大型铸钢件工艺
大型厚壁铸钢件托轮热处理工艺
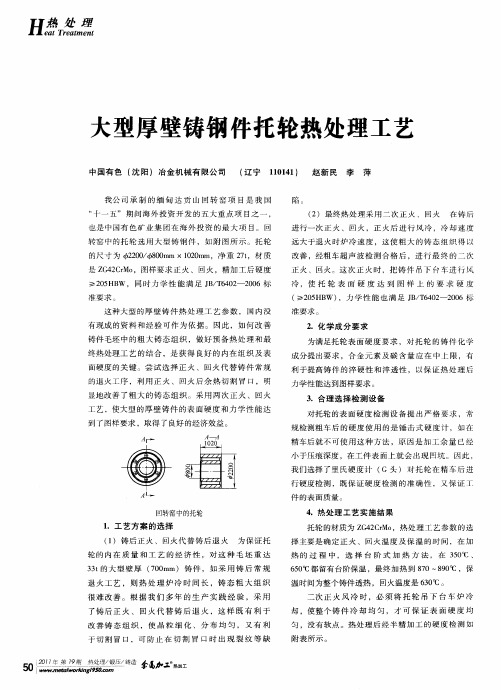
Tr a m e e t nt
大型厚壁铸钢件托轮热处理工艺
中 国 有 色 ( 阳 ) 冶 金 机 械 有 限公 司 沈 ( 宁 辽 10 4 ) 1 11 赵新 民 李 萍
我公 司 承 制 的 缅 甸 达 贡 山 回转 窑 项 目是 我 国 “ 一 五” 期 间海 外 投 资 开 发 的 五大 重 点 项 目之 一 , 十 也 是 中国有 色矿 业 集 团在 海 外 投 资 的最 大 项 目。 回
行硬 度检 测 ,既 保 证 硬 度检 测 的准 确性 ,又 保 证 丁
L' .
件 的表面质 量 。
回转窑 中的托轮
4 .热 处 理 工 艺 实 施 结 果
托 轮 的材质 为 Z 4 C Mo G 2 r ,热 处 理工 艺 参数 的选
1 .工 艺 方 案 的 选 择
( ) 铸后 正 火 、回火 代 替 铸后 退火 1 为保 证 托
准要 求 。
这种 大 型 的厚 壁 铸 件 热 处 理 工 艺 参数 , 国 内没
有 现成 的 资料 和 经 验 可 作 为 依 据 。 因 此 ,如 何 改 善
铸 件毛坯 中 的粗 大 铸 态 组 织 ,做 好 预 备 热 处 理 和 最
2 .化 学 成 分 要 求 为满 足托 轮 表 面 硬 度要 求 ,对 托 轮 的铸 件 化 学
转 窑 中的 托 轮选 用 大 型 铸 钢 件 ,如 附 图 所 示 。托 轮
陷。
( ) 最终热 处 理 采 用 二 次 正火 、 回火 在铸 后 2 进 行一 次 正火 、 回火 ,正 火 后 进 行 风 冷 ,冷却 速 度 远 大于退 火 时 炉 冷 速 度 ,这 使 粗 大 的铸 态组 织 得 以
铸钢件生产工艺要求及质量标准
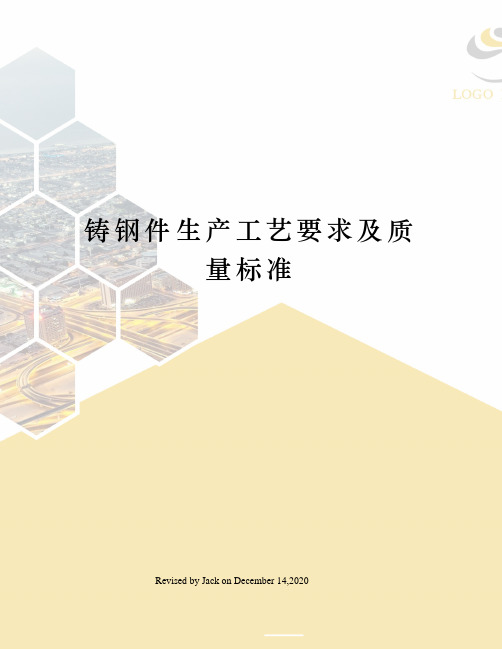
铸钢件生产工艺要求及质量标准Revised by Jack on December 14,2020铸钢件生产工艺要求及质量标准一、混砂工艺标准(一)材料要求:1、造型砂:符合GB9442-88 、JB435-63细粒砂要求,一般选用二氧化硅含量较高的天然砂或石英砂,原砂粒度根据铸件大小及壁厚确定,原砂的含泥质量分数应小于2%,原砂中的水份必须严格控制,且一般应进行烘干。
2、水玻璃:水玻璃模应根据铸件大小来确定。
(1)小砂型(芯)为加速硬化采用选用M=—的高模数水玻璃。
(2)中型砂型(芯)可选用M=—的水玻璃。
(3)生产周期长的大型砂型(芯)选用M=—的低模数水玻璃。
(二)混制比例(质量分数%)造型砂/水玻璃=100:6~8(三)混制时间:一般情况下混制5分钟,室温或水玻璃密度较大时可适当延长混砂时间。
(四)混制后要求:混制好的造型砂要求无块状或团状,流动性较好。
二、造型工艺要点:(一)基本原则:1、质量要求高的面或主要加工面应放在下面。
2、大平面应放在下面。
3、薄壁部分应放在下面。
4、厚大部分应放在上面。
5、应尽量减少砂芯的数量。
6、应尽量采用平直的分型面。
(二)基本要求:1、木模:要求轮廓完整,无裂纹、无破损、无残缺,表面光洁,尺寸符合铸造工艺图纸要求,并经常进行尺寸校验。
2、砂箱:砂箱的尺寸大小应根据木模规格确定,大、中型砂箱应焊接箱筋。
3、浇注系统:根据铸件的结构特点的工艺要求,选择适宜的浇注系统,通常采用顶注式、底注式。
(1)浇注系统设置基本原则:浇口、冒口安放位置合理,大小适宜不妨碍铸件收缩,便于排气、落砂和清理,应使铸型尺寸尽量减少,简化造型操作,节省型砂用量和降低劳动强度。
(2)内浇道位置的注意事项。
1)内浇道不应设在铸件重要部位。
2)应使金属液流至型腔各部位的距离最短。
3)应不使金属液正面冲击铸型和砂芯。
4)应使金属液能均匀分散,快速地充满型腔。
