铸钢件生产工艺要求及质量标准 (1)
技术质量指标铸钢件生产工艺.

模具、芯骨、工装、夹具、专用检测器具、专用加工设备原辅材料、备品、备件检验检验冶炼造型浇注铸件待冷却铸件出型清砂铸件清理铸件热处理铸件毛坯精整机加工发运包装油漆抛丸检验检验检验检验检验检验检验检验检验检验2、产品主要成份、性能、技术质量指标(1)材质要求具体化学成份为(%):C 0.17~0.23;Si≤0.60;Mn 1.0~1.50;P≤0.020;S≤0. 015;Cr≤0. 30;Mo≤0. 15;Ni≤0.40;Al≤0.020 ; Re0.2~0.35(加入量)(2)机械性能要求屈服强度≥230Mpa 抗拉强度≥450Mpa延伸率≥22% 冲击功≥40J1)按GB11352标准要求随炉提取试样,每一个炉号制备二组试样,其中一组备查。
2)为确保具有良好的焊接性能,节点铸件碳当量控制在CE≤0.42。
3)铸件表面质量符合设计要求,表面粗糙度达到GB6060.1标准要求。
4)铸件的探伤要求,按GB7233探伤, 采用6㎜探测头,管口焊缝区域150mm以内范围超声波100%探伤,质量等级为Ⅱ级,其余外表面10%超声波探伤,质量等级为IV级。
不可超声波探伤部位采用GB9444磁粉表面探伤,质量等级为III级。
5)节点的外形尺寸符合图样要求,管口外径尺寸公差按负偏差控制。
6)热处理按照Q/32182HQA05-2002标准要求,铸件进行正火处理(920±20℃,出炉空冷,加640±20℃回火处理)。
7)涂装处理要求:表面采用抛丸或喷砂除锈,除锈等级Sa2.5级,随即涂水性无机富锌底漆,厚度50μm,环氧云铁中间漆2×30μm。
3、铸造工艺参数(1)加工余量按照GB/T11350-89,CT12H/J级。
(2)模样线收缩率2.0%铸件毛坯尺寸偏差符合GB6414-86中CT12要求。
4、铸造工艺说明(1)为保证叉管与杆件相交处质量,考虑尽可能将支管水平放置,分二箱造型,在铸件上平面分型,整体分两半实模。
铸造生产的工艺操作规范
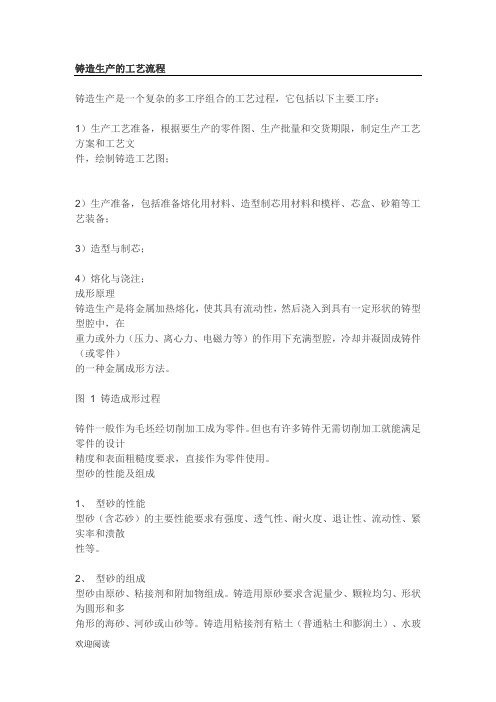
铸造生产的工艺流程铸造生产是一个复杂的多工序组合的工艺过程,它包括以下主要工序:1)生产工艺准备,根据要生产的零件图、生产批量和交货期限,制定生产工艺方案和工艺文件,绘制铸造工艺图;2)生产准备,包括准备熔化用材料、造型制芯用材料和模样、芯盒、砂箱等工艺装备;3)造型与制芯;4)熔化与浇注;成形原理铸造生产是将金属加热熔化,使其具有流动性,然后浇入到具有一定形状的铸型型腔中,在重力或外力(压力、离心力、电磁力等)的作用下充满型腔,冷却并凝固成铸件(或零件)的一种金属成形方法。
图1 铸造成形过程铸件一般作为毛坯经切削加工成为零件。
但也有许多铸件无需切削加工就能满足零件的设计精度和表面粗糙度要求,直接作为零件使用。
型砂的性能及组成1、型砂的性能型砂(含芯砂)的主要性能要求有强度、透气性、耐火度、退让性、流动性、紧实率和溃散性等。
2、型砂的组成型砂由原砂、粘接剂和附加物组成。
铸造用原砂要求含泥量少、颗粒均匀、形状为圆形和多角形的海砂、河砂或山砂等。
铸造用粘接剂有粘土(普通粘土和膨润土)、水玻璃砂、树脂、合脂油和植物油等,分别称为粘土砂,水玻璃砂、树脂砂、合脂油砂和植物油砂等。
为了进一步提高型(芯)砂的某些性能,往往要在型(芯)砂中加入一些附加物,如煤份、锯末、纸浆等。
型砂结构,如图 2 所示。
图2 型砂结构示意图工艺特点铸造是生产零件毛坯的主要方法之一,尤其对于有些脆性金属或合金材料(如各种铸铁件、有色合金铸件等)的零件毛坯,铸造几乎是唯一的加工方法。
与其它加工方法相比,铸造工艺具有以下特点:1)铸件可以不受金属材料、尺寸大小和重量的限制。
