重介质分选技术的(2013.09.08)
重介质分选

重介质分选重介质分选包括这样的选煤过程,将原煤浸没在液体中进行分选,液体的密度介于精煤和矸石之间。
由于灰份含量和密度之间有一定的相互关系,通过调节分选液体的密度,将原煤中的含灰杂质排除到要求的程度是可能的。
重介质分选方法具有下列由于其它选煤方法的特点:(1)在正常要求的密度范围内的任一分选密度点,即使入料中±0.1密度物含量很高,也能进行精确分选。
(2)能够控制分选密度的波动范围在±0.005以内。
(3)能够处理粒度范围很广的物料,其最大粒度可达35.6cm。
(4)因其处理量高和占地空间小,投资和运输费用相对较低。
(5)能够改变分选密度以适应市场需求的变化。
(6)能够处理数质量发生波动的入料。
1.块煤重介质分选重介质分选是实验室浮沉试验在工业上的实际推广,浮沉试验可用作重力分选的标准(效率100%)。
工业生产与实验室的浮沉分离并不完全相同,其理由是:工业采用悬浮液而不是真溶液作为分选介质;入料的给入和浮物沉物的排放会赢棋分选介质的扰动;分选槽中需要搅拌或上升流以保证分选介质呈悬浮状态;由于实际要求处理量高,不允许有足够的停留时间使邻近密度物得到完善分选。
理论上,任意力度均可进行重介质分选;实际上,重介质分选的粒度范围大约为0.5~150mm,有时粒度达到35.6mm也可以进行分选。
粒度大约在6.3mm以上的物料通常在静态重介分选机中处理,而粒度在0.5mm~6.3mm的物料一般在离新分选机(如重介旋流器)中分选。
理想的分选介质应是真溶液,并具有下列性质:价格低廉、易于与水混合、能够在较宽的密度范围内调节、稳定、无毒、无腐蚀性和粘度低。
虽然理想的介质并不存在,但已经开发了许多种重介质,并正在应用于工业生产中,将原煤分选为矸石和商品精煤。
根据实际生产情况,任何介质应具有下列性质:从使用角度应价格便宜,物理性质稳定、在分选过程中不分解、化学性质不活泼且不与煤气反应、易从产品中脱除、易从矸石中回收、在要求的分选密度时粘度低、在要求的密度范围内白吃密度稳定。
重介质选煤工艺简介

重介质选煤工艺简介内容介绍一、重介质选煤的基本概念二、重介质旋流器分选40-0mm不脱泥原煤的准备三、重介质旋流器分选40-0mm不脱泥原煤的工艺及设备四、煤泥水处理五、厂外产品的储运说明重介质选煤在我国的一九五八年开始,至今已45年了,但是到目前采用全重介旋流器选40-0mm不脱泥原煤新型工艺应用于工业生产在国内和国际都是最新的。
一、重介质选煤的基本概念重介质选煤是利用纯煤夹矸煤之间密度的不同,在一种特定密度的溶液(介质)中,使纯煤与夹矸煤或矸石进行分离的一种选煤方法,因此它的选煤效率和精确度较高。
重介质选煤按其采用的介质的不同可分为重液(真溶液)和重悬浮液(非均质溶液)先煤两种。
二、重介质旋流器分选40-0mm不脱泥原煤准备原煤进入筛分破碎车间,分别给入两台原煤分级筛,分级粒度为40mm。
+40mm的筛上产品分别给入两台手选皮带运输机,人工拣除杂物后分别给入两台原煤破碎机,破碎后的物料给入皮带运输机,再经转载皮带运输机将原煤返回。
原煤筛分破碎系统,从而构成半路破碎,目的是确保进入选煤车间入选原煤的粒度不超限和严格杜绝铣器、木块等杂物进入洗煤系统。
