螺柱超声波探伤
锻钢件的超声波探伤检查方法缺陷等级分类及判定标准

锻钢件的超声波探伤检查方法缺陷等级分类及判定标准1•目的规范公司锻钢件的超声波探伤检查方法,规范缺陷等级分类及判定标准2•内容2.1探伤装置使用脉冲反射式超声波探伤仪。
2.2探伤方法原则上采用单晶头垂直探伤法。
但是精密探伤及有特殊要求的部位,将同时采用其他探伤方法。
2.3探伤方向及探伤范围按下表实施探伤。
但是,认定有缺陷等异状时,必须从所有方向开始探伤。
探伤方向及扫查范围向:对半圆周进行全面探伤。
但小齿轮、螺纹轴、蜗轮、辊子等表层附近特别重要的锻钢件,要从整周开始进行全面探伤。
轴类锻钢件径向:外周全面探伤轴向:从两个方向进行全面探伤轴向:从两个方向开始进行全面探伤从长度方向,宽度方向,板厚方向三个方向开始进行全面探伤。
但齿条等表层附近特别重要的锻钢件,三个方向均需从两面开始全面探伤。
径向:对外周进行全面探伤轴向:从一个方向开始全面探伤。
但是,齿圈等表层附近特别重要的锻钢件要从两个方向起全面探伤。
径向:对外周进行全面探伤轴向:从一个方向开始全面探伤。
但是,齿轮、车轮等表层附近特别重要的锻钢件要从两个方向起全面探伤。
探伤表面的表面粗糙度要达至【Ra12.5以上较好精加工状态。
2.5测量范围的调整原则上,测定范围要调整至底面回波在显示屏时间轴上显现2次。
2.6探伤方式、使用频率和使用探头探伤方式,使用频率和使用探头见下表。
2.7探伤灵敏度的设定2.7.1底面回波方式的灵敏度设定⑴直径或壁厚在2mm以下的部位,将各不同直径或壁厚的致密部位上第1次底面回波高度(BG)调整至探伤仪显示器刻度板的80%。
然后,根据图4进行灵敏度的增幅,以此作为探伤起始灵敏度。
另外,对于超过检查部位的壁厚1/2以上的区域进行探伤时,需要进一步提高灵敏度12dB进行探伤。
关于小齿轮、螺纹轴、蜗轮、齿轮、齿条、车轮等表层附近特别重要的锻钢件,则用提高了12dB后的灵敏度进行全面或是从两面开始探伤。
⑵试验部位的壁厚超过2m时,使用探头专用的DGS曲线图。
铸、锻件的超声波探伤检测方法

•
斜探头——晶片面积为140mm2~
400mm2,频率为2.5MHZ。探测与表面垂
直缺陷宜用K1(45°),必要时用.表面要求与耦合剂:
• 表面要求:检测面表面要求平整,最好经 机加工,表面粗糙度Ra应小于6.3μm,□ 工件表面应去除氧化皮、污物等附着物。
• 耦合剂:机油、浆糊、甘油等。
•
dB 20lg 2—X2 —实心园柱体,上、下底面平
行(锻件)
•
dB
20 lg
2X 2
10(lg r 空心园锻件) R
• 要求:X≥3N “+”外园径向探测内孔凸柱面 反射,“-”内孔径向探测外园
• 凹柱面反射。实际调节时,将探头置于工 件表面,使底面回波调至基准波高,再提 高按上述相应公式计算得到△dB数,即调 好了检测灵敏度。
• (二)比例作图法的进行步骤
• 1.起始测定点的选择
• 如果探头在工件的某一部位发现了缺陷则 左右移动探头,若缺陷信号均由最高趋向 消失,这时就取缺陷消失的某一点为起始 测定点。如果探测对象为实心轴,当探头 沿整个圆周移动时,缺陷波均不消失,那 就任选一点作起始测定点。
• 2.逐点测量
• 从起始测定点开始,沿着出现缺陷波方向, 以一间隔选择测量点,进行逐点测量。间 隔选取越小,测定点越多,准确性越高。
射波幅均大于某一特当量基准反射波幅 (如均大于Φ2平底孔当量)。
• GB/T6402-91钢锻件超声波检验方法(国 标)定义为:在边长50mm立方体内,有5 个以上缺陷波高,超过产品技术条件规定 值的-6dB。
• 4. 游动回波
