钢板超声波检测工艺
超声波检测工艺规程

超声波检测工艺规程1适用范围1.1 本工艺适用于板厚为6-250mm得板材、碳素钢与低合金钢锻件、母材壁厚8—400mm得全焊透熔化焊对接焊缝及壁厚大于等于4mm,管径为57—1200mm碳素钢与低合金石油天然气长输、集输与其她油气管道环向对接焊缝、钢质储罐对接焊缝得超声波检测等、1。
2 本工艺规定了使用A型脉冲反射式超声波探伤仪进行检测过程中,对受检设备做出准确判定应遵循得一般程序与要求。
1、3 引用标准JB4730/T—2005《承压设备无损检测》SY/T4109-2005《石油天然气钢质管道无损检测》GB11345-89《钢焊缝手工超声波探伤方法与探伤结果得分级》JB/T9214-1999《A型脉冲反射式超声探伤系统测试方法》JB/T10062-1999《超声探伤用探头性能测试方法》GB50128—2005《立式圆筒形钢制焊接储罐施工及验收规范》2对检测人员得要求2、1 从事超声波检测人员必须经过培训,持证上岗。
只有取得质量技术监督部门颁发得超声波检测技术等级证书得人,方可独立从事与该等级相应得超声波检测工作、2、2 检测人员应具有良好得身体素质,其校正视力不得低于 5.0,并每年检查一次。
2、3检测人员应严格执行《检测作业安全防护指导书》与其它安全防护规定,确保安全生产。
3检测程序3、1根据工程特点与本工艺编制具体得《无损检测技术方案》。
3.2受检设备经外观检查合格后,由现场监理或检验员开据《无损检测指令》或《无损检测委托单》到检测中心。
3。
3 检测人员按指令或委托单要求进行检测准备,技术人员根据实际情况编制《探伤工艺卡》、3、4 检测人员按《超声波探伤仪调试作业指导书》等工艺文件进行设备调试。
3.5 外观检查合格后,施加耦合剂,实施检测,做好《超声波检测记录》。
3。
7 根据检测结果与委托单,填写相应得回执单或合格通知单、若有返修,还应出据《返修通知单》,标明返修位置等。
将回执单与返修通知单递交监理或检验员,同时对受检设备进行检验与试验状态标识。
超声波检测工艺规程完整
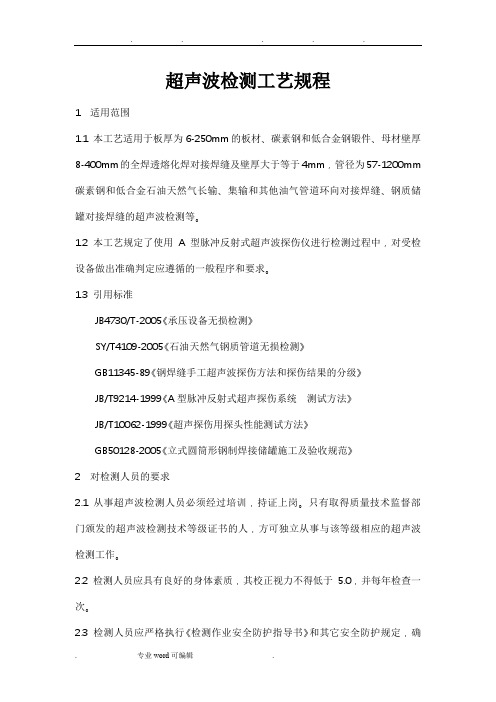
超声波检测工艺规程1适用范围1.1 本工艺适用于板厚为6-250mm的板材、碳素钢和低合金钢锻件、母材壁厚8-400mm的全焊透熔化焊对接焊缝及壁厚大于等于4mm,管径为57-1200mm 碳素钢和低合金石油天然气长输、集输和其他油气管道环向对接焊缝、钢质储罐对接焊缝的超声波检测等。
1.2 本工艺规定了使用A型脉冲反射式超声波探伤仪进行检测过程中,对受检设备做出准确判定应遵循的一般程序和要求。
1.3 引用标准JB4730/T-2005《承压设备无损检测》SY/T4109-2005《石油天然气钢质管道无损检测》GB11345-89《钢焊缝手工超声波探伤方法和探伤结果的分级》JB/T9214-1999《A型脉冲反射式超声探伤系统测试方法》JB/T10062-1999《超声探伤用探头性能测试方法》GB50128-2005《立式圆筒形钢制焊接储罐施工及验收规范》2对检测人员的要求2.1 从事超声波检测人员必须经过培训,持证上岗。
只有取得质量技术监督部门颁发的超声波检测技术等级证书的人,方可独立从事与该等级相应的超声波检测工作。
2.2 检测人员应具有良好的身体素质,其校正视力不得低于5.0,并每年检查一次。
2.3检测人员应严格执行《检测作业安全防护指导书》和其它安全防护规定,确保安全生产。
3检测程序3.1 根据工程特点和本工艺编制具体的《无损检测技术方案》。
3.2 受检设备经外观检查合格后,由现场监理或检验员开据《无损检测指令》或《无损检测委托单》到检测中心。
3.3 检测人员按指令或委托单要求进行检测准备,技术人员根据实际情况编制《探伤工艺卡》。
3.4 检测人员按《超声波探伤仪调试作业指导书》等工艺文件进行设备调试。
3.5 外观检查合格后,施加耦合剂,实施检测,做好《超声波检测记录》。
3.7 根据检测结果和委托单,填写相应的回执单或合格通知单。
若有返修,还应出据《返修通知单》,标明返修位置等。
将回执单和返修通知单递交监理或检验员,同时对受检设备进行检验和试验状态标识。
钢板超声波检测
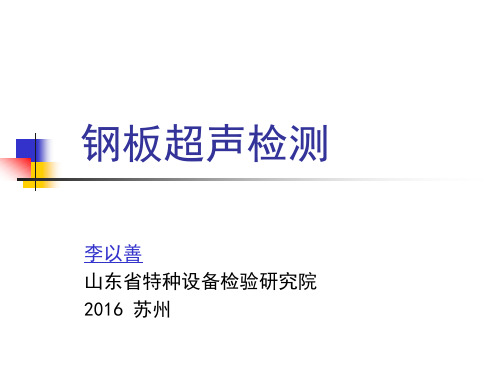
四、钢板横波检测
