注射模具浇注系统设计
模具设计-浇注系统

模具设计-浇注系统浇注系统是指模具中从注射机喷嘴开始到型腔为止的塑料流动通道﹐其由主流道﹑分流道﹑浇口及冷料穴组成。
1.1.主流道主流道是指从注射机喷嘴与模具接触的部位起﹐到分流道为止的这一段。
主流道一般设计成圆锥形﹐角度为2°~4°。
1.2.分流道分流道是指主流道与浇口之间的这一段﹐它是熔融塑料由主流道流入型腔的过渡段﹐也是浇注系统中通过断面变化和塑料转向的过渡段﹐能使塑料得到平稳的转换。
1.2.1.分流道的形状有圆形﹑半圆形和梯形等几种﹐从减小压力和热量损失的角度考虑﹐圆形流道是最优越的流道形状。
当分型面是平面或曲面时﹐一般采用圆形流道;细水口模一般选用梯形流道﹐当流道只开在前模或后模时﹐则选用梯形流道。
1.2.2.当塑件采用多浇口进浇以及一模多腔早时﹐要充分考虑进胶的均匀性﹐尽可能做到平衡进胶。
1.2.3.设计分流道大小时﹐应充分考卢制品的大小﹑壁厚﹑材料流动性等因素﹐流动性不好的材料如PC料其流道应相应加大﹐并且分流道的截面尺寸一定要大于制品壁厚﹐同时应选择合适的长度。
流道长则温度降低明显﹐流道短则剩余应力大﹐容易产生“喷池”。
1.2.4.梯形流道﹕W一般为5—8mm﹐H一般为4—6mm﹐H/W=2/31.2.5.分流道表面不要求很光﹐表面粗糙度一般达Ra3.2~1.6即可﹐因为分流道的表面稍有不光滑﹐就能使熔料的冷却皮层固定﹐有利于保温﹔浇口的表面粗糙度不能高于Ra0.4﹐否则易产生摩擦阻力。
1.3.浇口浇口是指分流道与塑件之间的狭窄部分。
它能使分流道输送来的熔融塑料的流速产生加速度﹐形成理想的流态﹐顺序﹑迅速地充满型腔﹐同时还起眷封闭型腔防止熔料倒流的作用﹐并在成型后便于使浇口与塑件分离。
常见浇口类型有直接浇口﹑侧浇口﹑潜伏式浇口﹑点浇口等多种。
设计时对大型单一型腔制品成型效果好﹐需注意唧嘴底部与产品之间是否要隔一段距离。
1.3.2.侧浇口侧浇口设置于制品分型面处﹐制品允许有浇口痕迹才可采用﹐侧浇口包括边缘浇口和搭接浇口﹐其浇口尺寸与制品壁厚﹑大小﹑材料等诸多因素有关﹐一般规格如下图﹕边缘浇口与搭接浇口的选择如下图﹕ 选择浇口位置时﹐就防止制品产生滞留现象﹐应远离厚﹑薄交接处﹐从厚的地方进浇﹐避免浇口正对柱位﹑碰穿位﹐防止型芯因冲击而变形。
注塑模具设计:第二章:浇注系统

第二章浇注系统注塑机喷嘴中熔融的塑料,经过主流道,分流道,最后通过浇口进入到模具型腔,然后经过冷却固化,得到所需要的制品。
所以注塑模具的浇注系统是指从注塑机喷嘴到型腔为止的塑料熔体的流动通道。
因为热塑性塑料的热传导率较低,流道中冷凝的表皮对芯部熔融的塑料祈祷保温作用,所以保证了流道芯部的塑料继续流动。
来自熔融的塑料的热加上由于流动摩擦二产生的摩擦热等于高温塑料与低温模具热交换所产生的热损失。
如果增加注射速度,冷凝层由于受到流动产生的高摩擦热而会变薄。
即:高速注射与低速注射对于冷凝层厚度影响的差别是比较明显的。
这就是为什么高压、高速注射容易将型腔填充饱满的主要原因之一。
浇注系统的型制与流动性为减少与热量的损失,必须使流道的表面积与体积之比保持最小,因为具有最小表面积与最大体积的形状是圆柱形,所以圆柱形是最优越的流道形状。
