金刚石刀具超精密切削加工)
论述金刚石刀具超精密切削的机理丶条件和应用范围

金刚石刀具超精密切削的机理丶条件和应用范围
金刚石刀具是超精密切削中常用的刀具材料,其切削机理、条件和应用范围如下:
1.切削机理:
⏹金刚石刀具的切削刃非常锋利,在切削过程中能够实现“切入式切削”,
使切削力大大减小。
⏹金刚石的硬度极高,切削时不易被工件材料磨损,能够保持良好的切削刃
形状。
⏹金刚石的传热性能极佳,能够快速地将切削热量传递出去,从而降低切削
温度,减少热损伤。
1.切削条件:
⏹刀具刃口半径:为了实现超精密切削,需要将刀具的刃口半径减小到亚微
米级,以提高切削的精度和表面粗糙度。
⏹切削用量:为了减小切削力和热量,需要选择较小的切削深度和进给速度,
以提高切削效率。
⏹工件材料:金刚石刀具适用于加工各种硬材料,如淬火钢、硬质合金等。
但是,对于一些韧性较大的材料,需要进行预处理或选择其他刀具材料。
1.应用范围:
⏹金刚石刀具广泛应用于超精密切削领域,如光学零件、轴承、硬盘磁头、IC
芯片等高精度、高表面质量的零件加工。
⏹在加工过程中,金刚石刀具还可以用于制作各种微细结构,如微孔、微槽
等。
综上所述,金刚石刀具的超精密切削需要满足一定的条件,并具有广泛的应用范围。
超精密加工中的金刚石刀具及刀具磨损分析

理论与实践经济与社会发展研究超精密加工中的金刚石刀具及刀具磨损分析齐齐哈尔工程学院 武晓迪摘要:各种超精密加工应用中将金刚石用作切削工具已经成为现实,然而其目的与意义并没有得到实质性分析。
据此,本文对超精密加工中应用金刚石作为切削刀具的现实意义进行分析。
关键词:超精密加工;切削工具;刀具磨损一、技术背景分析使用高速超精密车床加工玻璃和硅等脆性材料时,当所施加的切削深度低于临界值时,则认为其处于延性模式,并且可以容易地加工而不会形成裂纹。
因此,对于这些材料的延性至脆性转变具有重要意义,在这些材料中,临界切削深度的大小取决于零件的特性而变化。
通常,单晶硅经常用在微机电系统(MEMS)中,在该系统中,最终将材料加工成优质产品,并进行超精密研磨和抛光操作。
尽管硅材料的行为在室温下很脆,但建议使用金刚石车削工具以延性模式加工硅。
这减少了由陶瓷材料的脆性断裂引起的损坏,并提高了最终零件的生产率。
使用金刚石工具对铜,铝和镍等有色金属材料进行高速加工,以评估工具的磨损,切削力和表面光洁度。
实验针对不同的切割速度进行,例如较低的150m/min的速度和较高的4500m/min的速度。
在较低的切削速度下观察到的刀具磨损率大于较高的切削速度。
这可能是由于以较高的速度减少了刀具与工件啮合的时间。
它还降低了工具和工件界面之间的化学亲和力。
具有高负前角的金刚石工具可用于以超精密精度精加工该材料。
二、金刚石作为切削工具的意义制备塑料模具的需求不断增加,而塑料模具是制造CD光学头的非球面透镜和照相机的智能透镜所必需的。
刀具的切削刃必须锋利且没有不规则形状,以加工高精度非球面。
基于工具的清晰度,单晶金刚石(SCD)和多晶金刚石(PCD)之间存在主要差异。
SCD工具的切削刃是均匀的且没有不规则性,而PCD工具的切削刃则显示出微观的不规则性,从而导致金刚石颗粒的去除。
与PCD工具相比,SCD工具的主要缺点是其磨损寿命短。
它还用于将铝基板加工成精细的镜面涂层,该涂层用于计算机存储系统的硬盘驱动器中。
第2章超精密切削与金刚石刀具详解
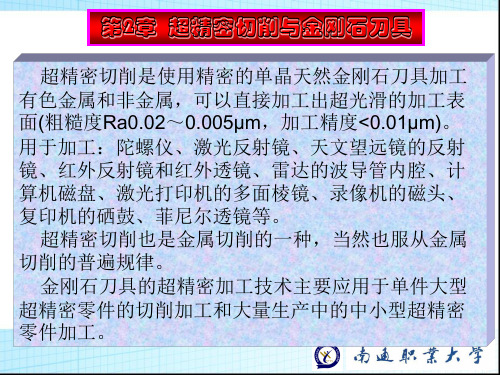