2、对比试块用钢板应与被检钢板厚度相同,声学特性相同 或相似。对比试块上的人工缺陷反射体为V形槽,角度为 60°,槽深为板厚的3%,槽的长度至少为25mm。对比试块 的尺寸、V形槽位置等见附图。对于厚度超过50mm的钢板, 要在钢板的底面加工第二个相同尺寸的校准槽。
四、钢板横波检测
二、钢板超声检测技术
3、试块:
பைடு நூலகம்
二、钢板超声检测技术
二、钢板超声检测技术
4、耦合剂:
二、钢板超声检测技术
5、检测灵敏度
二、钢板超声检测技术
6、扫查方式
二、钢板超声检测技术
7、检测灵敏度
二、钢板超声检测技术
8、叠加效应
出现叠加效应,一般应根据F1来评价缺陷。
二、钢板超声检测技术
钢板内部有气体,在轧制后不能焊合而造成的气孔。 厚钢板有时由于氢的析出聚集还会产生白点。 氧化铁皮压入是由于原料表面有氧化铁皮或在轧制过程中产生再生氧化铁皮未除尽,
在轧制完成后,钢板表面粘附一层灰黑色或红棕色氧化铁皮,一般呈块状或条状。 折叠的产生主要是操作不当,而使轧件刮框,或碰撞异物造成局部卷凸,或轧辊掉皮
六、钢板自动超声检测
6、缺陷的评判 对于有自动判定缺陷大小的超声波自动
探伤设备,缺陷的边界或指示长度由设 备自动计算。对于无自动判定缺陷大小 的超声波自动探伤设备,当发现可疑缺 陷后,缺陷的定位、定量由人工方法进 行。
缺陷的评判与接触式钢板探伤方法一致 。
七、钢板超声检测应用实例
1、用水浸法检测厚度为40mm的钢板,为使钢板的第四次底波与水界面 的第二次回波重合,水层的厚度应为(水中纵波波速为1480m/s,钢中 纵波波速为5900m/s):
钢板超声波检测标准

钢板超声波检测标准一、超声波探伤方法1.1 脉冲反射法脉冲反射法是一种常用的超声波探伤方法,适用于检测内部和表面缺陷。
通过在钢板上发射超声波,然后接收回波信号,分析信号的反射时间和波形变化,以确定钢板内部是否存在缺陷。
1.2 衍射时差法衍射时差法是通过测量超声波在钢板中传播的时间,结合已知的声速和钢板的厚度,计算出超声波的衍射时间,从而确定钢板内部是否存在缺陷。
二、探伤设备与器材2.1 超声波探伤仪超声波探伤仪应具有高灵敏度、高分辨率和高可靠性,能够准确测量超声波的传播时间和波形变化。
2.2 探头探头是超声波探伤的关键部件,应具有高灵敏度、高分辨率和高可靠性,能够准确测量超声波的传播时间和波形变化。
根据不同的探伤方法,需要选择不同类型的探头。
2.3 耦合剂耦合剂用于将探头与钢板表面紧密接触,以减少声波的反射和散射,提高探伤的准确性和可靠性。
三、探伤条件与环境3.1 温度与湿度超声波探伤应在适当的温度和湿度条件下进行,以避免环境因素对探伤结果产生影响。
3.2 清洁度超声波探伤前应对钢板表面进行清洁处理,以减少杂质的干扰和影响。
四、被检对象要求与制备4.1 钢板规格与材质超声波探伤适用于不同规格和材质的钢板,应根据具体的检测需求选择合适的钢板。
4.2 表面处理对于不同表面处理的钢板,如涂层、镀层等,应进行相应的处理,以避免对探头和耦合剂产生影响。
五、探伤操作要求与步骤5.1 校准仪器在进行超声波探伤前,应对探伤仪和探头进行校准,以确保测量结果的准确性和可靠性。
5.2 选择探头和耦合剂根据具体的检测需求选择合适的探头和耦合剂。
5.3 耦合与扫描将探头与钢板表面紧密耦合,并进行扫描操作。
根据信号的反射时间和波形变化确定是否存在缺陷。
对于不同的缺陷类型和位置,应进行相应的记录和分析。
钢板超声波检测方法

钢板超声波检测方法
超声波探头是用于发射和接收超声波信号的装置,通常由压电晶体或磁致伸缩材料制成。
超声波发射器通过电信号激励超声波探头发射超声波信号,而超声波接收器则接收被钢板内部缺陷反射的超声波信号。
超声波检测有两种主要的检测方法:传统的脉冲回波法和全脉冲法。
脉冲回波法是最常用的超声波检测方法之一、它的基本原理是通过将超声波信号发送到钢板中,当超声波信号遇到不同介质的边界时,一部分能量会被反射回来作为回波信号。
通过测量回波信号的时延和幅值,可以确定钢板中的缺陷位置、尺寸和性质。
全脉冲法是一种更高级的超声波检测方法。
它通过发送一串高能量的宽带脉冲信号,可以获得更清晰和详细的超声波回波信号,从而更准确地分析钢板的缺陷。
全脉冲法通过改变脉冲信号的频率和幅度,可以实现对不同深度和尺寸的缺陷进行检测。
超声波检测方法还可以通过不同的传感器排布方式来实现不同的检测需求。