主流道从注射机喷嘴到分浇为止的熔融塑料的流动通道。
1)定模部分由整体构成2)定模部分由两块模板所构成3)最普遍常用的主流道结构,是以浇口套的形式镶入模板中,为防止被喷嘴撞伤,采取淬火处理主流道的基本尺寸取决于两个方面:1,塑料的种类,所成型的制品质量和壁厚大小。
2与注射机喷嘴的几何参数有关。
浇口套的求半径比喷嘴的球半径大2~5mm,脱模斜度一般最小不低于1°,最大不超过4°。
因为,主流道的脱模斜度不能过大,否则在注塑时会产生涡流和流速过慢等现象主流道应保持光滑的表面,避免留有影响塑料流动或脱模的尖角毛刺等。
而且在主流道的末端还应设置冷料井以防止制品中出现固化的冷料(最先流入模具的塑料)。
设置冷料井,以便将这部分冷料存留起来。
这一点对分流道也同样重要。
分流道分流道可以理解为从主流道末端开始到浇口为止的塑料熔体的流动通道。
鉴于圆形截面的浇道必须设置在以分型面为界的动、定模两部分,所以对制造工艺要求较高,且启模时,分流道中经过冷却固化的塑料留在动、定模内是随机的。
所以实际制造中,U 性截面分流道或梯形截面的分流道比较常用,虽然热量损失较大一点,但加工制造比较简单,并且启模时,冷料留在动定模哪一部分,将是确定的。
模具浇注系统的设计原理

模具浇注系统的设计原理模具浇注系统是一种工业生产中常用的设备,用于将液态材料注入模具中,形成所需的产品形状。
它具有精确控制浇注过程、提高生产效率和产品质量等优点。
模具浇注系统的设计原理主要包括浇注过程控制、模具设计和与其他设备的协同工作等方面。
首先,模具浇注系统的设计原理涉及浇注过程的控制。
控制浇注过程是保证产品准确性和质量的关键。
在浇注过程中,需要控制液态材料的流动速度、浇注时间、温度等因素,以确保产品形状和尺寸的准确性。
这一过程需要使用传感器和控制器等设备监测和调节浇注参数。
传感器可以实时监测液态材料的流动速度和压力等参数,并将这些数据传输给控制器。
控制器则根据传感器数据调整浇注设备的工作状态,以实现准确的浇注过程控制。
其次,模具浇注系统的设计原理还需要考虑模具的设计。
模具是决定产品形状和尺寸的关键因素之一。
模具的设计需要根据产品的要求确定模具的形状、材料和开发方式等。
模具浇注系统要根据模具的形状和尺寸进行相应的调整和优化,以确保浇注过程的准确性和稳定性。
例如,对于需求复杂形状的产品,可以采用多腔模具设计,以提高生产效率和产品质量。
此外,模具浇注系统的设计原理还涉及与其他设备的协同工作。
在工业生产中,模具浇注系统通常需要与其他设备进行联动工作,以实现自动化生产。
例如,模具浇注系统可以与机器人手臂或传送带等设备配合使用,实现自动化的生产流程。
这需要设计合理的工作流程和设备间的信号传输机制,以实现协同工作和生产效率的提高。
综上所述,模具浇注系统的设计原理涉及浇注过程控制、模具设计和与其他设备的协同工作等方面。
通过精确控制浇注过程、优化模具设计和与其他设备的协同工作,模具浇注系统可以提高生产效率和产品质量,满足工业生产的需求。
注塑模具浇注系统设计素材

因此,设计时应尽量避免主流道偏离 模具中心,但在侧浇口浇注系统中,常常 由于以下原因,主流道位置必须偏离模具 中心: ①一模多腔中的制品大小悬殊; ②单型腔,制品较大,中间有较大的碰穿 孔,可以从内侧进料。但中间碰穿孔偏离 模具中心。
