精轧机常见问题解决
精轧机GL150常见故障处理障

精轧机GL150常见故障处理障精轧机GL150常见故障处理⒈ F07860 : External Fault 1 外部故障1电机温度超温故障,电机温度包括定子线圈U1,V1,W1,U2,V2,W2 绕组温度, 前轴承温度,后轴承温度,电机的温度已经超过电机的允许跳闸温度。
问题处理:从操作台的画面上查看哪一个温度过高,检查电机风机是否正常运行,检查电机冷却水是否已经通入,检查电机的前后轴承是否有问题。
⒉ A07850 : External Alarm 1 外部报警1电机温度超温报警,电机温度包括定子线圈U1,V1,W1,U2,V2,W2 绕组温度, 前轴承温度,后轴承温度,电机的温度已经超过电机的允许报警温度。
问题处理:从操作台的画面上查看哪一个温度过高,检查电机风机是否正常运行,检查电机冷却水是否已经通入,检查电机的前后轴承是否有问题。
⒊ F07861 : External Fault 2 外部故障2电机轴瓦润滑的稀油站有故障,包括稀油站的油压,油流,油温等故障。
问题处理:检查电机轴瓦润滑的稀油站,查看稀油站的油压,油流,油温是否有不正常的地方,排除故障后,使稀油站恢复正常,电机运行前,必须保证轴瓦润滑的稀油站无故障,否则不能合闸,起车。
⒋ F49110 : Fan monitoring: Differential pressure low fault threshold 功率柜风机监控:功率柜风机的压差低故障功率柜内的风压低,功率元件的冷却效果差,容易烧功率元件。
在+A112柜,+A200柜,+A212柜内各有一个白色的风压开关,风压开关可以从0Pa到1000Pa进行调节,其中每一个刻度为50Pa。
故障值: 0000 0001 (hex) 为+A112柜的风压故障故障值: 0000 0010 (hex) 为+A200柜的风压故障故障值: 0001 0000 (hex) 为+A212柜的风压故障问题处理:检查功率柜风机是否正常运行,检查功率柜风机的开关是否有跳闸的情况;检查功率柜(背面)的封堵情况是否良好,是否有漏风的情况,如果有应立刻将封堵做好;检查功率柜(正面)柜门通风是否良好,如果不好,要立刻清扫柜门的过滤网; 在适当的情况下,根据故障值可以减小相应功率柜风压开关的设定值,使此故障消除。
高速无扭精轧机组设备故障诊断分析

高速无扭精轧机组设备故障诊断分析高速无扭精轧机组是金属材料的精密加工设备,广泛应用于轧制不锈钢、铜、铝及其合金等材料。
在生产过程中,设备故障的出现会给生产带来严重影响,因此及时准确地诊断故障并采取正确的维修措施对于保障设备正常运转和生产进度至关重要。
本文将对高速无扭精轧机组设备故障诊断分析进行阐述,希望能对相关从业人员有所帮助。
一、故障现象描述1. 外径尺寸偏大或偏小:在生产过程中,外径偏大或偏小是一种常见的故障现象。
当外径偏大时,产品无法满足客户的要求,造成浪费;而当外径偏小时,则会影响产品的装配和使用效果,同样会给企业带来损失。
2. 螺纹拉伸不达标:在生产过程中,如果螺纹的拉伸性能达不到标准要求,那么产品的使用效果和安全性都会受到影响,严重时甚至会导致产品报废。
3. 生产效率低下:生产效率是衡量设备运行状态好坏的重要指标之一,如果生产效率低下,将会直接影响企业的产能和经济效益。
