气辅注塑工艺的应用
气辅注塑原理
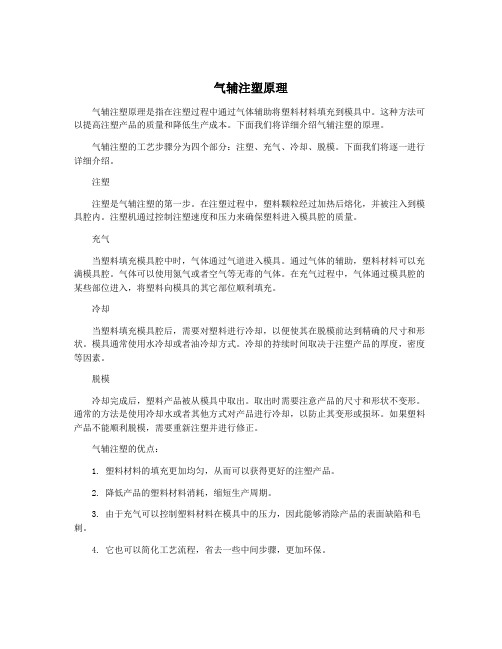
气辅注塑原理气辅注塑原理是指在注塑过程中通过气体辅助将塑料材料填充到模具中。
这种方法可以提高注塑产品的质量和降低生产成本。
下面我们将详细介绍气辅注塑的原理。
气辅注塑的工艺步骤分为四个部分:注塑、充气、冷却、脱模。
下面我们将逐一进行详细介绍。
注塑注塑是气辅注塑的第一步。
在注塑过程中,塑料颗粒经过加热后熔化,并被注入到模具腔内。
注塑机通过控制注塑速度和压力来确保塑料进入模具腔的质量。
充气当塑料填充模具腔中时,气体通过气道进入模具。
通过气体的辅助,塑料材料可以充满模具腔。
气体可以使用氮气或者空气等无毒的气体。
在充气过程中,气体通过模具腔的某些部位进入,将塑料向模具的其它部位顺利填充。
冷却当塑料填充模具腔后,需要对塑料进行冷却,以便使其在脱模前达到精确的尺寸和形状。
模具通常使用水冷却或者油冷却方式。
冷却的持续时间取决于注塑产品的厚度,密度等因素。
脱模冷却完成后,塑料产品被从模具中取出。
取出时需要注意产品的尺寸和形状不变形。
通常的方法是使用冷却水或者其他方式对产品进行冷却,以防止其变形或损坏。
如果塑料产品不能顺利脱模,需要重新注塑并进行修正。
气辅注塑的优点:1. 塑料材料的填充更加均匀,从而可以获得更好的注塑产品。
2. 降低产品的塑料材料消耗,缩短生产周期。
3. 由于充气可以控制塑料材料在模具中的压力,因此能够消除产品的表面缺陷和毛刺。
4. 它也可以简化工艺流程,省去一些中间步骤,更加环保。
气辅注塑是一种高效、环保、节能的注塑工艺。
它可以提高生产效率,降低生产成本,同时还能有效改善产品的质量和外观。
近年来,气辅注塑工艺广泛应用于各个领域。
它可以用于制造电子产品、医疗器械、汽车零配件、家用电器等。
它的灵活性和可塑性极高,满足了市场对产品多样化、品质一致化、成本低价化等需求。
在汽车零配件的制造中,气辅注塑的运用已成为一种趋势。
由于汽车零配件的尺寸和数量大,所以制造成本非常高。
而这里正是气辅注塑的优势所在。
利用气辅注塑工艺,能够更好的控制塑料材料在模具中的填充,从而提高产品的密度、强度和耐用性。
气体辅助注塑工艺原理及优点.
