管板式换热器详细设计解析
列管式换热器课程设计报告书
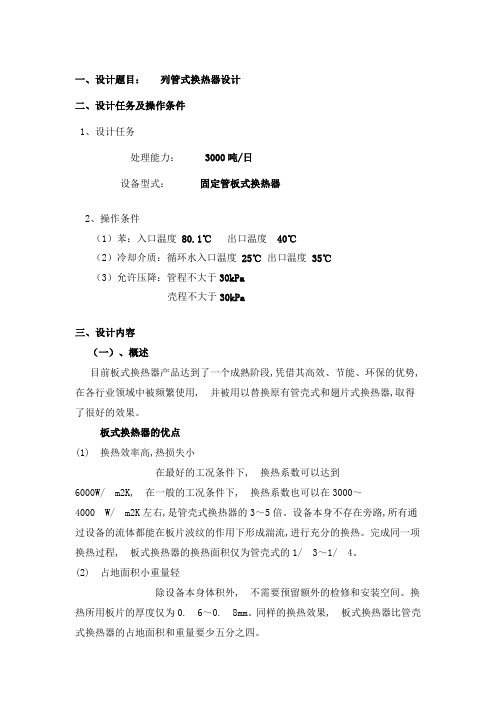
一、设计题目:列管式换热器设计二、设计任务及操作条件1、设计任务处理能力:3000吨/日设备型式:固定管板式换热器2、操作条件(1)苯:入口温度80.1℃出口温度40℃(2)冷却介质:循环水入口温度25℃出口温度35℃(3)允许压降:管程不大于30kPa壳程不大于30kPa三、设计内容(一)、概述目前板式换热器产品达到了一个成熟阶段,凭借其高效、节能、环保的优势,在各行业领域中被频繁使用, 并被用以替换原有管壳式和翅片式换热器,取得了很好的效果。
板式换热器的优点(1) 换热效率高,热损失小在最好的工况条件下, 换热系数可以达到6000W/ m2K, 在一般的工况条件下, 换热系数也可以在3000~4000 W/ m2K左右,是管壳式换热器的3~5倍。
设备本身不存在旁路,所有通过设备的流体都能在板片波纹的作用下形成湍流,进行充分的换热。
完成同一项换热过程, 板式换热器的换热面积仅为管壳式的1/ 3~1/ 4。
(2) 占地面积小重量轻除设备本身体积外, 不需要预留额外的检修和安装空间。
换热所用板片的厚度仅为0. 6~0. 8mm。
同样的换热效果, 板式换热器比管壳式换热器的占地面积和重量要少五分之四。
(3) 污垢系数低流体在板片间剧烈翻腾形成湍流, 优秀的板片设计避免了死区的存在, 使得杂质不易在通道中沉积堵塞,保证了良好的换热效果。
(4) 检修、清洗方便换热板片通过夹紧螺柱的夹紧力组装在一起,当检修、清洗时, 仅需松开夹紧螺柱即可卸下板片进行冲刷清洗。
(5) 产品适用面广设备最高耐温可达180 ℃, 耐压2. 0MPa , 特别适应各种工艺过程中的加热、冷却、热回收、冷凝以及单元设备食品消毒等方面, 在低品位热能回收方面, 具有明显的经济效益。
各类材料的换热板片也可适应工况对腐蚀性的要求。
当然板式换热器也存在一定的缺点, 比如工作压力和工作温度不是很高, 限制了其在较为复杂工况中的使用。
同时由于板片通道较小,也不适宜用于杂质较多,颗粒较大的介质。
管板式换热器详细设计
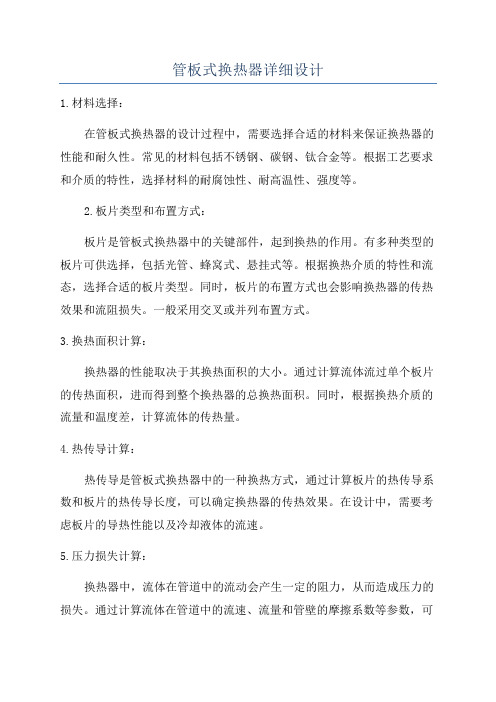
管板式换热器详细设计1.材料选择:在管板式换热器的设计过程中,需要选择合适的材料来保证换热器的性能和耐久性。
常见的材料包括不锈钢、碳钢、钛合金等。
根据工艺要求和介质的特性,选择材料的耐腐蚀性、耐高温性、强度等。
2.板片类型和布置方式:板片是管板式换热器中的关键部件,起到换热的作用。
有多种类型的板片可供选择,包括光管、蜂窝式、悬挂式等。
根据换热介质的特性和流态,选择合适的板片类型。
同时,板片的布置方式也会影响换热器的传热效果和流阻损失。
一般采用交叉或并列布置方式。
3.换热面积计算:换热器的性能取决于其换热面积的大小。
通过计算流体流过单个板片的传热面积,进而得到整个换热器的总换热面积。
同时,根据换热介质的流量和温度差,计算流体的传热量。
4.热传导计算:热传导是管板式换热器中的一种换热方式,通过计算板片的热传导系数和板片的热传导长度,可以确定换热器的传热效果。
在设计中,需要考虑板片的导热性能以及冷却液体的流速。
5.压力损失计算:换热器中,流体在管道中的流动会产生一定的阻力,从而造成压力的损失。
通过计算流体在管道中的流速、流量和管壁的摩擦系数等参数,可以得到压力损失的大小。
这个参数需要在设计中进行考虑,以确保设备工作时的正常运行。