如果主流道偏离模具中心不可避免,那 么,可以采取三种措施,来避免或减轻不 良后果对模具的影响: ①增加推杆固定板导柱(中托边)来承受顶 棍偏心产生的扭力; ②模具较大时,也可采用双顶棍孔或多 顶棍孔,使推杆固定板受到多点推力的作 用时,较易平衡推出; ③采用倾斜式主流道,避免顶棍孔偏心 (见图)
(2)型腔的数量
它决定分流道的走向、长短和大小。
(3)壁厚及内在外观质量要求
这些因素决定了浇口的位置和形式,最 终决定分流道的走向和大小。 注意:如果要采用自动化注塑,则分流 道必须确保在开模后留在后模,且容易推 落。
分流道的布置
在确定分流道的布置时,应尽量使流道 长度最短。但是,塑料以低温成型时,为 提高成型空间的压力来减少成型制品收缩 凹陷时,或欲得壁厚较厚的成型制品而延 长保压时间,减短流道长度并非绝对可行。 因为流道过短,则成型制品的残留应力 增大,且易产生飞边,塑料的流动不均, 所以流道长度应以适合成型制品的质量和 结构为宜。
(4)主流道应设计在浇口套内
主流道尽量避免直接做在模板内,或采 用镶拼结构,以防塑料进入接缝造成脱模 困难。
(5)主流道应尽量和模具中心重合
避免浇口套位置偏心或采用倾斜式主流 道。
倾斜式主流道设计
倾斜式主流道设计
一般地,要求主流道的位置应尽量与模具中心 重合,否则会有如下不良后果。 ①主流道偏离模具中心时,导致锁模力和胀型 力不在一条线上,使模具在生产时受到扭矩的作 用,这个扭矩会使模具一侧张开产生飞边,或者 使型芯错位变形,最终还会导致磨具导柱,甚至 注射机拉杆变形等严重后果。 ②主流道偏离模具中心时,顶棍孔也要偏离模 具中心,制品推出时,推杆板也会受到一个扭力 的作用,这个扭力传递给推杆后,会导致推杆磨 损,甚至断裂。
模具浇注系统的设计原则

模具浇注系统的设计原则①保证塑料熔体流动平稳设计浇注系统时,应注意使系统与模具中的排气结构相适应,使系统具有良好的排气性,从而保证塑料熔体经过系统或充填模腔时不发生涡流和紊流,以使制品获得良好的成型质量。
②流程应尽量短在充足成型和排气要求的前提下系统长度应尽量短,各段应尽量平直,以使塑料熔体在模具中的流程尽量短而且不发生弯曲,从而可减小注射压力和熔体的热量损失,并缩短熔体充模时间。
③防止型芯变形和嵌件位移设计浇注系统时,应尽量避开通过系统的塑料熔体正面冲击模腔内尺寸较小的型芯或嵌件,以防止熔体的冲击力使型芯发生变形或使嵌件发生位移。
④修整应尽量便利修整指制品成型后对其外观所做的各种修整工作,其中包括去除制品上的浇注系统凝料。
为了便利修整并无损制品外观和使用性能,浇注系统在模具中的位置和形状,尤其是浇口的位置和形状应尽量依据制品的形状和使用要求确定。
⑤防止制品变形和翘曲设计浇注系统时,应考虑如何减轻浇口相近的残余应力集中现象,以防止因应力过大而导致制品发生变形和翘曲。
例如对于深度很浅的大平面聚乙烯、聚丙烯制品若采纳料流速度较大的直接浇口成型,由于注射压力直接作用在制品上加之这些塑料取向本领较强,所以成型后很简单在浇口相近残余较大的时效应力和取向应力,并导致制品发生翘曲变形,为此可改换多点浇口形式。
