价值流程图VSM案例分析
价值流程图(VSM)案例分析27页PPT

1、最灵繁的人也看不见自己的背脊。——非洲 2、最困难的事情就是认识自己。——希腊 3、有勇气承担命运这才是英雄好汉。——黑塞 4、与肝胆人共事,无字句处读书。——周恩来 5、阅读使人充实,会谈使人敏捷,写作使人精确。——培根
精益生产3VSM(价值流图及价值流分析)(ppt34页)

•机加工:87% •去毛刺:100% •弯曲:99% •检测:99% •打标记:99% 累计的正常运行时间计量标准=0.87*1*0.99*0.99 *0.99=0.844(即84.4%)。
在对所有的数据达成一致意见以后,团队成员将价 值流管理的有关信息记录在了演示图板上。
•
每天都是美好的一天,新的一天开启 。20.11.820.11.806:5306:53:3506:53:35Nov- 20
•
人生不是自发的自我发展,而是一长 串机缘 。事件 和决定 ,这些 机缘、 事件和 决定在 它们实 现的当 时是取 决于我 们的意 志的。2020年11月8日 星期日 6时53分35秒 Sunday, November 08, 2020
•
感情上的亲密,发展友谊;钱财上的 亲密, 破坏友 谊。20.11.82020年11月8日星 期日6时53分35秒20.11.8
谢谢大家!
公司的一个主要客户——考得联合公司,与其供 应基地进行了合并。考得联合公司一直在审查和 分析其供应商既能满足质量和发货方面的需求同 时又能降低成本的能力。普莱梅尔制造公司与考 得联合公司的长期协议即将到期。考得联合公司 愿意保持与普莱梅尔制造公司的业务关系,但是 要求:
• 在未来的7年中每年降低成本5%。
2、价值流图的用途
价值流图有助于全面观察和理解产品 通过价值流过程时的物料流动和信息流动, 以及其中的增值
和非增值活动,从而发现浪费和确定需要改善 的地方,更容易找出问题所在。为改善活动定 下一个蓝图和方向。同时也便于员工了解企业 的状态,提供参与改善的机会。价值流图还可 以避免只应用个别的精益工具,进行局部、孤 立的改善。通过绘制现状图,设计理想状态图 并尽快付诸实施,通过这种方法,可以全面的 改善价值流,从而为客户和供应商带来最大的 利益。
VSM价值流分析
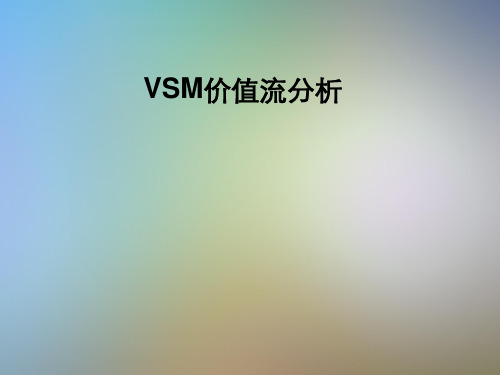
客户及需求
Weekly
Despatch
(4)
Dispense
(4)
I
7 days
Blend & Granulate
(25)
I
20 days
Bulk Testing
(5)
I
10 days
Filling Line 1
(33)
I
20 days
Bottle Testing
(5)
I
30 days
情景剧
续上页: (甲、乙闲聊中,服务员来到近前) 服务员:先生,找您零钱。 (服务员递给甲12元人民币) 乙:麻烦给我一张发票。 服务员:请稍等。(转身快步离去)
情景剧
续上页: (甲、乙不耐烦中,服务员来到近前) 服务员:先生,给您发票。 乙:谢谢,不过下次能不能快点。 服务员:好、好。(心情郁闷中,我已经来回走的很 快了,还要怎么样啊?)