6.结构设计:在管板式换热器的设计中,需要考虑结构的合理性和可行性。
包括设备的尺寸、管道的布局、管板的连接方式等。
同时还需要考虑换热器的维护和清洗。
通过合理的结构设计,可以提高换热器的使用寿命和性能。
7.安全性设计:在管板式换热器的设计中,需要考虑设备的安全性。
包括材料的选择、结构的强度、换热介质的流动性等。
同时,还需要考虑设备的操作安全和防护措施。
通过合理的安全性设计,可以降低设备的故障率和事故风险。
8.维护和保养:在设计完管板式换热器后,还需要考虑设备的维护和保养。
包括定期的检修、清洗和更换部件等。
通过合理的维护和保养,可以延长换热器的使用寿命,并保证设备的正常工作。
综上所述,管板式换热器的详细设计包括材料选择、板片类型和布置方式、换热面积计算、热传导计算、压力损失计算、结构设计、安全性设计和维护保养等多个方面。
板式换热器设计PPT课件

第10页/共55页
2 流程组合
➢根据工艺需要,可将板式换热器若干流道并联成一组,又将并联的组 串联在一起,形成冷热介质的通道,这叫做板式换热器的流程组合。 ➢流程数为1的流程组合称之为单流程;程数为2以上的流程组合,称之 为多流程。 ➢最简单的流程组合是“Z”形和“U”形。 ➢在多数场合,采用混合的流程组合型式。
法来求解。
tlm
tlm
tmax tmin ln tmax
tm tlm
tmin
的办
▪ 修正系数 随冷热流体的相对流动方向的不同组合而取不同的值。
▪当流体的温度沿传热面变化不大时,
(3)传热系数的计算
tm
1 2
tmax
tmin
▪可根得据到传热系f 数N的due值,。
Re
v,de
de
,4只A要s 求出Nu即 S
第5页/共55页
§ 2-2 板式换热器的基本构造
1 整体结构 ➢板式换热器的结构比较简单 ➢组成部分为:板片、密封垫片、 固定压紧板、活动压紧板、压紧螺 柱和螺母、上下导杆、前支柱等零 部件。 ➢如图1所示。
第6页/共55页
图2-2 板式换热器结构图
第7页/共55页
▪ 板片为传热元件,垫片为密封元件,垫片粘贴在板片的垫片槽内。 ▪粘贴好垫片的板片,按一定的顺序置于固定压紧板和活动压紧板之间, 用压紧螺柱将固定压紧板、板片、活动压紧板夹紧。 ▪压紧板、导杆、压紧装置、前支柱统称为板式换热器的框架。 ▪按一定规律排列的所有板片,称为板束。 ▪在压紧后,相邻的触点相互接触,使板片间保持一定的间隙,形成流体 的通道。 ▪换热介质从固定压紧板、活动压紧板上的接管中出入,并相间地进入板 片之间地流体通道,进行换热。
管板式换热器课程设计摘要
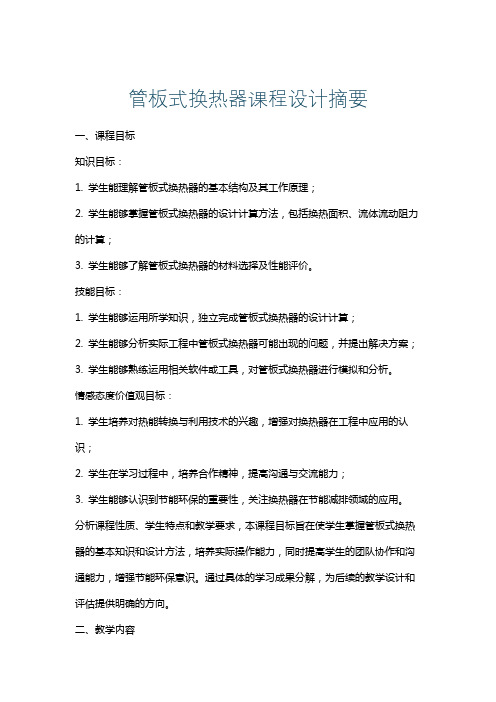
管板式换热器课程设计摘要一、课程目标知识目标:1. 学生能理解管板式换热器的基本结构及其工作原理;2. 学生能够掌握管板式换热器的设计计算方法,包括换热面积、流体流动阻力的计算;3. 学生能够了解管板式换热器的材料选择及性能评价。
技能目标:1. 学生能够运用所学知识,独立完成管板式换热器的设计计算;2. 学生能够分析实际工程中管板式换热器可能出现的问题,并提出解决方案;3. 学生能够熟练运用相关软件或工具,对管板式换热器进行模拟和分析。
情感态度价值观目标:1. 学生培养对热能转换与利用技术的兴趣,增强对换热器在工程中应用的认识;2. 学生在学习过程中,培养合作精神,提高沟通与交流能力;3. 学生能够认识到节能环保的重要性,关注换热器在节能减排领域的应用。
