失效分析基础
失效分析基本常识及操作计划流程培训
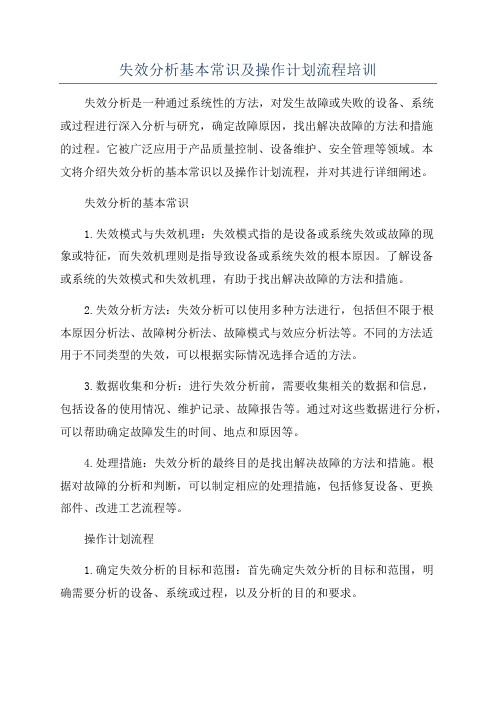
失效分析基本常识及操作计划流程培训失效分析是一种通过系统性的方法,对发生故障或失败的设备、系统或过程进行深入分析与研究,确定故障原因,找出解决故障的方法和措施的过程。
它被广泛应用于产品质量控制、设备维护、安全管理等领域。
本文将介绍失效分析的基本常识以及操作计划流程,并对其进行详细阐述。
失效分析的基本常识1.失效模式与失效机理:失效模式指的是设备或系统失效或故障的现象或特征,而失效机理则是指导致设备或系统失效的根本原因。
了解设备或系统的失效模式和失效机理,有助于找出解决故障的方法和措施。
2.失效分析方法:失效分析可以使用多种方法进行,包括但不限于根本原因分析法、故障树分析法、故障模式与效应分析法等。
不同的方法适用于不同类型的失效,可以根据实际情况选择合适的方法。
3.数据收集和分析:进行失效分析前,需要收集相关的数据和信息,包括设备的使用情况、维护记录、故障报告等。
通过对这些数据进行分析,可以帮助确定故障发生的时间、地点和原因等。
4.处理措施:失效分析的最终目的是找出解决故障的方法和措施。
根据对故障的分析和判断,可以制定相应的处理措施,包括修复设备、更换部件、改进工艺流程等。
操作计划流程1.确定失效分析的目标和范围:首先确定失效分析的目标和范围,明确需要分析的设备、系统或过程,以及分析的目的和要求。
2.收集故障数据和信息:收集与故障相关的数据和信息,包括设备的使用情况、维护记录、故障报告等。
通过对这些数据进行分析,可以帮助确定故障发生的时间、地点和原因等。
4.分析故障机理和模式:根据调查和观察的结果,对故障机理和模式进行分析,找出导致设备或系统失效的根本原因。
5.制定处理措施:根据对故障的分析和判断,制定相应的处理措施,包括修复设备、更换部件、改进工艺流程等。
同时,给出预防措施,以避免类似故障再次发生。
6.实施处理措施:根据制定的处理措施,组织实施修复、更换等工作。
同时,对工作结果进行检查和验证,确保故障得到彻底解决。
零件失效分析失效分析基础知识

表3 在一般工业工程中调查的失效原因的比例
起
因
材料选择不恰当 装配错误 错误的热处理 机械设计错误 未预见的操作条件 环境控制不够充分 不恰当的或缺少监测与质量控制 材料混杂
(%)
38 15 15 11 8 6 5
2
表4 航空零件失效原因的比例
起
因
保养不恰当 安装错误 设计缺陷 不正确的维修损坏 材料缺陷 未定原因
❖ 氢腐蚀(高温氢侵蚀)引起的蒸汽管道爆管事故
氢腐蚀是蒸汽管道、锅炉管与石油化工临氢高温装备中较常见的 失效模式。 这种失效模式可能没有明显的腐蚀现象,但是材料性能严重退化, 事故的隐患已经存在。在氢处理、重整、加氢裂化等装置中,温 度超过260℃,氢的分压大于689kPa,就有可能发生氢分子在钢 的表面分解为原子氢而发生腐蚀。氢腐蚀是原子氢进入钢铁材料, 并与碳化物反应生成甲烷(Fe3C+4H→3Fe+CH4),由于甲烷的分 子尺寸大而不易扩散,会使甲烷在晶界或相界面等处聚集产生局 部高压,形成微裂纹,进而材料脆化。
