铜冶炼水平与工艺水平
铜的精炼与冶炼
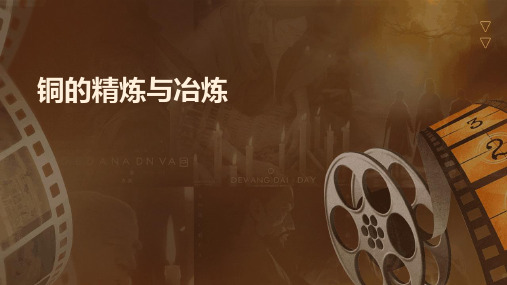
利用电解原理将粗铜提纯为高纯度铜,具有工艺成熟、操作简便的优势。
THANK YOU
鼓风炉熔炼
将铜矿石、熔剂和燃料放 入鼓风炉中,通过鼓入空 气进行氧化熔炼。
电炉熔炼
利用电能将矿石熔化,再 通过加入还原剂进行还原 熔炼。
铜的湿法冶炼
浸出
将矿石中的有用成分浸出到溶液 中,再通过化学反应将其提取出
来。
萃取
利用不同物质在两种不混溶液体中 的溶解度差异,实现有用成分的分 离和提取。
电积
将溶液中的铜离子还原成金属铜, 并收集沉积的铜粉。
03
铜的精炼工艺
粗铜的熔炼与铸造
熔炼
将铜矿石、返回料和熔剂等原料放入高温熔炉中熔化,形成粗铜。
铸造
将熔融的粗铜注入模具中,冷却凝固后形成阳极铜块。
铜的电解精炼
电解液制备
将硫酸和铜阳极板溶解在水中, 制成硫酸铜溶液作为电解液。
电解过程
将阳极铜块作为电解的阳极,阴 极为纯铜,通过直流电进行电解 。在电解过程中,阳极上的铜逐 渐溶解,并在阴极上析出纯铜。
全球铜资源分布广泛,但主要集中在 智利、美国、中国、秘鲁等国家和地 区。这些国家的铜矿储量和产量均居 世界前列。
铜的冶炼历史与现状
铜的冶炼历史
铜的冶炼技术可以追溯到公元前4000年左右的美索不达米亚文明时期。随着时 间的推移,铜的冶炼技术不断发展,逐渐形成了现代的冶炼工艺。
铜的冶炼现状
目前,全球铜冶炼产能主要集中在中国、美国、智利等国家。由于环保要求的 提高和资源的日益枯竭,现代冶炼工艺趋向于更加环保、节能和高效。
杂质去除
电解过程中,阳极上的其他金属 杂质也会溶解进入电解液中,通
过适当的处理方法将其去除。
铜冶炼技术对比解析

1992 1999 5家投产 16万吨/年矿 铜
单炉最高 产能
原料适应 性
原料预处 理
较差
粒度<1mm, 深度干燥, H2O<0.3%
适应性强
制粒或增湿, H2O 9%~11%
强
干燥,H2O< 1%
适应性强
适应性强
适应性强
粒度<100mm, 粒度<100mm, 制粒或增湿, H2O 10%~12% 不需要干燥。 不需要干燥。
S捕集率 炉寿命
150天
业内认可的先进熔炼工艺
闪速熔炼和熔池熔炼: ※Outokumpu闪速熔炼 ※ 浸没喷枪式熔炼(ISA/Ausmelt) ※ 三菱熔炼
闪速熔炼技术的进展
闪速炼铜工艺
●第一座炼铜闪速炉于1949年在芬兰哈里亚瓦尔塔 冶炼厂投入工业生产;目前还用于镍精矿的熔炼 ;1978年开始进行铜精矿的一步炼铜;1995年开 始进行冰铜的吹炼。 ●至今已有40台炼铜闪速炉建成投产,目前在运行 的有37台(其中有3台一步炼铜闪速炉,2台冰铜 吹炼闪速炉),6台炼镍闪速炉在生产。 ●炉体冷却结构的改进、冷却强度的提高,闪速炉 的单炉产能提高,最大达到原设计的3.65倍;闪 速炉的炉寿命延长,最长达到15年,一般10年左 右
产能大:单套系统最大铜产能超过40万吨/年
送风氧浓高:闪速熔炼氧浓达90%,ISA、
三菱、诺兰达熔炼氧浓达到65%,55%和 45%
自热或半自热熔炼:有效利用硫化矿物燃烧
所产生的热量;
冰铜品位高:均超过60%,可以高达75%
现代强化熔炼工艺的特点
高熔炼强度:闪速熔炼单炉铜精矿处理量首先突 破100万吨/年以上;Isa炉单炉铜精矿处理量达到 130万吨/年;三菱炉精矿处理量将超过100万吨/年 (温山)。 硫捕集率高,环保好:一般均超过95%。闪速熔 炼和三菱熔炼超过了99%,吨铜S的排放量不到 2kg,是最清洁的铜冶炼工艺 工艺控制自动化程度高:闪速炉实现了计算机在 线控制。