铸件材料可以是各种铸铁、铸钢、铝合金、铜合金、镁合金、钛合金、锌合金和各种特殊合金材料;铸件可以小至几克,大到数百吨;铸件壁厚可以从0.5 毫米到1 米左右;铸件长度可以从几毫米到十几米。
2)铸造可以生产各种形状复杂的毛坯,特别适用于生产具有复杂内腔的零件毛坯,如各种箱体、缸体、叶片、叶轮等。
铸钢件表面质量标准

铸钢件表面质量标准
铸钢件是工业生产中常见的零部件,其表面质量直接关系到零部件的使用寿命
和性能。
因此,对铸钢件表面质量的标准化要求非常严格。
本文将对铸钢件表面质量标准进行详细介绍,以便于大家更好地了解和掌握相关知识。
首先,铸钢件表面质量标准包括表面粗糙度、表面缺陷和表面涂装等多个方面。
表面粗糙度是指铸钢件表面的不平整程度,通常通过表面粗糙度仪进行测量。
根据不同的使用要求,铸钢件的表面粗糙度标准也有所不同。
一般来说,表面粗糙度越小,零部件的使用寿命和性能就越好。
其次,表面缺陷是指铸钢件表面的瑕疵和缺陷,包括气孔、夹渣、裂纹等。
这
些表面缺陷会严重影响铸钢件的使用性能,甚至导致零部件的失效。
因此,在生产过程中,必须严格控制铸钢件表面缺陷的产生,确保零部件的表面质量符合标准要求。
此外,表面涂装也是铸钢件表面质量标准中的重要内容。
表面涂装不仅可以美
化零部件的外观,还可以提高零部件的耐腐蚀性能和耐磨性能。
因此,在进行表面涂装时,必须严格按照相关标准进行操作,确保涂装质量符合要求。
总的来说,铸钢件表面质量标准是保证零部件质量的重要保障。
只有严格按照
标准要求进行生产和检测,才能确保铸钢件的表面质量达到标准,从而保证零部件的使用寿命和性能。
希望通过本文的介绍,大家能够更加深入地了解铸钢件表面质量标准的重要性,为生产实践提供参考。
铸钢件生产工艺要求及质量标准
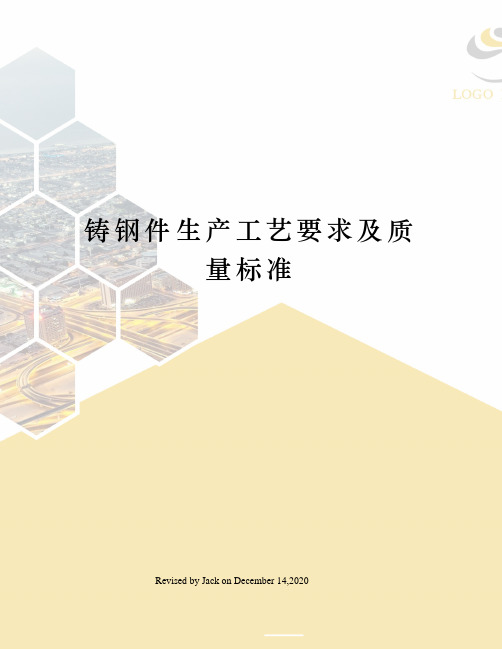
铸钢件生产工艺要求及质量标准Revised by Jack on December 14,2020铸钢件生产工艺要求及质量标准一、混砂工艺标准(一)材料要求:1、造型砂:符合GB9442-88 、JB435-63细粒砂要求,一般选用二氧化硅含量较高的天然砂或石英砂,原砂粒度根据铸件大小及壁厚确定,原砂的含泥质量分数应小于2%,原砂中的水份必须严格控制,且一般应进行烘干。
2、水玻璃:水玻璃模应根据铸件大小来确定。
(1)小砂型(芯)为加速硬化采用选用M=—的高模数水玻璃。
(2)中型砂型(芯)可选用M=—的水玻璃。
(3)生产周期长的大型砂型(芯)选用M=—的低模数水玻璃。
(二)混制比例(质量分数%)造型砂/水玻璃=100:6~8(三)混制时间:一般情况下混制5分钟,室温或水玻璃密度较大时可适当延长混砂时间。
(四)混制后要求:混制好的造型砂要求无块状或团状,流动性较好。
二、造型工艺要点:(一)基本原则:1、质量要求高的面或主要加工面应放在下面。
2、大平面应放在下面。
3、薄壁部分应放在下面。
4、厚大部分应放在上面。
5、应尽量减少砂芯的数量。
6、应尽量采用平直的分型面。
(二)基本要求:1、木模:要求轮廓完整,无裂纹、无破损、无残缺,表面光洁,尺寸符合铸造工艺图纸要求,并经常进行尺寸校验。
2、砂箱:砂箱的尺寸大小应根据木模规格确定,大、中型砂箱应焊接箱筋。
3、浇注系统:根据铸件的结构特点的工艺要求,选择适宜的浇注系统,通常采用顶注式、底注式。
(1)浇注系统设置基本原则:浇口、冒口安放位置合理,大小适宜不妨碍铸件收缩,便于排气、落砂和清理,应使铸型尺寸尽量减少,简化造型操作,节省型砂用量和降低劳动强度。
(2)内浇道位置的注意事项。
1)内浇道不应设在铸件重要部位。
