铸钢件产品热处理艺规范.doc
铸钢件常见热处理
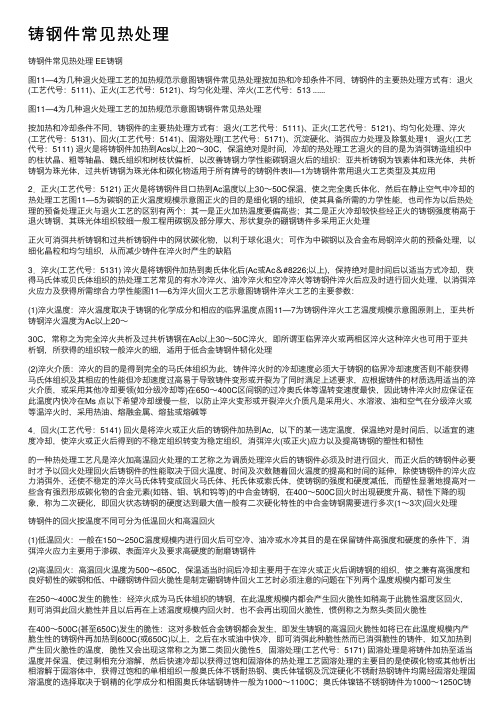
铸钢件常见热处理铸钢件常见热处理 EE铸钢图11—4为⼏种退⽕处理⼯艺的加热规范⽰意图铸钢件常见热处理按加热和冷却条件不同,铸钢件的主要热处理⽅式有:退⽕(⼯艺代号:5111)、正⽕(⼯艺代号:5121)、均匀化处理、淬⽕(⼯艺代号:513 ......图11—4为⼏种退⽕处理⼯艺的加热规范⽰意图铸钢件常见热处理按加热和冷却条件不同,铸钢件的主要热处理⽅式有:退⽕(⼯艺代号:5111)、正⽕(⼯艺代号:5121)、均匀化处理、淬⽕(⼯艺代号:5131)、回⽕(⼯艺代号:5141)、固溶处理(⼯艺代号:5171)、沉淀硬化、消弭应⼒处理及除氢处理1.退⽕(⼯艺代号:5111) 退⽕是将铸钢件加热到Acs以上20~30C,保温绝对是时间,冷却的热处理⼯艺退⽕的⽬的是为消弭铸造组织中的柱状晶、粗等轴晶、魏⽒组织和树枝状偏析,以改善铸钢⼒学性能碳钢退⽕后的组织:亚共析铸钢为铁素体和珠光体,共析铸钢为珠光体,过共析铸钢为珠光体和碳化物适⽤于所有牌号的铸钢件表ll—1为铸钢件常⽤退⽕⼯艺类型及其应⽤2.正⽕(⼯艺代号:5121) 正⽕是将铸钢件⽬⼝热到Ac温度以上30~50C保温,使之完全奥⽒体化,然后在静⽌空⽓中冷却的热处理⼯艺图11—5为碳钢的正⽕温度规模⽰意图正⽕的⽬的是细化钢的组织,使其具备所需的⼒学性能,也司作为以后热处理的预备处理正⽕与退⽕⼯艺的区别有两个:其⼀是正⽕加热温度要偏⾼些;其⼆是正⽕冷却较快些经正⽕的铸钢强度稍⾼于退⽕铸钢,其珠光体组织较细⼀般⼯程⽤碳钢及部分厚⼤、形状复杂的硼钢铸件多采⽤正⽕处理正⽕可消弭共析铸钢和过共析铸钢件中的⽹状碳化物,以利于球化退⽕;可作为中碳钢以及合⾦布局钢淬⽕前的预备处理,以细化晶粒和均匀组织,从⽽减少铸件在淬⽕时产⽣的缺陷3.淬⽕(⼯艺代号:5131) 淬⽕是将铸钢件加热到奥⽒体化后(Ac或Ac•以上),保持绝对是时间后以适当⽅式冷却,获得马⽒体或贝⽒体组织的热处理⼯艺常见的有⽔冷淬⽕、油冷淬⽕和空冷淬⽕等铸钢件淬⽕后应及时进⾏回⽕处理,以消弭淬⽕应⼒及获得所需综合⼒学性能图11—6为淬⽕回⽕⼯艺⽰意图铸钢件淬⽕⼯艺的主要参数:(1)淬⽕温度:淬⽕温度取决于铸钢的化学成分和相应的临界温度点图11—7为铸钢件淬⽕⼯艺温度规模⽰意图原则上,亚共析铸钢淬⽕温度为Ac以上20~30C,常称之为完全淬⽕共析及过共析铸钢在Ac以上30~50C淬⽕,即所谓亚临界淬⽕或两相区淬⽕这种淬⽕也可⽤于亚共析钢,所获得的组织较⼀般淬⽕的细,适⽤于低合⾦铸钢件韧化处理(2)淬⽕介质:淬⽕的⽬的是得到完全的马⽒体组织为此,铸件淬⽕时的冷却速度必须⼤于铸钢的临界冷却速度否则不能获得马⽒体组织及其相应的性能但冷却速度过⾼易于导致铸件变形或开裂为了同时满⾜上述要求,应根据铸件的材质选⽤适当的淬⽕介质,或采⽤其他冷却要领(如分级冷却等)在650~400C区间钢的过冷奥⽒体等温转变速度最快,因此铸件淬⽕时应保证在此温度内快冷在Ms 点以下希望冷却缓慢⼀些,以防⽌淬⽕变形或开裂淬⽕介质凡是采⽤⽕、⽔溶液、油和空⽓在分级淬⽕或等温淬⽕时,采⽤热油、熔融⾦属、熔盐或熔碱等4.