二、故障原因分析1. 设备磨损严重:设备长时间使用后,往往会出现各种磨损现象,比如轧辊表面磨损、导轨磨损等,这些磨损会直接影响设备的精度和稳定性。
2. 设备使用不当:操作人员在使用设备时如果没有按照操作规程进行操作,比如轧辊调整不当、刀具使用不当等,都可能会导致设备故障的发生。
3. 部件松动:高速无扭精轧机组设备中的各种连接部件,比如螺栓、销轴等,如果松动或者脱落,都会影响设备的正常运转。
4. 部件损坏:设备中的各种部件,比如轴承、齿轮等,如果损坏或者磨损严重,都会导致设备故障的发生。
5. 润滑不良:设备运行时需要一定的润滑保养工作,如果润滑不良或者润滑油污染,都会影响设备的正常运转。
三、故障诊断方法1. 视觉检查:通过对设备各个部位进行外观检查,观察是否存在明显的异常情况,比如磨损、松动、脱落等。
2. 测量检查:通过使用测量工具,比如卡尺、游标卡尺等,对设备的各个关键尺寸进行测量,查找是否存在超出标准的情况。
3. 振动检测:利用振动检测仪等工具,对设备运行时的振动情况进行监测,判断设备各部位轴承、齿轮等是否存在异常。
热轧精轧机活套液压控制及故障分析
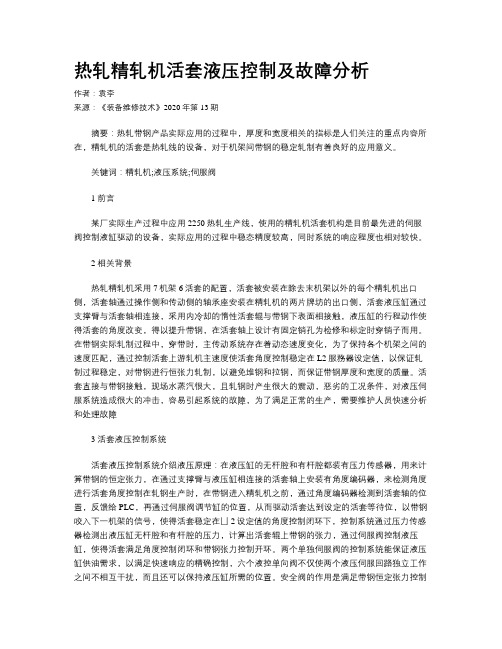
热轧精轧机活套液压控制及故障分析作者:袁李来源:《装备维修技术》2020年第13期摘要:热轧带钢产品实际应用的过程中,厚度和宽度相关的指标是人们关注的重点内容所在,精轧机的活套是热轧线的设备,对于机架间带钢的稳定轧制有着良好的应用意义。
关键词:精轧机;液压系统;伺服阀1 前言某厂实际生产过程中应用2250热轧生产线,使用的精轧机活套机构是目前最先进的伺服阀控制液缸驱动的设备,实际应用的过程中稳态精度较高,同时系统的响应程度也相对较快。
2 相关背景热轧精轧机采用7机架6活套的配置,活套被安装在除去末机架以外的每个精轧机出口侧,活套轴通过操作侧和传动侧的轴承座安装在精轧机的两片牌坊的出口侧,活套液压缸通过支撑臂与活套轴相连接,采用内冷却的惰性活套辊与带钢下表面相接触,液压缸的行程动作使得活套的角度改变,得以提升带钢,在活套轴上设计有固定销孔为检修和标定时穿销子而用。
在带钢实际轧制过程中,穿带时,主传动系统存在着动态速度变化,为了保持各个机架之间的速度匹配,通过控制活套上游轧机主速度使活套角度控制稳定在L2服務器设定值,以保证轧制过程稳定,对带钢进行恒张力轧制,以避免堆钢和拉钢,而保证带钢厚度和宽度的质量。
活套直接与带钢接触,现场水蒸汽很大,且轧钢时产生很大的震动,恶劣的工况条件,对液压伺服系统造成很大的冲击,容易引起系统的故障,为了满足正常的生产,需要维护人员快速分析和处理故障3 活套液压控制系统活套液压控制系统介绍液压原理:在液压缸的无杆腔和有杆腔都装有压力传感器,用来计算带钢的恒定张力,在通过支撑臂与液压缸相连接的活套轴上安装有角度编码器,来检测角度进行活套角度控制在轧钢生产时,在带钢进入精轧机之前,通过角度编码器检测到活套轴的位置,反馈给PLC,再通过伺服阀调节缸的位置,从而驱动活套达到设定的活套等待位,以带钢咬入下一机架的信号,使得活套稳定在凵2设定值的角度控制闭环下,控制系统通过压力传感器检测出液压缸无杆腔和有杆腔的压力,计算出活套辊上带钢的张力,通过伺服阀控制液压缸,使得活套满足角度控制闭环和带钢张力控制开环。
精轧机常见问题解决