原煤分级筛筛下物(—40mm)自流到原煤上仓皮带机经转载皮带机把原煤给入原煤中间仓,再把原煤给入位于仓下的皮带机,再经转载皮带机把原煤运至主洗厂房的煤介桶。
至此完成了原煤作业的全过程。
三、重介质旋流器选40-0mm不脱泥原煤的工艺及设备1.分选工艺工艺流程如图所示进入煤介混合桶的物料,经煤介泵以一定压力给入φ650mm主选旋流器,主选旋流器的溢流(精煤)经精煤弧形筛脱介,其筛上物进入精煤振动筛脱介,脱介筛第二段设喷水用于清洗产品,脱介筛上产品再经精煤离心机脱水脱介后,卸入精煤皮带运输机进入产品储运系统。
精煤离心机的离心液进入精煤稀介桶(进入稀介系统)。
精煤弧形筛筛下液进入精煤分流箱,分流箱中的一部分进入煤泥介质混合桶,另一部分与其它两台弧形筛筛下液一同进入介质汇集槽返回煤介混料桶。
重介质
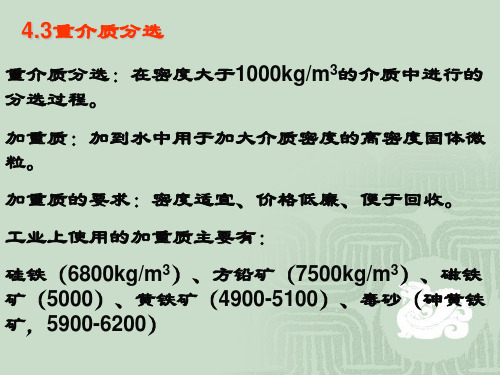
4.3.1.4 影响重悬浮液性质的因素
影响重悬浮液性质的因素主要包括悬浮液的固体 体积分数、加重质的密度、粒度和颗粒形状等。 固体体积分数影响重悬浮液的密度和粘度,悬浮 液的粘度随固体体积分数的增加而增加,存在临 界固体体积分数。
加重质的密度影响重悬浮液的密度,颗粒粒度 和形状影响悬浮液的粘度和稳定性。
分选:
介质回收:
介质的净化与再生:
从分选原理来看,重介质分选只和密度有关, 与粒度、形状无关,实际中与颗粒的密度有较 大关系。 主要是细粒级
用重介质分选煤时,给料的下限为3-6mm,上 限为300-400mm。用重介质分选金属矿石时, 给料的下限为1.5-3.0mm,上限为50-150mm, 若用重介质旋流器分选,给料粒度下限可以降 低到0.5-1.0mm。
优点:结构简单、运转可靠、便于操作,介 质循环量小。 缺点:分选面积小。
4.3.2.3 重介质振动溜槽
4.3.2.4
重介质旋流器
旋转重介质流 重介质流的快速旋转,加重质颗粒受到了相当大 的离心力场作用,使得加重质颗粒中密度较高、 粒度较粗的颗粒,在离心力作用下向器壁及底部 沉降,因而悬浮液受到了浓缩作用,导致了悬浮 液其密度在整个旋流器内呈不均匀分布。 分布规律是:悬浮液密度由中央向外随半径的增 加而增高;若旋流器正立安置,由上而下,则悬 浮液密度的分布是由小到大。
4.3重介质分选
重介质分选:在密度大于1000kg/m3的介质中进行的 分选过程。 加重质:加到水中用于加大介质密度的高密度固体微 粒。
加重质的要求:密度适宜、价格低廉、便于回收。
工业上使用的加重质主要有:
硅铁(6800kg/m3)、方铅矿(7500kg/m3)、磁铁 矿(5000)、黄铁矿(4900-5100)、毒砂(砷黄铁 矿,5900-6200)
重介质选煤技术.ppt

选煤厂员工技术培训
1、概述
1.1 重介质旋流器选煤的发展 重介质旋流器是在分级旋流器的基础上演变而来。
1945年荷兰国家矿山局提出了用重介质旋流器选末煤的方 法,并发明了DSM(圆柱圆锥形)重介质旋流器。由于 加重质由黄土改为磁铁矿,使这一技术真正用于工业。美、 德、英、法等国相继购买了这一专利应用于选煤,并不断 创新,研制了许多新型重介质旋流器:
24
选煤厂员工技术培训
3.2 加重质的选择
3.2.2 加重质的粒度组成特性
各国对磁铁矿粉的粒度要求是不同的,如:
25
选煤厂员工技术培训
3.2 加重质的选择
3.2.2 加重质的粒度组成特性
各国对磁铁矿粉的粒度要求是不同的,如:
26
选煤厂员工技术培训
3.2 加重质的选择
3.2.2 加重质的粒度组成特性
10
选煤厂员工技术培训
1、概述
1.4 重介质旋流器分类 (1)按其外形结构可分为:圆柱形、圆柱圆锥形重介质旋流器两 种。 (2)按其选后产品的种类可分为:二产品重介质旋流器;三产品 重介质旋流器。 (3)按物料给入旋流器的方式可分为:周边(有压)给原煤、给介 质的重介质旋流器;中心(无压)给原煤、周边(有压)给介质的重 介质旋流器。 (4)按旋流器的安装方式可分为:正(直)立式、倒立式和卧式三 种。
6
选煤厂员工技术培训
1、概述
1.1 重介质旋流器选煤的发展 80年代至90年代对重介质旋流器选煤工艺与设备进行
了一系列的改革和创新。先后推出重介质旋流器分选500mm不脱泥原煤的工艺;有压给料二产品和三产品重介质 旋流器;无压给料二产品和三产品重介质旋流器;分选粉 煤的小直径重介质旋流器以及“单一低密度介质、双段自 控选三产品(四产品)的重介质旋流器”选煤新工艺。1998 年推出了大型简化工艺重介质选煤技术,旋流器直径达到 1200/850,2003年旋流器直径达到1400/1000。到2005年 底,中国已有100多个选煤厂装备有上述各类重介质旋流器 约400多台。
重介质选煤工艺及分选效果影响分析

重介质选煤工艺及分选效果影响分析一、引言本文将从重介质选煤工艺的基本原理和流程、分选效果的影响因素等方面展开分析,以期为煤炭行业提供参考和帮助。
二、重介质选煤工艺的基本原理和流程重介质选煤工艺是指利用密度差异将煤和脏矸分离的一种选煤方法,其基本原理是通过在重介质中将煤和矸石分离,从而达到提高煤品质的目的。
在实际工艺中,重介质选煤的流程一般包括破碎、磨矿、重介质分选、浮选等环节。
下面将对这些环节进行具体介绍。
1. 破碎:煤炭矿石在选煤处理前需要先进行破碎,以便更好地进行下一步的选煤工艺。
破碎的目的是将原始煤炭矿石分解成较小的颗粒,方便后续的处理。
2. 磨矿:磨矿是为了将煤矿石中的煤与脏矸分开,一般采用球磨机或者辊磨机进行磨矿处理。
通过磨矿可以较为有效地将煤和脏矸进行分离。
3. 重介质分选:在重介质分选过程中,将煤、矸石和介质(一般是重质液体或者重质气体)混合在一起,利用它们之间的密度差异进行分离。
通过动力装置使得介质形成旋涡,然后将煤矸石混合物投入旋涡中,在旋涡中由于密度差异的作用,煤炭和矸石将会获得不同的位移,从而实现分离。
4. 浮选:在重介质分选之后,还需要进行浮选工艺,将煤炭进行进一步的分离和提纯,以获得更高品位的煤炭产品。
三、分选效果的影响因素重介质选煤工艺的分选效果受到很多因素的影响,下面将对其进行具体介绍。
1. 煤炭性质:煤炭的物理和化学性质对分选效果有着重要的影响。
主要包括煤的密度、粒度、矿物组成、灰分、硫分等参数。
一般来说,煤的密度越大、粒度越细,分选效果越好,而灰分、硫分等杂质越低,也有利于分选。
