超精密车削金刚石刀具刃口误差的高精度补偿
论述金刚石刀具超精密切削的机理丶条件和应用范围

金刚石刀具超精密切削的机理丶条件和应用范围
金刚石刀具是超精密切削中常用的刀具材料,其切削机理、条件和应用范围如下:
1.切削机理:
⏹金刚石刀具的切削刃非常锋利,在切削过程中能够实现“切入式切削”,
使切削力大大减小。
⏹金刚石的硬度极高,切削时不易被工件材料磨损,能够保持良好的切削刃
形状。
⏹金刚石的传热性能极佳,能够快速地将切削热量传递出去,从而降低切削
温度,减少热损伤。
1.切削条件:
⏹刀具刃口半径:为了实现超精密切削,需要将刀具的刃口半径减小到亚微
米级,以提高切削的精度和表面粗糙度。
⏹切削用量:为了减小切削力和热量,需要选择较小的切削深度和进给速度,
以提高切削效率。
⏹工件材料:金刚石刀具适用于加工各种硬材料,如淬火钢、硬质合金等。
但是,对于一些韧性较大的材料,需要进行预处理或选择其他刀具材料。
1.应用范围:
⏹金刚石刀具广泛应用于超精密切削领域,如光学零件、轴承、硬盘磁头、IC
芯片等高精度、高表面质量的零件加工。
⏹在加工过程中,金刚石刀具还可以用于制作各种微细结构,如微孔、微槽
等。
综上所述,金刚石刀具的超精密切削需要满足一定的条件,并具有广泛的应用范围。
超精密加工中的金刚石刀具及刀具磨损分析

理论与实践经济与社会发展研究超精密加工中的金刚石刀具及刀具磨损分析齐齐哈尔工程学院 武晓迪摘要:各种超精密加工应用中将金刚石用作切削工具已经成为现实,然而其目的与意义并没有得到实质性分析。
据此,本文对超精密加工中应用金刚石作为切削刀具的现实意义进行分析。
关键词:超精密加工;切削工具;刀具磨损一、技术背景分析使用高速超精密车床加工玻璃和硅等脆性材料时,当所施加的切削深度低于临界值时,则认为其处于延性模式,并且可以容易地加工而不会形成裂纹。
因此,对于这些材料的延性至脆性转变具有重要意义,在这些材料中,临界切削深度的大小取决于零件的特性而变化。
通常,单晶硅经常用在微机电系统(MEMS)中,在该系统中,最终将材料加工成优质产品,并进行超精密研磨和抛光操作。
尽管硅材料的行为在室温下很脆,但建议使用金刚石车削工具以延性模式加工硅。
这减少了由陶瓷材料的脆性断裂引起的损坏,并提高了最终零件的生产率。
使用金刚石工具对铜,铝和镍等有色金属材料进行高速加工,以评估工具的磨损,切削力和表面光洁度。
实验针对不同的切割速度进行,例如较低的150m/min的速度和较高的4500m/min的速度。
在较低的切削速度下观察到的刀具磨损率大于较高的切削速度。
这可能是由于以较高的速度减少了刀具与工件啮合的时间。
它还降低了工具和工件界面之间的化学亲和力。
具有高负前角的金刚石工具可用于以超精密精度精加工该材料。
二、金刚石作为切削工具的意义制备塑料模具的需求不断增加,而塑料模具是制造CD光学头的非球面透镜和照相机的智能透镜所必需的。
刀具的切削刃必须锋利且没有不规则形状,以加工高精度非球面。
基于工具的清晰度,单晶金刚石(SCD)和多晶金刚石(PCD)之间存在主要差异。
SCD工具的切削刃是均匀的且没有不规则性,而PCD工具的切削刃则显示出微观的不规则性,从而导致金刚石颗粒的去除。
与PCD工具相比,SCD工具的主要缺点是其磨损寿命短。
