表面处理的基本知识
合金表面处理基本知识

合金表面处理基本知识表面处理即是通过一定的方法在工件表面形成覆盖层的过程,其目的是赋以制品表面美观、防腐蚀的效果,进行的表面处理方法都归结于以下常用几种方法:1、镀(Plating)电镀(Electroplating) :将接受电镀的部件浸于含有被沉积金属化合物的水溶液中,以电流通过镀液,使电镀金属析出并沉积在部件上。
一般电镀有镀锌、铜、镍、铬、铜镍合金等,有时把煮黑(发蓝)、磷化等也包括其中。
2、热浸镀锌:通过将碳钢部件浸没温度约为510℃的溶化锌的镀槽内完成。
其结果是钢件表面上的铁锌合金渐渐变成产品外表面上的钝化锌。
热浸镀铝是一个类似的过程。
3、机械镀:通过镀层金属的微粒来冲击产品表面,并将涂层冷焊到产品的表面上。
一般螺丝多采用电镀方式,但用在电力、高速公路等室外的六角木螺钉等用热浸锌;电镀的成本一般每公斤为0.6——0.8元,热浸锌一般为1.5——2元/公斤,成本较高。
电镀的效果:电镀的质量以其耐腐蚀能力为主要衡量标准,其次是外观。
耐腐蚀能力即是模仿产品工作环境,设置为试验条件,对其加以腐蚀试验。
电镀产品的质量从以下方面加以控制:1、外观:制品表面不允许有局部无镀层、烧焦、粗糙、灰暗、起皮、结皮状况和明显条纹,不允许有针孔麻点、黑色镀渣、钝化膜疏松、龟裂、脱落和严重的钝化痕迹。
2、镀层厚度:紧固件在腐蚀性大气中的作业寿命与它的镀层厚度成正比。
一般建议的经济电镀镀层厚度为0.00015in~0.0005 in(4~12um).热浸镀锌:标准的平均厚度为54 um(称呼径≤3/8为43 um),最小厚度为43 um(称呼径≤3/8为37 um)。
3、镀层分布:采用不同的沉积方法,镀层在紧固件表面上的聚集方式也不同。
电镀时镀层金属不是均匀地沉积在外周边缘上,转角处获得较厚镀层。
在紧固件的螺纹部分,最厚的镀层位于螺纹牙顶,沿着螺纹侧面渐渐变薄,在牙底处沉积最薄,而热浸镀锌正好相反,较厚的镀层沉积在内转角和螺纹底部,机械镀的镀层金属沉积倾向与热浸镀相同,但是更为光滑而且在整个表面上厚度要均匀得多。
公共基础知识表面处理技术基础知识概述
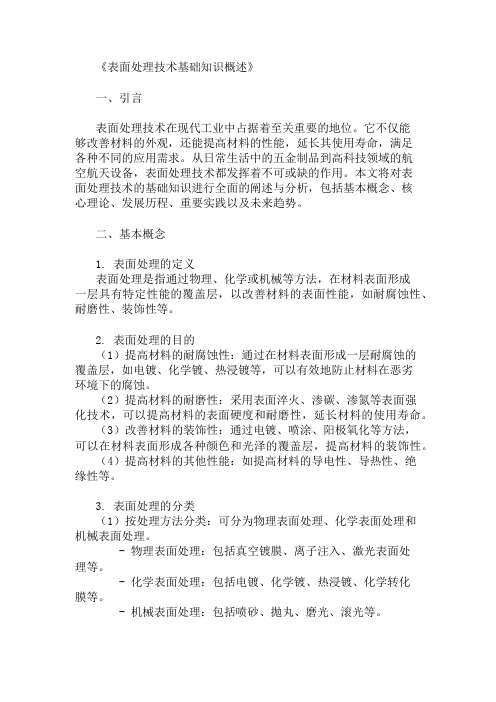
《表面处理技术基础知识概述》一、引言表面处理技术在现代工业中占据着至关重要的地位。
它不仅能够改善材料的外观,还能提高材料的性能,延长其使用寿命,满足各种不同的应用需求。
从日常生活中的五金制品到高科技领域的航空航天设备,表面处理技术都发挥着不可或缺的作用。
本文将对表面处理技术的基础知识进行全面的阐述与分析,包括基本概念、核心理论、发展历程、重要实践以及未来趋势。
二、基本概念1. 表面处理的定义表面处理是指通过物理、化学或机械等方法,在材料表面形成一层具有特定性能的覆盖层,以改善材料的表面性能,如耐腐蚀性、耐磨性、装饰性等。
