【精品】管壳式换热器
管壳式换热器规格标准
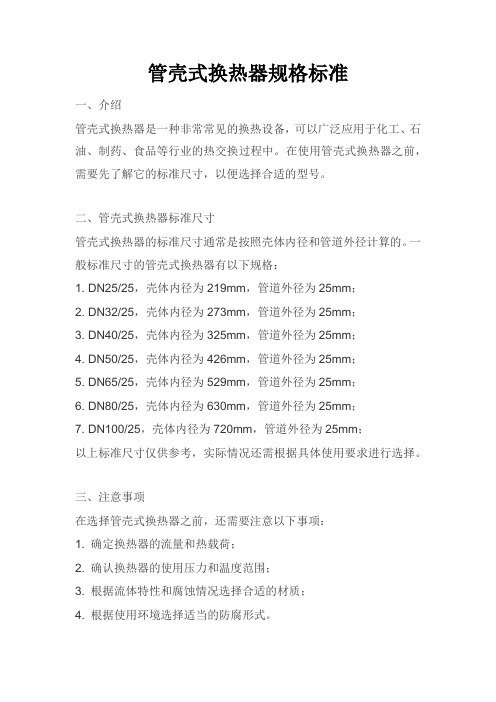
管壳式换热器规格标准一、介绍管壳式换热器是一种非常常见的换热设备,可以广泛应用于化工、石油、制药、食品等行业的热交换过程中。
在使用管壳式换热器之前,需要先了解它的标准尺寸,以便选择合适的型号。
二、管壳式换热器标准尺寸管壳式换热器的标准尺寸通常是按照壳体内径和管道外径计算的。
一般标准尺寸的管壳式换热器有以下规格:1. DN25/25,壳体内径为219mm,管道外径为25mm;2. DN32/25,壳体内径为273mm,管道外径为25mm;3. DN40/25,壳体内径为325mm,管道外径为25mm;4. DN50/25,壳体内径为426mm,管道外径为25mm;5. DN65/25,壳体内径为529mm,管道外径为25mm;6. DN80/25,壳体内径为630mm,管道外径为25mm;7. DN100/25,壳体内径为720mm,管道外径为25mm;以上标准尺寸仅供参考,实际情况还需根据具体使用要求进行选择。
三、注意事项在选择管壳式换热器之前,还需要注意以下事项:1. 确定换热器的流量和热载荷;2. 确认换热器的使用压力和温度范围;3. 根据流体特性和腐蚀情况选择合适的材质;4. 根据使用环境选择适当的防腐形式。
以上是关于管壳式换热器标准尺寸的介绍,希望能帮助您了解相关知识并选择合适的型号。
二、管壳式换热器国家标准规格1. 壳体尺寸壳体尺寸一般以壳体直径和长度表示。
国家标准中规定的壳体直径从50mm到5000mm不等,长度也有所不同,最长可达20m。
2. 管束数量管壳式换热器管束数量的多少直接决定了热交换的效率。
国家标准中规定管壳式换热器的管束数量应在1到12根之间,具体数量可根据使用条件及要求来进行选择。
3. 温度管壳式换热器的工作温度一般受制于材质、管束数量以及流体性质等多个因素。
国家标准中对于常用的曲率半径、沸点温度、加热量及换热系数等参数进行了规定。
4. 压力管壳式换热器的工作压力也是一个重要的参数。
管壳式换热器结构设计
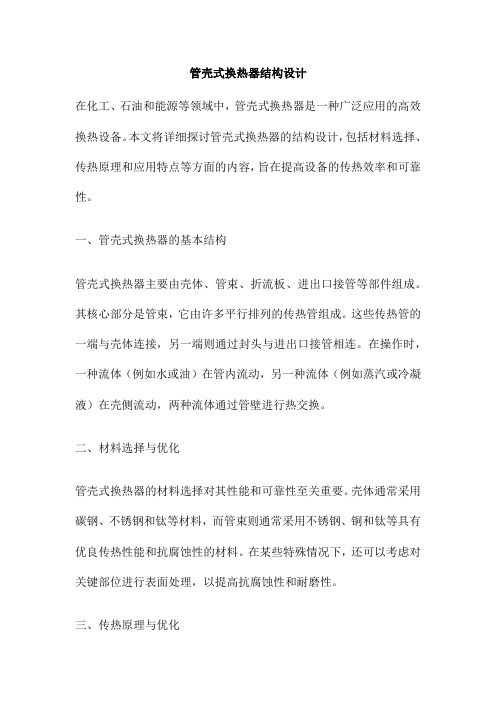
管壳式换热器结构设计在化工、石油和能源等领域中,管壳式换热器是一种广泛应用的高效换热设备。
本文将详细探讨管壳式换热器的结构设计,包括材料选择、传热原理和应用特点等方面的内容,旨在提高设备的传热效率和可靠性。
一、管壳式换热器的基本结构管壳式换热器主要由壳体、管束、折流板、进出口接管等部件组成。
其核心部分是管束,它由许多平行排列的传热管组成。
这些传热管的一端与壳体连接,另一端则通过封头与进出口接管相连。
在操作时,一种流体(例如水或油)在管内流动,另一种流体(例如蒸汽或冷凝液)在壳侧流动,两种流体通过管壁进行热交换。
