精益生产经营管理体系
如何构建精益生产体系

如何构建精益生产体系精益生产体系的构建方法精益生产是一种高效率、高质量、灵活性强的生产方式,其基本原理和方法对制造业有着积极的意义。
以下是构建精益生产体系的几种方法:1.准时化准时化是指在需要的时间、按需求量生产所需的产品。
为了实现准时化,需要采用及时生产(JIT)方式控制现场生产流程。
看板管理是其中的一种工具,可以使信息流程缩短,使生产过程中的物料流动顺畅。
及时生产方式的看板信息包括零件号码、品名、制造编号、形式、容量、发出看板编号、移往地点、零件外观等。
看板在生产线上分为领取看板和生产看板。
2.标准作业标准作业是将作业人员、作业顺序、工序设备的布置、物流过程等问题做最适当的组合,以达到生产目标而设立的作业方法。
它是以人的动作为中心、按没有浪费的操作顺序进行生产的方法。
标准作业是管理生产现场的依据,也是改善生产现场的基础。
3.少人化精益生产提高效率的目标之一是少人化。
少人化就是根据产量的多少来增减人工,从而达到用最少的人员满足顾客的生产需求。
实现少人化,必须满足以下3个前提条件:采用一个流生产;要经常审核、修改作业标准和作业标准组合;有具备能操作多种工序的能力的训练有素的作业人员。
4.快速换产快速换产是一种能有效缩短产品切换时间的理论和方法。
切换时间是指从前一种产品加工结束转换到能生产出后一种产品的合格时所需要的时间。
快速换产的理论和方法称为SMED。
5.柔性化柔性生产是通过系统结构、人员组织、运作方式和市场营销等方面的改革,使生产系统能对市场需求变化作出快速的适应,同时消除冗余无用的损耗,力求企业获得更大的效益。
计算机及自动化技术是柔性生产的物质技术基础。
例如柔性制造系统(FMS)是以统一的信息控制系统和自动物料储运系统连接起来的一组加工设备,能在不停机的情况下实现多品种工件的加工,并具有一定管理功能。
柔性生产是全面的,不仅是设备的柔性,还包括管理、人员和软件的综合柔性。
与柔性生产相适应,当前国际上柔性管理也开始出现。
精益生产运营管理体系

精益生产运营管理体系引言精益生产运营管理体系是一种基于精益生产和运营管理原则的综合性管理体系。
它通过消除浪费、提高效率和质量,实现最大化价值创造的目标。
本文将介绍精益生产运营管理体系的原则、方法和实施步骤。
原则精益生产运营管理体系遵循以下原则:1.价值导向精益生产运营管理体系的核心是追求价值创造。
通过从客户角度出发,了解客户的需求和价值观,以及产品或服务对客户的价值,从而确定生产和运营的目标。
2.流程优化精益生产运营管理体系通过优化流程来提高效率和质量。
它通过消除各种类型的浪费,如过度生产、库存过多、等待时间和运输时间过长,实现流程的精益化。
3.持续改进精益生产运营管理体系鼓励持续改进。
通过实施一系列改进活动,包括现场管理、质量管理、团队合作和绩效评估,以实现不断提高生产和运营过程的效率和质量。
方法1.价值流图价值流图是精益生产运营管理体系中的重要工具之一。
它用于识别产品或服务的价值流,并可视化整个生产和运营流程。
价值流图可帮助团队识别和消除流程中的浪费,从而提高效率和质量。
2.5S整理5S整理是一种用于改善工作环境和提高效率的方法。
它包括整理(排序)、整顿(整理)、清扫(清洁)、清洁(清洁)和脚印(维护)五个步骤。
通过实施5S整理,可以创造一个清洁、有序和安全的工作环境,提高工作效率。
3.小步快跑小步快跑是精益生产运营管理体系中的一项重要原则。
它强调通过迭代和快速试验来解决问题和改进流程。
通过快速试验和学习,团队可以快速识别和解决问题,并逐步改进生产和运营过程。
实施步骤1.识别关键价值流首先,团队需要识别关键的产品或服务价值流。