2. 表面处理的目的(1)提高材料的耐腐蚀性:通过在材料表面形成一层耐腐蚀的覆盖层,如电镀、化学镀、热浸镀等,可以有效地防止材料在恶劣环境下的腐蚀。
(2)提高材料的耐磨性:采用表面淬火、渗碳、渗氮等表面强化技术,可以提高材料的表面硬度和耐磨性,延长材料的使用寿命。
(3)改善材料的装饰性:通过电镀、喷涂、阳极氧化等方法,可以在材料表面形成各种颜色和光泽的覆盖层,提高材料的装饰性。
(4)提高材料的其他性能:如提高材料的导电性、导热性、绝缘性等。
3. 表面处理的分类(1)按处理方法分类:可分为物理表面处理、化学表面处理和机械表面处理。
- 物理表面处理:包括真空镀膜、离子注入、激光表面处理等。
- 化学表面处理:包括电镀、化学镀、热浸镀、化学转化膜等。
- 机械表面处理:包括喷砂、抛丸、磨光、滚光等。
(2)按处理目的分类:可分为防护性表面处理、装饰性表面处理和功能性表面处理。
- 防护性表面处理:主要目的是提高材料的耐腐蚀性和耐磨性。
- 装饰性表面处理:主要目的是改善材料的外观,提高其装饰性。
- 功能性表面处理:主要目的是提高材料的特定性能,如导电性、导热性、绝缘性等。
三、核心理论1. 表面物理化学表面物理化学是研究材料表面的物理和化学性质的学科。
它涉及到表面张力、表面能、吸附、润湿等概念。
在表面处理过程中,了解材料表面的物理化学性质对于选择合适的处理方法和工艺参数至关重要。
表面处理知识

耐蚀钢
防锈铝
镜面材料
2.表面处理在金属防护方面的作用
防止金属腐蚀的方法主要包括三个方面:
2)改善腐蚀环境和介质
避免腐蚀发生
物
干燥剂
体
产品
2.表面处理在金属防护方面的作用
防止金属腐蚀的方法主要包括三个方面:
3)应用表面涂覆层和电化学保护方法
隔离金属与腐蚀介质的直接接触 抑制腐蚀过程
非金属覆盖
电镀 热喷涂 热浸镀 耐蚀金属包复
涂料涂装(喷漆、喷粉) 塑料衬里或包复 转化膜
2.表面处理在金属防护方面的作用
金属表面保护层的要求 即金属上涂覆层的基本性能
1)结合强度--要求结合牢固、附着力强 2)孔隙率及密度--膜层致密、完整无孔、不透介质 3)耐蚀性--在大气、水、等介质中良好的稳定性、
7.1 镀锌层
由于锌相对于铁基体为阳极性镀层,在有电解液存在时,锌层为 阳极,先发生腐蚀,从而钢基体受到了保护
镀层中存在微孔 钝化膜是致密的
钝化膜 镀锌层
钢基材
7、膜层结构特点及其防护机理与防护能力
7.1 镀锌层
在遭遇腐蚀介质时: 首先是钝化膜产生腐蚀变化(即变黑); 当钝化膜被腐蚀穿底后,发生锌层的腐蚀、氧化,即出现白色粉状物。
e A
E
e
+
R
阴
+ 阳离子 阳
极 电解液
极
阴离子 -
5.2 表面转化
5.2.1 阳极氧化机理
氧化膜的生长过程包含两 个方面
膜的电化学生成过程 膜的化学溶解过程
只有膜层的生成速度恒大于溶解速度时,才 能获得较厚的氧化膜
