钢板超声波检测工艺
钢板超声波探伤时扫描速度和灵敏度的调节方法
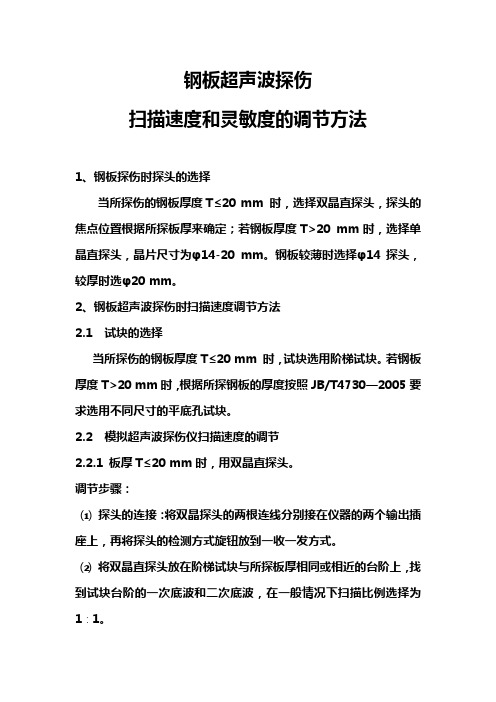
钢板超声波探伤扫描速度和灵敏度的调节方法1、钢板探伤时探头的选择当所探伤的钢板厚度T≤20 mm 时,选择双晶直探头,探头的焦点位置根据所探板厚来确定;若钢板厚度T>20 mm时,选择单晶直探头,晶片尺寸为φ14-20 mm。
钢板较薄时选择φ14探头,较厚时选φ20 mm。
2、钢板超声波探伤时扫描速度调节方法2.1 试块的选择当所探伤的钢板厚度T≤20 mm 时,试块选用阶梯试块。
若钢板厚度T>20 mm时,根据所探钢板的厚度按照JB/T4730—2005要求选用不同尺寸的平底孔试块。
2.2 模拟超声波探伤仪扫描速度的调节2.2.1 板厚T≤20 mm时,用双晶直探头。
调节步骤:⑴探头的连接:将双晶探头的两根连线分别接在仪器的两个输出插座上,再将探头的检测方式旋钮放到一收一发方式。
⑵将双晶直探头放在阶梯试块与所探板厚相同或相近的台阶上,找到试块台阶的一次底波和二次底波,在一般情况下扫描比例选择为1∶1。
⑶调节仪器的水平旋钮,将台阶的一次底波先调到仪器荧光屏水平刻度相对应的位置,如10 mm。
然后调节仪器的深度粗调和微调旋钮,将台阶的二次波调到相应的位置,如20 mm。
(在这里需要着重强调一点就是:要正确判断试块台阶的一次底波和二次底波,不能把质量不好的双晶直探头的固有波判断为试块台阶的二次波。
)在调节的过程中常常会遇到二次波调不到相应的位置,这时就要改变仪器的深度粗调旋钮,然后反复调节深度微调旋钮,使二次波最终调到相应的位置。
⑷按上述方法调节好扫描速度后,始脉冲会自动移到仪器荧光屏以外。
为了验证扫描速度调整是否准确,可在阶梯试块上不同的台阶上测试其厚度。
2.2.2 板厚T>20 mm 时,用单晶直探头,晶片直径φ14-20mm。
调节步骤⑴将探头线与仪器的输出插座连接,探头的方式选择单收发方式。
⑵将探头放在CSK-ⅠA试块25mm厚的面上,找到试块的1-4次底波,调节仪器的粗调和微调旋钮,将1次波和4次波分别调到仪器扫描线的25和100处,此时按深度1∶1的扫描速度就调节好了。
钢结构超声波探伤检测如何取样

钢结构超声波探伤检测如何取样应随机选取焊缝长度的20%检测。
建筑钢结构检测取样方法及数量;第一部分:见证取样检测;一、钢材质量;对属于下列情况之一的钢材,应对钢材进行化学成分分;(1)国外进口钢材;(2)钢材混批;(3)板厚等于或大于40mm,且设计有Z向性能要;(4)建筑结构安全等级为一级,大跨度钢结构中主要;(5)设计有复验要求的钢材;(6)对质量有疑义的钢材;1、化学成分分析(主控项目);(1)检验指标:建筑钢结构检测取样方法及数量第一部分:见证取样检测一、钢材质量对属于下列情况之一的钢材,应对钢材进行化学成分分析和力学性能的抽样复验:(1)国外进口钢材;(2)钢材混批;(3)板厚等于或大于40mm,且设计有Z向性能要求的厚板;(4)建筑结构安全等级为一级,大跨度钢结构中主要受力构件所采用的钢材;(5)设计有复验要求的钢材;(6)对质量有疑义的钢材。
1、化学成分分析(主控项目)(1)检验指标:碳、硅、锰、硫、磷及其他合金元素(2)依据标准:《钢和铁化学成分测定用试样的取样和制样方法》GB/T20066-2006《建筑结构检测技术标准》GB/T50344-2004(3)取样方法及数量:钢材化学成分分析,可根据需要进行全成分分析或主要成分分析。