常见的传感器排布方式有直线排布、阵列排布和旋转探头排布等。
直线排布适用于直线或近似直线的缺陷检测;阵列排布则可以实现多个传感器同时工作,提高检测效率;旋转探头排布可以实现对钢板全面无死角的检测。
除了以上的方法,超声波检测还可以结合其他的检测技术,如激光光谱分析、红外热像仪、磁粉探伤等,以提高检测的准确性和可靠性。
总的来说,钢板超声波检测方法是一种非破坏性、高效、高精度的检测方法,在钢板行业中具有广泛的应用前景。
厚钢板超声波自动探伤检验方法国家标准

《厚钢板超声波自动探伤检验方法》国家标准编制说明一、工作简况1 任务来源2007年10月,全国无损检测标准化技术委员会向重庆钢铁集团有限公司下发了《关于起草厚钢板超声波自动探伤检验方法国家标准任务书》,2008年底该标准转由全国钢标准化技术委员会归口。
2 编制单位主编制单位:重庆钢铁股份有限公司参加编制单位:冶金工业信息标准研究院等3 工作过程3.1 主要过程简介从上世纪80年代到现在,国内已有舞阳钢铁公司、首钢公司、宝钢公司、重钢公司等多家钢铁企业投建了钢板超声波自动探伤设备,既有国内自行研制的,也有从国外引进的,各探伤设备的技术条件各不相同,技术参数参差不齐,且对缺陷的判定标准也各不相同,为规范钢板超声波自动探伤的技术条款,确保所探钢板的实物质量,并结合国内目前自动探伤的现状和发展趋势,由全国无损检测标准化技术委员会提出,重庆钢铁集团有限公司和重庆市技术质量监督局承接起草。
重钢于2008年3月成立了标准编制小组,开始了标准的起草编制工作,标准编制组首先征求了一些单位的意见,查阅标准资料,收集了ISO、EN等国际国外主要标准。
编制组经过收集和对比国内外相关标准,了解国内超声自动探伤设备使用现状和发展趋势,并经过系列试验,提出了标准征求意见稿征求意见,编制组根据前期征求和反馈的意见,于2009年6月完成了本讨论稿。
3.2 收集的国内外主要标准包括ASTM A578 特殊设备用的普通钢板和包覆钢板的直波束超声探伤检验的标准规范ASTMA435 钢板的直射束纵向超声波检验EN 10160 厚度大于或等于6毫米的钢板制品的超声波检验(平面反射法)GB/T 2970 厚钢板超声波检验方法JB/T4730 承压设备无损检测方法3.3 对相关的国内标准进行对比分析,本次标准修订主要参照GB/T2970和JB/T4730等标准。
二、标准编制原则本标准的制订遵循以下原则:1、标准的主要内容以GB/T 2970—2004《厚钢板超声波检验方法》标准为基础,参照国外先进标准ASTM A578、ASTMA435和EN 10160。
钢板超声波检测作业指导书
检
尺寸
测 距 离 - 波 幅 曲 线 1、 将探头置于试块有槽的一面,使主声束对准槽的宽边,找出第一个全跨距反射
的确定
的最大波幅,调整仪器,使该反射波的最大波幅为满刻度的 80%,在显示屏上
记录下该信号的位置。
2、 不改变仪器的调整状态,移动探头,得到第二个全跨距信号,并找出信号最大
反射波幅,在显示屏上记录下该信号的位置。
3、 板材探头在钢板边缘或剖口预定线两侧检测区域 1 、、最大单个缺陷指示长度 Lmax>30mm 2 、最大单个缺陷指示面积 S>100mm² 3 、在任意 1m 检测长度内,单个缺陷指示长度为 15mm<L≤30mm,评定范围
内缺陷个数>3 个。
编制(资格): X X X
(UT-Ⅱ) 2016 年 12 月 21 日
合格级别 II 级
耦合剂 化学浆糊
扫描调节
声程 1:2
检测时机
下料前
纵 探头型
2.5P30Z
试块型号 2#对比试块
波号
订正:
/
订正:3#对比试块
检 基准灵 测 敏度调
深度 85mm 的Φ5 平底孔反射波调至 80%
节
订正:在 3#对比试块上绘制Φ5 平底孔的距离-波幅曲线,并以此曲线作为基准灵敏度
扫查方 式1
3、 在显示屏上将上述内容所确定的点连成一直线,此线即为距离-波幅曲线。
S 1、 白点、裂纹等危害性缺陷, 不允许缺陷 2、 板材中部检测区域
①、最大单个缺陷指示面积 S>100mm² ②、在任意 1m×1m 检测面积内,单个缺陷指示面积为 50mm²<S≤100mm², 评定范围内缺陷个数>10 个
75 75
6000
1 板材超声检测