5.2 表面转化
5.2.1 阳极氧化机理
金属表面处理工艺基础知识

一.鋁及其合金的表面處理二.不鏽鋼的表面處理三.手機金屬表面處理工藝簡述一、AL表面處理:噴砂發絲蝕刻可以根據需要將鏡面、噴砂面、發絲面組合成不同的表面效果。
表面處理樣品一:拋光+噴砂拋光鏡面拋光+發絲陽極處理雙色陽極雙色陽極表面處理樣品二:蝕刻+陽極二、SUS 表面處理:發絲PVD 、電鍍可根據需要而選用。
發絲拋光+噴砂噴砂+發絲蝕刻LOGO表面處理樣品一:蝕刻圖案拋光鏡面拋光+發絲噴砂表面處理樣品二:表面處理樣品三:表面處理綜合:經過表面處理的產品不再隻有單一顏色、單一效果,可以加上各種圖案、紋理以及同時展現多種表面效果,為產品注入新的創意,呈現特別的風貌。
三.手機金屬表面處理振動研磨(11)機械拋光(23)化學蝕刻(37)陽極(62)鑽雕(82)移印&絲印(96)電泳涂裝(110)振動研磨1.振動研磨的原理工作物與研磨機在機器的圓環型盆內作螺旋和軌形路線進行,機器本身重量與支撐的彈簧使研磨機環狀盆座上、下、左、右高頻率振幅的轉動,研磨機內工作物運轉的速度由上、下馬達重量的差度來調整變化。
2.研磨的功能去毛刺(研磨所能去掉的毛刺是指沖壓時由於刀口變鈍而未切除的余料);去臟污,提高表面光潔度。
噴砂工藝噴砂+陽極噴砂的定義:噴砂的設備半自動設備1手動設備全自動設備喷砂的目的1.达到粗化表面的效果2.去油污,氧化皮,砂眼3.去除毛刺,毛边4.消除工件应力5.增加工件表面附着力,可作电镀,喷漆,阳极等的前处理加工•機械拋光的特點與機理•拋光的應用•拋光耗材介紹•拋光機台的種類•拋光不良原因的分析機械拋光的特點與機理一.拋光特點:拋光是對零件表面進行的光飾加工,主要是去除上道工序的加工痕跡,如刀痕,劃印,麻點.尖棱.毛刺等改善零件表面粗糙度,獲得光亮平整的表面,增加美觀.可提高工件抗疲勞和抗腐蝕的性能.二.拋光機理:拋光是切削加工, 塑性加工和化學作用的綜合過程.微細磨粒進行的是切削加工.磨擦引起高溫而產生擠擦工件表面層的是塑性加工.拋光劑的介質在溫度和壓力作用下與金屬表面層發生的是化學作用三. 拋光類型•粗拋:是用砂輪.砂帶對經過或未經過磨光的表面進行拋光,它對基材有一定的磨削作用,能去除較粗的磨痕.拉傷及輕微變形•中拋:是用較硬的拋光輪(如麻輪)對經過粗拋的表面作進一步的加工,它可除去粗拋留下的劃痕,產生中等光亮的表面.•精拋:用軟輪(多數用棉布輪)拋光獲得鏡面般光亮表面,它對基本材料的磨削最小.是拋光的最后工序.拋光的應用珠寶首飾餐炊廚房機動車無線通訊拋光耗材的介紹拋光劑:拋光劑常溫下分固體,液體兩種.固體拋光膏又分為油脂性和非油脂性兩類,液體拋光劑分為乳濁狀型,液體油型及液狀非油脂型三類.