回⽕(⼯艺代号:5141) 回⽕是将淬⽕或正⽕后的铸钢件加热到Ac,以下的某⼀选定温度,保温绝对是时间后,以适宜的速度冷却,使淬⽕或正⽕后得到的不稳定组织转变为稳定组织,消弭淬⽕(或正⽕)应⼒以及提⾼铸钢的塑性和韧性的⼀种热处理⼯艺凡是淬⽕加⾼温回⽕处理的⼯艺称之为调质处理淬⽕后的铸钢件必须及时进⾏回⽕,⽽正⽕后的铸钢件必要时才予以回⽕处理回⽕后铸钢件的性能取决于回⽕温度、时间及次数随着回⽕温度的提⾼和时间的延伸,除使铸钢件的淬⽕应⼒消弭外,还使不稳定的淬⽕马⽒体转变成回⽕马⽒体、托⽒体或索⽒体,使铸钢的强度和硬度减低,⽽塑性显著地提⾼对⼀些含有强烈形成碳化物的合⾦元素(如铬、钼、钒和钨等)的中合⾦铸钢,在400~500C回⽕时出现硬度升⾼、韧性下降的现象,称为⼆次硬化,即回⽕状态铸钢的硬度达到最⼤值⼀般有⼆次硬化特性的中合⾦铸钢需要进⾏多次(1~3次)回⽕处理铸钢件的回⽕按温度不同可分为低温回⽕和⾼温回⽕(1)低温回⽕:⼀般在150~250C温度规模内进⾏回⽕后可空冷、油冷或⽔冷其⽬的是在保留铸件⾼强度和硬度的条件下,消弭淬⽕应⼒主要⽤于渗碳、表⾯淬⽕及要求⾼硬度的耐磨铸钢件(2)⾼温回⽕:⾼温回⽕温度为500~650C,保温适当时间后冷却主要⽤于在淬⽕或正⽕后调铸钢的组织,使之兼有⾼强度和良好韧性的碳钢和低、中硼钢铸件回⽕脆性是制定硼钢铸件回⽕⼯艺时必须注意的问题在下列两个温度规模内都可发⽣在250~400C发⽣的脆性:经淬⽕成为马⽒体组织的铸钢,在此温度规模内都会产⽣回⽕脆性如稍⾼于此脆性温度区回⽕,则可消弭此回⽕脆性并且以后再在上述温度规模内回⽕时,也不会再出现回⽕脆性,惯例称之为熬头类回⽕脆性在400~500C(甚⾄650C)发⽣的脆性:这对多数低合⾦铸钢都会发⽣,即发⽣铸钢的⾼温回⽕脆性如将已在此温度规模内产脆⽣性的铸钢件再加热到600C(或650C)以上,之后在⽔或油中快冷,即可消弭此种脆性然⽽已消弭脆性的铸件,如⼜加热到产⽣回⽕脆性的温度,脆性⼜会出现这常称之为第⼆类回⽕脆性5.固溶处理(⼯艺代号:5171) 固溶处理是将铸件加热⾄适当温度并保温,使过剩相充分溶解,然后快速冷却以获得过饱和固溶体的热处理⼯艺固溶处理的主要⽬的是使碳化物或其他析出相溶解于固溶体中,获得过饱和的单相组织⼀般奥⽒体不锈耐热钢、奥⽒体锰钢及沉淀硬化不锈耐热钢铸件均需经固溶处理固溶温度的选择取决于钢精的化学成分和相图奥⽒体锰钢铸件⼀般为1000~1100C;奥⽒体镍铬不锈钢铸件为1000~1250C铸钢中含碳量越⾼,难熔合⾦元素越多,则其固溶温度应越⾼含铜的沉淀硬化铸钢,由于铸态有硬质富铜相在冷却过程中沉淀,致使铸钢件硬度升⾼为软化组织、改善加⼯性能,铸钢件需经固溶处理其固溶温度为900~950C经快冷后可得到铜的质量分数为1.0%~1.5%的过饱和单相组织6.沉淀硬化处理(时效处理) 铸件经固溶处理或淬⽕后,在室温或⾼于室温的适当温度保温,在过饱和固溶体中形成溶质原⼦偏聚区和(或)析出弥散漫衍的强化相⽽使⾦属硬化的处理称为沉淀硬化处理(或时效处理)在⾼于室温下进⾏的称为⼈⼯时效其实质是:在较⾼的温度下,⾃过饱和固溶体中析出碳化物、氮化物、⾦属间化合物及其他不稳定的中间相,并弥散漫衍于基体中,故⽽使铸钢的综合⼒学性能和硬度提⾼时效处理的温度直接影响铸钢件的最终性能时效温度过低,沉淀硬化相析出缓慢;温度过⾼,则因析出相的堆积长⼤导致过时效,⽽得不到最佳的性能所以应根据铸钢件的牌号及规定的性能要求选⽤时效温度奥⽒体耐热铸钢时效温度⼀般为550~850C,⾼强度沉淀硬化铸钢为500C,时间为1~4h 含铜的低硼钢和奥⽒体耐热钢铸件以及低合⾦的奥⽒体锰钢铸件多采⽤时效处理图11-8为截⾯25mm试样的时效效果7.消弭应⼒处理其⽬的是消弭铸造应⼒、淬⽕应⼒和机械加⼯形成的应⼒,稳定尺⼨⼀般加热到Ac,以下100~200C保温绝对是时间,随炉慢冷铸件的组织没有变化碳钢、低硼钢或⾼硼钢铸件都可以进⾏处理8.除氢处理⽬的是去除氢⽓,提⾼铸钢的塑性加热到l70~200C或280~320C,长时间保温进⾏处理没有组织变化主要⽤于易于产⽣氢脆倾向的低硼钢铸件⼆、钢的整体热处理整体热处理是对⼯件整体进⾏穿透加热常⽤的要领有退⽕、正⽕、淬⽕和回⽕1.