这可以通过与客户和利益相关者进行讨论和分析来实现。
价值流图是一个有用的工具,可以帮助团队可视化整个流程。
2.分析价值流一旦关键价值流被识别,团队将对其进行详细分析。
这包括确定每个步骤的价值、浪费和瓶颈,并识别优化的机会。
价值流图可以帮助团队更好地理解流程中的问题和挑战。
什么是精益生产管理TPS
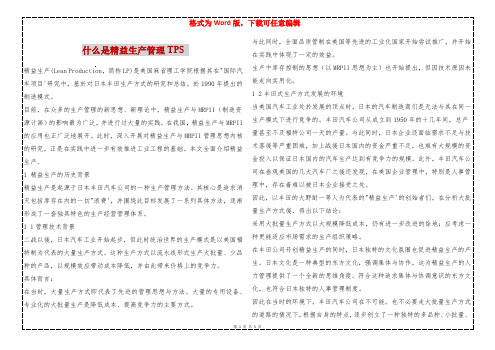
高质量和低消耗的生产方式。
1 3精益生产效率的体现从50年代到70年代,丰田公司虽以独特的生产方式取得了显着的成就,但当时日本及整个西方经济呈现高速增长,即使采用美国相同的大批量生产方式也能取得相当规模的生产效果。
因此,这一时期丰田生产方式并没有受到真正高度的重视,仅仅在丰田汽车公司及其配套商的部分日本企业中得以实施。
1973年的石油危机,给日本的汽车工业带来了前所未有的机遇,同时也将整个西方经济带入了黑暗的缓慢成长期。
市场环境发生变化後,大批量生产所具有的弱点日趋明显,与此同时,丰田公司的业绩开始上升,与其他汽车制造企业的距离越来越大,精益生产方式开始真正为世人所瞩目。
1 4美国对精益生产的研究石油危机以後,丰田生产方式在日本汽车工业企业中得到迅速普及,并体现了巨大的优越性。
此时、整个日本的汽车工业生产水平已迈上了一个新台阶,并在1980年以其1100万辆的产量全面超过美国,成为世界汽车制造第一大国。
在市场竞争中遭受了惨重失败的美国,在经历了曲折的认识过程後,终於意识到致使市场竞争失败的关键,是美国汽车制造业的生产水平已落後於日本,而落後的关键又在於日本采用了全新的生产方式丰田生产方式。
1985年,美国麻省理工学院的Daniel Roos教授等筹资500万美元,用了近5年的时间对90多家汽车厂进行考察,井将大批量生产方式与丰田生产方式进行对比分析,於1995年,出版了《改造世界的机器)("The Machine that changed the World')一书,将丰田生产方式定名为精益生产(Lean Production),并对其管理思想的特点与内涵进行了详细的描述。
1 5世界各国对精益生产的实践随着日本制造业在国际竞争中的节节胜利以及世界各国对精益生产的研究的逐步深入,精益生产方式在实践上也逐步被诸多企业所采用。
首先在汽车行业内,几乎所有的大型汽车制造厂商都开始吸收精益生产的思想,推行"准时化(JIT)'生产,加强企业间的协作┅┅。
精益生产体系

管理百科:精益生产体系“精益生产体系”是由丰田创造的生产管理体系,精益生产体系的结构可以简述为:一个基础、七个支撑和追求七个“零”的极限目标1989年,美国麻省理工学院发表了著名的《改变世界的机器》的报告。
该报告总结了丰田的生产方式,指出它的重大历史意义,并把日本取得成功的生产方式称为“精益生产”。
精益生产的基本目的:企业在运营过程中,要同时获得极高的生产率、极佳的产品质量和很大的生产柔性,并且消除价值流中的一切浪费(降低生产成本)。
在精益生产中,“需求拉动式生产”是其实现基本目的的基础。
需求拉动式生产以准时化生产为核心,以降低成本、持续改善和提高为目标,通过需求拉动式组织方式的实现来逐步消除无效生产,压缩库存储备,降低生产成本,更加及时和有效地满足市场需求的变化,不断改进和完善系统运行方式,从而逐步达到精益生产的要求。
“精益生产体系”的结构可以简述为:一个基础、七个支撑和追求七个“零”的极限目标。
一个基础:即以5S为管理手段的良好现场基础。
所谓5S,即1、整理2、整顿3、清扫4、清洁5、素养。
七个支撑:1、生产的快速转换与维护体系;2、精益品质保证与防错自动化体系;3、柔性化生产体系;4、均衡化和同步化体系;5、现场作业IE研究体系;6、生产设计与高效物流体系;7、产品开发设计体系。