1.精轧机组工艺调整应注意的问题有:(1)精轧机组的工艺调整一般只调整第一架次和成品架次,其他架次不得随意调整,其原因有两个:1)动了其中某一架的辊缝,会破坏各架间的微张力关系,造成产品尺寸波动;2)滚动导卫的导辊开口度是根据样棒精确调整的,若放大某一架辊缝,会造成来料变大,导致导辊使用寿命降低甚至损坏导轮而出废品;若收小某一道次辊缝,会造成来料变小,导轮夹持不稳,会出现倒钢现象。
(2)当成品尺寸高度过大,宽度也过大时,应先调第一架轧机,后调成品轧机;第一架、成品架轧机的累计调整量不得超过0.3mm。
(3)当发现钢坯表面质量不好时,应停机检查辊环、导卫中有无异物。
2.精轧机组生产工艺的特点有:采用固定道次间轧辊转速比,以单线微张力无扭转高速连续轧制的方式;进行合理的孔型设计和精确的轧件尺寸计算,配合以耐磨损的轧槽;采用较小直径的轧辊;以椭—圆孔型系统轧制多规格产品;机架中心距尽可能地小,以减轻微张力对轧件断面尺寸的影响;精轧前及精轧道次间进行轧件穿水冷却,进行轧件变形温度的控制。
3.精轧机组调整的方法在轧制过程中,应根据取样的尺寸及烧木印的情况来调整精轧机。
一般只调整精轧机第一架和最后一架,而其他架次不得随意调整。
下面举例说明:(1)成品垂直直径较大、水平直径稍小时,压小成品架次的辊缝;(2)成品垂直直径较小、水平直径正好时,放大成品架次的辊缝;(3)成品垂直直径正好、水平直径较大时,压小第一架次的辊缝;(4)成品垂直直径正好、水平直径较小时,放大第一架次的辊缝。
如经过上述调整后仍达不到要求,应检查前面机组的来料尺寸,放大或缩小前面机组的最末架次的辊缝。
一般精轧机第一架和最后一架轧机的辊缝累计调整量不得超过0.3mm。
4.精轧机组机架间堆钢的原因有:(1)导卫粘钢;(2)导轮不转或轴承烧坏;(3)轧件劈头;(4)导卫或辊环装错;(5)辊缝设定不当或来料尺寸不合要求;(6)导卫未紧固;(7)压辊键断使辊片松动;(8)辊片碎;(9)轧辊轴轴瓦磨损或破裂。
精轧产品质量缺陷描述及解决办法

精轧产品质量缺陷描述及解决办法一、目的目标:为明确粗轧各类产品质量缺陷的定义、名称,分析各类产品缺陷的产生原因,预防产品缺陷的发生,规范产品质量管理,提升产品质量,特制定本标准。
二、管理职责:本标准自颁布之日起开始实施,由品质管理部负责解释。
序号缺陷名称图片缺陷定义产生原因解决措施1 擦伤因物体间棱与面或面与面接触后产生相对滑动或错动而在板面产生成束(或组)分布的伤痕1、粗轧过程中,带材与导辊接触时产生相对摩擦造成擦伤;2、张力使用不当,开卷或卷取时产生层间错动;3、操作不当导致带材层间滑动;4、卷取后调运、搬运过程中层间错动。
1、定期检查导辊转动情况,发现不转或不同步时,联系设备人员处理;2、严格按照工艺要求使用张力;3、控制打底串层和错层,打底打紧后才能退出助卷器;4、料卷吊离托盘时,必须先用钢带打好。
2 划伤尖锐的物体接触板面,在相对滑动时造成的单条状分布的伤痕。
1、轧机辊道上粘铝使带材表面划伤;2、轧机导板、导路等有尖锐凸起物。
1、定期检查和擦拭导辊;2、定期检查导板和导路,发现凸起物清理干净再生产,升速前确认各导板已到位。
序号缺陷名称图片缺陷定义产生原因解决措施3 粘伤带材表面呈点状、片状或条状伤痕,一般有周期性。
1、轧辊表面粘铝,轧制后带材表面周期性粘伤;2、轧制油喷射压力低、喷淋量小,异物带入轧辊粘伤;3、来料有粘铝,轧制后带材表面周期性粘伤;4、来料温度高或单卷连轧,导致油膜厚度薄,辊和料直接接触粘伤。