5)不要正对铸型中的冷铁和芯撑。
4、冒口(1)冒口设置基本原则:1)根据铸件的结构和工艺要求正确选择冒口的形状、大小和安放位置。
大型铸钢件中频淬火工艺试验

关键词 : 铸钢 ; 中频 淬火 ; 硬度 ; 化层 深度 ; 硬 裂纹
中图 分类 号 :G 5.4T 129T 133 T 16 3 ;G 6 .;H 3.3 文 献标 志码 : B 文章 编号 : 0 — 722 1)9— 05 0 1 0 36 (000 03 — 2 0
表2 1 一6试样 中频淬 火工艺参数
试 样 工 件 转 速 淬火 温度 编 号 / m ・ n 1 / ( m miI ) ℃
1 2 l0 3 lO 3 9 0 0 9 0 2
频 率 ,z H
功 率 / W k
2 5 3 0
淬火 介质
裂纹 。
收稿 日期 :00— 4—1 21 0 2
从表 5可 以看 出 , 过 着 色 探 伤 检 验 , 8 , 经 7 ,
9试 样 中频淬 火后 均未 发 现 淬 火裂 纹 , 是 , 于 但 由
与锻 件 相 比 , 件 内部 存 在 着 大 量 的气 孔 、 铸
砂眼, 而且 还 存在 着 比锻 件严 重 得 多 的疏 松 等 铸 造 缺陷 , 对 其 进 行 中频 淬 火 加 热 过 程 中 , 些 在 这 气孔 和 严 重 的疏 松 部 位 将 会 形 成 局 部 涡 流 , 使 致 缺 陷处 温度 过高 , 易 导 致 淬 火 裂 纹 。 为 了解 决 极
! 量
= !
轴承
2 1 年9 00 期
CN41— 11 /TH Be  ̄n 48 a g 201 , 0 No. 9
大 型铸 钢 件 中频 淬 火 工 艺 试 验
王 明礼 , 小 东 , 翠 丽 , 丽 霞 , 运玲 孙 陈 王 孙
( 阳 L C轴 承 有 限公 司 技 术 中心 , 南 洛 Y 河 洛阳 4 13 ) 7 09
大型铸钢件的生产流程

大型铸钢件的生产流程一、原材料准备大型铸钢件的生产流程首先需要准备合适的原材料,一般采用高质量的铸造钢材作为基础材料。
这些原材料需要经过严格的检验和筛选,确保其质量符合要求。
二、模具制造接下来,根据大型铸钢件的设计图纸,制造适用于铸造的模具。
模具的制造需要考虑到铸件的形状、尺寸和结构特点,同时还要保证模具的材质和加工工艺能够满足铸造的需求。
三、熔炼和浇注在模具制造完成后,进行熔炼和浇注工艺。
首先,将预先准备好的铸造钢材放入炉内进行熔炼,通过高温加热使其达到熔点。
然后,将熔化的钢液倒入模具中,待其冷却凝固后,得到初步成型的铸钢件。
四、去除模具和修整当铸钢件冷却后,需要将模具从铸钢件上移除。
这一步骤通常需要使用专门的工具和设备,以确保模具的完整性和铸钢件的表面质量。
同时,还需要对铸钢件进行修整,去除可能存在的毛刺、气孔和缺陷,使其达到设计要求。
五、热处理和机械加工铸钢件经过修整后,需要进行热处理和机械加工。
热处理的目的是改变铸钢件的组织结构和性能,提高其硬度和强度。
机械加工则是根据铸钢件的具体要求,进行切削、钻孔、铣削等工艺,使其达到精密加工的要求。
六、表面处理为了提高铸钢件的外观质量和耐腐蚀性能,需要对其进行表面处理。
常见的表面处理方法包括喷砂、喷涂、电镀等,通过这些方法可以使铸钢件表面光滑、均匀,并且具有一定的防腐蚀能力。
七、质量检验在大型铸钢件的生产流程中,质量检验是非常重要的环节。
通过对铸钢件的尺寸、外观、物理性能等方面进行严格检测,确保其质量符合设计要求和客户需求。
常用的检验方法包括超声波检测、磁粉检测、硬度测试等。
八、包装和运输对已经通过质量检验的铸钢件进行包装和运输。
为了防止铸钢件在运输过程中受到损坏,通常会采用合适的包装材料进行包装,同时选择合适的运输方式和工具,确保铸钢件安全到达目的地。
总结大型铸钢件的生产流程包括原材料准备、模具制造、熔炼和浇注、去除模具和修整、热处理和机械加工、表面处理、质量检验以及包装和运输等环节。