2)应使金属液流至型腔各部位的距离最短。
3)应不使金属液正面冲击铸型和砂芯。
4)应使金属液能均匀分散,快速地充满型腔。
5)不要正对铸型中的冷铁和芯撑。
4、冒口(1)冒口设置基本原则:1)根据铸件的结构和工艺要求正确选择冒口的形状、大小和安放位置。
铸钢件国标
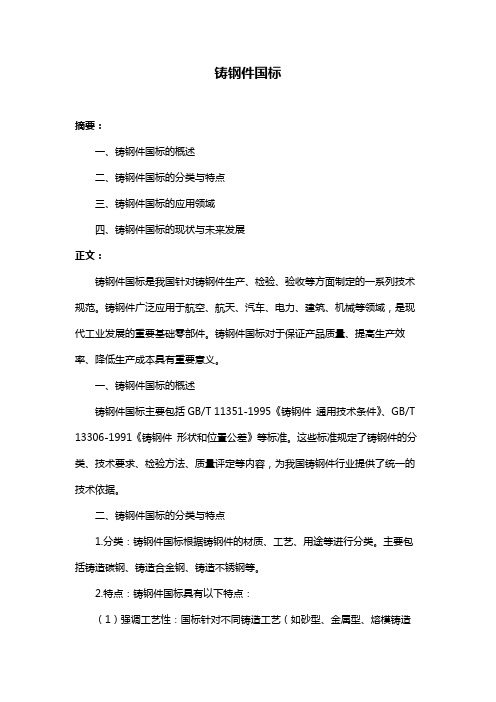
铸钢件国标摘要:一、铸钢件国标的概述二、铸钢件国标的分类与特点三、铸钢件国标的应用领域四、铸钢件国标的现状与未来发展正文:铸钢件国标是我国针对铸钢件生产、检验、验收等方面制定的一系列技术规范。
铸钢件广泛应用于航空、航天、汽车、电力、建筑、机械等领域,是现代工业发展的重要基础零部件。
铸钢件国标对于保证产品质量、提高生产效率、降低生产成本具有重要意义。
一、铸钢件国标的概述铸钢件国标主要包括GB/T 11351-1995《铸钢件通用技术条件》、GB/T 13306-1991《铸钢件形状和位置公差》等标准。
这些标准规定了铸钢件的分类、技术要求、检验方法、质量评定等内容,为我国铸钢件行业提供了统一的技术依据。
二、铸钢件国标的分类与特点1.分类:铸钢件国标根据铸钢件的材质、工艺、用途等进行分类。
主要包括铸造碳钢、铸造合金钢、铸造不锈钢等。
2.特点:铸钢件国标具有以下特点:(1)强调工艺性:国标针对不同铸造工艺(如砂型、金属型、熔模铸造等)制定了相应的要求和检验方法。
(2)注重质量控制:国标对铸钢件的尺寸公差、形状和位置公差、表面质量等提出了明确要求,有利于确保产品质量。
(3)强化检验与评定:国标规定了铸钢件的检验方法、检验频率、不合格品处理等内容,确保产品合格率。
三、铸钢件国标的应用领域铸钢件国标在我国铸钢件行业得到了广泛应用,对航空、航天、汽车、电力、建筑、机械等领域产生了积极影响。
遵循国标生产铸钢件,有利于提高产品质量和竞争力,满足国内外市场需求。
四、铸钢件国标的现状与未来发展随着我国工业的快速发展,铸钢件国标在技术要求、检验方法等方面不断完善,逐步与国际接轨。
未来,铸钢件国标将继续发挥重要作用,推动我国铸钢件行业技术创新和产业结构优化升级。
总之,铸钢件国标在保障我国铸钢件产品质量、提高生产效率、降低生产成本等方面具有重要意义。
铸钢 标准
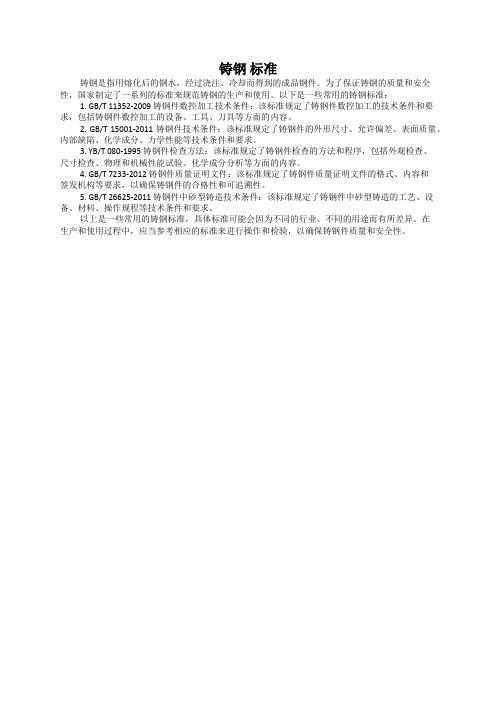
铸钢标准
铸钢是指用熔化后的钢水,经过浇注、冷却而得到的成品钢件。
为了保证铸钢的质量和安全性,国家制定了一系列的标准来规范铸钢的生产和使用。
以下是一些常用的铸钢标准:
1. GB/T 11352-2009 铸钢件数控加工技术条件:该标准规定了铸钢件数控加工的技术条件和要求,包括铸钢件数控加工的设备、工具、刀具等方面的内容。
2. GB/T 15001-2011 铸钢件技术条件:该标准规定了铸钢件的外形尺寸、允许偏差、表面质量、内部缺陷、化学成分、力学性能等技术条件和要求。
3. YB/T 080-1995 铸钢件检查方法:该标准规定了铸钢件检查的方法和程序,包括外观检查、
尺寸检查、物理和机械性能试验、化学成分分析等方面的内容。
4. GB/T 7233-2012 铸钢件质量证明文件:该标准规定了铸钢件质量证明文件的格式、内容和
签发机构等要求,以确保铸钢件的合格性和可追溯性。
5. GB/T 26625-2011 铸钢件中砂型铸造技术条件:该标准规定了铸钢件中砂型铸造的工艺、设备、材料、操作规程等技术条件和要求。
以上是一些常用的铸钢标准,具体标准可能会因为不同的行业、不同的用途而有所差异。
在
生产和使用过程中,应当参考相应的标准来进行操作和检验,以确保铸钢件质量和安全性。
铸钢件生产工艺流程
件的形状和尺寸。