JIT(Just In Time)即准时制生产,有日本丰田公司首先提出,其思想核心是倒排生产计划,提高生产能力和采购能力。
七个极限目标:1、零切换调整2、零库存、3、零浪费4、零不良生产、5、零装备故障6、零生产停滞7、零安全事故精益生产方式JIT支柱与终极目标零浪费为精益生产方式JIT终极目标,具体表现在PICQMDS七个方面,目标细述为:(1)零转产工时浪费(Products0多品种混流生产)将加工工序的品种切换与装配线的转产时间浪费降为零或接近为零。
(2)零库存(Inventory0消减库存)将加工与装配相连接流水化,消除中间库存,变市场预估生产为接单同步生产,将产品库存降为零。
精益管理体系构建浅谈
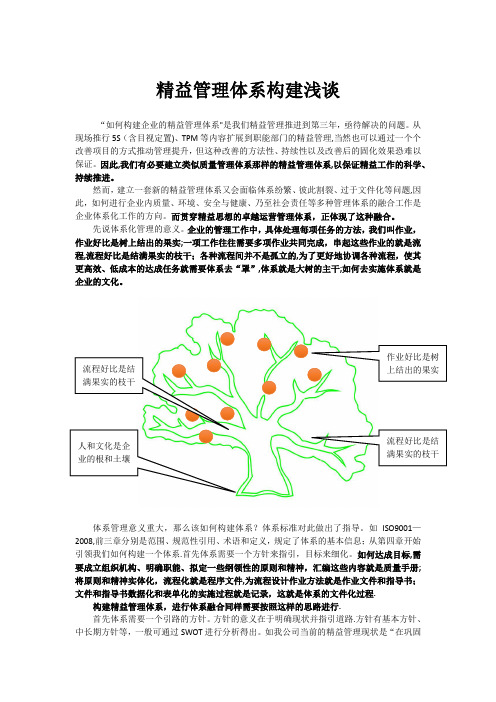
精益管理体系构建浅谈“如何构建企业的精益管理体系"是我们精益管理推进到第三年,亟待解决的问题。
从现场推行5S (含目视定置)、TPM 等内容扩展到职能部门的精益管理,当然也可以通过一个个改善项目的方式推动管理提升,但这种改善的方法性、持续性以及改善后的固化效果恐难以保证。
因此,我们有必要建立类似质量管理体系那样的精益管理体系,以保证精益工作的科学、持续推进。
然而,建立一套新的精益管理体系又会面临体系纷繁、彼此割裂、过于文件化等问题,因此,如何进行企业内质量、环境、安全与健康、乃至社会责任等多种管理体系的融合工作是企业体系化工作的方向。
而贯穿精益思想的卓越运营管理体系,正体现了这种融合。
先说体系化管理的意义。
企业的管理工作中,具体处理每项任务的方法,我们叫作业,作业好比是树上结出的果实;一项工作往往需要多项作业共同完成,串起这些作业的就是流程,流程好比是结满果实的枝干;各种流程间并不是孤立的,为了更好地协调各种流程,使其更高效、低成本的达成任务就需要体系去“罩”,体系就是大树的主干;如何去实施体系就是企业的文化。
体系管理意义重大,那么该如何构建体系?体系标准对此做出了指导。
如ISO9001—2008,前三章分别是范围、规范性引用、术语和定义,规定了体系的基本信息;从第四章开始引领我们如何构建一个体系.首先体系需要一个方针来指引,目标来细化。
如何达成目标,需要成立组织机构、明确职能、拟定一些纲领性的原则和精神,汇编这些内容就是质量手册;将原则和精神实体化,流程化就是程序文件,为流程设计作业方法就是作业文件和指导书;文件和指导书数据化和表单化的实施过程就是记录,这就是体系的文件化过程. 构建精益管理体系,进行体系融合同样需要按照这样的思路进行.首先体系需要一个引路的方针。
方针的意义在于明确现状并指引道路.方针有基本方针、中长期方针等,一般可通过SWOT 进行分析得出。
如我公司当前的精益管理现状是“在巩固作业好比是树上结出的果实 流程好比是结满果实的枝干 流程好比是结满果实的枝干 人和文化是企业的根和土壤现场改善的基础上,正逐步拉动从设计、人力资源、运营(计划、采购、质量、生产)到营销等各部门开展解决问题、提高效率、降低成本的改善工作。
精益生产管理体系及三大要点

精益生产管理体系及三大要点精益生产管理体系(Lean Production Management System)是一种提升生产效率、降低成本和提高质量的管理方法和理念。
它是在日本丰田生产方式(Toyota Production System)的基础上发展起来的,旨在通过消除浪费、优化流程和提高员工参与度来实现持续的改善和精益化生产。
精益生产管理体系的三大要点是:1. 消除浪费(Eliminate Waste):精益生产管理体系的核心是消除浪费。
浪费是指任何不会增加产品或服务价值的活动或过程。