铜冶炼技术

铜冶炼过程中会产生大量的废水,这些废水中含有重金属 离子和有害物质,如果未经处理直接排放,会对水体造成 严重污染。
固体废弃物处理
铜冶炼过程中会产生大量的固体废弃物,包括炉渣、污泥 等,这些废弃物如果未经处理随意堆放,会对土壤和环境 造成污染。
铜冶炼过程中的安全问题
高温熔炼过程
铜冶炼过程中需要将铜矿石高温熔炼成铜液,这个过程中如果操作 不当,会造成高温烫伤和爆炸等安全事故。
同时将铜提取出来。
熔炼设备
采用鼓风炉、电炉或反射炉进行 熔炼。
熔炼过程
熔炼过程中需加入适量的熔剂, 以除去杂质和调节熔融物的成分
。
铜的吹炼
吹炼目的
01
通过向熔融物中鼓入空气,使杂质氧化并从熔融物中分离出去
,得到粗铜。
吹炼设备
02
采用转炉或连续吹炼炉进行吹炼。
吹炼过程
03
吹炼过程中需控制温度和气氛,以保证杂质的有效去除和粗铜
的质量。
铜的电解精炼
电解精炼目的
通过电解过程,使粗铜中的杂质进入阳极泥中, 得到纯度较高的电解铜。
电解设备
采用电解槽进行电解精炼。
电解过程
电解过程中需控制电流密度、电解液成分和温度 等参数,以保证电解铜的质量。
03
铜冶炼的环保与安全
铜冶炼过程中的环保问题
废气排放
铜冶炼过程中会产生大量的废气,包括二氧化硫、氮氧化 物等,这些废气如果未经处理直接排放,会对大气环境造 成严重污染。
铜精矿的焙烧与制团
焙烧目的
通过高温焙烧,使铜精矿 中的硫氧化,生成二氧化 硫气体,同时去除部分杂 质。
焙烧方式
采用回转窑或沸腾焙烧炉 进行焙烧。
制团
铜冶炼水平与工艺水平

铜冶炼水平与工艺水平1)火法冶炼工艺当前,全球矿铜产量的75%-80%是以硫化形态存在的矿物经开采、浮选得到的铜精矿为原料,火法炼铜是生产铜的主要方法,特别是硫化铜精矿,基本全部采用火法冶炼工艺。
火法处理硫化铜精矿的主要优点是适应性强,冶炼速度快,能充分利用硫化矿中的硫,能耗低。
其生产过程一般由以下几个工序组成:备料、熔炼、吹炼、火法精炼、电解精炼,最终产品为电解铜。
原料制备工序:将铜精矿、燃料、熔剂等物料进行预处理,使之符合不同冶炼工艺的需要。
熔炼工序:通过不同的熔炼方法,对铜精矿造硫熔炼,炼成含铜、硫、铁及贵金属的冰铜,使之与杂质炉渣分离;补出的含二氧化硫烟气经收尘后用于制造硫酸或其他硫制品,烟尘返回熔炼炉处理。
吹炼工序:除去冰铜中的硫铁,形成含铜及贵金属的粗铜,炉渣和烟尘返回上一工序处理。
火法精炼工序:将粗铜中硫等杂质进一步去除,浇铸出符合电解需要的阳极板。
电解精炼工序:除去杂质,进一步提纯,生产出符合标准的阴极铜成品,并把金银等贵金属富集在阳极泥中。
传统熔炼方法如鼓风炉熔炼、反射炉熔炼和电炉熔炼,由于效率低、能耗高、环境污染严重而逐渐被新的富氧强化熔炼工艺所代替[[3]新的富氧强化熔炼可分为闪速熔炼和熔池熔炼两大类,前者包括奥托昆普型闪速熔炼和加拿大国际银公司闪速熔炼等,后者包括诺兰达法、三菱法、艾萨法、奥斯麦特法和瓦纽可夫法以及我国自主开发的水口山法、白银炉熔炼、金峰炉熔炼等技术。
铜铳吹炼方法有传统的卧式转炉、连续吹炼炉、虹吸式转炉。
新型吹炼技术包括艾萨吹炼炉、三菱吹炼炉和闪速吹炼炉等。
粗铜的火法精炼在阳极炉内进行,对于转炉产出的液态粗铜采用回转式阳极炉或固定式反射炉精炼,经氧化、还原等作业进一步脱除粗铜中的铁、铅、锌、砷、锑、铋等杂质,并浇铸成含铜99.2%-99.7%的阳极板。
铜电解工艺有传统电解法、永久阴极电解法和周期反向电流电解法3种。