1 板材超声检测板材主要用于制造压力容器的壳体,一般厚度为6~250mm[3 ] ,大多数压力容器用的钢板厚度为8~40mm.钢板制造厂多采用超声局部水浸法检测,压力容器制造厂多采用接触法复验.在用压力容器一般不进行钢板超声检测,当发现测厚异常以及鼓包等特殊情况时再做该项工作.压力容器用钢板的检验与验收采用JB 4730 标准8. 1 款压力容器钢板超声检测及附录H 压力容器钢板横波检测,当使用双晶直探头时,应附合JB4730 标准中附录G双晶直探头性能要求.特别要注意所使用探头的距离2波幅曲线.1. 1 厚度20mm钢板的超声检测应使用 2. 5MHz 单晶直探头(圆晶片直径为60mm 时,也可取钢板无缺陷的完好部位的第一次反射底波来校准灵敏度(JB 4730 修订版要求板厚大于等于探头的三倍近场区) .6~250mm厚钢板超声检测的扫查方式,缺陷判别和质量等级的评定见JB 4730 标准[3 ] .我国钢板超声检测标准与德国和日本是一致的.1. 4 压力容器钢板横波检测压力容器钢板一般不进行横波检测,除非用户有特殊需要时,JB 4730 —1994 附录H 明确规定该方法用来检测钢板中非夹层性缺陷,并作为直探头超声检测的补充.1. 5 复合板超声检测总厚度> 8mm 的压力容器用轧制复合钢板的超声检测方法和缺陷等级评定在JB 4730 标准中有规定.而爆炸复合钢板的超声检测在JB 4733 —1996《压力容器用爆炸不锈钢复合钢板》附录A爆炸不锈钢复合钢板超声波检测方法中有规定.它是利用复合钢板本身调节灵敏度,将探头置于复合钢板完全结合部位,调节第一次底波高度为荧光屏满幅度的80 %.当第一次底波高度不大于5 %荧光屏满幅度的部位为未结合部位,将探头由未结合部位向四周移动,直至底波高度升为满幅度的40 % ,以探头中心确定未结合区界限.其结合状态中B1 和B2级分别与日本J IS G3601 标准中的B1F 和B2S 相近,B1 级爆炸复合钢板要求结合率为100 % ,严于日本标准的规定,以满足临氢压力容器的使用要求.1. 6 压力容器用铝及铝合金和钛及钛合金板材的超声检测对于铝及铝合金和钛及钛合金板材的超声检测灵敏度和质量等级评定国内是这样规定的:(1) 将探头置于待检板材完好部位,调节第一次底波高度为荧光屏满幅度的80 % ,以此作为基准灵敏度.检测方法同钢板.(2) 板材质量仍是根据单个缺陷指示长度,单个缺陷指示面积以及板材中是否有裂纹等危害性缺陷存在来评定.2 钢管超声检测钢管超声检测一般采用横波斜射法,它适用于壁厚t 与外径D 之比≤0. 2 的管作周向扫查和任何t/ D 比值的管作轴向扫查.当t/ D > 0. 2 时,可采用纵波斜射法或变型横波斜射法作周向扫查.虽然超声可用于检测碳钢,低合金钢和不锈钢管,但它不适用于分层缺陷的检测,采用尖角槽作对比试块的人工缺陷,若缺陷回波比尖角槽回波高时,则判为不合格.钢管的超声检测与日本工业标准是一致的.3 锻件超声检测3. 1 压力容器钢锻件超声检测压力容器用碳素钢和低合金钢锻件的超声检测和缺陷等级评定见JB 4730 标准[3 ]8. 2 款压力容器锻件超声检测,而横波检测应按附录I 压力容器锻件横波检测的要求进行.使用纵波直探头时应采用CS1 和CS2 试块,使用双晶直探头时要用专用试块.超声检测原则上应安排在热处理后,槽,孔,台阶加工前进行,不得已时只好在热处理前进行,但在热处理后仍应对锻件进行尽可能全面的检测.另外当材质的衰减系数> 4dB/ m时,要考虑修正缺陷当量[4 ] .如材质衰减对检测结果影响较大,应重新进行热处理.根据单个缺陷大小,由缺陷引起底波降低量及密集区缺陷占检测总面积的百分比来进行缺陷等级评定.锻件超声检测内容与美国,日本标准一致.3. 2 压力容器奥氏体钢锻件超声检测奥氏体钢晶粒粗大,衰减大,因此宜用低频探头,一般用直探头检测.对筒形锻件必要时还应进行横波检测.实际检测时用纵波斜探头效果较好.对小锻件应采用平底孔试块校正灵敏度,当被检锻件厚度> 600mm 时,在锻件无缺陷部位将底波高度调至满刻度的80 % ,以此作为基准.记录三种情况,即①底波高度降为25 %以下的部位. ②游动信号.③大于基准线50 %的信号.直探头检测的等级分为五级,作者认为压力容器行业中分为三级就足够了;斜探头检测的等级分为两级.压力容器奥氏体钢锻件超声检测的内容与美国是一致的.4 高压螺栓的超声检测直径>M50 的高压螺栓件超声检测和缺陷等级评定可按JB 4730 标准[3 ]8. 5 款高压螺栓件的超声检测,直径M32 的高压螺栓件可参考上述标准内容.