钢的退⽕与正⽕(1)退⽕与正⽕的⽬的在呆板零件和⼯⽣产模型等⼯件的加⼯制造过程中,退⽕和正⽕经常作为预备热处理⼯序,安排在铸、锻、焊⼯序之后、切削(粗)加⼯之前,⽤以消弭前⼀⼯序所带来的某些缺陷,为随后的⼯序做筹办例如,在铸造或锻造等热加⼯以后,钢件中不但存在残存应⼒,并且组织粗⼤不均匀,成分也有偏析,这样的钢件⼒学性能差劲,淬⽕时也容易造成变形和开裂⼜如,在铸造或锻造等热加⼯以后,钢件硬度经常偏低或偏⾼,并且不均匀,严重影响切削加⼯性能退⽕和正⽕的主要⽬的有:①调整硬度以便进⾏切削加⼯;②消弭残存应⼒,防⽌钢件的变形、开裂;③细化晶粒,改善组织以提⾼钢的⼒学性能;④为最终热处理作好组织筹办(2)退⽕⼯艺及应⽤钢的退⽕是将钢件加热到适当温度,保温绝对是时间,然后缓慢冷却,以获得接近均衡组织状态的热处理⼯艺①完全退⽕与等温退⽕完全退⽕是指将钢件完全奥⽒体化(加热⾄Ac3以上30~50℃)后,随之缓慢冷却,获得接近均衡组织的退⽕⼯艺出产中为提⾼出产率,⼀般随炉冷⾄600℃摆布,将⼯件出炉空冷完全退⽕的主要缺点:完全退⽕主要⽤于:图 3-15 ⾼速⼯具钢的完全退⽕与等温退⽕⼯艺曲线为缩短完全退⽕时间,出产中常采⽤等温退⽕⼯艺,⾏将钢件加热到Ac3以上30~50℃(亚共析钢)或Acl 以上10~20℃(共析钢、过共析钢),保温适当时间后,较快冷却到珠光体转变温度区间的适当温度并保持等温,使奥⽒体转变为珠光体类组织,然后在空⽓中冷却的退⽕⼯艺等温退⽕与完全退⽕⽬的不异,但转变较易节制,所⽤时间⽐完全退⽕缩短约1/3,并可获得均匀的组织和性能特别是对某些硼钢,出产中常⽤等温退⽕来代替完全退⽕或球化退⽕图3-15为⾼速⼯具钢完全退⽕与等温退⽕的⽐较②球化退⽕是指将共析钢或过共析钢加热到Ac1点以上10~20℃,保温绝对是时间后,随炉缓冷⾄室温,或快冷到略低于Arl 温度,保温⼀段时间,然后炉空⾄600℃摆布空冷,使钢中碳化物球状化的退⽕⼯艺,如图3-16所⽰图 3-16 T10钢的球化退⽕⼯艺曲线图 3-17 粒状珠光体显微组织过共析钢及合⾦⼯具钢热加⼯后,组织中常出现粗⽚状珠光体和⽹状⼆次渗碳体,钢的硬度和脆性不仅增长,钢的切削性变差,且淬⽕时易产⽣变形和开裂为消弭上述缺陷,可采⽤球化退⽕,使珠光体中的⽚状渗碳体和钢中⽹状⼆次渗碳体均呈球(粒)状,这种在铁素体基体上弥散漫衍着球状渗碳体的复相组织,称为“球化体”,如图3-17所⽰对于存在有严重⽹状⼆次渗碳体的钢,可在球化退⽕前,进步前辈⾏⼀次正⽕近些年球化退⽕的发展与应⽤(⾃阅)③去应⼒退⽕(见书)若采⽤⾼温退⽕(如完全退⽕),也能够更彻底地消弭应⼒,但会使氧化、脱碳严重,还会产⽣⾼温变形,故为了消弭应⼒,通常为采⽤低温退⽕④廓张退⽕(均匀化退⽕)(见书)(3)正⽕⼯艺及应⽤正⽕是指将钢件加热到Ac3(亚共析钢)或Accm(过共析钢)以上30~50℃,经保温后在空⽓中冷却的热处理⼯艺正⽕与退⽕的主要区别是正⽕冷却速度稍快,得到的组织较藐⼩,强度和硬度有所提⾼,操作简便,出产周期短,成本较低低碳钢和低碳硼钢经正⽕后,可提⾼硬度,改善切削加⼯性能(170~230HBS规模内⾦属切削加⼯性较好);对于中碳布局钢制作的较重要件,可作为预先热处理,为最终热处理作好组织筹办;对于过共析钢,可消弭⽹状⼆次渗碳体为球化退⽕作好组织筹办对于使⽤性能要求不⾼的零件,以及某些⼤型或形状复杂的零件,当淬⽕有开裂危险时,可采⽤正⽕作为最终热处理⼏种退⽕与正⽕的加热温度规模及热处理⼯艺曲线,如图3-18所⽰(a)加热温度规模(b)热处理⼯艺曲线图 3-18 ⼏种退⽕与正⽕⼯艺⽰意图2.