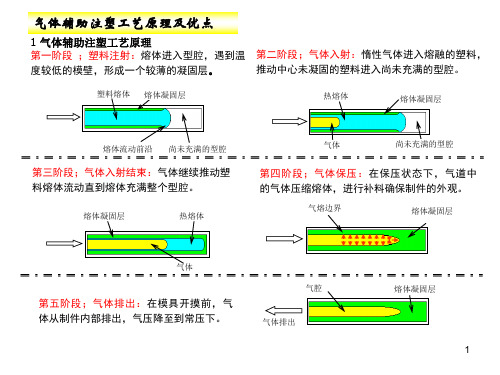
1 气体辅助注塑工艺原理 第一阶段 ;塑料注射:熔体进入型腔,遇到温 第二阶段;气体入射:惰性气体进入熔融的塑料,
度较低的模壁,形成一个较薄的凝固层。
推动中心未凝固的塑料进入尚未充满的型腔。
塑料熔体 熔体凝固层
热熔体
熔体凝固层
熔体流动前沿 尚未充满的型腔
第三阶段;气体入射结束:气体继续推动塑 料熔体流动直到熔体充满整个型腔。
射嘴进气方式,即使用专用的自封闭式或主动式气辅射嘴,在塑料注射结束后,将 高压气体依靠射嘴直接进入塑料内部,按气道形成一个延展的封闭空间-气腔并保持一 定压力,直至冷却,在模具打开之前,通过座台后退使射嘴与制品料道强行分离,使气 体排出制品。
图4自封闭气辅射嘴
图5主动式气辅射嘴 7
(2) 气针进气方式 气针进气方式即在模具的某个特定位置,安装排气装置-气针。当塑料注入型腔后,
2
气辅技术应用
气体辅助注射可以应用在除特别柔软的塑料以外的任何热塑性塑料和部分热 固性塑料。
根据气辅成型制品的结构形状不同,大致分为3类: (1).棒类制品,类似把手之类大壁厚制件; (2).板类制品,容易产生翘曲变形和局部表面收缩的大平面制件; (3).特殊制品,由传统注塑技术难以一次成型的特殊结构的制件。
(5).气道截面尺寸变化应平缓过渡,以免引起收缩不均。 (6).气道入口不应设置在外观面或制件承受机械外力处。
(7).进气口位置应接近浇口,以保证气体与熔体流动方向一致,但两者距离应>30mm, 以避免类制品
气辅注塑成型技术的主要应用之一就是板类制件的成型。因为气体总是沿 着阻力最小的方向前进,容易在较厚的部位进行穿透,因此,在板类制品设计时常 将加强筋作为气道,气道一般设在制品的边缘或壁的转角处。对制品的设计也就是 对加强筋和肋板的设计,即气道的设计。基本原则如下: (1).在设计制作加强筋时,应避免设计又细又密的加强筋。 (2).“手指”效应是大平面制件容易产生的主要问题。 (3).当制件仅由一个气针进气而形成多个加强筋或肋板(气道)时,气道不能形 成回 路。 (4).为避免熔体聚集产生凹陷,气道末端的外形应采用圆角过渡。 (5).采用多点进气时,气道之间的距离不能太近。 (6).气道布置尽量均匀,尽量延伸至制品末端。
气体辅助注射成型技术在汽车注塑件生产中的应用

维普资讯
F
E
A
T
U
R
E
S
气体辅 助注射成型技术 在汽车注塑件生产 中的应 用
介绍 了气体辅助注射成型技术 的基本原理和 工艺特点 ,以捷 达轿
车保 险杠和解放载 货车把手件为例 ,说明 了气辅 技术在汽车注塑件生
产 中的具体 应用 。
1 基本原理 .