二、材料选择与优化管壳式换热器的材料选择对其性能和可靠性至关重要。
壳体通常采用碳钢、不锈钢和钛等材料,而管束则通常采用不锈钢、铜和钛等具有优良传热性能和抗腐蚀性的材料。
在某些特殊情况下,还可以考虑对关键部位进行表面处理,以提高抗腐蚀性和耐磨性。
三、传热原理与优化管壳式换热器的传热原理主要是通过对流传热和热传导的组合来实现的。
为了提高设备的传热效率,可以采用以下措施:1、改变折流板的形状和布置,以增加壳侧流体的湍流度。
2、选择具有高导热系数的材料,以提高管壁的热传导性能。
3、适当增加管束数量和布置密度,以增加传热面积。
四、应用特点与优势管壳式换热器在各种工业领域中得到了广泛应用,主要特点有:1、结构紧凑,占地面积小,易于布置。
2、材料选择广泛,适用于各种不同的工艺条件和腐蚀性介质。
3、传热效率高,能够实现两种流体的有效热交换。
4、制造工艺成熟,操作维护方便,使用寿命较长。
五、结论本文对管壳式换热器的结构设计进行了全面分析,包括材料选择、传热原理和应用特点等方面的内容。
通过合理的结构设计,可以显著提高管壳式换热器的传热效率和可靠性,使其在各种工业领域中发挥更加重要的作用。
随着技术的不断进步,管壳式换热器的设计和制造水平也将不断提升,为工业生产带来更大的价值。
六、展望随着工业生产的不断发展和能源紧缺的压力日益增大,管壳式换热器的应用前景更加广阔。
管壳式换热器结构介绍
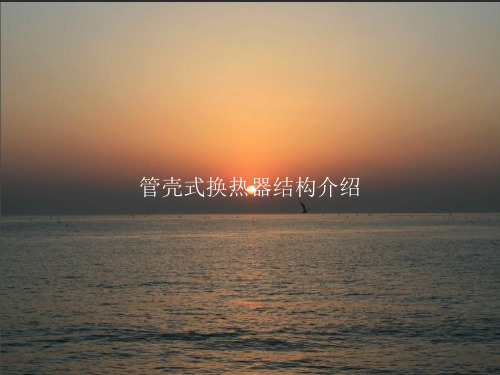
后封头
L型后封头:和A型前封头相同 M型后封头:和B型前封头相同 N型后封头:和N型前封头相同 U型:U型管束,管束可移动,壳侧容易清洗;热膨胀处理优秀,经济无法兰; 缺点是管侧无法清洗,更换管束困难,弯头部位容易冲刷损伤, P型封头和W型封头已经被淘汰,不在使用, S型封头:其尺寸特点是其后封头要比壳体的直径大,优点是可以解决换热 器设计过程中的两个问题,一是可以消除换热器的热应力,二是换热器的管
造遵循标准:国外TEMAASME国内GB151、GB150
换热器封头选取原则
1、管壳侧是否需要清洗; 2、是否需要移动管束; 3、是否需要考虑热膨胀; 前封头类型:A、B、C、D、N 后封头类型:L、M、N、P、S、T、W 后封头又分为固定式、浮头式以及U型管,相对于固定式,浮头式造价更高、 需要更大的壳径、低的换热效果由于泄漏流C的存在,优点则是一端具有自 由度可以处理好热膨胀问题,
温度,
5、设备结构的选择
对于一定的工艺条件,首先应确定设备的形式, 例如选择固定管板形式还是浮头形式等,参
螺纹管性能特点
在管子类型中,螺纹管属于管外扩展表面的类型,在普通换热管外壁轧制成 螺纹状的低翅片,用以增加外侧的传热面积,螺纹管表面积比光管可扩展 1.6-2.7倍,与光管相比,当管外流速一样时,壳程传热热阻可以缩小相应的倍 数,而管内流体因管径的减小,则压力降会略有增大,螺纹管比较适宜于壳