钢的淬⽕与回⽕(1)淬⽕是将钢加热⾄临界点(Ac3 或Ac1)以上,保温后以⼤于VK的速度冷却,使奥⽒体转变成马⽒体(或下贝⽒体)的热处理⼯艺淬⽕的⽬的:为了得到马⽒体组织,是钢的最主要的强化⽅式1)淬⽕⼯艺①淬⽕加热温度在选择淬⽕加热温度时,应尽量使获得的组织硬度越⼤越好;获得的晶粒越⼩越好图3-19 碳钢淬⽕加热温度规模⽰意图对于亚共析钢,淬⽕温度⼀般为Ac3以上30~50℃,淬⽕后得到均匀藐⼩的M 和少数残存奥⽒体,若淬⽕温度过低,则淬⽕后组织中将会有F,使钢的强度、硬度减低;若加热温度跨越 Ac3以上(30~50℃),奥⽒体晶粒粗化,淬⽕后得到粗⼤的M,钢的⼒学性能变差,且淬⽕应⼒增⼤,易导致变形和开裂对于共析钢或过共析钢,淬⽕加热温度为Ac1以上30~50℃,淬⽕后得到藐⼩的马⽒体和少数残留奥⽒体(共析钢),或藐⼩的马⽒体、少数渗碳体和残留奥⽒体(过共析钢),由于渗碳体的存在,钢硬度和耐磨性提⾼若温度过⾼,如过共析钢加热到Accm以上温度,由于渗碳体全部溶⼊奥⽒体中,奥⽒体的碳的质量分数提⾼,Ms温度减低,淬⽕后残留奥⽒体量增多,钢的硬度和耐磨性减低此外,因温度⾼,奥⽒体晶粒粗化,淬⽕后得到粗⼤的马⽒体,脆性增⼤若加热温度低于Acl点,组织没发⽣相变,达不到淬⽕⽬的碳钢淬⽕加热温度规模如图3-19所⽰对于硼钢,由于⼤多数合⾦元素有阻碍奥⽒体晶粒长⼤的作⽤,故⽽淬⽕加热温度⽐碳钢⾼,使合⾦元素在奥⽒体中充分溶解和均匀化,以获得较好的淬⽕效果实际出产中,淬⽕加热温度的确定,尚需思量⼯件形状尺⼨、淬⽕冷却介质和技术要求等因素②淬⽕加热时间加热时间包孕升温⽂保温时间凡是以装炉后温度达到淬⽕加热温度所需时间为升温时间,并以此作为保温时间的开始;保温时间是指钢件烧透并完成奥⽒体均匀化所需时间加热时间受钢件成分、形状、尺⼨、装炉⽅式、装炉量、加热炉类型、炉温⽂加热介质等影响经验公式(见书)③淬⽕冷却介质钢进⾏淬⽕时冷却是最关键的⼯序,淬⽕的冷却速度必须⼤于临界冷却速度,快冷才能得到马⽒体,但快冷总会带来内应⼒,往往会导致⼯件的变形和开裂那么,怎样才能既得到马⽒体⽽⼜减⼩变形和开裂呢?理想的淬⽕冷却介质如图3-20所⽰出产中,常⽤的冷却介质是⽔、油、碱或盐类⽔溶液⽔是最常⽤的冷却介质,它有较强的冷却能⼒,且成本低,但其缺点是在650~400℃规模内冷却能⼒不敷强,⽽在300~200℃规模内冷却能⼒⼜很⼤,因此常会导致淬⽕钢的内应⼒增⼤,导致⼯件变形开裂,因此,⽔在出产中主要⽤于形状简略、截⾯较⼤的碳钢零件的淬⽕图3-20 理想淬⽕冷却速度曲线如在⽔中加⼊盐或碱类物质,能增长在650~400℃规模内的冷却能⼒,这对保证⼯件,特别是碳钢的淬硬是⾮常有利的,但盐⽔仍具备清⽔的缺点,即在300~200℃规模内冷却能⼒很⼤,⼯件变形开裂倾向很⼤常⽤的盐⽔液体浓度为10%~15%,盐⽔对⼯件有锈蚀作⽤,淬⽕后的⼯件应仔细清洗盐⽔⽐较适⽤于形状简略、硬度要求⾼⽽均匀、表⾯要求光洁、变形要求不严格的碳钢零件淬⽕常⽤的油有机油、变压器油、柴油等油在300~200℃规模内的冷却速度⽐⽔⼩,有利于减⼩⼯件变形和开裂,但油在650~400℃规模内冷却速度也⽐⽔⼩,不利于⼯件淬硬,因此只能⽤于低硼钢与硼钢的淬⽕,使⽤时油温应节制在40~100℃内为了减少⼯件淬⽕时的变形,可采⽤盐浴作为淬⽕介质,如熔化的NaN03、KN03等主要⽤于贝⽒体等温淬⽕,马⽒体分级淬⽕其特点是沸点⾼,冷却能⼒介于⽔于油之间,常⽤于处理形状复杂、尺⼨较⼩和变形要求严格的⼯件2)淬⽕要领由于⽬前还没有理想的淬⽕介质,故⽽在实际出产中应根据淬⽕件的详细情况采⽤不同的淬⽕要领,⼒求达到较好的效果常⽤的淬⽕要领如图3-21所⽰①单液淬⽕这种要领操作简略,易实现机械化凡是形状简略、尺⼨较⼤的碳钢件在⽔中淬⽕,硼钢件及尺⼨很⼩的碳钢件在油中淬⽕图 