2. 介质性质:介质的选择和性质直接影响到分选效果。
一般采用的介质有重质液体和重质气体,不同的介质会对分选效果产生不同的影响。
其参数包括粘度、密度、流动性等。
3. 设备参数:重介质选煤设备的参数也会对分选效果产生重要影响。
主要包括旋涡器的结构和参数、浮选机的类型和规格等。
合理的设备参数能够提高重介质选煤工艺的分选效果。
重介分选技术
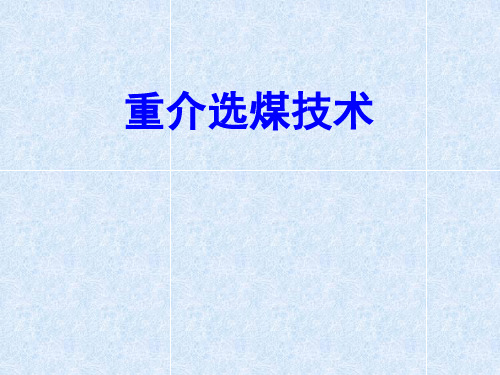
该旋流器分选时,因为物料与悬浮液分开给入,是该类型旋流器具有如下特点: ① 有利于悬浮液密度的测定和调整; ② 物料不用定压漏斗或泵给入,即可降低厂房高度,减轻泵与管道的磨损; ③ 同时高密度物料与旋流器壁接触时间短,物料粉碎程度低,旋流器各部件磨损比D.S.M 小,使用寿命长。
D.W.P型重介质旋流器的技术规格
Whirlpool分选机(简称DWP)。一种无椎体的旋流器,如国产的HMCC和英国的沃西尔圆筒 重介旋流器。
机体为圆筒形,筒长与直径之比为3:1~6:1,它是一种无压给料式重介旋流器。该旋流器 的特点是:分选物料与悬浮液分开给入,物料属无压自重给料,在给料箱内液加入少量悬浮液。 悬浮液的泵压为0.06~0.15MPa。沿切线给入圆筒下部(圆筒呈25°~30°倾角安装)。它的分 选过程是沿切线压入的悬浮液,从底至顶造成一股上升的空心旋涡流。沉物与一部分高密度 (起浓缩作用)悬浮液沿筒壁上升,从沉物排出口排出。浮物与低密度悬浮液聚集在涡流中心 向下流动,通过排出口排出。这种分选过程也称为动力-旋涡过程。
重介选煤技术
重介质选煤因具有分选精度高、对原煤适应性强、易于实现自动控制等优点, 已成为选煤工业发展的首选技术。在主要产煤国家,重介质选煤已上升为主导地位。 20世纪80年代,国外基本以跳汰选为主。到90年代,重介质选煤比例已由第二位上升 为第一位。目前,美国的重介质选煤比例已占66%,法国占60%,加拿大为56%,澳 大利亚和南非跳汰选煤已基本淘汰。值得注意的是,大直径重介质旋流器、有压给料 和无压给料三产品重介质旋流器和煤泥重介质旋流器的出现,重介质旋流器的应用已 越来越广泛。美国使用重介质旋流器的选煤厂的比例已上升到51.5%,澳大利亚新 建的选煤厂大多采用大直径重介质旋流器作为主再选设备,我国新建选煤厂和老厂技 术改造也广泛采用该项技术。
固体物料分选学---重介质分选

理细粒级矿物,采用小冲程、高冲次。
22
16.3.2 给料水和筛下补加水
给料浓度一般为30-50%。 筛下补加水: 处理窄级别物料时可大些,提高分层速度, 处理宽级别物料时应小些,以增加吸入作用。
16.3.3 床层厚度和人工床石
床层厚度:筛板到溢流堰的高度。 取决于跳汰机类型、欲分选组分的密度差和给 料粒度决定。 密度差大:薄—增加分层速度,提高处理能力 密度差小:厚—提高高密度产物质量
d 3
6
a
e 6 3d d v td 6 3 g d 2 v c 2d 6 3 d d v c td 6 3 a
d d v t g 6 d v c 2 d d v c t a
10
代入vc=颗粒速度v-介质速度u,得颗粒加速度:
d d v t g 6 d v u 2 a
