概括分析和故障诊断方法的过程监控
工业监控系统的故障诊断

工业监控系统的故障诊断工业监控系统在现代工业生产中起着至关重要的作用。
它能够实时监测并控制生产过程中的各种参数和变量,从而确保生产的稳定性和高效性。
然而,由于各种原因,监控系统也会出现故障,这可能会导致生产中断,造成经济损失。
因此,故障诊断成为了工业监控系统运维中的一个关键环节。
一、故障诊断的重要性工业监控系统的故障可能源自硬件问题或软件问题。
硬件问题包括传感器故障、设备损坏等,而软件问题可能涉及编程错误、通信故障等。
无论是硬件问题还是软件问题,及时准确地诊断故障并采取相应措施,对于确保工业生产的顺利进行至关重要。
故障诊断能够帮助工程师定位故障源,并提供解决方案,从而最大程度地减少生产中断,降低维修成本。
二、故障诊断的方法1. 人工诊断人工诊断是最直观、最普遍的方法之一。
通过经验丰富的工程师对监控系统进行检查和排查,以确定故障根源和解决方案。
然而,人工诊断存在一定的局限性,依赖于工程师的经验和知识水平,不能保证诊断的准确性和速度。
2. 数据分析工业监控系统通常会记录大量的数据,包括传感器数据、生产参数、报警记录等。
通过对这些数据进行分析,可以发现异常,并进一步定位故障源。
数据分析可以利用统计学方法、机器学习算法等进行,能够提高诊断的准确性和效率。
3. 模型建立与仿真建立工业监控系统的模型,并进行仿真测试,可以帮助诊断故障。
通过对模型进行异常检测和故障注入,可以模拟各种故障情景,并分析监控系统的响应。
这种方法能够帮助工程师更好地理解系统运行过程,快速定位故障。
三、故障诊断的挑战工业监控系统的故障诊断面临着一些挑战。
首先,监控系统的复杂性不断增加,其中涉及的组件和参数非常多,使得故障诊断变得更加困难。
其次,故障模式多样化,涉及到硬件和软件的多个方面,需要综合考虑。
此外,故障诊断需要在生产运行过程中实时进行,时间和效率要求很高。
四、故障诊断的未来发展方向未来,随着人工智能和物联网技术的不断提升,故障诊断将有更大的发展空间。
工业过程监控中的异常检测与故障诊断研究
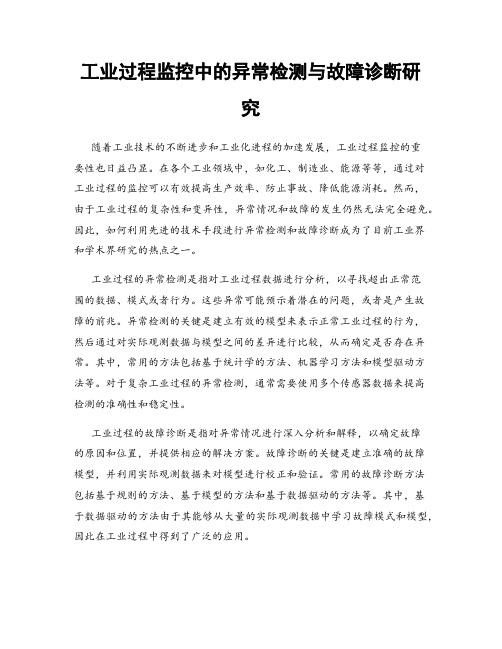
工业过程监控中的异常检测与故障诊断研究随着工业技术的不断进步和工业化进程的加速发展,工业过程监控的重要性也日益凸显。
在各个工业领域中,如化工、制造业、能源等等,通过对工业过程的监控可以有效提高生产效率、防止事故、降低能源消耗。
然而,由于工业过程的复杂性和变异性,异常情况和故障的发生仍然无法完全避免。
因此,如何利用先进的技术手段进行异常检测和故障诊断成为了目前工业界和学术界研究的热点之一。
工业过程的异常检测是指对工业过程数据进行分析,以寻找超出正常范围的数据、模式或者行为。
这些异常可能预示着潜在的问题,或者是产生故障的前兆。
异常检测的关键是建立有效的模型来表示正常工业过程的行为,然后通过对实际观测数据与模型之间的差异进行比较,从而确定是否存在异常。
其中,常用的方法包括基于统计学的方法、机器学习方法和模型驱动方法等。
对于复杂工业过程的异常检测,通常需要使用多个传感器数据来提高检测的准确性和稳定性。
工业过程的故障诊断是指对异常情况进行深入分析和解释,以确定故障的原因和位置,并提供相应的解决方案。
故障诊断的关键是建立准确的故障模型,并利用实际观测数据来对模型进行校正和验证。
常用的故障诊断方法包括基于规则的方法、基于模型的方法和基于数据驱动的方法等。
其中,基于数据驱动的方法由于其能够从大量的实际观测数据中学习故障模式和模型,因此在工业过程中得到了广泛的应用。
为了实现工业过程监控中的异常检测和故障诊断,一般需要经历以下几个主要步骤。
首先,收集和预处理工业过程的实时数据,包括传感器数据、控制信号和操作日志等,并进行数据清洗和去噪处理,以保证数据的可靠性和准确性。
然后,根据工业过程的具体特点和需求,选择合适的异常检测和故障诊断方法,并进行模型训练和参数调优等工作。
