用宏程序编程车削梯形螺纹ok
在数控车床上用宏程序加工梯形螺纹

不是理想的加工方法。
ቤተ መጻሕፍቲ ባይዱ
为了解决“直进分”和“斜进法”的缺点,就
必须改善刀具的切削方式。通过分析,最后选用
(见图3)“分层切削法”。“分层切削法”是先
把螺纹X向分成若干层,
每层Z向再进行若干次粗
切削,再进行左、右精车
切削。每层刀具只需沿左
右牙型线切削,背吃刀量
小,从而使排屑比较顺
利,刀具的受力和受热情
图3 分层切削法
起刀点Z轴偏 移量(CE)的计 算公式为
图7
CE=BE-BC=(AH+tan15°×HE)-BC =(P/4+tan15°×HE)-BC 即起刀点Z轴偏移量(螺纹右侧留0.1mm的精 加工量)参数变量为
#8=#2/4+TAN[15]*[#1-#3]/2-#6/2-0.1;
每层Z轴的切削余量(DF)的计算公式为
M 机床自动化 achine Tools Automation
在数控车床上用宏程序加工梯形螺纹
中国北车永济新时速电机电器有限责任公司 (山西 044502) 陈建军 永济电机高级技工学校 (山西 044500) 张丽波
一、梯形螺纹在数控车床上的加工工艺
数控车加工螺纹有三种指令:G32、G92、 G76。其中G32、G92的进刀方式为“直进法” (见图1);G76的进刀方式为“斜进法”(见图 2)。
DF=BF-BD=2(AH+tan15°×HE)-BD
即每层Z轴的切削余量(螺纹左侧留0.1mm的 精加工量)参数变量为
#9=#2/2+TAN[15]*[#1-#3]-#6-0.1
(3)外螺纹Tr36×6程序
O8888; M03S200; G00X100Z50; T0101; G00X40Z10; #1=36;(螺纹大径及公称直径) #2=6;(螺距) #3=#1-#2/2;(螺纹中径) #4=0.5;(牙顶间隙) #5=#1-#2-2*#4;(螺纹小径) #6=1(T型螺纹刀刀尖宽) #7=0.366*#2-2*TAN[15]*#4;(牙底槽宽) #8=#2/4+TAN[15]*[#1-#3]/2-#6/2-0.1;(起 到点Z轴偏移量,右侧留0.1mm) #9=#2/2+TAN[15]*[#1-#3]-#6-0.1;(每层Z 轴的切削余量,左侧留0.1mm) #10=0.5(X轴的吃刀量) N1IF[#1LE#5]GOTO4;(判断切削直径,如果X值 ≤小径,则执行N4程序段) N2IF[#9LE0.1]GOTO3;(判断每层Z轴切削余量如 果余量≤0.1mm,则执行N3程序段) G00Z[10+#8];(Z轴起刀点) G92X#1Z-42F#2;(切削螺纹) #8=#8-0.3;(重新计算Z轴起刀点偏移量,递减0.3mm) #9=#9-0.3;(重新计算每层Z轴切削余量,递减0.3mm) GOTO2;(无条件执行N2程序段) N3#1=#1-#10;(重新计算切削直径X值) #8=#2/4+TAN[15]*[#1-#3]/2-#6/2-0.1(重新 计算Z轴起刀点偏移量) #9=#2/2+TAN[15]*[#1-#3]-#6-0.1;(重新计 算每层Z轴切削余量) IF[#1GE33]THEN#10=0.5(判断切削直径,对X轴吃刀 量重新赋值)
用宏程序加工梯形螺纹
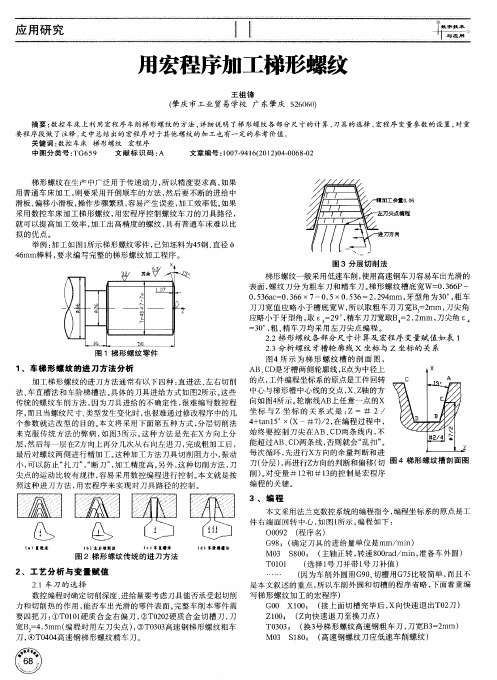
梯 形 螺 纹 在 生 产 中广 泛 用 于 传 递 动 力 , 以精 度 要 求 高 , 果 所 如 用普通车床加工 , 要采用开倒顺车的方法 , 则 然后 要 不 断 的 进 给 中 滑 板 、 移 小 滑 板 , 作 步骤 繁 琐 , 易 产 生 误 差 , 工 效 率 低 。 果 偏 操 容 加 如 采 用 数 控 车 床 加 工梯 形螺 纹 , 宏 程 序 控 制 螺 纹 车 刀 的刀 具 路 径 , 用 就可 以提高加工 效率 , 加工 出高精度的螺纹 , 有普通车床难以 比 具 拟的优点 。 举例 : 工如 图l 加 所示 梯 形 螺纹 零件 , 已知 坯 料 为 4 钢 、 径 5 直 4 mm棒 料 , 求 编 写 完 整 的 梯 形 螺 纹 加 工 程 序 。 6 要