它还用于将铝基板加工成精细的镜面涂层,该涂层用于计算机存储系统的硬盘驱动器中。
基于泽尼克多项式系数的大相对孔径表面超精密车削误差的补偿方法

(n t ue o d m pia e h o o y o c o U ie s y S z o 1 0 6 C i a I s t t fMo e O t lT c n lg ,S o h w n v ri , u h u 2 5 0 , h n ) i c t
王 毅 , 景 池 余
( 州大 学 现代 光 学技 术研 究所 , 苏 苏州 2 5 0 ) 苏 江 10 6 摘 要 :超精 密车 削误 差补偿 是提 高超精 密 车 削工 艺水平 的 关键 技 术 。首先 对 超精 密 车 削 中的 各种
误 差进 行 了简单的分析 与归 纳 ,指 出刀具 刃 口几何 形状 误 差与机 床 导轨 非线性 误 差具有 相 同的表 现
k n m ais x s h d h e s me f r a , d o o t e c u d e o e s td c o d n t t e i e tc a i S a t a o m t a b t n h f h m o l b c mp n ae a c r i g o h
a c r ig o c o dn t m e s rm e t e u t ro d g tl n ef r m ee wa p o o e a u e n r s l f m i ia i tre o tr s r p s d, a d h e r tc l ac lto n t o ei a c lu a n i
…
v
’…
、-
一
Vo . 141 NO. 3
I fa e n s r E g n e i g n r d a d La e n i e rn r
M a. 0 2 r 2 1
超级精密加工论文
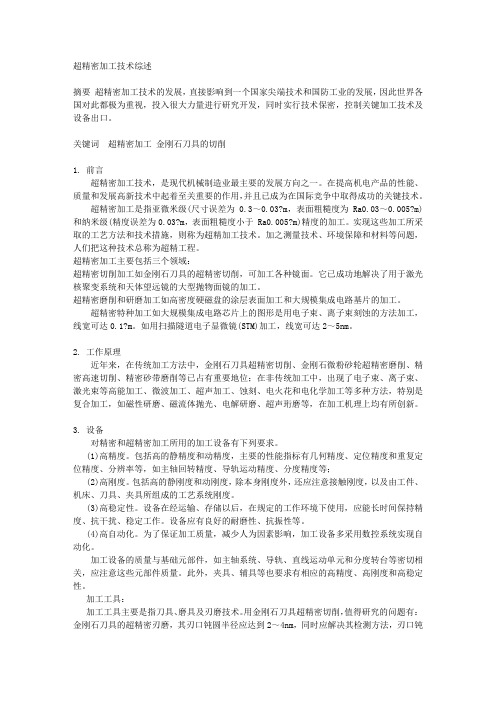
超精密加工技术综述摘要超精密加工技术的发展,直接影响到一个国家尖端技术和国防工业的发展,因此世界各国对此都极为重视,投入很大力量进行研究开发,同时实行技术保密,控制关键加工技术及设备出口。
关键词超精密加工金刚石刀具的切削1. 前言超精密加工技术,是现代机械制造业最主要的发展方向之一。
在提高机电产品的性能、质量和发展高新技术中起着至关重要的作用,并且已成为在国际竞争中取得成功的关键技术。
超精密加工是指亚微米级(尺寸误差为0.3~0.03?m,表面粗糙度为Ra0.03~0.005?m)和纳米级(精度误差为0.03?m,表面粗糙度小于 Ra0.005?m)精度的加工。
实现这些加工所采取的工艺方法和技术措施,则称为超精加工技术。
加之测量技术、环境保障和材料等问题,人们把这种技术总称为超精工程。
超精密加工主要包括三个领域:超精密切削加工如金刚石刀具的超精密切削,可加工各种镜面。
它已成功地解决了用于激光核聚变系统和天体望远镜的大型抛物面镜的加工。
超精密磨削和研磨加工如高密度硬磁盘的涂层表面加工和大规模集成电路基片的加工。
超精密特种加工如大规模集成电路芯片上的图形是用电子束、离子束刻蚀的方法加工,线宽可达0.1?m。
如用扫描隧道电子显微镜(STM)加工,线宽可达2~5nm。
