纯镍的数控车削加工工艺优化
数控机床加工工艺的优化方法

数控机床加工工艺的优化方法现代制造业的发展离不开数控机床的应用。
数控机床通过计算机控制系统,能够实现高精度、高效率的加工过程。
然而,在实际应用中,如何优化数控机床的加工工艺,提高加工效率和质量,一直是制造业工程师们所关注的问题。
本文将探讨一些数控机床加工工艺的优化方法。
首先,合理选择切削参数是优化数控机床加工工艺的关键。
切削参数包括切削速度、进给速度和切削深度等。
合理选择切削参数可以有效地降低加工时间和成本,提高加工质量。
切削速度是指刀具在切削过程中的线速度,它直接影响切削力和切削温度。
在选择切削速度时,需要考虑材料的硬度、刀具的材料和刀具的磨损情况等因素。
进给速度是指工件相对刀具的移动速度,它直接影响加工表面的粗糙度和加工效率。
在选择进给速度时,需要根据工件的材料和形状、刀具的类型和刀具的磨损情况等因素进行综合考虑。
切削深度是指刀具在一次切削中所切掉的工件材料的厚度,它直接影响切削力和切削温度。
在选择切削深度时,需要根据工件的材料和形状、刀具的类型和刀具的磨损情况等因素进行综合考虑。
其次,合理选择刀具材料和刀具几何形状也是优化数控机床加工工艺的重要方法。
刀具材料的选择直接影响切削力、切削温度和切削寿命。
常见的刀具材料有高速钢、硬质合金和陶瓷等。
高速钢刀具具有良好的韧性和切削性能,适用于一般的切削工艺。
硬质合金刀具具有较高的硬度和耐磨性,适用于高硬度材料的切削工艺。
陶瓷刀具具有较高的硬度和耐高温性能,适用于高温合金和陶瓷等脆性材料的切削工艺。
刀具几何形状的选择直接影响切削力、切削温度和加工表面质量。
常见的刀具几何形状有直刃刀具、球头刀具和锥度刀具等。
直刃刀具适用于平面加工和开槽等工艺。
球头刀具适用于球面加工和倒角等工艺。
锥度刀具适用于锥度加工和螺旋加工等工艺。
最后,合理选择加工路径和刀具路径也是优化数控机床加工工艺的关键。
加工路径是指刀具在工件上的运动轨迹,它直接影响加工时间和加工质量。
在选择加工路径时,需要考虑工件的形状和尺寸、刀具的类型和刀具的磨损情况等因素。
镍基合金Inconel718薄壁件铣削加工数控程序和切削参数优化

Op t i mi z a t i o n o f NC P r o g r a mmi n g a n d Cu t t i n g P a r a me t e r s i n Mi l l i n g o f
I n c o ne l 7 1 8 Thi n. wa l l Pa r t s
减小切削力波动 ,有助于改善薄壁件加 工过 程中的稳定性 。
关键词 :数控编程 ;有 限元仿真 ;工艺仿真 ;切 削力 ;切 削温度
中图分 类号 :T G 5 0 6 文献标 志码 :A 文章编号 :1 0 0 1 - 3 8 8 1( 2 0 1 6 )2 1 —1 0 9 - 5
S h a n d o n g U n i v e r s i t y , J i n a n S h a n d o n g 2 5 0 0 6 1 , C h i n a )