之后,对实时数据进行实时监测和分析,并根据预设的阈值或规则进行异常报警和故障诊断。
最后,根据监控结果和故障诊断的分析,及时采取相应的措施进行异常处理和故障修复。
工业生产线的自动化监控与故障诊断

工业生产线的自动化监控与故障诊断工业生产线的自动化监控与故障诊断在现代工业生产中扮演着至关重要的角色。
它不仅可以提高生产效率和产品质量,还可以降低成本和人力资源的需求。
本文将介绍工业生产线自动化监控的基本原理和常用技术,以及故障诊断的方法和应用。
一、工业生产线自动化监控1.1 监控系统架构工业生产线自动化监控系统一般由传感器、监控设备、控制器和人机界面组成。
传感器负责检测生产线上各种参数,如温度、压力、速度等。
监控设备将传感器采集到的数据传输给控制器,控制器根据设定的参数进行控制,并将监控数据显示在人机界面上。
1.2 监控技术工业生产线的自动化监控可以使用多种技术实现。
其中,最常见的是远程监控技术和无线监控技术。
远程监控技术利用网络将生产线上的监控数据传输到远程服务器上,可以通过互联网实现远程实时监控和数据分析。
这种技术可以帮助生产线实时发现问题,并进行及时的处理,提高生产效率和产品质量。
无线监控技术使用无线传感器网络将监控数据传输到控制系统。
这种技术可以减少布线成本,提高系统的灵活性,并且适用于不同规模和复杂度的生产线。
二、工业生产线故障诊断2.1 故障诊断方法工业生产线故障诊断是及时发现和解决生产线故障的关键步骤。
常见的故障诊断方法包括规则推理、神经网络和模糊逻辑等。
规则推理方法基于专家经验和规则库,通过逻辑推理分析监控数据,找出可能的故障原因。
这种方法适用于经验丰富的专家系统,并且具有良好的可解释性。
神经网络方法通过网络训练学习生产线的正常状态和故障模式,进而对监控数据进行分类和识别。
这种方法可以自动学习特征和模式,并具有较强的泛化能力。
模糊逻辑方法通过建立模糊推理规则和模糊集来处理不确定性和模糊性。
它可以更好地处理生产线故障的模糊性特征,并具有良好的可靠性和鲁棒性。
2.2 故障诊断应用工业生产线故障诊断广泛应用于各个领域,如汽车制造、电子设备、食品加工等。
通过实时监测和故障诊断可以及时发现和处理生产线的故障,保持生产线的正常运行。
故障诊断实施的步骤
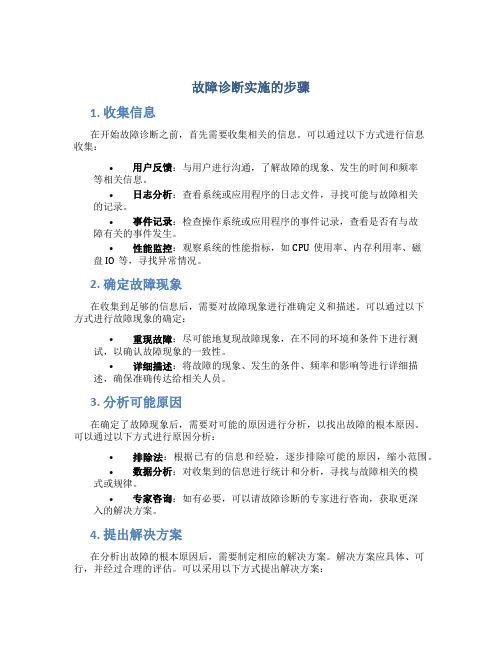
故障诊断实施的步骤1. 收集信息在开始故障诊断之前,首先需要收集相关的信息。
可以通过以下方式进行信息收集:•用户反馈:与用户进行沟通,了解故障的现象、发生的时间和频率等相关信息。
•日志分析:查看系统或应用程序的日志文件,寻找可能与故障相关的记录。
•事件记录:检查操作系统或应用程序的事件记录,查看是否有与故障有关的事件发生。
•性能监控:观察系统的性能指标,如CPU使用率、内存利用率、磁盘IO等,寻找异常情况。
2. 确定故障现象在收集到足够的信息后,需要对故障现象进行准确定义和描述。
可以通过以下方式进行故障现象的确定:•重现故障:尽可能地复现故障现象,在不同的环境和条件下进行测试,以确认故障现象的一致性。
•详细描述:将故障的现象、发生的条件、频率和影响等进行详细描述,确保准确传达给相关人员。
3. 分析可能原因在确定了故障现象后,需要对可能的原因进行分析,以找出故障的根本原因。
可以通过以下方式进行原因分析:•排除法:根据已有的信息和经验,逐步排除可能的原因,缩小范围。
•数据分析:对收集到的信息进行统计和分析,寻找与故障相关的模式或规律。
•专家咨询:如有必要,可以请故障诊断的专家进行咨询,获取更深入的解决方案。
4. 提出解决方案在分析出故障的根本原因后,需要制定相应的解决方案。
解决方案应具体、可行,并经过合理的评估。
可以采用以下方式提出解决方案:•修复故障:根据故障的原因,制定相应的修复方案,并进行实施。
•升级或更新:如故障是由软件或系统版本不兼容引起的,可以考虑升级或更新相应的软件或系统。