拋光機台的種類手動拋光機拋光輪拋光機馬達吸塵管工作原理:利用驅動馬達帶動圓盤使其行進,工件主軸之齒輪被鏈條循序帶動前進且自轉,當工件主軸行進至布輪下方時,仍連續前進且自轉,從而使工件和拋光布輪產生摩擦,達到工件表面光亮之效果.化學蝕刻目錄⏹一.化學蝕刻概述⏹二.蝕刻理論介紹一.化學蝕刻概述1.1 什么是化學蝕刻?針對金屬材料的不同化學特性,選擇特定的化學試劑與其反應,最終形成具一定精度尺寸的各種所需圖案的過程.1.2 適用材質?Al(鋁合金)、SUS(不鏽鋼)?二.蝕刻理論介紹2.1 化學蝕刻技術主要應用於:a. PCB製造b.標牌銘板類製作2.2 核心技術包括:a.防蝕遮蔽b.圖案生成c.蝕刻d.去遮蔽陽極一.陽極概述二.陽極產品介紹五.陽極不良分析一.陽極概述1>1移動通訊產品對陽極氧化工藝的要求a.很好的防護性與裝飾性b.耐磨性,有較高硬度c.色澤均一,膜層透明d.外面面不允許的缺陷1>3 應用飾物化妝品美容品建材交通3c產品203040504820226024時間/s 電壓/V2>7鋁陽極氧化膜生成曲線A.膜層生長B.陰擋層形成C.膜層穩定生成,直到溶解與生長速率達到平衡陽極生產線主線陽極生產用的挂具二.陽極產品介紹Display frame樣品鑽雕一.鉆石雕刻概述二.設備組成三.鉆雕加工的特點四.鉆石雕刻的目的一.鉆石雕刻概述鉆石雕刻是一種機械表面加工方法, 一般來說作為需雕刻的工件,其表面比較粗糙且不平整,為了獲得光亮平整的表面,就需要采用一些機械加工的方法加以修飾,而鉆石雕刻可獲光亮平整且條紋均勻一致的表面,因而很多工件機械表面加工都采用鉆石雕刻加工的方法,目前鉆石雕刻技術廣泛應用於銘板,手機外殼,標志等字模或圖案表面之加工.四.鉆石雕刻的目的●獲得平整,光亮的外觀●獲得均勻一致的條紋移印&絲印介紹。
表面处理基本知识
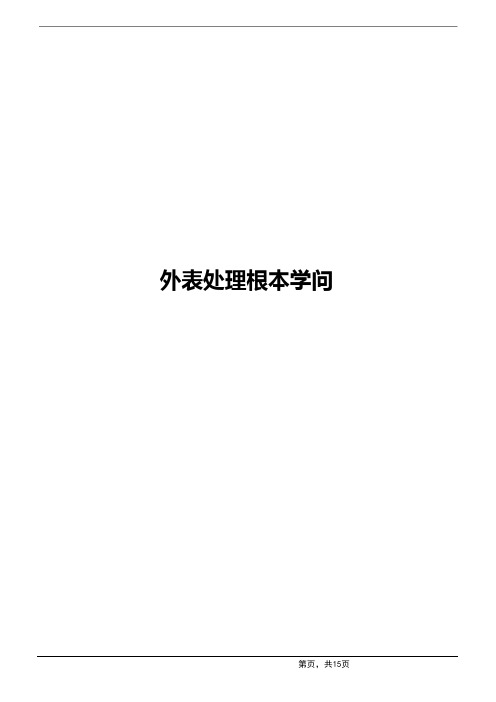
外表处理根本学问V2 筒状砂带工件V1移开工作台前言用物理或化学方法来转变工件外表的状态,通过去除或添加肯定的材料对工件外表进展肯定的处理,从而获得所需要的一些外表的性能,如除油,防锈,装饰,抗氧化等等统称外表处理。
由于外表处理种类较多且受篇幅限制,仅对以下几种我司常见的外表处理作根本介绍。
第一章 拉丝拉丝是一种砂带磨削加工,通过砂带对金属外表进展磨削加工,以去除金属外表缺陷,并形成具有肯定粗糙度,纹路均匀的装饰外表。
工作原理见以下图:从上图可以看出,当工作台面带开工件移动(速度为 V1),同时砂纸也以肯定的速度(V2)在转动,但 V1 和 V2 速度不相等,存在有肯定的速度差。
砂纸与工作台之间的间隙预先已调整好, 当工件被送到工作台和砂纸之间。
砂纸与工件产生相对的运动,工件就被拉出沿运动方向的纹路。
一、加工范围参数:拉丝机有效拉丝最大宽度(指垂直于拉丝方向的外形尺寸)为 850mm 。
拉丝方向最小外形尺寸要大于 235mm 。
假设长度不够,则需要作拉丝治具。