目前大多数电解铜厂都使用传统电解法,永久阴极电解法和周期反向电流电解法是20世纪70年代以来发展的新技术。
我国铜冶炼技术的进步及发展
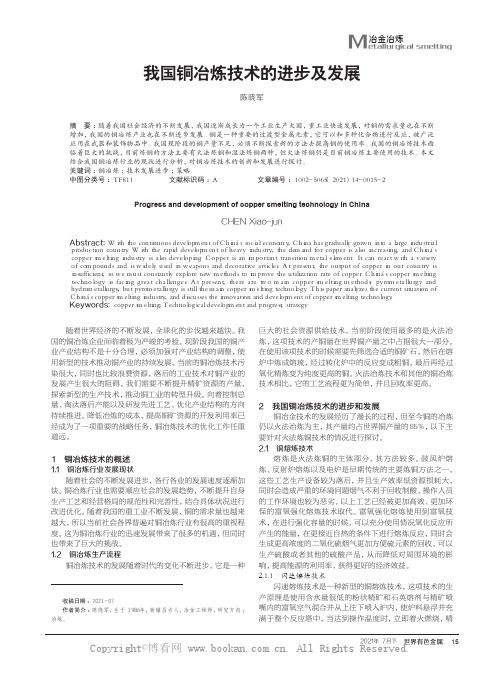
冶金冶炼M etallurgical smelting 我国铜冶炼技术的进步及发展陈晓军(新疆五鑫铜业有限责任公司,新疆 昌吉 831100)摘 要:随着我国社会经济的不断发展,我国逐渐成长为一个工业生产大国,重工业快速发展,对铜的需求量也在不断增加,我国的铜冶炼产业也在不断进步发展。
铜是一种重要的过渡型金属元素,它可以和多种化合物进行反应,被广泛应用在武器和装饰物品中。
我国现阶段的铜产量不足,必须不断探索新的方法去提高铜的使用率。
我国的铜冶炼技术面临着巨大的挑战,目前炼铜的方法主要有火法炼铜和湿法炼铜两种,但火法炼铜仍是目前铜冶炼主要使用的技术。
本文结合我国铜冶炼行业的现状进行分析,对铜冶炼技术的创新和发展进行探讨。
关键词:铜冶炼;技术发展进步;策略中图分类号:TF811 文献标识码:A 文章编号:1002-5065(2021)14-0015-2Progress and development of copper smelting technology in ChinaCHEN Xiao-jun(Xinjiang Wuxin Copper Co., Ltd., Changji 831100, China)Abstract: With the continuous development of China's social economy, China has gradually grown into a large industrial production country. With the rapid development of heavy industry, the demand for copper is also increasing, and China's copper smelting industry is also developing. Copper is an important transition metal element. It can react with a variety of compounds and is widely used in weapons and decorative articles. At present, the output of copper in our country is insufficient, so we must constantly explore new methods to improve the utilization rate of copper. China's copper smelting technology is facing great challenges. At present, there are two main copper smelting methods: pyrometallurgy and hydrometallurgy, but pyrometallurgy is still the main copper smelting technology. This paper analyzes the current situation of China's copper smelting industry, and discusses the innovation and development of copper smelting technology.Keywords: copper smelting; Technological development and progress; strategy随着世界经济的不断发展,全球化的步伐越来越快。