重力加速度因素 只与密度有关 阻力加速度因素
与密度、粒度有 关;高密度细粒 与低密度粗粒不 能有效分层
附加推力加速 度因素 只与密度有关 水流a向下时: 高密度颗粒滞 留上层,a应 尽量减少
11
16.1.3 偏心连杆机构跳汰机内水流的运动特性及 物料的分层过程 偏心连杆式传动机构
19
16.2 跳汰机
常用的跳汰机:隔膜跳汰机、圆形跳汰机、无 活塞跳汰机、动筛跳汰机和离心跳汰机等。 旁动型隔膜跳汰机
演
筛
板
示
隔
膜
20
16.3 影响跳汰分选的工艺因素
可调节因素:冲程、冲次、给料水、筛下补加 水、人工床层厚度、给矿量等
不可调或调节有限的因素:给料的密度和粒度 组成、床层厚度、筛板落差、跳汰周期曲线等
重选法选矿方法及工作原理

重选法选矿方法及工作原理重选法选矿方法及工作原理矿山机械行业选矿方法重选工艺比较简单,采用的重选选矿设备也比较简单,不需要昂贵的浮选药剂,尾矿对环境的污染也比较小。
重选法根据作用原理的不同,可以分为重介质选矿、跳汰选矿、摇床选矿、溜槽选矿、水力或风力分级、洗矿。
1、重介质选矿:重介质选矿是在比重较大的介质中使矿粒按比重分选的一种选矿方法。
重介质的比重介于重矿粒比重和轻矿粒比重之间,把物料给入重介质中,结果比重大于重介质比重的矿粒则下沉,比重小于重介质比重的矿粒则浮在重介质的表层。
然后将已分离的轻、重矿物分别截取,即完成分选过程。
常用的重介质选矿设备振动溜槽主要由槽体、传动装置、分离隔板和机架四部分组成,常用于赤铁矿、锰矿等黑色金属矿石的选别,也可用于其它有色金属矿石的选别。
重介质振动溜槽工作时,先将浓度较高的重介质从振动槽的首端给入槽中,在槽体的往复摇动作用下,介质转入悬浮状态,形成流动性较大的具有一定分选比重的介质床层。
然后,原矿从槽的首端给入,由于槽体的运动,矿石边向前运动,边开始按比重进行分层。
比重大于分选比重的重矿粒,穿过介质床层,沉积于槽的底部,并在槽体摇动作用下向前滑行,从分离隔板下面排出。
比重小于分选比重的轻矿粒,则悬浮于介质床层的上层,随介质的流动,由分离隔板上面排出。
由水室通过两层筛板的筛孔给到槽内的上升水,主要是控制和调节介质床层的稳定性和均匀性,并帮助介质床层中的矿石移动。
分选出的轻重产物分别入脱介筛,脱除的稀介质经脱水后再循环使用。
2、跳汰选矿:跳汰是最重要的重选法之一。
跳汰过程的实质是使不同比重的矿粒混合物,在垂直运动的变速介质(水或空气)流中按比重分层,比重小的矿粒位于上层,比重大的矿粒位于下层。
然后再借助机械的作用和水流的作用将其分成比重不同的产物,分别排出。
河南省荥阳市矿山机械制造厂跳汰选矿设备跳汰机分为水力跳汰机和风力跳汰机,风力跳汰机用得很少,根据结构和水流运动方式不同,水力跳汰机可分为活塞式、隔膜式、无活塞式、水力鼓动式和动筛式跳汰机五种。
- 1、下载文档前请自行甄别文档内容的完整性,平台不提供额外的编辑、内容补充、找答案等附加服务。
- 2、"仅部分预览"的文档,不可在线预览部分如存在完整性等问题,可反馈申请退款(可完整预览的文档不适用该条件!)。
- 3、如文档侵犯您的权益,请联系客服反馈,我们会尽快为您处理(人工客服工作时间:9:00-18:30)。