2. 工作原理近年来,在传统加工方法中,金刚石刀具超精密切削、金刚石微粉砂轮超精密磨削、精密高速切削、精密砂带磨削等已占有重要地位;在非传统加工中,出现了电子束、离子束、激光束等高能加工、微波加工、超声加工、蚀刻、电火花和电化学加工等多种方法,特别是复合加工,如磁性研磨、磁流体抛光、电解研磨、超声珩磨等,在加工机理上均有所创新。
3. 设备对精密和超精密加工所用的加工设备有下列要求。
(1)高精度。
包括高的静精度和动精度,主要的性能指标有几何精度、定位精度和重复定位精度、分辨率等,如主轴回转精度、导轨运动精度、分度精度等;(2)高刚度。
包括高的静刚度和动刚度,除本身刚度外,还应注意接触刚度,以及由工件、机床、刀具、夹具所组成的工艺系统刚度。
超精密切削及金刚石刀具
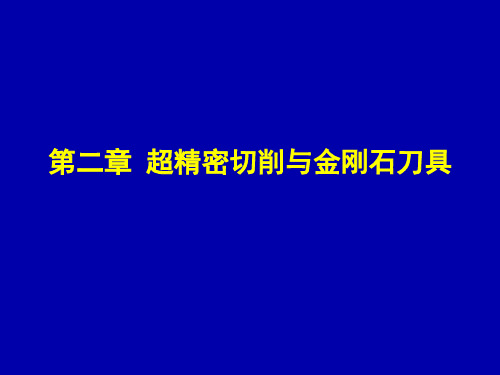
二)金刚石刀具的性能特点 极高的硬度,维氏硬度达HV10000。 极高的耐磨性,天然金刚石耐磨性为硬质合金的80-120
倍,人造金刚石为硬质合金的60-80倍。
刀刃非常锋利,天然单晶金刚石刀具刀刃钝园半径可达
纳米级。
摩擦系数低,金刚石与一些有色金属之间摩擦系数比其
它刀具都低,约为硬质合金刀具的一半。
格常数,各边夹角分别
c
b Y
以α、β、γ表示 。
根据6个参数间的相互关
系,可将全部空间晶格 归属于7种类型:三斜、
a
单斜、正交、六方、菱
方、四方、立方。金刚
X
晶格常数 a,b,c
石属于六方晶系。
2、晶体中的晶面和晶轴
晶面:通过原子中心的平面,即晶体中各种方位上 的原子面。 Z
晶轴:与晶面垂直的轴
2、对加工表面组织位错的影响
刃口半径越小,位错密度越小,切削变形越小,表 面质量越高。
四)刀刃锋锐度对加工表面残留应力的影响
刃口半径越小,残留应力越低。 背吃刀量越小,残留应力越小,但当背吃刀量减小到临界 值时,背吃刀量减小,残留应力增大。
五、超精密切削的最小切削厚度
使用极其锋利的金刚石刀具在机床最佳条件下可
导热性能高,导热系数为硬质合金的1.5-9倍,铜的2-6倍
。
热胀系数低,热胀系数比硬质合金小几倍,约为高速钢
的1/10,因此,金刚石刀具不会产生很大的热变形。
各向异性,单晶金刚石晶体不同晶面及晶向的硬度、耐
磨性、微观强度、研磨加工的难易程度以及与工件材料之
间的摩擦系数等相差很大,因此,设计和制造单晶金刚石 刀具时,必须进行晶体定向。
三)金刚石的晶体结构 1、晶体结构
影响单点金刚石超精密车削加工精度因素的研究

影 响单点金 刚石超 精密车削加工精度 因素的研 究
权 艳 红
( 云南广播 电视大学光电工程学院, 云南 昆明 6 5 0 5 0 0)
单 点金 刚石车 削( s P D T ) 加工技术 是获得纳米级
表 面 粗糙 度 及 形 状精 度 的加 工技 术 ,其 是 用超 精 密