K型壳体:主要用于管程热介质,壳侧蒸发的工况,在废热回收条件下使用,
X型壳体:冷热流体属于错流流动,其优点是压降非常小,当采用其他壳体 发生振动,且通过调整换热器参数无法消除该振动时可以使用此壳体形式,
其不足之处是流体分布不均匀,X型壳体并不经常使用,
在化工工艺手册中,I型壳体类型可EDR软件中的不是同一种壳体,其形式见 I1,它的使用方式仅有一种搭配,就是BIU,U型管换热器,
四种管壳式换热器的结构特点
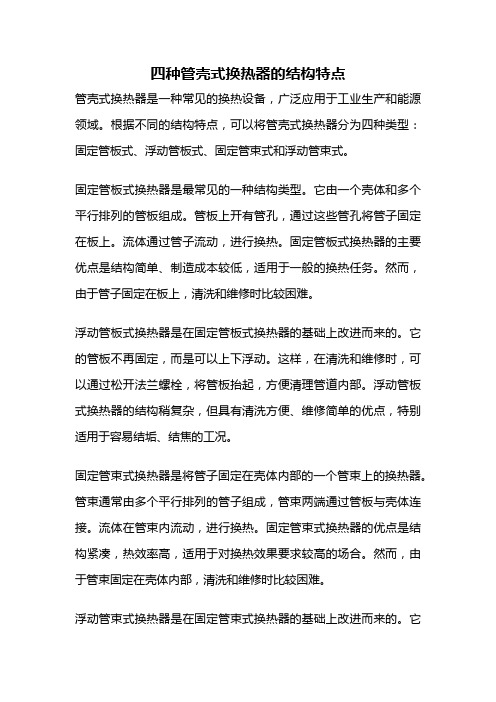
四种管壳式换热器的结构特点管壳式换热器是一种常见的换热设备,广泛应用于工业生产和能源领域。
根据不同的结构特点,可以将管壳式换热器分为四种类型:固定管板式、浮动管板式、固定管束式和浮动管束式。
固定管板式换热器是最常见的一种结构类型。
它由一个壳体和多个平行排列的管板组成。
管板上开有管孔,通过这些管孔将管子固定在板上。
流体通过管子流动,进行换热。
固定管板式换热器的主要优点是结构简单、制造成本较低,适用于一般的换热任务。
然而,由于管子固定在板上,清洗和维修时比较困难。
浮动管板式换热器是在固定管板式换热器的基础上改进而来的。
它的管板不再固定,而是可以上下浮动。
这样,在清洗和维修时,可以通过松开法兰螺栓,将管板抬起,方便清理管道内部。
浮动管板式换热器的结构稍复杂,但具有清洗方便、维修简单的优点,特别适用于容易结垢、结焦的工况。
固定管束式换热器是将管子固定在壳体内部的一个管束上的换热器。
管束通常由多个平行排列的管子组成,管束两端通过管板与壳体连接。
流体在管束内流动,进行换热。
固定管束式换热器的优点是结构紧凑,热效率高,适用于对换热效果要求较高的场合。
然而,由于管束固定在壳体内部,清洗和维修时比较困难。
浮动管束式换热器是在固定管束式换热器的基础上改进而来的。
它的管束可以上下浮动,方便清洗和维修。
浮动管束式换热器的结构复杂,但具有清洗方便、维修简单的优点,特别适用于容易结垢、结焦的工况。
四种管壳式换热器的结构特点分别是:固定管板式换热器结构简单、制造成本低;浮动管板式换热器清洗和维修方便;固定管束式换热器热效率高;浮动管束式换热器清洗和维修方便。
每种结构类型都有其适用的场合,选择合适的换热器结构可以提高换热效率,降低维护成本,确保设备的正常运行。
管壳式与板式水水换热器的比较分析

管壳式与板式水水换热器的比较分析管壳式和板式水水换热器是两种常见的换热设备,它们在应用范围、换热效果、维护保养等方面都有不同的特点。
本文将分析对比这两种换热器的优缺点,以帮助读者选择适合自己的换热器。
一、管壳式水水换热器管壳式换热器是由一个管壳和多个外管、内管组成的传热设备。
内管和外管之间的空间中流体进行传热,通常用于高温、高压、高粘度、易腐蚀、易结垢的介质换热。