但是应当指出,采纳多点浇口成型制品时,由于各浇口相近收缩与其它部位不等,也特别简单引起制品整体翘曲变形,尤其对于大型薄壁制品,使用多点浇口时特别要注意此问题、⑥应与塑料品种相适应不同的塑料具有不同的流动性,特别是对硬质聚氯乙稀、聚丙烯酸酯和聚甲醛等成型性差的塑料,其流道和浇口的选择是否合适,对于制品的性能、外观以及成型周期和生产成本都有很大影响。
另外,有些塑料还会由于浇口设计不当而导致浇口表壁与熔体之间产生较大摩擦,从而引起塑料褪色。
⑦合理设计冷料穴冷料穴设计不当,简单使制品发生成型缺陷。
假如冷料穴失效,使前锋冷料进入模腔会导致制品产生冷疤或冷斑。
10浇注系统设计
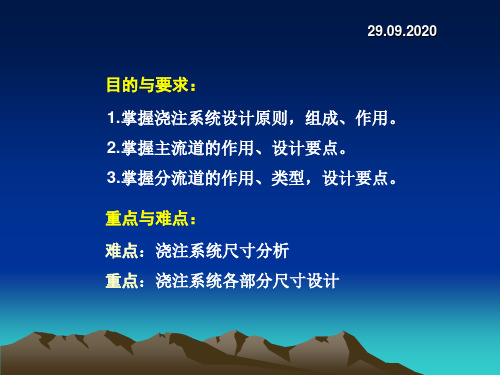
锥度对于流动性差的塑料 可取到6度。
主流道大端尺寸D:
Q1 D 2( )3(cm)
其中: D:大端直径,cm; Q:流经该流道的熔体的体积流率,cm3/s; γ:熔体在该流道的剪切速率,1/s;主流道: 5x103。
29.09.2020
目的与要求: 1.掌握浇注系统设计原则,组成、作用。 2.掌握主流道的作用、设计要点。 3.掌握分流道的作用、类型,设计要点。 重点与难点: 难点:浇注系统尺寸分析 重点:浇注系统各部分尺寸设计
29.09.2020
一、普通浇注系统的组成及设计原则 (一)浇注系统的概念
浇注系统:指由注射机喷嘴中喷出的塑料熔体进入型腔的流动 通道。 作用:使塑料熔体平稳有序地填充型腔,并在填充和凝固过程 中把注射压力充分传递到各个部分,以获得组织致密的塑件。
29.09.2020
29.09.2020
4.在多腔模中,各个型腔浇口方位必须保持一致
29.09.2020
5.减少熔结痕和提高熔结痕的强度
29.09.2020
6.浇口位置应使浇口便于修整
29.09.2020
29.09.2020
7.防止料流将型芯或嵌件挤歪变形
29.09.2020
(二)浇注系统平衡 计算多型腔模具各浇口的BGV值,同一塑件的多腔 模各浇口BGV值相同,不同塑件的多腔模各浇口的 BGV值与塑件质量成正比
29.09.2020
29.09.2020
主浇道穿过两块模板时应呈阶梯状,或采用浇口套
保证顺利拔出
H7/m6(过渡)、H7/n6(过盈)
27第二十七课 浇注系统设计 教案

任务四注射模具设计—浇注系统设计教学内容(板书)第二十七课浇注系统的设计1、冷料穴的设计注射成型时,喷嘴前端的熔料温度较低,为防止其进入型腔,通常在流道末端设置用以集存这部分冷料的冷料穴。
设置熔料流动方向的转折处,以便将冷料入穴中存留起来。
1、带钩形拉料杆的冷料穴2、带球头拉料杆的冷料穴应该指出,并非所有注射模都需开设冷料穴,有时由于塑料的工艺性能好和成型工艺条件控制得好,可能很少产生冷料,如果塑件要求不高时可不设冷料穴。
2、浇口的设计1)浇口位置的选择(1)避免引起熔体破裂现象克服上述缺陷的办法通常有两种:一是加大浇口尺寸,以降低流速。
二是采用冲击型浇口。
(2)有利于熔体流动和补缩浇口的位置应开设在塑件截面最厚处。