XX有限公司
SMT段 A线 价值流程图Value Stream Mapping(VSM)
采购部
生产管理部
采购计划
物料计划
生产计划
大客户部
机种名称:
订单流 L/T
客户订单量(P/O QTY:pcs) 2,195
ALMCB V3.3
客户产能需求TT/pcs(Sec) 577
客户交货周期(计划生产需求) 7
人数 面积
100 Lot/天
0.012 H/Lot
1
天
0.012 H/Lot
1
人
3
M2
目检
代号
名称
信息 单位
C/O 换线/模时间
/ Sec/次
价值流程图-VSM

PROCESSES
Products
Receiving Cutting Strip Soldering Crimp Insertion molding test inspect Pack
A
x
x
x
x
x
x
x
x
x
B
x
x
x
x
x
x
x
x
x
C
x
x
x
一次质量
2 x/ day
发运
I
500 pcs
Inventory Part A = 750 pcs Part B = 600 pcs Part C = 1650 pcs
# of shifts =
环节6:定义信息流
绘制从收到订单到下达生产订单(客户旳订单,生产订 单,采购订单)旳信息流。
统计生产订单及有关产品。 统计生产计划系统及随产品经过系统旳文件材料。 统计你怎样与供给商和客户沟通。 统计信息怎样整顿和发放,例如:电子方式,手工方式,
区别流动中旳推动和拉动。 包括产品接受和质量检验旳全部控制。
推动
流程生产不考虑下游(内部 )客户流程旳实际需求,直 接推动未完毕产品经过流程 。生产根据既定计划。
VS
拉动
每个后续生产环节都是前一 流程环节旳客户。当需要时 (拉动)由客户要求数量, 而不是简朴旳根据前面生产 环节生产并直接送到客户处 (推动)。
怎样辨认流程中旳挥霍?
价值流图(VSM)
价值流图消除挥霍
价值流图旳目旳在揭发挥霍旳起源。
我们应着眼于回答下述问题: “我们怎样能够仅生产下个流程所需,并仅在该流程需要时生产旳方式
价值流程图
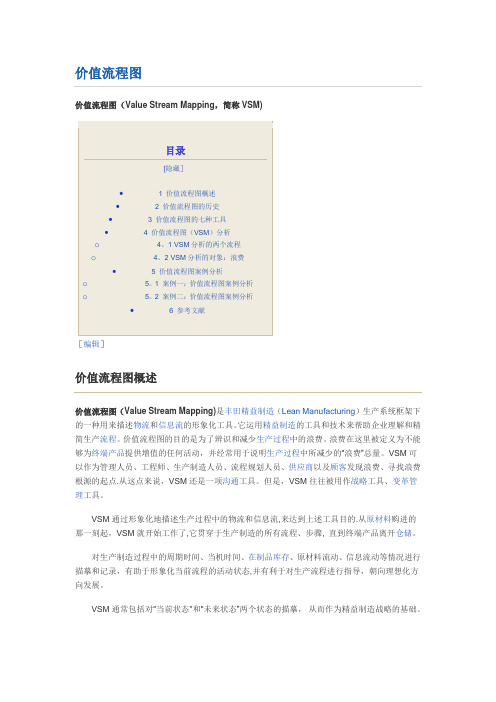
价值流程图价值流程图(Value Stream Mapping,简称VSM)[编辑]价值流程图概述价值流程图(Value Stream Mapping)是丰田精益制造(Lean Manufacturing)生产系统框架下的一种用来描述物流和信息流的形象化工具。
它运用精益制造的工具和技术来帮助企业理解和精简生产流程。
价值流程图的目的是为了辨识和减少生产过程中的浪费。
浪费在这里被定义为不能够为终端产品提供增值的任何活动,并经常用于说明生产过程中所减少的“浪费”总量。
VSM可以作为管理人员、工程师、生产制造人员、流程规划人员、供应商以及顾客发现浪费、寻找浪费根源的起点.从这点来说,VSM还是一项沟通工具。
但是,VSM往往被用作战略工具、变革管理工具。
VSM通过形象化地描述生产过程中的物流和信息流,来达到上述工具目的.从原材料购进的那一刻起,VSM就开始工作了,它贯穿于生产制造的所有流程、步骤, 直到终端产品离开仓储。
对生产制造过程中的周期时间、当机时间、在制品库存、原材料流动、信息流动等情况进行描摹和记录,有助于形象化当前流程的活动状态,并有利于对生产流程进行指导,朝向理想化方向发展。
