轻压下技术在高碳钢方坯连铸生产应用中的参数选取
轻压下技术在连铸中的应用及研究
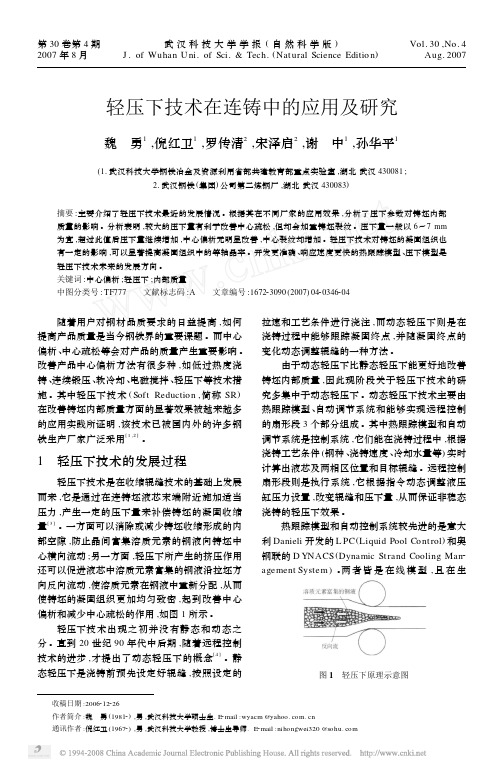
T H EMAL TRAC KIN G[6 ] ,它们也能模拟连铸过 好[8 ,9 ] 。
程中的非稳态情况 ,实时地给出液相穴末端位置 和液相穴的形状 ,但只是离线模型 。
2 轻压下技术的应用效果
扇形段技术最先进的是奥钢联的 SMA R T
轻压下技术在板坯连铸中应用非常普遍 ,在
扇形段和西马克公司的 Cyberlink 扇形段 。其中 方坯连铸中特别是大方坯连铸中的应用也得到了
由于动态轻压下比静态轻压下能更好地改善 铸坯内部质量 ,因此现阶段关于轻压下技术的研 究多集中于动态轻压下 。动态轻压下技术主要由 热跟踪模型 、自动调节系统和能够实现远程控制 的扇形段 3 个部分组成 。其中热跟踪模型和自动 调节系统是控制系统 ,它们能在浇铸过程中 ,根据 浇铸工艺条件 (钢种 、浇铸速度 、冷却水量等) 实时 计算出液芯及两相区位置和目标辊缝 。远程控制 扇形段则是执行系统 ,它根据指令动态调整液压 缸压力设置 ,改变辊缝和压下量 ,从而保证非稳态 浇铸的轻压下效果 。
1 轻压下技术的发展过程
轻压下技术是在收缩辊缝技术的基础上发展 而来 ,它是通过在连铸坯液芯末端附近施加适当 压力 ,产生一定的压下量来补偿铸坯的凝固收缩 量[3] 。一方面可以消除或减少铸坯收缩形成的内 部空隙 ,防止晶间富集溶质元素的钢液向铸坯中 心横向流动 ;另一方面 ,轻压下所产生的挤压作用 还可以促进液芯中溶质元素富集的钢液沿拉坯方 向反向流动 ,使溶质元素在钢液中重新分配 ,从而 使铸坯的凝固组织更加均匀致密 ,起到改善中心 偏析和减少中心疏松的作用 ,如图 1 所示 。
轻压下 技 术 出 现 之 初 并 没 有 静 态 和 动 态 之 分 。直到 20 世纪 90 年代中后期 ,随着远程控制 技术的进步 ,才提出了动态轻压下的概念[4] 。静 态轻压下是浇铸前预先设定好辊缝 ,按照设定的
连铸方坯动态轻压下位置

连铸方坯动态轻压下位置张松;杨彦宏【摘要】为准确确定铸坯凝固末端的位置,合理选择压下区域,为实施动态轻压下提供有效技术手段,利用数值模拟方法计算某炼钢厂2#铸机连铸方坯中温度场,用传热模型分析了45#钢在某工艺下的铸坯温度分布图.固相率0.3为轻压下初始点,压下区间总长度为10 m且拉速0.76 m/min时的压下量为0.7 mm/m.【期刊名称】《辽宁科技大学学报》【年(卷),期】2010(033)002【总页数】4页(P132-135)【关键词】连铸方坯;温度场;动态轻压下【作者】张松;杨彦宏【作者单位】辽宁科技大学,材料科学与冶金学院,辽宁,鞍山,114051;辽宁科技大学,机械工程与自动化学院,辽宁,鞍山,114051【正文语种】中文【中图分类】TF777在连铸生产中,板坯内部一般都会存在中心偏析、中心疏松及内裂等缺陷,影响了铸坯内部质量。
抑制内部缺陷问题最有效且经济的方法是采用轻压下技术[1]。
凝固末端的轻压下技术始于20世纪70年代末,是在辊缝收缩的基础上发展起来的。
在铸坯凝固末端,对铸坯施以2%-3%的压下量,以阻止凝固末端富集偏析元素的钢液向下流动,减少中心偏析[2]。
动态轻压下技术已成为现代连铸机关键技术的重要组成部分[3]。
在铸坯凝固过程中,坯壳至中心分为固态、固-液态、液-固态和液态四个区域。
由于选分结晶,在铸坯凝固末端的残余液相中含有的溶质浓度很高,当这些残余液相在铸坯中心部位凝固时,会产生很严重的中心偏析[4]。
在铸坯凝固过程中,如果柱状晶发达,会在凝固末端形成“搭桥”,阻碍上游钢液向下游动,凝固末端的残余液相不能被上游溶质浓度低的钢液稀释,就会在铸坯中心形成一条偏析带。