❖ 催化裂化装置再生器的硝酸盐应力腐蚀失效
➢ 裂纹均从内表面开始向外表面扩展,裂纹发生部位未见明显塑 性变形,裂纹宽度较窄,向纵深发展并多数穿透壁厚;
➢ 裂纹呈树枝状,断口有典型的沿晶特征; ➢ 腐蚀产物的水溶液PH值在5~6,呈现酸性; ➢ 断口表面腐蚀产物中的氮含量均明显高于基体金属中的氮含量; ➢ 结论是NO3-引起的应力腐蚀开裂。
上海汽车锻造总厂生产的汽车钢板弹簧产生早期失效,综合 分析发现:表面存在较多较深的弹坑及局部脱碳。
应力状态:弯曲疲劳
缺陷:
➢ 降低应力集中的措施
强化材料,降低应力集中的作用
整体强化 局部强化
失效分析的基础知识
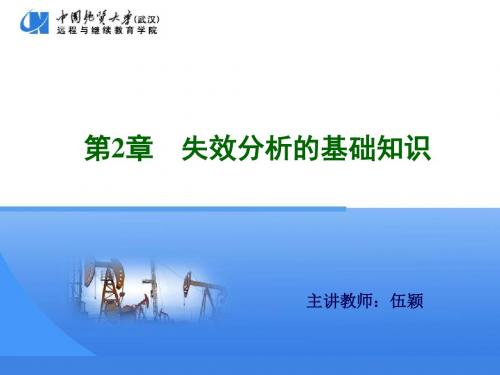
中国地质大学远程教学
25
2.5.2 单向拉(压)应力
知识点14 许用应力的定义。 所谓许用应力就是允许达到的应力。对机械零件最基本的要求就是具备
足够的强度,为了保证零件在外力作用下,能够安全可靠地工作,应使
它的工作应力低于材料的承受能力,使构件的强度留有必要的储备,因 此,常把材料的强度指标除以大于1的系数 ,作为设计时应力的最高限
7
2.2 应力集中与零件失效
2.2.1 应力集中与应力集中系数
知识点4 应力集中与应力集中系数的定义。 零件截面有急剧变化处,就会引起局部地区的应力高于受力体 的平均应力,这一现象称为应力集中,表示应力集中程度大小 的系数称为应力集中系数。 应力集中的程度首先是与缺口的形状有关。一般来说,圆孔孔 边的应力集中程度最低。 影响应力集中系数的因素还很多,如零件结构,缺口位置、大 小,材料种类,载荷性质等,具体情况应具体分析。
中国地质大学远程教学
10
2.2.3 降低应力集中的措施
知识点6 降低应力集中的措施。 1.从强化材料方面降低应力集中的作用 采取局部强化以提高应力集中处的材料疲劳强度,从而减少应力 集中的危害。 2.从设计方面降低应力集中系数
(1)变截面部位的过渡。
(2)根据零件的受力方向和位置选择适当的开孔部位。 (3)在应力集中区附近的低应力部位增开缺口和圆孔。
韧性的定义:所谓韧性是材料从变形到断裂全过程中吸收能量的大小,
是强度和塑性的综合表现。
为了在设计计算中能直接应用材料的韧性指标,提出了应力场强度因子 的概念,并建立了如下关系
K1 Y
式中 Y——裂纹体的几何因子函数。该函数是一个和裂纹形状、加载
Y ;
方式以及试样几何因素有关的量,是一个无量纲的系数。有中心穿透裂
失效分析知识点

失效分析知识点第一章概论1.失效的定义:当这些零件失去其应有的功能时,则称该零件失效。
2.失效三种情况:(1).零件由于断裂、腐蚀、磨损、变形等从而完全丧失其功能;(2).零件在外部环境作用下,部分的失去其原有功能,虽然能工作,但不能完成规定功能,如由于磨损导致尺寸超差等;(3).零件能够工作,也能完成规定功能,但继续使用时,不能确保安全可靠性。