VSM通常包括对“当前状态"和“未来状态”两个状态的描摹,从而作为精益制造战略的基础。
价值流程图(VSM)分析的是两个流程:第一个是信息(情报)流程,即从市场部接到客户订单或市场部预测客户的需求开始,到使之变成采购计划和生产计划的过程;第二个是实物流程,即从供应商供应原材料入库开始,随后出库制造、成品入库、产品出库,直至产品送达客户手中的过程.此外,实物流程中还包括产品的检验、停放等环节。
企业在进行价值流程图(VSM)分析时,首先要挑选出典型的产品作为深入调查分析的对象,从而绘制出信息(情报)流程和实物流程的现状图,然后将现状图与信息(情报)和实物流程的理想状况图相比较,发现当前组织生产过程中存在的问题点,进而针对问题点提出改进措施。
价值流程图
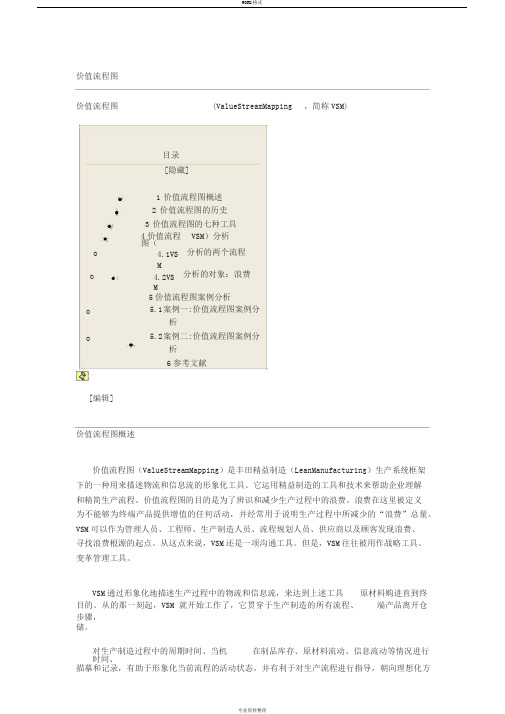
价值流程图价值流程图(ValueStreamMapping ,简称VSM)目录[隐藏]1价值流程图概述2价值流程图的历史3价值流程图的七种工具4价值流程图(VSM)分析o 4.1VSM分析的两个流程o 4.2VSM分析的对象:浪费5价值流程图案例分析o 5.1 案例一:价值流程图案例分析o 5.2 案例二:价值流程图案例分析6参考文献[编辑]价值流程图概述价值流程图(ValueStreamMapping)是丰田精益制造(LeanManufacturing)生产系统框架下的一种用来描述物流和信息流的形象化工具。
它运用精益制造的工具和技术来帮助企业理解和精简生产流程。
价值流程图的目的是为了辨识和减少生产过程中的浪费。
浪费在这里被定义为不能够为终端产品提供增值的任何活动,并经常用于说明生产过程中所减少的“浪费”总量。
VSM可以作为管理人员、工程师、生产制造人员、流程规划人员、供应商以及顾客发现浪费、寻找浪费根源的起点。
从这点来说,VSM还是一项沟通工具。
但是,VSM往往被用作战略工具、变革管理工具。
VSM通过形象化地描述生产过程中的物流和信息流,来达到上述工具目的。
从的那一刻起,VSM就开始工作了,它贯穿于生产制造的所有流程、步骤,原材料购进直到终端产品离开仓储。
对生产制造过程中的周期时间、当机时间、在制品库存、原材料流动、信息流动等情况进行描摹和记录,有助于形象化当前流程的活动状态,并有利于对生产流程进行指导,朝向理想化方向发展。
VSM通常包括对“当前状态”和“未来状态”两个状态的描摹,从而作为精益制造战略的基础。
价值流程图(VSM)分析的是两个流程:第一个是信息(情报)流程,即从市场部接到客户订单或市场部预测客户的需求开始,到使之变成采购计划和生产计划的过程;第二个是实物流程,即从供应商供应原材料入库开始,随后出库制造、成品入库、产品出库,直至产品送达客户手中的过程。
此外,实物流程中还包括产品的检验、停放等环节。
2024版价值流程图VSM案例分析PPT课件

价值流程图VSM案例分析PPT课件目录•引言•案例分析:某制造企业生产流程优化•案例分析:某电商平台订单处理流程改进•案例分析:某医院患者就诊流程优化•总结与展望01引言提高生产效率降低成本提升产品质量目的和背景通过价值流程图VSM分析,识别生产过程中的浪费环节,优化生产流程,提高生产效率。
减少生产过程中的非增值活动,降低生产成本,提高企业竞争力。
通过价值流程图VSM分析,发现生产过程中的问题点,改进生产工艺,提升产品质量。