铜冶炼工艺(3篇)

第1篇一、引言铜是人类历史上最早使用的金属之一,具有优良的导电性、导热性、耐腐蚀性和可塑性。
随着科技的进步和工业的发展,铜在各个领域的应用越来越广泛。
铜冶炼工艺是指从铜矿石中提取铜金属的一系列物理和化学过程。
本文将详细介绍铜冶炼工艺的原理、流程以及主要设备。
二、铜矿石的类型铜矿石主要分为两大类:硫化铜矿石和氧化铜矿石。
硫化铜矿石主要含有黄铜矿(CuFeS2)、辉铜矿(Cu2S)等硫化物,氧化铜矿石主要含有赤铜矿(Cu2O)、孔雀石(CuCO3·Cu(OH)2)等氧化物。
三、铜冶炼工艺流程1. 铜矿石破碎与磨矿铜矿石破碎与磨矿是将铜矿石从原生矿石中分离出来的第一步。
通过破碎机将矿石破碎成一定粒度,再通过磨矿机将矿石磨成细粉,以利于后续的浮选和冶炼。
2. 浮选浮选是将铜矿石中的硫化物和氧化物进行分离的过程。
将磨好的矿石加入浮选剂,通过调整pH值和搅拌,使硫化物与水形成泡沫,从而实现铜矿物与其他矿物的分离。
3. 精选精选是将浮选得到的铜精矿进行进一步处理,以提高铜的品位。
精选方法有火法精选、湿法精选等。
4. 炼铜炼铜是将精选后的铜精矿进行熔炼,提取铜金属。
炼铜方法主要有火法炼铜、湿法炼铜等。
(1)火法炼铜火法炼铜是将铜精矿在高温下进行熔炼,使铜与硫反应生成硫化铜,然后通过吹炼氧化硫化铜,使铜转化为氧化铜。
火法炼铜主要包括熔炼、吹炼、精炼等过程。
熔炼:将铜精矿加入熔炼炉中,加入助熔剂(如石灰石)和燃料(如焦炭),在高温下熔炼,使铜精矿中的硫化物转化为硫化铜。
吹炼:将熔炼得到的熔融硫化铜吹入转炉中,通过吹入空气,使硫化铜氧化成氧化铜,同时将硫氧化成二氧化硫气体排出。
精炼:将吹炼得到的氧化铜熔融,加入氧化剂(如氧气)和还原剂(如碳),使氧化铜还原成铜金属,同时将杂质氧化去除。
(2)湿法炼铜湿法炼铜是将铜精矿经过溶解、氧化、结晶等过程,提取铜金属。
湿法炼铜主要包括浸出、氧化、结晶、电解等过程。
浸出:将铜精矿加入浸出槽中,加入浸出剂(如硫酸、硝酸)和氧化剂(如氧气、空气),使铜精矿中的铜溶解于浸出剂中。
夏朝的冶金技术古代冶炼与铸造的工艺突破
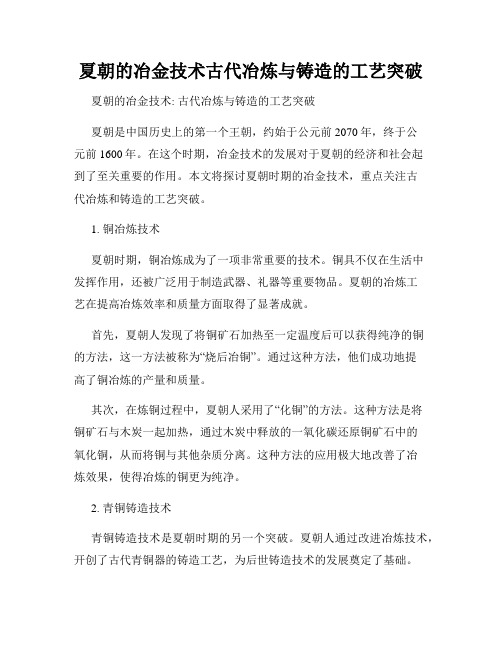
夏朝的冶金技术古代冶炼与铸造的工艺突破夏朝的冶金技术: 古代冶炼与铸造的工艺突破夏朝是中国历史上的第一个王朝,约始于公元前2070年,终于公元前1600年。
在这个时期,冶金技术的发展对于夏朝的经济和社会起到了至关重要的作用。
本文将探讨夏朝时期的冶金技术,重点关注古代冶炼和铸造的工艺突破。
1. 铜冶炼技术夏朝时期,铜冶炼成为了一项非常重要的技术。
铜具不仅在生活中发挥作用,还被广泛用于制造武器、礼器等重要物品。
夏朝的冶炼工艺在提高冶炼效率和质量方面取得了显著成就。
首先,夏朝人发现了将铜矿石加热至一定温度后可以获得纯净的铜的方法,这一方法被称为“烧后冶铜”。
通过这种方法,他们成功地提高了铜冶炼的产量和质量。
其次,在炼铜过程中,夏朝人采用了“化铜”的方法。
这种方法是将铜矿石与木炭一起加热,通过木炭中释放的一氧化碳还原铜矿石中的氧化铜,从而将铜与其他杂质分离。