3. 失效分析定义:对失效产品为寻找失效原因和预防措施所进行的一切技术活动。
也就是研究失效的特征和规律,从而找出失效的模式和原因。
4. 失效分析过程:事前分析(预防失效事件的发生)、事中分析(防止运行中设备发生故障)、事后分析(找出某个系统或零件失效的原因)。
5. 失效分析的意义:(1).失效分析的社会经济效益:失效将造成巨大的经济损失;质量低劣、寿命短导致重大经济损失;提高设备运行和使用的安全性。
(2).失效分析有助于提高管理水平和促进产品质量提高;(3).失效分析有助于分清责任和保护用户(生产者)利益;(4).失效分析是修订产品技术规范及标准的依据;(5).失效分析对材料科学与工程的促进作用:材料强度与断裂;材料开发与工程应用。
第二章失效分析基础知识一.机械零件失效形式与来源:1.按照失效的外部形态分类:(1)过量变形失效:扭曲、拉长等。
原因:在一定载荷下发生过量变形,零件失去应有功能不能正常使用。
(2)断裂失效:一次加载断裂(静载荷):由于载荷或应力超过当时材料的承载能力而引起;环境介质引起的断裂:环境介质和应力共同作用引起的低应力脆断;疲劳断裂(交变载荷):由于周期作用力引起的低应力破坏。
(3)表面损伤失效:磨损:由于两物体接触表面在接触应力下有相对运动,造成材料流失所引起的一种失效形式;腐蚀: 环境气氛的化学和电化学作用引起。
(4).注:断裂的其他分类断裂时变形量大小:脆性断裂、延性断裂;裂纹走向与晶相组织的关系:穿晶断裂、沿晶断裂;2.失效的来源:(1).设计的问题:高应力部位存在沟槽、机械缺口及圆角半径过小等;应力计算错误;设计判据不正确。
失效分析基础知识
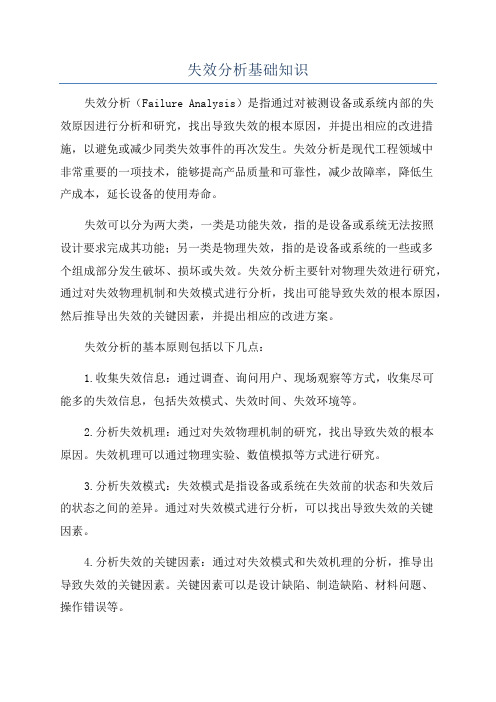
失效分析基础知识失效分析(Failure Analysis)是指通过对被测设备或系统内部的失效原因进行分析和研究,找出导致失效的根本原因,并提出相应的改进措施,以避免或减少同类失效事件的再次发生。
失效分析是现代工程领域中非常重要的一项技术,能够提高产品质量和可靠性,减少故障率,降低生产成本,延长设备的使用寿命。
失效可以分为两大类,一类是功能失效,指的是设备或系统无法按照设计要求完成其功能;另一类是物理失效,指的是设备或系统的一些或多个组成部分发生破坏、损坏或失效。
失效分析主要针对物理失效进行研究,通过对失效物理机制和失效模式进行分析,找出可能导致失效的根本原因,然后推导出失效的关键因素,并提出相应的改进方案。
失效分析的基本原则包括以下几点:1.收集失效信息:通过调查、询问用户、现场观察等方式,收集尽可能多的失效信息,包括失效模式、失效时间、失效环境等。
2.分析失效机理:通过对失效物理机制的研究,找出导致失效的根本原因。
失效机理可以通过物理实验、数值模拟等方式进行研究。
3.分析失效模式:失效模式是指设备或系统在失效前的状态和失效后的状态之间的差异。
通过对失效模式进行分析,可以找出导致失效的关键因素。
4.分析失效的关键因素:通过对失效模式和失效机理的分析,推导出导致失效的关键因素。