其优点主要有以下几点:1. 适用范围广:管壳式换热器可以适用于多种工业领域,如化工、石化、制药、航空航天等。
2. 效率高:由于管壳式换热器的传热面积大,因此效率相对较高。
3. 维护保养方便:管壳式换热器可以进行组件化维护,随时更换外管和内管,便于清洗和维护。
但管壳式水水换热器也有其缺点:1. 制作成本高:管壳式换热器的制造成本较高,因为需要制造大量外管和内管。
2. 占用空间大:管壳式换热器由于外形尺寸较大,占用的空间相对较大。
3. 流体压降大:由于管壳式换热器的内部设计,流体的压降大,需要消耗更多的能量。
二、板式水水换热器板式换热器是由多个密封的板组成,板上的通道构成流体的管道,在板上进行传热。
板式换热器通常用于低温、低压、低粘度、不易腐蚀、不易结垢的介质换热。
其优点主要有以下几点:1. 占用空间小:板式换热器通常比管壳式换热器小,占用的空间相对较小。
2. 制作成本低:板式换热器的制造成本相对较低,因为只需要制造少量密封板即可。
3. 传热效果好:由于板式换热器的传热面积大,传热效果好。
但板式换热器也有其缺点:1. 不适用于高温高压:由于板式换热器的密封性不够,不适用于高温、高压介质。
2. 维护保养复杂:由于板式换热器的结构复杂,维护保养需要额外耗费一定的时间和精力。
3. 稳定性差:由于板式换热器板间的连接处容易出现渗漏情况,不够稳定。
综上所述,管壳式水水换热器和板式水水换热器在适用范围、效率、维护保养等方面都有不同的特点。
根据实际需要选择适合自己的换热器是关键。
管壳式换热器原理
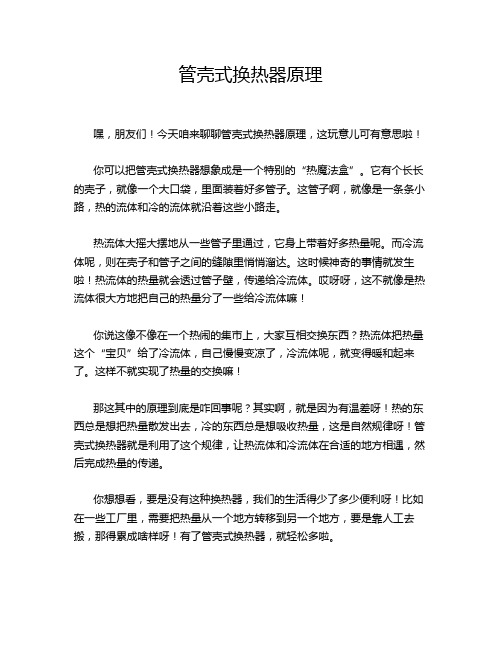
管壳式换热器原理嘿,朋友们!今天咱来聊聊管壳式换热器原理,这玩意儿可有意思啦!你可以把管壳式换热器想象成是一个特别的“热魔法盒”。
它有个长长的壳子,就像一个大口袋,里面装着好多管子。
这管子啊,就像是一条条小路,热的流体和冷的流体就沿着这些小路走。
热流体大摇大摆地从一些管子里通过,它身上带着好多热量呢。
而冷流体呢,则在壳子和管子之间的缝隙里悄悄溜达。
这时候神奇的事情就发生啦!热流体的热量就会透过管子壁,传递给冷流体。
哎呀呀,这不就像是热流体很大方地把自己的热量分了一些给冷流体嘛!你说这像不像在一个热闹的集市上,大家互相交换东西?热流体把热量这个“宝贝”给了冷流体,自己慢慢变凉了,冷流体呢,就变得暖和起来了。
这样不就实现了热量的交换嘛!那这其中的原理到底是咋回事呢?其实啊,就是因为有温差呀!热的东西总是想把热量散发出去,冷的东西总是想吸收热量,这是自然规律呀!管壳式换热器就是利用了这个规律,让热流体和冷流体在合适的地方相遇,然后完成热量的传递。
你想想看,要是没有这种换热器,我们的生活得少了多少便利呀!比如在一些工厂里,需要把热量从一个地方转移到另一个地方,要是靠人工去搬,那得累成啥样呀!有了管壳式换热器,就轻松多啦。