•改变配置:根据故障的情况,调整系统或应用程序的配置参数,达到修复故障的目的。
5. 实施解决方案在确定了解决方案后,需要进行实施。
实施解决方案时应注意以下几点:•备份数据:在实施解决方案之前,应对系统或数据进行备份,以防止意外情况发生。
•验证解决方案:在实施解决方案之后,需要验证是否成功解决了故障。
可以通过测试、监控等方式进行验证。
风电场监控系统的设备故障诊断与维修流程
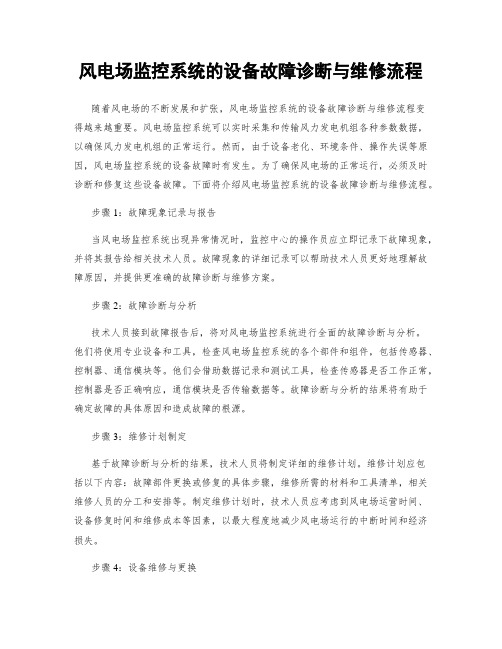
风电场监控系统的设备故障诊断与维修流程随着风电场的不断发展和扩张,风电场监控系统的设备故障诊断与维修流程变得越来越重要。
风电场监控系统可以实时采集和传输风力发电机组各种参数数据,以确保风力发电机组的正常运行。
然而,由于设备老化、环境条件、操作失误等原因,风电场监控系统的设备故障时有发生。
为了确保风电场的正常运行,必须及时诊断和修复这些设备故障。
下面将介绍风电场监控系统的设备故障诊断与维修流程。
步骤1:故障现象记录与报告当风电场监控系统出现异常情况时,监控中心的操作员应立即记录下故障现象,并将其报告给相关技术人员。
故障现象的详细记录可以帮助技术人员更好地理解故障原因,并提供更准确的故障诊断与维修方案。
步骤2:故障诊断与分析技术人员接到故障报告后,将对风电场监控系统进行全面的故障诊断与分析。
他们将使用专业设备和工具,检查风电场监控系统的各个部件和组件,包括传感器、控制器、通信模块等。
他们会借助数据记录和测试工具,检查传感器是否工作正常,控制器是否正确响应,通信模块是否传输数据等。
故障诊断与分析的结果将有助于确定故障的具体原因和造成故障的根源。
步骤3:维修计划制定基于故障诊断与分析的结果,技术人员将制定详细的维修计划。
维修计划应包括以下内容:故障部件更换或修复的具体步骤,维修所需的材料和工具清单,相关维修人员的分工和安排等。
制定维修计划时,技术人员应考虑到风电场运营时间、设备修复时间和维修成本等因素,以最大程度地减少风电场运行的中断时间和经济损失。
步骤4:设备维修与更换一旦维修计划制定完毕,技术人员将开始进行设备的维修与更换。
维修过程中,技术人员应严格按照维修计划进行操作,并遵循相关的安全操作规程。
若需要更换故障部件,他们应使用与原部件相同规格和型号的新部件,并确保其与其他部件兼容。
维修过程中,技术人员应记录每一个细节,以便于日后的维护和追踪。
步骤5:设备测试与验证设备维修与更换完成后,技术人员将对设备进行测试与验证,以确保其功能正常,与其他设备的协同工作正常。
故障诊断实施过程的步骤有

故障诊断实施过程的步骤有1. 收集信息•了解故障现象:仔细倾听用户的描述,了解故障的发生时间、频率、影响范围等详细信息。
•检查设备:观察设备的外观是否有物理损坏,检查连接线是否松动,逐一检查各个部件的工作状态。
•寻求背景信息:了解设备的使用历史、维护记录,分析是否有相关操作或事件与故障现象相关。
2. 确定故障范围•缩小故障范围:通过排除法逐步缩小故障范围,确定故障是否只发生在特定子系统或特定设备上。
•检查系统状态:利用系统监控工具、日志记录等方式检查系统各个组件的运行状态,查找异常迹象。
•进行初步排查:根据收集的信息,初步判断可能存在的故障类型,并在相应的范围内进行详细排查。
3. 分析故障原因•使用故障诊断工具:根据故障现象和已有经验,选择合适的故障诊断工具进行测试和分析,如网络分析工具、故障检测设备等。
•查找故障迹象:根据故障现象和收集的信息,查找并分析与故障相关的迹象,如错误日志、异常报告等。
•分析系统配置:检查系统的配置参数,排查是否存在配置错误或冲突导致的故障。
4. 提出解决方案•基于分析结果:根据故障原因的分析结果,提出解决方案并列出可行的修复措施。
•涉及风险评估:评估修复措施可能带来的风险,包括对系统的影响、操作的复杂性、成本等。