Ab s t r a c t :T h e l f u c t u a t i o n s o f c u t t i n g f o r c e ma y r e s u l t i n u n s t a b l e ma c h i n i n g p r o c e s s e s wh e n t h e t h i n — w a l l p a r t s a r e ma c h i n e d . S o c u t t i n g p r o c e s s n e e d s t o b e o p t i mi z e d .An o p t i mi z e d mo d e l o f NC p r o g r a mmi n g f o r mi l l i n g o f I n c o n e l 7 1 8 t h i n — wa l l p a r t s wa s e s t a b — l i s h e d . T h e p r e s e n t e d mo d e l c o n s i s t s o f NC p r o ra g mmi n g ,ma t e i r a l d a t a b a s e a n d C NC ma c h i n i n g s i mu l a t i o n . T h e s o l i d mo d u l e o f wo r k - p i e c e w a s d e v e l o p e d w i t h UG s o f t wa r e a n d NC c o d e s w e r e p r o ra g mme d . he T p a r a me t e r s o f c u t t i n g f o r c e a n d t e mp e r a t u r e or f I n c o n e l 7 1 8
车削加工镍基高温合金Inconel 718的加工工艺优化

车削加工镍基高温合金 Inconel 718的加工工艺优化摘要:在镍基高温合金的高速端面车削加工中,在某些特定的切削条件下,从被加工材料下分离出来的切屑会和已加工表面发生粘连,从而在工件表面上形成类似于毛刺的现象。
这种现象使得被加工表面的加工质量急剧下降,具体体现在表面光洁度的下降。
当冷却液被使用的时候,这种情况会有所改进,但是也依然存在。
用户反映在使用高温合金刀具切削 Inconel 718时,大量的工件发生此种现象,为此,在实验室开展了切削实验,对切屑的样品进行了成分分析,通过能谱分析,确定了毛刺的成分,并开展了针对不同切削参数下的切削实验,并对不同切削条件下的表面质量进行了检测。
综合以上实验和分析成果,通过对切削参数的优化,对切屑的流向和形式进行控制,从而抑制了粘接毛刺的产生,保证了产品表面质量。
关键词:高温合金高速车削毛刺工艺优化前言高温合金是指以铁、镍、钴为基,能在600℃以上的高温及一定应力作用下长期工作的一类金属材料;并具有较高的高温强度,良好的抗氧化和抗腐蚀性能,良好的疲劳性能、断裂韧性等综合性能。
高温合金为单一奥氏体组织,在各种温度下具有良好的组织稳定性和使用可靠性。
基于上述性能特点,且高温合金的合金化程度较高,又被称为“超合金”,是广泛应用于航空、航天、石油、化工、舰船的一种重要材料。
按基体元素来分,高温合金又分为铁基、镍基、钴基等高温合金。
铁基高温合金使用温度一般只能达到750~780℃,对于在更高温度下使用的耐热部件,则采用镍基和难熔金属为基的合金。
镍基高温合金在整个高温合金领域占有特殊重要的地位,它广泛地用来制造航空喷气发动机、各种工业燃气轮机最热端部件。