• 1)极高的硬度、极高的耐磨性和极高的弹性模量。 • 2)刃口能磨得极其锋锐,刃口半径值极小,能实现超薄切削厚度。 • 3)刀刃无缺陷,切削时刃形将复制在被加工表面上,从而得到超光滑的 镜面。 • 4)与工件材料的抗粘性好、化学亲和性小、摩擦系数低,以得到极好的 加工表面完整性。 • 不可替代的超精密切削刀具材料:单晶金刚石。
刃口半径为0.6μm、0.3μm
刃口锋锐度对加工表面有一 定的影响,相同条件下(背 吃刀量、进给量),更锋锐 的刀具切出的表面粗糙度更 小;速度的影响不是很大。
2.4 刀刃锋锐度对切削变形和加工表面质量的影响
二、刀刃锋锐度对切削变形和切削力的影响
锋锐车刀切削变形系数明显低于 较钝的车刀。 刀刃锋锐度不同,切削力明显不 同。刃口半径增大,切削力增大, 即切削变形大。背吃刀量很小时, 切削力显著增大。因为背吃刀量很 小时,刃口半径造成的附加切削变 形已占总切削变形的很大比例,刃 口的微小变化将使切削变形产生很 大的变化。所以在背吃刀量很小的 精切时,应采用刃口半径很小的锋 锐金刚石车刀。
2.7 刀具的要求及金刚石的性能和晶体结构
二、金刚石晶体的性能
• • • • 硬度最高,各向异性,不同晶向的物理性能相差很大。 优质天然单晶金刚石:多数为规整的8面体或菱形12面体,少数为6面立方体 或其他形状,浅色透明,无杂质、无缺陷。 大颗粒人造金刚石在超高压、高温下由子晶生长而成,并且要求很长的晶体 生长时间。 人造单晶金刚石已用于制造超精密切削的刀具。
2.3 切削参数变化对加工表面质量的影响
一、切削速度、进给量、修光刃和背吃刀量的影响
3、修光刃的影响
修光刃长度常取0.05~ 0.20mm。 修光刃的长度过长,对 加工表面粗糙度影响不 大。 修光刃有直线和圆弧两 种,加工时要精确对 刀,使修光刃和进给方 向一致。圆弧刃半径一般 取2~5mm。
金刚石刀具在数控机床中的应用

金刚石刀具在数控机床中的应用随着科技的不断进步和发展,数控机床在工业领域中扮演着重要的角色。
数控机床的出现大大提高了生产效率和加工质量,而金刚石刀具作为一种高性能的切削工具,在数控机床中的应用也越来越广泛。
本文将探讨金刚石刀具在数控机床中的应用,并分析其优势和挑战。
一. 金刚石刀具的基本特性金刚石刀具由金刚石颗粒和金属粉末经压制、烧结等工艺制成,具有极高的硬度、耐磨性和热稳定性。
这些特性使得金刚石刀具在切削加工中具备以下优势:1. 高硬度:金刚石刀具的硬度仅次于金刚石,可用于切削超硬材料如陶瓷和高硬度合金等。
2. 耐磨性:金刚石刀具具有出色的耐磨性,可在切削过程中保持较长的使用寿命。
3. 热稳定性:金刚石刀具具有良好的热稳定性,可承受高温切削环境下的工作,不易变形。
二. 金刚石刀具在数控机床中的应用领域1. 切削加工金刚石刀具广泛应用于数控机床的切削加工领域,包括车削、铣削、钻削、磨削等。
由于金刚石刀具的高硬度和耐磨性,可用于加工硬度较高的材料,如钛合金、高速钢等。
同时,金刚石刀具还能够提供更高的加工精度和表面质量。
2. 精密加工在数控机床的精密加工中,金刚石刀具的应用更能体现出其独特的优势。
例如,在汽车零部件的精密加工过程中,采用金刚石刀具可以实现更高的加工精度和更好的表面质量。
3. 工具磨损监测由于金刚石刀具的耐磨性较高,因此可以通过监测金刚石刀具的磨损情况,准确地评估刀具的使用寿命。
这对机床的保养和刀具的及时更换具有重要意义,可降低生产成本,并提高生产效率。
三. 金刚石刀具在数控机床中的挑战虽然金刚石刀具在数控机床中有广泛的应用前景,但面临着一些挑战和限制:1. 成本高昂:金刚石刀具的制造成本较高,所以其售价也相对较高,这给广泛应用带来了一定的限制。