分析课程性质、学生特点和教学要求,本课程目标旨在使学生掌握管板式换热器的基本知识和设计方法,培养实际操作能力,同时提高学生的团队协作和沟通能力,增强节能环保意识。
通过具体的学习成果分解,为后续的教学设计和评估提供明确的方向。
二、教学内容1. 管板式换热器的基本概念:包括换热器定义、分类及其应用场景,以课本第二章第一节为基础,使学生建立换热器的基本概念。
2. 管板式换热器结构及工作原理:详细讲解换热器的主要组成部分,如管束、壳体、管板等,并分析其工作原理,参考课本第二章第二节。
3. 换热器设计计算方法:介绍换热面积、流体流动阻力计算方法,结合课本第二章第三节的内容,指导学生进行实际计算。
4. 管板式换热器材料选择及性能评价:分析不同材料的适用性,介绍性能评价方法,以课本第二章第四节为依据。
5. 换热器设计实例分析:通过实际案例分析,使学生将所学理论知识应用于实践,提高解决实际问题的能力,参考课本第二章第五节。
6. 换热器在节能减排领域的应用:讲解换热器在节能环保方面的作用,拓展学生视野,结合课本第二章第六节。
教学内容安排和进度:共6个课时,第一、二课时讲解基本概念和结构工作原理;第三、四课时进行设计计算方法教学;第五课时分析材料选择及性能评价;第六课时进行设计实例分析和节能减排应用探讨。
四管程固定管板式换热器设计
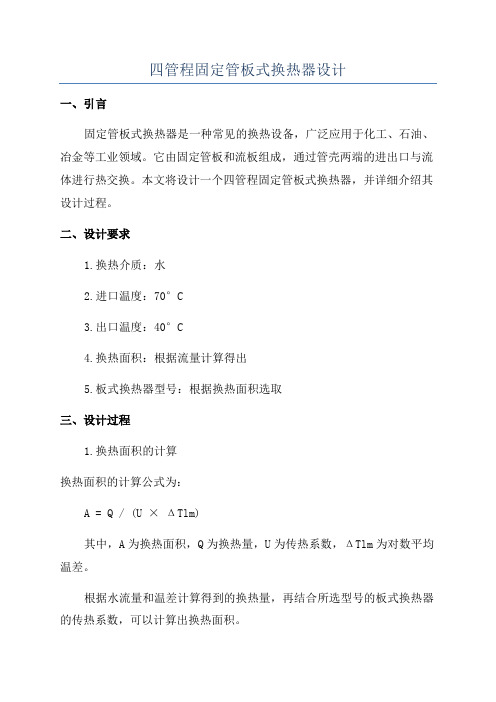
四管程固定管板式换热器设计一、引言固定管板式换热器是一种常见的换热设备,广泛应用于化工、石油、冶金等工业领域。
它由固定管板和流板组成,通过管壳两端的进出口与流体进行热交换。
本文将设计一个四管程固定管板式换热器,并详细介绍其设计过程。
二、设计要求1.换热介质:水2.进口温度:70°C3.出口温度:40°C4.换热面积:根据流量计算得出5.板式换热器型号:根据换热面积选取三、设计过程1.换热面积的计算换热面积的计算公式为:A = Q / (U × ΔTlm)其中,A为换热面积,Q为换热量,U为传热系数,ΔTlm为对数平均温差。
根据水流量和温差计算得到的换热量,再结合所选型号的板式换热器的传热系数,可以计算出换热面积。
2.板式换热器的选取根据计算得到的换热面积,选择合适的型号的板式换热器。
在选型时,要考虑换热器的材质、耐压性能、传热系数等因素。
3.管程的设计四、设计结果根据设计要求和计算过程,可以得出四管程固定管板式换热器的设计结果。
1.换热面积:根据计算结果得出换热面积为X平方米。
2.板式换热器型号:根据换热面积和选取条件,最终确定使用XX型号的板式换热器。
3.管程设计:根据流体的温度差和流速等因素,按照长度逐渐增加的方式,确定四个管程的设计。
五、结论本文根据给定的设计要求,设计了一个四管程固定管板式换热器,并详细介绍了设计过程。
设计结果包括换热面积、板式换热器型号和管程设计。
通过本文的设计,可以满足给定的换热要求,并提供一个可行的四管程固定管板式换热器设计方案。
管板式换热器设计说明书

管板式换热器设计说明书管板式换热器设计说明书一、概述管板式换热器是一种高效的换热设备,广泛应用于化工、石油、制药、食品等多个领域。
本设计说明书旨在介绍管板式换热器的设计原理、结构特点、选型方法、安装注意事项等相关内容。
二、设计原理管板式换热器采用管道和板式换热器结合的方式进行换热。
其主要原理是利用热流体在管道中流动时,通过管壁和板片与低温流体进行换热。
同时,管道和板片的结构也能使热流体均匀地流过,从而增强换热效果。
三、结构特点1.结构紧凑:管板式换热器体积小,结构紧凑,占用空间少,适用于场地狭小的场合。