价值流程图VSM简介定义价值流程图VSM是一种可视化工具,用于描述产品或服务的整个价值流,包括从原材料到最终产品或服务的所有活动。
作用帮助企业识别生产过程中的浪费环节,优化生产流程,提高生产效率和质量。
适用范围适用于制造业、服务业等各个领域的企业。
02案例分析:某制造企业生产流程优化当前生产流程存在过多的环节和等待时间,导致生产效率低下。
生产流程繁琐资源浪费严重质量问题突出生产过程中的物料、人力和时间等资源未能得到充分利用,造成资源浪费。
产品质量不稳定,客户投诉率高,影响企业声誉和市场竞争力。
030201企业现状及问题分析深入企业生产现场,全面了解现有生产流程、设备、人员配置等情况。
流程调研收集生产过程中的关键数据,如生产周期、在制品数量、设备利用率等。
数据收集基于调研和收集的数据,绘制价值流程图VSM ,直观展示生产过程中的价值流动情况。
VSM 绘制价值流程图VSM 构建识别并消除生产过程中的浪费环节,如减少等待时间、降低库存等。
消除浪费优化生产流程,合并或取消不必要的环节,提高生产效率。
简化流程加强产品质量控制,采用先进的质量管理方法和技术手段,提高产品质量稳定性。
强化质量控制生产流程优化方案设计01020304生产效率提升资源利用率提高产品质量改善企业竞争力增强实施效果评估通过优化生产流程,提高生产效率,缩短生产周期。
充分利用物料、人力和时间等资源,降低生产成本。
通过生产流程优化,提高企业市场竞争力,实现可持续发展。
价值流程图
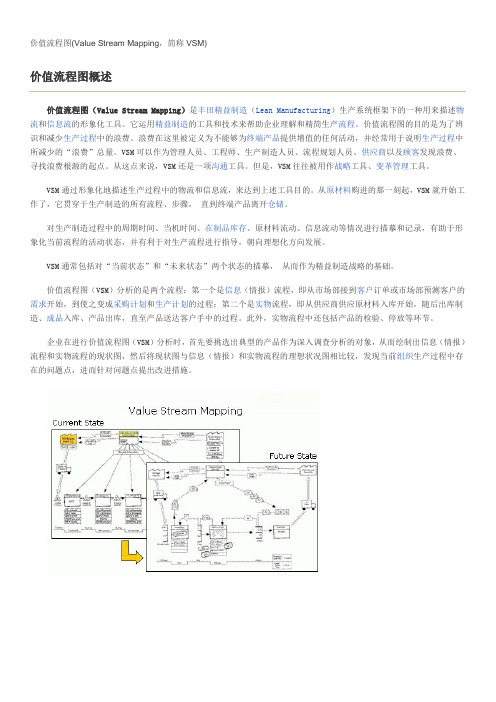
价值流程图(Value Stream Mapping,简称VSM)价值流程图概述价值流程图(Value Stream Mapping)是丰田精益制造(Lean Manufacturing)生产系统框架下的一种用来描述物流和信息流的形象化工具。
它运用精益制造的工具和技术来帮助企业理解和精简生产流程。
价值流程图的目的是为了辨识和减少生产过程中的浪费。
浪费在这里被定义为不能够为终端产品提供增值的任何活动,并经常用于说明生产过程中所减少的“浪费”总量。
VSM可以作为管理人员、工程师、生产制造人员、流程规划人员、供应商以及顾客发现浪费、寻找浪费根源的起点。
从这点来说,VSM还是一项沟通工具。
但是,VSM往往被用作战略工具、变革管理工具。
VSM通过形象化地描述生产过程中的物流和信息流,来达到上述工具目的。
从原材料购进的那一刻起,VSM就开始工作了,它贯穿于生产制造的所有流程、步骤,直到终端产品离开仓储。
对生产制造过程中的周期时间、当机时间、在制品库存、原材料流动、信息流动等情况进行描摹和记录,有助于形象化当前流程的活动状态,并有利于对生产流程进行指导,朝向理想化方向发展。
VSM通常包括对“当前状态”和“未来状态”两个状态的描摹,从而作为精益制造战略的基础。
价值流程图(VSM)分析的是两个流程:第一个是信息(情报)流程,即从市场部接到客户订单或市场部预测客户的需求开始,到使之变成采购计划和生产计划的过程;第二个是实物流程,即从供应商供应原材料入库开始,随后出库制造、成品入库、产品出库,直至产品送达客户手中的过程。
此外,实物流程中还包括产品的检验、停放等环节。
企业在进行价值流程图(VSM)分析时,首先要挑选出典型的产品作为深入调查分析的对象,从而绘制出信息(情报)流程和实物流程的现状图,然后将现状图与信息(情报)和实物流程的理想状况图相比较,发现当前组织生产过程中存在的问题点,进而针对问题点提出改进措施。
