热处理工艺规范(最新)
热处理工艺规范
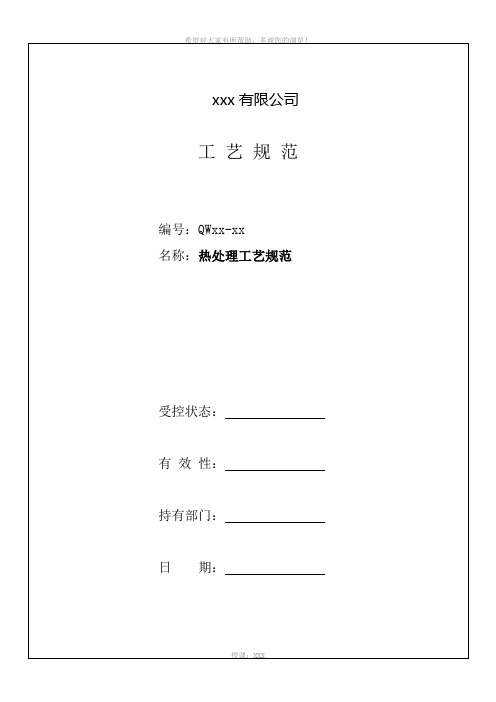
Ⅲ、Ⅳ、Ⅴ
允许温度偏差
±1℃
±3℃
5.1.5 高频淬火(感应热处理)加热电源及淬火机床:
5.1.5.1 感应加热电源输出功率及频率必须满足热处理要求,输出功率控制在±5%,或输出电压在±2.5%范围内。感应热处理机床和限时装置应满足工艺要求。
5.1.5.2 高频淬火机床精度要求如下表:
表5.1.5
5.3 仪表要求:
5.3.1 现场使用的控温和记录仪表等级应符合表5.1.1要求,检定周期按表5.1.3执行。
5.3.2 现场系统校验用的标准电位差计精度应不低于0.05级,分辨力不低于1μv,检定周期为6个月。
5.3.3 现场常用的热电偶技术要求,见下表:
表5.3.1
名 称
分度号
等级
使用温度
允许温度
(1)应向供货单位要求提供原材料质保书(包括生产厂家、牌号、规格、供货状态等)。
(2)若需要材料代用,必须向我司产品开发部办理材料代用手续。
(3)加强原材料管理,必须对原材料分类标识,防止混料,推荐使用前作火花鉴别等。
6.2 工艺参数控制:
严格按确定的《热处理作业检验指导书(或热处理工艺卡)》中具体工艺参数,包括热处理设备、装炉方式、装炉量、加热升温方式、加热温度、保温时间、冷却方式、冷却介质、冷却介质温度、渗剂种类、渗剂流量、感应加热温度、限时加热时间及电参数(阳极电压、阳极电流、槽路电压等);且按质量检验项目、标准与规范要求进行过程控制。
5.1.3 每台加热炉必须定期检测有效加热区,检测方法按GB/T9452和JB/T6049的规定,其保温精度应符合表5.1.2要求。应在明显位置悬挂带有有效加热区示意图的检验合格证。加热炉只能在有效加热区检验合格证规定的有效期内使用,检测周期见下表:
热处理淬火工艺规范

热处理车间淬火工艺规范一、调质1.1 调质定义为了达到产品的工艺硬度要求,得到回火索氏体,得到良好的强韧性,提高使用性能和寿命,因此曲轴和连杆产品需进行调质处理。
调质,即淬火加高温回火,以获得回火索氏体组织,主要用于中碳碳素结构钢或低合金结构钢以获得良好的综合机械性能。
1.1.1 淬火的定义淬火是将钢加热到临界温度Ac3 (亚共析钢)或Ac1 (过共析钢)以上温度,保温一段时间,使之全部或部分奥氏体化,然后以大于临界冷却速度的冷速快冷到Ms以下(或Ms附近等温)进行马氏体(或贝氏体)转变的热处理工艺。
通常也将铝合金、铜合金、钛合金、钢化玻璃等材料的固溶处理或带有快速冷却过程的热处理工艺也称为淬火。
1.1.2淬火的目的淬火的目的是使过冷奥氏体进行马氏体或贝氏体转变,得到马氏体或贝氏体组织,然后配合以不同温度的回火,以大幅提高钢的刚性、硬度、耐磨性、疲劳强度以及韧性等,从而满足各种机械零件和工具的不同使用要求。
也可以通过淬火满足某些特种钢材的铁磁性、耐蚀性等特殊的物理、化学性能。
1.1.3回火的定义回火是工件淬硬后加热到Ac1 (加热时珠光体向奥氏体转变的开始温度)以下的某一温度,保温一定时间,然后冷却到室温的热处理工艺。
按回火温度范围,回火可分为低温回火、中温回火和高温回火。
4.1.1低温回火:工件在150~250C进行的回火。
目的是保持淬火工件高的硬度和耐磨性,降低淬火残留应力和脆性,回火后得到回火马氏体,指淬火马氏体低温回火时得到的组织。
应用范围:主要应用于各类高碳钢的工具、刃具、量具、模具、滚动轴承、渗碳及表面淬火的零件等。
4.1.2中温回火:工件在350〜500 C之间进行的回火。
目的是得到较高的弹性和屈服点,适当的韧性。