体 短射 、气体注 射 、气 体保压 、
气辅 成型分 为4 个阶段 ,即熔 分 惰 性 气 体 可 以 重 复 使 用 ,其 余 排 入大 气 。制 件
图1气辅成型基本原理 图
5 汽车工艺与材料 T 6 l A 8
20年第 期 07 1
维普资讯
压两个阶段。 ・ 气体排 出和制 件顶 出
() 体 短射 a熔 () 体 注 射 b气
( 参见 图l) d。 经 过 保 压 冷却 ,制 件 具 有 足 够 高 的 刚 度 和 强 度 。利 用 回收装 置使 一 部
() c气体保压 () d 气体排 出
气辅成型技术概述
()气辅注射成型数值模拟分 2
捷达 轿车 前 保险 杠是 大 型 、
气 道布 置掏空 厚 壁部分 ,使壁 厚 析 更趋 一 致 ,也会 有效地 抑 制缩痕
的产 生 。
最 大值 出现 在熔 体的 保压 阶段 ,
气辅注塑加工工艺与一般注塑工艺
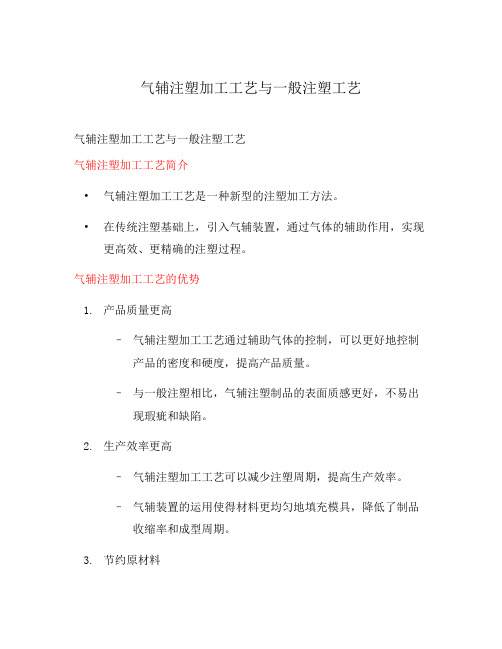
气辅注塑加工工艺与一般注塑工艺气辅注塑加工工艺与一般注塑工艺气辅注塑加工工艺简介•气辅注塑加工工艺是一种新型的注塑加工方法。
•在传统注塑基础上,引入气辅装置,通过气体的辅助作用,实现更高效、更精确的注塑过程。
气辅注塑加工工艺的优势1.产品质量更高–气辅注塑加工工艺通过辅助气体的控制,可以更好地控制产品的密度和硬度,提高产品质量。
–与一般注塑相比,气辅注塑制品的表面质感更好,不易出现瑕疵和缺陷。
2.生产效率更高–气辅注塑加工工艺可以减少注塑周期,提高生产效率。
–气辅装置的运用使得材料更均匀地填充模具,降低了制品收缩率和成型周期。
3.节约原材料–气辅注塑加工工艺由于材料分布更均匀,减少了材料的浪费。
–相比较于一般注塑,气辅注塑制品在制造时所需的原材料用量更少。
4.环保节能–气辅注塑加工工艺不需要额外的加热或冷却设备,节约了能源。
–通过优化制程,减少了废品率,降低了对环境的负面影响。
气辅注塑加工工艺的应用领域•电子产品:手机壳、电池壳、硬盘壳等。
•汽车配件:车灯壳、仪表板、车门把手等。
•家居用品:儿童玩具、家具配件、文具等。
一般注塑工艺的特点与局限性•一般注塑工艺在制品的表面平整度和精度方面有一定的局限性。
•一般注塑制造过程中,因为材料无法完全填充到模具中的每个角落,易产生瑕疵和缺陷。
结语气辅注塑加工工艺相对于一般注塑工艺具有众多优势,无论是产品质量、生产效率还是原材料的节约都占有明显的优势。
在如今注塑加工行业日益竞争激烈的背景下,气辅注塑加工工艺的应用前景非常广阔。
希望本文能对读者对气辅注塑加工工艺与一般注塑工艺有更深入的了解。
气辅注塑加工工艺的工作原理1.注塑过程中,将塑料颗粒加热融化。
2.融化的塑料通过注塑机的螺杆被注入模具腔中。
3.气辅装置通过喷嘴向注入的塑料中喷入压缩空气。
4.压缩空气通过气门控制,辅助塑料充填模具,使得塑料更加均匀地填充到模具的每个角落。
5.注塑机冷却塑料,然后开模取出制品。
气辅成型工艺
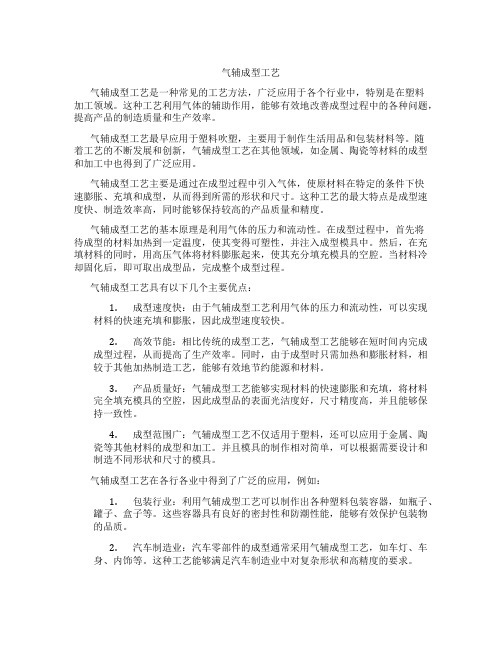
气辅成型工艺气辅成型工艺是一种常见的工艺方法,广泛应用于各个行业中,特别是在塑料加工领域。
这种工艺利用气体的辅助作用,能够有效地改善成型过程中的各种问题,提高产品的制造质量和生产效率。
气辅成型工艺最早应用于塑料吹塑,主要用于制作生活用品和包装材料等。