价值流程图的历史1980年代,丰田公司的首席工程师Taiichi Ohno与sensei Shigeo Shingo率先运用去除生产浪费的方法来获取竞争优势,他们的主要出发点是提高生产效率,而非提高产品质量。
- 1、下载文档前请自行甄别文档内容的完整性,平台不提供额外的编辑、内容补充、找答案等附加服务。
- 2、"仅部分预览"的文档,不可在线预览部分如存在完整性等问题,可反馈申请退款(可完整预览的文档不适用该条件!)。
- 3、如文档侵犯您的权益,请联系客服反馈,我们会尽快为您处理(人工客服工作时间:9:00-18:30)。
?计划和实 施
?实施计划,达到的理想状态
?三、价值流程图案例分析
粗车
钻孔
精车、抛光
检验
? 物料搬运由1个专人负责,搬运设备为手推车。搬运工 每班从仓库向车间搬运一次毛坯,从车间向装配工位搬运 两次成品零件。装配工位每天对该零件的需求为700件,每 料盘25件,并把他们的每月预测和每日需求信息发给车间
第二个是实物流程,即从供应商供应 原材料入库开始,随后出库制造、成品入 库、产品出库,直至产品送达客户手中的 过程。此外,实物流程中还包括产品的检 验、停放等环节。
企业在进行VSM分析时,首先要挑选出
?信息流
?供应 商
?生产控制
?每 周 计 划
?客户
?粗车
?1?有
?无 价
价 值
?钻孔 ?精车、抛光
同理依次计算出各工序间库存储备天数, 并绘制出当前价值流程图
?绘制当前价值流程图
?当前价值流程图
?分析当前价值流程图 装配工位每天对该零件的需求量为700件
,且其与车间和原料、半成品仓库均实行两班 制,每班有效时间25200s,使用率100%,因此
各工序作业节拍分析
容易看出,车间加工时间最长的工序粗车 时间为60s<72s,因此目前生产会造成制造过多 、过早的浪费。
其次,各工序间在制品库存最小库存储备天 数为0.25天,即
0.25x25200x2/60=210(min),很明显在制品库 存水平过高,会造成在制品库存的浪费。
此外,各工序作业统一由车间调度部门调 度,各工序间实行推动式生产,不利于及时响 应需求的变化和减少在制品库存。
?存在的问题
(1)目前生产会造成制造过多、过早的浪费;
调度部门。
车间调度部门把每周计划下发给零件加工 车间各工位和搬运工,此外,将其每月预测和 每周计划信息发给原料、半成品仓库。粗车工 位零件毛坯在制品库存为350件,以后三道工序 在制品库存以及零件成品在制品库存均为175件。
粗车工序零件毛坯库存储备天数 =350/700=0.5(天)
粗车和钻孔工序间库存储备天数 =175/700=0.25(天)
各工序生产还不平衡,易造成等待浪费。
该零件加工周期=60+35+55+25=175(s), 一个零件的生产加工时间(包括物流等时间) 即生产提前期=0.5+0.25+0.25+0.25+0.25=1.5( 天)。因此
因此,目前生产单位零件的生产过程时间 过长,也就是说生产提前期过长,这会造成生 产响应需求的能力降低,不利于企业竞争。
价值流改进重点在于物流和信息流。
?二、价值流程图
价值流程图( Value Stream Mapping ,VSM )是丰田精益制造( Learn Manufacturing )生产 系统框架下的一种用来描述物流和信息流的形象 化工具。目的是为了辨识和减少生产过程中的浪 费,并用于说明生产过程中所减少的“浪费”总 量。
