★钢水LF炉精炼成分稳定控制的措施
LF炉外精炼

LF炉外精炼随着现代科学技术的发展和工农业对钢材质量要求的提高,钢厂普遍采用了炉外精炼工艺流程,它已成为现代炼钢工艺中不可缺少的重要环节。
由于这种技术可以提高炼钢设备的生产能力,改善钢材质量,降低能耗,减少耐材、能源和铁合金消耗,因此,炉外精炼技术已成为当今世界钢铁冶金发展的方向。
对于炉外精炼技术存在的问题及发展方向有必要进行探讨。
随着炼钢技术的不断进步,炉外精炼在现代钢铁生产中已经占有重要地位,传统的生产流程(高炉→炼钢炉(电炉或转炉)→铸锭),已逐步被新的流程(高炉→铁水预处理→炼钢炉→炉外精炼→VD→连铸)所代替。
已成为国内外大型钢铁企业生产的主要工艺流程,尤其在特殊钢领域,精炼和连铸技术发展得日趋成熟。
精炼工序在整个流程中起到至关重要的作用,一方面通过这道工序可以提高钢的纯净度、去除有害夹杂、进行微合金化和夹杂物变性处理;另一方面,精炼又是一个缓冲环节,有利于连铸生产均衡地进行。
炉外精炼技术在生产中的应用目前得到公认并被广泛应用的炉外精炼方法有:LF法、RH法、VOD法。
而石钢采用的是LF炉外精炼。
LF是1971年由日本大同钢公司发明的,用电弧加热,包底吹氩搅拌。
一、LF炉的主体设备包括:1、变压器及二次回路;2、电极、电极提升柱及电极臂;3、炉盖及抽气罩;4、吹氩搅拌系统;5、钢包及钢包运输车;6、渣料、合金加入及称量系统。
二、炉外精炼技术的特点与功能炉外精炼是指在钢包中进行冶炼的过程,是将真空处理、吹氩搅拌、加热控温、喂线喷粉、微合金化等技术以不同形式组合起来,出钢前尽量除去氧化渣,在钢包内重新造还原渣,保持包内还原性气氛。
炉外精炼的目的是降低钢中的P、S、O、H、N、等元素在钢中的含量,以免产生偏析、白点、大颗粒夹杂物,降低钢的抗拉强度、韧性、疲劳强度、抗裂性等性能。
这些工作只有在精炼炉上进行,。
LF炉有如下独特的精炼功能:1、埋弧加热。
LF炉有3根石墨电极,加热时电极插入渣层中进行埋弧加热,因而辐射热小,减少对包衬的损坏,可减少电弧的热辐射损失,提高热效率,终点温度的精确度≤±5℃。
LF精炼过程的钢水温度控制

LF精炼过程的钢水温度控制1前言:近年来,随着洁净钢冶炼技术的发展,LF作为主要的炉外精炼手段,在洁净钢冶炼过程中得到了广泛应用,其生产技术也在不断地完善和发展。
同电弧炉相比,LF的熔池要深得多,为了保证连铸的生产顺行,LF冶炼过程的温度控制是其主要冶炼目标之一,因此其加热过程的温度控制显得非常重要。
本文在分析LF炉能量平衡的基础上,进行了LF精炼过程温度控制工业试验,对实现LF炉内钢液处理温度的合理控制有着重要意义。
2影响LF冶炼过程钢水温度变化的因素2 .1由于LF化学反应热效应很小,可以忽略不计,因此为LF炉提供的能量只有从变压器输出的电能,即变压器的有功功率e。
变压器二次侧输出的电能,一部分功率被线路上存在的电阻消耗掉,称之为线路损失的功率r,另一部分转变为电弧热量即电弧功率arc。
由电弧产生的热能arc 一部分传给熔池(炉渣和钢水),另一部分损失掉,传递给包衬和水冷包盖ar。
而电弧电能传给熔池的比例主要取决于电弧埋入炉渣的深度。
进入熔池的热量ab又可分为三大去向。
第一部分用于钢水和炉渣的加热升温所需热量m和渣料及合金熔化升温所需热量ch,两者之和即为加热熔池的热量bath。
第二部分是指通过包衬损失的热量ls,其中又分成两部分,一部分热量成为包衬耐火材料的蓄热ln而使包衬温度升高,另一部分是由包壳与周围大气的热交换而损失的热量shell。
第三部分热量是通过渣面损失的热量sa,其中一部分是通过渣面的辐射和对流传热的热损sl,另一部分是由熔池内产生的高温气体通过渣面排走的热量g。
上述分析可以清楚地表LF炉能量的输入和输出及其分配关系。
在LF炉的操作过程中,由于上述因素相互作用、相互影响,因此,其实际的温度控制较为复杂。