压力容器螺栓检测最好用小角度纵波直探头或5N14 窄脉冲探头,有利于发现螺纹根部细小裂纹.对于在役高压螺栓,由于清洗困难,磁粉检测效果不是很好,常采用超声检测.5 焊缝的超声检测焊缝质量直接影响产品的使用寿命及安全性,超声波探伤是保证焊缝质量的重要检测手段之一. 焊缝内部质量一般用射线来检测.但对于厚壁容器或焊缝中的裂纹,未熔合等危险性缺陷,超声检测方法优于射线检测.JB 4730 修订版对母材厚度为8~300mm的全焊透熔化焊对接焊缝的超声检测进行了明确规定.并指出应检测到整条焊缝,熔合线和热影响区.而过去人们认为,对焊缝的超声检测只是检测焊缝.5. 1 平板对接焊缝超声检测8~46mm 厚的平板对接焊缝采用二次波探伤,厚度> 46mm 的平板对接焊缝采用一次波探伤. 常用的耦合剂有机油,化学浆糊和水,有时也用甘油和润滑脂.常用探头频率为2. 5~5MHz.探头K值的选择要考虑三点[5 ] ,即①使声束能扫查到整个焊缝截面.②使声束中心线尽量与主要危险性缺陷垂直.③保证有足够的探伤灵敏度.这里应强调,对于薄板焊缝要考虑探头的前沿.前沿太大,容易造成缺陷漏检.压力容器超声检测一般不用声程法调节扫描速度.薄板焊缝的检测常用水平法调节,中厚板焊缝的检测常用深度法调节.距离2波幅曲线可制作在坐标纸上,也可制作在仪器面板上,需注意检测时要考虑声能损失差.检测时常用锯齿形扫查,需注意①扫查时探头要作10°~15°转动. ②扫查范围要符合要求.③每次前进齿距 d 不超过探头晶片直径.当锯齿形扫查发现缺陷时,可用左右扫查,前后扫查,转角扫查及环绕扫查来对缺陷进行定位,定量和缺陷性质的估判.有些材料的焊缝中容易产生横向裂纹, 这时常采用以下三种方式探测[6 ] :(1) 在已磨平的焊缝及热影响区表面以一种(或两种) K 值探头用一次波在焊缝上作正,反两个方向的全面扫查.(2) 用一种(或两种) K 值探头的一次波在焊缝两面双侧作斜平行探测.声束轴线与焊缝中心线夹角呈10°~20°.(3) 对于电渣焊中的八字形横裂纹,可用K1 探头在45°方向以一次波在焊缝两面双侧进行探测. 对于厚壁焊缝,为检测与探伤面几乎垂直的内部未熔合,有时可采用串列式扫查.但要注意,串列式扫查会有探测不到的区域(俗称盲区) ,必须用单斜探头补充探测.不允许存在反射波幅位于判废线和Ⅲ区的缺陷以及裂纹等危害性缺陷.最大反射波幅位于Ⅱ区的缺陷,按其长度评级[3 ] .JB 4730 修订版还规定了A ,B ,C 三个检测级别.一般压力容器适用于B 级,重要压力容器适用于C 级,支承件和结构件适用于A 级.5. 2 管座角焊缝的超声检测管座角焊缝的超声检测以直探头为主,对直探头扫查不到的区域,可采用斜探头检测.直探头探伤时,平底孔距离2波幅曲线可在CS1或CS2 试块上测试.其评定线灵敏度为<2mm 平底孔,定量线为<3mm 平底孔,判废线为<6mm 平底孔.而采用斜探头时,距离2波幅曲线的测试同平板对接焊缝.缺陷等级的评定与平板对接焊缝超声检测中缺陷的评定是一致的.5. 3 T形接头焊缝的超声检测6~50mm 厚压力容器全焊透T 形接头焊缝的超声检测要依据不同的焊缝结构形式,选择一种或几种方式组合实施检测.常用的探头是直探头(或双晶直探头) 和斜探头.直探头距离2波幅曲线的灵敏度是,评定线为<2mm平底孔,定量线为<3mm 平底孔,判废线为<4mm 平底孔.不允许存在反射波幅位于Ⅲ区的缺陷和裂纹等危害性缺陷.Ⅱ区内缺陷的质量等级评定见表1. 5. 4 缺陷自身高度的超声测试表1 Ⅱ区缺陷的质量等级评定( T形接头) mm为评价设备的安全性和估计使用寿命,要求知道缺陷的真实尺寸,特别是测定缺陷的自身高度.目前我国主要用端点衍射回波法,端部最大回波法和6dB 法.5. 4. 1 端点衍射回波法[7 ]由于该方法是根据缺陷端点反射波来辨认衍射回波,因此称为端点衍射回波法,缺陷自身高度根据缺陷两端点衍射回波间的延迟时间差值来确定.尽量采用直射法(一次波法) ,原则上应用 2. 5~5MHz K1 探头.测定前要精确校正时基线,特别要考虑测定孔的水平距离和深度距离的修正值.对于表面开口缺陷自身高度的超声检测,要区分探测面与缺陷在同一平面和不在同一平面两种情况.对于焊缝内部缺陷自身高度的超声检测,要区分是垂直于探测面的缺陷,还是倾斜的缺陷.当用端点衍射回波法无法识别缺陷时,可选用双斜探头V 型串接法进行测高.5. 4. 