?价值流程图
?主要内容
一、价值流概念 二、价值流程图 三、价值流程图案例分析
?一、价值流的概念
价值流是制造产品所需一切活动的总和,包含了 增值活动和不增值活动。
使用价值流分析意味着对全过程进行研究,而不 只是研究单个过程;改进全过程,而不是仅仅优化局 部。
据统计,增值活动约占企业生产和经营活动的 5%, 不增值活动约占 95%。因此,应在价值流中识别不增 值活动,通过持续不断地开展价值流改进,消除各种 浪费,降低成本。
同时,可以考虑采用流水线生产和拉式生 产相结合的生产和管理方式。因为这样不仅有 利于减少在制品库存,缩短提前期,也非常有 利于对装配工位需求的响应。此外,由于定拍 工序粗车节拍为60s,采取拉式生产有利于为减少 生产过多过早的浪费。
设备布置也应作相应调整,具体布置如图 所示
?未来价值流程图
需要注意的是,由于钻孔、精车抛光 、检验三道工序是2个人在U形生产线中完 成的,如采用逐兔式完成,因此每人115s 完成三道工序的生产即115s共完成两个工 件的加工,同时粗车工人120s完成两个毛 坯加工,因此相当于U形生产线中57.5s完 成一个零件的加工。因此,图3-2中后面三 道工序的加工周期标注57.5s。
(2)各工序生产还不平衡,易造成等待浪费;
(3)生产提前期过长,这会造成生产响应需求的 能力降低,不利 于企业竞争;
(4)在制品库存水平高,会造成在制品库存的浪 费;
(5)实行推动式生产,不利于及时响应需求的变
化和减少在制品
库存。
?改进方案设想
目前生产中钻孔和检验工序生产能力得不到 发挥,存在很大浪费。因此,可以考虑减少一 个作业者。因为钻孔和检验总共用时 35s+25s=60s,可以考虑将这两道工序合并。
?1
?1
?物料流
?VSM分析的对象Fra bibliotekVSM分析的主旨是暴露存在的浪费问题,并彻底排
除浪费。在JIT 生产方式中,凡是超出增加产品价值 所绝对必需的最少量的物料、设备、人力、场地和时 间的部分都是浪费。
VSM分析关注的八大浪费包括:
(1) 不良/ 修理的浪费 (5)库存的浪费
(2) 过分加工的浪费 (6)制造过多 /过早的浪费
VSM对生产制造过程中的周期时间、待机时间、 在制品库存、原材料流动、信息流动等情况进行 描摹和记录,有助于形象化当前流程的活动状态, 并有利于对生产流程进行指导,朝向理想化方向 发展。
VSM通常包括对“当前状态”和“未来状态”
?VSM分析的两个流程
第一个是信息流程,即从市场部接到 客户订单或市场部预测客户的需求开始, 到使之变成采购计划和生产计划的过程;
(3) 动作的浪费
(7)等待的浪费
(4) 搬运的浪费
(8)管理的浪费
? 价值流程图分析特征
价值流程图分析以客户的观点分析现有价值流程图 每一个活动的必要性,画出期待的价值流的未来状态 图,并制定实施计划。
(1)绘制出并简单显示出物流和信息流 (2)揭示产生浪费的原因 (3)创建一个改善的价值流 (4)创建和协调一个跨部门团队方法
? 价值流程图分析的好处
?(1)目视化工具 ?(2)信息沟通方式 ?(3)有利于发现存在的问题 ?(4)创建一个改善的价值流
?价值流程图分析步骤
?选择一个 ?产品
?从头到位聚焦一个产品、 过程或服务,搜集相关数据
? 分析当前问题: ? 信息、物料、交互
? 设计一个精益价值流 ? 建立想要达到的理想状态