若以150MPA-100H持久强度为标准,而目前镍合金所能承受的最高温度〉1100℃,而镍合金约为950℃,铁基的合金〈850℃,即镍基合金相应地高出150℃至250℃左右。
所以人们称镍合金为发动机的心脏。
目前,在先进的发动机上,镍合金已占总重量的一半,不仅涡轮叶片及燃烧室,而且涡轮盘,甚至后几级压气机叶片也开始使用镍合金。
浅谈数控车床加工工艺优化
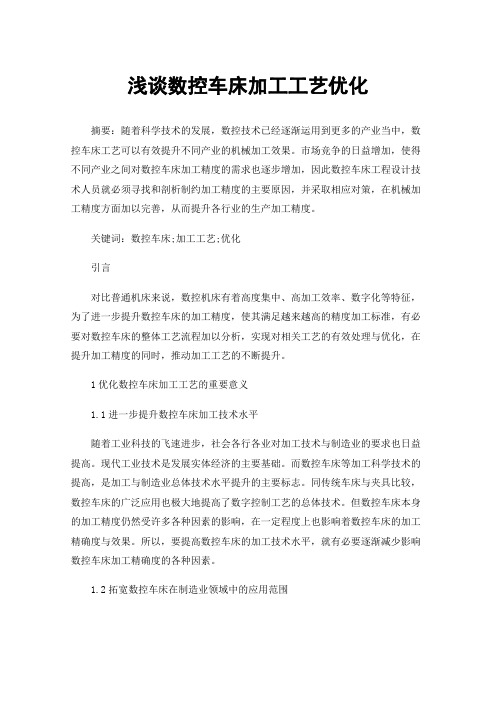
浅谈数控车床加工工艺优化摘要:随着科学技术的发展,数控技术已经逐渐运用到更多的产业当中,数控车床工艺可以有效提升不同产业的机械加工效果。
市场竞争的日益增加,使得不同产业之间对数控车床加工精度的需求也逐步增加,因此数控车床工程设计技术人员就必须寻找和剖析制约加工精度的主要原因,并采取相应对策,在机械加工精度方面加以完善,从而提升各行业的生产加工精度。
关键词:数控车床;加工工艺;优化引言对比普通机床来说,数控机床有着高度集中、高加工效率、数字化等特征,为了进一步提升数控车床的加工精度,使其满足越来越高的精度加工标准,有必要对数控车床的整体工艺流程加以分析,实现对相关工艺的有效处理与优化,在提升加工精度的同时,推动加工工艺的不断提升。
1优化数控车床加工工艺的重要意义1.1进一步提升数控车床加工技术水平随着工业科技的飞速进步,社会各行各业对加工技术与制造业的要求也日益提高。
现代工业技术是发展实体经济的主要基础。
而数控车床等加工科学技术的提高,是加工与制造业总体技术水平提升的主要标志。
同传统车床与夹具比较,数控车床的广泛应用也极大地提高了数字控制工艺的总体技术。
但数控车床本身的加工精度仍然受许多各种因素的影响,在一定程度上也影响着数控车床的加工精确度与效果。
所以,要提高数控车床的加工技术水平,就有必要逐渐减少影响数控车床加工精确度的各种因素。
1.2拓宽数控车床在制造业领域中的应用范围数控车床因其加工精确、制造效能高等优势正在快速替代传统机械。
数控机械加工技术的蓬勃发展,导致了数控车床在机械加工制造领域的使用范围更加广阔,而影响数控车床机械加工产品质量的各种因素,也抑制了数控车床在机械加工制造领域的广泛应用,但一些精密加工领域仍对数控车床的机械加工精度有着更高的需求,对精密工件的加工技术尚有较大的上升空间。
所以,深入研究数控车床生产精度的影响因子和改善策略,对于扩大其在工业方面的使用有着重大价值。
2影响数控车床加工误差精度的因素就目前我国数控车床的研发与使用现状分析,数控车床的数控过程在多数情形下,都需要通过半闭环控制的伺服系统进给控制器完成各工艺步骤的控制。
数控车床加工精度的工艺处理及优化_1

数控车床加工精度的工艺处理及优化发布时间:2022-07-18T07:19:10.126Z 来源:《城镇建设》2022年第5期(上)作者:齐红玲[导读] 数控车床加工过程中使用了计算机技术、高端机械技术、自动控制技术及自动检测技术等很多高新技术,齐红玲义煤集团宜阳义络煤业有限责任公司河南省洛阳市 471600摘要: 数控车床加工过程中使用了计算机技术、高端机械技术、自动控制技术及自动检测技术等很多高新技术,从某种程度上表明数控车具有非常高的自动化程度。
基于数控车迅速发展的今天,高新技术企业对数控技术专业人才的培养提高重视程度,并且注重数控加工技术与工艺流程的创新。
通过优化与创新数控车床加工方法,能够保证加工精准度,提升加工效率。
关键词:数控车床;加工;精度引言随着我国机械加工制造业的快速发展,对数控加工精度的要求也越来越高,这也给数控车床加工领域带来了新的挑战。