常见的浪费包括等待、过产、运输、库存、生产缺陷等。
通过识别和消除浪费,企业可以提高效率、降低成本并提高产品质量。
消除浪费需要全员参与,通过改进工作流程和制度来减少浪费的发生,从而达到提升整体生产效率和竞争力的目标。
2. 规范化流程(Standardize Processes):精益生产管理体系强调规范化的工作流程。
通过制定明确的工作规范和流程,可以减少变动和不确定性,提高生产过程的稳定性和一致性。
规范化流程可以减少错误和缺陷的发生,提高产品质量,并减少员工在执行任务时的不确定性和错误率。
通过标准化工作流程,企业还可以更好地掌握生产情况,及时调整和改进,实现持续改善。
3. 培养员工参与意识(Cultivate Employee Involvement):精益生产管理体系强调员工的积极参与和持续改进的文化。
企业需要鼓励员工参与生产过程的改善,并提供相关的培训和支持。
员工参与意识的培养可以激发员工的创新和贡献,促进团队合作和沟通,并建立起持续改进的机制。
员工是生产线上最了解实际情况的人,他们的参与和反馈可以帮助企业改善工作环境、流程和产品质量,从而提高整体生产效率。
总之,精益生产管理体系是一种通过消除浪费、规范化流程和培养员工参与意识来提升生产效率和产品质量的管理方法。
企业可以通过积极实施精益生产管理体系,不断改进和优化生产过程,提高竞争力和市场份额。
精益生产管理(完整版)

第一章精益生产的思想和方法企业经营的目的是向社会提供产品和服务,同时为企业创造利润。
为达到这一目的,企业必须投入人员、材料、设备、资金等资源,并通过对它们的有效使用和优化组合制造出社会所需要的产品.而利润的高低取决于投入和有效产出1的比例,即生产效率,班组是使产品增值的基本单元,是提高生产效率的主战场。
提高生产效率有以下三种途径:1.投入不变,产出增加;2.产出不变,投入减少;3。
投入减少,产出增加。
第一种途径适用于产品的成长期2,即市场对该产品的需求呈上升趋势的阶段;第二种途径适用于产品的成熟期或衰退期,即市场对该产品的需求渐趋稳定或下降的阶段;第三种途径显然是最理想的,因而难度也是最大的。
但是, 市场竞争的结果最终将导致第一和第二种途径的失效,从而使企业的经营状况步入低谷。
要避免这种状况,就必须采用第三种途径.精益生产的成功有力地证明了这一途径的优越性和有效性。
第一节精益生产的诞生及其特点精益生产方式是继单件生产方式和大量生产方式之后在日本丰田汽车公司诞生的全新生产方式。
精益的“精”就是指更少的投入,而“益”指更多的产出。
本世纪中叶,当美国的汽车工业处于发展的顶峰时,以大野耐一为代表的丰田人对美国的大量生产方式进行了彻底的分析,得出了两条结论:1.大量生产方式在削减成本方面的潜力要远远超过其规模效应所带来的好处2。
大量生产方式的纵向泰勒制3组织体制不利于企业对市场的适应和职工积极性、智慧和创造力的发挥基于这两点认识,丰田公司根据自身面临需求不足、技术落后、资金短缺等严重困难的特点,同时结合日本独特的文化背景,逐步创立了一种全新的多品种、小批量、高效益和低消耗的生产方式.这种生产方式在1973年的石油危机中体现了巨大的优越性,并成为80年代日本在汽车市场竞争中战胜美国的法宝,从而促使美国化费500万美元和5年时间对日本的生产方式进行考察和研究,并把这种生产方式重新命名为精益生产(LEAN PRODUCTION)。
精益生产管理体系

精益⽣产管理体系精益⽣产管理体系是⼀个包含了多种制造技术和管理技术的综合体系。
该体系由标准作业、均衡⽣产等基础性管理活动,以及准时化⽣产和⾃动化两⼤⽀柱构成。
⼀、标准作业标准作业是指在⽣产过程中,以⼈的操作为中⼼,去掉浪费的动作,把有价值的作业编排成有效的操作顺序,使之与设备布局以及节拍时间相吻合。