3 LF炉温度控制试验3. 1试验内容为了实现LF炉稳定的温度控制,首先根据150tLF炉的供电系统特点及电阻与电抗值,结合电、热参数绘制出不同电压下“电热特性曲线”,根据理论计算确定的工作点,对Q235A钢种进行了LF炉冶炼试验,试验安排及结果见表1。
LF精炼工艺制度及钢水处理效果
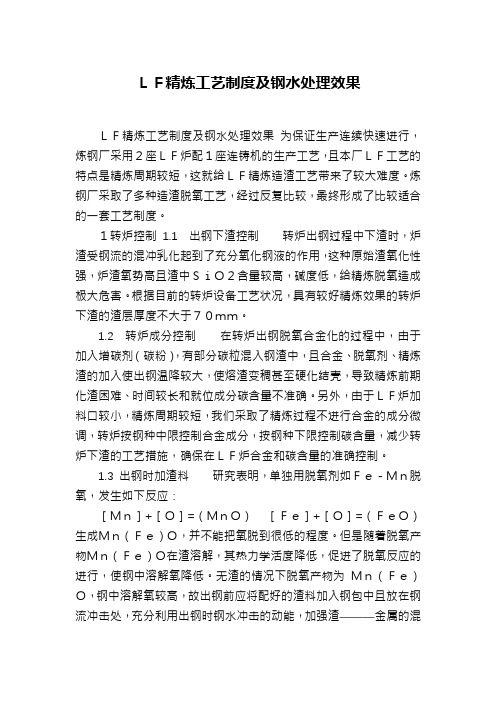
LF精炼工艺制度及钢水处理效果LF精炼工艺制度及钢水处理效果为保证生产连续快速进行,炼钢厂采用2座LF炉配1座连铸机的生产工艺,且本厂LF工艺的特点是精炼周期较短,这就给LF精炼造渣工艺带来了较大难度。
炼钢厂采取了多种造渣脱氧工艺,经过反复比较,最终形成了比较适合的一套工艺制度。
1转炉控制1.1出钢下渣控制转炉出钢过程中下渣时,炉渣受钢流的混冲乳化起到了充分氧化钢液的作用,这种原始渣氧化性强,炉渣氧势高且渣中SiO2含量较高,碱度低,给精炼脱氧造成极大危害。
根据目前的转炉设备工艺状况,具有较好精炼效果的转炉下渣的渣层厚度不大于70mm。
1.2转炉成分控制在转炉出钢脱氧合金化的过程中,由于加入增碳剂(碳粉),有部分碳粒混入钢渣中,且合金、脱氧剂、精炼渣的加入使出钢温降较大,使熔渣变稠甚至硬化结壳,导致精炼前期化渣困难、时间较长和就位成分碳含量不准确。
另外,由于LF炉加料口较小,精炼周期较短,我们采取了精炼过程不进行合金的成分微调,转炉按钢种中限控制合金成分,按钢种下限控制碳含量,减少转炉下渣的工艺措施,确保在LF炉合金和碳含量的准确控制。
1.3 出钢时加渣料研究表明,单独用脱氧剂如Fe-Mn脱氧,发生如下反应:[Mn]+[O]=(MnO)[Fe]+[O]=(FeO)生成Mn(Fe)O,并不能把氧脱到很低的程度。
但是随着脱氧产物Mn(Fe)O在渣溶解,其热力学活度降低,促进了脱氧反应的进行,使钢中溶解氧降低。
无渣的情况下脱氧产物为Mn(Fe)O,钢中溶解氧较高,故出钢前应将配好的渣料加入钢包中且放在钢流冲击处,充分利用出钢时钢水冲击的动能,加强渣———金属的混合,达到脱氧、脱硫的目的。
为此,我们采取了出钢过程加精炼渣的工艺制度,采取的精炼渣渣系为:CaO-Al2O3-MgO,主要成分见表1:表1精炼渣系的主要成分成分W(CaO) W(Al2O3) W(MgO) W(Fe2O3) W(TiO2) 精炼渣% 45.9 29.5 1.9 1.3 1.6 钢包中的w(Mn)/%2加热制度钢包精炼炉的二次测电压范围为150V~加热制度215V,分为4档,调方式为有载或无载。
炼钢生产中的钢水调理与成分控制策略

炼钢生产中的钢水调理与成分控制策略炼钢生产是钢铁行业中至关重要的环节之一,其中的钢水调理与成分控制是影响钢材质量和性能的重要因素。
本文将从钢水调理的基本概念、调理方法和成分控制策略三个方面进行论述,以期提供有关炼钢生产中钢水调理与成分控制的深入了解。
一、钢水调理的基本概念钢水调理是指在钢水冶炼过程中对钢水进行组分和温度的调整,以达到特定的化学成分和温度要求,确保钢水在浇铸过程中具备良好的流动性和凝固性能。
钢水调理主要包括合金元素控制、非金属夹杂物的减少和温度的控制。
合金元素控制是指通过适当添加或删除合金元素,使钢水的化学成分达到设计要求。
在钢铁生产中,常用的合金元素有铬、镍、钼、铜等。
通过合金元素的添加和控制,可以调整钢水的抗腐蚀性、强度和硬度等性能。
非金属夹杂物的减少是为了避免在钢铁生产过程中产生夹杂物,这些夹杂物会影响钢铁的力学性能和表面质量。
通过加入熔化剂和熔化处理,可以有效地减少夹杂物的含量,提高钢铁的品质。
温度的控制是钢水调理的另一个重要方面。
钢水在浇铸过程中需要具备一定的流动性和凝固性能,只有在适当的温度范围内才能实现这一要求。
因此,在钢水调理过程中,需要精确地控制钢水的温度,以确保良好的铸造效果。
二、钢水调理的方法钢水调理有多种方法,包括物理方法、化学方法和结构调理等。