• 定义:当探头在工件表面探测移动时,荧 光屏扫描线上缺陷波会随之游动,这说明 缺陷波相对于检测点至缺陷反射面位置 (即深度或声程)在不断变化,这种波称 游动回波,在轴类工件中常见。
超声波探伤检验标准[详]
![超声波探伤检验标准[详]](https://img.taocdn.com/s3/m/73a1143bba1aa8114431d9ae.png)
超声波探伤检验标准超声波探伤检验标准1 目的为了满足公司发展需要,特制定我公司液压支架超声波探伤件检验标准,提供超声波探伤检验依据,制定超声波探伤结果评定标准。
2 主要内容及使用范围规定了检验焊缝及热影响区缺陷,确定缺陷位置、尺寸和缺陷评定的一般方法及探伤结果的分级方法,适用于母材不小于8mm的铁素体类钢全焊透熔化焊对接焊缝脉冲反射法手工超声波探伤检验,不适用于以下情况焊缝的探伤检验:1)铸钢及奥氏体不锈钢焊缝;2)外径小于159mm的钢管对接焊缝;3)内径小于等于200mm的管座角焊缝;4)外径小于250mm和内外径之比小于80%的纵向焊缝。
3 检验等级3.1 检验等级的分级根据质量要求检验等级分为A.B.C三级,检验的完善程度A级最低,B级一般,C级最高,检验工作的难度系数按A.B.C顺序逐级增高。
应按照工件的材质.结构.焊接方法,使用条件及承受载荷的不同,合理地选用检验级别。
检验等级应按产品技术条件和有关规定选择或经合同双方协商选定。
注:A级难度系数为1,B级为5-6,C级为10-12。
3.2 检验等级的检验范围A级检验采用一种角度的探头在焊缝的单面单侧进行检验,只对允许扫查到的焊缝截面进行探测。
一般不要求作横向缺陷的检验。
母材厚度大于50mm时,不得采用A级检验。
B级检验原则上采用一种角度探头在焊缝的单面双侧进行检验,对整个焊缝截面进行探测。
受几何条件的限制,可在焊缝的双面单侧采用两种角度探头进行探伤。
母材厚度大于100mm时,采用双面双侧检验。
条件允许时应作横向缺陷的检验。
C级检验至少要采用两种角度探头在焊缝的单面双侧进行检验。
同时要作两个扫查方向和两种探头角度的横向缺陷检验。
母材厚度大于100mm时,采用双面双侧检验。
其它附加要求是:a.对接焊缝余高要磨平,以便探头在焊缝上作平行扫查;b.焊缝两侧斜探头扫查经过的母材部分要用直探头作检查;c.焊缝母材厚度大于等于100mm,窄间隙焊缝母材厚度大于等于40mm时,一般要增加串列式扫查。
超声波探伤方法和探伤标准
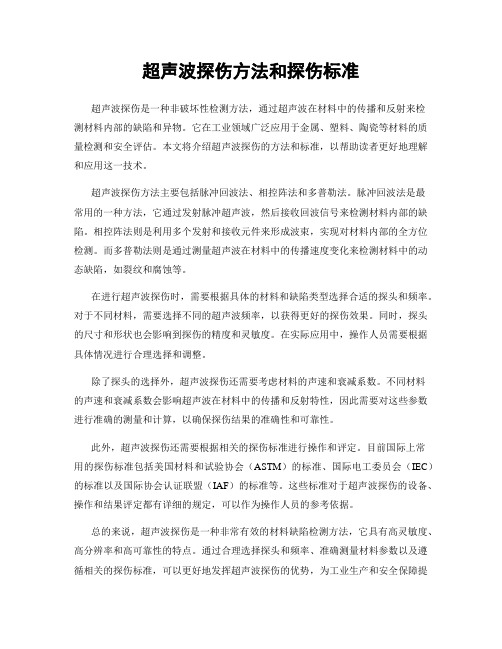
超声波探伤方法和探伤标准超声波探伤是一种非破坏性检测方法,通过超声波在材料中的传播和反射来检测材料内部的缺陷和异物。
它在工业领域广泛应用于金属、塑料、陶瓷等材料的质量检测和安全评估。
本文将介绍超声波探伤的方法和标准,以帮助读者更好地理解和应用这一技术。
超声波探伤方法主要包括脉冲回波法、相控阵法和多普勒法。
脉冲回波法是最常用的一种方法,它通过发射脉冲超声波,然后接收回波信号来检测材料内部的缺陷。
相控阵法则是利用多个发射和接收元件来形成波束,实现对材料内部的全方位检测。
而多普勒法则是通过测量超声波在材料中的传播速度变化来检测材料中的动态缺陷,如裂纹和腐蚀等。
在进行超声波探伤时,需要根据具体的材料和缺陷类型选择合适的探头和频率。
对于不同材料,需要选择不同的超声波频率,以获得更好的探伤效果。
同时,探头的尺寸和形状也会影响到探伤的精度和灵敏度。
在实际应用中,操作人员需要根据具体情况进行合理选择和调整。
除了探头的选择外,超声波探伤还需要考虑材料的声速和衰减系数。
不同材料的声速和衰减系数会影响超声波在材料中的传播和反射特性,因此需要对这些参数进行准确的测量和计算,以确保探伤结果的准确性和可靠性。