2. 技术要求高:金刚石刀具的加工工艺复杂,需要高精度和高温高压的条件,所以其生产过程要求较高的技术水平。
3. 刀具表面质量难以保证:由于金刚石刀具的硬度很高,常规的抛光或修整技术难以完成对其表面的加工,从而可能会影响到加工表面质量。
精密和超精密加工

1、精密和超精密加工的三大领域:超精密切削、精密和超精密磨削研磨、精密特种加工。
2、金刚石刀具进行超精密切削时,适合加工铝合金、无氧铜、黄铜、非电解镍等有色金属和某些非金属材料。
3、最硬的刀具是天然单晶金刚石刀具。
金刚石刀具的的寿命用切削路程的长度计算。
4、超精密切削实际能达到的最小切削厚度和金刚石刀具的锋锐度、使用的超精密机床的性能状态、切削时的环境条件等直接相关。
5、影响超精密切削极限最小切削厚度最大的参数是切削刃钝圆半径r n。
6、金刚石晶体有3个主要晶面,即(100)、(110)、(111),(100)晶面的摩擦因数曲线有4个波峰和波谷,(110)晶面有2个波峰和波谷,(111)晶面有3个波峰和波谷。
以摩擦因数低的波谷比较,(100)晶面的摩擦因数最低,(111)晶面次之,(110)晶面最高。
比较同一晶面的摩擦因数值变化,(100)晶面的摩擦因数差别最大,(110)次之,(111)晶面最小。
7、实际金刚石晶体的(111)晶面的硬度和耐磨性最高。
推荐金刚石刀具的前面应选(100)晶面。
8、(110)晶面的磨削率最高,最容易磨;(100)晶面的磨削率次之,(111)晶面磨削率最低,最不容易磨。
9、金刚石的3个主要晶面磨削(研磨)方向不同时,磨削率相差很大。
现在习惯上把高磨削率方向称为“好磨方向”,把低磨削率方向称为“难磨方向”。
10、金刚石磨损本质是微观解离的积累;破损主要产生于(111)晶面的解离。
11、金刚石晶体定向方法:人工目测定向、X射线晶体定向、激光晶体定向。
其中激光晶体定向最常用。
12、金刚石的固定方法有:机械夹固、用粉末冶金法固定、使用粘结或钎焊固定。
13、精密磨削机理包括:微刃的微切削作用,微刃的等高切削作用,微刃的滑挤、摩擦、抛光作用。
14、超硬磨料砂轮修整的方法有:车削法、磨削法、滚压挤轧法、喷射法、电加工法、超声波振动修整法。
电解在线修锐法(ELID—electrolytic in—process dressing),原理是利用电化学腐蚀作用蚀出金属结合剂。
金刚石精密切削的定义
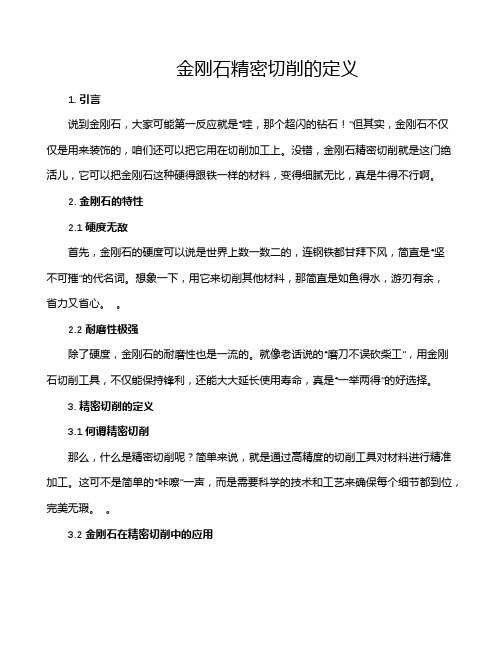
金刚石精密切削的定义1. 引言说到金刚石,大家可能第一反应就是“哇,那个超闪的钻石!”但其实,金刚石不仅仅是用来装饰的,咱们还可以把它用在切削加工上。
没错,金刚石精密切削就是这门绝活儿,它可以把金刚石这种硬得跟铁一样的材料,变得细腻无比,真是牛得不行啊。
2. 金刚石的特性2.1 硬度无敌首先,金刚石的硬度可以说是世界上数一数二的,连钢铁都甘拜下风,简直是“坚不可摧”的代名词。
想象一下,用它来切削其他材料,那简直是如鱼得水,游刃有余,省力又省心。
2.2 耐磨性极强除了硬度,金刚石的耐磨性也是一流的。
就像老话说的“磨刀不误砍柴工”,用金刚石切削工具,不仅能保持锋利,还能大大延长使用寿命,真是“一举两得”的好选择。
3. 精密切削的定义3.1 何谓精密切削那么,什么是精密切削呢?简单来说,就是通过高精度的切削工具对材料进行精准加工。
这可不是简单的“咔嚓”一声,而是需要科学的技术和工艺来确保每个细节都到位,完美无瑕。