(3)有利于型腔内气体排出(4)减少熔接痕和增强熔接强度(5)防止料流将型芯或嵌件挤压变形(6)保证流动比在允许范围内2)浇口的设计(1)直接浇口(2)中心浇口中心浇口适用于筒形、环形或中心带孔的塑件成型。
(3)侧浇口侧浇口为限制性浇口,适用于一模多腔,能大大提高生产效率,减少浇注系统耗量,浇口去除也较方便,是一种被广泛采用的浇口形式。
但侧浇口压力损失较大,保压补缩作用比直浇口弱,壳形件排气不便,易产生熔接痕;缩孔及气孔等缺陷。
侧浇口的截面形状通常为矩形。
a)为扇形浇口,常用来成形宽度较大的薄片状塑件。
b)为薄片式浇口,又称平缝式浇口,常用来成型大面积薄片塑件。
(4)点浇口又称针浇口或菱形浇口。
这种浇口有很多优点,几乎可以用于各种形式的塑件。
点浇口一般设在塑件的顶端,去除方便,不影响塑件的外观,浇口可自动拉断,可以实现自动化操作。
这种浇口尤其适用于圆筒形、壳形、盒形的塑件,但是流动性较差的塑料(例如PMMA、PC等)就不适于采用点浇口,而适用于流动性较好的ABS、PP、POM 等塑料。
(5)潜伏式浇口又称遂道式浇口或剪切浇口。
潜伏式浇口呈针点状,开模时流道凝料由推出机构推出,并与塑件从浇口处自动切断,省掉了切除浇口的工程。
注塑模具浇注系统设计
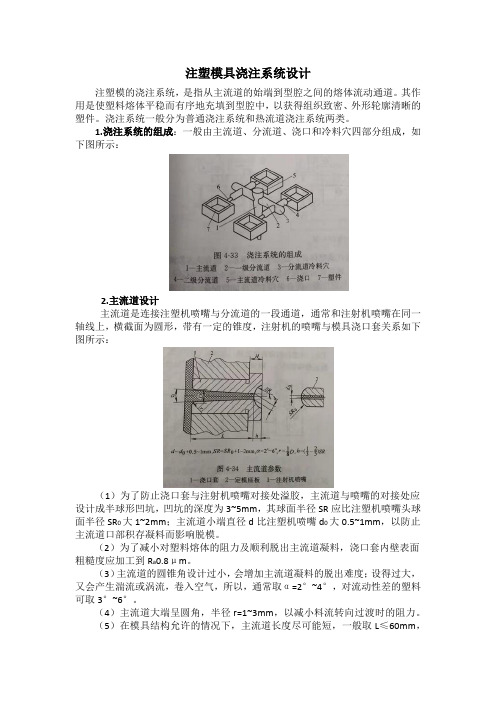
注塑模具浇注系统设计注塑模的浇注系统,是指从主流道的始端到型腔之间的熔体流动通道。
其作用是使塑料熔体平稳而有序地充填到型腔中,以获得组织致密、外形轮廓清晰的塑件。
浇注系统一般分为普通浇注系统和热流道浇注系统两类。
1.浇注系统的组成:一般由主流道、分流道、浇口和冷料穴四部分组成,如下图所示:2.主流道设计主流道是连接注塑机喷嘴与分流道的一段通道,通常和注射机喷嘴在同一轴线上,横截面为圆形,带有一定的锥度,注射机的喷嘴与模具浇口套关系如下图所示:(1)为了防止浇口套与注射机喷嘴对接处溢胶,主流道与喷嘴的对接处应设计成半球形凹坑,凹坑的深度为3~5mm,其球面半径SR应比注塑机喷嘴头球面半径SR0大1~2mm;主流道小端直径d比注塑机喷嘴d0大0.5~1mm,以防止主流道口部积存凝料而影响脱模。
(2)为了减小对塑料熔体的阻力及顺利脱出主流道凝料,浇口套内壁表面粗糙度应加工到R a0.8μm。
(3)主流道的圆锥角设计过小,会增加主流道凝料的脱出难度;设得过大,又会产生湍流或涡流,卷入空气,所以,通常取α=2°~4°,对流动性差的塑料可取3°~6°。
(4)主流道大端呈圆角,半径r=1~3mm,以减小料流转向过渡时的阻力。
(5)在模具结构允许的情况下,主流道长度尽可能短,一般取L≤60mm,过长会增加压力损失,使塑料熔体的温度下降过多,从而影响熔体的顺利充型。
另外,过长的流道还会浪费塑料材料、增加冷却时间。
(6)最常见的主流道的类型有以下几种形式,如下图所示。
由于浇口套在工作时经常与注塑机喷嘴反复接触、碰撞,所以浇口套常用优质合金钢制造,也可以选用T8、T10,并进行相应的热处理,保证足够的硬度,但其硬度应低于与注塑机喷嘴的硬度,以防止喷嘴被碰坏。
(7)对于小型模具,可将主流道浇口套与定位圈设计成整体式,不过大多数情况下,是将主流道浇口套和定位圈设计成两个零件,然后配合固定在模板上面。