同时,残余液相在凝固末端急速凝固时,会急剧收缩,产生缝隙,如不能得到钢液的补充,就会产生疏松[5]。
轻压下的目的,就是要通过机械压下来补偿铸坯凝固后期体收缩,抑制枝晶间浓化钢水向中心富集,减轻或焊和中心疏松,减轻中心偏析。
试析炼钢—精炼—连铸工艺生产高碳钢的质量控制
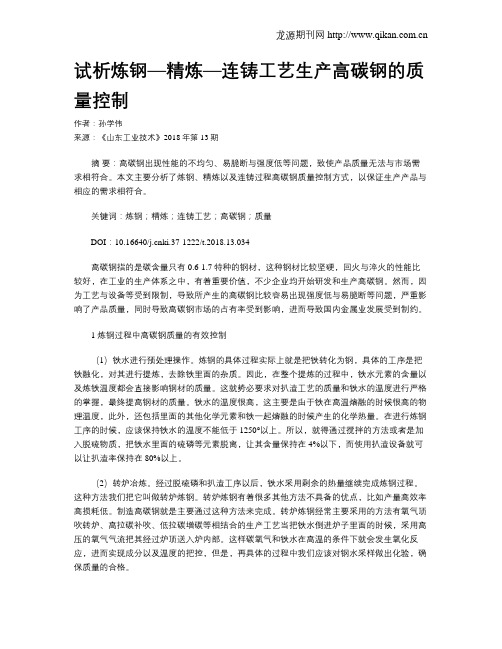
试析炼钢—精炼—连铸工艺生产高碳钢的质量控制作者:孙学伟来源:《山东工业技术》2018年第13期摘要:高碳钢出现性能的不均匀、易脆断与强度低等问题,致使产品质量无法与市场需求相符合。
本文主要分析了炼钢、精炼以及连铸过程高碳钢质量控制方式,以保证生产产品与相应的需求相符合。
关键词:炼钢;精炼;连铸工艺;高碳钢;质量DOI:10.16640/ki.37-1222/t.2018.13.034高碳钢指的是碳含量只有0.6-1.7特种的钢材,这种钢材比较坚硬,回火与淬火的性能比较好,在工业的生产体系之中,有着重要价值,不少企业均开始研发和生产高碳钢。
然而,因为工艺与设备等受到限制,导致所产生的高碳钢比较容易出现强度低与易脆断等问题,严重影响了产品质量,同时导致高碳钢市场的占有率受到影响,进而导致国内金属业发展受到制约。
1 炼钢过程中高碳钢质量的有效控制(1)铁水进行预处理操作。
炼钢的具体过程实际上就是把铁转化为钢,具体的工序是把铁融化,对其进行提炼,去除铁里面的杂质。
因此,在整个提炼的过程中,铁水元素的含量以及炼铁温度都会直接影响钢材的质量。
这就势必要求对扒渣工艺的质量和铁水的温度进行严格的掌握,最终提高钢材的质量。
铁水的温度很高,这主要是由于铁在高温熔融的时候很高的物理温度,此外,还包括里面的其他化学元素和铁一起熔融的时候产生的化学热量。
在进行炼钢工序的时候,应该保持铁水的温度不能低于1250°以上。
所以,就得通过搅拌的方法或者是加入脱硫物质,把铁水里面的硫磷等元素脱离,让其含量保持在4%以下,而使用扒渣设备就可以让扒渣率保持在80%以上。
(2)转炉冶炼。
经过脱硫磷和扒渣工序以后,铁水采用剩余的热量继续完成炼钢过程。
这种方法我们把它叫做转炉炼钢。
转炉炼钢有着很多其他方法不具备的优点,比如产量高效率高损耗低。
制造高碳钢就是主要通过这种方法来完成。
转炉炼钢经常主要采用的方法有氧气顶吹转炉、高拉碳补吹、低拉碳增碳等相结合的生产工艺当把铁水倒进炉子里面的时候,采用高压的氧气气流把其经过炉顶送入炉内部。
高碳钢连铸方坯质量控制

高碳钢连铸方坯质量控制蔡开科1.前言高碳钢制品入钢轨,硬线,钢丝等广泛应用于国民经济各个部门。
对高碳钢制品要求是:抗拉强度高,可承载较重的震动载荷承载能力大,使用安全可靠在高速条件下工作,运转平稳有良好的抗压性,耐磨性,耐腐蚀性等目前高碳钢生产有两件工艺:BOF(EAF)-LF(VD)-bloom大方坯BOF(EAF)-LF-Billet小方坯不管那种工艺,为获得高质量的产品,必须得到高质量的连铸坯。
(1)高的洁净度,非金属夹杂物类型,数量,尺寸分布如表1表1 洁净度要求硬线钢由于夹杂易造成的冷拔断裂如图1图1 夹杂物所致冷拔断裂重轨钢,滚珠钢由于脆性夹杂产生疲劳裂纹而断裂(2)铸坯良好的低倍结构要紧是指中心缺陷(锻孔,疏松,中心偏析)。
硬线钢的杯锥状断裂(图2)是由中心偏析所致图2 杯锥状断口硬线钢劈裂状断口(图3)要紧是由中心疏松缩孔引起的。
图3 劈裂状断口重轨钢由于中心偏析(C.S)而产生轨腰的断裂(图4)图4 钢轨形貌2.铸坯中夹杂物操纵当钢水凝固成固体后,铸坯中夹杂物数量就无法改变了。
因此铸坯中夹杂物决定于炼钢-精炼-连铸的全过程。