所采用的取样方法应保证分析试样能代表抽样产品的化学成分平均值。
分析试样应去除表面涂层、除湿、除尘、以及除去其他形式的污染。
分析试样应尽可能避开孔隙、裂纹、疏松、毛刺、折叠或其他表面缺陷。
制备的分析试样的质量应足够大,以便可能进行必要的复检验。
对屑状或粉末状样品,其质量一般为100g。
可采取钻、切、车、冲等方法制取屑状样品。
不能用钻取方法制备屑状样品时,样品应该切小或破碎,然后用破碎机或振动磨粉碎。
振动磨有盘磨和环磨。
制取的粉末分析试样应全部通过规定孔径的筛。
钢材化学成分的分析每批钢材取1个试样。
2、力学性能检验(主控项目)(1)检验指标:屈服点、抗拉强度、伸长率、冷弯、冲击功(2)依据标准:《钢及钢产品力学性能试验取样位置及试验制备》GB/T2975-1998《建筑结构检测技术标准》GB/T50344-2004(3)取样方法及数量:应在外观及尺寸合格的钢材上取样,产品应具有足够大的尺寸。
厚钢板超声波自动探伤检验方法国家标准

《厚钢板超声波自动探伤检验方法》国家标准编制说明一、工作简况1 任务来源2007年10月,全国无损检测标准化技术委员会向重庆钢铁集团有限公司下发了《关于起草厚钢板超声波自动探伤检验方法国家标准任务书》,2008年底该标准转由全国钢标准化技术委员会归口。
2 编制单位主编制单位:重庆钢铁股份有限公司参加编制单位:冶金工业信息标准研究院等3 工作过程3.1 主要过程简介从上世纪80年代到现在,国内已有舞阳钢铁公司、首钢公司、宝钢公司、重钢公司等多家钢铁企业投建了钢板超声波自动探伤设备,既有国内自行研制的,也有从国外引进的,各探伤设备的技术条件各不相同,技术参数参差不齐,且对缺陷的判定标准也各不相同,为规范钢板超声波自动探伤的技术条款,确保所探钢板的实物质量,并结合国内目前自动探伤的现状和发展趋势,由全国无损检测标准化技术委员会提出,重庆钢铁集团有限公司和重庆市技术质量监督局承接起草。
重钢于2008年3月成立了标准编制小组,开始了标准的起草编制工作,标准编制组首先征求了一些单位的意见,查阅标准资料,收集了ISO、EN等国际国外主要标准。
编制组经过收集和对比国内外相关标准,了解国内超声自动探伤设备使用现状和发展趋势,并经过系列试验,提出了标准征求意见稿征求意见,编制组根据前期征求和反馈的意见,于2009年6月完成了本讨论稿。
3.2 收集的国内外主要标准包括ASTM A578 特殊设备用的普通钢板和包覆钢板的直波束超声探伤检验的标准规范ASTMA435 钢板的直射束纵向超声波检验EN 10160 厚度大于或等于6毫米的钢板制品的超声波检验(平面反射法)GB/T 2970 厚钢板超声波检验方法JB/T4730 承压设备无损检测方法3.3 对相关的国内标准进行对比分析,本次标准修订主要参照GB/T2970和JB/T4730等标准。
二、标准编制原则本标准的制订遵循以下原则:1、标准的主要内容以GB/T 2970—2004《厚钢板超声波检验方法》标准为基础,参照国外先进标准ASTM A578、ASTMA435和EN 10160。
压力容器用钢板超声波探伤
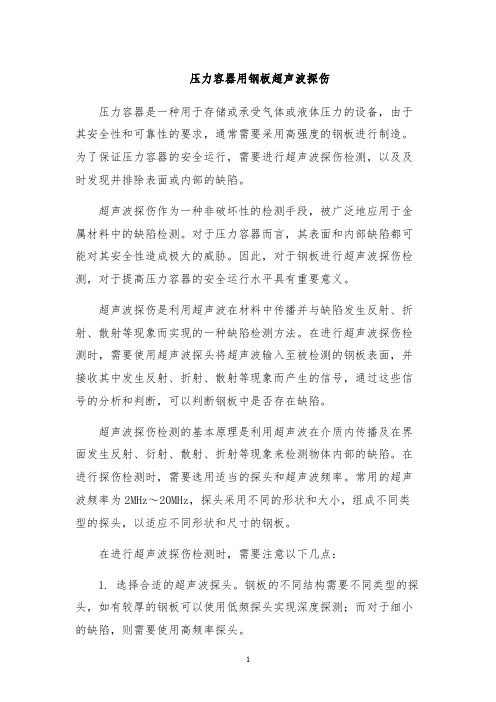
压力容器用钢板超声波探伤压力容器是一种用于存储或承受气体或液体压力的设备,由于其安全性和可靠性的要求,通常需要采用高强度的钢板进行制造。