3-3 、沉降规律 煤粒在介质中的分离运动服从干扰沉降的规律。被分选 煤粒及加重质颗粒分别进行干扰沉降。若两者粒度接近时, 两者的干扰沉降互相影响,于是正常的重介分选被破坏。这 是决定有效分选粒度下限的最重要因素。 总之,是在不同条件下,重介浮沉+干扰沉降
3-4、各粒级以及总的分选精度,取决于其分选力和干扰力的 作用强度和物料在分选机的停留时间(即粒群分离动力学规律)
图5 浅槽分选机原理
* 分选也受等沉比限制。但是,密度低于介质密度的精煤。不论 粒度大小,均浮起进精煤。只有密度接近介质密度的高灰中煤 和细粒矸石,其去向受等沉比限制。 例如:
d中 矸 床 2.6 1.65 0.95 19 d矸 中 床 1.7 1.65 0.05
b 旋流器内液流轴向速度 分布图
c 激光测速仪实测出的水力 旋流器内液流径向速度
图10
在水力旋流器中流体的基本运动形式和速度分布
2-3-2 密度分布
图11 旋流器中悬浮液的密度场 a-圆筒圆锥型旋流器,悬浮液的入料密度为1.40t/m3; b-圆筒型旋流器,悬浮液的入料密度为1.40t/m3;
2-3-3 旋流器的分选过程
4-5、三产品重介旋流器
三产品重介旋流器可简化流程,可用低密度介质实现高密 度分选,但分选精度稍差(二产品Ep = 0.02 ~0.04 ,三产品一 段 Ep1 = 0.02 ~0.05 ,二段 Ep2 = 0.04 ~0.07 ), 而且二段分选密 度不易调节。
4-6 、精选型三产品旋流器 精选型三产品旋流器具有极高分选精度适合极难选煤 和超纯煤的制备。
图12 旋流器的分选过程
悬浮液和煤粒进旋流器后,分别开始离心干扰沉降。并 在入料压力下被推向锥体和底流口。 按离心干扰沉降规律,精煤颗粒逐渐穿过轴向零速包络 面,进入内旋流,经溢流口排出成轻产物。 所有不能穿越零速包络面的高密度颗粒运动到锥底,由 底流口排出成重产物。 由于离心干扰沉降的结果,实际分选密度会高于介质密 度,细粒的分选密度和Ep值均会高于粗粒的相应数值。 ⑤ 可能达到的有效分选粒度下限,约为介质粒度d50的4-5倍。
在运动的介质中 介质会沉降分层。为保证介质相对均匀,常采用流动介质。 如与重力方向相反的上升流(浅槽分选机)u 。 于是:
对浮粒,上浮速度 +u
对静止颗粒,获得上浮速度 u
对沉粒,下沉速度 -u
显然: u越大,被带到溢流的颗粒的密 度越高,颗粒越细,被带到溢 流的颗粒的密度越高。
图4 矿粒处在运动介质中
(3) 重悬浮液分选原理剖析
3-1、重介选的基本要求 重介质悬浮液比较稳定,即加重质颗粒沉降慢,而同时 被分选的煤粒该浮的快速浮起,该沉的快速下沉。即要求加 重质粒度细(密度愈大要求越细),而被分选的煤粒相对较 粗,即要求加重质的粒度与被分选煤粒的粒度有较大差别 (约7~10倍)才能实现重介质分选; 3-2、阿基米德原理 煤在重悬浮液中分选和在真重液中一样,服从阿基米 德原理:密度小于颗粒周围介质平均密度者上浮,若大于 则下沉。
4-7 煤泥重介旋流器 原理:当煤的粒度是加重质粒度的10倍以上时,是重介选 原理;当煤粒度接近加重质粒度时,离心干扰沉降起作用,分 选效果变差(图13)。要降低分选粒度下限,可提高离心因数、 使用较高密度的超细加重质。 优点: * 分选精度高、下 限可达到0.1mm; * 费用较低(在重 介选煤厂中使用时); * 对氧化煤、难浮 煤泥具有优势。