下面将分别对这些方法进行介绍。
1. 物理方法物理方法是通过调整钢水的温度和流动性来控制钢水的成分。
钢水冶炼过程中,可以通过加热或降温来改变钢水的温度,从而实现对钢水成分的调控。
此外,还可以通过调整浇注速度、浇注方式和浇注时间等参数,来改善钢水的流动性和凝固性能。
2. 化学方法化学方法是通过添加特定的化学剂来调整钢水的成分。
在钢铁生产中,经常使用的化学剂有焙烧石灰、脱氧剂、矫正剂等。
这些化学剂可以改变钢水中的氧化物含量、气体含量和非金属夹杂物含量,从而控制钢水的化学成分。
3. 结构调理结构调理是通过改变钢水的结晶结构,来调整钢水的成分。
钢水精炼处理过程中化学成分的精确控制
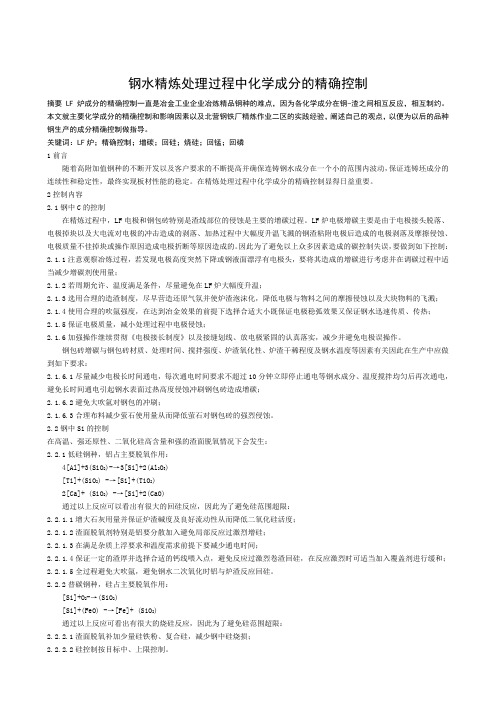
钢水精炼处理过程中化学成分的精确控制摘要 LF炉成分的精确控制一直是冶金工业企业冶炼精品钢种的难点,因为各化学成分在钢-渣之间相互反应,相互制约。
本文就主要化学成分的精确控制和影响因素以及北营钢铁厂精炼作业二区的实践经验,阐述自己的观点,以便为以后的品种钢生产的成分精确控制做指导。
关键词:LF炉;精确控制;增碳;回硅;烧硅;回锰;回磷1前言随着高附加值钢种的不断开发以及客户要求的不断提高并确保连铸钢水成分在一个小的范围内波动,保证连铸坯成分的连续性和稳定性,最终实现板材性能的稳定。
在精炼处理过程中化学成分的精确控制显得日益重要。
2控制内容2.1钢中C的控制在精炼过程中,LF电极和钢包砖特别是渣线部位的侵蚀是主要的增碳过程。
LF炉电极增碳主要是由于电极接头脱落、电极掉块以及大电流对电极的冲击造成的剥落、加热过程中大幅度升温飞溅的钢渣粘附电极后造成的电极剥落及摩擦侵蚀、电极质量不佳掉块或操作原因造成电极折断等原因造成的。
因此为了避免以上众多因素造成的碳控制失误,要做到如下控制:2.1.1注意观察冶炼过程,若发现电极高度突然下降或钢液面漂浮有电极头,要将其造成的增碳进行考虑并在调碳过程中适当减少增碳剂使用量;2.1.2若周期允许、温度满足条件,尽量避免在LF炉大幅度升温;2.1.3选用合理的造渣制度,尽早营造还原气氛并使炉渣泡沫化,降低电极与物料之间的摩擦侵蚀以及大块物料的飞溅;2.1.4使用合理的吹氩强度,在达到冶金效果的前提下选择合适大小既保证电极稳弧效果又保证钢水迅速传质、传热;2.1.5保证电极质量,减小处理过程中电极侵蚀;2.1.6加强操作继续贯彻《电极接长制度》以及接缝划线、放电极紧固的认真落实,减少并避免电极误操作。
钢包砖增碳与钢包砖材质、处理时间、搅拌强度、炉渣氧化性、炉渣干稀程度及钢水温度等因素有关因此在生产中应做到如下要求:2.1.6.1尽量减少电极长时间通电,每次通电时间要求不超过10分钟立即停止通电等钢水成分、温度搅拌均匀后再次通电,避免长时间通电引起钢水表面过热高度侵蚀冲刷钢包砖造成增碳;2.1.6.2避免大吹氩对钢包的冲刷;2.1.6.3合理布料减少萤石使用量从而降低萤石对钢包砖的强烈侵蚀。
LF精炼工艺流程及控制要点
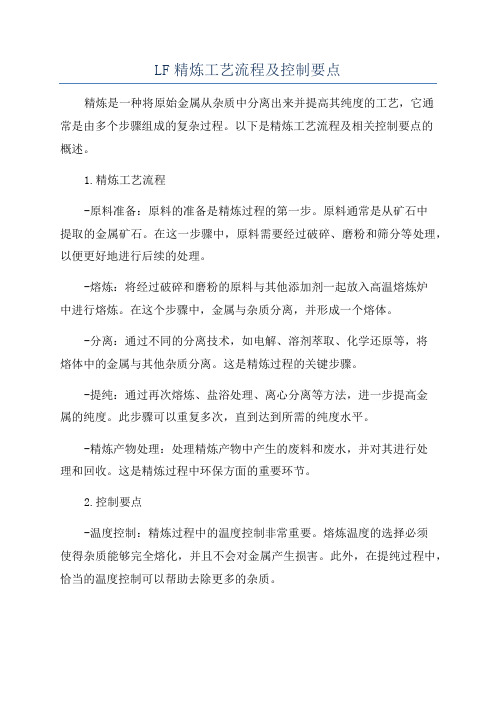
LF精炼工艺流程及控制要点精炼是一种将原始金属从杂质中分离出来并提高其纯度的工艺,它通常是由多个步骤组成的复杂过程。
以下是精炼工艺流程及相关控制要点的概述。
1.精炼工艺流程-原料准备:原料的准备是精炼过程的第一步。
原料通常是从矿石中提取的金属矿石。
在这一步骤中,原料需要经过破碎、磨粉和筛分等处理,以便更好地进行后续的处理。
-熔炼:将经过破碎和磨粉的原料与其他添加剂一起放入高温熔炼炉中进行熔炼。
在这个步骤中,金属与杂质分离,并形成一个熔体。
-分离:通过不同的分离技术,如电解、溶剂萃取、化学还原等,将熔体中的金属与其他杂质分离。
这是精炼过程的关键步骤。
-提纯:通过再次熔炼、盐浴处理、离心分离等方法,进一步提高金属的纯度。