图 3 分 层切 削 法
梯形螺纹一般采用低速车削 , 使用高速钢车刀容易车 出光滑的 表面 , 螺纹刀分为 粗车刀和精车刀 。 梯形螺 纹槽 底宽W= .6 P一 0 36 0 5 6 c 0 3 6×7 . 0 5 6=2 24 .3a = .6 —0 5× .3 .9 mm, 型 角 为 3 。 粗 车 牙 0, 刀 刀 宽值 应 略 小 于 槽 底 宽 w , 以 取 粗 车 刀 刀 宽B = rm, 尖 角 所 2 a 刀 应略小于牙型角 , E = 9 , 取 2 。精车刀刀宽取B =2 2 m , . r 刀尖角 £ a 3 。粗 、 车 刀 均 采 用 左 刀尖 点编 程 。 0, 精
2 工 艺分 析 与 变 量 赋 值 、
21车刀 的选 择 . 数控编程 时确定切削深度 、 给量要考虑刀具 能否承受起切削 进 力 和 切 削 热 的作 用 , 能否 车 出 光 滑 的 零件 表 面 。 整 车 削本 零件 需 完 要 四把 刀 : 0 0 硬 质 合 金 右 偏 刀 , ①T 1 1 ②T00 硬 质 合 金 切 槽 刀 , 22 刀 宽B = .rm( ,45 a 编程时用左刀 尖点 ) ̄T00 高速钢梯 形螺 纹粗车 , 33 刀 , T 44 速钢梯形螺纹精 车刀。 9 ( 00 高
B类宏程序加工梯形螺纹的方法和技巧

B类宏程序加工梯形螺纹的方法和技巧作者:陈未峰来源:《职业·中旬》2012年第03期一、B类宏程序在数控编程中的重要性在数控车削加工中,普通轴类零件的轮廓形状都可以利用G功能指令来完成加工。
但异形曲线和大螺距螺纹大大增加了零件的加工难度,G指令编程不好实现这类零件的有效加工。
例如梯形螺纹较之三角螺纹,螺距和牙型都大,而且精度高,牙型两侧表面粗糙度值较小,这样梯形螺纹车削时,吃刀深、走刀快、切削余量大、切削抗力大,导致梯形螺纹的车削加工难度较大。
与宏程序相比,一般程序的程序字为常量,一个程序只能描述一个几何形状,所以缺乏灵活性和适用性。
而用户宏程序本体中可以使用变量进行编程,还可以用宏指令对这些变量进行赋值、运算等处理,从而可以使用宏程序执行一些有规律变化的动作。
与A类宏程序相似,B类宏程序的变量也是由“#”符号和1至3位数字构成;但B类宏程序的数学运算可直接用数学符号完成,而不需采用G65语句,有效地提高了零件的编程灵活性和加工效率。
因此,使用B类宏程序加工有梯形螺纹的零件,对提高数控编程的效率是非常重要的。
二、球头梯形螺纹零件加工工艺分析1.球头梯形螺纹零件分析如图1所示,球头梯形螺纹轴由球面、曲面、退刀槽和梯形螺纹构成,其螺距为6mm,加工精度要求较高,球面和曲面加工简单。
在FANUC 0i数控系统机床上加工时,利用G73复合固定循环就可以进行有效加工,但由于梯形螺纹螺距较大和加工精度较高,致使梯形螺纹车削时,吃刀深、切削余量大、切削抗力大,车削加工难度较大。
利用普通G功能指令无法高质量、有效地完成该零件的加工,需利用B类宏程序进行切削加工。
2.计算相关尺寸,并查表确定公差该零件上梯形外螺纹为Tr36×6,螺距为6mm,公制梯形螺纹的牙型角为30°,梯形螺纹的牙型如图2所示,各基本尺寸计算结果如下:大径中径d2=d-0.5P=36-3=33,查表确定其公差,故;牙高h3=0.5P+ ac=3.5;小径d3=d-2 h3=29,查表确定其公差,故;牙顶宽f=0.366P=2.196;牙底宽W=0.366P-0.536ac =2.196-0.268=1.928螺纹中经三针测量法测量,如图3所示,用3.1mm的测量棒测量中径,则测量尺寸为M=d2+4.864dD-1.866P=32.88,根据中径公差确定公差,则(其中dD表示测量用量针的直径,P 表示螺距)。