在数控车床加工过程中,对产品加工精度和质量的科学控制尤为重要。
1数控车床加工工艺的应用优势数控车床搭载控制程序,能够实现自动化生产,其主要原理是借助事先编辑的编码或符号指令完成不同零件的自动化加工,在实际生产过程中表现出以下特征:1)有着较高的加工精度,并且能够保证稳定的加工质量输出。
2)可以实现多级坐标的联动,对一些相对较为复杂的零件也可以轻松完成加工。
3)当加工零件内部结构发生变动时,只需要改变数控程序就可以完成整个调整过程,并且数控机床允许自由调整加工量,其整体的生产效率要高于普通车床。
数控机床的一大优势在于其具有自动化生产技术,完全可以替代人力,使整体的生产成本大幅度下降。
4)数控机床对操作人员的专业素质有着较高的要求,尤其是维修工作,对相关人员的技术水平也有着较高的要求。
通过分析数控机床的特征并与传统加工工艺进行对比,前者所表现出的优势,无论是加工质量或是精度方面都更加突出,有着更高的生产效率。
无论是在生产基准或误差控制方面,数控车床表现更优,能够确保加工零件的质量达到标准要求。
数控机床的加工工艺优化和改进方法
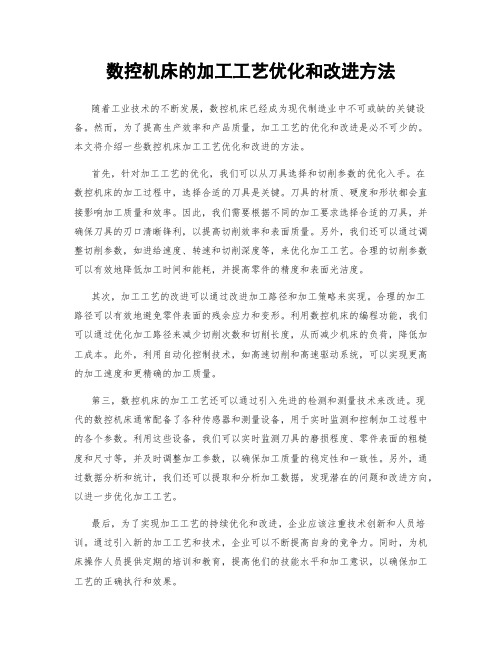
数控机床的加工工艺优化和改进方法随着工业技术的不断发展,数控机床已经成为现代制造业中不可或缺的关键设备。
然而,为了提高生产效率和产品质量,加工工艺的优化和改进是必不可少的。
本文将介绍一些数控机床加工工艺优化和改进的方法。
首先,针对加工工艺的优化,我们可以从刀具选择和切削参数的优化入手。
在数控机床的加工过程中,选择合适的刀具是关键。
刀具的材质、硬度和形状都会直接影响加工质量和效率。
因此,我们需要根据不同的加工要求选择合适的刀具,并确保刀具的刃口清晰锋利,以提高切削效率和表面质量。
另外,我们还可以通过调整切削参数,如进给速度、转速和切削深度等,来优化加工工艺。
合理的切削参数可以有效地降低加工时间和能耗,并提高零件的精度和表面光洁度。
其次,加工工艺的改进可以通过改进加工路径和加工策略来实现。
合理的加工路径可以有效地避免零件表面的残余应力和变形。
利用数控机床的编程功能,我们可以通过优化加工路径来减少切削次数和切削长度,从而减少机床的负荷,降低加工成本。
此外,利用自动化控制技术,如高速切削和高速驱动系统,可以实现更高的加工速度和更精确的加工质量。
第三,数控机床的加工工艺还可以通过引入先进的检测和测量技术来改进。
现代的数控机床通常配备了各种传感器和测量设备,用于实时监测和控制加工过程中的各个参数。
利用这些设备,我们可以实时监测刀具的磨损程度、零件表面的粗糙度和尺寸等,并及时调整加工参数,以确保加工质量的稳定性和一致性。
另外,通过数据分析和统计,我们还可以提取和分析加工数据,发现潜在的问题和改进方向,以进一步优化加工工艺。
最后,为了实现加工工艺的持续优化和改进,企业应该注重技术创新和人员培训。
通过引入新的加工工艺和技术,企业可以不断提高自身的竞争力。
同时,为机床操作人员提供定期的培训和教育,提高他们的技能水平和加工意识,以确保加工工艺的正确执行和效果。
综上所述,数控机床的加工工艺优化和改进是提高生产效率和产品质量的关键。
CNC机床加工中的加工工艺参数优化方法

CNC机床加工中的加工工艺参数优化方法在CNC机床加工过程中,合理的加工工艺参数选择对于提高加工质量、提高生产效率和降低生产成本至关重要。