此外,超声波探伤还需要根据相关的探伤标准进行操作和评定。
目前国际上常用的探伤标准包括美国材料和试验协会(ASTM)的标准、国际电工委员会(IEC)的标准以及国际协会认证联盟(IAF)的标准等。
这些标准对于超声波探伤的设备、操作和结果评定都有详细的规定,可以作为操作人员的参考依据。
总的来说,超声波探伤是一种非常有效的材料缺陷检测方法,它具有高灵敏度、高分辨率和高可靠性的特点。
通过合理选择探头和频率、准确测量材料参数以及遵循相关的探伤标准,可以更好地发挥超声波探伤的优势,为工业生产和安全保障提供可靠的技术支持。
希望本文所介绍的超声波探伤方法和标准能够对读者有所帮助,促进这一技术的应用和发展。
圆柱螺旋压缩弹簧超声波探伤方法

IC S 21. 160J 26JB/T7367.1-2000圆柱螺旋压缩弹簧超声波探伤方法Non–destructiv e ultraso nic testing method ofco iled helica l comp ressio n springs2000-04-24 发布2000-10-01 实施国家机械工业局发布JB/T7367.1-2000前言本标准是对原ZB J26 002—89《圆柱螺旋压缩弹簧超声波探伤方法》的修订。
修订时,对原标准作了编辑性修改,主要技术内容没有变化。
本标准由全国弹簧标准化技术委员会提出并归口。
本标准起草单位:机械科学研究院、第二汽车制造厂标准件厂。
11 范围本标准规定了圆柱螺旋压缩弹簧(以下简称弹簧)的超声波探伤方法。
本标准适用于钢丝为圆截面、直径为1.0~8.0 mm 、两端磨平的圆柱压缩弹簧在生产过程中进行的超声波探伤。
2 引用标准下列标准所包含的条文,通过在本标准中引用而构成为本标准的条文。
本标准出版时,所示版本均为有效。
所有标准都会被修订,使用本标准的各方应探讨使用下列标准最新版本的可能性。
JB/T 10061—1999 型脉冲反射式超声波探伤仪通用技术条件 JB/T 10062—1999 超声波用探头性能测试方法 3 一般规定3. 1 对于工作在主机关键部位并承受动载荷,须经100%检验的弹簧可进行超声波探伤。
3. 2 探伤人员必须经过有关部门的专门培训考核,并应取得相应的资格等级证书。
3. 3 本方法应能探出弹簧存在的裂纹、夹渣、焊接头等缺陷。
3. 4 采用接触式脉冲反射法进行超声波探伤。
3. 5 超声波探伤仪(以下简称探伤仪)和其它辅助设备应在没有强烈震动、高温、高频电磁场、灰尘大、腐蚀性液体和气体及光线过强的地方工作,探伤仪的荧光屏应避免阳光直射。
4 仪器、探头及耦合剂4. 1 探伤仪4. 1. 1 探伤仪应符合JB/T 10061的规定。
螺栓超声波测轴力原理

螺栓超声波测轴力原理
螺栓超声波测轴力是一种非破坏性检测方法,能够快速准确地测量螺栓的轴力。
该技术基于超声波的传播和反射原理,利用超声波在材料中传播和反射的特性,测量螺栓的轴向变形,从而确定螺栓的轴力状态。
1.超声波传播
超声波是一种机械波,它的波长通常在1毫米到1微米之间。
当超声波从一个介质到另一个介质传播时,会发生反射、折射和透射现象。
使用超声波进行测量时,将超声波发射器放在物体表面,超声波穿过物体并到达接收器。
2.声速与密度的关系
超声波在材料中传播的速度与材料的密度有关。
密度高的材料声速快,反之则慢。
因此,测量螺栓的轴力状态需要知道材料的密度和超声波在材料中的速度。
3.材料的应力状态
当螺栓发生轴向变形时,它的长度变化,超声波在螺栓中的传播时间也会发生变化。
此时,螺栓中的超声波会反射、折射和散射,导致超声波的传播路径发生变化。
因此,测量螺栓的轴力状态需要考虑材料的应力状态。
4.测量信号的捕获和处理