梯形螺纹的宏程序加工

梯形螺纹的宏程序加工摘要:梯形螺纹是数控车工加工的难点,宏程序是数控编程的难点,然而二者结合起来就会使数控机床加工梯形螺纹,操作者只要修改参数的数值就可以完成不同螺距与长度的梯形螺纹加工,十分的方便快捷。
关键词:数控车床FANUC系统梯形螺纹宏程序#1=A 梯形螺纹大径#2=B 梯形螺纹小径#3=B 梯形螺纹牙底槽宽#4=I 梯形螺纹车刀刀头宽度#5=J 梯形螺纹长度L#6=K 梯形螺纹螺距#7=D 升速段长#8=E 减速段长#9= 粗车转速#10= 精车转速#19=S 精加工余量(直径值)主程序:O0001;N10 G54 G40 G21;N20 T0404;调用梯形螺纹车刀N30 G65 P333;调用梯形螺纹宏程序N40 M05;主轴停止转动N50 M30;程序结束并返回程序开头宏程序;O333N10 M03 S#9;主轴正转,转速为#9N20 #30=FUP[[#1-#2-#19]/2/#18];根据背吃刀量和精加工余量计算径向粗车循环次数(下取整)N30 #31=[#1-#2-#19]/#30;计算径向粗加工每次背吃刀量(直径值)N40 #40=FUP[#3-#4-#19/2]/2/#20;计算Z向粗车循环次数;N50 #41=[#3-#4-#19/2]/2/#40;计算Z向粗加工每次背吃刀量N60 #28=1;径向切削次数初始值赋值N70 WHILE[#28GT#30]DO1;N80 G00 X[#1+3];车刀快速移动到X方向起刀位置N90 Z#7;车刀快速移动到Z方向起刀点N100 X[#1-#31];车刀径向切入一个背吃刀量N120 G32 Z-[#5+#8]F#6;粗车梯形螺纹N110 #29=1;Z向切削次数初始值赋值N130 WHILE[#29GT#40]DO2;N140 G00 X[#1+3];车刀快速返回到X方向起刀位置N150 Z#7;车刀快速移动到Z方向起刀点N160 W-#41;车刀Z向负向移动一个切削量N170 X[#1-#31];车刀径向进刀#31N180 G32 Z-[#5+#8]F#6;粗车梯形螺纹N190 G00 X[#1+3];车刀快速返回到X方向起刀位置N200 Z#7;车刀快速移动到Z方向起刀点N210W#41;车刀Z向正向移动一个切削量N220X[#1-#31];车刀径向进刀#31N230G32Z-[#5+#8]F#6;粗车梯形螺纹N240G00X[#1+3];车刀快速返回到X方向起刀位置N250Z#7;车刀快速移动到Z方向起刀点N260#29=#29+1;Z向移动次数增加1N270#41=#41*#29;Z向移动量递增N280END2;N290#28=#28+1;X向切削次数增加1N300#31=#31*#28;X向切削量递增N310END1;N320 #41=[#3-#4-#19/2]/2/#40;计算Z向粗加工每次背吃刀量N330#29=1;Z向切削次数初始值赋值N340S#10;选用精加工转速N350G00X[#1+3];车刀快速返回到X方向起刀位置N360Z#7;车刀快速移动到Z方向起刀点N370X#2;车刀进给到X向精车位置N380G32Z-[#5+#8]F#6;精车螺纹牙底N390WHILE[#29GT#40]DO3;N400G00X[#1+3];车刀快速返回到X方向起刀位置N410Z#7;车刀快速移动到Z方向起刀点N420X#2;车刀进给到X向精车位置N430W-#41;车刀Z向负向移动一个切削量N440G32Z-[#5+#8]F#6;精车螺纹牙底N450G00X[#1+3];车刀快速返回到X方向起刀位置N460Z#7;车刀快速移动到Z方向起刀点N470X#2;车刀进给到X向精车位置N