本文将探讨CNC机床加工中的加工工艺参数优化方法,以帮助企业在实际生产中取得更好的效果。
一、加工工艺参数的选择与优化1. 选择合适的切削速度切削速度是指切削工具在加工过程中与被加工材料之间的相对速度。
切削速度的选择需要考虑材料的切削性能、被加工材料的硬度等因素。
一般而言,材料越硬,切削速度就应该越低,以保证刀具寿命和加工表面质量。
2. 确定合适的进给速度进给速度是指工件相对于刀具在加工过程中的移动速度。
进给速度的选择需要考虑材料的切削性能、加工表面质量要求和生产效率等因素。
通常情况下,软材料可选用较高的进给速度以提高生产效率,而硬材料则应适当减小进给速度以确保加工质量。
3. 控制合适的切削深度切削深度是指刀具在一次切削中所进入被加工材料的深度。
切削深度的选择需要考虑材料的切削性能、刀具的刚性和加工表面质量要求等因素。
合适的切削深度可以提高生产效率,但过大的切削深度可能导致加工质量下降和刀具寿命缩短。
4. 优化刀具半径和刀具类型刀具半径和刀具类型的选择直接影响到切削力、表面质量和加工效率等方面。
选择合适的刀具半径可以减小切削力,提高加工表面质量;而合适的刀具类型可以提高切削效率和切削稳定性。
5. 合理选择冷却液和润滑剂冷却液和润滑剂在CNC机床加工过程中起到冷却切削区域、减少切削热和摩擦等作用。
选择合适的冷却液和润滑剂可以有效降低切削温度、减少切削力和延长刀具寿命。
二、加工工艺参数优化方法1. 实施试切试验试切试验是寻找合适加工工艺参数的一种有效方法。
通过在实际生产中进行试切试验,可以根据不同的工件材料和加工要求,确定最佳的切削速度、进给速度和切削深度等参数。
2. 运用数学模型和优化算法运用数学模型和优化算法是一种较为常用的加工工艺参数优化方法。
通过建立数学模型,将加工目标函数与加工参数联系起来,再利用优化算法求解最佳的加工工艺参数组合。
数控机床加工过程中的优化技巧分享
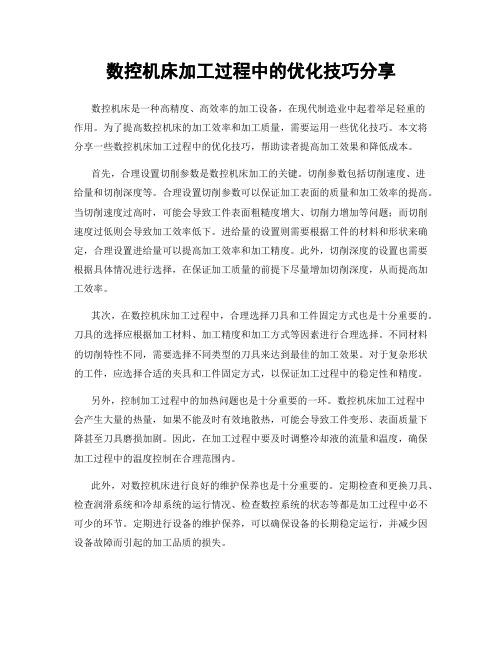
数控机床加工过程中的优化技巧分享数控机床是一种高精度、高效率的加工设备,在现代制造业中起着举足轻重的作用。
为了提高数控机床的加工效率和加工质量,需要运用一些优化技巧。
本文将分享一些数控机床加工过程中的优化技巧,帮助读者提高加工效果和降低成本。
首先,合理设置切削参数是数控机床加工的关键。
切削参数包括切削速度、进给量和切削深度等。
合理设置切削参数可以保证加工表面的质量和加工效率的提高。
当切削速度过高时,可能会导致工件表面粗糙度增大、切削力增加等问题;而切削速度过低则会导致加工效率低下。
进给量的设置则需要根据工件的材料和形状来确定,合理设置进给量可以提高加工效率和加工精度。
此外,切削深度的设置也需要根据具体情况进行选择,在保证加工质量的前提下尽量增加切削深度,从而提高加工效率。
其次,在数控机床加工过程中,合理选择刀具和工件固定方式也是十分重要的。
刀具的选择应根据加工材料、加工精度和加工方式等因素进行合理选择。
不同材料的切削特性不同,需要选择不同类型的刀具来达到最佳的加工效果。
对于复杂形状的工件,应选择合适的夹具和工件固定方式,以保证加工过程中的稳定性和精度。
另外,控制加工过程中的加热问题也是十分重要的一环。
数控机床加工过程中会产生大量的热量,如果不能及时有效地散热,可能会导致工件变形、表面质量下降甚至刀具磨损加剧。
因此,在加工过程中要及时调整冷却液的流量和温度,确保加工过程中的温度控制在合理范围内。