3.2 金刚石在精密切削中的应用金刚石在这方面可是个大明星!它不仅能处理金属,还能处理玻璃、陶瓷等硬材料,简直是“全能型选手”。
想想看,车床上转动的金刚石刀具,切割出完美的形状,那种感觉,简直让人拍手叫好,心中默默赞叹。
4. 优势与应用4.1 效率提升用金刚石进行精密切削,可以大幅提升加工效率。
因为它的切削速度快,切削温度低,不容易变形,真是“马到成功”的好帮手。
这样一来,企业不仅能节省时间,还能降低成本,真是一箭双雕。
4.2 广泛应用这项技术的应用可谓是遍地开花,无论是汽车、航空,还是电子产品,都能看到它的身影。
比如说,在手机屏幕的加工中,金刚石切削让屏幕边缘光滑得像丝绸一样,手感超赞。
5. 未来发展5.1 技术创新随着科技的发展,金刚石精密切削的技术也在不断创新。
新材料、新工艺层出不穷,让切削的精度和效率都在不断提高,未来可期啊!。
5.2 市场前景相信随着对高品质产品的需求增加,金刚石精密切削的市场前景会越来越广阔。
超级精密加工论文
超精密加工技术综述摘要超精密加工技术的发展,直接影响到一个国家尖端技术和国防工业的发展,因此世界各国对此都极为重视,投入很大力量进行研究开发,同时实行技术保密,控制关键加工技术及设备出口。
关键词超精密加工金刚石刀具的切削1. 前言超精密加工技术,是现代机械制造业最主要的发展方向之一。
在提高机电产品的性能、质量和发展高新技术中起着至关重要的作用,并且已成为在国际竞争中取得成功的关键技术。
超精密加工是指亚微米级(尺寸误差为0.3~0.03?m,表面粗糙度为Ra0.03~0.005?m)和纳米级(精度误差为0.03?m,表面粗糙度小于 Ra0.005?m)精度的加工。
实现这些加工所采取的工艺方法和技术措施,则称为超精加工技术。
加之测量技术、环境保障和材料等问题,人们把这种技术总称为超精工程。
超精密加工主要包括三个领域:超精密切削加工如金刚石刀具的超精密切削,可加工各种镜面。
它已成功地解决了用于激光核聚变系统和天体望远镜的大型抛物面镜的加工。
超精密磨削和研磨加工如高密度硬磁盘的涂层表面加工和大规模集成电路基片的加工。
超精密特种加工如大规模集成电路芯片上的图形是用电子束、离子束刻蚀的方法加工,线宽可达0.1?m。
如用扫描隧道电子显微镜(STM)加工,线宽可达2~5nm。
2. 工作原理近年来,在传统加工方法中,金刚石刀具超精密切削、金刚石微粉砂轮超精密磨削、精密高速切削、精密砂带磨削等已占有重要地位;在非传统加工中,出现了电子束、离子束、激光束等高能加工、微波加工、超声加工、蚀刻、电火花和电化学加工等多种方法,特别是复合加工,如磁性研磨、磁流体抛光、电解研磨、超声珩磨等,在加工机理上均有所创新。
3. 设备对精密和超精密加工所用的加工设备有下列要求。
(1)高精度。
包括高的静精度和动精度,主要的性能指标有几何精度、定位精度和重复定位精度、分辨率等,如主轴回转精度、导轨运动精度、分度精度等;(2)高刚度。
包括高的静刚度和动刚度,除本身刚度外,还应注意接触刚度,以及由工件、机床、刀具、夹具所组成的工艺系统刚度。
精密和超精密加工技术
1、通常将加工精度在0.1-1um、加工表面粗糙度R在0.02-0.1um之间的加工方法称为精密加工。
而将加工精度高于0.1um、加工表面粗糙度R小于0.01um的加工方法称为超精密加工。
2、提高加工精度的原因:提高制造精度后可提高产品的性能和质量,提高其稳定性和可靠性;促进产品的小型化;增强零件的互换性,提高装配生产率,并促进自动化装配。