3-21 常⽤淬⽕要领⽰意图②双液淬⽕先浸⼊冷却能⼒强的介质中,在组织将要发⽣马⽒体转变时当即转⼊冷却能⼒弱的介质中冷却的淬⽕⼯艺常⽤的有先⽔后油,先⽔后空⽓等此种要领操作时,如能节制好⼯件在⽔中停留的时间,就可有效的防⽌淬⽕变形和开裂,但要求有较⾼的操作技术主要⽤于形状复杂的⾼碳钢件和尺⼨较⼤的硼钢件③马⽒体分级淬⽕是将钢件浸⼊温度稍⾼或稍低于Ms点的盐浴或碱浴中,保持适当时间,待⼯件整体达到介质温度后掏出空冷,以获得马⽒体组织的淬⽕⼯艺,此法操作⽐双介质淬⽕容易节制,能减⼩热应⼒、相变应⼒和变形,防⽌开裂主要⽤于截⾯尺⼨较⼩(直径或厚度<12mm、形状较复杂⼯件的淬⽕④等温淬⽕是将钢件加热到奥⽒体化后,随之快冷到贝⽒体转变温度区间保持等温,使奥⽒体转变为贝⽒体的淬⽕⼯艺此法淬⽕后应⼒和变形很⼩,但出产周期长,效率低主要⽤于形状复杂、尺⼨要求精确,并要求有较⾼强韧性的⼩型⼯、⽣产模型及弹簧的淬⽕⑤冷处理为了尽量减少钢中残存奥⽒体,以获得最⼤数⽬的马⽒体,可采⽤冷处理,即把钢淬冷⾄室温后,继续冷却⾄-70~-80℃(或更低温度),保持绝对是时间,使残存奥⽒体在继续冷却过程中转变为M,这样可提⾼钢的硬度和耐磨性,并稳定钢件尺⼨获得低温的办法是采⽤⼲冰(固态CO2)和酒精的混合剂或冷冻机冷却只有特殊的冷处理才置于-103℃的液化⼄烯或-192℃的液态氮中进⾏(2)淬⽕缺陷(见书)①变形与开裂;②氧化和脱碳;③过热和过烧很抱歉,因为您在⽹易相簿发布了违规信息,账号被屏蔽被屏蔽时期他⼈没有办法访问您的相簿去帮忙中⼼,了解如何重新恢复服务更多信息咨询:137********。
铸钢件热处理
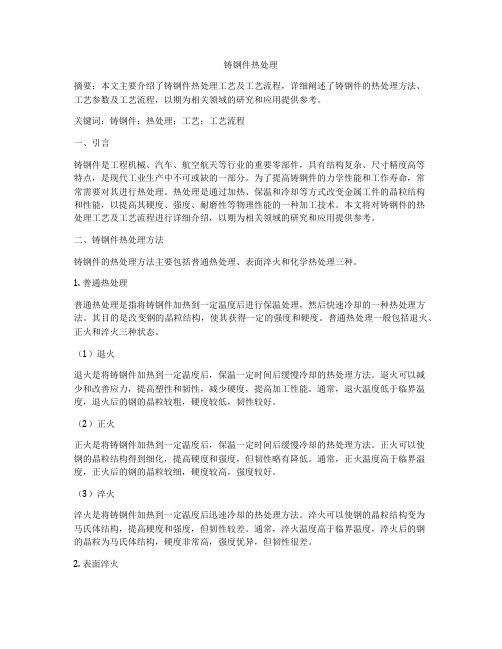
铸钢件热处理摘要:本文主要介绍了铸钢件热处理工艺及工艺流程,详细阐述了铸钢件的热处理方法、工艺参数及工艺流程,以期为相关领域的研究和应用提供参考。
关键词:铸钢件;热处理;工艺;工艺流程一、引言铸钢件是工程机械、汽车、航空航天等行业的重要零部件,具有结构复杂、尺寸精度高等特点,是现代工业生产中不可或缺的一部分。
为了提高铸钢件的力学性能和工作寿命,常常需要对其进行热处理。
热处理是通过加热、保温和冷却等方式改变金属工件的晶粒结构和性能,以提高其硬度、强度、耐磨性等物理性能的一种加工技术。
本文将对铸钢件的热处理工艺及工艺流程进行详细介绍,以期为相关领域的研究和应用提供参考。
二、铸钢件热处理方法铸钢件的热处理方法主要包括普通热处理、表面淬火和化学热处理三种。
1. 普通热处理普通热处理是指将铸钢件加热到一定温度后进行保温处理,然后快速冷却的一种热处理方法。
其目的是改变钢的晶粒结构,使其获得一定的强度和硬度。
普通热处理一般包括退火、正火和淬火三种状态。
(1)退火退火是将铸钢件加热到一定温度后,保温一定时间后缓慢冷却的热处理方法。
退火可以减少和改善应力,提高塑性和韧性,减少硬度,提高加工性能。
通常,退火温度低于临界温度,退火后的钢的晶粒较粗,硬度较低,韧性较好。
(2)正火正火是将铸钢件加热到一定温度后,保温一定时间后缓慢冷却的热处理方法。
正火可以使钢的晶粒结构得到细化,提高硬度和强度,但韧性略有降低。
通常,正火温度高于临界温度,正火后的钢的晶粒较细,硬度较高,强度较好。
(3)淬火淬火是将铸钢件加热到一定温度后迅速冷却的热处理方法。
淬火可以使钢的晶粒结构变为马氏体结构,提高硬度和强度,但韧性较差。
通常,淬火温度高于临界温度,淬火后的钢的晶粒为马氏体结构,硬度非常高,强度优异,但韧性很差。