大型铸钢件铸造工艺技术

大型铸钢件铸造工艺技术大型铸件生产周期长、工序复杂,一般要经历众多工序(如图2—1所示),合理设置其铸造过程中各项工艺是决定铸件最终成功铸造的关键要素。
图2—1大型铸钢件铸造工艺流程2.1大型铸钢件造型用砂铸钢件尤其是大型铸钢件大都采用自硬砂地面造型。
大型铸钢件通常具有厚大断面和高的金属静压头、浇注时间较长,加上铸件凝固过程中金属液体与砂型之间的热作用、机械作用、化学反应非常强烈;铸件表面,尤其在砂芯或砂型凹陷及转角处极易产生金属渗透粘砂,易造成铸件尺寸稳定性差和表面缺陷。
因而大型铸钢件对砂型的高温力学性能、型砂材料的抗粘砂能力要求非常高。
目前国内重机行业用于大型铸钢件的造型用砂主要有水玻璃砂(C02吹气硬化和有机醋自硬化)、树脂自硬砂〔峡喃树脂自硬砂、碱酚醛树脂自硬砂)国内一些主要大型铸件生产企业已逐步完成使用自硬砂铸造工艺的技术改造。
大型铸钢件的面砂一般采用铬铁矿砂等特种砂,这些原砂比硅砂的价格高出很多。
因此,对于旧砂再生系统中铬铁矿砂与石英砂的分离技术也是一项合理利用资源及降低成本的关键性技术。
2.2 铬铁矿砂在造型中的应用2.2.1铬铁矿呋喃树脂砂面砂应用实例(见表2—1)222 铬铁矿砂成份及选择铬铁矿砂属于铬尖晶石。
一般以(FeMg 0・(CrAIFe)2Q形式存在,其中杂质主要为CaO MnQ SiO2、TQ2等金属氧化物和碳酸盐化合物。
铬铁矿砂的比重为(4.4〜4.5 )3 3kg/cm,堆积比重为(2.0〜2.7 )kg/cm ,耐火度为2000土25C,熔融触点2040C。
铬铁矿砂的选择主要依据需要配制的型(芯)砂后的工艺参数、铸件质量以及旧砂再生回收率的高低来不断摸索确定。
铬铁矿砂的化学成分及质量分数(%见表2—1。
表2—1 铬铁矿砂的化学成分及质量分数(%2.2.2.1 酸耗值我们在采用呋喃树脂砂工艺时其催(固)化剂为磺酸、苯磺酸之类酸性固化剂硬化,要求原砂呈中性,如存在诸如滑石粉的碱性化合物,固化剂的消耗必然要加大,从而砂型固化慢甚至不能硬化。
铸钢铸造工艺
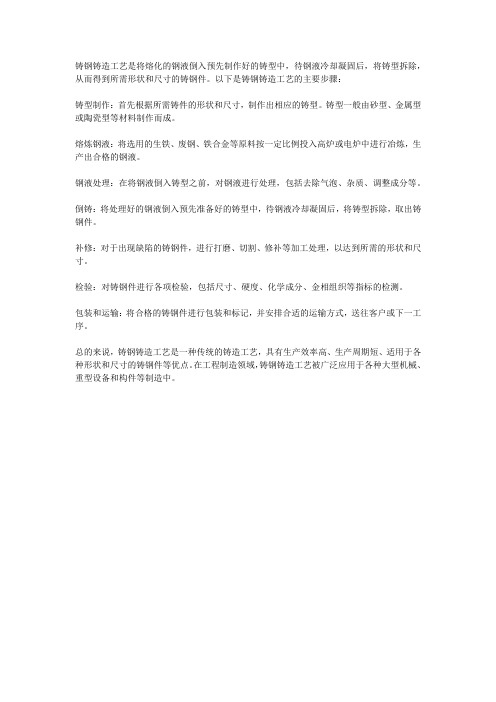
铸钢铸造工艺是将熔化的钢液倒入预先制作好的铸型中,待钢液冷却凝固后,将铸型拆除,从而得到所需形状和尺寸的铸钢件。
以下是铸钢铸造工艺的主要步骤:
铸型制作:首先根据所需铸件的形状和尺寸,制作出相应的铸型。
铸型一般由砂型、金属型或陶瓷型等材料制作而成。
熔炼钢液:将选用的生铁、废钢、铁合金等原料按一定比例投入高炉或电炉中进行冶炼,生产出合格的钢液。
钢液处理:在将钢液倒入铸型之前,对钢液进行处理,包括去除气泡、杂质、调整成分等。
倒铸:将处理好的钢液倒入预先准备好的铸型中,待钢液冷却凝固后,将铸型拆除,取出铸钢件。
补修:对于出现缺陷的铸钢件,进行打磨、切割、修补等加工处理,以达到所需的形状和尺寸。
检验:对铸钢件进行各项检验,包括尺寸、硬度、化学成分、金相组织等指标的检测。
包装和运输:将合格的铸钢件进行包装和标记,并安排合适的运输方式,送往客户或下一工序。
总的来说,铸钢铸造工艺是一种传统的铸造工艺,具有生产效率高、生产周期短、适用于各种形状和尺寸的铸钢件等优点。
在工程制造领域,铸钢铸造工艺被广泛应用于各种大型机械、重型设备和构件等制造中。
呋喃树脂自硬砂生产大型铸钢件工艺控制要点
2 1 年第 3期 01 21 0 1年 6月
・
铸
造
设
备
与 工
艺
F U D Y E UP N N E H O O Y O N R Q IME TA DT C N L G
铸 造 工艺 ・
呋喃树脂 自硬砂 生产大型铸钢件 工艺控制要点
于洪岩 , 俊珍 。 周
(. 1 天津市天重江天重工有限公 司, 天津 300 ;. 04 02西北工业集 团有限公司, 陕西 西安 704 ) 10 3