回火后得到回火屈氏体,指马氏体回火时形成的铁素体基体内分布着极其细小球状碳化物(或渗碳体)的复相组织。
应用范围:主要用于弹簧、发条、锻模、冲击工具等。
4.1.3高温回火:工件在500~650C以上进行的回火。
热处理工艺规范[1]
![热处理工艺规范[1]](https://img.taocdn.com/s3/m/da4ed32d8762caaedc33d477.png)
21
ZG20Mn(ZG20SiMn)
900~920
≥12
风冷
550~610
≥10
炉冷
530~590
≥8
22
ZG16Mn
880~920
≥12
风冷
590~610
≥10
炉冷
570~590
≥8
23
ZG35Cr1Mo(ZG35CrMo)
890~910
≥12
风冷
580~600
≥10
炉冷
560~580
≥8
24
660-680
≥8
27
ZG15Cr1Mo
940-960
≥12
风冷
680-700
≥10
炉冷
660-680
≥8
28
G17CrMo5-5
940-960
≥12
风冷
680-700
≥10
炉冷
660-680
≥8
29
ZG25MnNi
880~900
≥10
炉冷
30
ZG25CrNiMo
880~930
≥12
风冷
880~900
≥8
11
WC6
940-960
≥12
660-680
≥8
12
ZG17CrMo1V
980-1000
≥16
雾冷
940-960
≥16
雾冷
740-760
≥10
炉冷
700-720
≥10
13
GS-17CrMoV511(G17CrMoV5-10)
980-1000
≥16
雾冷
热处理工艺规范

➢ 本规范规定了本公司常用的金属的热处理 设备、工艺与质量检验方法
1
热处理工艺规范
目录
➢ 前言 1 规范范围 2 规范性引用文件 3 常用热处理方式定义 4 工艺分类代号 5 工件举例 6 热处理设备 7 工作要求 8 规范 9 热处理后工件的质量检验
2
热处理工艺规范
前言
本标准由技术部提出。 本标准由技术部起草。 本标准主要起草人:xx 本标准审核人:xx 本标准批准人:xx 本标准由技术部部归口并负责解释。 本标准于2019年10月首次发布,于2020年3月第一次修订。
14
热处理工艺规范
6 热处理设备 • 6.1 加热炉有效加热区实际温度偏差值(指炉罐内)
不应超过±20℃。 • 6.2 加热炉的每个加热区应配有温度测定及温度控制
自动记录装置。 • 6.3 加热炉的维护保养必须按制订的制度进行,并妥
善保管有关记录。
15
热处理工艺规范
7 工作要求 • 7.1 检查设备、仪表是否正常,并应事先将炉膛清理
干净。 • 7.2 核对材料与图样是否相符,了解零件的技术要求
和工艺规定。 • 7.3 选择好合适的工夹具,并考虑好装出炉的方法。
16
热处理工艺规范 8 规范 8.1 工艺的制定。应根据工件的特征(材料的牌号、处 理前的状态及形状、尺寸等)、热处理 目的、批量、热处理设备等具体条件来制定合理的热处 理工艺。 8.2 热处理工艺曲线见图1、图2
• 8.4 冷却时应以适当的速度,使工件各部分均匀冷 却。
• 8.5 如采用空冷,应在空气中散开冷却,不允许堆 放或置于潮湿的地上冷却。
20
热处理工艺规范 • 8.6 作为热处理后的辅助工序,清除工件的氧化皮
热处理(调质)工艺规范

热处理工艺规范1 目的本规范适用于本厂钢制零件在周期作业加热炉中的调质、固熔工序。
2 准备工作2.1检查设备及仪表是否正常。
2.2检查零件上的材料是否符合图样要求。
2.3检查零件的尺寸是否符合图样及工艺文件的规定。