炼钢是一个氧化过程,钢中夹杂物可用总氧T[O]来评判:T[O] = [O]D + [O]I出钢时:钢水中[O]I→O T[O] = [O]D=a[O]脱氧合金化后:[O]D(a[O])→O T[O] = [O]I由此,可用总氧T[O]来表示钢的洁净度,也确实是夹杂物水平。
为使钢中夹杂物少,必须操纵钢T[O],为此(1)降低[O]D,转炉终点a[O](2)降低[O]I,脱氧(夹杂物工程),精炼(3)防止钢水再污染:连铸过程2.1转炉终点氧操纵转炉终点a[O]是产生夹杂物的源头。
重点a[O]决定于:[C]终渣中(FeO)钢水温度图5 转炉终点钢中[C]与a[O]关系关于中高碳钢转炉终点操纵方法:低拉碳增碳法高拉碳补吹法两种方法结果比较于表2表2 低拉碳与高拉碳结果比较由表可知高拉碳法特点:增C量小,成品C波动小终点a[O]低对铁水S,P要求研低拉碳法特点:对铁水S,P要求可放宽些有利于脱S,P终点a[O]高增C量大,碳粉收得率不稳,成品C波动在±0.05%以上两种方法各有优缺点,各厂依照具体条件决定采纳哪种方法。
连铸坯动态轻压下的压下参数分析

第3卷第4期材 料 与 冶 金 学 报V o l .3N o .4 收稿日期:2004-06-18. 作者简介:林启勇(1980-),男,重庆梁平人,硕士研究生,E -m a i l :s y q i y o n g@s i n a .c o m ;朱苗勇(1965-),男,浙江诸暨人,东北大学教授,博士生导师.2004年12月J o u r n a l o fM a t e r i a l s a n d M e t a l l u r g yD e c .2004连铸坯动态轻压下的压下参数分析林启勇,蒋欢杰,朱苗勇(东北大学 材料与冶金学院,辽宁沈阳110004)摘 要:简述了连铸坯动态轻压下技术,介绍了该技术的关键工艺参数即压下区间、压下量和压下速率。
通过对近年来国内外对压下模型研究结果的分析和讨论,预测了动态轻压下压下模型的研究方向.关键词:连铸;中心偏析;轻压下;压下参数中图分类号:T F777 文献标识码:A 文章编号:1671-6620(2004)04-0261-05A n a l y s i s o f r e d u c t i o n p a r a m e t e r s o f d yn a m i c s o f t r e d u c t i o n i n c o n t i n u o u s c a s t i n gL I N Q i -y o n g ,J I A N G H u a n -j i e ,Z HU M i a o -y o n g(S c h o o l o fM a t e r i a l s a n d M e t a l l u r g y ,N o r t h e a s t e r nU n i v e r s i t y ,S h e n y a n g 110004,C h i n a )A b s t r a c t :T h e d y n a m i c s o f t r e d u c t i o n t e c h n o l o g y a n d t h e k e y t e c h n i c a l p a r a m e t e r s o f s o f t r e d u c t i o n f o r c o n t i n u o u s c a s t i n g w e r e p r e s e n t e di nt h i s p a p e r .B y r e v i e w i n g a n da n a l y z i n g t h ev a r i a b l e s ,t h es o f t r e d u c t i o n m o d e l sa c