480W#41;车刀Z向正向移动一个切削量N490G32Z-[#5+#8]F#6;精车螺纹牙底N500#29=#29+1;Z向移动次数增加1N510#41=#41*#29;Z向移动量递增N520END3;N530G00X[#1+3];车刀快速返回到X方向起刀位置N540Z#7;车刀快速移动到Z方向起刀点N550X#2;车刀进给到X向精车位置N560W-[#3-#4]/2;车刀移动到螺纹牙右侧面起点N570G32Z-[#5+#8]F#6;精车螺纹牙牙右侧面N580G00X[#1+3];车刀快速返回到X方向起刀位置N590Z#7;车刀快速移动到Z方向起刀点N600X#2;车刀进给到X向精车位置N610W[#3-#4]/2;车刀移动到螺纹牙左侧面起点N620G32Z-[#5+#8]F#6;精车螺纹牙牙左侧面N630G0X100;N640Z100;N650M99。
基于宏程序的螺纹车削编程与加工

基于宏程序的螺纹车削编程与加工螺纹车削是数控机床中非常重要的一种加工方式,可以根据不同的需求进行不同精度的加工,而宏程序则是一种可以将多个相同或相似的操作整合成一个程序以实现高效加工的方式。
在螺纹车削加工中,需要用到许多不同的参数,包括切削速度、切削深度、进给速度等等,这些参数都需要在编程过程中进行指定和调整,以保证最终的加工效果。
而使用宏程序的话,可以将这些参数设置为变量并进行统一的控制,大大减少了重复操作和调整参数的时间,提高了加工效率。
例如,在宏程序中可以设定一个变量表示螺纹的直径,然后在代码中通过调用这个变量来计算线速度和轴进给速度等参数,从而节省了大量时间和精力。
在具体实现上,宏程序可以由多行代码组成,每行代码都可以实现一个特定的操作,例如计算参数、调用函数等等。
在螺纹车削中,宏程序可以进行以下几个方面的操作:1. 设置初始参数,包括切削速度、进给速度、切削深度等等,从而进行统一控制。
2. 计算切削参数,例如计算线速度、轴进给速度和材料移除量等参数,以实现更精确的加工效果。
3. 调用相应的函数,例如使用M指令调用换刀功能、使用S指令调整切削速度等等。
4. 针对不同工件进行不同的宏程序设定,例如在需要加工多种不同型号的螺纹时,可以根据不同型号设定对应的宏程序,方便复用和调整。
通过使用宏程序,螺纹车削加工可以实现更高效,更精确的加工效果,同时也可以节省人力和时间成本,提高生产效率。
相关数据是指通过对某一特定主题的数据收集、整理、处理、分析等过程而获得的结果。
对于相关数据的分析,可以通过各种方式进行,包括制作表格、图表、统计分析等等。
以下是一些列出相关数据并进行分析的示例。
以“全国居民人均可支配收入”为例,可以从各省市的数据进行收集和整理,然后进行分析。
首先,可以制作一张表格,统计出各个省份、自治区和直辖市的平均可支配收入。
在这张表格中,还可以加入年份或者季度等时间维度,以追踪收入变化的趋势。
宏程序在梯形螺纹数控车削加工中的应用

数控系统宏程序可允许在编程阶段对变量予以设置,同时还可就变量实施算数、逻辑运算处理,利用程序开展条件转移与循环操作处理,从而加强对刀具的控制精确性,加工出形状更加复杂、性能更加优异的零件。加工时,及时做好对程序中的宏参数的测量与修改,以便实现对其精度的有效控制。在对切削用量进行调节亦或进行刀具更换时,仅需调整程序中#4、#5参数即可。进行多种不同螺距的梯形螺纹加工时,仅需调整宏程序内的X、Z等参数即可。因在低速切削时所采用的是高速钢刀具,所以主轴转速不宜过高。
关键词:宏程序;梯形螺纹;数控车削;加工应用
目前,我国在数控机床方面的发展已经有了很大的提高,各项数控技术和管理也在逐渐完善,但是还有很多的不足。专业人士经过调查研究发现,对数控编程不及时是造成数控机床发生故障的主要原因。所以说,数控的编程的效率能够在很大程度上关系到数控技术的价值。现在,数据技术已经在我国快速发展起来,其中宏程序是其必不可少的,它可以将数控编程进行扩展,进一步提高数控编程程序的范围,并且还可以使加工程序得到简化,大大提高数控机床的效率。