2.3.1调质件最好先经粗加工,断面大于100mm 的零件,当有内孔时,应钻孔后再调质,并且防止出现尖角。
2.3.2调质件的加工余量应大于允许的变形量。
2.4熟悉工艺要求,根据零件的毛坯重量、开头确定吊挂形式,吊挂部分可利用零件本身结构,也可在零件上另加。
2.5大型零件调质时必须检查所需的辅助冷却装置,当确认使用可靠后方可装炉。
2.6不同淬火温度的调质件,不得同炉处理,同炉处理件的有效厚度应相近。
3 工艺规范3.1 ASTM A350 LF2调质处理规范见表1。
3.1.2机械性能参数:MPa b 655485-=σ MPa 250≥s σ 22%≥δ 30%≥Φ3.1.3 LF2低温冲击韧性K A 要求:Ⅰ级 试验温度在-45.6℃ 三个试样平均值为K A ≥20J三个试样中一个试样冲击值为K A ≥16JⅡ级 试验温度在-18℃ 三个试样平均值为K A ≥27J三个试样中一个试样冲击值为K A ≥20J3.2 ASTM A182 F316、F321钢3.2.1 热处理工艺:3.2.2 机械性能参数:MPa b 515=σ MPa 205≥s σ 30%≥δ 50%≥Φ3.3 淬火冷却方法3.3.1调质件采用的淬火介质一般为水或油。
3.3.2形状简单、断面厚度不足100mm 的零件在水或油中冷却,终冷温度不予限制,以淬硬为原则。
3.3.3形状复杂、断面厚度大于100mm 的零件在淬火介质中冷至表面温度为150-200℃时取出空冷。
3.3.4采用水淬油冷的零件,水冷时间按每(3-5)mm 以1s 计算,水淬空冷的零件、水冷时间,当有效厚度小于30毫米的以S/2mm 计算,有效厚度大于30mm 的以S/1mm 计算的。
(完整)热处理工艺守则

一、热处理代号和材料标注方法(一)热处理代号1. 适用于结构钢和铸件代号:0—自然状态1—正火(或正火+回火)2—退火3—精锻+回火(如精锻或精辊叶片在精锻后只需高温回火)4—淬硬5—调质6—化学热处理(渗碳或氮化)7—除应力(包括活塞环定型处理)9—表面淬火或局部淬火2.适用铸造有色金属和奥氏体钢的代号:0—原始状态1—再结晶退火T—除应力退火T1-人工时效T4—淬火(固溶处理)T5—淬火和不完全时效T6-淬火和完全时效(固溶处理和完全时效到最高硬度)3.压力加工有色金属代号:0—原始状态M—退火C-淬火CZ—淬火和自然时效CS-淬火和人工时效(二)材料的标注方法:1.零件的材料或毛坯(包括铸锻件)如不作任何处理,也不作机械性能检查,则只标材料牌号(其热处理代号“0”在图纸上不标注)如:A3,20,35,ZQSn6—6-3。
2.零件的材料或毛坯在热处理后,不作硬度及机械性能检查者则只标注材料牌号和热处理代号:如:45-1,若有几种热处理,可用热处理代号按工艺路线顺序逐项填写:如:15CrMoA-1+7。
3.有些材料的技术条件,有几种检查组别,但强度等级只有一种或可按材料截面尺寸来决定强度等级,只注明材料牌号,热处理代号和检查组别:如:45—5(Ⅱ) 35CrMoA—5(Ⅱ)4.有些材料的技术条件,有几种组别,在同一热处理状态中有不同的强度等级,则注明材料牌号、热处理代号强度等级和检查组别,不需要规定检查组别时,检查组别可省略。
25Cr2MoVA-5 25Cr2MoVA-5如:735—Ⅲ 7355。
有些零件或者是比较重要或者是技术要求比较复杂,用上述标注方法不能说明全部要求者,则应注明标准号,在同一热处理状态中有不同的强度级别时,还应注明强度级别。
35CrMoA-5 35CrMoA-5如:Q/CCF M 3003-2003 590×Q/CCF M 3003—20036。