【.ini Taz ogJ nt nHev n ut O , T Ta i 04 0 C ia 1 a n i h n i gi T j n a a ayId syC . D,in n3 0 0 ,hn ; r L j
2Notw s d sr ru O, D, a h n i 0 4 , hn . r e tn u t gop C . h i y LT Xin S a x 0 3 C ia) 71
1 造型 用原辅 材 料的合 理控 制
11 原 砂 的 选择 .
高, 劳动强度低 , 尤其是铸型( ) 芯 溃散性好 , 铸件清 砂容易 , 旧砂通过再生可反复 回用 , 再生率在 9% 0 以上 , 且再 生后 的旧砂性能与新砂相 似 , 有些性能 指标甚至优于新砂 , 既可作背砂 , 也可作面砂 。 采用 呋喃树脂 自硬砂工艺生产铸钢件时 , 由于呋喃树脂 自硬砂发气量大且迅速 、 铸型导热性差 、 高温强度 高、 退让性差 , 造成铸钢件质量难以控制 , 表现在 : 易产生侵入性 的皮下气孔 ;铸钢件的热裂倾 向性 大; 浇注后砂型的导热性差 , 不利于形成铸件的顺 序凝 固。但是 , 只要通过对造型原辅材料进行科学 合理的控制 , 采用符合呋喃树脂 自硬砂生产要求的 铸造工艺方法 , 并严格控制生产操作过程 , 呋喃树
铸钢件生产工艺要求及质量标准
铸钢件生产工艺要求及质量标准一、混砂工艺标准(一)材料要求:1、造型砂:符合GB9442-88 、JB435-63细粒砂要求,一般选用二氧化硅含量较高的天然砂或石英砂,原砂粒度根据铸件大小及壁厚确定,原砂的含泥质量分数应小于2%,原砂中的水份必须严格控制,且一般应进行烘干。
2、水玻璃:水玻璃模应根据铸件大小来确定。
(1)小砂型(芯)为加速硬化采用选用M=2.7—3.2的高模数水玻璃。
(2)中型砂型(芯)可选用M=2.3—2.6的水玻璃。
(3)生产周期长的大型砂型(芯)选用M=2.0—2.2的低模数水玻璃。
(二)混制比例(质量分数%)造型砂/水玻璃=100:6~8(三)混制时间:一般情况下混制5分钟,室温或水玻璃密度较大时可适当延长混砂时间。
(四)混制后要求:混制好的造型砂要求无块状或团状,流动性较好。
二、造型工艺要点:(一)基本原则:1、质量要求高的面或主要加工面应放在下面。
2、大平面应放在下面。
3、薄壁部分应放在下面。
4、厚大部分应放在上面。
5、应尽量减少砂芯的数量。
6、应尽量采用平直的分型面。
(二)基本要求:1、木模:要求轮廓完整,无裂纹、无破损、无残缺,表面光洁,尺寸符合铸造工艺图纸要求,并经常进行尺寸校验。
2、砂箱:砂箱的尺寸大小应根据木模规格确定,大、中型砂箱应焊接箱筋。
3、浇注系统:根据铸件的结构特点的工艺要求,选择适宜的浇注系统,通常采用顶注式、底注式。
(1)浇注系统设置基本原则:浇口、冒口安放位置合理,大小适宜不妨碍铸件收缩,便于排气、落砂和清理,应使铸型尺寸尽量减少,简化造型操作,节省型砂用量和降低劳动强度。
(2)内浇道位置的注意事项。
1)内浇道不应设在铸件重要部位。
2)应使金属液流至型腔各部位的距离最短。
3)应不使金属液正面冲击铸型和砂芯。
4)应使金属液能均匀分散,快速地充满型腔。
5)不要正对铸型中的冷铁和芯撑。
4、冒口(1)冒口设置基本原则:1)根据铸件的结构和工艺要求正确选择冒口的形状、大小和安放位置。
浅谈大型铸钢件后处理工艺
差 ,仅 用 于 制 作 电机 零 件 或 渗 碳 零 件 ; 中碳 钢 Z G 2 5 ~ Z G 4 5 ,具 较 高 的综 合 力 学性 能. ,即强 度 高 、 有 优 良的塑 性 和 韧性 ,是 以适 于 制作 形 状 复 杂 、 强 度 和 韧 性 要 求 高 的零 件 , 如 锻 锤 机 架 和砧 座 、 轧 辊 和 高 压 阀 门等 ,是 碳 素 铸钢 中应 用 最 多 的一 类 ; 高 碳钢 Z G 5 5的熔 点低 , 其 铸 造性 能较 中碳 钢好 , 但 其 塑性 和韧性 较差 , 仅 用 于制作 少 数 的耐磨 件 。