3、精密和超精密加工目前包含三个领域:超精密切削;精密和超精密磨削研磨‘精密特种加工。
4、金刚石刀具的超精密切削加工技术,主要应用于两个方面:单件的大型超精密零件的切削加工和大量生产的中小型零件的超精密切削加工技术。
5、金刚石刀具有两个比较重要的问题:晶面的选择;切削刃钝圆半径。
6、超稳定环境条件主要是指恒温、防振、超净和恒湿五个方面的条件。
7、我国应开展超精密加工技术基础的研究,其主要内容包括以下四个方面:1)超精密切削、磨削的基本理论和工艺。
2)超精密设备的关键技术、精度、动特性和热稳定性。
3)超精密加工的精度检测、在线检测和误差补偿。
4)超精密加工的环境条件。
5)超精密加工的材料。
8、超精密切削实际选择的切削速度,经常是根据所使用的超精密机床的动特性和切削系统的动特性选取,即选择振动最小的转速。
9、超精密切削实际能达到的最小切削厚度和金刚石刀具的锋锐度、使用的超精密机床的性能状态、切削时的环境等都直接有关。
10、为实现超精密切削,刀具应具有如下性能:1)极高的硬度、极高的耐磨性和极高的弹性模量,以保证刀具有很长的寿命和很高的尺寸耐用度。
2)切削刃钝圆能磨得极其锋锐,切削刃钝圆半径r值极小,能实现超薄切削厚度。
3)切削刃无缺陷,切削时刃形将复印在加工表面上,能得到超光滑的镜面。
4)和工件材料的抗粘结性好、化学亲和性小、摩擦因素低,能得到极好的加工表面完整性。
11、SPDT——金刚石刀具切削和超精密切削。
12、晶体受到定向的机械力作用时,可以沿平行于某个平面平整地劈开的现象称为解理现象。
第2章超精密切削与金刚石刀具汇总
3. 刀刃形状对加工表面粗糙的影响 ✓ 直线修光刃(国内)、圆弧修光刃(国外)。 ✓ 修光刃太长对加工表面粗糙度影响不大。 ✓ 圆弧修光刃刀具加工表面质量较高,但是,制造、刃
磨复杂,成本高。
4. 背吃刀量对加工表面粗糙的影响 ✓ 在超精密加工中,背吃刀量一般都比较小,对加工
表面粗糙度的影响很小。 ✓ 但是如果ap太小,挤压严重,切削困难, 加工表面
材料、机床特性、切削环境等因素有关。 ✓ 目前,使用极其锋利的金刚石刀具在机床最佳条
件下可以实现纳米级连续稳定的切削。
常规切削与超精密切削加工
常规切削与超精密切削加工
常规切削与超精密切削加工
超精密切削加工
2. 刃口半径(钝圆半径)rn与最小切削厚度的关系
✓ 可见,最小切削厚度与刀具锋锐度、切削力、摩擦系数有关。
切削时,积屑瘤可增大刀具 前角,从而使切削力下降。
积屑瘤越高,切削力越大的主要原因 ✓ 积屑瘤圆弧半径 R 约为2-3 m,远远大于金刚石刀具刃
口半径 0.1-0.3 m。 ✓ 积屑瘤代替金刚石刀刃切削,积屑瘤与切屑间摩擦很严
重,摩擦力大大增加。 ✓ 积屑瘤的存在,导致切削厚度增加。 ✓ 积屑瘤的存在,加工表面粗糙度增加。 ✓ 使用切削液,可减小积屑瘤高度,减小加工表面粗糙度
防止积屑瘤的办法:
✓ 低速切削、或高速切削 ✓ 添加润滑液、较小摩擦 ✓ 增大刀具前角,减小刀—屑间的压力 ✓ 提高工件硬度,减小加工硬化
超精密切削刀时积屑瘤的生成规律
切削速度对积屑瘤产生的影响。 ✓ 与普通切削不同 ✓ 切削速度越高, 积屑瘤高度越低。
超精密切削刀时积屑瘤的生成规律
积屑瘤对切削力的影响 ✓ 积屑瘤越高,切削力越大 ✓ 与普通切削正好相反,普通
第二章 金刚石刀具精密切削加工
复习晶体结构
晶格模型
面心结构
晶体结构指晶体内部原子规则排列的方式.晶体结构不同, 其性能往往相差很大。为了便于分析研究各种晶体中原子 或分子的排列情况,通常把原子抽象为几何点,并用许多 假想的直线连接起来,这样得到的三维空间几何格架称为 晶格。