1、严格按照工艺要求使用油压、油温;2、通过检查粘铝周期确定是否来料粘铝;3、严禁高温轧制和单卷连轧。
4 中松带材中部变形不均匀而形成的不平整现象。
1、压下量过小,导致轧制力偏小;2、轧辊凸度过大,正弯值偏大;3、来料中松;4、中部喷淋量偏小,轧辊中部冷却不足;5、轧辊粗糙度偏小。
1、增大道次压下量;2、降低轧辊凸度,减小正弯值;3、从轧机入口检查是否来料中松;4、增加轧辊中部喷淋量;5、提高轧辊粗糙度,适当提高油温,降低喷油总量;6、提高降低轧制速度,减小出口张力。
精轧工作辊换辊系统常见故障分析l
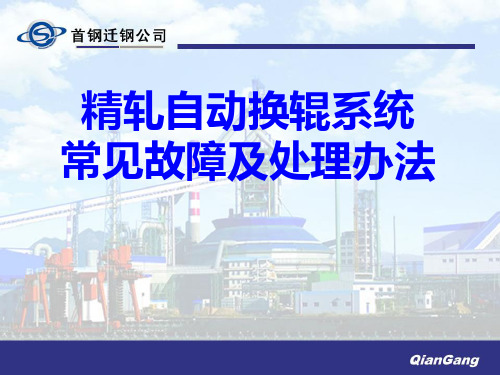
a -
b 1
a 1
b
a
30%
b 1
b PE01 YVH S 1/1-6 PE01 YV H S 2/1-6 PE 02 YVH 1/1-6
a PE03 YV H 1/1-6
b
-
0
P T
P T
P T
T
+
+
1
1
0
30%
1
OS
P E01 B S 4/1-6 I S co llapse clo se R oll gap
故障7 故障7 出入口导卫、擦辊器不到位 1、检查导卫现场实际位置及接近开关信号 2、检查擦辊器现场实际位置及压力开关显示压力值 3、必要时可先捅阀动作设备保证换辊 故障8 故障8 提升轨道 在推辊前要确认是否上升到位。 检查现场没有动作,要确认接近开关信号是否正常、机上阀台的电磁 阀的信号是否正确。如果接近开关信号正常、电磁阀已经得电,可以 在现场有人确认的情况下手动捅阀先换辊,然后再检查阀头和电磁铁, 如果手动不能捅动就要更换电磁阀;
精轧自动换辊系统 常见故障及处理办法
精轧机自动换辊分为四个阶段: 精轧机自动换辊分为四个阶段: 1、换辊前准备阶段 2、换辊前设备停机阶段 3、换辊阶段 4、换辊后设备恢复阶段
换辊前准备阶段
换辊过程: 换辊过程: 1、换辊小车从初始位置E1(磨辊间)把新辊推到精轧机前 的换辊平移盖板上(E7)(平移盖板位于飞剪侧); 2、换辊小车后退到位置E6,平移盖板向卷取机侧平移; 3、换辊小车前进到位置E11;
故障3 故障3、CVC窜辊不到位
1、换辊模式自动时序CVC窜辊不到位:确认工作辊处于平衡状态后, 可再次切换模式,重新执行自动时序; 2、长时间轧机内没有轧辊(检修恢复时),某一个CVC液压缸位置不 正确:在CVC窜辊处于手动或自动模式时,强制位置设定为0动作液压 缸:Nx_RS_WR_REF(G2) 3、如果出入口两侧位置一致且位置值在1mm内,可考虑封点操作
中精轧钢机跑偏故障分析及改进

中精轧钢机跑偏故障分析及改进我国国民经济的飞速发展,我国的钢铁的产量已跃居世界首位,年产量达7.17亿吨。
钢铁中轧钢机械是其中的关键设备之一,他的工作状况直接影响着生产效率、产品质量及生产的稳定性和连续性。
轧钢时由于工况比较恶劣,轧钢经常出现各种故障,对生产影响较大。
本文结合陕西龙门钢铁公司西安轧钢厂实际应用的精度轧生产线对其出现的故障进行了深入的分析,并提出相应的改进措施,经改进后轧钢厂生产线已出现了良好的生产效果,希望对国内相关的生产企业提供有益的借鉴和帮助。
1 轧钢机的主要故障-跑偏故障轧钢机在生产过程中由于工作环境恶劣,震动噪音大及各种不利因素的影响,轧钢机会发生自动横移的现象,其位移距离可达10—50mm,通常称为轧机跑偏现象。