超声波传递回来的信号经过接收器接收并转换成电信号,在信号处理器中进行处理。
信号处理器可以将信号中的波动频率、振幅和时间间隔等信息提取出来,然后计算螺栓的轴力状态。
焊接球和螺栓球节点钢网架焊缝超声波探伤实施细则

焊接球和螺栓球节点钢网架焊缝超声波探伤实施细则一、编制依据(1)《钢结构设计规范》GB 50017(2)《钢结构工程质量施工验收规范》GB 50205(3)《钢焊缝手工超声波探伤方法和探伤结果的分级》GB 11345(4)《钢结构超声波探伤及质量分级法》JG/T 203(5)《超声探伤用探头型号命名方法》ZBY 344(6)《超声探伤用探头性能测试方法》ZBY 231(7)《A型脉冲反射式超声探伤系统工作性能测试方法》ZBY 04001 (8)《超声探伤用1号标准试块技术条件》ZBY 232二、编制目的为正确使用DUT-810型金属超声波探伤仪检测焊接球和螺栓球节点钢网架焊缝的内部缺陷,保证检测精度,制定本细则。
三、适用范围本细则适用于母材厚度3.5-25mm、管径≮48mm普通碳素钢和低合金钢杆件与锥头或封板焊缝、球径≮120mm、管径≮76mm普通碳素钢和低合金钢焊接空心球及球管焊缝以及钢管对接焊缝的超声波探伤及确定缺陷位置、尺寸和缺陷评定。
3.0.2 用DUT-810型金属超声波探伤仪检测焊接球和螺栓球焊缝内部缺陷时,除应遵守本细则外,尚应符合国家现行有关标准的规定。
四、操作人员凡使用DUT-810型金属超声波探伤仪进行检测的人员,均应经专门培训方可进行测试。
五、金属超声波探伤仪、探头及耦合剂1、探伤仪使用A型显示脉冲反射式探伤仪。
其性能指标要求水平线性误差≮1%,垂直性能误差≮5%;衰减器或标准化增益控制器总调节量≮80dB,每档步进量≯2dB,在任意相邻的12dB内误差≯±1dB;当探伤仪与符合规定的斜探头连接后,在CSK-I C试块上得到灵敏度余量应大于评定线灵敏度10dB以上。
性能测试除灵敏度任意理的测试见附灵K外,其余均应按ZBJ 04001规定的方法进行测试。
2探头2.1规格检验壁厚>6mm杆件与锥头或封板焊缝以及钢管对接焊缝,宜选用横波斜探头并以使用频率5MHz、大角度、短前沿斜探头为主,见表1,其中K为折射角正切值,即K=tgβ。
钢结构高强螺栓检测项目

钢结构高强螺栓检测项目钢结构在现代建筑中扮演着重要角色,而螺栓则是连接结构中重要的组成部分。
保证螺栓的质量和安全性对于整个结构的稳定性至关重要。
本文将探讨钢结构高强螺栓检测项目的重要性、方法和应用。
项目背景钢结构在建筑、桥梁和其他工程中广泛使用,而高强螺栓是连接这些结构的关键部件。
为了确保建筑物的安全性和稳定性,必须对这些螺栓进行定期的检测和维护。
在现代建筑工程中,采用高强螺栓连接钢结构已成为主流做法。
检测方法1.视觉检查:通过肉眼观察螺栓表面是否有明显的损坏、生锈或磨损,这是最基本的螺栓检测方法之一。
2.超声波检测:通过超声波技术检测螺栓内部是否存在裂纹或其他缺陷,这种方法非常适用于检测螺栓的内部结构。
3.拉伸测试:通过施加不同的拉力来测试螺栓的强度和承载能力,这是一种常见的螺栓检测方法。
4.磁粉探伤:适用于检测螺栓表面和附近是否存在裂纹或缺陷,通过施加磁场和磁粉检测技术可以有效发现表面裂纹。
应用领域钢结构高强螺栓检测项目广泛应用于以下领域:•建筑工程:对建筑物中连接螺栓进行检测,确保建筑物结构的稳定性和安全性。
•桥梁工程:钢桥梁中使用的高强螺栓需要定期检测,以确保桥梁的承载能力和安全性。
•机械设备:在机械设备的组装过程中,高强螺栓的质量直接影响整个设备的运行效率和安全性。
•石化行业:高强螺栓在石化设备的安装中扮演重要角色,对螺栓进行检测可以确保设备的正常运行。