h i e v e di n r e c e n t y e a r s ,t h et r e n df o ri n v e s t i g a t i n g t h er e d u c t i o n m o d e l w a s d i s c u s s e d .K e y wo r d s :c o n t i n u o u s c a s t i n g ;c e n t e r s e g r e g a t i o n ;s o f t r e d u c t i o n ;r e d u c t i o n p a r a m e t e r s 中心偏析和疏松是连铸坯的主要缺陷之一,它严重影响了钢材的性能,如焊接性能、拉拔性能.铸坯轻压下就是针对消除该缺陷的一种新技术,如图1所示.其机理为[1]:在连铸坯液芯末端附近施加压力产生一定的压下量来补偿铸坯的凝固收缩量.轻压下一方面可以消除或减少铸坯收缩形成的内部空隙,防止晶间富集溶质元素的钢液向铸坯中心横向流动;另一方面,轻压下所产生的挤压作用可促进钢液中的溶质元素进行重新分配,从而使铸坯的凝固组织更加均匀致密,起到改善中心偏析和减少中心疏松的作用.在实际生产过程中,浇铸速度和浇铸温度等条件的不稳定会引起凝固末端位置的变化,轻压下位置也随之改变.随着控制和液压技术的发展和应用,实现了跟踪凝固末端进行适时轻压下,即所谓的动态轻压下.图1 辊式轻压下示意图F i g .1 S c h e m a t i cd i a g r a mo f s o f t r e d u c t i o nb y r o I I i n g动态轻压下技术的主要工艺参数有压下区间、压下量和压下速率.只有合理确定这些参数值才能达到消除或减少铸坯中心偏析与疏松的目的.对此,已有大量的研究报道.本文将对有代表性的最新研究进行评述与分析.1 压下区间对压下区间的研究已经多年,目前一致认为,中心偏析和疏松发生在凝固末端的液固两相区内[2].凝固末端两相区如图2所示.在液相线温度(固相率f s =0)和固相线温度(f s =1)之间的区域为两相区.图2 凝固末端两相区示意图F i g .2 S c h e m a t i cd i a g r a mo fm u s h y zo n e i n t h ee n do f s o I i d i f i c a t i o n由图2可知,从f s =0到f s =1处,钢液中杂质元素含量越来越大.q 2区内的凝固收缩可以通过左端非浓化钢液的流动来补偿;q 1区内的凝固收缩时得到q 2区内的浓化钢液的补充.由于相邻柱状晶的二次晶臂开始并完成相互联结,补充钢液较困难.在p 区内残余浓缩钢液被枝晶网封闭起来,凝固收缩时将得不到前沿钢液的补充.因此,q 2区流动将不会造成中心偏析的形成,反而均匀了该区内的溶质分布;q 1区的收缩则将导致富集杂质元素钢液的集中,从而促进中心偏析的形成.p 区的凝固收缩因没有钢液的补充将形成疏松.T a k a h a s h i 和S u z u k i [3]等的研究指出q 1和q 2相分界处的固相率为0.3~0.4,而q 1和p 分界处的固相率为0.6~0.7,因此,最佳轻压下实施区间应在铸坯中心固相率0.3~0.7的位置(图2中的q 1区).但钢种不同,所要求的固相率也不同.一般来说,中碳钢为0.3~0.7;高碳钢为0.4~0.7.按美国专利4687047所述,铸坯实行轻压下的适宜部位,相当于从铸坯中心固相率为0.1~0.3之间到铸坯中心固相率达到流动极限固相率f s c (f s c 是指钢液达到流动极限时的固相率,一般的经验,普通碳素钢的f s c =0.6,低合金钢的f s c=0.65~0.75)之间的一段铸坯,当f s >f s c 时,钢液粘性很大,基本不会流动,若此时进行压下,很可能对内部质量产生有害影响.