而且哦,管壳式换热器还有很多不同的类型呢,就像人有不同的性格一样。
有的适合处理高温的流体,有的适合处理腐蚀性的流体,各有各的特点和用处。
咱再说说它的优点吧。
它结构相对简单,容易制造和维护,这多好呀!就像一个老实可靠的朋友,不会给你找麻烦。
而且它的换热效率也不错呀,可以在很多场合大显身手。
当然啦,它也不是完美无缺的。
它可能会占比较大的空间,有时候还会有一些泄漏的问题。
但这也不能掩盖它的光芒呀!总之呢,管壳式换热器原理虽然看起来有点复杂,但只要你用心去理解,就会发现其实也不难。
它就像我们生活中的一个好帮手,默默地为我们服务着。
让我们的生活变得更加舒适和便利。
所以呀,可别小看了这个“热魔法盒”哦!原创不易,请尊重原创,谢谢!。
管壳式换热器优缺点
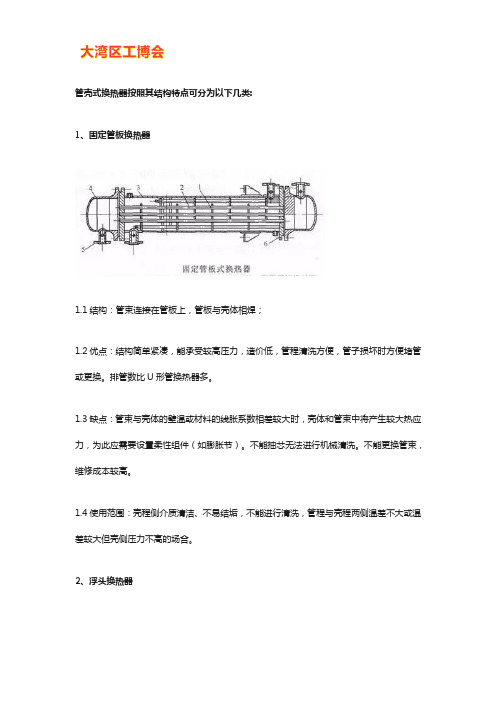
管壳式换热器按照其结构特点可分为以下几类:1、固定管板换热器1.1结构:管束连接在管板上,管板与壳体相焊;1.2优点:结构简单紧凑,能承受较高压力,造价低,管程清洗方便,管子损坏时方便堵管或更换。
排管数比U形管换热器多。
1.3缺点:管束与壳体的壁温或材料的线胀系数相差较大时,壳体和管束中将产生较大热应力,为此应需要设置柔性组件(如膨胀节)。
不能抽芯无法进行机械清洗。
不能更换管束,维修成本较高。
1.4使用范围:壳程侧介质清洁、不易结垢,不能进行清洗,管程与壳程两侧温差不大或温差较大但壳侧压力不高的场合。
2、浮头换热器2.1结构:两端管板中只有一端与壳体固定,另一端可相对壳体自由移动,称为浮头。
浮头由浮头管板,钩圈和浮头盖组成,是可拆连接,管束可从壳体中抽出。
管束与壳体的热形变互不约束,不会产生热应力。
2.2优点:可抽式管束,当换热管为正方形或转角正方形排列时,管束可抽出进行机械清洗,适用于易结垢及堵塞的工况。
一端可自由浮动,无需考虑温差应力,可用于大温差场合。
2.3缺点:结构复杂,造价高,设备笨重,材料消耗大。
浮头端结构复杂影响排管数。
浮头密封面在操作时易产生内漏。
2.4适用范围:适用于壳体和管束之间壁温差较大或壳程介质易结垢的场合。
浮头换热器在炼油行业或乙烯行业中应用较多,由于内浮头结构限制了使用压力和温度,一般情况下Pmax≤6.4MPa,Tmax≤400℃。
3、U形管换热器3.1结构:只有一块管板,管束由多根U形管组成,管的两端固定在同一块管板上,换热管可以自由伸缩。
3.2优点:以U形管尾部的自由浮动解决了温差应力的问题。
结构简单,价格便宜,承压能力强。
3.3缺点:由于受管弯曲半径的限制,布管较少。
壳程流体易形成短路。
坏一根U形管相当于坏两根管,报废率较高。
3.4适用范围:是换热器中唯一可用于高温、高压、高温差的换热器。
适用于管壳壁温差较大或壳程介质结垢需要清洗,又不适宜采用浮头式和固定管板的场合。