在实际超精密切削塑性材料时 ,主切削刃和前 刀面的主要任务是去除材料 ,切削层在前刀面的挤 压作 用 下发 生剪 切 滑 移 和塑性 变形 ,然 后 形 成 切 屑 沿前 刀面 流 出 , 如图 1 ( b ) 所示 。 前 刀 面的形 状直 接 影 响塑 性 变形 的程 度 、切 屑 的卷 曲形 式 和切 屑 刀具 之 问 的摩 擦 特 性 , 并 直 接 对 切 削力 、 切 削 温度 、 切 屑 的 折 断 方式 和 加工 表 面 品质 形成 显 著影 响 。主 切 削 刃 是 前 刀 面和后 刀 面 的交 线 ,实 际上前 刀 面 和后 刀 面 的交线 不 可 能为 理 想直 线 , 而 是 一微 观 交 接 的 曲线 。 该 曲线 的形状 可 以近似 用 与其 在 不 同位 置 的法 平 面 相交成交线的平均曲率半径来反映 ,称其为刃 口半 径p 。刃 口半径 越小 , 应 力越 集 中 , 变形 越 容易 , 切 削 力越 小 , 加工 表面 品质越 好 。 目前计算机仿真技术与求解方法 ,已经被广泛 应 用 于科 学研 究 的各 个 领域 ,此 方法 减 少 了物 理 实 验 的成 本 , 加 速 了实 验 的过 程 。 近年 来 , 有 限 元仿 真 1 单 点金刚石超精密 车削原 理 方 法也 被 广泛 的应 用 于 加工 过 程 的仿 真 中 ,作 为 一 种 预测 切 削力 与 工件 表 面 品质 的工具 ,如 图 2是 使 单点金刚石 车削加工技术是超精密加工中常用 用 MS C . Ma r c 进 行单 点金 刚石 车 削原 理 的仿 真 ,图 3 的 技术 。 由于 金 刚石 的硬 度 高 , 耐磨 性 强 , 导热 性 优 则是 通过 三维仿 真 的切 削力 变化 情况 。 越, 因此 , 金 刚 石刀 具 的刃 口可 以非 常锋利 ( 刃 口半 径 可 以小 于 0 . 0 5 m甚 至更 小) 。 在 理想状 态 下 , 采用 圆 2 影 响 加 工 精 度 的 因素 分 析 弧刃 单点 金 刚石刀 具进 行超 精 密车 削加 工时 , 在工 件 . 1 单 点金 刚石 机床设 备 加工表面形成轮廓峰和轮廓谷 , 它们之 ■
单晶金刚石车刀在超精密单点切削中的磨损分析

单晶金刚石车刀在超精密单点切削中的磨损分析磨损分析是评估单晶金刚石车刀在超精密单点切削中使用过程中的性能退化情况。
磨损是由切削力和摩擦力引起的,而超精密单点切削要求较小的切削力和摩擦力。
因此,单晶金刚石车刀的磨损是非常重要的。
首先,单晶金刚石车刀的磨损主要有两种形式:刃口磨损和表面磨损。
刃口磨损会导致车刀的切削边缘变钝,从而降低切削效率和切削质量。
表面磨损主要是由刀具与工件表面接触时产生的摩擦引起的。
这些磨损形式都会导致单晶金刚石车刀的使用寿命减少。
其次,可以通过磨损分析来确定单晶金刚石车刀的磨损程度。
常用的磨损评估方法有:测量切削力和刀具表面形貌、观察工件表面质量等。
测量切削力可以间接评估刃口磨损程度,如果切削力增加,则说明刃口已经磨损。
观察工件表面质量也可以判断磨损情况,如果工件表面粗糙度增加,则说明刃口已经损坏。
最后,还可以通过磨损分析找出导致单晶金刚石车刀磨损的原因。
可能的原因包括:切削条件不合适、切削速度过高、切削液不合适等。
通过找出磨损原因,可以采取相应的措施来减少磨损,延长单晶金刚石车刀的使用寿命。
总之,单晶金刚石车刀在超精密单点切削中的磨损分析是评估其使用寿命和性能的重要手段。
通过磨损分析,可以确定磨损程度,找出导致磨损的原因,并采取相应的措施来延长车刀的使用寿命。
此外,单晶金刚石车刀磨损分析还可以提供对刀具寿命的预测和刀具性能的改进。
