出成型设备投资较少,生产成本较低。
5. 可塑性强:挤出成型的塑料物料可根据需要选择,可以加入各种填充剂、增强剂等,增加塑料的性能。
四、挤出成型的应用领域塑料挤出成型技术广泛应用于建筑、包装、汽车、电子、家电等行业。
在建筑行业中,挤出成型制造的塑料管材、型材、板材等被广泛应用于室内装饰、给排水系统、电线电缆等方面。
在包装行业中,挤出成型用于制造各种塑料包装盒、瓶子、袋子等。
在汽车行业中,挤出成型的塑料制品用于汽车内饰、外饰等部件。
在电子和家电行业中,挤出成型的塑料制品用于电线电缆的保护管、电器外壳等。
6.5挤出成型工艺详解

问题 挤出成型原理
牵引速度略大于挤出速度 不同的塑件,牵引速度不同。
挤出成型工艺
挤出成型设备
产品工艺过程
思考与练习
2024年8月2日
第六章 塑料成型技术
四、挤出成型工艺条件
问题 挤出成型原理 挤出成型工艺 挤出成型设备 产品工艺过程 思考与练习
温度 压力
挤出速度 牵引速度
2024年8月2日
第六章 塑料成型技术
1、掌握挤出成型的特点; 2、熟悉挤出机的结构和主要部件的作用; 3、掌握挤出理论中影响生产和产品质量的因素; 4、熟悉管材、薄膜、板与片、拉伸膜的工艺。
第六章 塑料成型技术
6.3 挤出成型
一、概述
2024年8月2日
问题 挤出成型原理
1.挤出成型原理:将塑料塑化后使其在一定压力下通过某种 模具而形成截面形状与此模具相仿的连续体,并在固化后保 持该形状的成型方法。
•
与金属管相比,塑料管材有以下优点:相对密
度小,仅为金属的1/5、1/8,耐化学腐蚀性好,
电器绝缘性优良。耐磨性好。塑料管广泛用作各种
液体、气体输送管,尤其是某些腐蚀性掖体和气体,
如自来水管、排行管、农业排灌用管、化工管道、
石油管、煤气管等。
思考与练习
第六章 塑料成型技术
问题 挤出成型原理 挤出成型工艺 挤出成型设备 产品工艺过程 思考与练习
减小压力波动。
第六章 塑料成型技术
2024年8月2日
问题 挤出成型原理 挤出成型工艺 挤出成型设备 产品工艺过程 思考与练习
3.挤出速度 单位时间内由挤出机头和口模中挤出的塑化好
的物料量或塑件长度。它表示挤出能力的高低。 影响因素:机头、螺杆和料筒的结构、螺杆转速、 加热冷却系统的结构和塑料的性能 4.牵引速度 牵引速度与挤出速度相当,可略大于挤出速度。
挤出机工艺流程

挤出机工艺流程
《挤出机工艺流程》
挤出机是一种常用的塑料加工设备,它可以将塑料通过高温高压的方式挤出成型,被广泛应用于塑料制品的生产过程中。
下面将介绍挤出机的工艺流程。
首先是原料的准备。
塑料颗粒经过预处理后,被放入挤出机的进料口。
然后在挤出机内部通过螺杆的旋转和高温的加热下,原料被加热熔化,并转化为流动状态。
接着是挤出成型。
在螺杆的作用下,将熔化的原料从挤出机的模头中挤出,通过模头内的成型道口,形成了理想的截面形状,并在冷却水槽中迅速冷却固化。
之后是冷却与切割。
冷却固化后的塑料挤出件,经过牵引辊的牵引输送至切断装置处,被切割成特定长度的成品。
最后就是收集和包装。
切割好的成品被收集起来,进行质量检验和包装,最终成为可供销售的塑料制品。
整个过程中,挤出机的操作需要严格控制温度、压力和速度等参数,以确保产品的质量和稳定性。
同时,不同的原料和产品要求会有不同的工艺流程和工艺参数,生产过程中需要根据实际情况进行调整。