治具使用标准:用两层板焊接起来,其中下层为 2.0mm 厚的平板,上层为套材料的治具,但板厚略小于所需拉丝材料的板厚。
拉丝机适用最小料厚:0.5mm 。
二、加工特性:砂纸有不同的型号规格﹐ 其主要参数指针为每平方英寸所包含的砂粒的数目﹐ 如180#,220#砂纸,数值越大﹐表示单位面积所含的砂粒越多﹐所形成的纹路也就越细越浅 ,反之, 砂纸的型号越小,砂粒越粗所形成的纹路也就越粗越深.因此在工程图面上必需注明砂纸型号.假设没有特别说明和要求﹐一般选用 220#砂纸。
拉丝具有方向性:工程图面上必需注明是直纹还横纹拉丝(用双箭头表示)拉丝工件的拉丝面不能有任何凸起局部 ,否则会将该凸起局部拉平.非拉丝面允许消灭凸起 ﹐但前题是在拉丝时能避开此凸起或者做治具将工件垫起。
由于拉丝也属于一种磨削式加工﹐工件外表有去除材料﹐所以一般状况下拉丝工艺应当优先于其它外表处理进展﹐拉丝后再作电镀,氧化﹐烤漆等处理。
表面处理知识

• 镀层硬度:采用显微硬度计进行检测,一般有洛式硬 度,维式硬度,布氏硬度等 • 结合力:我司常用检测方法有两种。 • 弯折法:将试件弯折90度再复位,弯折处镀层无剥 落,开裂。 • 试锉法:将试件截断,用锉刀与试件截面呈45度角 来回试锉,镀层无剥落。 • 色差:对比色样采用目测检验。 • 耐高温测试:用高温测试烤箱检测,在一定温度及时 间里试件表面镀层无开裂,剥落。 • 盐雾测试:在规定的时间内,一定浓度的盐水连续喷 雾,镀层表面无腐蚀。 • 膜厚测试:采用电镀膜厚计进行检测
检测项目
• 表面外观:一般采用目测,常见的外观缺失有: A、针孔:表面针尖大小凹状小孔,和般情况下素材表面不良 (生锈等)素材为活性金属或烤漆粉不良 都易导致表面针孔。 B、堆积,桔皮:表面桔子皮状褶皱不良,烤漆粉流频差引起。 C、垂流:工件悬挂位置下端呈水滴状,烤漆粉流频过快引起。 D、粉薄,露铁:主要表现为工件的隐蔽面或内部,此类位置 受遮蔽不易上粉。 E、油渍,起泡:素材表面脏污或油污未清理干净,上粉后未 能附着于素材上,形成结团状起壳状不良。 F、水点:表面局部水点状凹陷,较平滑。 G、杂色:喷粉工具粉房未清理或烤漆粉本身有杂质,导致烤 漆后表面有均匀的点状其他颜色。 H、颗粒:烤漆粉不纯,有尘污混入或素材表面脏污,灰尘未 清理干净引起。
烤漆表面处理概述
定义: • 表面涂装是指将金属,瓷质,树脂等涂料扩散于其它物 体上,在物体表面形成有机连续膜的过程. 目的: • 增加物体的美观性. • 烤漆属于表面涂装的一个种类,我司常用的表面涂装还 有:披覆,电着等. • 用于物体的保护(防水,隔热,防电等). • 延长物体的使用寿命(抗氧化,耐腐蚀等). 烤漆的种类与方式 • 我司有两种常用的烤漆方式:粉体烤漆及液体烤漆. • 粉体烤漆是采用静电喷涂,使烤漆粉由于静电而均匀附 着在工件表面的方法.