2.换热效率高:管板式换热器采用多层板片进行换热,有效增加了换热面积,提高了换热效率。
3.应用广泛:管板式换热器适用于多种流体之间的换热,如液-液、气-液等。
4.可靠性高:管板式换热器采用优质材料制造,工艺先进,具有耐腐蚀、耐压等特点,具有较高的可靠性。
四、选型方法1.按照工艺要求确定换热参数:如换热量、流量、温度等。
2.确定流体性质:如流体介质、流速、粘度等。
3.进行换热器设计:选择合适的板片组合,计算换热器换热面积,确定尺寸和数量。
4.选择合适的材料:选择耐腐蚀、耐高温的合金材料,同时考虑生产成本。
五、安装注意事项1.在安装前,应仔细检查产品是否完好,检查连接处是否严密,以确保安装质量。
2.安装时应注意管路连接方式的选择,可选用法兰连接或焊接连接。
3.在碰到易燃易爆介质时,应注意防火防爆措施。
4.安装后应进行效验,检查管道连接是否泄漏,实验前应做好相应的准备工作。
六、总结管板式换热器具有结构紧凑、换热效率高、应用广泛、可靠性高等特点,是目前工业中使用的一种高效节能的换热设备。
在选型和安装过程中,应注意流体性质、工艺要求的确定,材料的选择和安装质量的保证。
固定管板式换热器工作原理
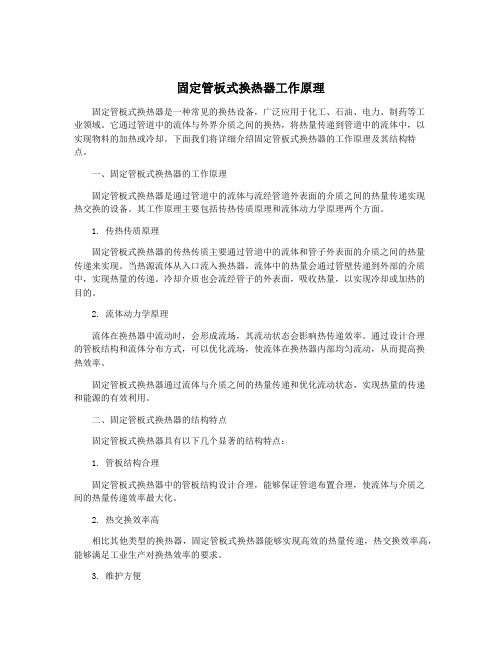
固定管板式换热器工作原理固定管板式换热器是一种常见的换热设备,广泛应用于化工、石油、电力、制药等工业领域。
它通过管道中的流体与外界介质之间的换热,将热量传递到管道中的流体中,以实现物料的加热或冷却。
下面我们将详细介绍固定管板式换热器的工作原理及其结构特点。
一、固定管板式换热器的工作原理固定管板式换热器是通过管道中的流体与流经管道外表面的介质之间的热量传递实现热交换的设备。
其工作原理主要包括传热传质原理和流体动力学原理两个方面。
1. 传热传质原理固定管板式换热器的传热传质主要通过管道中的流体和管子外表面的介质之间的热量传递来实现。
当热源流体从入口流入换热器,流体中的热量会通过管壁传递到外部的介质中,实现热量的传递。
冷却介质也会流经管子的外表面,吸收热量,以实现冷却或加热的目的。
2. 流体动力学原理流体在换热器中流动时,会形成流场,其流动状态会影响热传递效率。
通过设计合理的管板结构和流体分布方式,可以优化流场,使流体在换热器内部均匀流动,从而提高换热效率。
固定管板式换热器通过流体与介质之间的热量传递和优化流动状态,实现热量的传递和能源的有效利用。
二、固定管板式换热器的结构特点固定管板式换热器具有以下几个显著的结构特点:1. 管板结构合理固定管板式换热器中的管板结构设计合理,能够保证管道布置合理,使流体与介质之间的热量传递效率最大化。
2. 热交换效率高相比其他类型的换热器,固定管板式换热器能够实现高效的热量传递,热交换效率高,能够满足工业生产对换热效率的要求。
3. 维护方便固定管板式换热器的结构简单,维护方便,能够降低维护成本和维护难度。
4. 适用范围广泛固定管板式换热器可以适用于各种介质的热交换,包括液体、气体等不同形式的流体,适用范围广泛,适合不同的工业应用。
固定管板式换热器具有结构合理、热交换效率高、维护方便和适用范围广泛等特点,是一种非常重要的工业换热设备。
通过对其工作原理和结构特点的深入了解,可以更好地应用于工业生产实践中,提高生产效率和资源利用率。
板式换热器设计说明
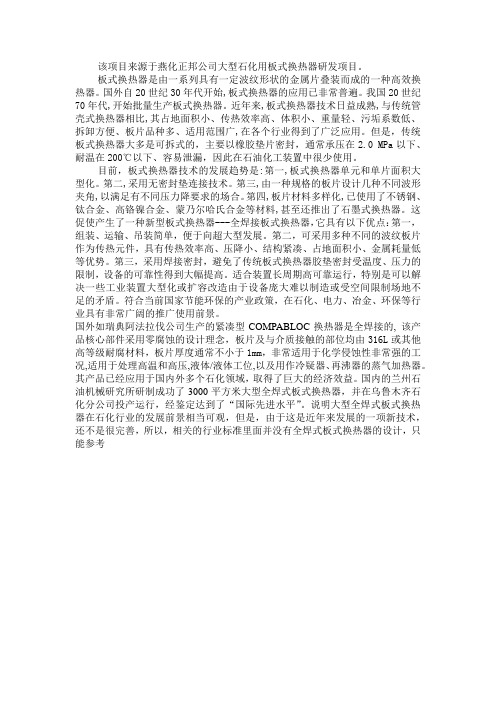
该项目来源于燕化正邦公司大型石化用板式换热器研发项目。