总之,挤出机工艺流程是一个复杂的加工过程,需要操作者具备专业的技能和经验,才能保证生产出优质的塑料制品。
- 1、下载文档前请自行甄别文档内容的完整性,平台不提供额外的编辑、内容补充、找答案等附加服务。
- 2、"仅部分预览"的文档,不可在线预览部分如存在完整性等问题,可反馈申请退款(可完整预览的文档不适用该条件!)。
- 3、如文档侵犯您的权益,请联系客服反馈,我们会尽快为您处理(人工客服工作时间:9:00-18:30)。
二、口模
口模是安装在挤出机末端的有孔部件,它使挤出物形成规定的横截面形 状。口模连接件是位于口模和料筒之间的那部分,这种组合装置的某些部分有时 称作机头或口模体。由于许多口模的特性是相当复杂的,口模和口模体(机头) 实际上是一回事。因此习惯上把安装在料筒末端的整个组合装置称为口模,但也 有称作机头的。
三、辅助设备
辅助设备是挤出生产不可缺少的部分,它与制品类型、质量和自动程度 有关,一般包括以下三类: ①挤出前处理物料的设备(如预热、干燥等); ②处理挤出物的设备(如冷却、定型、牵引、卷取、切割和检查等); ③控制生产条件的设备(如温度、电动机、螺杆转速和机头压力的控制仪表或微 型计算机)。
将挤出机、口模和辅助设备合理组合,即构成某一制品的生产线,由于 自动化程度和技术水平不同,其形式是多种多样的。
四、单螺杆挤出原理
为使挤出机达到稳定的产量和质量,一方面,沿螺槽方向一截面的质量 流率必须保持恒定且等于产量;另一方面,熔体的输送速率应等于物料的熔化速 率。如果不能实现这些条件,就会引起产量波动和温度波动。 (一)、固体输送
二、口模
凡是成形段横截面具有平行缝隙特征的机头,叫板材与片材挤出机头, 也称平缝形挤出机头。主要用于塑料板材、片材和平膜加工。
由挤出机提供的塑料熔体,从圆形逐渐过渡到平缝形,并要求在其出口 横向全宽方向上,熔体流速均匀一致,这是板材与片材挤出机头设计的关键。其 次,要求塑料熔体流经整个机头流道的压降要适度;以及停留时间要尽可能短, 且无滞料现象发生。
一、单螺杆挤出机ቤተ መጻሕፍቲ ባይዱ构
3、料筒 单螺杆挤出机的料筒是简单的空心钢圆筒,配有加料口,有时还有排气
口。塑料的塑化和加压过程都在其中进行,所承受的压力可达100MPa,工作温度 一般为180——250,因此料筒可看作是受压和受热的容器,同时还要耐磨和耐腐 蚀。料筒内表面有时经氮化处理或者用X—合金衬里。
料筒加热方法一般用电阻加热和电感加热等。为了防止塑料加热,或者 在停车时使之快速冷却,通常还设有冷却系统。 4、螺杆
供料的形式有粒状、粉状和带状等几种。加料装置一般采用加料斗,其 内应有切断料流、标定料量和卸除余料等装置。有的料斗还设有定时、定量供料 及内在干燥或预热等装置。此外,也有采用在减压下加料的,以适宜易吸湿塑料 的需要。为了避免粉料的“架桥”现象,在料斗中设置搅拌器或螺杆旋转送强制 加料器。为了塑料因升温而发黏,在加料孔周围应设置冷却夹套。
挤出成型工艺介绍
——设备
目录
一、单螺杆挤出机结构 二、口模 三、辅助设备 四、单螺杆挤出原理 五、挤出机一般操作方法 六、片材生产线
一、单螺杆挤出机结构
热塑性塑料的于法挤出过程可分两个阶段:第一阶段是使固态塑料熔化,并 在加压下使其通过口模而成为截面与口模相仿的连续体;第二阶段是将连续体冷却、定 型,使其失去塑性状态而变成固体,即得所需的制品。根据工艺要求,挤出设备一般是 由挤出机、口模(机头)、辅助设备等几部分组成的。