宏程序在梯形螺纹数控车削加工中的应用
摘要:近年来,我国科学技术在快速发展,机械行业也不断地将先进的科学技术应用到机械制造中。而在数控车削的加工过程中,梯形螺纹的制造是其中的一个极其繁杂的程序,这些年来,我国对梯形螺纹的加工技艺已经有了很大的改进,但从国际的科学水平上来看,该加工技术还有很大的发展空间。这篇文章主要分析了我国对梯形螺纹数控加工技术的现状,归纳出一些加工难点,将宏程序应用到梯形螺纹数控车削加工程序中,这样能够大大的提高!梯形螺纹加工程序的精确度,进而可以使梯形螺纹数控加工工艺得到快速的发展。
三、梯形螺旋数控车削加工技艺的改进。
通过对以上四种梯形螺纹加工方式的对比分析后发现,斜切法、车槽法、左右切削法均能够在一定程度上降低甚至完全杜绝三刃同时切削的情况,由此便能够确保刀尖的磨损情况得到有效改善,在进行废屑排除时也更加畅通,能够极大的规避振动与扎刀情况的出现,大幅提升刀具切削参数,保证梯形螺纹较高的加工质量水平。然而,要想十分熟练的掌握以上三种车削方式面临着较大挑战,且操作较为复杂,因此还有待进一步改进、优化。为了同时提高车削质量与效率,可将直切法与左右切削法相结合,以此形成“分层切削法”。利用这一方法实施梯形螺纹切削加工处理,可大幅改善梯形螺纹加工中的各种问题缺陷。
用宏程序加工螺纹的方法
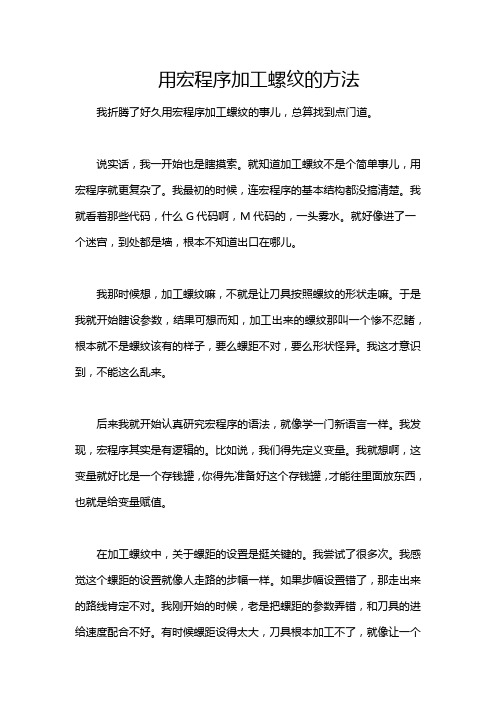
用宏程序加工螺纹的方法我折腾了好久用宏程序加工螺纹的事儿,总算找到点门道。
说实话,我一开始也是瞎摸索。
就知道加工螺纹不是个简单事儿,用宏程序就更复杂了。
我最初的时候,连宏程序的基本结构都没搞清楚。
我就看着那些代码,什么G代码啊,M代码的,一头雾水。
就好像进了一个迷宫,到处都是墙,根本不知道出口在哪儿。
我那时候想,加工螺纹嘛,不就是让刀具按照螺纹的形状走嘛。
于是我就开始瞎设参数,结果可想而知,加工出来的螺纹那叫一个惨不忍睹,根本就不是螺纹该有的样子,要么螺距不对,要么形状怪异。
我这才意识到,不能这么乱来。
后来我就开始认真研究宏程序的语法,就像学一门新语言一样。
我发现,宏程序其实是有逻辑的。
比如说,我们得先定义变量。
我就想啊,这变量就好比是一个存钱罐,你得先准备好这个存钱罐,才能往里面放东西,也就是给变量赋值。
在加工螺纹中,关于螺距的设置是挺关键的。
我尝试了很多次。
我感觉这个螺距的设置就像人走路的步幅一样。
如果步幅设置错了,那走出来的路线肯定不对。
我刚开始的时候,老是把螺距的参数弄错,和刀具的进给速度配合不好。
有时候螺距设得太大,刀具根本加工不了,就像让一个小孩迈很大的步子跑步,根本跑不起来,只会摔倒。
还有刀具的补偿也很重要。
我一开始没太在意这个,结果螺纹的尺寸总是加工不准确。
我就想,这刀具补偿就好比是给一个干活的人额外的支持,如果没有给够,活肯定干不好。
在实际操作中,我还发现要根据材料的不同调整参数。
比如加工钢料和铝料的时候,刀具的进给速度和转速就得变。
就好像你开车在不同路况下也得调整速度是一个道理。
要是在马路上开车照高速公路的速度开,那就得出事。
加工铝料的时候,可以稍微快一点,因为铝比较软好加工。
另外一个不确定的地方就是,不同系统的宏程序编写可能会有点差别。
比如我之前在一个老一点的机床系统上编宏程序,和新系统有些代码和格式上的不同。
我觉得要是想学好这个,最好是在同种系统的机床上多练习,就像学骑自行车,最好每天都骑同一辆车,熟悉了就好了。
浅谈宏程序在数控车床梯形螺纹加工中的应用

1 . 3 分层切削 法
分 层 切 削 法 是 在 总 结 直 进 法 和 斜 进 法 优 缺 点 的 基 础 上