方铅矿(7.8 t/m3)
2. 重介质选煤设备
(1) 重力分选机(分选槽),作为+13mm(或+6mm)块 煤的分选设备,现在都用悬浮液——磁铁矿粉和硅铁粉。
图1 重介质静力分选基本原理 1—给料;2—水平流动区;3—精煤:4—沉物; 5—上升流介质入口;6—水平流介质入口
1-1 设备种类
由于产品排出方法不同,演变出多种形式,包括两产品和 三产品。
溴仿(2.81 kg/l)等
无机盐溶液: 氯化铁,氯化钙,氯化锰,氯化
钡和氯化锌溶液等
重悬浮液:磨细高密度矿物+水 可用矿物有: 粘土(2.6t/m3) 煤矸石(2~2.6t/m3)
砂(2.65 t/m3)
重晶石(4.5 t/m3) 磁铁矿(5.18 t/m3)
硅铁(15%si)(6.8 t/m3)
在此条件下,若入料上限1mm,那么分选下限能达到 0.3mm左右。粒限越窄,中煤含量越少,分选精度越高。
(5) 重介质选煤的优点与缺点 * 优点 a.分选精度高,适合于难选和极难选煤; b.分选粒度范围宽; 静力分选槽1000~6mm 重介旋流器100(80,50)~0.2mm, 减少浮选量,提高细粒级的 分选效率。 c.结构简单,特别是重介质旋流器; d.分选比重易调节(三产品旋流器二段除外)容易自动化。 * 缺点 a.流程复杂(增加介质回收再生系统); b.能耗较大,介质有损耗,设备磨损大,加工费较高; c.重介质旋流器对入料煤质波动的适用能力很差。
(4) 各种重介分选设备的特点
4-1 强斯水砂分选机和水介旋流器 主要分选作用是干扰沉降,因而入选粒度范围的宽窄对 分选结果有较大影响,其分选精度也远不如其它真正的重 介质分选机和重介旋流器。 4-2 浅槽分选机 应用最广: 用于动力煤块(+6mm)和炼焦煤的预分选, 其结构简单,处理量大(>100t/m· h),分选精度高 (Ep=0.02-0.04)更重要的是可用较低密度介质(1.5kg/l) 实现较高密度的分选(1.9-2.0kg/l)。但是循环介质量大(达 到1:2),并且排矸链条磨损大。 假若上升介质流增大,干 扰沉降效应就明显,介质密度与实际分选密度的差距也增 大。
⑥ 轴向零速络面的形状,其最下端在何处结束,受到各种 因素的影响:
a : 入料密度组成 b : 溢流口和底流口尺寸比例 c : 给料量大小 d : 介质性质(粒度组成,煤泥含量,浓缩度) e : 入口介质压力 f : 旋流器的结构
⑦ 包络面最下端的分离密度,应该就是旋流器的分选密度。 该分选密度既与包络面下端介质密度有关,也与该处干 扰沉降强度有关,取决于干扰沉降作用的强弱。实际分选 密度也不同程度地高于该处实际介质密度。
图2 重介分选机的基本形式
1-2 重力分选机的原理
在静止的均匀介质中
颗粒所受的力:
重力 F重=ρ固· V· g 浮力 F浮=ρ介· V· g 倘若 F重-F浮=( ρ固-ρ介)· V· g
图3 矿粒在静止介质中受力
即 F重>F浮,颗粒下沉,粒越大,沉得越快。
F重=F浮,颗粒静止不动。 F重<F浮,颗粒上浮,粒越小,浮得越慢。