为了保证压力容器的安全运行,需要进行超声波探伤检测,以及及时发现并排除表面或内部的缺陷。
超声波探伤作为一种非破坏性的检测手段,被广泛地应用于金属材料中的缺陷检测。
对于压力容器而言,其表面和内部缺陷都可能对其安全性造成极大的威胁。
因此,对于钢板进行超声波探伤检测,对于提高压力容器的安全运行水平具有重要意义。
超声波探伤是利用超声波在材料中传播并与缺陷发生反射、折射、散射等现象而实现的一种缺陷检测方法。
在进行超声波探伤检测时,需要使用超声波探头将超声波输入至被检测的钢板表面,并接收其中发生反射、折射、散射等现象而产生的信号,通过这些信号的分析和判断,可以判断钢板中是否存在缺陷。
超声波探伤检测的基本原理是利用超声波在介质内传播及在界面发生反射、衍射、散射、折射等现象来检测物体内部的缺陷。
在进行探伤检测时,需要选用适当的探头和超声波频率。
常用的超声波频率为2MHz~20MHz,探头采用不同的形状和大小,组成不同类型的探头,以适应不同形状和尺寸的钢板。
在进行超声波探伤检测时,需要注意以下几点:1. 选择合适的超声波探头。
钢板的不同结构需要不同类型的探头,如有较厚的钢板可以使用低频探头实现深度探测;而对于细小的缺陷,则需要使用高频率探头。
2. 调整超声波发射声束的位置和角度。
在进行超声波探测时,需要将超声波发射声束对准被检测的区域,并调整探头的角度,以保证声波的传播路线与被探测物体表面垂直。
3. 依据超声波检测结果进行数据处理。
通过超声波探测并收集到的反射信号,计算出缺陷位置和尺寸,并进行数据分析和处理,以判断钢板中是否存在安全隐患。
钢板超声波探伤是一项重要的非破坏性检测技术,广泛应用于压力容器等领域。
只有不断完善超声波探测技术,提高其检测准确性和精度,才能更好地保障压力容器的安全运行。
钢板探伤国标3级

钢板探伤国标3级(原创实用版)目录1.钢板探伤的背景和意义2.钢板探伤的国标 3 级标准3.钢板探伤的常用方法和技巧4.钢板探伤的实际应用和注意事项正文钢板探伤是指利用超声波、射线等物理手段,对钢板的内部结构和缺陷进行检测和评估的一种技术。
在工业生产中,钢板是一种常用的材料,但是由于生产工艺和环境的影响,钢板可能会出现各种缺陷,如裂纹、气孔、夹杂等。
这些缺陷会影响钢板的性能和使用寿命,因此,对钢板进行探伤检测是非常重要的。
钢板探伤的国标 3 级标准是指按照国家标准 GB/T2970-2004《厚钢板超声波检验方法》进行的探伤检测。
这个标准规定了钢板探伤的检测方法、检测设备、检测结果的处理和表示等方面的内容。
按照这个标准,钢板探伤分为三个级别,分别是 I 级、II 级和 III 级。
其中,I 级为最高级别,要求检测的缺陷最小,III 级为最低级别,要求检测的缺陷最大。
钢板探伤的常用方法和技巧包括超声波探伤、射线探伤、磁粉探伤等。
其中,超声波探伤是最常用的一种方法,它利用超声波在钢板内部传播的特性,检测钢板内部的缺陷和结构变化。
射线探伤则利用射线对钢板进行透视,检测钢板内部的缺陷和裂纹。
磁粉探伤则利用磁粉在磁场作用下在钢板表面形成磁痕,从而检测钢板表面的缺陷和裂纹。
钢板探伤的实际应用非常广泛,它主要用于检测钢板的裂纹、气孔、夹杂等缺陷,以及钢板的厚度、密度、强度等性能指标。
在实际应用中,钢板探伤需要按照国家标准和设计要求进行,同时需要注意探伤的精度和可靠性,以及探伤结果的正确性和有效性。