标准作业经过对作业⽅法的研究后制定标准作业程序,包括对有关设施、环境、材料、负荷、动作等进⾏标准化。
实⾏标准作业的前提是以⼈的动作为中⼼考虑问题,并且是在同样条件下能够重复进⾏的作业。
⼆、均衡⽣产⽣产的均衡化是实现精益⽣产管理的最重要的前提条件。
均衡化⽣产要求的是⽣产数量的均衡和产品种类的均衡,即总装配线向各前⼯序领取零部件时,要均匀地领取各种零部件,实⾏混流⽣产。
要防⽌在某⼀段时间内集中⽣产同⼀种零部件,以免造成前⽅⼯序的闲忙不均,以及由此引发的⽣产混乱。
⽣产的均衡化使得零部件被领取时的数量变化达到最低程度,即各⼯序每天如⼀地以相近似的时间间隔领取数量相近的零部件,由此,各⼯序得以⼀定速度和⼀定数量进⾏⽣产。
均衡还包括⼯时、设备负荷的全部均衡。
设备、⼯装始终处于良好状态,材料、⽑坯供应准时,⼯⼈技术⽔平和出勤率良好、稳定等都是实现均衡⽣产的前提。
此外,加强⽣产技术准备部门、辅助⽣产部门、供应服务部门的⼯作,特别是优化⽣产计划和强化对⽣产过程的监控,则是实现均衡⽣产的重要保证。
三、⾃动化⾃动化是精益⽣产⽅式的两⼤⽀柱之⼀,也被称为“智能⾃动化”或者“具有⼈的判断能⼒的⾃动化”。
是让设备能⾃律地控制异常情况,是具有⼈的判断能⼒的⾃动化,⾃动化的主要理念是:应该在作业流程中及时进⾏源头质量管理,必须⽤有效的⽅法在发⽣异常或质量缺陷时⽴即探测到,并⽴即使⽣产暂停,使员⼯可以⽴即解决问题,避免异常扩⼤或质量缺陷进⼊到下游流程。
这种品质管理⽐事后检验出问题再设法纠正问题更具成效且成本更低。
⾃动化在很多时候含有“⾃动化”的含义,但绝不仅仅限于⽤机械化设备代替⼿⼯作业。
- 1、下载文档前请自行甄别文档内容的完整性,平台不提供额外的编辑、内容补充、找答案等附加服务。
- 2、"仅部分预览"的文档,不可在线预览部分如存在完整性等问题,可反馈申请退款(可完整预览的文档不适用该条件!)。
- 3、如文档侵犯您的权益,请联系客服反馈,我们会尽快为您处理(人工客服工作时间:9:00-18:30)。
精益生产经营管理体系主办单位:上海普瑞思管理咨询有限公司时间:2010年12月24-25日深圳培训费用:3800元/位(含培训费、讲义费、午餐、茶水费、奖品、税费、笔记本)【课程背景】◆丰田公司一部汽车平均赚取2000美金;同期通用公司平均每部车赚200美金。
10倍,为什么整整相差10倍?◆善于反思与学习的美国由麻省理工学院,投入5年时间与众多一流学者,基于对日本丰田生产方式(Toyota Production System)的研究与总结,提出的一种生产管理新思想:精益生产(Lean Production,简称LP)这种核心是消灭一切“浪费”的思想,并围绕此目标发展了一系列流线化、TPM、看板管理、IE技术等具体方法,逐渐形成了一套独具特色的生产经营管理体系。
◆精益生产究竟是什么?究竟在做什么?◆理解错误可能从初始就导致了应用的失败。
“理不明则行不正”,正确的认识与理解,对精益的实现生死攸关,甚至直接影响到企业十年后的市场地位。
【课程目标】◆掌握精益生产的核心原理及思想精髓,如何通过推行精益生产来提升经营业绩;◆学习精益价值流(VSM)图,从精益价值流切入剖析工厂制造成本,掌握通过精益价值流改善缩短制造周期的方法;◆学习精益生产常用工具:价值流图、现场七大浪费、SMED等,价值分析及浪费识别的工具、方法,通过运用消除浪费的工具即刻提升生产效率30%◆掌握建立拉动式(PULL)生产系统的方法,通过拉动式生产实施降低库存50%,大幅缩短制造周期;◆学习如何通过单元化生产(CELL PRODUCTION)实施化解多品种少批量给企业带来的困惑;◆掌握快速换线SMED的精髓及实施步骤,全面提高设备整体效率(OEE),彻底降低设备成本;◆精益生产的价值体现:精益生产为企业带来的效益分析,制造业如何通过精益生产的有效实施提升核心竞争力;◆精益生产成功实施的管理基础:精益生产要求下的的计划物控(PMC)体系;供应商管理体系;生产现场管理体系;IE工程支持体系分析;◆精益生产项目管理技巧:精益生产项目推行组织设计;项目的策划与计划;精益生产项目实施过程中的日常管理;精益生产项目负责人必备的基本能力。