单螺杆挤出机是由一根阿基米德螺杆在加热料筒中旋转构成的。这种挤 出机的大小一般以螺杆直径表示。单螺杆挤出机一般由传动装置、加料装置、料 筒和螺杆等几部分组成,如下图所示:
一、单螺杆挤出机结构
一、单螺杆挤出机结构
1、传动装置 传动装置是带动螺杆转动的部分,通常是由电动机、减速机构和轴承等
所组成。在挤出过程中,如果螺杆转速有变化,就会引起料流压力的波动,所以 在正常操作条件下,不管螺杆的负荷是否发生变化,螺杆的转速都维持不变,借 以保持制品的质量稳定。但在不同的场合下,又要求螺杆的转速能够改变,以便 加工不同的制品或塑料。为满足上述要求,挤出机的传动装置最好采用无级调速。 2、加料装置
螺杆是挤出机的关键部件,通过它的转动,物料才能在料筒内移动,得 到增压和部分热量。螺杆的几何参数,诸如直径、长径比、各段长度比例以及螺 槽深度等,对螺杆的工作特,性均有重大影响。例如,挤出机的产量是随螺杆直 径和长径比的增大而增加的。另外,改变螺杆的几何形状(如设置屏障螺纹或销 钉等),也可提高挤出物的质量和产量。
筛板也是口模组合装置的组成部分,它是由多孔圆板组成,并安装在料 筒和口模体之间。筛板的主要作用是使物料由旋转运动变为直线运动、增加反压、 支撑过滤网等。这种过滤网是由不同数目和粗细的金属丝组成的,其作用是过滤 熔融料流和增加料流阻力,借以滤去机械杂质和提高混合或塑化效果。
二、口模
口模一般是由口模分配腔、 引流道和口模成型段(“模唇”)这 三个功能各异的几何区组成的。口模 分配腔是把进人口模的熔体分配在整 个横截面上,该截面的形状与最终产 品的形状近似,但与熔体输送设备的 出口不同;引流道是使熔体呈流线型 流入最终的口模出口;口模成型段 (“模唇”)是赋予挤出物以适当的 截面形状,并消除在前两区所产生的 不均匀流动经历。
一、单螺杆挤出机结构
通用螺杆的螺距(导程)与螺杆的外径(D)相等,即螺旋角(θ)为 17.66.螺杆的有效长度为20D_30D。螺纹宽度为0.1D。根据塑料在螺杆上的运转 情况而分为加料、压缩和计量三个段,各段的功能是不同的。
一、单螺杆挤出机结构
(1)加料段 加料段是自塑料入口向前延伸的一段距离,其长度为4D——5D。 塑料在这段仍然是固体状态。这段螺杆的主要功能是从加料斗攫取物料传送给压 缩段(固体输送),同时使物料受热,由于物料的密度小,螺槽的深度(Hf)较 大,约为0.1D——0.15D,,并保持根径不变。 (2)压缩段 压缩段(过渡段)是螺杆中部的一段,塑料在这段中,除受热、 压实和熔化外,同时还将夹带的空气向加料段排出。为适应这一变化,通常使这 一段螺槽由深逐渐变浅,直至计量段的螺槽深度(Hm)。这样,既有利于制品的 质量,也有利于物料的升温和熔化。通常,将加料段深度与计量段深度之比 (Hf/Hm)称为螺槽深度比(对于这种等导程螺杆,它接近于压缩比),其值为 2——4。它取决于所加工塑料的种类、进料时的聚集状态和挤出制品的形状。 (+)计量段计量段(均化段)是螺杆的最后一段,其长度为6D——10D。这段的 功能是使熔体进一步塑化均匀,并使料流定量、定压由机头和口模的流道排出。 这段螺槽的深度比较浅,且根径不变,Hm为(0.02——0.06)D。