关键因素可以是设计缺陷、制造缺陷、材料问题、操作错误等。
5.提出改进措施:根据分析结果,提出相应的改进措施,包括设计改进、制造改进、材料改进、操作改进等。
改进措施应该能够消除或减少导致失效的关键因素,从而提高设备或系统的可靠性和安全性。
失效分析常用的方法和技术包括材料分析、断口分析、显微分析、化学分析、热分析、电子显微镜观察等。
这些方法和技术可以帮助工程师深入了解失效的原因和机制,从而提出有效的改进措施。
失效分析在工程领域中具有广泛的应用,包括电子设备、机械设备、化工设备、航空航天设备等各个领域。
通过对失效进行分析和研究,可以提高产品的可靠性和质量,减少故障率,降低生产成本,延长设备的使用寿命。
失效分析基本常识以及操作流程

失效分析基本常识以及操作流程失效分析是一种通过分析和探究事物、系统或过程发生失效的原因和机制的方法。
它可以帮助我们识别并改进潜在的问题,以提高系统的可靠性和性能。
以下是关于失效分析的基本常识与操作流程。
一、失效分析的基本常识1.失效模式与效应分析(FMEA):FMEA是一种通过分析预测和评估失效模式及其严重性、发生概率和检测能力的方法。
它可以在设计、生产和使用阶段预防或减少失效。
2.失效树分析(FTA):FTA是一种通过将失效进行因果关系的图形化表示来分析系统失效的方法。
它能够帮助确定导致一些具体失效的事件链。
3.事故树分析(ETA):ETA是一种通过将事故及其后果进行因果关系的图形化表示来分析事故发生的方法。
它可以帮助识别和评估事故的潜在原因及其对系统的影响。
4.失效模式、原因和影响分析(FMEDA):FMEDA是一种通过分析失效模式、失效原因和失效影响的方法来评估系统的可靠性。
它通常用于评估硬件系统。
5.人因分析:人因分析是一种通过分析人因相关的错误、失误和措施来评估和改进工作系统和流程的方法。
它可以帮助减少人为失误和提高操作效率。
二、失效分析的操作流程1.确定分析目标:确定需要进行失效分析的系统、产品或过程,并明确分析的目标和范围。
例如,是为了解决一个特定的问题,还是为了提高整体系统的可靠性等。
2.收集相关数据:收集和整理与失效有关的数据和信息,包括过去的失效记录、测量数据、使用情况等。
这些数据将为后续的分析提供基础。
3.选择适当的工具和方法:根据分析的目标和需要,选择适合的失效分析方法和工具,如FMEA、FTA、ETA等。
有时需要结合多种方法进行分析。
4.定义失效模式与效应:识别和描述可能的失效模式及其对系统的影响。
这包括对失效模式的描述和分类,以及对失效的严重性进行评估。
5.分析失效原因:通过追溯失效模式,分析导致失效发生的可能原因和机制。
这包括对失效原因的分类和评估,以及确定潜在缺陷和改进点。
Chap5-1 失效分析基础
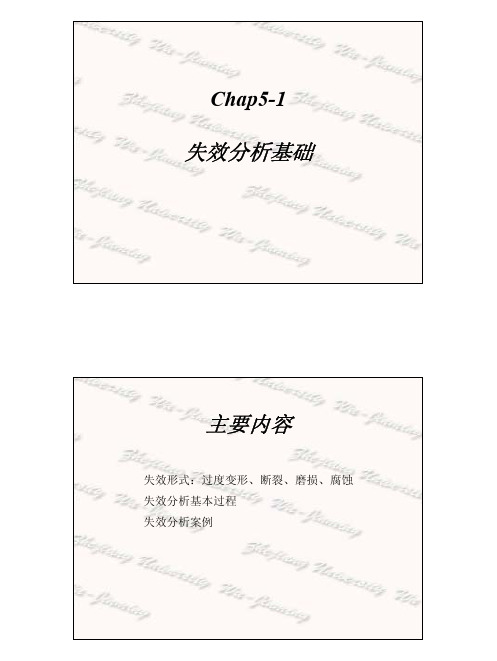
Chap5-1失效分析基础主要内容失效形式:过度变形、断裂、磨损、腐蚀失效分析基本过程失效分析案例失效失效失效基本因素•设计因素:材料、尺寸、结构、工艺等;•制造因素•装配因素•材质因素:成分、夹杂等;•运转维修因素失效形式过度变形(畸变)失效弹性畸变原因:零件形状、尺寸;材料的弹性模量;零件的工作温度;载荷大小等。