此步骤可以重复多次,直到达到所需的纯度水平。
-精炼产物处理:处理精炼产物中产生的废料和废水,并对其进行处理和回收。
这是精炼过程中环保方面的重要环节。
2.控制要点-温度控制:精炼过程中的温度控制非常重要。
熔炼温度的选择必须使得杂质能够完全熔化,并且不会对金属产生损害。
此外,在提纯过程中,恰当的温度控制可以帮助去除更多的杂质。
-化学反应控制:根据不同的精炼过程,化学反应控制往往是必不可少的。
正确选择和控制反应剂的加入量和反应时间,可以提高精炼效果和产出的纯度。
-溶剂选择:对于溶剂萃取和其他液相分离技术,正确选择和控制溶剂的使用是至关重要的。
溶剂的选择取决于金属和杂质之间的相互作用,以及溶剂的物理和化学性质。
-废物处理:在精炼过程中产生的废物必须进行安全处理和有效回收。
合理设计废物处理系统,并采用适当的处理方法,如过滤、沉淀、离心等,可最大限度地减少对环境的污染。
-质量控制:在整个精炼过程中,质量控制是至关重要的。
使用精密的分析方法对金属样品进行测试,并采取相应的措施,以确保产品符合相关的质量要求。
总结起来,精炼工艺流程及其控制要点是一个复杂的过程,需要针对不同的金属和杂质制定合适的控制策略。
LF精炼炉基本工艺
04
lf精炼炉操作要点
安全操作规程
操作前检查
确保炉体、管道、阀门等设备 完好无损,无泄漏现象。
严格控制温度
遵循工艺要求,控制炉内温度 ,避免超温引起设备损坏或安 全事故。
防止气体泄漏
定期检查炉体和管道的密封性 ,确保气体不泄漏,防止中毒 和爆炸。
操作人员培训
操作人员需经过专业培训,熟 悉安全操作规程,掌握应急处
案例二:某有色金属企业lf精炼炉工艺应用
总结词
扩大产品品种、提高生产效率
详细描述
该有色金属企业利用lf精炼炉工艺,成功开发出多种高附加值产品,拓展了市场应用领域。同时,通 过改进工艺参数和设备配置,提高了生产效率和能源利用效率,降低了生产成本。
案例三:某新材料企业lf精炼炉工艺创新
总结词
突破技术瓶颈、提升竞争力
VS
详细描述
该新材料企业针对特定产品需求,创新性 地开发出新型lf精炼炉工艺。通过采用先 进的熔炼技术和材料制备方法,成功突破 了关键材料制备的技术瓶颈,提高了产品 质量和性能,增强了企业在国内外市场的 竞争力。
THANKS
感谢观看
表面处理
对铸锭表面进行清理、修整和抛光等处理,以提高产品的外观质量。
成品检测与包装
检测标准与项目
根据产品标准和客户要求,制定相应的检测标准和项目,对成品 进行全面的质量检测。
检测方法与设备
选择合适的检测方法和设备,确保检测结果的准确性和可靠性。
包装与标识
对合格的成品进行包装和标识,以便于运输、存储和使用。
03
lf精炼炉工艺参数
熔炼温度
熔炼温度
熔炼温度是lf精炼炉工艺中的重要参数,它决定了钢水的温度 和流动性。熔炼温度过高可能导致钢水氧化和氮化,而熔炼 温度过低则可能导致钢水流动性差,影响铸锭质量。
LF精炼过程钢中硫、磷、氮、氧含量控制
LF精炼过程钢中硫、磷、氮、氧含量控制作者:钱丹丹陈志月闫若璞来源:《中国科技博览》2016年第07期[摘要]将转炉、平炉或电炉中初炼过的钢液移到另一个容器中进行精炼的炼钢过程,也叫“二次炼钢”。
炼钢过程因此分为初炼和精炼两步进行。
初炼:炉料在氧化性气氛的炉内进行熔化、脱磷、脱碳和主合金化。
精炼:将初炼的钢液在真空、惰性气体或还原性气氛的容器中进行脱气、脱氧、脱硫,去除夹杂物和进行成分微调等。
这样将炼钢分两步进行,可提高钢的质量,缩短冶炼时间,简化工艺过程并降低生产成本。
[关键词]LF精炼脱硫脱磷氮、氧含量 s非金属夹杂物中图分类号:U231.92 文献标识码:A 文章编号:1009-914X(2016)07-0277-011.引言:钢材的质量及性能是根据需要而确定的,不同的需要,要有不同的元素含量。
硫;是钢中的有害杂物,含硫较高的钢在高温进行压力加工时,容易脆裂,通常叫做热脆性。