晶胞
Z
晶胞
c
b Y
a
X
晶格常数 a , b, c
人造单晶金刚石刀具 金刚石刀具 PCD刀具
多晶金刚石刀具
CVD金刚石薄膜涂层刀具
CVD金刚石刀具 金刚石厚度膜焊接刀具
金刚石刀具的性能特点
极高的硬度和耐磨性:硬度达HV10000,是自然界最硬的物质, 具有极高的耐磨性,天然金刚石耐磨性为硬质合金80-120倍,人 造金刚石耐磨性为硬质合金60-80倍。 各向异性能:单晶金刚石晶体不同晶面及晶向的硬度、耐磨性能 、微观强度、研磨加工的难易程度以及与工件材料之间的摩擦系 数等相差很大,因此,设计和制造单晶金刚石刀具时,必须进行 晶体定向。
二、典型机床简介
Pneumo 公司的MSG-325超精密车床
采用T形布局,机床空气主轴的径向圆跳动和轴向 跳动均小于等于0.05μm。床身溜板用花岗岩制造,导 轨为气浮导轨;机床用滚珠丝杠和分辨率为0.01μm的 双坐标精密数控系统驱动,用HP5501A双频激光干涉仪 精密检测位移。
DTM-3大型超精密车床
分为:液体静压和空气静压
供油压力恒定的液体静压轴承
主轴始终悬浮 在高压油膜上
液体静压轴承与气压轴承
1、液体静压轴承主轴
优点
回转稳定性好 刚度高 无振动
缺点
回转运动有温升 回油时有空气进入油源 注:空气静压轴承原理与静
- 1、下载文档前请自行甄别文档内容的完整性,平台不提供额外的编辑、内容补充、找答案等附加服务。
- 2、"仅部分预览"的文档,不可在线预览部分如存在完整性等问题,可反馈申请退款(可完整预览的文档不适用该条件!)。
- 3、如文档侵犯您的权益,请联系客服反馈,我们会尽快为您处理(人工客服工作时间:9:00-18:30)。
一是指向传统加工方法不易达到的精度界限挑战的加
工,即超高精度加工,如计算机磁盘及各种金属反射镜的超
精密镜面加工;
二是向实现微细尺寸界限挑战的加工,即所谓微细加工
技术(Micro-fabrication),如微电子电路制造中的电子束、 光子束和离子束刻蚀加工以及离子注入、分子外延等工艺技
术。
10 10
当前,在制造业中,占主要地位的仍是传统加工方法, 而非传统的特种加工和复合加工是解决新的难加工材料加工、 实现更高精度和特殊加工要求零件加工的有效手段。
99
第1章 绪 论
1.4 精密和超精密加工技术概述
1.4.1 精密和超精密加工的概念和含义
就“加工”这个词而言,应理解为一个广泛的概念。超精密 加工包含两个含义:
现阶段精密、超精密加工精度范围:
一般加工: 加工精度10μm左右, Ra > 0.1μm 精密加工: 加工精度0.1~1μm, Ra=0.02~0.1μm 超精密加工: 加工精度< 0.1μm, Ra < 0.01μm 发展方向:加工精度 < 1nm(10-3μm), Ra<0.005μm纳米加工
般都在刀尖处磨成折线或圆弧形过渡刃。
34
第2章 超精密切削与金刚石刀具
1)前角γ0 --前刀面与基面间夹角
2)后角α0 -- 后刀面与切削平面间 夹角
3)主偏角kr --主切削刃在基面上投 影与进给方向间夹角
4)刀尖角εr --主切削刃与副切削刃 在基面上投影间夹角
5)刃倾角λs -- 主切削刃与基面之间夹角
36
第2章 超精密切削与金刚石刀具
5) 刀具刃口锋锐度ρ ➢ 刃口圆弧半径ρ越小,切削厚度就越薄,越能够减小切
削表面弹性恢复和表面变质层。 ➢ ρ与切削刃的加工方位有关,普通刀具5~30μm,金刚石
刀具<10nm,最好能够< 5nm; ➢ 从物理学的观点,刃口半径ρ有一极限(后续介绍)。