表面处理知识

采用光谱分析、电子能谱等手段检测表面元素组成,以评估表面处 理效果。
质量控制标准与规范
国家标准
企业标准
遵循国家相关标准,如GB/T 11854-1999《铸造磨球技术条件》 等,确保表面处理质量符合行业 要求。
制定企业内部的表面处理质量控 制标准,明确各项技术指标和检 测方法,确保产品质量稳定可靠。
收集质量检测数据,进行统计分 析,找出表面处理质量问题的原 因,制定相应的改进措施。
06
表面处理发展趋势与挑战
新技术与新材料的发展趋势
1 2
纳米技术
纳米材料在表面处理中的应用逐渐增多,如纳米 涂层、纳米薄膜等,能够提高表面的耐磨、耐腐 蚀和光学性能。
激光表面处理
激光技术以其高能量密度和精确控制的特点,在 表面硬化、熔覆、合金化等方面展现出巨大潜力。
种类
常见的氧化处理有发黑、 发蓝、发黄等,可根据需 要进行选择。
喷涂
定义
喷涂是通过喷枪或喷嘴将 涂料喷涂到物体表面的过 程。
应用
喷涂广泛应用于建筑、家 具、汽车等领域的涂装和 修复,可以提高物体的美 观性和耐久性。
种类
喷涂可根据涂料的性质和 应用分为油漆喷涂、塑料 喷涂、金属喷涂等。
抛光
定义
抛光是通过磨料或抛光剂对物体 表面进行磨削和抛光,使表面光
表面处理知识
目 录
• 表面处理概述 • 表面处理技术 • 表面处理材料 • 表面处理工艺流程 • 表面处理质量控制 • 表面处理发展趋势与挑战
01
表面处理概述
定义与分类
定义
表面处理是指通过物理、化学或电化 学方法,对材料表面进行清洁、改性 或涂覆的过程,以达到所需的表面性 能和外观。
金相知识-表面处理金相检验

零件渗碳后直接淬火其金相组织有何特点? 零件的表面渗碳层为粗针状的马氏体和较多的残
留奥氏体,虽然沿晶的网状碳化物不多,但因内应力 过大,容易产生裂纹。零件心部基体为板条马氏体。
简述渗碳淬火工件的常见缺不均匀;
20CrMnTi经渗碳加回火后,从表层到心部的各层 组织是什么?
表层是高碳针状回火马氏体加少量残留奥氏体; 次表层为回火马氏体加回火托氏体;心部为低碳板 条马氏体加少量铁素体。
生产中发现20钢在可控气氛炉920℃渗碳、860℃淬 油后,表层硬度上不去。原因何在?