总之,钢板探伤是一种非常重要的技术,它有助于确保钢板的质量和性能,从而保证工业生产的安全和稳定。
钢板桩验收中的测量与检测方法
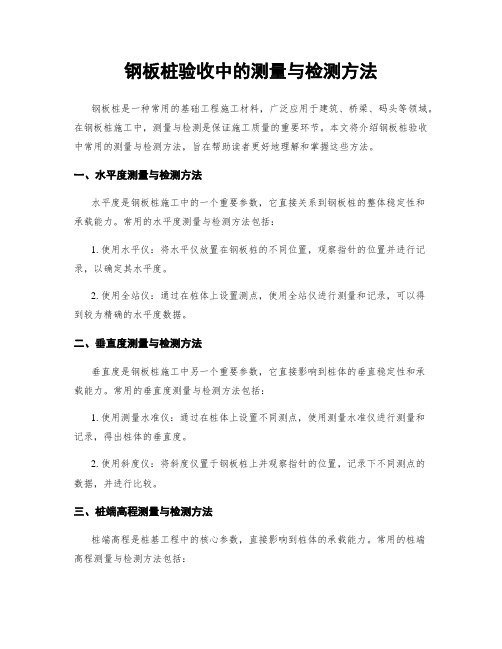
钢板桩验收中的测量与检测方法钢板桩是一种常用的基础工程施工材料,广泛应用于建筑、桥梁、码头等领域。
在钢板桩施工中,测量与检测是保证施工质量的重要环节。
本文将介绍钢板桩验收中常用的测量与检测方法,旨在帮助读者更好地理解和掌握这些方法。
一、水平度测量与检测方法水平度是钢板桩施工中的一个重要参数,它直接关系到钢板桩的整体稳定性和承载能力。
常用的水平度测量与检测方法包括:1. 使用水平仪:将水平仪放置在钢板桩的不同位置,观察指针的位置并进行记录,以确定其水平度。
2. 使用全站仪:通过在桩体上设置测点,使用全站仪进行测量和记录,可以得到较为精确的水平度数据。
二、垂直度测量与检测方法垂直度是钢板桩施工中另一个重要参数,它直接影响到桩体的垂直稳定性和承载能力。
常用的垂直度测量与检测方法包括:1. 使用测量水准仪:通过在桩体上设置不同测点,使用测量水准仪进行测量和记录,得出桩体的垂直度。
2. 使用斜度仪:将斜度仪置于钢板桩上并观察指针的位置,记录下不同测点的数据,并进行比较。
三、桩端高程测量与检测方法桩端高程是桩基工程中的核心参数,直接影响到桩体的承载能力。
常用的桩端高程测量与检测方法包括:1. 使用水准仪:在桩体顶部和底部设置测点,使用水准仪进行测量,得出桩端高程的差值。
2. 使用激光水准仪:将激光水准仪设置在桩体的上方,并通过激光束与接收器进行测量,得出桩端高程的数据。
四、桩身质量检测方法桩身质量是钢板桩验收中不可忽视的一个要素,直接影响到钢板桩的使用寿命和安全性。
常用的桩身质量检测方法包括:1. 目测检查:通过观察桩体是否存在裂缝、变形、腐蚀等问题,初步判断桩身的质量情况。
2. 超声波检测:通过将超声波传感器贴附在桩体表面,测量超声波的传播时间和反射强度,得出桩体的质量情况。
五、桩头水平度测量与检测方法桩头水平度是钢板桩验收中关注的一个重要参数,直接影响到桩体的使用效果和安全性。
常用的桩头水平度测量与检测方法包括:1. 目测检查:通过观察桩头是否平整、与水平面是否垂直等,初步判断桩头水平度的情况。
板材超声波探伤

△ 利 用 F1 评 价 缺 陷 。 出 现 叠 加 效 应 时 , 当 板 厚 较 薄 时 可 用 F2 评 价 缺 陷 , 其 目 的 是 减 少 近 场 区 影 响 。 实 际 上 , 应 根 据 晶 片 直 径 的 尺 寸 大 小 及 F1 不 清 晰 时 , 可 用 F2 来 评 价 缺 陷 , 用 F2 和 B2 评 价 时 , 基 准 灵 敏 度 以 第二次反射波校正。 如 采 用 直 径 为 Ф 14 m m ~ 20 m m 的 直 探 头 探 伤 钢 板 , 一 般 当 板 厚 δ < 20 m m 时 , 可 采 用 F 2 评 价 缺 陷 。 1.3 探 头 与 扫 查 方 式 1. 3.1 频 率 2.5 ~ 5MHz ,40mm 以 下 钢 板 检 测 频 率 为 5MHz ,40mm 以 上 钢 板 检 测 频 率 为 2.5MHz 晶 片 直 径 : Ф14 ~ Ф25mm 探头形式: 单晶直探头 钢板检测 联合双晶直探头 适用于板厚 δ 较薄的钢板检测,因盲区小, 适 用 于 板 厚 δ 较 大 的 钢 板 检 测 ,用 于 20mm 以 上