- 1、下载文档前请自行甄别文档内容的完整性,平台不提供额外的编辑、内容补充、找答案等附加服务。
- 2、"仅部分预览"的文档,不可在线预览部分如存在完整性等问题,可反馈申请退款(可完整预览的文档不适用该条件!)。
- 3、如文档侵犯您的权益,请联系客服反馈,我们会尽快为您处理(人工客服工作时间:9:00-18:30)。
浇注系统是用于将注射机料筒中塑化好的塑料熔体经喷 嘴平稳的引入到模具型腔各部位,同时将注射压力和保压力 均匀的传递到型腔各处,以获得外观清晰,内在质量优良的 塑件。 作用: 1〉输送熔体; 2〉传递压力。
2020/4/2
资料仅供参考,不当之处,请联系改正。
主流道的设计
主流道是熔融塑料由注 射机喷嘴喷出时最先经 过的部位,与注射机喷 嘴同轴。因之与熔融塑 料、注射机喷嘴反复接 触、碰撞,一般不直接 开设在定模上,而是制 成可拆卸的浇口套,用 螺钉或配合形式固定在 定模板上 ,主流道的基 本结构和安装形式如图42。
分流道与型腔之间的一段截面狭小、长度很短的料流通 道。熔体进入型腔的入口。是整个浇注系统的关键部分。
2020/4/2
资料仅供参考,不当之处,请联系改正。
(4)冷料穴(cold-slug well) 一般位于主流道末端分型面动模一侧,分流道较长时,
在其末端也设有冷料穴。冷料穴主要用于收集喷嘴前端和熔 体流动前锋的冷料,避免冷料进入型腔对塑件质量造成影响。 有时,在型腔最后充满部位,为避免熔接缝对制品质量的影 响,也设置冷料穴,制品成形后切除。
2020/4/2
二、分流道的截面形状 资料仅供参考,不当之处,请联系改正。
(1)分流道的主要截面形状:
❖ 圆形截面 分流道效率最高;根据塑件实际情况分流道直径D可在4~ 8mm内最好。制造麻烦,将分流道分设在模板两侧,对合 时产生错口现象。
❖ 半圆形截面 效率比圆形差,加工起来简单
❖ 梯形截面 加工起来较为简单,截面也利于物料的流动,最常用。D在 4~8mm选择。
2020/4/2
资料仅供参考,不当之处,请联系改正。
注射模分流道的设计
分流道是主流道与浇口的中间连接部分,其 作用是熔料分流和转换方向。
一、分流道的设计要点
❖ 截面积:满足注射工艺的条件下尽量小 ❖ 分布:紧凑、对称,尽量缩小成型区域总面积 ❖ 形状:截面积与周长之比尽量大 ❖ 长度:尽量短;各型腔的分流道长度尽量相等 ❖ 转向:次数尽量少且圆角过渡 ❖ 内表面粗糙度:不必很光以使料流外层形成一
非平衡式布局的主要特点是,主流道至各型腔的分流道长度及熔体流 程各不相同。致使各型腔的熔体充模时间不同,温度分布与压力传递 不同,塑件质量不一致。
2020/4/2
资料仅供参考,不当之处,请联系改正。
实际生产中有时将不同尺寸大小的塑件放在同一模具中成形, 如图10所示。这对保证塑件质量是不利的。应尽量避免这种 设计。
分流道无 冷料穴
有冷料穴, 合理
2020/4/2
平衡式分流道 资料仅供参考,不当之处,请联系改正。
2020/4/2
平衡式分流道 (最常用) (Balanced) 资料仅供参考,不当之处,请联系改正。
2020/4/2
资料仅供参考,不当之处,请联系改正。
(2)非平衡式分流道(non-Balanced)