这是轧钢机生产过程中经常发生的状况,频率可达每月30~50次。
跑偏故障发生后,轧机跑偏会造成跑槽和导卫之间横向错位,使轧件不能顺利进入导卫,在连续的轧钢过程中轧件不能由出口导卫进入下一跑槽,造成废钢事故。
此时必须停机,重新调整轧辊位置,这样会严重影响轧钢的生产效率和质量。
为此跑偏故障是轧钢过程中的主要故障之一[2-3],是影响轧钢生产的关键因素。
2 跑偏现象的分析与改进2.1 跑偏故障产生的原因轧钢机通常是由多台轧钢机组成的连续生产线。
如西安轧钢厂的中精轧钢机为由12架轧机组成的线材生产线,当轧辊磨损或轧制品种变换时,必须将轧辊从横向拆卸下来,进行更换。
为了减少停机时间,加快轧辊的更换和调整速度,现代化的轧机都配有如图1所示的液压换辊装置,利用平移油缸可快速地将换辊小车和轧座、轧辊整体移出进行更换,然后返回工作位。
为保证轧钢过程中生产的稳定性和可靠性,换辊和复位后应该将机座牢固地固定起来,为此采用了图2所示的加紧油缸进行复位后的锁紧。
从理论分析可知,当精轧机组平移油缸,活塞的直径D1为100mm,活塞杆的直径600mm,最大压强为14MP,其平行推力为:F精左=109.9kNF精右=70.3kN中精轧机活塞直径D2为140mm,活塞杆直径90mm时,F中精左=215.4kNF中精右=136.4kN而夹紧油缸所施加的横向夹紧力为80KN,摩擦角为10度,摩擦系数取u=0.2时,施加在轧钢机上的夹紧力为:F精夹=184.3kNF中精夹=276.5kN此时,精轧机组和中精机组的夹紧力远大于平移油缸的推力,即F精夹=184.3 kN F精左= 109.9kNF中精夹= 276.5 kN F中精左=215.4kN只要夹紧缸工作正常,轧钢机组可以牢靠地固定相应的位置上不发生轧机跑偏现象,图3所示为加紧油缸工作时的受力分析。
高速线材精轧机滚动导卫常见失效原因分析及解决措施

高速线材精轧机滚动导卫常见失效原因分析及解决措施刘可可(线材事业部)0前言线材事业部二高线精轧机组采用10架次45度无扭轧机机型,并在椭圆轧件进入圆孔型时使用滚动导卫,滚动导卫的作用是保证轧制过程中轧件的顺利咬入和轧制的顺利进行。
目前,二高线Ф6. 5mm热轧盘圆的成品速度可达85m/s以上,精轧机组的导卫导辊也在超高速下运行,因此对滚动导卫的要求也较高,对滚动导卫的维护和保养尤其重要。
1精轧机滚动导卫失效原因分析滚动导卫由导卫盒、导卫板、支臂、导辊、轴承、鼻锥等部件组成。
造成滚动导卫失效的主要原因是导辊、轴承、导卫板等零部件过早失效。
其中以导辊失效最为常见,轴承次之,导卫板失效极少发生。
故以下主要侧重分析导辊和轴承过早失效的原因,并提出改进措施,从而保证滚动导卫的使用寿命有大幅度的提高。
1.1水冷导辊在轧制中直接与轧件接触,此时轧件温度在1000℃以上,导辊过热会加速其磨损,通过热传导使导辊内的轴承受热膨胀,造成轴承烧毁,无法正常使用,所以导辊的冷却非常重要。
1.1.1冷却水水压控制不当相关研究证明,冷却水水压一般应维持在0.5 MPa[1]。
如果水压太大,当冷却水打到导辊表面时会被弹出来,起不到好的冷却效果;当冷却水水压小于0.5MPa时,由于水压小,冷却水无法冲破导辊表面蒸汽膜,造成冷却效果不佳。
1.1.2冷却水水质有问题由于水中含有油和其他杂质,造成导辊冷却不够,引起导辊过热,加速其磨损。