常见换热器:管壳式换热器

常见换热器:管壳式换热器列管式换热器(tubular exchanger)是目前化工行业上应用最广的一种换热器。
它主要由壳体、管板、换热管、封头、折流挡板等组成。
所需材质,可分别采用普通碳钢、紫铜、或不锈钢制作。
在进行换热时,一种流体由封头的连结管处进入,在管流动,从封头另一端的出口管流出,这称之管程;另一种流体由壳体的接管进入,从壳体上的另一接管处流出,这称为壳程。
列管换热器的分类:1.固定管板式换热器。
结构比较简单、紧凑、造价便宜,但管外不能机械清洗。
此种换热器管束连接在管板上,管板分别焊在外壳两端,并在其上连接有顶盖,顶盖和壳体装有流体进出口接管。
通常在管外装置一系列垂直于管束的挡板。
同时管子和管板与外壳的连接都是刚性的,而管内管外是两种不同温度的流体。
因此,当管壁与壳壁温差较大时,由于两者的热膨胀不同,产生了很大的温差应力,以至管子扭弯或使管子从管板上松脱,甚至毁坏换热器。
为了克服温差应力必须有温差补偿装置,一般在管壁与壳壁温度相差50℃以上时,为安全起见,换热器应有温差补偿装置。
但补偿装置(膨胀节)只能用在壳壁与管壁温差低于60~70℃和壳程流体压强不高的情况。
一般壳程压强超过0.6Mpa时由于补偿圈过厚,难以伸缩,失去温差补偿的作用,就应考虑其他结构。
2.U型管换热器每根换热管皆弯成U形,两端分别固定在同一管板上下两区,借助于管箱内的隔板分成进出口两室。
此种换热器完全消除了热应力,结构比浮头式简单,但管程不易清洗。
此类换热器的特点是管束可以自由伸缩,不会因管壳之间的温差而产生热应力,热补偿性能好;管程为双管程,流程较长,流速较高,传热性能较好;承压能力强;管束可从壳体内抽出,便于检修和清洗,且结构简单,造价便宜。
但管内清洗不便,管束中间部分的管子难以更换,又因最内层管子弯曲半径不能太小,在管板中心部分布管不紧凑,所以管子数不能太多,且管束中心部分存在间隙,使壳程流体易于短路而影响壳程换热。
- 1、下载文档前请自行甄别文档内容的完整性,平台不提供额外的编辑、内容补充、找答案等附加服务。
- 2、"仅部分预览"的文档,不可在线预览部分如存在完整性等问题,可反馈申请退款(可完整预览的文档不适用该条件!)。
- 3、如文档侵犯您的权益,请联系客服反馈,我们会尽快为您处理(人工客服工作时间:9:00-18:30)。
6.1 概述 6.2 管壳式换热器 6.3 传热强化技术
过程设备设计
6.2.1 基本类型 6.2.2 管壳式换热器结构 6.2.3 管板设计 6.2.4 膨胀节设计 6.2.5 管束振动和防止
1
6.2 管壳式换热器
过程设备设计
本章 重点
教学重点: 管壳式换热器结构。
教学难点: 管板设计、管束振动。
特点
与浮头式、U形管式换热器一样, 清洗维修方便;
可处理不清洁、易结垢介质,能 承受高温、高压(无温差应力)。
17