大 型铸 钢 件 后 处 理 工 艺 与 铸 件 的材 质 关 系 密 切, 这 里 首 先 介 绍 下 铸 钢 的分 类 , 按 照化 学 成 分 铸
等, 对 硝 酸 的耐腐 蚀 性很 高 , 主要 用 于 制作 化 工 、 石
钢可分为碳素铸钢和合金铸钢两大类 , 其 中以碳 素
铸 钢应 用 最广 , 占铸 钢 总产 量 的 7 0 %以上 。
D 0 I: 1 0. 3 96 9/ . 1. 1 5 S n. 1 0 06 — 96 5 8. 2 01 3. 0 5. 0 0 3
大 型 铸 钢 件 的制 造 业 是 国家 装 备 制 造 的 基 础
根据合金元素总量的多少 ,合金铸钢可分为低 合金钢和高合金钢两大类。 ①低合金铸钢 , 我国主要应用锰系、 锰硅系及铬 系等 。如 Z G 4 0 M n 、 Z G 3 0 Mn S i l 、 Z G 3 0 C r l Mn S i l 等 。用
有足 够 的强度 和韧性 , 在铸 件凝 固后 , 还 要在砂 型 中 停 留 一段 时 间方 能 打 箱 ,一 般 来 说 铸 件 温 度 降 至 2 0 0 ~ 4 5 0 ℃才 可 以打箱 落砂 , 所 以铸件 在 型 内应有 足 够 的冷却 时 间。 大 型铸 钢 件 浇 铸 后 ,降 温 缓 慢 ,温 度 降 低 到
大型铸钢件后的处理工艺
大型 铸钢 件 的冷 却落 砂 工艺 1、 大 型 铸 钢 件 的冷 却 、 开 箱 大型铸 钢件浇 注后 , 为 了防止 因冷却速 度过快 而产生 变形 、 裂纹 等缺 陷, 保 证 大型铸 钢 件在 清砂 时有 足够 的强度 和韧 性 , 在铸 件凝 固后 , 还 要在 砂型 中停
一
、
不锈钢 种 类多 , 有 些可 以在 常温下 切割 冒 口 ,  ̄ t B 1 8 / 8型 铬镍钢 和铬 锰钢 。 也有 一些钢 像 高铬 钢 、 铬 钼钢 铸件 需 要 在一 定 的温度 下 热割 , 中小 件可 在3 0 0 ℃, 大件 在 6 0 0  ̄ C左 右进 行切 割 。 如 Z GC r 2 8需 要 把铸件 加 热到 7 0 0 ' C左 右 , 在 保温 坑 内露 出 冒 口部 分趁 热切 割 , 割后 在保 温 坑缓 冷 。 三, 大 型铸 钢件 的热 处 理工 艺 大 型铸钢 件 的热 处理 目前 常用 的几 种 热处理 方 式 : 1 、 扩散 退火 ( 高 温均 匀化 退火 ) : 用于 消除 或减 轻铸钢 件 中的成 分偏 析 , 改 善某 些可溶 性夹 杂物 ( 如 硫化 物等 ) 的形态 , 使 铸件 的化学 成分 、 内部组 织和 力 学 性 能趋 于均 匀和 稳定 。 2 、 正火 、 回火 : 通 过重 结晶细 化 内部组 织 , 提高 强度和 韧性 , 使 得铸 件得 到 良好 的综 合力 学性 能 , 并使 工件 的切 削 加工 性能 得到 改善 。 3 、 退火 : 稳定 铸 件尺 寸 、 组织 与性 能 , 使 铸件 的塑 性 、 韧 性得 到明 显提 高 。 4 、 调质: 淬火 后高温 回火的 热处理方 法 。 调质处 理可 以使钢 的性 能 , 材质 得 到很大 程度 的调 整 , 强度、 塑 性和 韧性 都较 好 , 具有 良好的 综合机 械 性能 。 5 、 消除应 力退火 : 消除铸件 中的 内应力 , 主要 用于修补 件 、 焊 补件及 粗加 工 应力 的消 除 , 消 除应力 退火 必 须低于 铸 件 回火温 度 l f ' 3 0 " C; 保温 时 间一 般为 6/ 2 5 h 以上 ( 5 为工 件最 大 壁厚 , mm) , 随后 在炉 内缓 冷 。 