※(型1)砂(任对务生2产打)成开重本浇的注要影后响的性很铸(大型,,地有取些出位砂铸种)件占,是成打本碎砂的已比型浇例注铸很后大的造。铸生型,产取出的铸主件。要或者说是基本工序,往往以 ((14) )任设务备该:去热除道处热理工处炉理序,时冷生来却成水衡的池氧量。化皮/计算铸造生产能力、劳动生产率(效率)、生产技术
-8-
三. 后道工序 1.开箱落砂 (1)任务 打开浇注后的铸型,取出铸件,打碎已浇注后的铸型,取出
铸件。是后道工序的第一步,是砂再生处理的第一步; (2)重要性 (注意事项) 及时开箱,保证砂箱的流转,浇出来的铸件
及时进入下道工序,防止铸件出现裂纹和震坏。 2.清砂 (1)任务 将铸件表面、内腔残留的型砂清除掉,去除芯骨和铸件表面的
-4-
2.烘烤和上涂料
(1)任务(目的) 对制备好的砂型和砂芯烘烤,上涂料,防止铸件出现气 孔,防止粘砂、冲刷,提高铸件表面光洁度。
(2)重要性 对提高铸件表面光洁度,防止粘砂、冲砂,防止气孔起很大 的甚至是决定性的作用。
(3)涂料 我公司用锆英粉醇基涂料,涂料的基本组成(骨料)是锆英粉,
化学结构式是ZrO2·SiO2, ZrO2含量越高越好,铸钢生产要求含ZrO2
中因醇类物质的挥发涂料变粘度,影响涂刷,用工业无水酒精稀释。刷
涂料时要避免涂料堆集,影响铸件尺寸,过厚的涂料层不易烘干,会造
成铸件气孔。
-5-
3.合箱(配模) (1)任务(内容)将制备好的砂型和砂芯装配起来,准备浇注。有时要放内
铸钢件生产工艺要求及质量标准
铸钢件生产工艺要求及质量标准一、混砂工艺标准(一)材料要求:1、造型砂:符合GB9442-88 、JB435-63细粒砂要求,一般选用二氧化硅含量较高的天然砂或石英砂,原砂粒度根据铸件大小及壁厚确定,原砂的含泥质量分数应小于2%,原砂中的水份必须严格控制,且一般应进行烘干。
2、水玻璃:水玻璃模应根据铸件大小来确定。
(1)小砂型(芯)为加速硬化采用选用M=2.7—3.2的高模数水玻璃。
(2)中型砂型(芯)可选用M=2.3—2.6的水玻璃。
(3)生产周期长的大型砂型(芯)选用M=2.0—2.2的低模数水玻璃。
(二)混制比例(质量分数%)造型砂/水玻璃=100:6~8(三)混制时间:一般情况下混制5分钟,室温或水玻璃密度较大时可适当延长混砂时间。
(四)混制后要求:混制好的造型砂要求无块状或团状,流动性较好。
二、造型工艺要点:(一)基本原则:1、质量要求高的面或主要加工面应放在下面。
2、大平面应放在下面。
3、薄壁部分应放在下面。
4、厚大部分应放在上面。
5、应尽量减少砂芯的数量。
6、应尽量采用平直的分型面。
(二)基本要求:1、木模:要求轮廓完整,无裂纹、无破损、无残缺,表面光洁,尺寸符合铸造工艺图纸要求,并经常进行尺寸校验。
2、砂箱:砂箱的尺寸大小应根据木模规格确定,大、中型砂箱应焊接箱筋。
3、浇注系统:根据铸件的结构特点的工艺要求,选择适宜的浇注系统,通常采用顶注式、底注式。
(1)浇注系统设置基本原则:浇口、冒口安放位置合理,大小适宜不妨碍铸件收缩,便于排气、落砂和清理,应使铸型尺寸尽量减少,简化造型操作,节省型砂用量和降低劳动强度。
(2)内浇道位置的注意事项。
1)内浇道不应设在铸件重要部位。
2)应使金属液流至型腔各部位的距离最短。
3)应不使金属液正面冲击铸型和砂芯。
4)应使金属液能均匀分散,快速地充满型腔。
5)不要正对铸型中的冷铁和芯撑。
4、冒口(1)冒口设置基本原则:1)根据铸件的结构和工艺要求正确选择冒口的形状、大小和安放位置。
浅谈铸钢节点生产工艺要求
浅谈铸钢节点生产工艺要求摘要:铸钢节点构造复杂,外形尺寸大,重量较重,属特殊超大超重节点,制作精度要求高。