37
ρ
第2章 超精密切削与金刚石刀具
• 在所处时代,用一般技术水平即可实现的精度称普通加工。
• 必须用较高精度加工机械、工具及高水平加工技术才能达到 的精度,属于精密加工。
• 一般方法不能轻而易举地达到,需要采用先进的技术经过探 讨、研究、实验之后才能达到的精度,且这一精度指标尚不能 普及的加工技术称为超精密加工。
12 12
第1章 绪 论
18 18
第1章 绪 论
高尺寸精度
金刚石切削
超
高精度 高形位精度 加工
超精密磨削
磨料加工
精
低粗糙度
精密研磨、抛光 (无磨料研抛)
密 加
物理加工
电火花加工 等离子加工 激光加工 电子束加工
工
超声波加工
方
法
微细尺寸加工
喷射加工 微波加工 原子束加工
精密特 种加工
化学加工
化学能加工 电解加工 精密电铸
光刻加工
3
第1章 绪 论
1.3 加工方法分类
Manufacturing Machining Fabrication
1.3.1 根据加工方法机理和特点分类
Processing
可以分为三大类:去除加工、结合加工、变形加工
(1) 去除加工 ——从工件上去除不需要那部分材料的加工方法。
主要包括:
切削、铣削、钻削、磨削、研磨、珩磨、电火花加工、 电解加工、蚀刻、等离子加工、激光加工、脱碳处理等。
(3) 变形加工 ——利用力、热、分子运动等手段使工件产生变形, 改变其尺寸、形状和性能。
主要包括: 锻造、热流动加工、铸造、液体流动加工等。
77
第1章 绪 论
1.3.2 根据加工过程中材料的流动形态来分类
——去除加工是使材料逐渐减少,一部分材料变为切屑,这 种流动称之为分散流;
——结合加工是使材料逐渐增加,这种流动称之为汇合流; ——变形加工是使材料形变而量不变,这种流动称之为直通
SPDT加工精度: • 粗糙度Ra=0.02-0.005μm • 非球面形状精度≤ 0.1μm • 平面度≤0.06 μm
光学棱镜、镜头 无氧铜、铝合金件28
第2章 超精密切削与金刚石刀具
(1)平面镜切削示例
0. 5μm
塑性域加工 脆塑过渡切削 脆性域切削
29
第2章 超精密切削与金刚石刀具
30
第2章 超精密切削与金刚石刀具
44
第1章 绪 论
(2) 结合加工 ——利用理化方法将不同材料结合在一起的制造方法, 又分为附着、注入和连接三种。
附着(Deposition)加工: 在工件表面上覆盖一层物质,是一种弱结合,包括: 化学镀、化学气相沉积、电镀、真空蒸镀、离子镀、物理气相沉ຫໍສະໝຸດ 等;55第1章 绪 论
注入(Injection)加工: 在工件表面注入某些元素,使之与基体材料产生物化反应,
16 16
第1章 绪 论
实现精密、超精密加工的基本条件:
超精密加工 工具
超精密加工 环境
超精密加工 设备
精密超精密 加工技术
工件材料
超精密 测量技术
17 17
第1章 绪 论
1.4.3 超精密加工技术的范畴与种类
超精密加工技术的研究内容主要包括: • 超精密加工的机理 • 超精密加工的设备制造技术 • 超精密加工工具及刃磨技术 • 超精密加工测量技术和误差补偿技术 • 超精密加工工作环境条件
(1)良好的导热特性(热导率和比热容高); (2)在相同条件下计算其摩擦面的温升,仅为其它工具
材料的1/5; (3)膨胀系数低,抗热冲击; (4)耐热性和耐热损伤性有一限度。最大问题是金刚石
(2)球面镜切削示例
球面镜加工原理
1-主轴;2-凹面镜;3-刀具轴
31
第2章 超精密切削与金刚石刀具