•制定优先级:根据故障的影响程度和解决方案的可行性,确定解决方案的优先级,合理分配资源。
5. 执行解决方案•实施修复措施:按照确定的解决方案进行实施,包括改变系统配置、替换故障部件、调整设备设置等操作。
•监控变化:在实施过程中,随时监控变化情况,确保修复措施的有效性,并及时采取调整措施。
•验证修复效果:对修复后的系统进行功能测试、性能测试或其他适当的验证,确保故障已经得到完全解决。
6. 记录和总结•故障记录:详细记录故障发生的时间、现象、原因和解决方案,方便日后参考和类似故障的诊断。
•总结经验:从故障实施过程中总结经验教训,包括故障处理的技巧、常见故障的特点、故障预防措施等。
故障诊断概述分析
故障诊断概述分析故障诊断是指通过分析问题的根本原因和解决方法,来找到和解决设备或系统故障的过程。
它是维修和维护工作中的一个重要环节,能够提高设备的稳定性和可靠性,减少生产停机时间,提高产品质量。
故障诊断的过程通常包括以下几个步骤:故障现象描述、故障复现、故障分类、故障分析、解决方案制定和故障修复。
首先,故障诊断开始于用户的故障现象描述。
用户会提供一些关于故障现象的基本信息,如发生时间、发生频率、影响范围等。
这些信息对故障的定位和分析非常重要。
其次,故障复现是非常关键的一步。
只有在准确复现故障的情况下,才能进行有效的故障分析和解决方案制定。
通常,工程师会按照用户提供的信息和自己的经验,尝试在实验室环境中复现故障。
然后,故障分类是故障诊断的一个重要步骤。
故障可以分为硬件故障和软件故障。
硬件故障通常涉及设备的物理部分,如电路板、传感器等,而软件故障通常涉及设备的编程和配置,如程序错误、配置问题等。
通过分类故障,可以进一步缩小故障范围,快速定位问题。
接下来,故障分析是确定故障根本原因的一项重要任务。
工程师会通过分析收集到的数据、设备文档和相关信息,来找到故障的起因。
故障分析通常是一个逐步深入的过程,需要对设备的各个方面进行仔细研究和分析。
在故障分析的基础上,制定解决方案是下一步。
解决方案可能包括更换损坏的硬件组件、修复软件错误、重新配置设备等。
制定解决方案时,工程师需要考虑到多种因素,如故障修复的可行性、成本、时间和维修的效果等。
最后,故障修复是故障诊断的最终目标。
当工程师确定了解决方案后,会进行相应的维修和修复工作。
在此过程中,需要对设备进行验证和测试,确保故障得到了彻底的修复。
总结起来,故障诊断是一个复杂而系统的过程,需要工程师具备丰富的知识和经验。
通过故障诊断,可以准确地找到故障的根本原因,并采取适当的措施来解决问题。
这对于提高设备性能和可靠性,降低维修成本和生产停机时间都具有重要意义。
因此,故障诊断是维修和维护工作中不可或缺的一环。
工业过程质量监控与故障诊断方法研究
工业过程质量监控与故障诊断方法研究工业过程的质量监控与故障诊断是现代制造业中一个重要的研究领域。
随着工业技术的不断发展和提升,对工业过程质量的要求变得越来越高,而且由于生产环境的复杂性,工业过程中故障的发生也不可避免。
因此,如何实时监控工业过程的质量,并及时诊断与处理发生的故障成为了一个具有挑战性的问题。
一、质量监控方法1. 数据采集与处理:工业过程质量监控的第一步是收集相关的数据。
常用的数据采集方法包括传感器、摄像头等。
采集到的数据经过预处理和滤波等处理方法,提取出有用的信息进行后续分析。
2. 统计方法:统计方法是工业过程质量监控中常用的一种方法。
通过统计学原理,对采集到的数据进行分析并建立数学模型,从而判断工业过程是否处于正常运行状态。
常用的统计方法包括均值检验、方差分析等。
3. 机器学习方法:随着机器学习技术的迅猛发展,越来越多的研究者开始将机器学习方法应用于工业过程质量监控中。
机器学习方法通过训练样本来建立模型,实现对工业过程进行监控和预测。
常用的机器学习方法包括支持向量机、神经网络等。
4. 基于模型的方法:基于模型的方法是一种较为传统且常用的方法。