塑性畸变原因:材质缺陷、使用不当、设计失误。
断裂断裂分类¾按断口宏观形貌:韧性断裂、脆性断裂;¾按断裂模式:穿晶断裂、沿晶断裂;¾按断裂机制:解理断裂、纯剪切断裂、微孔聚集型断裂韧性断裂与脆性断裂判断标准:材料断裂前是否发生明显宏观塑性变形。
一般规定光滑拉伸试样的断面收缩率小于5%为脆性断裂;大于5%为韧性断裂。
失效形式—断裂光滑圆柱静拉伸试样的典型宏观断口特征韧性断裂(断口三区)纤维区放射区剪切唇脆性断裂断裂面与正应力垂直断口平齐光亮呈放射状或结晶状脆性断裂宏观断口形貌薄板矩形拉伸试样断口:人字纹形貌,其放射方向与裂纹扩展方向平行,尖顶指向裂纹源。
圆柱拉伸试样断口:相同断裂机制,人字纹形貌更明显。
穿晶断裂与沿晶断裂穿晶断裂可以是韧性断裂,也可以是脆性断裂(低温下);沿晶断裂多数是脆性断裂。
失效形式—断裂冰糖状断口沿晶断裂(脆性)放射状断口穿晶断裂(脆性)微孔型断口穿晶断裂(韧性)解理断裂沿特定界面发生的脆性穿晶断裂微孔聚集型断裂失效形式—断裂微孔(a)形核、(b)长大、(c)聚合直到断裂,其基本特征是韧窝等轴韧窝拉长韧窝韧窝底部的颗粒表明微孔往往在硬质点处形核。
疲劳断裂失效形式—断裂疲劳断裂——机件在变动载荷作用下经过较长时间工作后发生的低应力脆断宏观断口特征——贝纹线常见疲劳断裂零件——轴、齿轮、弹簧等瞬时断裂区贝纹线疲劳裂纹扩展区疲劳源区失效形式——磨损磨损失效¾磨损基本类型:粘着磨损、磨粒磨损、冲蚀磨损、表面疲劳磨损、微动磨损等。
¾影响因素:1.摩擦副材质2.工况参数:载荷、滑动速率、滑动距离、温度、介质、润滑等。
失效分析基本常识以及操作流程

提交分析报告
任务来源 分析过程
背景描述
分析结果
记录和图片 综合评审
分析实质原因 提出纠正措施
工艺
设计结构 材料
测试方法 使用条件 质量控制
9/24/2019
21
6.0 操作流程-1
9/24/2019
22
6.0 操作流程-2
9/24/2019
23
6.0 操作流程-3
9/24/2019
24
6.0 操作流程-4
30
9.0 FA工程师因该具备的能力
1. 要懂基础的物理科学,对物理对电路都要有 一定的基础,否则无法解释一些本质现象, 思路也不宽。
2. 要熟悉产品封装工艺,这个是失效分析的基 础,不然没法给结论。
9/24/2019
31
9.0 FA工程师因该具备的能力
3. 要懂电路和机械装配图。 4. 熟悉材料科学,会分析各种材料的相关问题。 5. 要对业界的所有失效分析设备,材料分析设
9/24/2019
6
2.0 研究对象和要求
2.1 需要做失效分析的对象
现场使用的失效样品(客诉样品) 可靠性试验失效样品 生产筛选失效样品(特大异常样品)
9/24/2019
7
2.0 研究对象和要求
2.2 失效分析层次要求
任一产品或系统的构成都是有层次的,失效原因也 具有层次性,如系统-单机-部件(组件)-零件(元 件)-材料。