板式换热器是由一系列具有一定波纹形状的金属片叠装而成的一种高效换热器。
国外自20世纪30年代开始,板式换热器的应用已非常普遍。
我国20世纪70年代,开始批量生产板式换热器。
近年来,板式换热器技术日益成熟,与传统管壳式换热器相比,其占地面积小、传热效率高、体积小、重量轻、污垢系数低、拆卸方便、板片品种多、适用范围广,在各个行业得到了广泛应用。
但是,传统板式换热器大多是可拆式的,主要以橡胶垫片密封,通常承压在2.0 MPa以下、耐温在200℃以下、容易泄漏,因此在石油化工装置中很少使用。
目前,板式换热器技术的发展趋势是:第一,板式换热器单元和单片面积大型化。
第二,采用无密封垫连接技术。
第三,由一种规格的板片设计几种不同波形夹角,以满足有不同压力降要求的场合。
第四,板片材料多样化,已使用了不锈钢、钛合金、高铬镍合金、蒙乃尔哈氏合金等材料,甚至还推出了石墨式换热器。
这促使产生了一种新型板式换热器---全焊接板式换热器,它具有以下优点:第一,组装、运输、吊装简单,便于向超大型发展。
第二,可采用多种不同的波纹板片作为传热元件,具有传热效率高、压降小、结构紧凑、占地面积小、金属耗量低等优势。
第三,采用焊接密封,避免了传统板式换热器胶垫密封受温度、压力的限制,设备的可靠性得到大幅提高。
适合装置长周期高可靠运行,特别是可以解决一些工业装置大型化或扩容改造由于设备庞大难以制造或受空间限制场地不足的矛盾。
符合当前国家节能环保的产业政策,在石化、电力、冶金、环保等行业具有非常广阔的推广使用前景。
国外如瑞典阿法拉伐公司生产的紧凑型COMPABLOC换热器是全焊接的,该产品核心部件采用零腐蚀的设计理念,板片及与介质接触的部位均由316L或其他高等级耐腐材料,板片厚度通常不小于1mm,非常适用于化学侵蚀性非常强的工况,适用于处理高温和高压,液体/液体工位,以及用作冷疑器、再沸器的蒸气加热器。
- 1、下载文档前请自行甄别文档内容的完整性,平台不提供额外的编辑、内容补充、找答案等附加服务。
- 2、"仅部分预览"的文档,不可在线预览部分如存在完整性等问题,可反馈申请退款(可完整预览的文档不适用该条件!)。
- 3、如文档侵犯您的权益,请联系客服反馈,我们会尽快为您处理(人工客服工作时间:9:00-18:30)。
换热器设计1.换热器选型说明1.1 换热器类型换热器类型很多,按其用途分,有加热器、冷却器、冷凝器、蒸发器和再沸器。
按其结构分,有列管式、板式等。
不同类型换热器,其性能各异。
管型换热器又可以分为蛇管式换热器、套管式换热器、管壳式换热器。
板型换热器可分为螺旋板式换热器、板式换热器、板翘式换热器。
换热器的结构分类见下表:表1-1 换热器的结构分类1.2 换热器类型选择换热器选型时需要考虑的因素是多方面的,主要有:①流体的性质;②热负荷及流量大小;③温度、压力及允许压降的范围;④设备结构、材料、尺寸、重量;⑤价格、使用安全性和寿命。
在换热器选型中,除考虑上述因素外,还应对结构强度、材料来源、制造条件密封性、安全性等方面加以考虑。
1.3 管壳式换热器的分类与特点在众多类型的换热器结构中,管壳式换热器是用得最广泛的一种换热设备类型。
它的突出优点是:单位体积设备所能提供的传热面积大,传热效果好,结构坚固,而且可以选用的结构材料范围也比较宽广,清洗方便,处理量大,工作可靠,故适应性较强,操作弹性较大。
它的设计资料和数据比较完善,目前在许多国家已有系列化标准,因而在各种换热器的竞争发展中占有绝对优势。
综合考虑该类型换热器的优点和本次设计工艺的特点,大部分都采用的是管壳式换热器。