6.2.2 管壳式换热器结构
过程设备设计
管程
壳程
管程
(a) BEM立式固定管板式换热器
18
6.2.2 管壳式换热器结构
管程——与管束中流体相通的空间 壳程——换热管外面流体及相通空间
过程设备设计
平面形 椭圆形 碟形 球形 挠性薄管板等
应用——壳体和管束之间壁温差较大或壳程介质易 结垢的场合。
10
6.2.1 基本类型
结构
三、U形管式换热器
过程设备设计
U形管
(C)BIU U形管式换热器
11
U形管式换热器
12
6.2.1 基本类型
优点 缺点
应用
过程设备设计
结构比较简单、价格便宜,承压能力强。
受弯管曲率半径限制,布管少; 管束最内层管间距大,管板利用率低; 壳程流体易短路,传热不利。 当管子泄漏损坏时,只有外层U形管可更 换,内层管只能堵死,坏一根U形管相当 于坏两根管,报废率较高。
流体无腐蚀性或有轻微腐蚀性时, 管板采用压力容器用碳素钢或低合金钢板或锻件制造; 腐蚀性较强时,用不锈钢、铜、铝、钛等材料, 为经济考虑,采用复合钢板或堆焊衬里。
28
6.2.2 管壳式换热器结构
2.管板结构
厚度—— 满足强度前提下,尽量减少管板厚度
过程设备设计
热应力
(a) BEM立式固定管板式换热器
2
管壳式换热器
3
6.2.1 基本类型
6.2.1 基本类型
一、固定管板式 二、浮头式 三、U形管式 四、填料函式 五、釜式重沸器
过程设备设计
4
6.2.1 基本类型
结构
一、固定管板式换热器
过程设备设计
(a) BEM立式固定管板式换热器
5
双管程固定管板换热器
6
6.2.1 基本类型
过程设备设计
优点
三角形布管多,但不易清洗; 正方形及转角正方形较易清洗
P≥1.25d0
24
6.2.2 管壳式换热器结构
过程设备设计
表6-1 常用换热管中心距/mm
换热管外径do 12 14 19 25 32 38 45 57 换热管中心距 16 19 25 32 40 48 57 72
25
6.2.2 管壳式换热器结构
翅片管(在给热系数低侧) 螺旋槽管 螺纹管
2.换热管尺寸
φ19×2、φ25×2.5和φ38×2.5mm无缝钢管 φ25×2和φ38×2.5mm不锈钢管
标准管长1.5、2.0、3.0、4.5、6.0、9.0m等
21
6.2.2 管壳式换热器结构
过程设备设计
小管径
单位体积传热面积增大、结构紧凑、 金属耗量减少、传热系数提高 阻力大,不便清洗,易结垢堵塞
——结构简单、紧凑、能承受较高的压力,造价 低,管程清洗方便,管子损坏时易于堵管或更换。
缺点
——当管束与壳体的壁温或材料的线膨胀系数相 差较大时,壳体和管束中将产生较大的热应力。
应用
——适用于壳侧介质清洁且不易结垢并能进行溶 解清洗,管、壳程两侧温差不大或温差较大但壳 侧压力不高的场合。
为减少热应力,通常在固定管板式换热器中设置柔性元件 (如膨胀节、挠性管板等),来吸收热膨胀差。