【培训形式】◆世界及国内著名企业通过推行精益生产降低成本的改善案例分享;◆课程内容实战性,技术性强,寓理论于实战方法中,课堂生动,让学员在轻松的环境中演练管理技术,达到即学即用的效果。
【课程大纲】一. 精益生产基础⊙精益生产的起源及其发展⊙丰田生产系统(TPS)管理精髓⊙影片欣赏:TPS诞生历史记录片⊙精益生产的基本原理⊙从客户的角度认识价值⊙识别流程中非增值(浪费)的活动⊙精益价值流图简介⊙精益价值流图制作方法⊙如何通过精益价值流图实施工厂管理改善⊙精益生产工具:增值活动识别(VALUE);精益价值流图(VSM)二. JIT拉动式生产系统⊙制造周期时间(MCT)定义及计算方法⊙拉动系统的种类及其运用⊙物料补充拉动系统⊙准时化交货JIT/KANBAN的定义⊙生产线物料补充系统定义及建立方法⊙生产线物料补充频率计算⊙生产线物料补充看板数量计算⊙生产线流程间半成品看板数量计算⊙经济性批量计算方法⊙采购物料补充拉动系统简介⊙供应商管理库存(VMI)与准时化交货(JIT)⊙准时化交货JIT/KANBAN的有效实施⊙小组活动:拉动式生产模拟⊙精益生产工具:制造周期时间(MCT);KANBAN拉动式生产;采购补充拉动系统(PULL);供应商管理库存VMI/JIT三. 七大浪费与效率改善⊙现场七大浪费的定义与分析⊙效率的定义与分析⊙运输带来的浪费分析⊙如何通过工厂布局改善减少运输浪费⊙如何通过流程及工具优化减少运输浪费⊙库存带来的浪费分析⊙如何通过改善计划物控管理降低库存⊙如何通过生产流程优化降低库存⊙动作浪费与损失分析⊙消除动作浪费的原则与方法⊙等待造成的工厂效率损失分析⊙如何通过改善异常时间管理减少等待⊙如何通过生产线平衡优化减少等待损失⊙缺陷与重复处理带来的浪费分析⊙防错防呆(POKAYOKE)原理⊙防错防呆在生产现场管理中的运用⊙精益生产工具:七大浪费;防错防呆、生产线平衡与改善方法四. 单元化布局及快速换线⊙生产线布局的设计原则⊙单元化布局原理及在生产中的运用⊙单元化布局设计及管理方法⊙如何通过单元化布局的运用缩短制造周期⊙如何通过单元化生产化解多品种少批量给企业带来的困惑⊙工厂中设备使用成本分析⊙综合设备效率(OEE)定义⊙影响综合设备效率的因素分析⊙OEE计算方法及分析技巧⊙综合设备效率(OEE)改善实施步骤⊙生产换线效率损失分析⊙快速换线SMED定义及发展历史⊙SMED实施要点及推行步骤⊙SMED实施成功案例分享⊙工厂成功实施精益生产改善的关键⊙精益生产项目实施的不同组织模式⊙精益生产工具:OEE设备效率管理;单元化生产(CELL)、SMED快速换线方法五. 精益工厂的管理基础1.计划物控(PMC)与精益生产⊙计划物控的职能及组织结构分析:传统意义PMC的职能分析;PMC不健全的企业管理后果⊙PMC精益管理与拉动式生产建立传统的生产计划与拉动式生产计划的区别;拉动式生产计划有效实施的条件与基础⊙物料控制与精益生产传统的物料需求分析与精益物料需求分析的区别;传统物料控制与精益物料控制的区别⊙衡量精益PMC组织的绩效指标:库存、制造周期、OTD2.供应商管理与精益生产⊙供应商的选择准则:匹配、距离、价格竞争力、快速反应⊙供应商质量管理方法:供应商的审核与评估;供应商退出机制;供应商辅导与提升;供应商及时供货(JIT)的来料质量管理⊙建立精益供应链:多品种少批量供货支持;准时化交付体系(JIT)支持;供应商管理库存(VMI)3.