结论钢结构高强螺栓检测项目对于确保建筑物、桥梁和机械设备的安全性至关重要。
通过采用多种检测方法,可以有效发现螺栓的潜在问题,及时进行维护和更换,从而保障整体结构的稳定性和安全性。
在工程领域中,对钢结构高强螺栓进行定期检测已成为一项必不可少的工作,值得重视和推广。
- 1、下载文档前请自行甄别文档内容的完整性,平台不提供额外的编辑、内容补充、找答案等附加服务。
- 2、"仅部分预览"的文档,不可在线预览部分如存在完整性等问题,可反馈申请退款(可完整预览的文档不适用该条件!)。
- 3、如文档侵犯您的权益,请联系客服反馈,我们会尽快为您处理(人工客服工作时间:9:00-18:30)。
一. 超声波探伤仪检测方法
探头与紧固螺栓耦合的位置及超声束投射方向如附图所示。
螺栓的材料牌号为A3或者20#钢,长度规格包括:80、110、120、130、140、150、160mm等,直径规格包括:20、22、24、28、30、36mm等(随设备型号及吨位不同而有区别)。
[1] 探伤设备:
WT2007型超声探伤仪,2.5P14直探头。
耦合剂为黄油(液压缸下密封盖的紧固螺栓暴露端朝下,需采取仰探方式)和机油(液压缸上密封盖的紧固螺栓暴露端是浸没在缸外冷却油中的,可以直接把探头浸入油中与螺栓端面耦合,但是探头与探头电缆接连处要用胶带纸严密包裹,防止机油渗入影响电接触)。
[2] 探伤灵敏度的设定:
先在荷兰试块或CSK-ⅠA试块100mm高的平面上进行直射纵波1:2定标,使荧光屏水平线的满刻度为200mm。
然后将探头耦合在一支长度为150mm、直径20mm的同材料状态的完好螺栓端面的中心位置上,并稍作移动以找到最大底波,调整仪器灵敏度使该最大回波高度达到50%满屏高,再增益20dB作为探伤起始灵敏度。
(这种设定的指导思想主要有两个方面考虑,其一是由于超声波是在一个近似细长圆柱形的物体中传播,有波制导存在,因此只能是参照超声波在无限大介质中的传播规律,调整到大体相当于可发现75mm处的Φ2平底孔当量作为起始灵敏度;其二,对于这种埋桩螺栓,最常出现疲劳裂纹的位置是在中间光杆部分两端的螺纹接入处或者说是接近密封件的结合界面处,如附图所示。
因此只要能确定螺栓的底波以确认螺栓长度,并有足够的探测灵敏度即可,如果探测灵敏度太高的话则会因为螺纹段的杂乱回波太多太高而影响对裂纹回波的判定。
)
[3] 缺陷判断:
应该说,超声波原位探伤时的一个有利条件是螺栓正处在拉伸应力作用下(加载状态),因此如果存在疲劳裂纹时,裂纹的开隙度要比拆卸后(卸载)的状态大得多,这对超声波检测来说是非常有利的。
在实际探测中,有些螺栓的端面是不平整的,对于存在车削加工时留下的凸出物必须除掉(锉平或铲除)以保障耦合质量,而端面下凹时则可采用黄油填补耦合的方法(注意不要有空气隙存在),此外应该平稳地扶持探头以保持耦合稳定。
将探头平稳地耦合在螺栓端面上,应能正确地找到最大底波并根据该底波前沿在水平刻度线上的位置判定螺栓长度是否正确(因为如果螺栓已经严重断裂时,断裂处的回波将会几乎完全遮蔽底波,则显示出的螺栓长度显然是远远短于规定尺寸的)。
在始波与底波之间因为螺纹部分的沟槽存在而必然有杂草状回波出现,并且随探头在螺栓端面上做小范围移动时会显示幅度变化(与螺纹沟槽的光洁度、螺栓直径及侧壁效应有关)。
在检测中如果发现有明显高出周围杂波(信噪比大于2或者明显高出6dB)的单峰回波且其位置在密封件结合面附近处,则可认为是裂纹波,此时应记录该螺栓在设备上的位置(或者编号)并做好标记,通知设备维修人员将此螺栓更换。
三. 效果
采用原位超声波探伤可以免除整台设备大拆卸造成停产周期太长之弊,一旦探伤发现有某个或某些螺栓存在疲劳裂纹时只需要局部拆卸进行个别更换,不需要象以前那样全部拆卸下来并全部替换,这对于降低设备维修人员的劳动强度、缩短检修周期以及节约材料费用等都是非常有好处的。