大锻件如叶轮、铸造轴、整体转子等的材料标注方法钢号锻件级别×标准编号7。
不锈钢管热处理工艺规范
不锈钢管热处理工艺规范1. 引言本文档旨在规范不锈钢管热处理工艺,确保产品质量和工艺稳定性。
热处理是不锈钢管生产过程中的重要环节,对材料的性能和组织结构具有重要影响。
遵循本规范可以提高产品的强度、耐腐蚀性和使用寿命。
2. 工艺流程2.1 进料检查在进行热处理前,需要对进料的不锈钢管进行检查。
主要检查项包括外观质量、尺寸精度和化学成分。
确保进料材料符合要求,否则应及时通知原材料供应商。
2.2 预处理在进行热处理之前,要对不锈钢管进行预处理,以去除表面污染物和氧化层。
常用的方法包括酸洗、喷丸和电解抛光等。
2.3 加热将预处理后的不锈钢管放入炉内进行加热。
加热过程中,应根据不同材质和要求确定合适的加热温度和时间。
要注意避免温度过高或过低造成不锈钢管的形变或组织结构异常。
2.4 保温加热完成后,要进行一定时间的保温处理。
保温时间的长短应根据不锈钢管的厚度和材质进行科学确定,以保证组织结构的均匀性和稳定性。
2.5 冷却保温结束后,需要进行冷却处理。
冷却的方式可以采用自然冷却或人工冷却,具体根据材料的要求进行选择。
2.6 检验在完成热处理后,对不锈钢管进行检验。
主要检查项包括尺寸精度、物理性能和化学成分。
确保产品符合相关标准和要求。
3. 工艺控制与质量保证3.1 温度控制在加热和保温过程中,要严格控制温度。
采用合适的温度控制设备和技术手段,确保温度的准确性和稳定性。
3.2 时间控制加热、保温和冷却的时间都需要进行控制。
根据不同材质和要求确定合适的时间参数,以保证工艺的规范性和产品的质量。
3.3 检验控制热处理过程中的检验工作要进行规范控制。
采用合适的检测设备和方法,进行尺寸、物理性能和化学成分等方面的检验,确保产品质量符合要求。
3.4 记录与报告热处理过程应进行全程记录。
记录包括进料检查、工艺参数、检验结果等内容。
并及时生成报告,以备后续追溯和分析。
4. 安全与环保4.1 安全措施在进行热处理工艺时,要严格遵守安全操作规程和要求。
(完整)热处理加工工艺规范
热处理加工工艺规范1范围本规范规定了热处理的工艺规则,适用于本公司的热处理加工。
2准备工作2.1根据加工路线单核对工件数量,检查材料是否符合要求,并根据图样了解热处理的种类。
2。
2检查工件是否有碰撞伤痕、裂纹等缺陷。
2。
3检查炉子及炉温仪表使用情况是否正常2.4严禁带电进出炉操作,工件离电热体不宜太远,以防局部过热。
一般工件离炉壁应大于100mm,离炉顶大于200mm。
2.5形状复杂或细长轴等工件,在堆放时要按有关操作要求装入炉内,严禁悬空堆放.3退火3。
1对于45#、40Cr钢件分别加热到800-840℃,830—850℃,保温2—3小时,然后以小于100℃/H的速度缓慢冷却至500—600℃出炉空冷.3.2对于T7-T9,T10-T12钢件分别加热到740—760℃,750-770℃,保温2—4小时,然后以小于200℃/H的速度缓慢冷却至500—600℃出炉空冷。
3.3对于合金钢等特殊材料,按有热处理工艺学有关技术资料要求操作。
3.4一般件可不预热低温进炉,当温度升到500—600℃时,应保温1—2小时后再继续升温. 3.5出炉时对于形状复杂或细长工件,宜用钳子或其他夹具垂直或水平放置在适当地方。
4正火4.1通常用于正火的材料为含碳量不超过0。
5%的碳素钢、低合金钢的锻件、铸钢件。
4。
2对于Q235、20#、Q345等材料加热到880℃-930℃,保温1-3小时后出炉空冷。
4。