1.7
钢板横波检验按附录 B 规定要求 非夹层性缺陷
适用范围 探头
K1 2MHz~5MHz 25mm 长 V 形 槽 深 为 板 厚 3 % V 形槽的距离-波幅曲线, 按 不 同 板 厚 根 据 B.4 规 定 调 节
人工缺陷 灵敏度
验 收 标 准 按 B.6 规 定 : 等 于 或 超 过 距 离 - 波 幅 曲 线 信 号 不 合 格 , 发现分层类缺陷按纵波检测规定处理。
8 / 26
1.6 质 量 等 级 判 定 : 按 JB/T4730-2005 标 准 4.1.7 条 规 定 评 定 。 单 个 缺 陷 指 示 长 度 按 4.1.7.1 规 定 , 单 个 缺 陷 指 市 面 积 按 4.1.7.2 规 定 。 JB/T4730-2005 标 准 标 准 中 表 3 钢 板 质 量 分 级 表 中 数 据 适 用 于 非 白点、裂纹等危险缺陷,即非危险缺陷。白点、裂纹等危险缺 陷,都判为 V 级。
钢结构典型焊缝的超声波检测

钢结构典型焊缝的超声波检测摘要:本文针对钢结构中比较典型的几种焊缝的超声波检测方法,介绍了对这几种焊接接头的扫查方式,并通过理论计算实现了对缺陷的准确定位。
关键词:钢结构超声波检测焊缝缺陷定位Ultrasonic Testing of Typical Weleded Joints of Steel Structures(No. 52 Institute of China North Industries Group CooperationYantai BranchYantai264003China)Abstract: In the paper,we introduce scinning mode of ultrasonic testing in typical weleded joints of steel structures ,and get the accurate location for defece according to the calculated gradient.Key words: Steel Structure Ultrasonic Testing Weleded Joints location of defece1、引言随着钢结构行业的快速发展和焊接技术的逐渐提高, 构造复杂化,大跨度、超高层钢结构日渐增多,焊缝焊接形式也日趋多样化。
无损检测作为控制焊接质量的主要手段起到至关重要的作用,而超声波检测以方便、经济、有效等优点被用来控制焊缝内部质量的主要方法。
但随着焊接形式的多样化,对焊缝的超声波检测带来了一些困难,有时对缺陷的定位问题也很难准确把握,怎样根据实际焊接形式采用合理的超声波检测方法需要我们针对问题逐渐完善。
2、钢结构典型焊缝的检测要点2.1对接焊缝对接接头是钢结构中最重要也是最为常见的的焊接形式,绝大部分对接接头采用全熔透焊接,要求焊缝与母材等强,探伤的要求也往往较高。
- 1、下载文档前请自行甄别文档内容的完整性,平台不提供额外的编辑、内容补充、找答案等附加服务。
- 2、"仅部分预览"的文档,不可在线预览部分如存在完整性等问题,可反馈申请退款(可完整预览的文档不适用该条件!)。
- 3、如文档侵犯您的权益,请联系客服反馈,我们会尽快为您处理(人工客服工作时间:9:00-18:30)。
.