通过建立数学模型来描述工业过程的运行规律,进而进行监控和诊断。
常见的基于模型的方法包括状态观测器、卡尔曼滤波器等。
二、故障诊断方法1. 统计分析方法:统计分析方法是一种常用的故障诊断方法。
通过对工业过程数据进行统计分析,检测异常数据,并对异常数据进行诊断分析,找出故障的原因。
常用的统计分析方法包括偏差分析、相关性分析等。
2. 人工智能方法:人工智能方法是近年来在故障诊断领域中得到广泛应用的一种方法。
通过机器学习、模式识别等人工智能技术,对工业过程数据进行分析与处理,识别可能存在的故障,并提供相应的诊断方案。
常见的人工智能方法包括基于规则的专家系统、基于案例推理的方法等。
3. 基于模型的方法:基于模型的方法在故障诊断领域也是一种常用的方法。
通过建立数学模型来描述工业过程的运行特征,与实际数据进行比对,找出模型与实际数据的差异,从而判断是否存在故障。
故障诊断与分析的关键步骤
故障诊断与分析的关键步骤故障诊断与分析是一个系统性的过程,旨在找出问题的根本原因,并提供相应解决方案。
在进行故障诊断和分析时,需要遵循一系列关键步骤,以确保结果的准确性和完整性。
以下是故障诊断与分析的关键步骤。
1. 收集信息故障诊断与分析的第一步是收集故障发生时的相关信息。
这包括故障的描述、发生时间、发生地点和影响范围等。
此外,还需要收集现场数据、监测记录、日志文件和备份数据等相关信息,以便为分析提供充分的材料。
2. 分类和优先级排序在收集到足够的信息后,需要对故障进行分类和优先级排序。
这可以帮助确定哪些故障需要首先处理和解决。
常见的分类标准包括故障类型、故障影响范围和故障重要性等。
通过分类和优先级排序,可以提高故障处理的效率和效果。
3. 制定假设基于收集到的信息和故障的分类,可以制定一些初步的假设来解释故障的原因。
这些假设可以帮助确定进一步的分析方向和确定需要采取的措施。
制定假设时需要考虑到可能的原因和相关的潜在问题。
4. 数据分析在制定假设后,需要进行数据分析来验证或排除假设。
数据分析可以包括统计分析、图表绘制、对比和模式识别等。
通过分析数据,可以找出故障的共性和规律,并进一步缩小故障的范围和原因。
5. 实验验证数据分析之后,需要进行实验验证来确定故障的根本原因。
这涉及到将制定的假设转化为实际的实验或测试,并记录相关数据和结果。
实验验证可以通过采取不同的操作或调整不同的参数来观察故障是否得以解决,从而验证假设的准确性。
6. 故障定位一旦确定了故障的根本原因,需要进行故障定位以确定出故障的具体位置和范围。
故障定位可以通过使用仪器设备、检查相关设备或进行线路追踪等方法来实现。
故障定位有助于进一步确定需要采取的修复措施和工作范围。
7. 解决方案制定在完成故障定位后,需要制定具体的解决方案来修复故障。
解决方案应该包含具体的步骤、所需资源、注意事项和预期成果等。
解决方案的制定应该基于之前的数据分析和实验验证结果,并结合相关的技术知识和经验。
故障诊断流程分析DOC
故障诊断流程分析DOC故障诊断是指通过一系列系统化的步骤和方法,找出设备或系统出现故障的原因和解决办法的过程。
故障诊断流程是指进行故障诊断工作时的一系列操作步骤。
下面将介绍一个常用的故障诊断流程分析。
1.收集信息:在进行故障诊断之前,首先需要收集相关的信息。
这包括故障现象的描述、发生故障的设备或系统的型号和配置、是否有过类似的故障、是否有过维护或更改等。
这些信息可以帮助诊断人员更好地了解故障的背景和上下文。
2.确定目标:在收集了足够的信息后,需要明确故障诊断的目标。
例如,是要找出故障的根本原因还是解决当前的故障现象。
确定目标可以让诊断人员更加专注和有针对性地进行故障诊断。
3.制定假设:根据收集到的信息和目标,诊断人员可以提出一些可能的故障原因的假设。
这些假设可以基于以往的经验、类似故障的分析或系统的特点。
制定假设可以帮助诊断人员进行思维的导向,提高故障诊断的效率。