此外,对数控机床进行良好的维护保养也是十分重要的。
定期检查和更换刀具、检查润滑系统和冷却系统的运行情况、检查数控系统的状态等都是加工过程中必不可少的环节。
定期进行设备的维护保养,可以确保设备的长期稳定运行,并减少因设备故障而引起的加工品质的损失。
最后,合理选择数控编程和使用优化的加工路径也是提高加工效率和加工质量的关键。
数控编程要求程序简洁、清晰,同时要考虑到加工的具体情况和加工路径的优化。
合理的加工路径可以减少空行程,缩短加工时间,提高加工效率。
- 1、下载文档前请自行甄别文档内容的完整性,平台不提供额外的编辑、内容补充、找答案等附加服务。
- 2、"仅部分预览"的文档,不可在线预览部分如存在完整性等问题,可反馈申请退款(可完整预览的文档不适用该条件!)。
- 3、如文档侵犯您的权益,请联系客服反馈,我们会尽快为您处理(人工客服工作时间:9:00-18:30)。
[1-4]
(1)传感器 传感器是进行在线监测的基础。传感器直接获取被测 物体的运动参数,包括位移、速度、加速度。通过转化器, 可将它们转换成便于传送的物理量。为便于传输方便,一 般转换为电信号。 (2)信号处理单元 信号处理单元是在线监测的桥梁。由于信号传输过程 中会有损耗和失真,需要用信号处理单元对传感器采集来 的信号进行放大、整形、A / D 转换等操作,使得信号在传 输过程中不失真。 (3)计算机 计算机是在线监测的核心。传输来的信号通过计算机 进行运算、处理,完成最后结果的显示和打印功能。 图 2 是在线监测系统传感器贴片示意图。
1 纯镍材料的性能 金属加工技术是数控车削加工工艺的重要内容。在确 定加工方案前,要充分了解金属的性能,结合金属的特性 制定可行的加工工艺方案。 纯镍是一种耐腐蚀性强、 机械强度大、 塑性良好的金属, 用于机械制造等多个方面。其中,工业上应用最广泛的是 耐碱性、耐腐蚀性、机械性能好的 N6 材料。纯镍 N6 的机 械性能,如表 1 所示。
表 1 纯镍 N6 的机械性能
性能 抗拉强度 σb/(kg/mm) 伸长率 δ/% 布氏硬度 HB/(kg/mm) 冲击韧性 αk/(kg·m/cm) 数值 50 ~ 90 2 ~ 20 120 ~ 240 31
大回转半径等,都是挑选机床时需要考虑的因素。 2.2 车削刀具的选择及切削用量 刀具是对工件切削的重要工具。选择刀具时,要综合 考虑工件、刀具以及机床三方面的因素。只有这三个方面 相互适应、相互协调,才能实现对工件的加工。对于刀具 的挑选,要重点考虑以下两个因素。 刀具的材质和性能。刀具的性能直接影响加工精度, 而刀具的材质制约着刀具的性能。一般情况下,刀具的材 质越好,性能也相对越好。选择刀具时,不但要考虑刀具 的强度、导热性、硬度等物理特性,还要考虑经济适用性, 做到刀具的材质、性能以及经济适用性三者平衡。 刀具的形状和尺寸。刀具的外形需要根据要加工的工 件进行具体选择,最优的选择是能满足更多的工件完成加 工工作。同时,在各种条件都允许的情况下,可以适当选 择直径较大的刀具, 这有利于提高切削效率, 延长使用寿命。 切削用量控制着各个工序的运行,每道工序的参数指 标都和切削用量息息相关。编程过程中,要重点考虑切削 用量。切削用量会对切削深度、进给速度、切削速度产生 影响,因此合理确定的切削用量可以加快工作效率,保证 加工工艺快速高效完成。 3 纯镍的数控车削加工工艺优化 3.1 纯镍的数控车削加工工艺存在的问题 经多次试验验证,在对纯镍材料进行加工的过程中, 存在刀具磨损严重、使用寿命短、生产效率低下的问题。 