上一层次的失效原因即是下一层次的失效现象。 凭我们现有资源和技术能力,结合产品特性,失效 分析适宜以器件为单元建立失效模式。分析机理达到零 件(如芯片\壳体\滤波片\插芯套组件等)层次即可。
9/24/2019
8
- 1、下载文档前请自行甄别文档内容的完整性,平台不提供额外的编辑、内容补充、找答案等附加服务。
- 2、"仅部分预览"的文档,不可在线预览部分如存在完整性等问题,可反馈申请退款(可完整预览的文档不适用该条件!)。
- 3、如文档侵犯您的权益,请联系客服反馈,我们会尽快为您处理(人工客服工作时间:9:00-18:30)。
6. 验证CA的有效性
– 在线检测 – 客户反馈
7. 完成FACA报告
– 归档保存
失效分析的注意事项
熟悉产品性能, 结构, 材料, 元件, 生产工艺,质量标准及检测方法; 失效背景资料尽可能详细准确, 尤其是”间歇性”失效案例, 要有精确 的失效现象/工作及环境条件的描述; 失效样品要避免污染和二次破坏; 样品分析要循序渐进,确保前一步检测不影响后一步检测, 由表及里, 由 非破坏性测试到破坏性测试; 数据收集和分析要坚持以下6个原则:
剖面分析法(Cross-section check)
• • • 工作原理: 就是通过研磨,切割等方法来展现样品的剖面,从而获得相关数据; 优点: 配合其他工具(如显微镜, SEM, EDX等)可以直观地检查内部结构; 缺点: 属于破坏性检测.样品制备比较麻烦,研磨/切割时应力或污染会影响剖面的状态,从而影 响检查,必要时可用离子刨光(FIB)来获得一个理想的剖面.
激光多普勒振动仪(LDV)
• 通过实时测量在外部激励下部件表面位移随时间的变化曲线, 可以很容易获得被测结构的 动态力学特性(如频率响应函数).
成分分析
元素测试:
• 俄歇电子能谱(AES)
– – – – 分析深度: 1–5 nm 空间分辨率: 10nm 探测极限: 0.1%原子浓度 可分析原子序数>2的所有元素
失效分析基础
什么是失效?
失效就是产品丧失或没有达到预期的功能. 它包 括以下四种情况:
1. 2. 3. 4. 产品在规定的条件下,不能完成其规定的功能; 产品在规定的条件下,一个或几个性能参数不能保持在规定的范围内; 即使产品在规定的条件下具有完成规定功能的能力,但因操作者的失误 而造成产品功能的丧失; 由于环境变化影响,导致功能丧失.
•
紫外分光光度仪(UPS)
– 由于分子中价电子的跃迁而产生 特定分子紫外光吸收谱图; – 样品的萃取或淋洗液.
元素及分子片段测试:
• 二次离子质谱仪(SIMS)
– – – – 分析深度: 0.5–2nm 空间分辨率: 200nm 探测极限: PPM-PPB(所有元素) 属于定性分析.
• 气相色谱质谱联用仪(GC-MS)
基本失效类型
基本失效类型 电路失效 可能原因 连接缺陷 静电或过载损伤 元件不匹配 结构缺陷 尺寸不合 结构失效 粘合不良 覆材分层 压力损伤 断裂 腐蚀 材料失效 掺杂 磨损 变形 性能退化
什么是失效分析?