2-2
重介质旋流器的种类
图8 两产品重介质旋流器的基本形式
图9 三产品重介质旋流器的2-3-1 旋流器中流体运动的基本形式及速度分布
1.外旋流; 2.空气柱; 3.内旋流; 4.最大切线速度轨迹面; 5循环流; 6.轴向零速包络面;
7.短路流
a 水力旋流器中流体的 基本运动形式
国内生产经验: 简化的生产流程:将部分循环介质从精煤弧形筛下分 流出,用泵给入煤泥重介质旋流器分选。认为这样做可以 得到较细的介质,希望达到更细的分选粒度下限。实际上 部分地起到改善主选旋流器分选下限,降低从精煤磁选尾 矿回收的粗粒精煤的灰分。
多用φ150~300mm重介旋流器,处理<0.5mm煤泥 加重质粒度:100%<0.075mm 分选精度: EP=0.06~0.10; 介 耗: 2kg/t原煤左右。 精煤回收:弧型筛、高频筛、离心机等(0.2~0.3mm)
浮选
其它
9.5
5
受2008年开始的世界性经济危机对我国经济发展影响,同时 我国经济调控和转型,要求到2020年单位GDP碳排放量降低 40~45%和不断提高可再生能源比例等政策,对我国煤炭生产和 洗选的发展都产生重要影响
二、重介质选煤的历史和现状 1 . 重介质选煤的历史 有机重液: 三氯乙烷(1.46kg/l) 四氯化碳(1.6 kg/l) 二溴乙烷(2.17 kg/l)
三、重介质选煤的原则工艺流程
主要有三类:
1.块煤排矸(+13或+25mm进重力分选机或动筛跳汰机),末
煤不入选;
2. 块煤排矸(重力分选机或动筛)+末煤重介旋流器;
3. 块煤(+50或+80mm)破碎与末煤混合用旋流器分选。
需要全粒级入洗时,第3类流程较简单,但在没有原煤均质化
的情况下,第3类流程不是最优选择。
存在问题: ①分流的循环介质量有限; ②大型旋流器分选粒度下限较粗,部分煤泥损失到了矸 石和中煤中(中、矸磁选尾矿中); ③煤泥重介旋流器的轻产物需经分级处理(将小于分选 粒度下限的部分分离出去)。
4-8 TBS分选机
原理:干扰沉降分级和分选。单一密度的物料(如砂子) 它就是分级机,多密度多粒度入料可以作为按密度分选的设 备,但是粒度范围受限制,即
颗粒粒度mm 图13 颗粒粒度对重介质分选精度的影响
煤泥重介的缺点:
*介质制备费用增加; *介质回收的难度增大,介耗增加;
*细粒精煤回收困难;
煤泥重介现状与经验:
在美国、南非、澳大利亚和俄罗斯都有研究,并 在生产中成功地应用。我国近年来也注意该工艺的开 发和应用。
国外生产经验:
分选粒度范围:1~0.1mm; 精煤回收用打击弧形筛、德瑞克高频筛分级(0.15或0.1mm); ①尽可能预先脱除-0.1mm部分; ②加重质的粒度:>90%-40μm,>50%-10μm; ③循环介质要退磁。
因此,要根据煤质和分选密度的要求,可在介质密度、上 升流、水平流 、循环介质量和矸石排放速度等因素进行合理调 节,以便达到良好的分选效果并降低介耗。
(2) 离心力分选机——重介质旋流器
为提高重介质分
选机的生产能力及分 选更细粒度的煤,开 始研究分离力大得多 (十几倍到几十倍重 力)的分选机——重 介质旋流器。 1945年荷兰矿山局 研制了DSM旋流器。