磷;能使钢的可塑性及韧性明显下降,特别的在低温下更为严重,这种现象叫做冷脆性。
通常情况下,氮被视为钢中的有害元素,而氧元素主要以氧化物系非金属夹杂物的形式存在于钢中。
减少LF 炉精炼工艺过程钢液增氧、去除钢中氢含量是生产优质钢的关键环节。
此外,控制钢中夹杂物是提高钢材使用性能的有效途径。
2.转炉LF精炼脱硫与脱磷2.1脱硫2.1.1脱硫方法硫是钢中的长存元素之一,它会使大多数钢种的加工性能和使用性能变坏,因此除了少数易切削钢种外,它是需要在冶炼中脱除的有害元素。
硫在钢中以[FeS]形式存在,常以[S]表示。
钢中含锰高时,还会有一定的[MnS]存在。
目前炼钢生产中能有效脱除钢中硫的方法有碱性氧化渣脱硫、碱性还原渣脱硫和钢中元素脱硫三种。
2.1.2 脱硫影响因素脱硫影响因素与碱性氧化渣脱硫不同,LF碱性还原渣脱硫反应方程式为:[FeS]+(CaO)=(CaS)+(FeO)(1) [MnS]+(CaO)=(CaS)+(MnO)(2)由于钢中的[S]大部分以[FeS]形式存在,因此脱硫反应主要以式(1)为主。
冶金工业炉外精炼(LF)的应用分析
冶金工业炉外精炼(LF)的应用分析山西通才工贸有限公司山西临汾 043409摘要:钢液精炼是钢铁生产过程中的重要环节,因为它可以降低氧化合金的利用率。
这意味着,通过精炼,可以减少废料的产生,同时提高钢材的质量。
在过去,精炼通常在转炉内进行,但是,这种方法存在一些问题,例如回收率不均衡等。
为了解决这些问题,炉外精炼(LF)技术被广泛采用。
这种技术可以显著改善钢液的纯度,从而提高钢材的质量。
除了提高钢材的质量,炉外精炼(LF)技术还可以减少转炉内渣量到5%,这意味着这种技术可以提高炉渣的浮率。
这对于钢铁生产是非常重要的,因为高浮率可以减少废料的产生。
炉外精炼(LF)技术在保证钢材稳定生产方面起着举足轻重的作用。
这种技术可以确保钢铁生产的过程中不会出现问题,从而保证钢材的质量和数量。
关键词:冶金工业炉;外精炼(LF);应用1冶金工业中炉外精炼(LF)的应用意义炉外精炼技术在冶金行业中的应用越来越广泛,它在钢铁生产过程中扮演着至关重要的角色。
炉外精炼可以改进热力条件,降低气体压力,改善真空现象。
这样,就可以保证炼钢过程中的温度、压力和气氛等因素的稳定性,从而提高冶金反应速度,保证炼钢过程的均匀性。
此外,炉外精炼可以提高渣钢的反应面积,加快反应速度。
在炉外精炼的过程中,通过对渣钢进行预处理和加入适当的精炼剂,可以提高渣钢的反应活性,使其与精炼剂充分混合,从而促进反应的进行,提高反应效率和产量。
炉外精炼装置具有加热功能,可以精确控制反应条件,满足各阶段的供热要求,实现精细的配方调整。
这样,就可以根据不同的生产需求,对炉外精炼装置进行精细的调节和控制,从而实现最佳的生产效果。
总的来说,炉外精炼技术的应用,不仅可以提高钢铁生产的效率和产品质量,而且可以降低能源消耗和环境污染,具有非常重要的经济和社会效益。
因此,在未来的钢铁生产中,炉外精炼技术将会得到更加广泛的应用和推广。
2炉外精炼(LF)简介钢铁生产是工业生产中非常重要的一环。
LF精炼操作过程控制要点
LF精炼操作过程控制要点精炼是冶金行业的重要环节,它的目的是通过各种物理和化学处理方法,从原始金属中去除杂质,提高纯度和质量。
精炼操作过程的控制是确保产品质量稳定和生产效益的关键。
下面是一些精炼操作过程控制的要点,以确保安全高效的生产。
1.原料检测和管理:确保原料的质量和纯度与生产要求相匹配,进行适当的检测和测试。
建立原料管理制度,对原料进行分类储存和标识,防止混淆和误用。
2.温度控制:精炼过程中的温度对产品的纯度和质量有着直接影响。
确保加热和冷却设备的正常运行和精确的温度控制。
监测和记录温度变化,及时调整操作参数。
3.压力控制:精炼过程中的压力也是一个重要的控制参数,对保证操作安全和产品质量具有重要影响。