2. 表面淬火表面淬火是将铸钢件工件的表面加热到一定温度后进行淬火,使表面产生马氏体,从而提高表面硬度和耐磨性的一种热处理方法。
热处理工艺规范[1]
![热处理工艺规范[1]](https://img.taocdn.com/s3/m/da4ed32d8762caaedc33d477.png)
21
ZG20Mn(ZG20SiMn)
900~920
≥12
风冷
550~610
≥10
炉冷
530~590
≥8
22
ZG16Mn
880~920
≥12
风冷
590~610
≥10
炉冷
570~590
≥8
23
ZG35Cr1Mo(ZG35CrMo)
890~910
≥12
风冷
580~600
≥10
炉冷
560~580
≥8
24
660-680
≥8
27
ZG15Cr1Mo
940-960
≥12
风冷
680-700
≥10
炉冷
660-680
≥8
28
G17CrMo5-5
940-960
≥12
风冷
680-700
≥10
炉冷
660-680
≥8
29
ZG25MnNi
880~900
≥10
炉冷
30
ZG25CrNiMo
880~930
≥12
风冷
880~900
≥8
11
WC6
940-960
≥12
660-680
≥8
12
ZG17CrMo1V
980-1000
≥16
雾冷
940-960
≥16
雾冷
740-760
≥10
炉冷
700-720
≥10
13
GS-17CrMoV511(G17CrMoV5-10)
980-1000
≥16
雾冷
铸件热处理工艺指导书.doc
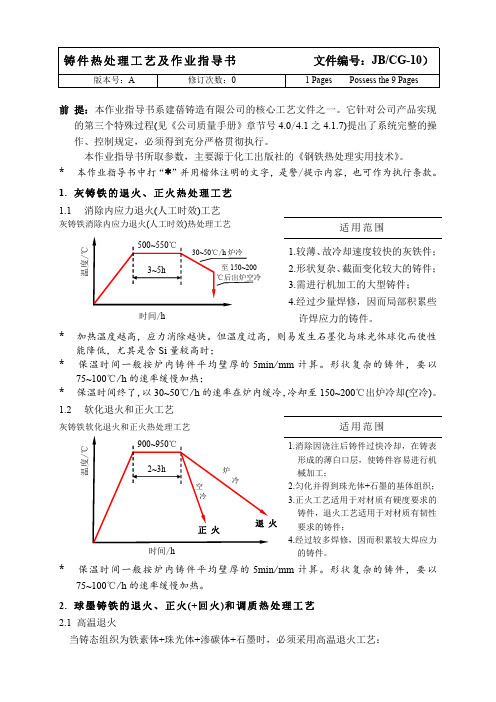
版本号:A修订次数:01Pages Possess the9Pages前提:本作业指导书系建蓓铸造有限公司的核心工艺文件之一。
它针对公司产品实现的第三个特殊过程(见《公司质量手册》章节号4.0/4.1之4.1.7)提出了系统完整的操作、控制规定,必须得到充分严格贯彻执行。
本作业指导书所取参数,主要源于化工出版社的《钢铁热处理实用技术》。
*本作业指导书中打“*”并用楷体注明的文字,是警/提示内容,也可作为执行条款。
1.灰铸铁的退火、正火热处理工艺1.1消除内应力退火(人工时效)工艺灰铸铁消除内应力退火(人工时效)热处理工艺适用范围1.较薄、故冷却速度较快的灰铁件;2.形状复杂、截面变化较大的铸件;3.需进行机加工的大型铸件;4.经过少量焊修,因而局部积累些许焊应力的铸件。
*加热温度越高,应力消除越快。
但温度过高,则易发生石墨化与珠光体球化而使性能降低,尤其是含Si量较高时;*保温时间一般按炉内铸件平均壁厚的5min/mm计算。
形状复杂的铸件,要以75~100℃/h的速率缓慢加热;*保温时间终了,以30~50℃/h的速率在炉内缓冷,冷却至150~200℃出炉冷却(空冷)。
1.2软化退火和正火工艺灰铸铁软化退火和正火热处理工艺适用范围*保温时间一般按炉内铸件平均壁厚的5min/mm计算。
形状复杂的铸件,要以75~100℃/h的速率缓慢加热。
2.球墨铸铁的退火、正火(+回火)和调质热处理工艺2.1高温退火当铸态组织为铁素体+珠光体+渗碳体+石墨时,必须采用高温退火工艺:版本号:A修订次数:02PagesPossess the 9Pages球墨铸铁高温退火热处理工艺适用范围1.获得铁素体球墨铸铁;2.分解渗碳体和珠光体,提高机械性能;3.改善加工性能,使工件容易加工且不易变形。
*退火温度越高,渗碳体组织分解速度越快,白口现象越易消除。
但温度过高将使铸件机械性能反而变坏,发生变形和表面氧化失碳,故须严格控制温度上限。