随着工艺的不断发展和创新,气辅成型工艺在其他领域,如金属、陶瓷等材料的成型和加工中也得到了广泛应用。
气辅成型工艺主要是通过在成型过程中引入气体,使原材料在特定的条件下快速膨胀、充填和成型,从而得到所需的形状和尺寸。
这种工艺的最大特点是成型速度快、制造效率高,同时能够保持较高的产品质量和精度。
气辅成型工艺的基本原理是利用气体的压力和流动性。
在成型过程中,首先将待成型的材料加热到一定温度,使其变得可塑性,并注入成型模具中。
然后,在充填材料的同时,用高压气体将材料膨胀起来,使其充分填充模具的空腔。
当材料冷却固化后,即可取出成型品,完成整个成型过程。
气辅成型工艺具有以下几个主要优点:1.成型速度快:由于气辅成型工艺利用气体的压力和流动性,可以实现材料的快速充填和膨胀,因此成型速度较快。
2.高效节能:相比传统的成型工艺,气辅成型工艺能够在短时间内完成成型过程,从而提高了生产效率。
同时,由于成型时只需加热和膨胀材料,相较于其他加热制造工艺,能够有效地节约能源和材料。
3.产品质量好:气辅成型工艺能够实现材料的快速膨胀和充填,将材料完全填充模具的空腔,因此成型品的表面光洁度好,尺寸精度高,并且能够保持一致性。
4.成型范围广:气辅成型工艺不仅适用于塑料,还可以应用于金属、陶瓷等其他材料的成型和加工。
并且模具的制作相对简单,可以根据需要设计和制造不同形状和尺寸的模具。
气辅成型工艺在各行各业中得到了广泛的应用,例如:1.包装行业:利用气辅成型工艺可以制作出各种塑料包装容器,如瓶子、罐子、盒子等。
这些容器具有良好的密封性和防潮性能,能够有效保护包装物的品质。
2.汽车制造业:汽车零部件的成型通常采用气辅成型工艺,如车灯、车身、内饰等。
气体辅助注塑工艺简介

气体辅助注塑工艺简介1.气体辅助注塑目前所指的气体辅助注塑:是指将氮气注射入产品内,使产品内部形成中空。
模具打开前,控制器会将塑胶工件内的氮气释放回大气中。
2.气辅注塑成形工艺的优势1)低射胶、低锁模力;2)压力分布均匀、收缩均匀、残余应力低、不易翘曲,尺寸稳定;3)消除凹陷,型面再现性高;4)省塑料,可用强度及价格更低的塑料;5)可用强度和价格更低的模具金属;6)厚薄件一体成型,减少模具及装配线数目;7)可用较厚的筋,角板等补强件,提高制品刚性,使得制件公称厚度得以变薄。
8)增强设计自由度。
3.气辅射胶控制工艺1)短射工艺,即胶料未完全充满型腔时,继之以氮气注射;2)满射工艺,塑胶熔体充满型腔之后,停止注射,继之以氮气注射。
短射工艺的特点:在气辅注塑中,塑胶注射取决于胶件形状及胶料性能,在以下条件才可进行短射。
1)胶件必须有独立完整的气体通道,即气流在穿透胶件时,无分支气道可走。
2)气体通道中多余胶料有足够的溢流空间。
3)胶料流动性优良,粘度不可太低,尽量避免使用含破坏高分子键的填充物的胶料。
4)胶料导热度较低,有可较长时间保持熔融状态的能力。
满射工艺特点:胶件射胶完成,通过气体代替啤机,防止胶件收缩。
其优点在于,啤机保压是以射胶量及压力来防止胶件收缩,气辅保压,则以气体穿透塑胶收缩后的空间,防止胶件表层埸陷。