从生产实践来看,济南钢铁公司新引进奥钢联的新中厚板坯在压下区间为0.5~0.95,铸坯质量良好[4].芬兰的R a u t a r u u k k i 钢铁公司6号板坯上进行生产试验[5],钢种为w [C ]=0.088%的微合金钢,得出在浇铸210m m×(1250~1475)m m 尺寸时的最佳压下区间为0.3~0.9;在浇铸尺寸为210m m×1825m m 的最佳压下区间为0.15~0.8.台湾省中钢的大方坯连铸机生产表明,在0.55~0.75的区域进行压下能取得很好的效果[6].韩国浦项对S 82尺寸为250m m×330m m 的方坯实施压下的压下位置为f s =0.3~0.7的区域[7].对于压下区间目前没有一个定值,一般企业都是根据试验修正后取得最佳值.很显然该值和钢的成分、铸坯断面及生产设备有关.从生产实践得出的数据可以看出,板坯比大方坯的压下区间大,而且开始压下(f s 值大时开始,值小时结束)所对应的f s 值比方坯要大.这是由于p 区间如果也能轻微压下,则可以减少因凝固时未能得到补充的凝固收缩所形成的中心疏松.板坯的窄边坯壳较薄,温度较高,变形抗力较小,易实现轻压下;而方坯压下时坯壳较厚,温度较低,变形抗力大,压下难以实现.2 压下量与压下速率压下量要完全补偿压下区间内钢液在凝固过程中的体积收缩量,才能防止富集溶质钢液的流动.但是压下量过大会使铸坯内部产生裂纹,并使轻压下区夹辊受损.压下量过小,对中心偏析和疏松改善不明显.压下量大小必须满足三个要求:①能够补偿压下区间内的凝固收缩,减少中心偏析和中心疏松;②避免铸坯产生内裂;③压下时产生的反作用力要在铸机扇形段许可载荷范围内.压下速率是单位时间的压下量(m m /s ),最佳压下速率应和凝固速率一致,如果压下速率小于凝固速率,压下将不及时,凝固补偿不充分,仍出现中心偏析.同时,压下量对应于应变,压下速率对应于应变率,压下量和压下速率过大,将会导致铸坯的应变和应变率过大,一旦超过其许可范围就会形成裂纹.目前主要从铸坯高温物性、压下效率、压下量和压下速率等几方面开展研究.262材料与冶金学报 第3卷2.1铸坯高温物性铸坯高温物性包括随温度变化的弹性模量E、塑性模量、屈服极限σs、瞬时热膨胀系数α,以及铸坯在不同温度和变形条件下的临界应变值和临界应力值.它们是计算铸坯轻压下过程中位移、应力应变及判定内裂纹形成的基础.铸坯的受力来自两个方面:由自身温度不均匀产生的热应力和外加载荷产生的机械力.热应力的计算关键要了解铸坯在不同温度下的瞬时膨胀系数.只有明确了铸坯随温度变化的弹性模量和与温度和应变率相关的屈服应力,才能进行铸坯的应力应变计算.瞬时膨胀系数主要和含碳量有关,由实验测定.文献[8]中给出了在w[C]= 0.1%(参考温度t r e f=1495℃)和w[C]=0.7%(参考温度tr e f=1406℃)时的膨胀系数,如图3所示.图3碳质量分数为0.1%和0.7%时的平均热膨胀系数F i g.3T h e r m a I e x p a n s i v i t y v s t e m p e r a t u r ef o r0.1p c t a n d0.7p c t c a r b o n s t e e I s由图3可以看出,w[C]=0.1%的钢在发生包晶相变时体积发生明显变化,而w[C]=0.7%的钢的体积变化随温度变化不明显.许多研究者用实验所得数据回归出高温下钢的强度极限σB和弹性模量E随温度和化学成分的变化规律.一般情况下,钢的σB和E是随温度升高而降低的.