确保设备的密封性和稳定性,监测和记录压力变化,及时调整操作参数。
4.流量控制:精炼过程中的流体流量需要精确控制,以确保反应和处理的均匀和持续。
安装适当的流量计和调节阀,监测和记录流量变化,及时调整操作参数。
5.添加剂和催化剂的控制:在精炼过程中,常常需要添加特定的剂量剂和催化剂,以促进反应和提高纯度。
确保添加剂和催化剂的质量和纯度,确保正确的添加剂量,避免过量或不足。
6.操作人员培训和管理:培训操作人员,使其了解精炼过程的原理、工艺和控制要点。
设立标准操作程序,确保操作规范和操作人员的安全意识。
7.检测和分析:建立完善的检测和分析体系,对产品的质量进行监测和评估。
对关键参数进行实时监测,及时调整操作参数以控制产品质量和过程稳定性。
8.故障排除和维护:及时发现并解决设备故障,确保设备的正常运行。
定期对设备进行维护和保养,以延长设备寿命和提高工作效率。
9.数据记录和分析:建立完善的数据记录和分析系统,对生产过程进行数据采集和分析。
通过统计和分析过程数据,及时调整操作参数以优化生产效益和质量控制。
10.环境保护和安全措施:在精炼操作过程中,确保操作环境的安全和设备的正常运行,采取必要的环境保护和安全措施,避免事故和污染。
- 1、下载文档前请自行甄别文档内容的完整性,平台不提供额外的编辑、内容补充、找答案等附加服务。
- 2、"仅部分预览"的文档,不可在线预览部分如存在完整性等问题,可反馈申请退款(可完整预览的文档不适用该条件!)。
- 3、如文档侵犯您的权益,请联系客服反馈,我们会尽快为您处理(人工客服工作时间:9:00-18:30)。
钢水LF 炉精炼成分稳定控制的措施陈永金覃强周汉全(转炉炼钢厂)刘川俊(技术中心)摘要:总结稳定控制150 t LF 炉精炼钢水中C、Si、Mn、P、S、Al、Ti、气体等的措施及其效果。
关键词:钢水精炼;LF 炉;稳定;C;Si;Mn;P;S;Al;Ti;气体1 前言随着柳钢高附加值钢种的不断开发以及客户要求的不断提高,确保连铸钢水成分在一个小的范围内波动,保证连铸坯成分的连续性和稳定性,最终实现材质性能的稳定,显得日益重要。
尤其是在精炼处理过程中钢水成分的精确控制。
目前,柳钢通过LF 精炼炉一般能控制w(C)在±0.02 %,w(Si)、w(Mn)在±0.03%,w(S)、w(P)≤目标值。
在LF 精炼炉实现钢液成分的精确控制,必须遵循下列原则:钢液脱氧良好;造好精炼渣;取样具有代表性;钢水质量;准确的合金成分;在线快速分析。
2成分稳定控制措施2.1 钢中C 的控制在精炼过程中,LF 电极、钢包内衬特别是渣线部位的侵蚀等都是增碳过程。
LF 电极增碳主要是由于大电流的冲击造成电极端部剥落,加热过程中大幅度升温飞溅的钢渣粘附于电极,电极质量或操作原因造成电极掉块等造成[1]。
因此为了避免上述因素造成的碳控制失误,要做到如下控制:(1)注意观察精炼过程,若发现电极高度突然下降或钢液面漂浮有电极头,要将其造成的增碳进行考虑,并在调碳过程中适当减少增碳剂使用量。
(2)尽量避免在LF 炉大幅度升温,尽量减少电极长时间通电,且每次通电时间要求不超过10 min。
停止通电后待钢水成分、温度搅拌均匀后再次通电。
避免长时间通电引起钢水表面过热,过度侵蚀、冲刷钢包砖造成的增碳。
(3)选用合理的造渣制度,尽早营造还原性气氛,并使炉渣泡沫化,降低电极与物料之间的摩擦侵蚀以及大块物料的飞溅。
造渣过程中,合理布料,减少萤石使用量,从而降低萤石对钢包砖的强烈侵蚀。
(4)选用合理的吹氩强度,保证钢水迅速传质、传热,避免大吹氩对钢包的冲刷。
(5)保证电极质量,减少处理过程中电极侵蚀。
(6)加强操作如接电极、放电极紧固等,减少并避免电极误操作。
(7)取样前,留意顶渣状态,避免形成电石渣在炉渣化透后造成钢液增碳。
(8)事故钢水回精炼炉升温时,需考虑覆盖剂增碳量。