20钢渗碳后表层变为高碳钢,心部为低碳钢。 淬火温度和保温时间的选择要以既要考虑表层能得 到高硬度,但渗层又不能产生网状渗碳体(变脆)、 心部得到板条马氏体,消除铁素体为原则。在此原 则下淬火温度尽量提高,保温时间不宜过长。
网状和针状的二次渗碳体;表面全脱碳;渗碳过渡层 太陡;碳化物聚集成大块状;过热组织(即粗大马氏 体针);渗层较多的残余奥氏体,心部较多的铁素体; 黑色组织(晶界出现托氏体和贝氏体组织)。
20CrMo钢正火后能获得什么组织组成物,为什么? 钼对正火(或热轧)态钢而言,能使组织从珠光
体形态向贝氏体形态转变,20CrMo钢经正火后即 为贝氏体组织;55SiMnMo弹簧钢,以及近来研制 的超高强度钢32CrMoVA,由于含有元素Mo,正火 或淬火后均能获得贝氏体组织。
要薄,称为软氮化(亦称氮碳共渗)。
举例
轮齿工作 面和齿顶
渗碳
裂纹位置 在齿根槽
底面
3.3 在中温(800 ~ 860 ℃)阶段,基体组织大
部分为奥氏体和铁素体(两相区),碳、氮原子的 扩散速度都比较大,浓度也比较高,称为碳氮共渗 (氰化)。 4、化学热处理的分类
- 1、下载文档前请自行甄别文档内容的完整性,平台不提供额外的编辑、内容补充、找答案等附加服务。
- 2、"仅部分预览"的文档,不可在线预览部分如存在完整性等问题,可反馈申请退款(可完整预览的文档不适用该条件!)。
- 3、如文档侵犯您的权益,请联系客服反馈,我们会尽快为您处理(人工客服工作时间:9:00-18:30)。
7
2021/3/7
CHENLI
2.1 电镀常识
表面处理的基本过程大致分为三个阶段: 前处理,中间处理和后处理。
8
2021/3/7
CHENLI
2.1.1 前处理
零件在处理之前,程度不同地存在着毛 刺和油污,有的严重腐蚀,给中间处理带 来很大困难,给化学或电化学过程增加额 外阻力,有时甚至使零件局部或整个表面 不能获得镀层或膜层,还会污染电解液, 影响表面处理层的质量。包括除油、浸蚀 (酸洗)、磨光、抛光、滚光、喷砂、局 部保护、装挂、加辅助电极等。
12
2021/3/7
CHENLI
电镀图示
13
2021/3/7
CHENLI
2.2.1 阳 极
能够接受反应物所给出电子的电极, 即发生氧化反应的电极。
14
2021/3/7
CHENLI
2.2.2 阴 极
反应于其上获得电子的电极,即发生 还原反应的电极。
15
2021/3/7
CHENLI
2.2.3 钝 化
表面处理基础知识
暨GB/T13911标准宣贯
1
2021/3/7
CHENLI
1 表面处理概论
金属的腐蚀 表面处理的目的 常用的表面处理方法 常用金属材料的表面处理
2
2021/3/7
CHENLI
1.1 金属的腐蚀
化学腐蚀
金属与介质发生化学作用而产生的腐蚀。它的特点是金属与干燥 的气体相接触,在金属表面发生氧化还原反应(不产生电流),生成 相应的化合物。
31
2021/3/7
CHENLI
2.4.4 机械抛光
借助于高速旋转的抹有抛光膏的抛光 轮,以提高金属制件表面光亮度的机械加 工过程。
32
2021/3/7
CHENLI
2.4.5 有机溶剂除油
利用有机溶剂清除制件表面油污的过 程。
20
2021/3/7
CHENLI
2.3.1 化学钝化
将制件放在含有氧化剂的溶液中处理, 使表面形成一层很薄的钝态保护膜的过程。
21
2021/3/7
CHENLI
2.3.2 化学氧化
通过化学处理使金属表面形成氧化膜 的过程。
22
2021/3/7
CHENLI
2.3.3 电化学氧化
在一定电解液中以金属制件为阳极, 经电解,于制件表面形成一层具有防护性, 装饰性或其它功能氧化膜的过程。
铜及铜合金
(防腐蚀)镀锌、镀镉、镀镍、钝化; (耐磨)镀硬铬、化学镀镍; (导电及便于钎焊)镀金、镀银、镀锡。