针对铸钢节点类型多、铸造工艺复杂、要求高等特点,制订铸钢节点生产工艺要求,以确保工程质量。
关键词:铸钢节点;铸造工艺;工艺要求。
Abstract:large cast steel nodes, with complex structures, large overall dimensions and heavier weights, they are of a kind of special oversized and overweight node with high requirement of production precision. To adapt to the multiple types, complex casting process and high requirement of cast steel nodes, the author develops the production process requirement of cast steel nodes to ensure the quality and progress of the project.Keywords: cast steel nodes; casting process; process requirement.1混沙工艺标准1.1材料要求:(1)造型沙:符合GB9442-88[1]细粒砂要求,一般选用二氧化硅含量较高的天然砂或石英砂,原砂粒度根据铸件大小及壁厚确定,原砂的含泥质量分数应小于2%,原砂中的水份必须严格控制,且一般应进行烘干。
(2)水玻璃:小砂型(芯)为加速硬化采用选用M=2.7—3.2的高模数水玻璃;中型砂型(芯)可选用M=2.3—2.6的水玻璃;生产周期长的大型砂型(芯)选用M=2.0—2.2的低模数水玻璃。
新版铸造行业标准规范(铸造行业标准有哪些)
铸造行业准入条件为引导铸造产业健康、有序和可持续发展,促进铸造行业产业结构优化升级,遏制低水平重复建设和产能盲目扩张,保护生态环境,推进节能减排,提高资源、能源利用水平,提升我国装备制造业整体实力,推进我国从世界铸造大国向铸造强国转变,根据有关法律法规和产业政策,制定本准入条件。
一、建设条件和布局(一)铸造企业的布局及厂址的确定应符合国家产业政策和相关法律法规,符合各省、自治区、直辖市铸造业和装备制造业发展规划。
(二)国务院有关主管部门和省、自治区、直辖市人民政府划定的风景名胜区、自然保护区和水源地及其他需要特别保护的区域(一类区)的铸造企业不予认定;在二类区和三类区(一类区以外的其他地区),新(扩)建铸造企业和原有铸造企业的各类污染物(大气、水、厂界噪声、固体废弃物)排放标准与处置措施均应符合国家和当地环保标准的规定。
(三)新(扩)建铸造企业应通过“建设项目环境影响评价审批”及“职业健康安全预评估”,并通过项目环境保护和职业健康安全防护设施“三同时”验收。
二、生产工艺(一)企业应根据生产铸件的材质、品种、批量,合理选择低污染、低排放、低能耗、经济高效的铸造工艺。
(二)不得采用粘土砂干型/芯、油砂制芯、七〇砂制型/芯等落后铸造工艺。
三、生产装备(一)企业应配备与生产能力相匹配的熔炼设备和精炼设备,如冲天炉、中频感应电炉、电弧炉、精炼炉(AOD、VOD、LF炉等)、电阻炉、燃气炉等。
炉前应配置必要的化学成分分析、金属液温度测量装备,并配有相应有效的通风除尘、除烟设备与系统。
(二)铸造用高炉应符合工业和信息化部颁布的《铸造用生铁企业认定规范条件》并通过工业和信息化部认定。
(三)企业应配备与生产能力相匹配的造型、制芯、砂处理、清理等设备。
采用砂型铸造工艺的企业应配备旧砂处理设备。