(9)精炼过程中,需补加大量高碳合金如高碳铬铁、高碳锰铁等进行成分调整时,应考虑加入合金后的增碳量。
此外,在转炉出钢脱氧合金化的过程中,由于加入增碳剂,有一部分碳粒混入钢渣中,使熔渣变稠甚至硬化、结壳,在LF 炉送电处理过程中,混入渣中的碳粒逐渐进入钢液而使钢液增碳。
为解决这一问题,采取了炉前按钢种下限碳含量控制,减少转炉下渣量,优化石灰加入量和LF 炉第一次通电结束后中强搅3~5min后取样的措施,确保LF 炉碳含量命中钢种成分设计要求。
2.2 钢中Si 的控制在高温、强还原性、二氧化硅含量高和高还原性炉渣条件下,会发生回硅反应[1]。
因此,在精炼工序钢水Si 含量能否稳定控制在预定范围内,主要取决以下因素:转炉终渣成分和下渣量、LF炉的脱硫负荷、钢包顶渣的化学成分、钢包顶渣成渣路线与钢水中酸溶铝含量的合理匹配等。
2.2.1 低硅控铝系列低硅控铝系列,Al 起主要脱氧作用。
此外,Ti、Ca 元素与O 结合能力都比Si 要强。
因此,它们均可将SiO2中Si 置换出来,发生回硅反应。
为了避免Si 失控,采取的主要措施:(1)根据钢种成分设计特点、出钢下渣量,确定各工序合理的石灰加入量,保证炉渣碱度及良好流动性,从而降低二氧化硅活度。
(2)出钢过程严禁加铝系合金。
如必须加铝铁,应在合金化前加入少量进行弱脱氧,使其第一时间与钢水中氧发生反应,而不会上浮至表面将渣中SiO2还原。
(3)合金量比较大的低硅钢种,应尽可能减少合金中含硅量。
并由炉前与调度提前联系,要求使用铝钢用罐。
(4)严格控制使用含硅较低的精炼渣和改质剂等造渣原材料,避免钢水增硅。
同时,造渣过程中的顶渣脱氧剂尤其是铝粒要分散加入,避免局部脱氧过深而增硅。
(5)在满足夹杂物上浮要求、温度符合浇注要求的情况下,尽量减少通电时间。
(6)减少精炼过程脱氧加铝量,钢水到站后将w钢水(A)l 调至0.01%~0.03 %,即可满足脱硫要求。
Al 控制过高,既增加了钢中酸溶铝的损失,又会导致钢液回硅趋势增加。
(7)事故钢水待精炼期间,严禁加入任何脱氧剂,如钢芯铝、铝粒、改质剂、精炼渣等。
待生产节奏正常后,方可进行调渣、控铝。
(8)规范吹氩制度,避免全程大吹氩,减少渣钢间回硅反应。
(9)保证一定的渣厚并选择合适的钙线喂入点,控制好喂线量和喂线速度,减少或避免钢液“沸腾”造成钢水回硅。
2.2.2非低硅控铝、不控铝系列非低硅控铝系列,在调整硅时,尽可能在炉渣变白后加入;非低硅不控铝系列,采用硅锰合金进行成分调整时,注意增硅量。
此外,渣面需加强脱氧,减少钢中硅烧损。
采用硅钙钡强化脱氧、硅钙线进行钙处理时,增硅量也需考虑。
2.3 钢中Mn 的控制在LF 处理过程中,特别是在强还原性渣工艺条件下,渣中MnO 将会被还原进入钢水中,出现精炼过程中的“回锰”现象。
回锰量主要取决于钢包渣中的MnO含量和顶渣的还原性,并且发生在LF处理前期、造白渣结束这一时期。
因此,在LF 进行合金微调时,必须根据转炉终点氧化性、出钢下渣量、LF 处理工艺状况等预判回锰量,尽量在渣面脱氧结束、回锰反应基本结束后再调整锰,尤其是对于锰含量范围非常窄的钢种一定要注意。
2.4 钢中P 的控制钢中P主要决定于转炉终点P 含量和出钢过程下渣量,LF 精炼过程基本不承担去P 任务。
在LF 造白渣处理过程中,由于强烈的还原性气氛,钢包渣中的P2O5基本全部被还原进入钢水中。
而在出钢过程由于加入顶渣,渣量增加,降低了渣中的P2O5含量,同时由于钢包渣中的氧化性氛围降低,发生回磷。
因此有效地控制出钢下渣量、降低转炉渣中的P2O5含量、降低转炉终点钢水中的P 含量是控制钢中P 含量的重点。
在减少精炼过程回磷方面,主要是增加石灰加入量,保证顶渣碱度,降低渣中五氧化二磷活度等,这些措施对抑制回磷的作用比较有限,往往需要牺牲精炼工艺的完整性,尤其是冶炼低硫控铝系列的钢种。
2.5 钢中S 的控制实践证明,脱硫是导致精炼时间延长的主要因素。