管壳式换热器是把管子与管板连接,再用壳体固定。
它的型式大致分为固定管板式、釜式、浮头式、U型管式、滑动管板式、填料函式及套管式等几种。
表1-2管壳式换热器的性能对比表2. 换热器设计举例.本工艺主要分为三个部分:预处理反应部分、吸收部分和精馏部分。
这三个部分总共有26台换热器(换热器,冷凝器,再沸器)。
我们主要对吸收部分的E0202换热器做详细设计。
2.1 设计任务和设计条件.本工艺流程中,丙烯腈分离塔T-106底侧线出来的循环水经给原料丙烯加热后,用液氨将其从69.62℃进一步冷却至4℃之后,与新鲜循环水混合进入混合器做为氢氰酸吸收塔T-103的吸收剂。
设计条件表2-1:2.2 确定设计方案2.2.1 选择换热器类型两流体温差变化情况:热流体(循环水)进口温度69.62℃,出口温度4℃;冷流体(液氨)进口温度-25℃,出口温度-24.36℃。
两流体均不易结垢且能够清洗,管、壳侧温差较大,综合考虑,初步确定选用固定管板式换热器。
2.2.2 流程安排从两流体的进、出口温度来看,热流股(循环水)属于被冷却介质,为了方便散热,宜走壳程;考虑到冷流股(液氨)对管道具有一定的腐蚀作用,为了避免壳体和管束同时被腐蚀,宜走管程。
2.3 确定物性数据定性温度:对于低粘度液体液氨和水,其定性温度可以取流体进出口温度的平均值。
故 壳程流体的定性温度为: T 壳 =2462.69+℃=36.81℃ 管程流体的定性温度为:T 管 =2)36.24(25-+-℃=-24.68℃根据定性温度,分别查取壳程和管程流体的有关物性数据 表2-2。
2.4 估算传热面积在热损失可以忽略不计的条件下,对于无相变的工艺物流,由传热基本方程式Q=KA Δt m 来估算传热面积。
1. 传热量Q=t c W ph h ∆=414351⨯5.12⨯(69.62-4)=1.39*108(KJ/h )=38611.1KW2. 液氨量W c =)(12t t c Q pc -=)2536.24(*075.510*39.18+-=4.28*107(kg/h ) 3. 平均传热温差循环水 69.62℃ → 4℃ 液氨 -25℃ ← -24.36℃ 温差 94.62℃ 28.36℃Δt m =2121ln t t t t ∆∆∆-∆=36.2862.9436.2862.94In-=54.99℃(以逆流计)计算温差校正系数εΔt ,首先得算出R 和P ,再按温差校正系数图查取εΔt 值。
R=冷流体的温升热流体的温降=53.10225--36.24-4-62.691221==--)(t t T TP=两流体最初温差冷流体的温升=()0068.025--62.6925--36.24-1112==--)(t T t t 按单壳程,双管程结构,查温差校正系数图得:εΔt ≈0.98 所以 平均传热温差: Δt m =εΔt Δt m .=54.99*0.98=53.89℃ 3. 估算传热面积参照热交换器的总传热系数概算值表,假设总传热系数K=780W/(m 2.k) 则所需传热面积为:A=mt K Q∆=780*89.53*6.310*39.18= 918.6(m 2)取安全系数1.04,则 A p =918.6*1.04= 955.3(m 2) 2.5工艺结构尺寸 1. 管径和管内流速选用Φ25X2.5的16Mn 材质的传热管,取管内流速为u i =1.15m/s. 2. 管程数和传热管数根据传热管内径和流速确定单程传热管数,管长l 取12m 。