2 端部最大回波法尽量采用直射法(一次波法) ,原则上应用2. 5~5MHz K1 探头,最好是聚焦斜探头,可以对表面开口缺陷和内部缺陷进行自身高度的测试.气孔和夹渣情况则比较复杂,如确有需要,应增加X射线复检.成群的横向缺陷会造成超声束散射,造成检测困难,这时可对妨碍检测的焊缝表面进行打磨,必要时再增加射线检测.5. 4. 3 6dB 法尽量采用直射法(一次波法) ,原则上应用2. 5~5MHz K1 探头.最好是聚焦斜探头.若缺陷回波只有单峰,且变化比较明显,则以最大回波处作为起始点;若回波高度变化很小,可将回波迅速降落前的半波高度值作为6dB 法测高的起始点;若缺陷端部回波比较明显,则以端部最大回波处作为6dB法的起始点.(1) 内部缺陷自身高度值H 用下式计算H = ( W2 - W1) cosθ (1)式中W1 , W2 ———缺陷上下边缘至入射点的声程θ———折射角(2) 表面开口缺陷自身高度值H′的测试分两种情况,即直射法检测和一次反射回波法检测,分别计算如下H′= W2cosθ (2)H′= t - W1cosθ (3)式中t ———壁厚缺陷自身高度的超声检测方法与欧洲标准和日本有关资料是一致的.5. 5 缺陷性质估判依据缺陷性质估判还没有非常成熟的方法,它与检测人员的经验密切相关.焊缝中缺陷分为点状,线性,体积状和平面状缺陷.对点状缺陷,可认为是点状夹渣或气孔,一般不再进一步定性.对于线性,体积状和平面状缺陷性质的估判,主要依据①材料(包括母材与焊材) . ②工件(包括结构型式与坡口形式) . ③焊接工艺和焊接方法.④缺陷位置(包括水平位置和深度位置) .⑤缺陷的大小和取向.⑥缺陷最大反射回波高度.⑦缺陷定向反射特性.⑧缺陷回波静态波形.⑨缺陷回波动态波形.5. 6 奥氏体不锈钢焊缝的超声检测超声检测方法可用于厚度为10~50mm 奥氏体不锈钢对接焊缝,不适用于直径≤159mm 的管子对接环焊缝及外径≤500mm筒体纵焊缝.与德国一样,我国也推荐采用纵波斜探头(高阻尼窄脉冲) .在满足探测条件情况下,也可选用双晶纵波斜探头或聚焦纵波斜探头.使用专用的对比试块制作距离2波幅曲线,其灵敏度如表2 所示.裂纹,未熔合和未焊透等危害性缺陷评为Ⅲ级,对于Ⅱ区缺陷按表3 评级.5. 7 铝及铝合金焊缝的超声检测表2 距离2波幅曲线灵敏度表3 奥氏体不锈钢焊缝Ⅱ区缺陷的等级评定厚度≥8mm 的铝及铝合金焊缝可用超声法检测.参照欧洲(英国) 有关标准,试块中的反射孔是<2mm横通孔(JB 4730[3 ]为<5mm 横通孔) ,试块的测定适用范围为8~80mm.其距离2波幅曲线灵敏度如表2 所示.不允许存在反射波幅位于或超过判废线的缺陷以及裂纹等危害性缺陷, Ⅱ区的缺陷评级见表4. 表4 铝及铝合金焊缝Ⅱ区缺陷的等级评定5. 8 钛制压力容器对接焊缝超声检测≥8~80mm 厚的钛容器可用超声法检测,该方法不适用于外径< 159mm 的钛管对接焊缝,内径≤200mm的管座角焊缝以及外径< 250mm 或内外径之比25mm 的未结合部位.欧洲标准与上述(4) 相比要严一些,它不允许存在。
板材超声波探伤
△ 利 用 F1 评 价 缺 陷 。 出 现 叠 加 效 应 时 , 当 板 厚 较 薄 时 可 用 F2 评 价 缺 陷 , 其 目 的 是 减 少 近 场 区 影 响 。 实 际 上 , 应 根 据 晶 片 直 径 的 尺 寸 大 小 及 F1 不 清 晰 时 , 可 用 F2 来 评 价 缺 陷 , 用 F2 和 B2 评 价 时 , 基 准 灵 敏 度 以 第二次反射波校正。 如 采 用 直 径 为 Ф 14 m m ~ 20 m m 的 直 探 头 探 伤 钢 板 , 一 般 当 板 厚 δ < 20 m m 时 , 可 采 用 F 2 评 价 缺 陷 。 1.3 探 头 与 扫 查 方 式 1. 3.1 频 率 2.5 ~ 5MHz ,40mm 以 下 钢 板 检 测 频 率 为 5MHz ,40mm 以 上 钢 板 检 测 频 率 为 2.5MHz 晶 片 直 径 : Ф14 ~ Ф25mm 探头形式: 单晶直探头 钢板检测 联合双晶直探头 适用于板厚 δ 较薄的钢板检测,因盲区小, 适 用 于 板 厚 δ 较 大 的 钢 板 检 测 ,用 于 20mm 以 上
1.7
钢板横波检验按附录 B 规定要求 非夹层性缺陷
适用范围 探头