这种方法的应用极大地改善了冶炼效果,使得冶炼的铜更为纯净。
2. 青铜铸造技术青铜铸造技术是夏朝时期的另一个突破。
夏朝人通过改进冶炼技术,开创了古代青铜器的铸造工艺,为后世铸造技术的发展奠定了基础。
在夏朝时期,青铜器的制作工艺经历了从单一铸造到多种复合工艺的转变。
初期的青铜器多是以铸铁为主,铸造方法相对简单。
然而,随着冶炼技术的发展,夏朝人逐渐掌握了铜和锡的合金比例,使得铸造更加精细。
此外,夏朝时期的铸造技术还涉及到砂型铸造的应用。
夏朝人使用砂质材料制作模具,将熔化的青铜倒入模具中进行铸造。
这一工艺的应用使得铸造过程更为灵活,为制作更复杂的青铜器提供了可能。
3. 对社会经济的影响夏朝的冶金技术突破不仅对工艺领域产生了重要的影响,也对当时的经济和社会发展起到了积极的推动作用。
首先,冶金技术的进步提高了生产力水平。
稳定的铜冶炼和青铜铸造工艺为生产工具的制造提供了基础,促进了农业生产和手工业的发展。
由于夏朝人能够制造更多更高质量的农具和生活用具,农田耕作效率得到了提高,人民生活质量也得到了改善。
废杂铜冶炼工艺及发展趋势
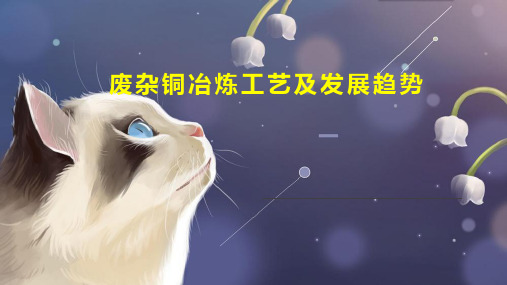
本研究创新点
本研究通过设计和实施一个全面的废杂铜冶炼过程污染物迁移转化实验,旨在 深入探讨污染物之间的相互转化机制及其影响因素。同时,结合现代分析技术 和数值模拟方法,对冶炼过程中的污染物排放进行精准预测与评估,为优化污 染控制策略提供科学依据。
研究方法
本研究采用实验模拟与数值模拟相结合的方法进行。首先,设计不同工艺参数 下的废杂铜冶炼实验,收集各工况下的烟气、废水和固体废物样本。其次,利 用ICP-AES、GC-MS等现代分析技术对样本中的污染物成分进行定性与定量分 析。最后,结合实验数据,运用CDE(Coupled Discrete Element)模型对 废杂铜冶炼过程中的污染物迁移转化进行数值模拟,以揭示各因素对污染物排 放的影响规律。
2、控制反应条件:冶金炉可以提供适当的化学环境,例如控制炉内气氛(氧 气、氮气等),以促进或抑制某些化学反应。
3、分离和纯化金属:通过冶金炉内的熔炼和精炼过程,可以有效地分离和纯 化金属铜,去除其中的杂质。
4、提高能源效率:冶金炉通常使用燃料(如煤、石油或天然气)作为热源, 这些燃料在炉内燃烧产生的热量被有效利用,提高了能源效率。
2、湿法冶炼技术:该技术主要采用化学还原剂将铜从废杂铜中还原出来。在 浸出过程中,加入酸或碱将废杂铜中的金属溶解出来,再通过置换反应得到金 属铜。湿法冶炼技术具有环保性能好、金属回收率高等优点,但生产成本较高 且对技术要求严格。未来,应进一步探索低成本、高效率的湿法冶炼技术,并 加强自动化技术的应用。
结论
本次演示通过对废杂铜冶炼过程中污染物迁移转化规律的研究,揭示了各因素 对污染物排放的影响规律及其相互转化机制。研究结果对于制定全过程污染控 制策略,优化废杂铜冶炼工艺具有重要指导意义。然而,本研究仍存在一定的 局限性,例如实验样本的代表性不足和数值模型简化等。
- 1、下载文档前请自行甄别文档内容的完整性,平台不提供额外的编辑、内容补充、找答案等附加服务。
- 2、"仅部分预览"的文档,不可在线预览部分如存在完整性等问题,可反馈申请退款(可完整预览的文档不适用该条件!)。
- 3、如文档侵犯您的权益,请联系客服反馈,我们会尽快为您处理(人工客服工作时间:9:00-18:30)。