(3)大型金刚石刀具切削机床示例
LLNL的LODTM超精密车床
• Work table: 1.65 m dia
• Figure accuracy: 0.028 μm
• Surface finish :3.5-9.0 nm
32
第2章 超精密切削与金刚石刀具
(4) 微构形或曲面加工
菲涅耳(Fresnel)透镜
平面度<0.06 µm;表面粗糙度Rmax<0.02 µm
33
具备加工面型检测功能,以补偿刀具磨损
第2章 超精密切削与金刚石刀具
2.2 金刚石刀具结构与特性
2.2.1 刀具角度知识的复习
• 前刀面Aγ ——刚形成的切屑沿其流出的刀面 • 后刀面Aa —— 与工件加工表面相对的刀面 • 切削刃S—— 前刀面与后刀面的交线,承担主要切削工作 • 刀尖 —— 主、副切削刃的实际交点,为了强化刀尖,一
是具有共价键、离子键、金属键的强结合,用以改变工件表层材 料的力学机械性质,包括:
氧化、氮化、活性化学、阳极氧化、晶体生长、离子生长、 离子束外延等;
连接(Jointed)加工: 将两种相同或不同材料通过物化方法连接一起,包括: 激光焊接、气焊、RP快速成形制造(3D打印制造)等;
66
第1章 绪 论
20 20
第1章 绪 论
工件材料与加工方法
无机 硬脆 材料
材料 半导体材料、陶瓷 … 玻璃、石英 … 蓝宝石、金刚石 …
软质金属塑料
耐热合复合材料
超精密加工方法 超精密磨削 超精密研磨 超精密抛光
超精密金刚石切削
超精密磨削 超精密研磨、抛光
21 21
第1章 绪 论
对材料难加工的重新认识 难加工材料不再难加工 可优化零件的加工工艺过程 传统加工:加工→ 淬火→加工 特种加工:淬火→ 加工(电解)
去除材料的单位为10-3cm时将以龟裂的形式发生破坏;以微 米(μm)级尺寸去除,则表现为位错,这一层次的加工属于精 密加工。
14 14
第1章 绪 论
按去除尺寸单位划分精度等级
Ⅲ一Ⅳ区间称为普通精度 Ⅱ一Ⅲ区间为精密加工 I一Ⅱ区间为超精密加工
15 15
第1章 绪 论
1.4.2 精密、超精密加工精度的范围与条件
27
第2章 超精密切削与金刚石刀具
2.1 金刚石超精密加工技术概述
超精密切削可以分为超精密车削、超精密铣削、超精密镗
削和超精密钻削,其中最常用的是金刚石刀具超精密车削,一
般称为单刃金刚石车削 (Simple Point Diamond Turming, SPDT) 。
SPDT主要应用: • 激光或红外平面 • 非球面反射镜 • 磁盘铝基底 • 多面棱镜等
19 19
第1章 绪 论
1.4.4 超精密加工的材料对象与应用
高硬度、高强度耐热合金
超
金属
(应用:航空、 航天、原子能工业)
精
材料
非铁金属材料
密
(应用:激光技术、光学、电子工业)
加
工
的
材
料
非金属
材料
高分子有机材料 (应用:光学、化学、电子工业)
复合材料 (应用:航天、能源工业) 无机硬脆材料
(应用:电子、原子能、能源工业)
对零件结构设计带来变革 重新衡量结构工艺性的优劣
传统加工中方孔的工艺性差 22 22
第1章 绪 论
1.4.5 精密、超精密加工技术的重要性
发展高技术和新产品的技术基础 当代高技术的产品,都是靠当代最高的加工技术-超精 密加工来实现的。 超精密加工的直接效果是促进了各种产品技术性能的提 高,也就相应地促进了机械、电子、航空、航天、激光 核聚变等高技术的发展。
加工 精度 概念 的时 代发 展性
13 13
第1章 绪 论
另一种概念是从被加工部位发生破坏和去除材料大小的尺 寸单位来划分各种加工。