(完整)热处理工艺守则

一、热处理代号和材料标注方法(一)热处理代号1. 适用于结构钢和铸件代号:0—自然状态1—正火(或正火+回火)2—退火3—精锻+回火(如精锻或精辊叶片在精锻后只需高温回火)4—淬硬5—调质6—化学热处理(渗碳或氮化)7—除应力(包括活塞环定型处理)9—表面淬火或局部淬火2.适用铸造有色金属和奥氏体钢的代号:0—原始状态1—再结晶退火T—除应力退火T1-人工时效T4—淬火(固溶处理)T5—淬火和不完全时效T6-淬火和完全时效(固溶处理和完全时效到最高硬度)3.压力加工有色金属代号:0—原始状态M—退火C-淬火CZ—淬火和自然时效CS-淬火和人工时效(二)材料的标注方法:1.零件的材料或毛坯(包括铸锻件)如不作任何处理,也不作机械性能检查,则只标材料牌号(其热处理代号“0”在图纸上不标注)如:A3,20,35,ZQSn6—6-3。
2.零件的材料或毛坯在热处理后,不作硬度及机械性能检查者则只标注材料牌号和热处理代号:如:45-1,若有几种热处理,可用热处理代号按工艺路线顺序逐项填写:如:15CrMoA-1+7。
3.有些材料的技术条件,有几种检查组别,但强度等级只有一种或可按材料截面尺寸来决定强度等级,只注明材料牌号,热处理代号和检查组别:如:45—5(Ⅱ) 35CrMoA—5(Ⅱ)4.有些材料的技术条件,有几种组别,在同一热处理状态中有不同的强度等级,则注明材料牌号、热处理代号强度等级和检查组别,不需要规定检查组别时,检查组别可省略。
25Cr2MoVA-5 25Cr2MoVA-5如:735—Ⅲ 7355。
有些零件或者是比较重要或者是技术要求比较复杂,用上述标注方法不能说明全部要求者,则应注明标准号,在同一热处理状态中有不同的强度级别时,还应注明强度级别。
35CrMoA-5 35CrMoA-5如:Q/CCF M 3003-2003 590×Q/CCF M 3003—20036。
大锻件如叶轮、铸造轴、整体转子等的材料标注方法钢号锻件级别×标准编号7。
铸钢的热处理要求
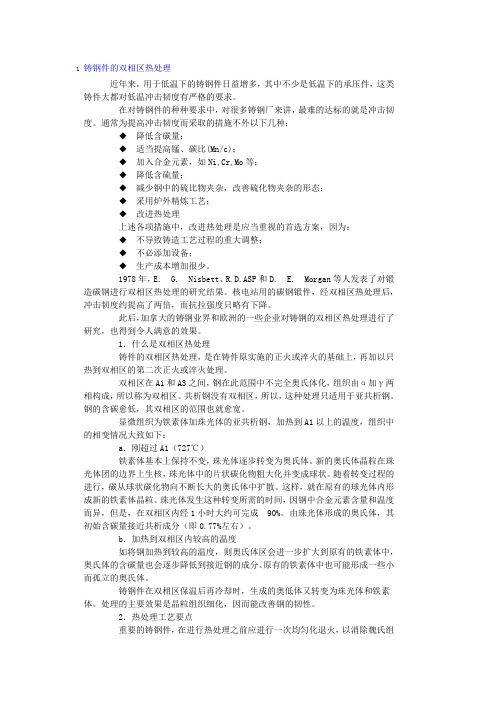
A.采用正火处理的情况
碳钢铸件和低合钢铸件,一般都采用正火或正火、回火处理。正火处理时,加热温度应在A3以上30-50℃,保温时间按铸件截面厚度确定,一般为每25mm厚度1小时。
进行双相区热处理时,将经正火处理的铸件再次加热到A1以上,A3以下的某一温度,保温后空冷。A3的具体值因钢的含碳量和合金元素含量而不同,可从热处理手册中查到,双相区处理的具体温度值值,应由试验的结果确定,可先在试验室用试样作不同的处理,从而选取效果最佳的温度。
双相区处理后,再进行回火处理,回火的温度视要求的硬度而定。
重要的铸钢件,在进行热处理之前应进行一次均匀化退火,以消除魏氏组织。均匀化退火的温度一般在A3以上100-150℃,在此温度下保温后炉冷。一般的铸钢件,可以不进行这种处理。除有特殊要求的铸钢件外,一般都采用退火、正火或调质等热处理工艺。
采用退火处理的铸钢件,对力学性能的要求一般都不高,对这类铸件,不必用双相区处理。
此后,加拿大的铸钢业界和欧洲的一些企业对铸钢的双相区热处理进行了研究,也得到令人满意的效果。
1.什么是双相区热处理
铸件的双相区热处理,是在铸件原实施的正火或淬火的基础上,再加以只热到双相区的第二次正火或淬火处理。
双相区在A1和A3之间,钢在此范围中不完全奥氏体化,组织由α加γ两相构成,所以称为双相区。共析钢没有双相区,所以,这种处理只适用于亚共析钢。钢的含碳愈低,其双相区的范围也就愈宽。
◆降低含硫量;
◆减少钢中的硫比物夹杂,改善硫化物夹杂的形态;
◆采用炉外精炼工艺;
◆改进热处理