铜冶炼水平与工艺水平1)火法冶炼工艺当前,全球矿铜产量的75%-80%是以硫化形态存在的矿物经开采、浮选得到的铜精矿为原料,火法炼铜是生产铜的主要方法,特别是硫化铜精矿,基本全部采用火法冶炼工艺。
火法处理硫化铜精矿的主要优点是适应性强,冶炼速度快,能充分利用硫化矿中的硫,能耗低。
其生产过程一般由以下几个工序组成:备料、熔炼、吹炼、火法精炼、电解精炼,最终产品为电解铜。
原料制备工序:将铜精矿、燃料、熔剂等物料进行预处理,使之符合不同冶炼工艺的需要。
熔炼工序:通过不同的熔炼方法,对铜精矿造硫熔炼,炼成含铜、硫、铁及贵金属的冰铜,使之与杂质炉渣分离;补出的含二氧化硫烟气经收尘后用于制造硫酸或其他硫制品,烟尘返回熔炼炉处理。
吹炼工序:除去冰铜中的硫铁,形成含铜及贵金属的粗铜,炉渣和烟尘返回上一工序处理。
火法精炼工序:将粗铜中硫等杂质进一步去除,浇铸出符合电解需要的阳极板。
电解精炼工序:除去杂质,进一步提纯,生产出符合标准的阴极铜成品,并把金银等贵金属富集在阳极泥中。
传统熔炼方法如鼓风炉熔炼、反射炉熔炼和电炉熔炼,由于效率低、能耗高、环境污染严重而逐渐被新的富氧强化熔炼工艺所代替[[3]新的富氧强化熔炼可分为闪速熔炼和熔池熔炼两大类,前者包括奥托昆普型闪速熔炼和加拿大国际镍公司闪速熔炼等,后者包括诺兰达法、三菱法、艾萨法、奥斯麦特法和瓦纽可夫法以及我国自主开发的水口山法、白银炉熔炼、金峰炉熔炼等技术。
铜锍吹炼方法有传统的卧式转炉、连续吹炼炉、虹吸式转炉。
新型吹炼技术包括艾萨吹炼炉、三菱吹炼炉和闪速吹炼炉等。
粗铜的火法精炼在阳极炉内进行,对于转炉产出的液态粗铜采用回转式阳极炉或固定式反射炉精炼,经氧化、还原等作业进一步脱除粗铜中的铁、铅、锌、砷、锑、铋等杂质,并浇铸成含铜99.2%-99.7%的阳极板。
铜电解工艺有传统电解法、永久阴极电解法和周期反向电流电解法3种。
目前大多数电解铜厂都使用传统电解法,永久阴极电解法和周期反向电流电解法是20世纪70年代以来发展的新技术。
2)熔炼工序(1)富氧强化熔炼工艺富氧强化熔炼工艺是目前铜火法冶炼的主流技术,包括闪速熔炼工艺和熔池熔炼工艺,其中熔池熔炼工艺又分为顶吹、底吹和侧吹工艺。
a.闪速熔炼工艺闪速熔炼的生产过程是用富氧空气或热风,将干精矿喷入专门设计的闪速炉的反应塔,精矿粒子在空间悬浮1-3s时间,与高温氧化性气流迅速发生硫化矿物的氧化反应,并放出大量的热,完成熔炼反应即造锍的过程。
反应的产物落入闪速炉的沉淀池中进行沉降,使铜锍和渣得到进一步的分离。
该工艺技术具有生产能力大、能耗低、污染少等优点,单套系统最大矿铜产能可达40万t/a以上,适用于规模20万t/a以上的工厂。
但是要求原料进行深度干燥到含水<0.3%,精矿粒度<1mm,原料中杂质铅加锌不宜高于6%。
工艺的缺点是设备复杂、烟尘率较高,渣含铜比较高,需要进行贫化处理。
闪速熔炼工艺技术在能效和环保方面的特点:闪速熔炼的铜精矿氧化反应迅速,单位时间内放出的热量多,加快了熔炼速度,使熔炼的生产率大幅度提高,为反射炉与电炉熔炼的两倍。
采用了富氧工艺后,在铜精矿含硫正常情况下可实现自热熔炼,大大降低了燃料的消耗。
由于精矿中硫化物的氧化反应程度高,且采用高浓度的富氧空气熔炼,烟气量少,烟气中的SO2浓度可提高到30%以上,有利于烟气制硫酸过程中硫的回收和环境保护。
闪速法铜冶炼工艺技术为《国家重点行业清洁生产技术导向目录》(第二批)中公布推广的清洁生产技术。
对比闪速炉反应塔的熔炼过程,熔池熔炼也是一个悬浮颗粒与周围介质的热与质的传递过程。