6 、 水 韧处 理 : 高 锰钢 等奥 氏体 铸件 需要 进 行水韧 处理 。 四. 大 型铸 钢件 的修 补 工艺 大 型铸钢件 在成 型过程 中 , 表 面和 内部常会产 生一 些铸造缺 陷 , 如 气 L 、 缩 松、 夹杂 等 。 1、 缺 陷 的 清 除 将 缺 陷部 位预热 到 1 2 5  ̄ 2 0 0  ̄, 用碳 弧气 刨将 有缺 陷的 焊缝 刨除 , 用 砂 轮 机打 磨 去除掉 所 有的 碳 化物 。 对 缺 陷部 位进 行 MT 或着 色探 伤 , 确 认无 任 何 缺 陷后 方可 进行 焊接 修补 。
- 1、下载文档前请自行甄别文档内容的完整性,平台不提供额外的编辑、内容补充、找答案等附加服务。
- 2、"仅部分预览"的文档,不可在线预览部分如存在完整性等问题,可反馈申请退款(可完整预览的文档不适用该条件!)。
- 3、如文档侵犯您的权益,请联系客服反馈,我们会尽快为您处理(人工客服工作时间:9:00-18:30)。
大型铸钢件工艺设计的关键技术武汉钢铁重工集团铸钢车间孙凡摘要:简要介绍大型铸钢件的铸造工艺设计的铸件的工艺性分析、铸造工艺方案选择、铸造工艺参数的选定、铸件成形的控制、铸件的热处理技术、铸造工艺装备的设计、铸件的后处理技术及计算机数值模拟技术等关键技术。
1 零件的工艺性研究铸造工艺设计时,首先要仔细地阅读和研究铸件的制造或采购技术条件、质量要求。
如探伤要求,表面质量要求,机械性能要求,特殊热处理要求等,其次,要研究零件的结构特点,如质量要求高的表面或主要的加工面,主要的尺寸公差要求等,再次,研究材料化学成分,特别是铸造合金中含碳量,合金元素含量作用和机理。
这些对下一步的工艺设计有直接影响。
需格外重视,做好零件的工艺性研究,能为工艺设计奠定良好的开端。
1.1 材料的工艺性分析在大型铸件的制造中,材料的物理性能和机械性能,对工艺参数的选定、浇冒口和冷铁设置、热处理技术、铸件的后处理技术等都有重大影响。
深入了解铸造合金中含碳量,合金元素含量对铸态组织形态的影响,对力学性能的影响,了解材料的凝固方式,收缩倾向,冒口补缩效果,了解材料的热导率,热应力倾向等,对工艺设计有重要意义。
在砂型条件下,随着合金中碳的质量分数量增加,结晶温度范围扩大。
低碳钢为逐层凝固方式,中碳钢为中间凝固方式,高碳钢为体积凝固方式凝固,但改变冷却条件,可以改变结晶温度范围,从而改变合金的凝固方式。
由于凝固方式的不同,窄结晶温度范围的合金,容易形成细小的晶粒组织,补缩性好,热烈倾向小;反之,宽结晶温度范围的合金,容易形成粗大的晶粒组织,补缩性差,热烈倾向大。
因此,高碳钢的厚大部位,要采取强制冷却工艺缩小结晶温度范围,改善晶粒组织。
合金中的碳、锰、铬等元素的含量增加,可以提高强度,提高淬透性,却降低导热性,直接影响铸件各部位冷却、加热的温度差,因此,合金钢较容易造成高的残余应力。
工艺上要减少各部位浇注后冷却、热处理加热的温度差。
合金在相变时,各种组织组成相的比体积不同,会产生相变应力,其中,马氏体的比体积最大,马氏体相变最容易产生较大的相变应力。
碳、锰、铬等淬透性元素含量高的合金钢,冷割冒口时极易产生裂纹,原因就是导热性差热应力大,产生马氏体转变导致相变应力大,必须热割冒口,1.2 铸件结构的工艺性分析对于需要铸造的零件,必须检查它的结构是否符合铸造工艺的基本要求。
因为有时对铸件的结构,作很小的改动,并不影响铸件的使用性能, 但却大大地简化了铸造工艺,有利于提高铸件质量。
在铸造生产中, 对铸件结构的基本要求有以下几点:铸件的壁厚应大于铸件允许的最小壁厚,以免产生浇不足等缺陷。
铸件的尺寸越大,合金液充满铸型也就越困难,铸件允许的最小壁厚也应越大。
铸件的壁厚应尽可能地均匀,否则铸件容易产生缩孔和裂纹。
壁厚相差悬殊, 在厚的部分容易形成缩孔,在厚薄交接处容易形成裂纹。
尽量避免铸件上部( 指铸件在浇注位置) 有较大的水平面,最好带有合理的斜度,以有利于气体和熔渣等的排出,减少形成气孔和渣眼的可能。