K1 2MHz~5MHz 25mm 长 V 形 槽 深 为 板 厚 3 % V 形槽的距离-波幅曲线, 按 不 同 板 厚 根 据 B.4 规 定 调 节
人工缺陷 灵敏度
验 收 标 准 按 B.6 规 定 : 等 于 或 超 过 距 离 - 波 幅 曲 线 信 号 不 合 格 , 发现分层类缺陷按纵波检测规定处理。
8 / 26
1.6 质 量 等 级 判 定 : 按 JB/T4730-2005 标 准 4.1.7 条 规 定 评 定 。 单 个 缺 陷 指 示 长 度 按 4.1.7.1 规 定 , 单 个 缺 陷 指 市 面 积 按 4.1.7.2 规 定 。 JB/T4730-2005 标 准 标 准 中 表 3 钢 板 质 量 分 级 表 中 数 据 适 用 于 非 白点、裂纹等危险缺陷,即非危险缺陷。白点、裂纹等危险缺 陷,都判为 V 级。
超声波检测工艺规程(完整资料).doc
【最新整理,下载后即可编辑】超声波检测工艺规程1适用范围1.1 本工艺适用于板厚为6-250mm的板材、碳素钢和低合金钢锻件、母材壁厚8-400mm的全焊透熔化焊对接焊缝及壁厚大于等于4mm,管径为57-1200mm碳素钢和低合金石油天然气长输、集输和其他油气管道环向对接焊缝、钢质储罐对接焊缝的超声波检测等。
1.2 本工艺规定了使用A型脉冲反射式超声波探伤仪进行检测过程中,对受检设备做出准确判定应遵循的一般程序和要求。
1.3 引用标准JB4730/T-2005《承压设备无损检测》SY/T4109-2005《石油天然气钢质管道无损检测》GB11345-89《钢焊缝手工超声波探伤方法和探伤结果的分级》JB/T9214-1999《A型脉冲反射式超声探伤系统测试方法》JB/T10062-1999《超声探伤用探头性能测试方法》GB50128-2005《立式圆筒形钢制焊接储罐施工及验收规范》2对检测人员的要求2.1 从事超声波检测人员必须经过培训,持证上岗。
只有取得质量技术监督部门颁发的超声波检测技术等级证书的人,方可独立从事与该等级相应的超声波检测工作。
2.2 检测人员应具有良好的身体素质,其校正视力不得低于5.0,并每年检查一次。
2.3检测人员应严格执行《检测作业安全防护指导书》和其它安全防护规定,确保安全生产。
3检测程序3.1 根据工程特点和本工艺编制具体的《无损检测技术方案》。
3.2 受检设备经外观检查合格后,由现场监理或检验员开据《无损检测指令》或《无损检测委托单》到检测中心。
3.3 检测人员按指令或委托单要求进行检测准备,技术人员根据实际情况编制《探伤工艺卡》。
3.4 检测人员按《超声波探伤仪调试作业指导书》等工艺文件进行设备调试。
3.5 外观检查合格后,施加耦合剂,实施检测,做好《超声波检测记录》。
3.7 根据检测结果和委托单,填写相应的回执单或合格通知单。
若有返修,还应出据《返修通知单》,标明返修位置等。
- 1、下载文档前请自行甄别文档内容的完整性,平台不提供额外的编辑、内容补充、找答案等附加服务。
- 2、"仅部分预览"的文档,不可在线预览部分如存在完整性等问题,可反馈申请退款(可完整预览的文档不适用该条件!)。
- 3、如文档侵犯您的权益,请联系客服反馈,我们会尽快为您处理(人工客服工作时间:9:00-18:30)。
敦邦钢结构工程钢板超声波检测工艺
编制人:
审核人:
审批人:
2011年5月
敦邦钢结构工程
目录
1. 总则 (1)
2. 检测人员 (2)
3. 探头、仪器。
试块与耦合剂 (2)
4. 检测 (4)
5. 缺陷的测定与评定 (5)
6. 钢板的质量分级 (6)
7. 检测报告 (6)
8. 钢板超声波检测工艺卡 (6)
1.总则:
1.1本方案适用于敦邦钢结构工程工厂原材料钢板的超声波检验
1.2编制本检测方案的依据为:
1.2.1《钢结构工程施工质量验收规》GB50205-2001;
1.2.2 《厚钢板超声波检验方法》GB/T2970-2004
1.3本方案需要更改或对其容有疑问,以及发生记载外的重要事项时,要同设计单位协商,经同意后进行检查,如有发生上述事项,做成书面文件发布给相关人员。
2.检验人员
2.1从事原材料钢板的超声检测人员,必须经过技术培训,并取得认可的与其
工作相对应的书;由Ⅰ级及II级以上人员担任。
签发报告由II级及II级以上
人员担任。
各技术资格等级人员只能从事与该等级相应的超声检测工作并负相应的