4.实施测试:在制定了假设后,需要进行实际的测试来验证这些假设的正确性。
这可以包括检查设备或系统的各个部分、使用仪器仪表进行测量和监测、进行试验等。
通过测试可以获取更多的信息,进一步缩小故障的范围。
5.分析结果:在进行了一系列的测试后,诊断人员需要对结果进行分析。
这包括对测试数据进行解读、对比实际情况和设备或系统的正常工作情况、结合假设和经验进行推理等。
分析结果可以进一步排除错误的假设,找出故障的真正原因。
6.确定解决方案:根据对故障原因的分析,诊断人员可以确定解决故障的方案。
这可以包括修复设备或系统的具体部件、更换部件、调整配置参数等。
确定解决方案可以让诊断人员在解决故障时更加有针对性和高效率。
7.实施解决方案:最后,诊断人员需要实施确定的解决方案。
这可以包括进行修复、更换部件、调整配置参数等。
在实施解决方案的过程中,需要密切关注设备或系统的反应和效果,确保解决方案的有效性。
以上是一个基本的故障诊断流程分析。
在实际应用中,还可以根据具体的情况进行调整和拓展。
- 1、下载文档前请自行甄别文档内容的完整性,平台不提供额外的编辑、内容补充、找答案等附加服务。
- 2、"仅部分预览"的文档,不可在线预览部分如存在完整性等问题,可反馈申请退款(可完整预览的文档不适用该条件!)。
- 3、如文档侵犯您的权益,请联系客服反馈,我们会尽快为您处理(人工客服工作时间:9:00-18:30)。
概括分析和故障诊断方法的过程监控Carlos F. Alcala, S. Joe Qin∗化学工程、材料科学的Mork Family部门,电气工程的Ming Hsieh 部门,南加州大学,美国,洛杉矶,CA90089文章信息文章历史:2011年二月24日网上可用故障诊断摘要在过程监控,一些诊断方法已用于故障诊断。
这些方法从不同的背景和考虑演变而来。
在本文中,五个现有诊断方法被总结和分析。
结果表明,它们能被统一成三种一般方法,使得原有的诊断方法成为普遍问题的特殊情况。
同时,一种新形式的相对分配被提出。
一项诊断能力的分析表明,一些诊断方法不保证正确的诊断,即使是简单的传感器故障和大的量级。
对于故障的故障等级,蒙特卡罗模拟被应用与比较诊断方法的性能。
1、介绍过程监控是工业用的检测和诊断的反常行为的过程。
多元统计方法和基于模型方法用于过程的监控。
在统计方法是一种很常见的用于工业的方法是主成分分析(PCA)【11、18、19】。
利用主成分分析法(PCA)隔开测量空间分为主成分子空间(PCS)和残子空间(RS)。
故障检测利用故障检测指标。
当故障检测指标之一超出它的控制限度,故障就被发现。
断层被发现后,有必要对其诊断原因。
有几种方法进行故障诊断。
其中的一些方法检查一个故障检测指标变量的分配,利用的是这样一个观点:作分配的变量会有高值。
被提出的分析分配方法包括了彻底分解的分配(CDC)、部分分解的分配(PDC)、斜交的分配(DC)、基于重建的分配(RBC),和基于角度的方法(ABC)。
表1显示了诊断方法,提出他们的作者和他们被用于的评价指标。
由此可见,一些诊断方法并没有被提出用于所有的故障检测的指标。
此外, Dunia et al. [6]建议对于关系到RBC的故障诊断,用一种重建索引。
但是,尚不清楚,是否这些诊断方法是独立的,哪一种方法会优于某一特定的检测指标。
对故障诊断的必然要求是尽可能多地避免误诊。
虽然分配计划作为故障诊断方法被广泛地应用, 但直到最近才给出了诊断能力的不严谨分析[1,2]。
分配平面图主要在故障情况下计算变量分配,挑选出一番大分配变量作为故障的可能原因。
因为这个想法,一个定义明确的分配分析需要有以下可取的性能。
1、当没有缺点的存在时,所有可变分配应该有显著的相同的意思。
当故障存在时,这将建立一个水平基准用来比较分配;2、如果错误主要归功于一个变量,那个变量的分配应该是最大的。
本文的目的是揭示哪一个的故障诊断方法具有上述特性。