失效分析是一门研究失效机理,发现失效因素,寻找解决办法, 从而消除失效再发生的工程. 它贯穿于产品的设计,生产,使用的 整个过程, 是提高产品质量的必由之路. 它主要包括以下两种行为模式:
3. 数据收集
– 外观检测 – 常规性能检测 – 对比可追溯的测试记录,从而判断是 漏检还是检测后损坏 – 若是漏检, 则须通过优化测试或用 新的测试方法来提高在线检测能力 – 非破坏性物理检测 (不破坏样品表 面,结构及材料特性) – 破坏性检查(极限检测, 分解, 剖面, 内部结构, 化学检测 等)
X-射线扫描(X-ray Scan)
• • • • 工作原理: 由于被检工件内部结构密度不同,对X射线的阻挡能力也不一样,因此X射线图像能 清晰地展现被检样品内部的细微结构. 主要用途: 主要检测电子组装(Flip-chip/CSP/BGA等焊点隐藏器件)缺陷包括:错位,虚焊,桥连, 立碑,焊料不足,气孔,内层走线断裂, 器件漏装等等. 优点: 可快速在线测试, 样品检测范围310 x 310mm(Max.) 缺点: 只能检测金属缺陷, 不能克服重叠影响, 分辨率较低.
– 失效的现象及概率 – 失效时的工作/测试条件和环境状况 – 生产/包装/储藏信息
4. 数据分析
– – – – 相关人员讨论 相关因素分析 鉴别根本原因 验证根本原因
2. 准备样品
– 失效样品要有代表性 – 失效样品无二次破坏 – 有适当的合格样品作对比
5. 寻找解决办法
– – – – 提供FA报告 相关部门讨论 基于成本及效力的衡量标准 实验验证
什么是FEMA?
• FMEA 就是在产品设计或生产过程中, 通过对产品各组成单元潜在的各 种失效模式及其对功能的影响, 与产生后果的严重程度进行分析, 提出 可能采取的预防改进措施,以提高产品可靠性的一种设计分析方法。 • FMEA行为包括如下步骤:
– – – – – – – – – 绘制产品的功能框图和可靠性框图; 确定分析的范围,列出每一个零件所有已知和潜在的失效模式; 确定每一个失效模式造成的影响; 确定每一个失效模式发生的原因,提出预防措施; 确定失效检测的方法; 确定每一个失效模式发生的概率,1-10由小到大; 确定每一个失效模式的严重程度, 1-10,加重; 估计每一失效模式被发现的难易程度,用“不易测度表示”1-10概率由大到小; 根据不同的风险优先指数,采取不同程度的对策.
抗震测试 (Shock tester)
• 衡量产品在一定外部机械冲击下的可靠性; • 设计不合格, 结构/材料缺陷都会影响到抗震性能.
声波探侧 (Aco内部因气/液体泄露, 部件间摩擦或碰撞而产生的声波信号,从而 检测产品缺陷;
Q& A?
机械特性检查
共振测试 (Resonance)
• 了解特殊部件的固有频率, 减少特定的工作条件下的共振影响; • 异常的共振特性也能反映出部件外在和内在的缺陷;
硬度测试 (Hardness)
• 衡量材料机械特性之一的参数;
耐磨性测试 (Wear-ability)
• 衡量材料机械特性之一的参数;
元素及化学态测试:
• X射线光电子能谱仪(XPS) – X射线照固体表面, 激发光电子, 其结合能反映表面成分; – 分析深度: 5–10nm – 空间分辨率: 10um
• 能量色散谱仪(EDS)
– – – – 分析深度: 1–3 um 空间分辨率: 10nm 探测极限: 0.1%原子浓度 可分析原子序数>4的所有元素
1. 2. 3. 4. 5. 6. 要确保数据真实可靠, 不要忽视误差; 要基于数据的客观判断, 不要主观臆断; 要持开放的心态积极讨论, 不要先入为主 要逻辑严密,因果关系清楚, 不要似是而非; 要做到”明察秋毫”, 不要”吞舟是漏” 要澄清所有疑问, 不要草草收兵.