所不同的是,悬浮粒子是处在一个强烈搅动的液一气两相介质中,受液体流动、气体流动及两种流体间的相互作用以及动量交换的影响。
由于熔池熔炼过程的传热与传质效果好,可大大强化冶金过程,达到提高设备生产率和降低冶炼过程能耗的目的,因此,20世纪70年代后熔池熔炼得到了迅速发展。
富氧顶吹熔炼工艺熔炼系统由3个炉b.富氧顶吹熔池熔炼工艺富氧顶吹熔池熔炼工艺是通过喷枪把富氧空气强制鼓入熔池,使熔池产生强烈搅动状态加快了化学反应的速度,充分利用了精矿中的硫、铁氧化放出的热量进行熔炼,同时产出高品位冰铜。
熔炼过程中不足的热量由燃煤和燃油提供。
子组成,即熔炼炉、贫化炉和吹炼炉。
铜精矿、熔剂、返料、燃料煤经配料仓按预定要求计量配料后送制粒机加水制粒,以含水9%-10%的勃团料方式,由加料皮带从炉子顶加料口投入炉内。
经过制粒混有燃料煤的混合铜精矿,一旦粒料加入熔融层,粒料中水分马上就挥发掉,粒料变成粉末与冰铜和渣激烈地搅动并进行反应,形成一个气、固、液三相快速的传质传热,熔炼炉就变成一个高速的反应器。
熔炼需要的富氧空气通过喷枪鼓入熔池,为了便于生产期间的温度控制,还可从喷枪加入燃油对炉温进行微调,熔炼产生的冰铜和炉渣混熔体由炉子底部的放铜口(或虹吸硫口)及溜槽放出,进入贫化电炉澄清分离。
熔炼炉含尘烟气经余热锅炉降温和粗收尘后(其中余热锅炉部分豁结烟尘在锅炉的振打作用和重力影响下回到熔炼炉)进入电收尘器进一步除尘,出口烟气进入硫酸厂制酸。
余热锅炉收下的烟尘返配料系统,电收尘器收下的烟尘实现开路单独处理,贫化炉渣定期水淬。
冰铜分批送吹炼炉吹炼成粗铜:吹炼渣返贫化炉或水淬,水淬渣返回熔炼配料,粗铜进精炼炉。
吹炼炉烟气与熔炼一样,经余热锅炉、电收尘后,与熔炼炉净化烟气合并一起送硫酸车间制酸。
目前主要富氧顶吹熔炼工艺为奥斯迈特炉和艾萨炉熔炼技术。
富氧顶吹熔炼工艺具有以下特点:熔炼速度快,生产率高。
其中,艾萨炉用于铜精矿熔炼,床能力最高已达238t/(m2·d),一般达到190.8t/(m2·d),是目前炼铜方法中床能力最高的一种。
这种炉子在提高富氧浓度时,生产能力可以成倍增加。
年产10万t/a的工厂与年产20万t/a的工厂在炉子直径和高度上变化不大,只是富氧浓度不同。
系统建设投资少,生产费用低。
由于处理能力大,炉子结构简单,因此,建设速度快,投资少。
建设一座顶吹浸没炉的投资,一般只有相同规模的闪速熔炼炉投资的60%-70%。
原料的适应性强,可处理铜精矿、大块含铜原料,含铜电子废料等。
原料制备简单,铜精矿原料不需要经过特别准备,将含水量小于10%的精矿制成颗粒或混捏后直接入炉。
操作简便,自动化程度高,生产过程用计算机在线控制1台炉子,每班仅需要4-6名操作人员。
燃料适应性广,喷枪可以使用粉煤、碳粉、油和天然气,燃料调节比大。
有良好的劳动卫生条件,除喷枪口和加料口外,熔炼炉为密闭式生产,烟气外排少。
熔池熔炼过程是负压进行,余热锅炉和电收尘密封好,冶炼烟气不会外溢,烟气中的SO2浓度稳定且含量高,有利于烟气制硫酸过程中硫的回收和环境保护。
c.富氧侧吹熔炼工艺富氧侧吹熔池熔炼的生产过程是通过侧吹炉两侧的风口向炉内鼓入富氧压缩空气,在富氧压缩空气的作用下,熔体在侧吹炉内形成剧烈搅拌,由炉顶加入混矿,通过炉气干燥后,在熔体内形成气一液一固三相间的传质、传热过程,完成造渣、造锍反应,形成的渣锍共熔体在贫化前床内澄清分离,得到水淬渣和冰铜。
形成的高温烟气经余热锅炉生产蒸汽,烟气送制酸。
该工艺技术具有效率高、能耗低、对原料的适应性强、处理能力大、环保、操作简单、投资少等优点。