自1996年起每年进行定期检测,按照我们目前采用的检测工艺与探伤灵敏度进行过检查的设备至今尚未出现因螺栓断裂而造成的设备故障。
一. 检测方法
探头与紧固螺栓耦合的位置及超声束投射方向如附图所示。
螺栓的材料牌号为A3或者20#钢,长度规格包括:80、110、120、130、140、150、160mm等,直径规格包括:20、22、
24、28、30、36mm等(随设备型号及吨位不同而有区别)。
[1] 探伤设备:
WT2007型超声探伤仪,2.5P14直探头。
耦合剂为黄油(液压缸下密封盖的紧固螺栓暴露端朝下,需采取仰探方式)和机油(液压缸上密封盖的紧固螺栓暴露端是浸没在缸外冷却油中的,可以直接把探头浸入油中与螺栓端面耦合,但是探头与探头电缆接连处要用胶带纸严密包裹,防止机油渗入影响电接触)。
[2] 探伤灵敏度的设定:
先在荷兰试块或CSK-ⅠA试块100mm高的平面上进行直射纵波1:2定标,使荧光屏水平线的满刻度为200mm。
然后将探头耦合在一支长度为150mm、直径20mm的同材料状态的完好螺栓端面的中心位置上,并稍作移动以找到最大底波,调整仪器灵敏度使该最大回波高度达到50%满屏高,再增益20dB作为探伤起始灵敏度。
(这种设定的指导思想主要有两个方面考虑,其一是由于超声波是在一个近似细长圆柱形的物体中传播,有波制导存在,因此只能是参照超声波在无限大介质中的传播规律,调整到大体相当于可发现75mm处的Φ2平底孔当量作为起始灵敏度;其二,对于这种埋桩螺栓,最常出现疲劳裂纹的位置是在中间光杆部分两端的螺纹接入处或者说是接近密封件的结合界面处,如附图所示。
因此只要能确定螺栓的底波以确认螺栓长度,并有足够的探测灵敏度即可,如果探测灵敏度太高的话则会因为螺纹段的杂乱回波太多太高而影响对裂纹回波的判定。
)
[3]缺陷判断:
应该说,超声波原位探伤时的一个有利条件是螺栓正处在拉伸应力作用下(加载状态),因此如果存在疲劳裂纹时,裂纹的开隙度要比拆卸后(卸载)的状态大得多,这对超声波检测来说是非常有利的。
在实际探测中,有些螺栓的端面是不平整的,对于存在车削加工时留下的凸出物必须除掉(锉平或铲除)以保障耦合质量,而端面下凹时则可采用黄油填补耦合的方法(注意不要有空气隙存在),此外应该平稳地扶持探头以保持耦合稳定。
将探头平稳地耦合在螺栓端面上,应能正确地找到最大底波并根据该底波前沿在水平刻度线上的位置判定螺栓长度是否正确(因为如果螺栓已经严重断裂时,断裂处的回波将会几乎完全遮蔽底波,则显示出的螺栓长度显然是远远短于规定尺寸的)。
在始波与底波之间因为螺纹部分的沟槽存在而必然有杂草状回波出现,并且随探头在螺栓端面上做小范围移动时会显示幅度变化(与螺纹沟槽的光洁度、螺栓直径及侧壁效应有关)。
在检测中如果发现有明显高出周围杂波(信噪比大于2或者明显高出6dB)的单峰回波且其位置在密封件结合面附近处,则可认为是裂纹波,此时应记录该螺栓在设备上的位置(或者编号)并做好标记,通知设备维修人员将此螺栓更换。
二. 超声波探伤仪探伤效果
采用原位超声波探伤可以免除整台设备大拆卸造成停产周期太长之弊,一旦探伤发现有某个或某些螺栓存在疲劳裂纹时只需要局部拆卸进行个别更换,不需要象以前那样全部拆卸下来并全部替换,这对于降低设备维修人员的劳动强度、缩短检修周期以及节约材料费用等都是非常有好处的。
自1996年起每年进行定期检测,按照我们目前采用的检测工艺与探伤灵敏度进行过检查的设备至今尚未出现因螺栓断裂而造成的设备故障。
文章链接:中国化工仪器网/Tech_news/Detail/118998.html。