各种旧砂的回用率应达到:水玻璃砂(再生)≥60%,呋喃树脂自硬砂(再生)≥90%,碱酚醛树脂自硬砂(再生)≥70%,粘土砂≥95%。
- 1、下载文档前请自行甄别文档内容的完整性,平台不提供额外的编辑、内容补充、找答案等附加服务。
- 2、"仅部分预览"的文档,不可在线预览部分如存在完整性等问题,可反馈申请退款(可完整预览的文档不适用该条件!)。
- 3、如文档侵犯您的权益,请联系客服反馈,我们会尽快为您处理(人工客服工作时间:9:00-18:30)。
铸钢件生产工艺要求及质量标准一、混砂工艺标准(一)材料要求:1、造型砂:符合GB9442-88 、JB435-63细粒砂要求,一般选用二氧化硅含量较高的天然砂或石英砂,原砂粒度根据铸件大小及壁厚确定,原砂的含泥质量分数应小于2%,原砂中的水份必须严格控制,且一般应进行烘干。
2、水玻璃:水玻璃模应根据铸件大小来确定。
(1)小砂型(芯)为加速硬化采用选用M=—的高模数水玻璃。
(2)中型砂型(芯)可选用M=—的水玻璃。
(3)生产周期长的大型砂型(芯)选用M=—的低模数水玻璃。
(二)混制比例(质量分数%)造型砂/水玻璃=100:6~8(三)混制时间:一般情况下混制5分钟,室温或水玻璃密度较大时可适当延长混砂时间。
(四)混制后要求:混制好的造型砂要求无块状或团状,流动性较好。
二、造型工艺要点:(一)基本原则:1、质量要求高的面或主要加工面应放在下面。
2、大平面应放在下面。
3、薄壁部分应放在下面。
4、厚大部分应放在上面。
5、应尽量减少砂芯的数量。
6、应尽量采用平直的分型面。
(二)基本要求:1、木模:要求轮廓完整,无裂纹、无破损、无残缺,表面光洁,尺寸符合铸造工艺图纸要求,并经常进行尺寸校验。
2、砂箱:砂箱的尺寸大小应根据木模规格确定,大、中型砂箱应焊接箱筋。
3、浇注系统:根据铸件的结构特点的工艺要求,选择适宜的浇注系统,通常采用顶注式、底注式。
(1)浇注系统设置基本原则:浇口、冒口安放位置合理,大小适宜不妨碍铸件收缩,便于排气、落砂和清理,应使铸型尺寸尽量减少,简化造型操作,节省型砂用量和降低劳动强度。
(2)内浇道位置的注意事项。
1)内浇道不应设在铸件重要部位。
2)应使金属液流至型腔各部位的距离最短。
3)应不使金属液正面冲击铸型和砂芯。
4)应使金属液能均匀分散,快速地充满型腔。
5)不要正对铸型中的冷铁和芯撑。
4、冒口(1)冒口设置基本原则:1)根据铸件的结构和工艺要求正确选择冒口的形状、大小和安放位置。
2)根据冒口的有效补缩范围合理地确定冒口数量。
(2)冒口设置基本要求:1)对于壁厚不均匀的铸件,每个热节部位都必须设置冒口。
2)应尽量设置在铸件被补缩部位的顶部或近旁。
3)当铸件在不同高度上有热节需要补缩时,可设置多个冒口,但各冒口的补缩区必须隔开。
4)冒口最好不设置在铸件重要的或受力较大的部位。
5)应尽量使内浇道通过冒口。
6)冒口应尽量不设置在铸件应力集中处。
7)冒口最好设置在铸件需要机械加工的表面上。
(三)造型操作:1、操作流程顺序是:选取合适砂箱→放置木模→填砂→紧实→放置上砂箱→安置浇冒口→填砂→紧实→起模修型→硬化2、操作方法及质量标准(1)根据铸件模型的形状和大小,选取合适的砂箱。
(2)把铸件模型放到砂箱内的适当位置。
(3)往砂箱中加入适当造型砂,使用工具将砂箱中的造型砂紧实,紧实程度要适中。
(4)用刮板刮去高出砂箱的造型砂,使砂型表面和砂箱的边缘平齐。
(5)用毛刷清理模型表面浮砂,覆盖塑料薄膜并使薄膜平整。
(6)放置上砂箱,上、下砂箱箱口要对齐。
(7)在上砂箱中合适位置放置浇冒口,添加造型砂并紧实。
(8)分箱起模,修型并扎气眼硬化。
3、砂型型腔质量要求(1)砂型无飞边、无毛刺、无残缺,型腔内干净无残砂等异物。