生产执行与精益生产⊙标准化作业的实施:标准化作业实施方法;为什么说标准化作业是现场改善的起点和基础?⊙现场5S与目视化:做好5S及目视化管理的最基本要求;5S及目视化对精益上产纵深推进的意义⊙生产主管在精益生产中的角色:现场改善的主导者:IE? 精益专员?还是生产主管?各自的利弊分析4.工程部门(IE)精益生产⊙工业工程(IE)在工厂的职能定位组织架构;工作范围;对企业的贡献分析⊙IE在推行精益生产过程中的角色:支持角色 VS 主推角色六. 精益生产项目管理技巧1.精益生产项目经理必备的能力⊙组织策划能力:精益生产项目的范围;阶段性目标;参与的部门与人员;项目预期收益;资源投入等⊙团队管理能力:精益生产项目团队的管理;如何提升项目经理的影响力与执行力;团队激励措施⊙沟通协调能力:项目经理的沟通技巧;如何提高与团队成员的沟通效果;2.精益生产项目实施步骤⊙项目启动的必要条件:合适的团队组建;成员职责、目标;最高管理者授权;启动大会的规格与主持⊙项目中短期计划的制定:项目的分解计划;样板线、试点工程的选择;项目月计划、周计划⊙项目进度控制:现场项目管理与问题解决;周项目进度会议;月总结会议;日常进度沟通⊙项目阶段性总结:阶段性总结报告;收益分析;改善案例展示与宣传;颁奖与激励3.项目实施过程中的问题与解决⊙部门协作问题:其他部门为何很被动?为什么有人“阳奉阴违“?⊙失败的挫折:如何面对不成功的改善?样板线效率不升反降怎么办?⊙Q&A:学员提问及问题解答答【主讲老师】罗忠源(JAMES LUO)◆精益制造及制造成本管理专家,首席顾问。
◆知名制造业实战派讲师,资深顾问。
◆机械工程学士、工商管理硕士(MBA),拥有十多年著名外资企业生产、工程、品质及供应链中高层管理经验。
背景经历:亚洲最大的精密五金冲压、注塑产品服务提供商AMTEK公司生产及工程经理,著名港资EMS企业NAMTAI GROUP 生产工程经理,世界500强FLEXTRONICS供应商品质、IE工程、运营及精益生产六西格玛高级经理。
罗老师具有多年的管理顾问及培训经验,服务过的企业获得了良好收益。
为许多客户主导实施过精益管理改善项目,获得广泛好评。
核心领域:精益生产-六西格玛管理培训、精益工厂建立与管理、IE工业工程、质量管理、制造业成本管理、制造业项目管理等专题培训及专案咨询辅导。
服务企业:美的集团、伟易达集团、立白集团、德国BOSCH、台湾蔚盛集团、香港亚伦电器、烽火通讯、麦科特光电、高飞电子、美律电子(深圳)有限公司、久隆汽车配件、台资国威运动器材、港泰玩具、阿波罗(中国)有限公司、瑞声科技、当纳利印刷、九星印刷、中威制衣、昌利行、乐华(箭牌)陶瓷、濮耐股份、长沙卷烟厂、大同机械、龙大食品等。
杰出成果:1、在FLEXTRONICS独立完成6个黑带项目和推行精益生产系统及指导企业内部管理改善,领导团队为企业节省近500万美元成本2、主导FLEXTRONICS DG精益价值流(VSM)分析和改善,使其所辅导的工厂生产效率提升约25%;3、2006年3月带领导团队辅导美的电磁炉厂精益生产及制程品质改善项目,短时间内效率提升约20%;4、2006年8月带领团队进驻阿波罗实施精益流程改善项目,揭开阿波罗这家大型民营企业的改革序目,效率4个月内提升50%以上;5、 2007年2月年带领团队为美的日电集团下属的:美的微波电器事业部; 美的洗碗机事业部;美的热水器;美的厨房电器;美的环境电器事业部(风扇)全面推行精益运营管理;6、2008年3月带领团队为台资美律电子提供精益生产咨询辅导服务;主要生产线效率提升20%以上。