转炉终点S 含量过高,势必造成LF 处理的渣料加入量大,造成LF 处理时间延长,消耗增加。
因此在冶炼低硫钢时,应采用铁水预脱硫、优质废钢,控制入炉铁水S 含量和转炉终点S 含量,以减轻LF 脱硫负担。
当然,钢包底吹状况、处理周期、来钢条件、精炼操作等都会对脱硫造成影响。
在提高LF 脱硫效率方面,主要有以下几点:(1)控制转炉出钢钢水质量,如降低钢水初始氧化性、减少出钢下渣量、合适的硫含量和温度等;(2)尽快造好还原性强炉渣是快速脱硫的前提条件,控制好钢中Al含量是保持白渣的必要条件;(3)确保一定的渣量亦是实现高脱硫率的必要条件;(4)监控好钢包底吹状况,生产w钢(S)≤0.010 %的钢种,严禁使用氩气小或单边通气的钢包。
2.6 钢中Al、Ti 的控制Al、Ti 由于自身化学性质的特点,即强还原性和易氧化性,因此会发生Al、Ti 的烧损现象。
为稳定控制钢中Al、Ti 含量,主要采取的措施:(1)造渣工艺前移。
根据出钢氧、下渣量,加入适量的渣料,在出钢、炉后吹氩过程,完成脱氧、初造渣工艺;(2)顶渣采用CaO- SiO2- Al2O3渣系,将钢包顶渣控制在合适范围内,保持顶渣良好的流动性和较高的渣温,保证脱氧、脱硫效果,同时避免顶渣过稀;(3)造白渣时,加入仅供造白渣脱氧需要的铝,等到炉内精炼白渣成形,再加入的增铝剂也不容易被二次氧化;(4)LF 调铝控钛时,需考虑精炼过程中Al、Ti 的烧损以及浇注过程中Al、Ti 的正常损失;(5)全程尽量避免大吹氩减少Al、Ti 烧损。
脱硫时,需考虑铝的烧损;(6)喂钙线过程中,控制好喂线速度,避免钢液翻滚严重,造成Al、Ti 二次氧化。
2.7 钢中气体的控制由于在LF 处理过程中,电弧冲击区处于高温状态下,O、N 在钢水中的平衡溶解度增加,并且在电弧的作用下气体分子发生电离,造成LF处理过程中钢水增氮和钢水中的自由氧浓度增加。
因此在LF 处理过程中要控制好顶渣的特性,形成发泡能力良好的精炼渣,保证埋弧加热,同时在LF处理过程中可以加入适量的埋弧渣,以提高精炼渣的发泡能力。
此外,保持好精炼过程炉内还原性气氛,有利于减少钢水二次氧化和吸氮现象,保证钢水纯净度。
2.8操作与管理(1)生产组织:生产组织是否合理,生产节奏是否稳定,对成分精确控制、钢水洁净度均产生较大影响。
通过加强与调度、钢包、行车的沟通,确保精炼周期和工艺操作的完整性;(2)钢包净空:正常合金加入量是以一定的钢包净空下钢水装入量进行计算,因此钢包在净空较大或较小时应该适当减少或增加合金用量,尤其是加入量本来就很少的合金如硼铁等;(3)渣厚控制:要保证加入的合金顺利进入钢水中,避免炉渣的阻粘造成合金加入浪费和成分控制难度大;(4)渣的氧化性:减少合金在炉渣中的氧化烧损。
精炼过程造渣效果不好,使各种反应不能正常进行,造成钢液中的元素成分不稳定;(5)贵重合金的使用及管理:加强贵重合金的分类存放与管理,避免加错合金等低级事故的发生;(6)钢液未得到充分搅拌,特别是在LF炉精炼过程中大量补加合金后尚未均匀就开始取样,也会造成成分的不稳定;(7)吹氩控制不合理,导致易氧化元素损失量比较大,合金回收率较低。
生产中,注意加强吹氩监控,执行好精炼吹氩工艺。
3结语通过提高工序交接质量如将铁水入炉标准、转炉终点C- T- O- P 控制目标、炉前上精炼的接收标准等纳入各小组经济责任制、加强放钢操作及挡渣锥的烘烤与管理、规范炉前操作、优化生产工艺等措施,使得精炼炉的化学成分的波动范围进一步缩小,成分综合中限命中率由2010 年的87.7%提高到2011 年的90.5%,品种钢内控命中率由2010 年的98.27%提高到2011年的98.94%,提高了炼钢的效率,为柳钢150 t系统新产品的开发打下了坚实的基础。
参考文献1 倪勤盛. 钢水精炼处理过程中化学成分的精确控制. 见:中国金属学会. 第七届中国钢铁年会论文集. 北京:冶金工业出版社,2009.63~66。