管子根数:N t =doL A π=12025.03.955⨯⨯π≈980.2取981根按单管程设计,传热管过长,宜采用多管程结构。
根据本设计实际情况,采用标准设计,现取换热管长l=6m. 则该换热器的管程数为: N p =l L =612=2(管程) 传热总管数: N t =981⨯2=1962(根) 3. 平均传热温差校正与壳程数温差校正系数εΔt 与流体的进出口温度有关,也与换热器的壳程数及管程数有关。
首先得计算出R 和P ,再按温差校正系数图查取εΔt 值,得:εΔt ≈0.98 由于εΔt ≈0.98〉0.8,同时壳程流体流量较大,故取单壳程合适。
4. 传热管排列及管心距采用组合排列法,即每程内均按正三角形排列,隔板两侧采用正方形排列。
因为正三角形排列在相同的管板面积上可排较多的管子,并且管外表面传热系数较大;正方型排列,管外易于进行机械清理。
综合考虑组合排列的优点和该换热器的特点,传热管采用组合排列法。
取 管心距a=1.25d o则管心距为: a=1.25×25=31.25≈32mm 隔板中心到离其最近一排管中心距离为:S=2a +6=232+6=22(mm ) 各程相邻管的管心距为: 2S=2⨯22mm=44mm通过管中心线管数: N TC =1.1t N =1.1⨯1962=48.7 5. 壳体内径采用多管程结构,壳体内径可按下式计算,取管板利用率η=0.80,则壳体内径为:D=1.05a ηNt =1.05⨯32⨯80.01962=1664.0(mm )按卷制壳体的进级档,圆整可取D=1700mm 6. 折流板采用弓形折流板,取弓形折流板圆缺高度为壳体内径的25%。
(1)切去的圆缺高度为: h=0.25D=0.25⨯1700mm=425(mm) (2)取折流板间距为: B=0.20D=0.20⨯1700mm=390(mm )按标准圆整后取B=450mm(3) 折流板数N B : N B =折流板间距传热管长-1=4506000-1≈12.3取13(块)折流板圆缺面水平装配。
不设旁流挡板,N B0=0. 7. 拉杆(1) 拉杆直径 表2-3:换热管的外径为25mm ,所以拉杆直径为16mm (2) 拉杆数量 表2-4:拉杆数量:查拉杆数量与壳体公称直径表,本换热器壳体内径为1700mm,拉杆直径φ=16mm,所以拉杆数量为10. (3)拉杆尺寸拉杆的长度=L +a d+L b ,如下表2-5 的标准:从表中可以得到:直径d=16mm 的拉杆; 拉杆螺纹公称直径d n =16mm; , 管板上拉杆孔深L d =20mm; L b ≥60mm. L a =20mm 拉杆长度=L +a d+L b ≥96mm拉杆与管板的固定形式:全焊接方法8. 防冲挡板:液体物料2ρυ=1221.72⨯2.52=7635.6kg/(m.s 2)>740 kg/(m.s 2),要设置防冲挡板。
9. 接管(1) 壳程流体进出口接管:取接管内液体的流速为u 1=2.5m/s,则接管内径为:D 1=14πυv h=5.2)72.12213600(4143514⨯⨯⨯πm=0.219 m=219mm圆整后可取管内径为250mm.(2) 管程流体进出口接管:取接管内流体的流速为u 2=2.65m/s,则接管内径为:D 2=24πυv c=65.2)37.6713600(1078.447⨯⨯⨯⨯πm= 0.951m=951mm圆整后可取管内径为 1000mm 10. 