铝及铝合金
(防腐蚀)硫酸阳极化(热水封闭或铬酸盐封闭); (识别标记)硫酸阳极化后着色; (减少对基体疲劳性能影响)铬酸阳极化、化学氧化。
6
2021/3/7
CHENLI
2 电镀的基本知识
在一定环境下使金属表面正常溶解反 应受到严重阻碍,并在比较宽的电极电位 范围内使金属溶解反应速度降到很低的作 用。
16
2021/3/7
CHENLI
2.2.4 氢 脆
由于浸蚀,除油或电镀等过程中金属 或合金吸收氢原子(使基体金属晶格歪扭, 造成较大内应力)而引起的脆性。
17
2021/3/7
CHENLI
电镀及复合电镀 如镀锌、镀镍-二氧化硅复合镀层 化学镀 如化学镀镍 电化学处理 如阳极氧化 化学处理 如钢铁氧化、磷化
5
2021/3/7
CHENLI
1.4 常用金属材料的表面处理
钢铁材料
(防腐蚀)镀锌、镀镉、镀镍、氧化、磷化; (耐磨)镀硬铬、化学镀镍; (导电及便于钎焊)镀铜、镀银、镀锡。
2.2.5 基体材料
能在其上沉积金属或形成膜层的材料。
18
2021/3/7
CHENLI
2.2.6 电 解
使电流通过电解质溶液而在阳极,阴 极引起氧化还原反应的过程。
19
2021/3/7
CHENLI
2.3 镀覆方法术语
2.3.1 化学钝化 2.3.2 化学氧化 2.3.3 电化学氧化 2.3.4 电 镀 2.3.5 磷 化 2.3.6 钢铁发蓝(钢铁化学氧化) 2.3.7 光亮电镀
电化学腐蚀
相互接触的不同金属,在电解液中会发生腐蚀。它的特点是金属 与周围介质作用的过程中,使金属从不带电的原子状态变成离子状态, 产生有电流的氧化还原反映。
3
2021/3/7
CHENLI
1.2 表面处理的目的
防腐蚀 装饰外观 抗磨损 电性能 工艺要求
4
2021/3/7
CHENLI
1.3 常用的表面处理方法
9
2021/3/7
CHENLI
2.1.2 中间处理
是赋予零件各种预期性能的主要阶段, 是表面处理的核心,表面处理质量的好坏 主要取决于这一阶段的处理。
10
2021/3/7
CHENLI
2.1.3 后处理
是对膜层和镀层的辅助处理。
11
2021/3/7
CHENLI
2.2 电镀过程中的基本术语
2.2.1 阳 极 2.2.2 阴 极 2.2.3 钝 化 2.2.4 氢 脆 2.2.5 基体材料 2.2.6 电 解
23
2021/3/7
CHENLI
2.3.4 电 镀
利用电解原理,使金属或合金沉积在 制件表面,形成均匀、致密、结合力良好 的金属层的过程。
24
2021/3/7
CHENLI
2.3.5 磷 化
在钢铁制件表面上形成一层不溶解的 磷酸盐保护膜的处理过程。
25
2021/3/7
CHENLI
2.3.6 钢铁发蓝(钢铁化学氧化)
将钢铁制件在空气中加热或浸入氧化 性的溶液中,使之于表面形成通常为蓝 (黑)色的薄氧化膜的过程。
26
2021/3/7
CHENLI
2.3.7 光亮电镀
在适当条件下,从镀槽中直接得到具 有光泽镀层的电镀。
27
2021/3/7
CHENLI
2.4 镀前处理和镀后处理术语
2.4.1 化学除油 2.4.2 电解除油 2.4.3 出 光 2.4.4 机械抛光 2.4.5 有机溶剂除油 2.4.6 除 氢 2.4.7 镀前处理 2.4.8 镀后处理
28
2021/3/7
CHENLI
2.4.1 化学除油
在碱性溶液中借助皂化作用和乳化作 用清除制件表面油污的过程。
29
2021/3/7
CHENLI
ห้องสมุดไป่ตู้ 2.4.2 电解除油
在含碱溶液中,以制件作为阳极或阴 极,在电流作用下,清除制件表面油污的 过程。
30
2021/3/7
CHENLI
2.4.3 出 光
在溶液中短时间浸泡,使金属形成光 亮表面的过程。