4.气辅压力分析:现我们看以下气辅压力与啤机压力的对比:1)气辅压力a)低气压800psi=56.34kg/cm2b)中气压1500psi=105.63 kg/cm2c)高气压2500psi=176.06kg/cm22)啤机压力a)100 TON注塑最大压力188Mpa=1917 kg/cm2b)280 TON注塑最大压力150Mpa=1530 kg/cm2c)650TON注塑最大压力153Mpa=1560 kg/cm2从以上压力对比可知,氮气压力只相当于普通啤机注塑压力的十分之一,甚至更少。
气辅注塑

1)封闭式气体注射(SEALED INJECTION GAS)方法: * 是把气体直接注入模腔内,使塑料成品中空的方法。无需采用活阀,只是 通过简单模具加工,把气辅气嘴装在模具中。 * 在同一模具上,可有单一或多个注入气体的地方,这视乎同产品的需要, 慕求令产品有良好效果和提供产品设计有较大的灵活性。
太小会使气体流动失去控制 7.冷却要尽量均匀,内外壁温差要尽量小
8.在流道上放置合理流道半径的截流块,辅助注塑设备按工艺需求大致应有以下几类: 1、氮气机:主要用于氮气的制造 2、氮气增压器:主要是将氮气的气压加大,以便于氮气的注入 3、气辅控制器:主要用于控制氮气注入量、气压、时间及排气的控制,是
• 降低生产成本
– 由于减少了壁厚,因此降低了零件成品的总重量. – 由于壁厚较小,因此缩短了冷却时间和循环时间. – 由于降低了锁模力和注塑保压压力,能源消耗成本降低. – 由于零件的集成化,从而降低了装配成本.
• 降低投资成本
– 由于注射压力较低,因此可以降低注塑机的锁模压力,可使用吨位较小的注塑 机.
整个气辅设备的控制中心 4、气辅配件:主要有气针、气管及各种接头等,用于气辅设备与模具的连
接
因各种设备加在一起,占用的空间较大,现有很大一部分已采用一体化的气 辅系统。
END
同传统注射成型工艺相比.应用气体辅助注塑技术,有以下优点:
• 自由设计
– 综合功能较为复杂的塑胶零件可以整装为单一的组件. – 可以在同一零件上结合厚壁和薄壁部分. – 使用空心的"加强筋"部分可以提高其强度.
• 提高零件质量
– 由于减小了微收缩,因此扭曲和变形就减少了. – 消除缩痕. – 由于注射点的数量减少,所以波纹和熔接线也相应减少.
气辅注塑工艺的应用
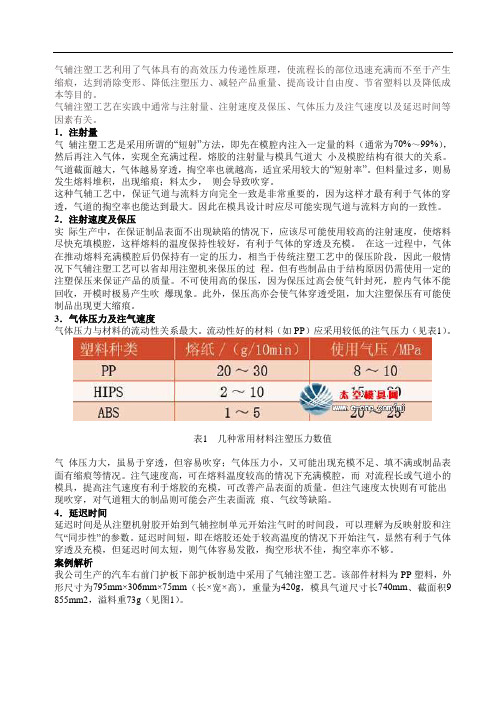
气辅注塑工艺利用了气体具有的高效压力传递性原理,使流程长的部位迅速充满而不至于产生缩痕,达到消除变形、降低注塑压力、减轻产品重量、提高设计自由度、节省塑料以及降低成本等目的。
气辅注塑工艺在实践中通常与注射量、注射速度及保压、气体压力及注气速度以及延迟时间等因素有关。
1.注射量气辅注塑工艺是采用所谓的“短射”方法,即先在模腔内注入一定量的料(通常为70%~99%),然后再注入气体,实现全充满过程。
熔胶的注射量与模具气道大小及模腔结构有很大的关系。
气道截面越大,气体越易穿透,掏空率也就越高,适宜采用较大的“短射率”。
但料量过多,则易发生熔料堆积,出现缩痕;料太少,则会导致吹穿。
这种气辅工艺中,保证气道与流料方向完全一致是非常重要的,因为这样才最有利于气体的穿透,气道的掏空率也能达到最大。
因此在模具设计时应尽可能实现气道与流料方向的一致性。
2.注射速度及保压实际生产中,在保证制品表面不出现缺陷的情况下,应该尽可能使用较高的注射速度,使熔料尽快充填模腔,这样熔料的温度保持性较好,有利于气体的穿透及充模。
在这一过程中,气体在推动熔料充满模腔后仍保持有一定的压力,相当于传统注塑工艺中的保压阶段,因此一般情况下气辅注塑工艺可以省却用注塑机来保压的过程。