上述各项措调整;
◆不必添加设备;
◆生产成本增加很少。
铸钢热处理
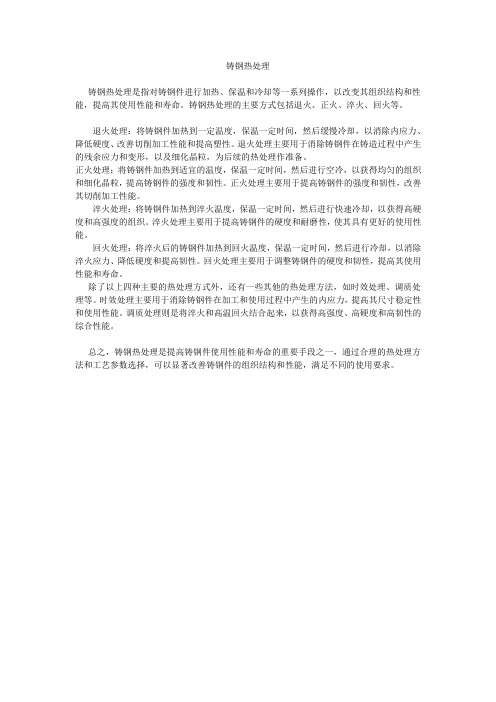
铸钢热处理
铸钢热处理是指对铸钢件进行加热、保温和冷却等一系列操作,以改变其组织结构和性能,提高其使用性能和寿命。
铸钢热处理的主要方式包括退火、正火、淬火、回火等。
退火处理:将铸钢件加热到一定温度,保温一定时间,然后缓慢冷却,以消除内应力、降低硬度、改善切削加工性能和提高塑性。
退火处理主要用于消除铸钢件在铸造过程中产生的残余应力和变形,以及细化晶粒,为后续的热处理作准备。
正火处理:将铸钢件加热到适宜的温度,保温一定时间,然后进行空冷,以获得均匀的组织和细化晶粒,提高铸钢件的强度和韧性。
正火处理主要用于提高铸钢件的强度和韧性,改善其切削加工性能。
淬火处理:将铸钢件加热到淬火温度,保温一定时间,然后进行快速冷却,以获得高硬度和高强度的组织。
淬火处理主要用于提高铸钢件的硬度和耐磨性,使其具有更好的使用性能。
回火处理:将淬火后的铸钢件加热到回火温度,保温一定时间,然后进行冷却,以消除淬火应力、降低硬度和提高韧性。
回火处理主要用于调整铸钢件的硬度和韧性,提高其使用性能和寿命。
除了以上四种主要的热处理方式外,还有一些其他的热处理方法,如时效处理、调质处理等。
时效处理主要用于消除铸钢件在加工和使用过程中产生的内应力,提高其尺寸稳定性和使用性能。
调质处理则是将淬火和高温回火结合起来,以获得高强度、高硬度和高韧性的综合性能。
总之,铸钢热处理是提高铸钢件使用性能和寿命的重要手段之一,通过合理的热处理方法和工艺参数选择,可以显著改善铸钢件的组织结构和性能,满足不同的使用要求。
锻造及锻后热处理工艺规范DOC

目录1.钢质自由锻件加热工艺规范2.钢锭(坯)加热规范若干概念3.加热操作守则4.锻造操作守则5.锻件锻后冷却规范6.锻件锻后炉冷工艺曲线7.锻件锻后热装炉工艺曲线8.冷锻件校直前加热、校直后(补焊后)回火工艺曲线9.锻件各钢种正火(或退火)及高温回火温度表10.锻件有效截面计算方法钢质自由锻件加热工艺规范一.范围:本规范规定了钢质自由锻件的通用加热技术条件。
本规范适用于碳素钢、合金钢、高合金钢、高温合金钢(铁基、镍基)的冷、热、半热钢锭(坯)的锻造前加热二.常用钢号分组和始、终锻加热温度范围:注1:始锻温度为锻前加热允许最高炉温,由于钢锭的铸态初生晶粒加热时过热倾向比同钢号钢坯小,故两者的锻前加热温度相差20℃~30℃;注2:根据产品的特性、锻件技术条件、变形量等因素,始锻温度可以适当调整;注3:本规范未列入的钢种,可按化学成分相近的钢号确定;注4:重要的、关键产品的、特殊材质的钢号,其加热工艺曲线由技术部编制;注5:几种不同的钢种,不同尺寸的钢锭(或坯料),在同一加热炉加热时,要以合金成分高的,尺寸大的钢锭(或坯料)为依据编制加热工艺曲线。
三.冷钢坯。
钢锭加热规范:钢锭(坯)加热规范若干概念1.钢锭(坯)入炉前的表面温度≥550℃的称为热钢锭,400~550℃的称为半热钢锭(坯),≤400℃的称为冷钢锭。
2.锻件半成品坯料的加热平均直径计算原则:δ -壁厚H- 高度或长度D- 外径1)实心圆类:当D>H时,按H计算;当D<H时,按D计算。
2)筒类锻坯:H>D 当H>δ时,按1.3δ计算。
3)空心盘(环)类:H<D当H>δ时,按δ计算;当H<δ时,按H计算。
3.为了避免锻件粗晶组织,最后一火的始锻温度可按其剩余锻造比(Y)确定:Y=1.3~1.6 最高加热温度1050℃Y<1.3 最高加热温度950℃4.不同钢种不同规格的坯料同炉加热时,装炉温度和升温速度均按较低的选用,保温时间按较长的选用。