(2)型腔应干燥,硬化程度高,合箱前要保证充分干燥(冬季可适当延长硬化和烘烤时间)。
(3)砂型轮廓完整、清晰,合箱箱印或记号完整清晰。
(4)浇口、冒口位置设置合理、大小符合要求;排气孔通畅、浇注系统根据铸件设置合理。
4、合箱合箱就是把砂型和砂芯按要求组合在一起成为铸型的过程。
习惯上也称拼箱、配箱或扣箱。
合箱工作一般按以下步骤进行:(1) 全面检查、清(扫、修理所有砂型和砂芯,特别要注意检查砂芯的烘干程度和通气道是否通畅。
不符合要求者,应进行返修或废弃。
(2) 按下芯次序依次将砂芯装入砂型,并严格检查和保证铸件壁厚、砂芯固定、芯头排气和填补接缝处的间隙。
(3) 仔细清除型内散砂,全面检查下芯质量,在分型面上沿型腔外围放上一圈泥条或石棉绳,以保证合箱后分型面密合,避免液态金属从分型面间隙流出。
随后即可正式合上箱。
(4) 放上压铁或用螺栓、金属卡子固紧铸型。
放好浇口杯、冒口圈。
在分型面四周接缝处抹上砂泥以防止跑火。
最后全面清理场地,以便安全方便地浇注。
三、钢液的熔炼工艺要求:(一)操作流程选择炉料(废钢)→熔化钢液→清理钢液废渣→添加金属矿石→钢液材质化验分析→根据化验分析进行钢液材质处理→脱氧→钢液出炉(一)炉料的选择要求:1、根据准备浇铸件材质的要求,合理选择炉料搭配使用。
产品钢号,应在投料时就控制成份含量。
出炉前半小时取炉前样送检分析。
2、对含有油污,污垢的炉料下炉前要进行清理。
3、对含有镀锌的炉料最好不用。
4、所选用的炉料必须严格控制S、P有害元素的含量。
5、严格遵守熔炼工艺制度。
尽量采用满功率,快速溶炼。
(二)浇注前钢液材质化验出炉前半小时取炉前样送检进行化验分析,钢液的材质应符合铸件材质允许的范围内,不符合的应进行调质,直到符合要求。
(三)脱氧把钢液表面的杂质处理后,进行脱氧处理:1、脱氧剂加入顺序:先加锰铁,后加硅铁,最后加入纯铝。
注:脱氧剂锰铁、硅铁在出炉前5—8分钟加入,纯铝在出炉时加入。
钢液1480—1500℃加锰铁、硅铁,1610—1630℃加纯铝。
2、脱氧剂的加入量(占钢液质量分数%)注:脱氧剂可分多批次加入,钢包每次接钢水前,应放入小块纯铝进行终脱氧处理。
四、浇注工艺要求(一) 浇注前的准备工作(1) 了解浇注合金的种类、牌号、待浇注铸型的数量和估算所需金属液的重量。
(2) 检查浇包的修理质量、烘干预热情况及其运输与倾转机构的灵活性和可靠牲。
(3) 熟悉各种铸型在车间所处的位置,以确定浇注次序。
(4) 检查浇口、冒口圈的安放及铸型的紧固情况。
(5) 清理浇注场地,保证浇注安全。
(二) 浇注操作要点为了获得合格铸件,必须控制浇注温度、浇注速度,严格遵守浇注操作规程。
(1) 浇注温度浇注温度对铸件质量影响很大,因此应根据合金种类、铸件结构和铸型特点确定合理的浇注温度范围。
金属液由炉中注入浇包时,温度都会降低。
根据碳钢的型号,选择适宜的浇注温度,一般浇注温度在1540—1580℃(浇包内钢水温度)。
(2) 浇注操作要点1)浇注之前需除去浇包中金属液面上的熔渣。
2)依规定的浇注速度和时间范围进行浇注。
3)有冒口的铸型,浇注后期应按工艺规范进行点注和补注。
对大中型铸件在浇注成型后,冒口要加保温盐进行保温。
补火要及时,大型冒口要采取多次补火,补火时间要控制在冒口内的钢液凝固结壳前进行。
4)一般浇注大、中型铸钢件时,钢水要在钢包内静置1—2min镇静后进行浇注。
5)在保证型腔内的气体排出顺畅的条件下,对要求同时凝固的铸件可采用较高浇注速度,对要求实现顺序凝固的铸件,尽可能采用较低的浇注速度。
6)较厚大铸件或采用底注式浇注系统时,浇注速度可先快后慢,对薄壁小件浇注速度可先慢后快。