但有些制品由于结构原因仍需使用一定的注塑保压来保证产品的质量。
不可使用高的保压,因为保压过高会使气针封死,腔内气体不能回收,开模时极易产生吹爆现象。
此外,保压高亦会使气体穿透受阻,加大注塑保压有可能使制品出现更大缩痕。
3.气体压力及注气速度气体压力与材料的流动性关系最大。
流动性好的材料(如PP)应采用较低的注气压力(见表1)。
表1 几种常用材料注塑压力数值气体压力大,虽易于穿透,但容易吹穿;气体压力小,又可能出现充模不足、填不满或制品表面有缩痕等情况。
注气速度高,可在熔料温度较高的情况下充满模腔,而对流程长或气道小的模具,提高注气速度有利于熔胶的充模,可改善产品表面的质量。
- 1、下载文档前请自行甄别文档内容的完整性,平台不提供额外的编辑、内容补充、找答案等附加服务。
- 2、"仅部分预览"的文档,不可在线预览部分如存在完整性等问题,可反馈申请退款(可完整预览的文档不适用该条件!)。
- 3、如文档侵犯您的权益,请联系客服反馈,我们会尽快为您处理(人工客服工作时间:9:00-18:30)。
气辅注塑工艺的应用
一、前言
气辅注塑工艺是国外八十年代研究成功,九十年代才得到实际应用的一项实用型注塑新工艺,其原理是利用高压隋性气体注射到熔融的塑料中形成真空截面并推动熔料前进,实现注射、保压、冷却等过程。
由于气体具有高效的压力传递性,可使气道内部各处的压力保持一致,因而可消除内部应力,防止制品变形,同时可大幅度降低模腔内的压力,因此在成型过程中不需要很高的锁模力,除此之外,气辅注塑还具有减轻制品重量、消除缩痕、提高生产效率、提高制品设计自由度等优点。
近年来,在家电、汽车、家具等行业,气辅注塑得到越来越广泛的应用,前景看好。
科龙集团于98年引进一套气辅设备用于生产电冰箱、空调器的注塑件。
二、气辅设备
气辅设备包括气辅控制单元和氮气发生装置。
它是独立于注塑机外的另一套系统,其与注塑机的唯一接口是注射信号连接线。
注塑机将一个注射信号注射开始或螺杆位置传递给气辅控制单元之后,便开始一个注气过程,等下一个注射过程开始时给出另一个注射信号,开始另一个循环,如此反复进行。
气辅注塑所使用的气体必须是隋性气体(通常为氮气),气体最高压力为35MPa,特殊者可达70MPa,氮气纯度≥98%。
气辅控制单元是控制注气时间和注气压力的装置,它具有多组气路设计,可同时控制多台注塑机的气辅生产,气辅控制单元设有气体回收功能,尽可能降低气体耗用量。
今后气辅设备的发展趋势是将气辅控制单元内置于注塑机内,作为注塑机的一项新功能。
三、气辅工艺控制
1.注气参数
气辅控制单元是控制各阶段气体压力大小的装置,气辅参数只有两个值:注气时间(秒)和注气压力(MPa)。
2.气辅注塑过程是在模具内注入塑胶熔体的同时注入高压气体,熔体与气体之间存在着复杂的两相作用,因此工艺参数控制显得相当重要,下面就讨论一下各参数的控制方法:
a.注射量
气辅注塑是采用所谓的“短射”方法(short size),即先在模腔内注入
一定量的料(通常为满射时的70-95%),然后再注入气体,实现全充满过程。
熔胶注射量与模具气道大小及模腔结构关系最大。
气道截面越大,气体越易穿透,掏空率越高,适宜于采用较大的“短射率”。
这时如果使用过多料量,则很容易发生熔料堆积,料多的地方会出现缩痕。
如果料太少,则会导致吹穿。