29
6.2.2 管壳式换热器结构
过程设备设计
厚度计算标准 GB151《管壳式换热器》
美国管式换热器制造商协会标准TEMA
西德AD标准
厚度
“厚管板”——GB151《管壳式换热器》、 美国管式换热器制造商协会标准TEMA
“薄管板”——西德AD标准8-20mm
30
6.2.2 管壳式换热器结构
薄管板
目前主要有
管、壳壁温差较大或壳程介质易结垢需要 清洗,又不宜采用浮头式和固定管板式的 场合。特别适用于管内走清洁而不易结垢 的高温、高压、腐蚀性大的物料。
13
6.2.1 基本类型
结构
四、填料函式
过程设备设计
填料函式密封
(d) AFP填料函双壳程换热器
14
6.2.1 基本类型
过程设备设计
优点
结构较浮头式简单,加工制造方便; 节省材料,造价比较低廉; 管束从壳体内可抽出; 管内、管间都能进行清洗,维修方ቤተ መጻሕፍቲ ባይዱ。
缺点 应用
填料处易泄漏。
4MPa 以下,且不适用于易挥发、易燃、 易爆、有毒及贵重介质,使用温度受填 料的物性限制。
注:填料函式换热器现在已很少采用。
15
6.2.1 基本类型
结构
五、釜式重沸器
过程设备设计
蒸发空间
(f)
管束可以为浮头式、U形管式和固定管板式结构
16
6.2.1 基本类型
过程设备设计
过程设备设计
26
6.2.2 管壳式换热器结构
二、管板
过程设备设计
作用
用来排布换热管; 将管程和壳程流体分开,避免冷、热流体混合; 承受管程、壳程压力和温度的载荷作用。
27
6.2.2 管壳式换热器结构
1.管板材料
过程设备设计
力学性能 介质腐蚀性(及tube-tubesheet间电位差对腐蚀影响) 贵重钢板价格
过程设备设计
管程
壳程
管程
(a) BEM立式固定管板式换热器
19
6.2.2 管壳式换热器结构
6.2.2.1 管程结构 6.2.2.2 壳程结构
过程设备设计
一、换热管 二、管板 三、管箱 四、管束分程 五、换热管与管板连接
20
6.2.2 管壳式换热器结构
一、换热管
1.换热管型式
光管 强化传热管
过程设备设计
7
6.2.1 基本类型
结构
二、浮头式
过程设备设计
浮头端可自由伸缩,无热应力
浮头端
8
浮头式换热器 9
6.2.1 基本类型
过程设备设计
优点——管间和管内清洗方便,不会产生热应力;
缺点——结构复杂,造价比固定管板式换热器高, 设备笨重,材料消耗量大,且浮头端小盖 在操作中无法检查,制造时对密封要求较 高。
用于较清洁的流体
大管径
粘性大或污浊的流体
22
6.2.2 管壳式换热器结构
3.换热管材料
金属材料
碳素钢 低合金钢 不锈钢 铜 铜镍合金 铝合金 钛等
非金属材料
过程设备设计
石墨 陶瓷 聚四氟乙烯等
23
6.2.2 管壳式换热器结构
4.换热管排列形式及中心距
30°
60°
90°
过程设备设计
45°
p
管桥强度 清洗通道