.
江苏敦邦钢结构工程有限公司
钢板超声波检测工艺
编制人:
审核人:
审批人:
2011年5月
江苏敦邦钢结构工程有限公司
.
.
目 录
1. 总则.......................................................................................................................1
2. 检测人员...............................................................................................................2
3. 探头、仪器。试块与耦合剂...............................................................................2
4. 检测........................................................................................................................4
5. 缺陷的测定与评定................................................................................................5
6. 钢板的质量分级....................................................................................................6
7. 检测报告.................................................................................................................6
8. 钢板超声波检测工艺卡.........................................................................................6
.
.
1.总则
:
1.1
本方案适用于江苏敦邦钢结构工程有限公司工厂原材料钢板的超声波检验
1.2 编制本检测方案的依据为:
1.2.1《钢结构工程施工质量验收规范》GB50205-2001;
1.2.2
《厚钢板超声波检验方法》GB/T2970-2004
1.3
本方案需要更改或对其内容有疑问,以及发生记载外的重要事项时,要同设计
单位协商,经同意后进行检查,如有发生上述事项,做成书面文件发布给相关人员。
2.检验人员
2.1
从事原材料钢板的超声检测人员,必须经过技术培训,并取得认可的与其
工作相对应的资格证书;由Ⅰ级及II级以上人员担任。签发报告由II级及
II级以上人员担任。各技术资格等级人员只能从事与该等级相应的超声检测工作
并负相应的技术责任,Ⅰ级人员必须在II级或II级以上人员的指导下进行检测;
2.2
从事超声波检测人员校正视力不得低于1.0并且必须每年检查一次。
3.仪器、探头、试块与耦合剂
3.1探伤仪
3.1.1
超声检测设备均应具有产品质量合格证或合格的证明文件,并按规范要求予以
鉴定;
3.1.2
采用数字型可记录的A型脉冲反射式探伤仪;
3.1.3
在荧光屏满刻度的80%范围内呈线性显示,衰减器精度为任意相邻12dB以内,
最大累计误差不超过1dB。水平线性误差不大于1%,垂直线性误差不大于5%,
其余指标应符合GB/T 8651 JB/T 10061的规定。
3.2 探头
3.2.1
直探头选用按下表;
板厚 所用探头 探头标称频率/MHz
6~13 双晶片直探头 5
>13~60 双晶片直探头或单晶片直探头 ≥2.0
>60 单晶片直探头 ≥2.0
3.2.2 双晶片直探头性能应符合GB/T 2970附录A的要求。
3.2.3 探头直径应在10-30mm之间
3.3 试块
.
.
3.3.1
标准试块:下面图样试块或CBⅠ、CBⅡ试块;
3.3.2
试块图样:
.
.