管板结构根据:壳体的内径为1700mm ,圆整后的公称直径为1800mm ;操作压力=0.132MPa, 定性温度=36.81℃ 查固定管板式换热器管板尺寸得到有关尺寸:固定管板长度D=1960mm; D 1=1910mm; D 2=1790mm; D 3=1798mm; D 5=D 6=1800mm; D 7=1850mm; b=50mm; c=14mm; d=27mm 螺栓孔数=64个. ;2.6 换热器核算 2.6.1 热流量核算 1. 壳程表面传热系数α用克恩法计算:14.03155.000)(Pr 36.0we e R d μμλα=当量直径: d e =025.014.3)025.0414.3032.023(4)423(4220202⨯-=-d d a ππ=0.02m (三角形排列) 壳程流体流通截面积: o S =BD(1-a d 0)=0.45×1.7×(1-032.0025.0)=0.167m 2 壳程流体流速及雷诺数分别为:流速 u 0=s m s w h /564.0167.0)72.12213600(4143510=⨯=雷诺数 Re 0=9.1766700078.072.1221564.002.0=⨯⨯=μρdu普朗特常数:Pr=27.57578.000078.01012.53=⨯⨯=λμp c 黏度校正: 08.1)00045.000078.0()(14.014.0==w μμ壳程表面传热系数为:)/(6.555608.1)27.5()9.17667(02.07578.036.0)(Pr Re 36.023155.014.03155.000℃⋅=⨯⨯⨯==m w d w eμμλα2. 管内表面传热系数管程流体流通截面积: S i =222308.0981)02.0(414.34m n d i =⨯⨯=π管程流体流速及雷诺数:流速 u i =s m S w ic /575.0308.0)37.6713600(1028.47=⨯⨯=雷诺数 Re i =5.2086690000037.037.671575.002.0=⨯⨯=μρdu普朗特常数:Pr=325.05785.0000037.010075.53=⨯⨯=λμp c管内表传热系数为:4.48230)325.0()5.2086690(02.05785.0023.0Pr Re 023.04.08.04.08.0===i i i i d λαw/(m 2.k) 3. 污垢热阻和管壁热阻 查取污垢系数表,可取管外侧污垢热阻: R o =0.0006 m 2.k/w 管内测污垢热阻: R i =0.000172 m 2.k/w表2-5 常用金属材料的热导率/[W/(m.k)]16MnDG 在该条件下的热导率近似为50 W/(m·k) 管壁热阻: R w =wbλ=500025.0=0.00005 (m 2.k/w)b ——传热管壁厚,m ; λm ——管壁热导率,m.k/w. 4. 总传热系数K 0)./(8556.555610006.00225.0025.00005.002.0025.0000172.002.04.48230025.01112000000k m W R d d R d d R d d K m w i i i i =++⨯++⨯=++++=αα5 传热面积裕度传热面积A c 为: A c =28099.8376.389.538551039.1m t K Q m =⨯⨯⨯=∆ 换热器的实际传热面积为: A p =201.92419626025.0m lN d =⨯⨯⨯=ππ 传热面积裕度;: H=ccp A A A -=99.83799.8371.924-=10.28%传热面积裕度合适,该换热器能够为完成生产任务。