技术责任,Ⅰ级人员必须在II级或II级以上人员的指导下进行检测;
2.2从事超声波检测人员校正视力不得低于1.0并且必须每年检查一次。
3.仪器、探头、试块与耦合剂
3.1探伤仪
3.1.1超声检测设备均应具有产品质量合格证或合格的证明文件,并按规要求予以鉴
定;
3.1.2采用数字型可记录的A型脉冲反射式探伤仪;
3.1.3在荧光屏满刻度的80%围呈线性显示,衰减器精度为任意相邻12dB以,最大
累计误差不超过1dB。
水平线性误差不大于1%,垂直线性误差不大于5%,其余
指标应符合GB/T 8651 JB/T 10061的规定。
3.2探头
3.2.1 直探头选用按下表;
3.2.2双晶片直探头性能应符合GB/T 2970附录A的要求。
3.2.3探头直径应在10-30mm之间
3.3 试块
3.3.1标准试块:下面图样试块或CBⅠ、CBⅡ试块;
3.3.2试块图样:
3.4 耦合剂
一般情况使用水作为耦合剂。
4. 检测
4.1 检测时间
原则上在钢板进厂时进行,也可在下料前进行。
4.2 检测面
可以从钢板任一轧制面进行检测,被检钢板的表面应平整,应清除影响检测的氧化皮、锈蚀、油污、及其它外部杂质。
4.3 检测灵敏度
4.3.1 检测灵敏度应计入试样与被检钢板之间的表面耦合声能损失(dB)。
4.3.2用双晶片直探头检测时,用图1试样或同厚度钢板上的第一次底波高度调整到满
刻度的50%,再提高10dB作为检测灵敏度。
4.3.3用单晶片直探头检测时,用图2试样平底孔的第一次反射波高度调整到满刻度的
50%来校准。
4.3.4板厚大于探头3倍近场区时,检测灵敏度用计算法、通过第一次底面回波高度来
确定。
4.4探头扫查形式
4.4.1探头沿垂直于钢板压延方向、间距不大于100mm的平行线进行扫查;在钢板周
围50mm(板厚大于100mm时,取板厚的一半)及坡口预定线(合同或技术协议中
确定具体位置)两侧各25mm沿周边进行扫查。
4.4.2用双晶片探头时,探头隔声层应与压延方向平行(垂直于压延方向扫查)。
4.4.3根据合同、技术协议书或图样的要求,也可采用其他形式的扫查。
探头扫查示意图
4.5检测速度
检测速度应不大于200mm/s。
5. 缺陷的测定与评定
5.1在检测过程中,发现下列情况应记录
5.1.1缺陷第一次反射波(F1)波高大于或等于满刻度的50%。
5.1.2当底面第一次反射波(B1)波高未达到满刻度时,缺陷第一次反射波(F1)波与
第一次反射波(B1)波高之比大于或等于满刻度的50%。
5.1.3当底面(或板端部)第一次反射波(B1)波高低于满刻度的50%。
5.2 缺陷的边界或指示长度的测定方法
5.2.1检测出缺陷后,在周围进行检测,以确定缺陷的延伸。
5.2.2用双晶片探头确定缺陷的边界或指示长度时,探头移动方向应与探头的隔声层
相垂直。
5.2.3利用半波高度法确定缺陷的边界或指示长度。
5.2.4确定钢板中缺陷的边界或指示长度时,移动探头,将板底面(或端部)第一次
反射波升高到检测灵敏度条件下荧光屏满刻度50%。
此时,探头中心点即为缺陷的
边界点。
5.3缺陷指示长度的评定规则
单个缺陷按其表现的最大长度作为该缺陷的指示长度,若指示长度小于40mm时,则其长度可不作记录。
5.4单个缺陷指示面积的评定规则
5.4.1单个缺陷按其表现的面积作为该缺陷的单个指示面积。
5.4.2当多个缺陷的相邻间距小于100mm或间距小于相邻缺陷(以指示长度来比较)
的指示长度(取其较大值)时,其各块缺陷面积之和也作为单个缺陷单个指示面积。
5.5 缺陷密集的评定规则
在任一1m×1m检测面积,按缺陷面积占的百分比来确定。
6. 钢板的质量分级
6.1 钢板质量分级见下表
在钢板周边50mm(板厚大于100mm,取板厚的一半)可检测区域及坡口预定线两侧各25mm,单个缺陷的指示长度不得大于或等于50mm。
7.检测报告
7.1工件经检测后,要如实认真填写检测报告提交委托单位。
7.2检测报告应包括下列容:
7.2.1 工程情况:工程名称、委托单位;
7.2.2工件情况:材料牌号、编号、数量;
7.2.3 检测条件:探伤仪型号、探头类型、探头标称频率、晶片尺寸、耦合剂、对比试样等;
7.2.4检测结果:缺陷位置、缺陷分布示意图、缺陷等级及其他;
7.2.5检测人员、审核人员、报告签发人及资格等级,检测日期、检测单位等。
8. 钢板超声波检测工艺卡。