3对于45#、40Cr钢分别加热至830-880℃,850-890℃,保温1—3小时出炉空冷。
4.4保温时间可根据工件的有效厚度决定,参考下表:4.5正火规范相同的零件,可在同炉处理,但截面有效厚度必须相近。
4。
6不同尺寸的零件在同炉处理中,若同时出炉时,其保温时间就按最大截面所需的保温时间计算,但允许小件到达其本身尺寸所需保温时间后单独出炉.4.7多件装炉时工件断面尺寸小于100mm者,其间隙应大于50mm.技术要求较高的零件严禁小件外面套大件。
热处理工艺规范
淬火加热 1060~1070oC
6)不同类型的零件在淬火冷却过程中应遵守下列原则:
轴、套筒、圆环类零件:应沿轴心方向垂直进入冷却剂,并在冷却剂中上下窜动。
垫圈类零件:应径向垂直进入冷却剂。 长板类零件:选择横向侧面进入冷却剂为好。
有盲孔凹面的零件:盲孔凹面向上进入冷却剂。
1060 ~1070 风冷
510~ 520
56~ 60
550~ 560
48~ 52
200~ 220
58~ 62
1020 ~1040
油
500~ 520 520~ 530 560~ 580
55~ 58 54~ 56 44~ 48
820~ 840
油
19空淬火炉淬火风冷,回 火两次。
核对温度仪表,正确执行工艺;改 变或搅拌冷却介质;严格检查原材 料,改进预先热处理; 采取保护加热。
加热温度过高;原始晶粒太大。
严格控制温度;进行预先热处理。
变形与 开裂
原材料组织不均匀, 有冶炼金属缺陷; 加热 温度过高; 冷却太快或不均; 零件的结构形状 复杂; 二次淬火前未经正火或退火处理; 未及 时回火或回火不充分。 合金工具钢锻件, 锻造 比小:材质内碳化物严重,锻打时没击碎。
第4 页 共6 页
四川华林设备有限公司
却不允许堆放或置于潮湿的地上冷却,大件或要求硬度高的零件方可在流动空气中或其它介
质中冷却。
3.加热设备:退火、正火主要采用箱式炉,必要时可选用真空炉。
4.操作方法
1)零件装炉时,必须放置在预先确定的有效加热区内,装置量、装炉方式及堆放形式的
确定应以保正零件均匀加热和冷却,且不造成有害缺陷的原则;装箱退火时,箱间距离应大
热处理工艺
使二次渗碳体或珠光体中的渗碳体球化,以降低硬度,改善切削加工性能。
蔓延退火
熔点以下100~200℃
减少化学成份和组织的不匀称
去应力退火
Ac1线以下(普通为500~600℃)
消除工件中残留内应力
正火(空冷)
加热温度
组织
目的
亚共析钢
Ac3+30~50℃
F+S
(1)作为总算热处理:细化晶粒、匀称组织
(2)作为预先热处理:对结构较大的合金结构钢前,淬火或调质前常举行正火,消除魏氏组织和带状组织,并获得细小而匀称的组织。
(3)改善切削加工性能:调节硬度
过共析钢
Accm+30~50℃
S+ Fe3CⅡ
热处理工艺
组织
目的
彻低退火
(重结晶退火)
亚共析钢:Ac3+20 Nhomakorabea30℃F+P
组织匀称化和细化,得到临近平衡状态的组织,以降低硬度,改善切削加工性能。因为冷却速度缓慢,还可消除内应力。
等温退火
亚共析钢:高于Ac3
过共析钢:高于Ac1
快冷到A1~550℃之间,保温,然后再缓慢冷却。
同上
球化退火
过共析钢:高于Ac1
- 1、下载文档前请自行甄别文档内容的完整性,平台不提供额外的编辑、内容补充、找答案等附加服务。
- 2、"仅部分预览"的文档,不可在线预览部分如存在完整性等问题,可反馈申请退款(可完整预览的文档不适用该条件!)。
- 3、如文档侵犯您的权益,请联系客服反馈,我们会尽快为您处理(人工客服工作时间:9:00-18:30)。
华尔泰经贸有限公司铸钢件产品热处理艺规范