单台熔炼炉的粗铜产能可达15万t/a。
富氧侧吹熔池熔炼是一种富氧强化炼铜工艺,这就使得熔炼炉烟气量大大减少,提高了熔炼炉的热效率。
由于可以充分利用熔炼的反应热,大大减少了燃料消耗。
熔炼烟气SO2浓度8%-14%,有利于采用二转二吸技术制酸,硫的总捕集率达到98.45%。
d.氧气底吹熔炼工艺该工艺技术为我国自主开发的铜熔炼工艺技术。
混合矿料不需要干燥、磨细,配料后由皮带传输,连续从炉顶加料口加入炉内的高温熔池中,氧气和空气通过底部氧枪连续送入炉内的铜流层,氧气以大量的小气泡动态的悬浮于熔体中,有很大的气一液相接触面积,有极好的反应动力学条件,连续加入的铜精矿不断地被迅速氧化、造渣。
硫生成的二氧化硫烟气从炉子的排烟口连续地进入余热锅炉,经电收尘后制酸处理。
炉内形成的炉渣从底部定期放出,由渣包吊运至缓冷场,缓冷后进行渣选矿。
形成的铜锍从侧面放锍口定期放出,由铜毓包吊运到P-S转炉吹炼。
工艺特点:工艺过程简单、原料适应性强、能源消耗低、投资相对省、噪声低、操作环境好、劳动强度低、容易掌握和操作,产能规模在5万-25万t/a。
底吹熔炼技术最显著的特点就是能耗低、环保好:由于氧浓度高(富氧空气氧浓度可达75%),因而排出烟气量小,热损失少,反应强度高,因此很容易实现无碳自热熔炼,炉料中不需要另外配煤,节省了燃料以及煤燃烧所用的氧气,保证了氧气的充分有效利用,能耗很低。
该技术整套系统采用较高负压操作且密封性好,无烟气外溢现象,无低空污染。
(2)密闭鼓风炉熔炼工艺鼓风炉熔炼工艺是一种历史悠久的冶炼方法。
由于这种工艺能耗较高,熔炼烟气SO2浓度低,不宜有效回收,造成对大气的严重污染,所以我国己要求在2007年底以前,全部淘汰该冶炼工艺。
3)吹炼工序(1)P-S转炉吹炼技术1905年Peirce和Smith成功应用碱性耐火材料内衬卧式吹炼转炉,用于铜的吹炼,近百年来该技术己成为世界上普遍采用的成熟工艺。
转炉的铜锍吹炼过程中,向转炉中连续吹入空气,当熔体中FeS氧化造渣被除去后,炉内仅剩Cu2S (即白冰铜),Cu2S继续吹炼氧化生成Cu2O,Cu2O再与未被氧化的Cu2S发生交互反应获得金属铜。
该工艺成熟可靠,设备和操作简单,投资低,不加燃料吹炼,可用空气和低浓度的富氧空气。
能够利用剩余热量处理工厂中的含铜中间物料(粗铜壳、残阳极、烟尘、冷冰铜等),还能够处理外购的冷杂铜,生产成本低。
该工艺适用范围广,无论生产规模大小,铜锍品位高低均可应用该工艺:P-S转炉吹炼工艺为分周期、间断作业;其缺点是炉体密闭差,漏风大,烟气S02浓度低,设备台数多,物料进出需要吊车装运,低空污染较严重。
(2)闪速吹炼工艺闪速吹炼工艺技术发明于1979年,在奥托昆普闪速熔炼直接生产粗铜的技术基础上发展而成,20世纪80年代中期在美国肯尼柯特应用成功。
闪速吹炼工艺技术是将熔炼炉产出的熔融的铜毓进行水淬,磨细干燥后在闪速炉中用富氧空气进行吹炼得到粗铜,基本原理和工艺过程同闪速熔炼,但是加入的是高品位铜锍,吹炼过程连续作业。
该工艺适用于年产20万t 粗铜以上大规模工厂。
(3)顶吹浸没吹炼工艺顶吹浸没吹炼炉由炉顶加料孔加入干铜毓、熔剂,或底部溶池面上流入铜毓。
富氧空气或空气进行吹炼作业。
吹炼炉喷枪垂直插入固定的炉身,即奥斯迈特炉。
闪速吹炼与闪速熔炼炉搭配使用即双闪工艺,由于该工艺为连续吹炼技术,取消一般吹炼工艺用吊车吊装铜包及渣包等操作,且设备密封性能好,无烟气泄漏,彻底解决铜冶炼行业吹炼工序低空污染问题,大大降低无组织排放造成的SO2和含重金属烟尘污染程度。