通过磨损分析,可以获取关于刀具磨损速率和刀具寿命的重要信息。
这些信息对于制定合理的刀具更换计划非常关键,以避免频繁更换刀具或过度使用磨损严重的刀具。
磨损分析还可以帮助改进单晶金刚石车刀的设计和制造工艺。
通过观察磨损形态和区域,可以了解刀具的磨损机制和影响因素。
这对于优化刀具的材料、几何形状和涂层等方面非常有价值。
例如,可以针对刀具的磨损情况进行改进,使其更耐磨、更耐用,并提高切削效率和切削质量。
此外,磨损分析还可以通过对比不同切削条件下的磨损情况,寻找最佳的切削参数组合。
金刚石刀具超精密切削加工)
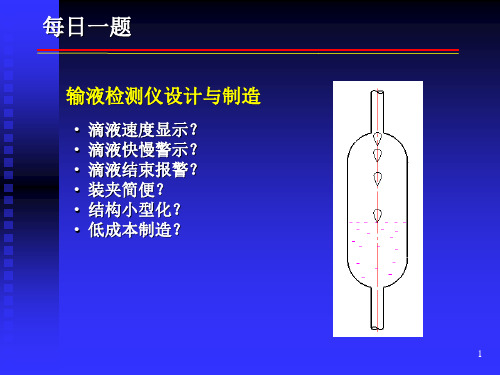
第2章 超精密切削与金刚石刀具
5) 刀具刃口锋锐度ρ ➢ 刃口圆弧半径ρ越小,切削厚度就越薄,越能够减小切
削表面弹性恢复和表面变质层。 ➢ ρ与切削刃的加工方位有关,普通刀具5~30μm,金刚石
刀具<10nm,最好能够< 5nm; ➢ 从物理学的观点,刃口半径ρ有一极限(后续介绍)。
37
ρ
第2章 超精密切削与金刚石刀具
(2)球面镜切削示例
球面镜加工原理
1-主轴;2-凹面镜;3-刀具轴
31
第2章 超精密切削与金刚石刀具
(3)大型金刚石刀具切削机床示例
LLNL的LODTM超精密车床
• Work table: 1.65 m dia
• Figure accuracy: 0.028 μm
• Surface finish :3.5-9.0 nm
35
第2章 超精密切削与金刚石刀具
2.2.2 超精密切削对刀具性能的要求
1) 极高的硬度、极高的耐磨性和极高的弹性模量,保证 长的刀具寿命。
2) 刀刃无缺陷,足够的强度,耐崩刃性能。 3) 切削时切削刃的粗糙度将决定加工表面的粗糙度, 普
通刀刃的粗糙度Ry0.3~5 μm,金刚石刀具刀刃的粗 糙度Ry0.1~0.2 μm,特殊情况Ry1nm,极难刃磨。 4) 化学亲和性小、与工件材料的抗粘结性好、摩擦系数 低,能得到极好的加工表面完整性。
(3) 变形加工 ——利用力、热、分子运动等手段使工件产生变形, 改变其尺寸、形状和性能。
主要包括: 锻造、热流动加工、铸造、液体流动加工等。
77
第1章 绪 论
1.3.2 根据加工过程中材料的流动形态来分类
——去除加工是使材料逐渐减少,一部分材料变为切屑,这 种流动称之为分散流;
- 1、下载文档前请自行甄别文档内容的完整性,平台不提供额外的编辑、内容补充、找答案等附加服务。
- 2、"仅部分预览"的文档,不可在线预览部分如存在完整性等问题,可反馈申请退款(可完整预览的文档不适用该条件!)。
- 3、如文档侵犯您的权益,请联系客服反馈,我们会尽快为您处理(人工客服工作时间:9:00-18:30)。
Co pe a i n f rEr o fDi m o o ’ m ns to 0 r ro a nd To lSCuti tng
Edg n S ng e Di m o ei i l a nd Tur i n ng
W A NG Yi Y U i — h1 期
21年 1 01 月
光 电工 程
Op o El cr n cEn i e rn t — e to i g n e i g
V l 8 NO 1 03 l- . .