为了去做诊断方法的分析,他们被表达为一般形式,以便他们可以与任何故障检测指标[3]一起使用。
然后,结果表明该诊断方法可以统一为一般的诊断方法,对这些方法和控制极限提供了参考。
此外,一种新形式的相对分配被提出。
统一方法的诊断能力分析和他们的相对分配,并对其结果进行了不同诊断方法的对比。
蒙特卡罗模拟被应用于比较诊断方法的性能当单一传感器的适度等级的故障在一个系统中发生。
最后,给出了结论。
表1 诊断方法.2. 利用主成分分析法(PCA)对故障检测 2.1. PCA 模型在一个有n 个测量变量的项目中,一个PCA 模型可以在正常条件下,利用m 个测量建立而来。
测量被排列在一个数据矩阵如:[]Tm x x x X )(...)2()1(= (1)其中然后,这些资料依比例决定到零均值方差和单位效果,并且其误差协方差矩阵的计算如下:X X m S T 11-=(2) 协方差矩阵被本征分解来获得主要因素,模型的其余载荷是:[]P PS ~=[]T P P ~~00⎥⎦⎤⎢⎣⎡ΛΛ (3) 其中,并且分别是主要载荷和S 的本征值。
保留在这个模型的主成分的数量(PCs)是l 。
这些推测到主要因素和残余子空间, X与~X 计算如下:Cx x PP xT ==ˆ x C x P P x T ~~~~==其中C 和C ~是对PCS 和RS 的投影矩阵的预测。
2.2. 故障检测指标故障检测指标用于侦测的行为过程。
有几种解释的故障检测指标,其中,最流行的是讨论平方预测误差(SPE),它也被称为Q 统计,即霍特林的T²统计和两者指标的结合。
这里总结了这些故障检测指标。
更多的细节中给出了Qin[12]。
2.2.1. 平方预测误差(SPE) SPE 定义为:x C x x P P x SPE TTT~~~== (4)它的控制限制2δ是这样计算()SPE SPE h g 22αχδ=有着(1−α)×100%的可信度,12/θθ=SPE g ,221/θθ=SPE h ,∑+-=nl i i 121λθ和i λ是第i 个本征值由S . Jackson 和Mudholkar[7]为故障检测及衍生另一个控制限使用三阶矩近似提出的这个指标。
2.2.2. 霍特林的T²统计 T ²被定义为Dx x x P P x T T T T =Λ=-12 (5)其中T P P D 1-Λ=,控制限制为)(22l αχτ=可信度为 (1−α)×100%。
2.2.3. 组合指数ϕ由Yue 和 Qin [21]提出的组合指数,被定义为φϕT x =x (6)其中22~τδφDC+=(7)该指标的控制限为)(22ϕαϕχζh g =,其中 ϕg =21242411δθτδθτ++ (8) ϕh =42422121)1(δθτδθτ++ (9)并且它有(1−α)×100%的可信度。
2.2.4.综合索引2.2.5.因为故障检测指标是二次方形式,所以符号可以只考虑一个一般指数Index ,Index(x )简化为 Index(x )=M x T x其中M 是显示在表2为每个检测指标。
控制极限的Index (x) 可以使用结果框 [4]计算出。
)(2Index Index h g αχη= (11)其中Index g =}{}{2SM tr SM tr (12)并且Index h =22}{}]{[SM tr SM tr (13)表达式tr {A}是指矩阵A 的轨迹,控制线的可信度为(1−α)×100%。
表 2 M 的值3. 故障诊断方法 3.1. 完全分解的分配完全分解的分配将故障检测指数分解为变量分配的总和。
这是一种在工业上广泛使用的方法,当SPE 指数[9]一起应用的时候,他被称为分配平面图。
Wise et al.[17]为T²指数提出了CDC 。
一般来说,CDC 被定义为 Index(x)=∑∑=====ni Index i ni TiTCDC x MxMMx x 112)2/1(2)2/1()(ξ其中Index i CDC =x M M x T i i T )2/1()2/1(ξξ (14)在这里i ξ是单位矩阵的第i 列i ξ=[]T0100 (15)对于SPE ,M=C ~。