铸件的结构应保证泥芯能牢固地安置在铸型里。
铸件的结构应使造型时减少分型面和砂芯,简化造型操作,有利于后处理。
2 工艺方案的确定在选定铸造工艺方案时,必须考虑铸造车间的具体条件,如铸造设备运转情况、生产能力,铸件的结构和尺寸、技术要求以及生产数量等。
下面就铸造工艺方案选择的主要原则,进行初步讨论。
2.1 浇注位置的选择铸件浇注位置的选择, 对铸件质量、造型方法、砂箱尺寸、机械加工余量等都有着很大的影响。
在选定浇注位置时应以保证铸件质量为主,一般应注意下面的几个原则:应将铸件上质量要求高的表面或主要的加工面,放在铸型的下面。
或者置于铸型的侧面或倾斜放置进行浇注。
应把截面较厚的部分放在铸型的上部或侧面。
这样便于在铸件的厚壁处放置冒口,造成良好的顺序凝固,有利于铸件补缩。
薄壁部分放在铸型的下部,或者置于铸型的侧面立着或倾斜着浇注,这样有利于金属的充填。
对于具有大平面的铸件,应将铸件的大平面放在铸型的下面,这样可使铸件的大平面不容易产生夹砂等缺陷。
对于带有泥芯的铸件,应使泥芯能放置牢固并在合箱时便于检验。
长、宽、高三个方向高度方向尺寸应最小,减少偏析和跑火机率,有利于补缩。
1.3铸型分型、分模面的选择铸型分型面、分模面选择得正确,可以简化造型操作,提高劳动生产率,使铸件尺寸准确, 减少废品等。
在选择时,一般应注意下面几点:尽量把铸件的大部分或全部放在同一铸型内,从而减少因错箱造成的尺寸偏差,还可使高度减低,便于合箱。
应使铸件的加工面及加工基准面,放在同一个铸型内。
由于加工面与加工基准面都处在同一个型内,当铸件的加工面很多,又不可能都与基准面放在分型面的同一侧时,则应尽量使加工的基准面与大部分的加工面放在分型面同一侧。
从而减少因错箱造成的加工余量不够。
应使铸模容易从铸型中取出,并尽量减少活块模、高大的吊砂和弯曲的分型面等。
尽量减少泥芯的数量。
这样可以省去制造和安放泥芯的工作,也可减少由此造成的误差及产生的披缝,降低铸件的制造成本。
铸件的不加工表面应尽量避免有披缝,提高铸件的外观质量。
3.工艺参数的设计铸造生产的工艺方案决定以后, 还应根据产品零件图的形状、尺寸和技术要求, 选定好各种铸造工艺参数。
铸造工艺参数是由金属种类和铸造方法等的特点决定的。
其内容主要包括铸造收缩率、机械加工余量、拔模斜度、铸造圆角和芯头尺寸等,还有工艺补正量和分型负数等。
选择铸造工艺参数时必须根据实际的生产情况,灵活运用。
3.1铸造收缩率对于铸钢件在铸型内凝固和冷却过程中收缩和变形规律的掌握,是保证获得铸件基本外形轮廓和尺寸精度的关键技术。
影响铸件收缩率的因素较多,主要的有:铸型的退让性,铸件的材料,铸件的结构。
铸型的退让性好,铸件的收缩率增大。
随着铸件的尺寸增大,铸型的退让性变差,铸件的收缩率也就减小。
铸件的结构复杂,收缩困难,铸件的收缩率减小。
铸件的材料的不同,收缩率不同。
同一成分浇注的铸钢件,因结构形状不同,收缩率不同,同一个铸件,由于结构上的原因,其轴向与径向或长、宽、高三个方向的收缩率可能不一致。
对于尺寸要求较精确的铸件,各个方向应给以不同的收缩率。
其中以自由收缩时的收缩率最大。
所以铸造收缩率要结合实际情况来选择。
在实际生产中,一般的铸件,特别是尺寸不大的铸件,各个方向都用同一的收缩率,尽管这样会造成一些误差,但由于误差一般不大,而这样大大便于铸模的加工制造。
3.2 机械加工余量加工余量是参照机械加工余量表和结合生产实际情况而确定的。
加工余量应当合理地选定。
加工余量过大,不仅浪费金属,增加机械加工工作量, 有时还会因截面变厚,热节变大,使铸件晶粒粗大, 甚至造成缩孔或缩松。
加工余量过小,不能把铸件的加工表面全部切净,使零件达不到要求的精度和光洁度。
加工余量的大小与铸造金属的种类、生产条件以及铸件尺寸和加工面部位等有关。