提 出的新方 法 ,也 是使 用宏程 序加 工梯 形螺 纹 的主 要方 法 ( 如 图 l中 的 C所 示 ) , 将 梯 形 螺 纹 加 工 余 量 均 匀 分 为 若 干 层 ,进 完第 一 刀后 ,向左或 向右 移动 刀具 ,去 除第一 层 余 量 ,然后 依次往 复 由外至 内逐 层去 除余量 ,最后 进行 精 加 工 。这 种 方 法 在 加 工 过 程 中 ,每 层 加 工 时 , 刀 具 沿 着 螺 纹 的左 右牙 型加 工,刀 具 吃刀量 小且始 终 只有 1 个 侧刃 参 与 切 削 ,排 屑 比 较 顺 利 ,刀 具 的 受 力 和 散 热 情 况 得 到 改 善 ,
1 2 2
现代 制造技术与装 备
2 0 1 5 第5 期 总 第2 2 8 期
浅 谈 宏 程序 在 数 控 车床 梯 形 螺纹 加 工 中的应 用
宋 胄
( 泰 州机 电高等职业技 术学校 ,
摘
要 :本 文主要 对 梯形 螺纹在 数控 车床 上 的加 工 工艺进行 研 究 ,并通 过 实例对 梯形 螺 纹的 宏程序 编程 进行
刀左 侧刃 、车 刀右侧 刃 )同时进 行切 削,切 削 的力度会 随
着 热 能 的增 加 而 增 长 ,刀 头 的 磨 损 也 会 加 剧 ,容 易发 生 “ 崩 刀 ”现 象 。 1 . 2 斜 进 法 斜 进法 主要 是指 车刀沿 着牙 型角 方 向斜 向进 给 至牙底 深 处 , 在 进 给 过 程 中 间歇 进 入 。 在 加 工 过 程 中 , 螺 纹 车 刀 至 始 至 终 只有 一 个 刀 刃 参 与 切 削 , 排 屑 顺 畅 , 刀 具 受 力 和 受 热情 况均 较好 ,不 易产生 “ 崩 刀 ” 现 象 , 但 由于 在 加 工
- 1、下载文档前请自行甄别文档内容的完整性,平台不提供额外的编辑、内容补充、找答案等附加服务。
- 2、"仅部分预览"的文档,不可在线预览部分如存在完整性等问题,可反馈申请退款(可完整预览的文档不适用该条件!)。
- 3、如文档侵犯您的权益,请联系客服反馈,我们会尽快为您处理(人工客服工作时间:9:00-18:30)。
用宏程序编程车削梯形螺纹梯形螺纹较之三角螺纹,其螺距和牙型都大,而且精度高,牙型两侧面表面粗糙度值较小,致使梯形螺纹车削时,吃刀深、走刀快、切削余量大、切削抗力大,这就导致了梯形螺纹的车削加工难度较大。
1普通车床车削梯形螺纹方法车削梯形螺纹时,通常采用高速钢材料刀具进行低速车削,低速车削梯形螺纹一般有如图1所示的四种进刀方法:直进法、左右切削法、车直槽法和车阶梯槽法。
通常直进法只适用于车削螺距较小(P<4mm)的梯形螺纹,而粗车螺距较大(P>4mm)的梯形螺纹常采用左右切削法、车直槽法和车阶梯槽法。
下面分别探究一下这几种车削方法:图1梯形螺纹车削的四种进刀方法直进法:直进法也叫切槽法,如图1(a)所示。
车削螺纹时,只利用中拖板进行横向(垂直于导轨方向)进刀,在几次行程中完成螺纹车削。
这种方法虽可以获得比较正确的齿形,运动轨迹也很简单,但由于刀具三个切削刃同时参加切削,振动比较大,牙侧容易拉出毛刺,不易得到较好的表面品质,并容易产生扎刀现象,因此,它只适用于螺距较小的梯形螺纹车削。
左右切削法:左右切削法车削梯形螺纹时,除了用中拖板刻度控制车刀的横向进刀外,同时还利用小拖板的刻度控制车刀的左右微量进给,直到牙形全部车好,如图1(b)所示。
用左右切削法车螺纹时,由于是车刀两个主切削刃中的一个在进行单面切削,避免了三刃同时切削,所以不容易产生扎刀现象。
另外,精车时尽量选择低速(v=4~7m/min),并浇注切削液,一般可获得很好的表面质量。
车直槽法:车直槽法车削梯形螺纹时一般选用刀头宽度稍小于牙槽底宽的矩形螺纹车刀,采用横向直进法粗车螺纹至小径尺寸(每边留有0.2~0.3mm的余量),然后换用精车刀修整,如图1(c)所示。