不仅如此,通过热传导使轴承受热膨胀,造成轴承烧毁,使导卫无法继续正常使用。
1.1.3冷却水喷射口堵塞冷却水在循环使用的过程中,水中含有大颗粒的杂质,造成喷射口堵塞,或者轧件表面脱落的氧化铁皮堵塞喷射口,引起导辊冷却不充分。
无论以上是哪个原因造成导辊冷却不好,都会引起导卫使用寿命降低,因此一定要加以重视,找出解决措施。
1.2油气油气是保证导辊轴承正常工作的一个关键因素,它直接作用于轴承,以满足轴承润滑的需要。
- 1、下载文档前请自行甄别文档内容的完整性,平台不提供额外的编辑、内容补充、找答案等附加服务。
- 2、"仅部分预览"的文档,不可在线预览部分如存在完整性等问题,可反馈申请退款(可完整预览的文档不适用该条件!)。
- 3、如文档侵犯您的权益,请联系客服反馈,我们会尽快为您处理(人工客服工作时间:9:00-18:30)。
1.精轧机组工艺调整应注意的问题有:
(1)精轧机组的工艺调整一般只调整第一架次和成品架次,其他架次不得随意调整,其原因有两个:1)动了其中某一架的辊缝,会破坏各架间的微张力关系,造成产品尺寸波动;
2)滚动导卫的导辊开口度是根据样棒精确调整的,若放大某一架辊缝,会造成来料变大,导致导辊使用寿命降低甚至损坏导轮而出废品;若收小某一道次辊缝,会造成来料变小,导轮夹持不稳,会出现倒钢现象。
(2)当成品尺寸高度过大,宽度也过大时,应先调第一架轧机,后调成品轧机;第一架、成品架轧机的累计调整量不得超过0.3mm。
(3)当发现钢坯表面质量不好时,应停机检查辊环、导卫中有无异物。
2.精轧机组生产工艺的特点有:
采用固定道次间轧辊转速比,以单线微张力无扭转高速连续轧制的方式;
进行合理的孔型设计和精确的轧件尺寸计算,配合以耐磨损的轧槽;
采用较小直径的轧辊;以椭—圆孔型系统轧制多规格产品;
机架中心距尽可能地小,以减轻微张力对轧件断面尺寸的影响;
精轧前及精轧道次间进行轧件穿水冷却,进行轧件变形温度的控制。
3.
精轧机组调整的方法
在轧制过程中,应根据取样的尺寸及烧木印的情况来调整精轧机。
一般只调整精轧机第一架和最后一架,而其他架次不得随意调整。
下面举例说明:
(1)成品垂直直径较大、水平直径稍小时,压小成品架次的辊缝;
(2)成品垂直直径较小、水平直径正好时,放大成品架次的辊缝;
(3)成品垂直直径正好、水平直径较大时,压小第一架次的辊缝;
(4)成品垂直直径正好、水平直径较小时,放大第一架次的辊缝。
如经过上述调整后仍达不到要求,应检查前面机组的来料尺寸,放大或缩小前面机组的最末架次的辊缝。
一般精轧机第一架和最后一架轧机的辊缝累计调整量不得超过
0.3mm。
4.精轧机组机架间堆钢的原因有:
(1)导卫粘钢;
(2)导轮不转或轴承烧坏;
(3)轧件劈头;
(4)导卫或辊环装错;
(5)辊缝设定不当或来料尺寸不合要求;
(6)导卫未紧固;
(7)压辊键断使辊片松动;
(8)辊片碎;
(9)轧辊轴轴瓦磨损或破裂。
6. 精轧机各机架间采用活套的作用是:
(1)缓冲金属流量的变化,给控制调整以时间,并防止成叠进钢,造成事故。
(2)调节各架的轧制速度以保证连轧常数,当各种工艺参数产生波动时发出信号和命令,以便快速进行调整。
(3)带钢能在一定范围内保持恒定的小张力,防止因张力过大引起带钢拉缩,造成宽度不均匀甚至拉断。
(4)精轧最后几个机架间的活套,还可以调节张力,以控制带钢厚度。
活套支持器主要有电动、气动、液压及气—液联合4种。