7)温高缓,温低急;引流准、浇注稳,收流猛;包口近杯,不断流,不准碰杯,注意挡渣,防止飞溅,不准半浇,允许点补(缩),遇有穿漏,迅速处理。
8)浇注后待铸件凝固完毕,要及时卸除压铁和箱卡,以减少铸件收缩阻力,避免裂纹。
五、铸件清理铸件凝固冷却到一定温度后,把铸件从砂箱中取出,去掉铸件表面及内腔中的型砂和芯砂的工艺过程称为落砂,落砂通常分为人工落砂和机械落砂两种。
铸件在未完全凝固前,不准搬动铸件,也不准在600℃以上喷水强冷。
铸件一般经自然冷却2—3小时后进行清件。
(一)工作流程清理铸件表面、型腔废砂→气割铸件浇口、冒口、毛刺→再次清理铸件残砂→焊补铸件→打磨铸件→质量验收(二)操作方法及质量标准1、准备工作按照要求佩戴好劳保用品,并对工作环境进行安全确认;准备好所用机器设备和工具,并认真检查,确保机器设备、工具完好,能正常、安全运行和使用。
2、正常操作(1)利用风镐或水清砂机进行铸件废砂清理。
(2)铸件废砂清理完毕,按照《气割安全技术操作规程》操作割枪,切割铸件浇口、冒口、飞边、毛刺。
(3)铸件切割完毕,符合要求。
按照《电焊工安全技术操作规程》操作电焊机,对铸件残缺部位进行焊补,确保铸件完整。
(4)焊补完毕,复合工艺要求。
利用砂轮机对铸件切割、焊补等部位进行打磨处理,保证切割部位和焊补部位光洁、平整。
(5)打磨完毕,进行验收,准备热处理六、铸钢件退火热处理铸钢件退火是将铸钢件加热到AC3以上20-30℃,保温一定时间冷却的热处理工艺。
(一)退火热处理工艺一般要求:1、按照热处理工艺要求升温、冷却。
2、将需要热处理的铸件按合金种类、铸件大小、壁厚相同的类型进行退火。
3、根据铸件的形状、壁厚、化学成分选择合适的加热速度。
(二)退火热处理具体操作1、退火炉的检查(1)炉门关闭正常、严密。
(2)无跑烟、跑火现象。
(3)热电偶完好。
(4)温度仪指示正常。
(5)鼓风机运行正常2、工件填装要求:(1)工件装填不得过于严密,须留有一定空隙。
(2)工件码放须稳固、整齐。
(3)工件码放应坚持防止加热变形的原则。
3、工件加热、保温、降温冷却要求(1)加热:通常以200-400℃/小时的速度加热到860℃.(2)保温:根据工件的厚度确定保温时间为2-3小时左右。
(3)降温:随炉缓慢冷却到500℃后出炉,空气冷却至正常。
(三)工件出炉工件冷却至正常温度后出炉,应分类码放整齐。
七、铸钢件质量验收标准1、外形完整、光洁;无飞边、毛翅、残缺,多肉;无砂眼、气孔、缩孔等铸造缺陷。
2、形状、尺寸,加工量符合铸造工艺图纸要求。
3、各种元素含量在规定范围内。
4、符合GB/T11352-89一般工程用碳钢件的质量标准。
1铸钢件用铸钢制作的零件就是铸钢件了。
与铸铁性能相似,但比铸铁强度好。
铸钢件在铸造过程中易出现气泡、角度定位不准确等缺点,在长期使用中就有可能出现机壳断裂的现象。
2铸钢铸钢用以浇注铸件的钢。
铸造合金的一种。
铸钢分为铸造碳钢、铸造低合金钢和铸造特种钢3类。
①铸造碳钢:以碳为主要合金元素并含有少量其他元素的铸钢。
含碳小于%的为铸造低碳钢,含碳%~%的为铸造中碳钢,含碳大于%的为铸造高碳钢。
随着含碳量的增加,铸造碳钢的强度增大,硬度提高。
铸造碳钢具有较高的强度、塑性和韧性,成本较低,在重型机械中用于制造承受大负荷的零件,如轧钢机机架、水压机底座等;在铁路车辆上用于制造受力大又承受冲击的零件如摇枕、侧架、车轮和车钩等。
②铸造低合金钢:含有锰、铬、铜等合金元素的铸钢。
合金元素总量一般小于5%,具有较大的冲击韧性,并能通过热处理获得更好的机械性能。
铸造低合金钢比碳钢具有较优的使用性能,能减小零件质量,提高使用寿命。
③铸造特种钢:为适应特殊需要而炼制的合金铸钢,品种繁多,通常含有一种或多种的高量合金元素,以获得某种特殊性能。