铸件的尺寸大,变形往往也大,加工余量需要大一些,铸件上面( 指浇注时位置) 与底面和侧面相比,表面质量较差,加工余量也需要大一些。
小的孔槽一般不宜铸出。
否则,不但使造型工艺复杂,而且会因孔槽的偏斜, 给机械加工带来困难。
3.3 拔模斜度拔模斜度取法有三种:增加壁厚法、加减壁厚法、减少壁厚法。
拔模斜度选取时不应超出铸件的壁厚公差要求。
由于大件的起模往往需要借助机械装置,设置不当时,过小容易损坏工装或型芯,过大影响铸件形状结构或加工余量。
为了方便芯盒起模, 要把铸模的垂直壁做成向起模面扩大的斜度,需要与配合的型芯一致,拔模斜度过大最好做成劈模,避免过大的拔模斜度。
铸件要加工的侧面,一般按增加铸件壁厚的方法确定。
铸模在起模方向如已有足够的结构斜度,便不再加拔模斜度。
金属模的拔模斜度可比木模稍小些。
3.4 铸造圆角铸造圆角是不可忽视的工艺因素,因尖角砂在浇注时容易造成冲砂、砂眼和粘砂等缺陷,而且转角没有圆角过渡的铸件会因容易产生较大的铸造应力而裂开。
没有圆角过渡的铸件的强度也较低,因尖锐的棱角部分在结晶时会形成强度较低的薄弱面,因这时薄弱面是垂直于受力方向的,当铸件受力时,很容易从薄弱面处裂断。
铸件如果做有圆角,就改善了这种情况。
3.5 工艺补正量工艺补正量是用于补正由于铸造收缩率选用不当或其它工艺原因造成铸件局部尺寸的偏差。
大型铸件的工艺补正量有时非常重要,结构复杂、尺寸较大,影响因素多,形状和尺寸变化很难把握,补正量的选取往往起到纠正挽救的特殊效果。
其设置经验性很强,需要长期摸索和积累。
3.6 分型负数由于修型和烘干过程中砂型的变形,引起分型面不能严密贴合, 为了防止浇注时产生跑火,合箱时需在分型面上放上耐火泥条或石棉绳,这样就增加了型膛的高度。
为了使铸件尺寸符合要求, 在铸模上需减去相应的高度,这个减去的尺寸称为分型负数。
分型负数随砂型尺寸增大而增加,其值约为l-5 毫米。
要使铸件的形状和尺寸符合要求,除了要正确设计上述的铸造工艺参数外,还需要有严格的工艺操作规程来保证。
例如,砂型紧实度要符合要求,木模要干燥,起模时松模不能过大,修型时不能过分光压,合箱时放入的泥条不要过高等,而铸模的磨损,涂料上得过厚,砂型和泥芯受热膨胀等都会使铸件尺寸变小,铸模的变形和结构松动,也会影响铸件的形状和尺寸。
上面就一些主要铸造工艺参数进行讨论。
在选定工艺参数时要注意下面两点:(1)影响铸造工艺参数的因素很多,一定要结合实际来选定,并作必要的修正。
(2)各个铸造工艺参数之间是有联系的,要综合考虑,相互配合,不断修正,例如,铸件收缩量的误差,可用机械加工余量来补偿。
工艺参数确定以后,要精确计算铸件的浇注重量,浇注重量对下一步的工艺设计和生产操作有重大影响,是浇、冒口设计,熔炼、浇注的基础数据,最好采用三维软件进行计算。
4 铸件成形的控制主要包括浇、冒系统,冷铁设计。
控制充型过程和凝固过程,在铸造生产过程中起着重要的作用。
许多的铸造缺陷都与上述两个过程直接相关,如缩松、缩孔、卷气、冷隔、夹渣等。
是铸造工艺的关键技术之一。
4.1 液态金属充型过程控制液态金属充型过程控制将影响浇注的成败和铸件质量,大型铸件的浇注工艺应满足大流量、快速平稳充型的基本要求。
大型铸件的浇注多采用多包多浇道同时浇注,充型过程控制的关键是:(1)严格控制钢液的浇注温度和补浇钢液的温度,(2)协调好各包、各浇口的开启步调时间和顺序,(3)严格控制浇注时间,(4)要设置防止残砂、钢渣、引流砂进入型腔的措施,如防砂帽、溢流口、缓流浇道等。
4.2 铸件的结晶、凝固与收缩控制对于大型铸钢件,保证铸件凝固顺序和补缩效率,这是控制铸造缺陷,获得优质大型铸钢件的重要条件。
需要合理设置冒口的尺寸、数量、位置,考虑到充分补缩的要求,通常需要设置足够的冒口补贴,并配合适当的挂砂冷铁,挂砂冷铁设计时,冷铁布置、挂砂层厚度、挂砂层附着强度等工艺因素对控制凝固顺序,防止缺陷均有重大影响。