因为C ~是全幂等的,C C ~~)2/1(=。
因此x x C x C x M ~~~)2/1()2/1(=== (16)并且()22~~i T i SPE i x xCDC ==ξ(17) 对于2T 指数()()2212x P P CDC T T i T i -Λ=ξ (18)Wise et al. [17]定义2T i CDC ,通过重排()221_12x P P x P P x T TTTΛ=Λ=- (19)通过令φ=M ,ϕi CDC 被定义,这在以前还未被发表过。
3.2. 部分分解的分配顾名思义,部分分解的分配(PDC)部分分解一个故障检测指数作为变量分配的总和。
这是Nomikos[10] 为2T 指数首次提出。
对于2T 指数的PDC 被定义为()∑∑===⎪⎭⎫ ⎝⎛===ni T i i T n i T i i TTTx D x x D x Dlx x Dx x x T 112ξξξξ其中x D x PDC T i i T T i ξξ=2(20)先前的结果利用的关系I=∑=ni T i i 1ξξ。
通常情况下,D 被M 所代替x M x PDC T i i T Index i ξξ= (21)这里,应该注意到,即使M 和T i i ξξ是正数的半正定矩阵,T i i M ξξ也许不是半正定矩阵[16]。
这个事实的结果是PDC 有可能是一个负值。
Westerhuis et al.[16]为在有两个变量的系统的T²指标提出这个结果。
3.3. 对角线的分配Qin et al. [13] 通过维持这种指标的多元嵌2T 过程监控,提出了块诊断分配来定义块分配。
Cherry and Qin [5]把他和ϕ索引一起使用。
在极限情况下,每个块仅包括一个变量,变量对角分配(DC)可以被定义为类似的方式如下:22i ii T i i T i i T T ix d x D x DC===ξξξξ (22)它可以被看作是对该极限情况的对角线的分配降低第i 个单变量进行监测。
虽然这是不推荐用于故障检测,因为它忽略了变量相关性,它可以作为一种分配分析方法的故障进行诊断。
对一般指标,DC 的计算方法是x M x DC T i i T i i T Index i ξξξξ= (23)3.4. 基于重建的分配重建分配使用一定数量的重建故障检测指标变量方向沿的变量的分配的重建。
它由Alcala and Qin [1,2]提出,沿着变量方向i ξ的重建指数是Index(T i x )=()()()221221f x M x M i Ti ξ-= (24)其中,f 是被决定的重建的部分,通过最小化上述指标得出的最佳重建为f 给出了最优值。
()()Mx M f T iiT i ξξξ1-= (25)RBC 被定义为:()221f M RBC i Index i ξ=()Mx M M x T i i T i i T ξξξξ1-= (26)()iT iT i M Mx ξξξ2=(27) 3.5. 基于角度的分配Raich 和 Cinar [14],Yoon 和 MacGregor [20]用角度信息分析。
基于角度的分配的正式定义如下:对于一个故障样本X ,第i 个变量的基于角度的分配由X 和i ξ之间的角度在投射或旋转()21M 后测量而出。
放映的向量是()i i M ξξ21= ()x M x 21=变量i 的ABC 是x 和i ξ之间角度的余弦的平方,也就是2⎪⎪⎭⎫ ⎝⎛=x x ABC i T i Indexi ξξ=()Mx x M Mx T i T i T i ξξξ2 (28)=()x Index RBC Indexi (29)可以看出,ABC 与RBC 的不同在于独立变量的指标(X )。
因此,诊断结果是与ABC 和RBC 相同的。