随着铸造件产品种类增多,对外业务增大,方便更好的管理铸造件产品,特制定本规定,要求各部门严格按照规定执行。
1目的:
为确保铸钢产品的热处理质量,使其达到国家标准规定的力学性能指标,以满足顾客的使用要求,特制定本热处理工艺规范。
2范围
本规范适用于本公司生产的各种精铸、砂铸产品的热处理,材质为各种低碳钢、中碳钢、低合金钢、中合金钢、高合金钢、铸铁及有色合金。
3术语
3.1退火:指将铸钢产品加热到规定的温度范围,经保温一段时间后,
降温出炉的操作工艺。
3.2正火:指将铸钢产品加热到规定的温度范围,经保温一段时间后,
从炉中取出,在空气中冷却下来的操作工艺。
3.3淬火:指将铸钢产品加热到规定的温度范围,经保温一段时间后,
快速冷却的操作工艺。
3.4回火:指将淬火后的铸钢产品加热到规定的温度范围,经保温一
段时间后出炉,冷却到室温的操作工艺。
3.5调质:淬火+回火
4 职责
4.1热处理操作工艺由公司技术部门负责制订。
4.2热处理操作工艺由生产部门负责实施。
4.3热处理操作者负责教填写热处理记录,并将自动记录曲线转换到
热处理记录上。
4.4检验员负责热处理试样的力学性能检测工作,负责力学性能检测
结论的记录以及其它待检试样的管理。
5 工作程序
5.1每次装炉前应对设备进行检查,把炉底板上的氧化渣清除干净,
错位炉底板应将其复位后再装,四周应留有足够的间隙,轻拿轻放,装炉应结实,摆放合理。
5.2装炉时大铸件产品放在下面,对易产生热处理变形的铸件,必须
作好防变形或反变形处理,力学性能试样应装在高温区,对特别小的铸件采用铁桶或其它框类工装集中盛放。
5.3炉车上的铸钢件入炉时,应缓慢推进,仔细观察铸钢件是否与炉
壁碰撞,关闭炉门,通电后应经常观察炉内工作状况。
5.4作好铸件产品后续热处理的准备工作,严格控制出炉温度,对水
淬铸件应控制入水时间,水池应有足够水量,以保证淬火质量。
5.5作业计划应填写同炉热处理铸件产品的材质、名称、规格、数量、
时间等要素,热处理园盘记录纸可多次使用,但每处理一次都必须与热处理工艺卡上的记录曲线保持一致。
6 不合格品的处置
6.1热处理试样检验不合格,应及时通知相关部门。
6.2技术部门负责对不合格品的处置。
7 附表
7.1碳钢及低合金钢铸件正火、退火加热温度表7.2碳钢及低合金钢铸件退火工艺
7.3铸钢件直接调质工艺
7.4铸钢件经预备热处理后的调质工艺
7.5低合金铸钢件正火、回火工艺
7.6铸钢件淬火温度,回火温度
7.7补焊后铸件热处理规范
7.8气割补焊后退火规范
7.9高锰钢铸件的水韧处理工艺
附表:
7.1碳钢及低合金钢铸件正火、退火加热温度表
7.2碳钢及低合金钢铸件退火工艺
7.3铸钢件直接调质工艺
7.4铸钢件经预备热处理后的调质工艺
注:1、截面小于100mm,形状简单的碳素铸钢件可采用水淬;形状复杂及截面大于100mm 者,采用水淬油冷。
2、合金钢铸件采用油冷。
4、冷却时间计算公式:
油冷:t=9~12s/mm×δ
水冷:t=1.5~2s/mm×δ
水淬油冷:水T=0.8~1s/mm×δ
油 T=7~9s/mm×δ
式中:T——冷却时间s;δ有效截面厚度mm
7.5低合金铸钢件正火、回火工艺
7.6-1铸钢件淬火温度
7.6-2铸钢件回火温度
7.7补焊后铸件热处理规范
7.8气割补焊后退火规范
碳钢铸件的热处理方法有全退火、正火及正火加回火。
7.9高锰钢铸件的水韧处理
高锰钢铸件的热处理规范
注:
1.从开炉门到工件淬入水中的时间不得大于30s。
2.工件全部入水后,在水池中上下左右摆动。
3.水温保持在30℃以下,淬火后最高水温不超过60℃。