如果气道与流料方向完全一致,那么最有利于气体的穿透,气道的掏空率最大。
因此在模具设计时尽可能将气道与流料方向保持一致。
b.注射速度及保压
在保证制品表现不出现缺陷的情况下,尽可能使用较高的注射速度,使熔料尽快充填模腔,这时熔料温度仍保持较高,有利于气体的穿透及充模。
气体在推动熔料充满模腔后仍保持一定的压力,相当于传统注塑中的保压阶段,因此一般讲气辅注塑工艺可省却用注塑机来保压的过程。
但有些制品由于结构原因仍需使用一定的注塑保压来保证产品表现的质量。
但不可使用高的保压,因为保压过高会使气针封死,腔内气体不能回收,开模时极易产生吹爆。
保压高亦会使气体穿透受阻,加大注塑保压有可能使制品表现出现更大缩痕。
c.气体压力及注气速度
气体压力与材料的流动性关系最大。
流动性好的材料(如PP)采用较低的注气压力。
几种材料推荐压力如下:
塑料种类熔纸(g/10min)使用气压(MPa)
PP20~308~10
HIPS2~1015~20
ABS1~520~25
气体压力大,易于穿透,但容易吹穿;气体压力小,可能出现充模不足,填不满或制品表面有缩痕;注气速度高,可在熔料温度较高的情况下充满模腔。
对流程长或气道小的模具,提高注气速度有利于熔胶的充模,可改善产品表面的质量,但注气速度太快则有可能出现吹穿,对气道粗大的制品则可能会产生表面流痕、气纹。
d.延迟时间
延迟时间是注塑机射胶开始到气辅控制单元开始注气时的时间段,可以理解为反映射胶和注气“同步性”的参数。
延迟时间短,即在熔胶还处于较高温度的情况下开始注气,显然有利于气体穿透及充模,但延迟时
间太短,气体容易发散,掏空形状不佳,掏空率亦不够。
四、气辅模具
气辅模具与传统注塑模具无多大差别,只增加了进气元件(称为气针),并增加气道的设计。
所谓“气道”可简单理解为气体的通道,即气体进入后所流经的部分,气道有些是制品的一部分,有些是为引导气流而专门设计的胶位。
气针是气辅模具很关键的部件,它直接影响工艺的稳定和产品质量。
气针的核心部分是由众多细小缝隙组成的圆柱体,缝隙大小直接影响出气量。
缝隙大,则出气量也大,对注塑充模有利,但缝隙太大会被熔胶堵塞,出气量反而下降。
五、气辅应用实例
气辅注塑最适宜于具有粗大柱孔或厚筋的制品以及胶位粗大内部有孔穴的制品(如手柄类、衣架类),国内几间大型电视机厂家都采用气辅注塑工艺生产电视机前框,可节省原材料10%~20%并大幅度降低锁模力。
冰箱顶盖板是大型平板注塑件,质量要求高,其模具采用直浇口入胶,在传统注塑时极易产生变形,影响冰箱的装配。
采用气辅后,变形量得到有效控制,拱曲变形量由原来的1.7~2 mm减少到0.5mm以下。
空调器的横向风板是一长条型结构,截面形状“不规则”,由于表面不允许有熔接痕,模具采取单点水口入胶,料流程长,用传统注塑极易产生变形、缩痕,装在空调器上会影响风向电机的转动,严重者甚至会烧毁电机,因此改善变形量显得尤为重要。
采用气辅工艺后此问题迎刃而解,变形量由原来的3~4mm降为1 mm以内。
手柄则是另一类型的制品,在气辅出现前它是由两件制品装配而成,需要做两付模具而且装配后强度不够,整体也不够美观。
采取气辅后
可“合二为一”,省略一付模具及装配工序。
六、总结
气辅注塑是近年兴起的一项新工艺,在国外已得到广泛应用,在国内尚处于初始阶段,目前大型家电厂已陆续开始应用这项新工艺,相信随着各厂商对气辅工艺认识的加深,这项新工艺会应用得越来越普遍。