202点
❖ 采用α=3°~6°的圆锥孔以便取出浇口凝料(锥角太大注射速度缓慢, 形成涡流);锥孔内壁粗糙Ra=0.63μm; 锥孔大端有1°~2°的过渡圆 角(减小料流转向时的流动阻力)
❖ 当与注射区直接接触时,出料端端面直径D尽量小(太大,型腔内部反 压力太大,弹出)
❖ 扁形截面(扁梯形) 扁形截面的分流道的流动情况变差,但分流道冷却却比以上 形状好很多。宽度和深度根据实际需要来定。
2020/4/2
资料仅供参考,不当之处,请联系改正。
(2)分流道的断面形状选择
据理论分析可知,等断面积条件下,正方形的周长最长,圆形最短, 其它形状介于两者之间。据此 ◎ 从增加传热面积考虑,热固性塑料模具的分流道最好采用正方形,可 提高传热面积。但流道凝料不易脱模。 ◎ 从减少散热面积考虑,热塑性塑料模具最好选用圆形截面分流道,可 减少热量损失。 ◎ 从降低压力损失考率,同等截面积时,圆形截面的周边最短,其熔体 流动阻力较小,压力损失就小。 分流道的截面形状如图14所示。
资料仅供参考,不当之处,请联系改正。
(1)主流道(sprue) 是连接注射机喷嘴与模具分流道之间的一段圆锥形通道,
其作用是将塑料熔体从注射机喷嘴引入模具。(引料入模) (2)分流道(runner)
是主流道与浇口之间的料流通道。在多型腔或单型腔多 浇口模具中,分流道是将来自主流道的熔体均匀的分配至各 型腔或同一型腔的各部位,并对熔体进行分流和转向。按模 具类型的不同,分流道可分为一级或多级,有的模具没有分 流道。 (3)浇口(gate)
❖ 浇口套的凹球面与注射机喷嘴头的凸球面吻合:Sr=SR+(0.5~1)mm (SR注射机喷嘴头半径); d=d1+(0.5~1)mm(d1注射机喷嘴头内径) 端面凹球面深度L2=3~5 mm
❖ 定位环外径D1与注射机的定位孔间隙配合;定位环厚度 L1= 5~10mm ❖ 浇口套端面与定模相配合部分的平面高度一致 ❖ 浇口套长度L尽量短(L太大,压力损失太大,物料降温过大) 。 ❖ 浇口套材质为T8A淬硬处理,硬度应小于注射机喷嘴硬度
层冷却皮层保温。Ra=1.6um ❖ 凝料脱出:当分流道在定模侧或较长时应设拉
料杆 如图4-5 ❖ 其他:应考虑冷却系统的方式和布局
2020/4/2
资料仅供参考,不当之处,请联系改正。
分流道对熔体流动的阻力要小,在保证熔体顺利充模要求的 前提下,分流道的截面积与长度尽量取小值。分流道转折处 应有圆角过渡,表面粗糙度Ra = 1.6 ~ 0.8为宜。(增大外层流动 阻力,避免熔体流动时产生表面滑移,使中心层有较高的剪 切速率)。 分流道较长时,在其末端应开设冷料穴,如图15所示。
2020/4/2
资料仅供参考,不当之处,请联系改正。
❖ 三、分流道的布局形式
分流道的布局取决于型腔的布局,两者应统一协调,相互制约。
分流道和型腔的分布有两种布局方式:(1)平衡式布局;(2)非平衡式布局。 两种方式各有特点,因此在实践中都广泛应用。
(1)平衡式分布的特点是:从主流道到各个型腔的分流道,其长度、截面尺寸及其 形状都完全相同,以保证各个型腔同时均衡进料,同时注射完毕。即保证各型腔 的熔体温度、压力、充模时间都相等。