切削过程中,纯镍材料与刀具的摩擦会产生强烈的震动和 高噪声(经检测已超过 100dB)。由于刀具的磨损非常严重, 在切削一个工件时就要更换十余次刀具。频繁更换刀片造 成工件的表面光度不够,只能在加工后期使用锉刀纱布对 工件继续打光磨平,浪费了大量人力物力。此外,每次更 换刀具都要经历编程、对刀、关闭启动计算机等工序,容 易造成计算机故障。事实上,经此工艺加工的工件,不能 很好地保障质量,且生产效率低下。如果造成一件工件成 为废品,将会产生较大的经济损失。可见,这样进行批量 生产时,产品效率和质量均不能保证。因此,探寻优化纯 镍的车削加工工艺迫在眉睫。此外,选择采用耐磨性能较 好的刀具进行切削时,上述问题仍然存在。因此,还需要 寻找新的途径解决上述问题。 (下转第 131 页)
由表 1 可知,纯镍材料的机械强度大,加工性能较差, 被列为难加工的材料之一。在对纯镍材料进行车削时,刀 具会因纯镍的机械性能等原因产生较大的磨损。车削时, 切削热主要集中在刀刃附近,后刀面易出现沟槽,影响纯 镍材料的车削加工。因此,深入探讨解决上述问题的方法, 对优化纯镍材料的数控车削加工工艺十分重要。 2 数控车削加工工艺简介 数控车削加工的主要目的是对工件进行精密加工,主 要方法是通过操纵控制系统控制数控机床刀具的轨迹,以 完成工件的车削过程。进行加工前,确定刀具和工件处于 同一个坐标系中是极为关键的一点。随着技术的不断发展, 编程语言的规范化、控制系统的智能化使得数控机床的加 工工艺逐渐标准化、成熟化。数控车削加工工艺主要包括八 个过程:加工工艺分析;程序的编程;加工过程中的装刀; 装刀组;加工前的对刀;粗加工工艺;半精加工工艺;精加 工。这八个主要的加工过程能够保证加工过程的顺利进行。 同时,加工技术和加工方法的协调合作,才能实现对工件 的精密加工。下面简单介绍数控车削的主要加工工艺。 2.1 加工机床的选择 选择加工机床时,要考虑工件的因素和数控机床参数 等因素。因为数控机床都有一定的使用范围,因而在选择 时要做出相应判断。选择机床时,要根据工件的尺寸、形 状、结构、加工要求等进行挑选。同时,机床自身的性能、 参数等也会对工件的加工产生一定限制,如主轴转速、最
工 艺 与 装 备
129
在线诊断系统在 CSP 减速机上的应用
邱碧涛 1,2 董 江 3 刘德军 3 张堂正 2
(1. 冶金装备及其控制教育部重点实验室(武汉科技大学),武汉 430081;2. 武钢研究院,武汉 430080; 3. 武汉钢铁公司条材总厂 CSP 分厂,武汉 430080)
摘 要:CSP 产线由于品种规格跨度大,对设备的状态提出了更高要求。为了提高设备的投入率,降低设备 运行故障, 有必要对设备的运行状态进行监控, 并对发生的故障进行预测。 通过监测 CSP 精轧机组减速箱运动状态, 发现减速箱啮合齿轮出现周向破损缺陷,并对设备的运行负荷进行调整,降低了减速箱的负荷。在设备年修时, 拆开故障减速箱外壳发现,减速箱啮合齿轮确实发生了明显的周向疲劳剥落缺陷。 关键词:CSP 故障诊断 减速箱
128
现代制造技术与装备
201数控车削加工工艺优化
唐永亮
(中国电子科技集团公司第十二研究所,北京 100016)
摘 要:本文将结合纯镍材料的性能,探究纯镍的车削加工工艺优化技术,进而推动数控车削加工工艺的创 新和发展。 关键词:机械加工 纯镍 数控车削 加工工艺