这种方法简单、易懂、易掌握,但是在车削较大螺距的梯形螺纹时,刀具因其刀头狭长,强度不够而易折断:切削的沟槽较深,排屑不顺畅,致使堆积的切屑把刀头“砸掉”:进给量较小,切削速度较低,因而很难满足梯形螺纹的车削需要。
车阶梯槽法:为了降低“直槽法”车削时刀头的损坏程度,我们可以采用车阶梯槽法,如图1(d)所示。
此方法同样也是采用矩形螺纹车刀进行切槽,只不过不是直接切至小径尺寸,而是分成若干刀切削成阶梯槽,最后换用精车刀修整至所规定的尺寸。
这样切削排屑较顺畅,方法也较简单,但要换刀效率不高。
综上所述:除直进法外,其他三种车削方法都能不同程度地减轻或避免三刃同时切削,使排屑较顺畅,刀尖受力、受热情况有所改善,从而不易出现振动和扎刀现象,还可提高切削用量,改善螺纹表面品质。
所以,左右切削法、车直槽法和车阶梯槽法获得了广泛的应用。
2数控车削梯形螺纹方法的选用根据上述分析,数控车床车削梯形螺纹采用“分层法“比较合适。
分层法”车削梯形螺纹实际上是直进法和左右切削法的综合应用。
在车削梯形螺纹时,“分层法”通常不是一次性就把梯形槽切削出来,而是把牙槽分成若干层(每层深度根据具体情况设定),转化成若干个较浅的梯形槽来进行切削,从而降低了车削难度。
每一层的切削都采用先直进后左右的车削方法,由于左右切削时槽深不变,刀具只须做向左或向右的纵向进给即可(如图2所示),因此它比上面提到的左右切削法的运动轨迹要简单得多。
第三刀右移刀切削第二刀左移刀切削第一刀直进刀切削图2分层法车削梯形螺纹图3宏程序编程车削梯形螺纹本文以加工一个Tr80×10的梯形螺纹(如图3所示)为例介绍用宏程序编写加工程序(采用FANUC 0i Mate TC 系统)28010φ68Tr 80X 10图3梯形螺纹零件图(1)数值计算①梯形螺纹加工尺寸计算表1梯形螺纹的计算式及其参数值名称代号计算公式及参数值(mm )牙顶间隙ac 0.5大径d 公称直径Φ80中径d 2d 2=d-0.5P=75小径d 1d 3=d-2h=69牙高h h=0.5P+ac=5.5牙顶宽f f=0.366P=3.66牙槽底宽ww=0.366P-0.536ac=3.392②左(右)移刀量的计算牙深30左(右)移刀量当前层背吃刀量如上图可以得出分层切削时左(右)移刀量计算式为Ⅰ、当刀头宽度等于牙槽底宽时,左(右)移刀量=tan15°×(牙深—当前层背吃刀量);Ⅱ、当刀头宽度小于于牙槽底宽时,左(右)移刀量=tan15°×(牙深—当前层背吃刀量)+(牙槽底宽—刀头宽度)/2(2)“分层法”车削梯形螺纹的刀具选择“分层法”车削梯形螺纹所用的粗车刀和精车刀与其它加工方法基本相同,只是粗车刀的刀头宽度小于牙槽底宽,刀具刀尖角略小于梯形螺纹牙型角。
(3)参考程序①编程分析用宏程序编程时变量的设置是核心内容,一是要变量尽可能少,避免影响数控系统计算速度,二是便于构成循环。
经过分析本例中要4个变量,#1为刀头到牙槽底的距离,初始值为 5.5mm,#2为背吃刀量(半径值),#3为(牙槽底宽—刀头宽度)/2,#4为每次切削螺纹终点X坐标。
本例中编程关键技术是要利用宏程序实现分层切削和左右移刀切削。
利用G92螺纹加工循环指令功能,左右移刀切削只需将切削的起点相应移动0.268*[#1-#2]+#3(右移刀切削)或者-0.268*[#1-#2]-#3(左移刀切削)就可以实现。
分层切削的实现通过#1和#2变量实现,每层加工三刀后,让#1=#1-#2实现进刀,而在每层中螺纹的X坐标不变,始终为#4=69.0+2*[#1-#2]。