3.4
耦合剂
一般情况使用水作为耦合剂。
4. 检测
4.1
检测时间
原则上在钢板进厂时进行,也可在下料前进行。
4.2
检测面
可以从钢板任一轧制面进行检测,被检钢板的表面应平整,应清除影响检测的氧化皮、
锈蚀、油污、及其它外部杂质。
4.3
检测灵敏度
4.3.1
检测灵敏度应计入试样与被检钢板之间的表面耦合声能损失(dB)。
4.3.2
用双晶片直探头检测时,用图1试样或同厚度钢板上的第一次底波高度调整到满
刻度的50%,再提高10dB作为检测灵敏度。
4.3.3
用单晶片直探头检测时,用图2试样平底孔的第一次反射波高度调整到满刻度的
50%来校准。
4.3.4
板厚大于探头3倍近场区时,检测灵敏度用计算法、通过第一次底面回波高度来
确定。
4.4
探头扫查形式
4.4.1
探头沿垂直于钢板压延方向、间距不大于100mm的平行线进行扫查;在钢板周
围50mm(板厚大于100mm时, 取板厚的一半)及坡口预定线(合同或技术协议中
确定具体位置)两侧各25mm内沿周边进行扫查。
4.4.2
用双晶片探头时,探头隔声层应与压延方向平行(垂直于压延方向扫查)。
4.4.3
根据合同、技术协议书或图样的要求,也可采用其他形式的扫查。
.
.
探头扫查示意图
4.5
检测速度
检测速度应不大于200mm/s。
5. 缺陷的测定与评定
5.1
在检测过程中,发现下列情况应记录
5.1.1
缺陷第一次反射波(F1)波高大于或 等于满刻度的50%。
5.1.2
当底面第一次反射波(B1)波高未达到满刻度时,缺陷第一次反射波(F1)波与
第一次反射波(B1)波高之比大于或 等于满刻度的50%。
5.1.3
当底面(或板端部)第一次反射波(B1)波高低于满刻度的50%。
5.2
缺陷的边界或指示长度的测定方法
5.2.1
检测出缺陷后,在周围进行检测,以确定缺陷的延伸。
5.2.2
用双晶片探头确定缺陷的边界或指示长度时,探头移动方向应与探头的隔声层
相垂直。
5.2.3
利用半波高度法确定缺陷的边界或指示长度。
5.2.4
确定钢板中缺陷的边界或指示长度时,移动探头,将板底面(或端部)第一次
反射波升高到检测灵敏度条件下荧光屏满刻度50%。此时,探头中心点即为缺陷的
边界点。
5.3
缺陷指示长度的评定规则
单个缺陷按其表现的最大长度作为该缺陷的指示长度,若指示长度小于40mm时,则其
长度可不作记录。
5.4
单个缺陷指示面积的评定规则
5.4.1
单个缺陷按其表现的面积作为该缺陷的单个指示面积。
5.4.2
当多个缺陷的相邻间距小于100mm或间距小于相邻缺陷(以指示长度来比较)
的指示长度(取其较大值)时,其各块缺陷面积之和也作为单个缺陷单个指示面积。
5.5
缺陷密集的评定规则
在任一1m×1m检测面积内,按缺陷面积占的百分比来确定。
.
.
6. 钢板的质量分级
6.1
钢板质量分级见下表
6.2
在钢板周边50mm(板厚大于100mm,取板厚的一半)可检测区域内及坡口预定线两侧各
25mm内,单个缺陷的指示长度不得大于或等于50mm。
7.检测报告
7.1
工件经检测后,要如实认真填写检测报告提交委托单位。
7.2
检测报告应包括下列内容:
7.2.1
工程情况:工程名称、委托单位;
7.2.2
工件情况:材料牌号、编号、数量;
7.2.3
检测条件:探伤仪型号、探头类型、探头标称频率、晶片尺寸、耦合剂、对比试样
等;
7.2.4
检测结果:缺陷位置、缺陷分布示意图、缺陷等级及其他;
7.2.5
检测人员、审核人员、报告签发人姓名及资格等级,检测日期、检测单位等。
8. 钢板超声波检测工艺卡
级别 不允许存在的单个缺陷的指示长度/mm 不允许存在的单个缺陷的指示面积/cm2 在任一1m×1m检测面积内不允许存在的缺
陷面积百分比/%
以下单个缺陷的指
示面积不记/cm2
Ⅰ ≥80 ≥25 >3 <9
Ⅱ ≥100 ≥50 >5 <15
Ⅲ ≥120 ≥100 >10 <25
Ⅳ ≥150 ≥100 >10 <25