失效分析的常用仪器/方法
表面形貌尺寸检查
有机物分子结构测试:
• 红外光谱仪(IR spectrum)
– 由于分子振动和转动而产生特定 分子红外光吸收谱图; – 可以直接分析样品表面(反射式), 也可以分析样品的萃取或淋洗液 (透射式).
•
原子吸收光谱仪(AAS)
– 主要用于金属的微痕量测定 – 样品制备为液体 – 探测极限: 10ng/ml
什么是RCA?
• RCA 就是对失效事件进行层层分析, 持“抽丝剥茧”的态 度, 以求发现首要原因或根本原因. • RCA 行为包括如下步骤:
– – – – – 分析数据(背景/失效现象等) 将失效分解为基本事件; 列出可能原因; 鉴别和验证根本原因; 寻找纠正措施.
• RCA 行为的特点:
– – – – 由结果到原因的逆向追踪; 如同侦探调查案件,从证据和痕迹进行分析; 确保事件与其原因有严密的因果关系; 将原因追查之最底层次.
– 用于Out-gas成分测试
内部结构检查
超声波扫描(SAM)
• • • • • 工作原理: 超声波传播若遇到不同密度或弹性系数之物质时,会产生反射回波, 反射回波强度 会因材料密度不同而有所差异. 利用此特性来对元件内部进行非破坏性检测; 主要用途: 主要用于检查内部裂纹、分层、夹杂物、附着物、空洞、孔洞等缺陷; 扫描范围:0.25×0.25mm~320×320mm 扫描分辨率0.1微米 检测时, 样品是放水中的, 属于无损探测.
显微镜
• 放大倍数: (5–10000倍)
光学轮廓仪
• 是利用白光干涉原理对样品表面进行快速, 重复性高, 高分辨率的三维测量; • 样品要求: 非金属膜层, 非透明膜层, 上下台面平整; • 垂直测量范围: 0.1nm–10mm
原子力显微镜(AFM)
• 是利用微小探针与待测物之间交互作用力(原子/分子间引力与斥力), 来呈现待测物的表面 之物理特性; • Z方向测量范围<6um, 分辨率: 0.1nm • XY方向测量范围: (Max)90*90um; 分辨率: 10nm • 可检测: 表面形貌, 表面力学特性, 磁信号, 硬度等.
产品失效不仅会导致经济上的巨大损失,甚至酿成 悲剧,而且会损害产品质量信誉,降低竟争力,最终危及 企业的生存和发展. 成功的失效分析有助于企业:
纠正设计错误 缩短研发时间 提高生产优率 减少或避免使用中的失效概率 保证产品的可靠性 提高客户的满意度
失效分析的基本步骤
1. 收集失效背景资料
电子显微镜(SEM)
• 是根据电子光学原理, 用电子束和电子透镜代替光束和光学透镜, 使物质的细微结构在非 常高的放大倍数下成像的仪器. 可分为扫描式, 反射式, 发射式和透射式电子显微镜; • 透射式电子显微镜样品必须制成电子能穿透的,厚度为100~2000 Å的薄膜; • 极限分辨率: 发射式电子显微镜(1nm); 透射式电子显微镜(0.2nm)
• FEMA行为的特点:
– – – – 是确认潜在产品生产/使用中所有失效原因的系统性分析; 將“失效的严重性、失效发生的可能性、失效检测的可能性”三方面量化分析; 是一种统计工具, 用于风险的控制/评估/管理; 在FEMA的行为组织中, 包含了诸多RCA行为(确定每类失效模式发生的原因).
失效分析的必要性
行为模式 Root Cause Analysis (RCA) 主要目标 对已发生的失效案例进行分 析,寻找解决办法. 行为构成 研究失效机理 分析根本原因 寻找解决办法 分析失效模式 Failure Mode & Effect Analysis (FMEA) 对新产品新工艺可能发生的 失效模式及影响进行系统和 量化的分析,寻找预防办法. 分析失效影响 评估危害程度 寻找预防办法