②参考程序(此程序已运用于FANUC0i Mate TC系统车床加工零件)参考程序注释O0001;程序号N10T0101;换01号刀具,调用01号偏置值N20M08;打开切削液N30M03S180;主轴正转,转速为180r/minN40G00X90.0Z10.0;刀具快速移动到点(90,10)N50#1=5.5;#1为刀头到牙槽底的距离,初始值为5.5mm N60#2=0.2;#2为背吃刀量(半径值)N70#3=(牙槽底宽—刀头宽度)/2;#3为(牙槽底宽—刀头宽度)/2N80WHILE[#1GE0.2]DO1;当#1≥0.2,执行循环1,底部留0.2mm的精车余量N90#4=69.0+2*[#1-#2];#4为每次切削螺纹终点X坐标N100G00Z5.0;移动到直进刀切削的循环起点N110G92X#4Z-286.0F10.0;直进刀车削螺纹N120G00Z[5+0.268*[#1-#2]+#3];移动到右移刀切削的循环起点N130G92X#4Z-286.0F10.0;右移刀车削螺纹N140G00Z[5-0.268*[#1-#2]-#3];移动到左移刀切削的循环起点N150G92X#4Z-286.0F10.0;左移刀车削螺纹N160#1=#1-#2;构成循环N170END1;当#1<0.2,跳出循环1N180G00X200.0Z150.0;快速退刀N190M09;关闭切削液N200M30;程序结束说明:①参考程序以工件右端面中心为编程原点。
②若螺纹的表面粗糙度要求不高,可以只用一把粗车刀加工即可,执行完程序后进行测量,根据测量结果判断是否需要调整牙槽底宽的余量。
若中径尺寸未到,可以适当调整#3的数值,直至合格为止。
背吃刀量可以根据工件材料、刀具选择,只需修改#2的数值即可。
③若螺纹的表面粗糙度要求较高,先用粗车刀粗车,除底部留有余量外,侧面余量在#3变量上调节,要留余量则在#3=(牙槽底宽—刀头宽度)/2基础上减去所留余量,如0.2的侧面余量,则#3=(牙槽底宽—刀头宽度)/2-0.2;再用精车刀精车,依然使用该程序,只修改刀具指令和#3即可。
4应用宏指令将梯形螺纹加工程序模块化应用宏指令,将左右移刀法加工梯形螺纹模块化,应用时只需将宏指令中的自变量赋值修改一下即可加工不同尺寸的梯形螺纹而宏程序中的内容不需修改。
通过上述程序和分析,梯形螺纹加工需要的自变量有:#1=(A)每一刀的进刀深度(半径值),(本例中初始值为牙高 5.5mm);#2=(B)背吃刀量;(本例中为0.2mm)#3=(C)刀头宽度偏差=(牙槽底宽—刀头宽度)/2;#4=(I)螺纹小径;#5=(J)螺距;#6=(K)螺纹长度;(1)主程序O0002;程序号N10T0101;选择刀具并调用刀具偏置值N20M08;打开切削液N30M03S200主轴正转,转速为200r/minN40G65P1000A_B_C_I_J_K_;宏指令调用程序O1000,并给变量赋值N50G00Z150.0;刀具快速沿Z轴退刀N60G00X200.0;刀具快速沿X轴退刀N70M09;关闭切削液N80M30;程序结束(2)宏程序O1000;程序号N10#7=#4+2*[#1];计算出螺纹公称直径N20G00X[#7+5.0]Z15.0;刀具快速移动到工件外一点,准备加工螺纹N30WHILE[#7GT#4]DO1;当#7>#4时,执行循环1N40#1=#1-#2;刀具每次进刀0.2mm,构成循环N50#7=#4+2*[#1];计算出每一刀螺纹终点X坐标N60G00Z10.0;移动到直进刀切削的循环起点N70G92X#7Z-[#6+2.0]F#5;直进刀车削螺纹N80G00Z[10.0+0.268*[#1]+#3];移动到右移刀切削的循环起点N90G92X#7Z-[#6+2.0]F#5;右移刀车削螺纹N100G00Z[10.0-0.268*[#1]-#3];移动到左移刀切削的循环起点N110G92X#7Z-[#6+2.0]F#5;左移刀车削螺纹N120END1;当#7<#4时,跳出循环外N130M99;子程序结束并返回主程序5结束语宏程序是程序编制的高级形式,程序编制的质量与编程人员的素质息息相关,因为宏程序中应用了大量的编程技巧,如数学关系的表达、加工刀具的选择、走到方式的取舍等。
掌握宏程序可以解决复杂工件加工或者避免烦琐的数学计算。