J n. 0l a 2 1
文 章编号 : 10 ~ 0 X(0 1o 一 0 8 0 0 3 5 1 2 1) l0 9 — 5
me s r me tr s l fo d g t l n e f r me e. is, e al d t e r t a ac lt n r lt d wi o e s t n me h d a u e n e u tr m i i tre o t r F rt d t i o e i lc lu ai eae t c mp n ai t o a i e h c o h o
w a d ed sde uc .The t fe ta e o p ns to wa i ult d b c m pu e.Fi ly n, hee f c f rc m e a in s sm a e y o t tr na l, 5 m ,r di 0 m m ,wo k 0m a us5 r
Ab t a t sr c :Th o e s t n meh df rt eer r f im o d t o ’ c t n d ei ab t e n c c n l g id r h ec mp n a i t o o r o a n l u t g e g ot — e kt h o o y t h n e e o h o d o S i s l e o t h g c u a y a p e i u f c ’ d r cl o m ai n a t rsn l d a n u n n . p cal o t e b g r lt e a e t r i h a c r c s h r s ra e S i t f r t fe i g e imo d t r i g Es e il t h i ea i p r e c e y o y v u a p e i, n u n ei i g r T a i o a o e s t n wa o ea c r i g t eme s r me t e u t r m r f e mee , s h rc i f e c sb g e. r dt n l mp n ai sd n c o d n t a u e n s l fo p o l t r l i c o oh r i whc o k l n a u e n i e a d c u e w r c s i g e ce c . n w o e s t n meh d wa r t u ih t o o g me s r me tt n a s d l p o e s f in y A e c mp n a i t o sf s y p t m o n i o i l f r r n t e a t l.i ih t e c re t n o h no f da n o l u t g e g s d n c o dn o o wa d i h ri e n wh c h o r c i f t e e . o imo d t o ’ c t n d e wa o e a c r i g t c o r S i
对于大相对 口径 ,深度非球 面的车削,金刚石刀具刃口误差对最终的面形 的影响非常大。传统 补偿方法是根据轮
廓仪 的 测 量结 果对 刀 具 刃 口误 差进 行 修 正 ,但 是 该 方 法存 在 测 量 时 间长 , 高频 误 差 大 ,加 工效 率 低 的缺 点 , 本 丈
最先提 出利用车 削表面面形误 差拟舍后 的泽尼克多项 式系数对刀具刃 口误 差进行加工补偿 ,首先对该补偿方法进
预 期 ,精 度 高 ,误 差 收 敛速 度 快 。
关键词:超精 密车 削;刀具刃 口误 差;补偿;光学加 3 -
中图 分 类 号 :T 7 6 H1 1 G 0 ;T 6 文 献标 志码 :A d i l.99 .s. 0 .0 X. 1.1 1 o : 03 6 /i n1 35 1 2 O . 9 js 0 01 0
(ntuefMo enO t a c nlg ,o c o n est S zo 10 6dag u rvne C ia Istt o i dr p i leh ooy S oh w U i r y uh u2 0 , ins o i , h ) c T v i, 5 P c n
行 了详细的理论推导 , 然后对补偿效果进行计 算机模拟 , 最后在 N n t h 5 单 点金 刚石车床上完成了口径 5 a oe 2 0 c 0mm, 半径 5 大相对 口径实验件 的超精密车削及修正车 削,面形精度 PV 8 m, MS 7 i 。充分证 明该补偿符合 0mm =6 n R = n n
超 精 密 车削 金 刚石 刀具 刃 口误差 的 高精 度 补 偿
王 毅 ,余 景 池
(苏 州 大学 现 代光 学 技 术 研 究 所 ,江 苏 苏 州 2 0 10 6) 5 摘 要 :超精 密 车 削 中的 金 刚石 刀具 刀 口误 差 的 补 偿 问题 一 直 是 制 约 高精 度 非球 面 车 削 直接 成形 的瓶 颈 技 术 , 尤 其