它们与化学成分和温度t(℃)的关系表示如下[9]:σB=40140+640w[C]2-880w[S i]+170w[M n]-7680w[P]-1260w[S]-25.94t+0.0001726t2k P a(1) E=30230080+4209560w[C]-14120080w[C]2+ 2012890w[S i]-518690w[M n]-1176840w[P]-17064180w[S]-508950t+1.3524k P a(2)以上两式中的w[C]、w[S i]、w[M n]、w[P]、w[S]的单位为%.当铸坯超过弹性变形范围,将发生塑性变形.H a n等研究出了温度和应变率两个变量与应力的本构方程[10]:˙εP=A e x p(-Q/R T)[s i n h(βK)]1/m(3)σ=Kεn P(4)式中A、β、m为常数,εP为有效塑性应变,σ为应力,K为强度系数,n为变形强化系数,Q为变形能,R为摩尔气体常数.该公式和实际塑性变形测量结果很吻合.内裂纹敏感区在Z S T(Z e r o S t r e n g t h T e m p e r a t u r e)和Z D T(Z e r o D u c t i b i l i t y T e m p e r a t u r e)之间[11].在该区域(对应的两相区固相率约为0.99和0.8)内,铸坯的受力或变形超过一定程度时,将会产生内裂纹[12].常用临界应变作为裂纹形成的判据.不少学者研究了临界应变和一些相关变量(成分、应变率等)的关系[13].应变率和临界应变的关系如图4所示[12],临界应变和含碳量的关系如图5所示[14].图4应变率和临界应变的关系F i g.4I n f I u e n c e s o f s t r a i na n d s t r a i n r a t eo n f o r m a t i o no f i n t e r n a I c r a c k s从图4可以看出,对同一钢种质量分数分别为:C0.15%,M n0.6%,P0.02%,S0.012%)进行不同应变率实验,可以看出应变率越小,临界应变值越大,这可能与钢的变形太慢发生高温蠕变效应有关;随着应变率的增大,临界应变值急剧下降;当应变率下降到约3×10-4/s时,临界应变变化很小.图5中虚线为理论计算值[14],其余为实验值[13].可以看出,在w[C]=0~0.1%和0.17%~0.65%之间,临界应变是下降的;当w[C]=0.1%~0.17%之间,临界应变上升,这可能与发生包晶相变有关.2.2压下效率为了更好地确定压下量,使铸坯内部液芯的压缩量能满足凝固的收缩量,解决铸坯表面的压362第4期林启勇等:连铸坯动态轻压下的压下参数分析图5 含碳量和临界应变关系的计算值与实验值(在应变率为5×10-4/s 时)F i g.5 T h ec a I c u I a t e dc r i t i c a I s t r a i na s a f u n c t i o n o f c a r b o n c o n t e n t a t t h es t r a i n r a t eo f 5×10-4/s a I o n g wi t h t h em e a s u r e d f r a c t u r es t r a i n 下量不能全部传递到内部凝固末端的问题,提出压下效率概念,即:η=液芯厚度的减少量铸坯表面压下量(5)I t o 等[15]经过对不同形状的铸坯的轻压下试验,拟合出压下效率公式:η=e x p (2.36λ+3.73)×(R 420)0.587(6)式中R 为压下辊辊径,λ为铸坯形状指数.2.3 压下量和压下速率Y o k o y a m a [16]等对钢液凝固时的体积收缩率进行了研究,得出体积收缩率为4%.Z e z e [17]等人对液芯厚度与压下量、压下速率与压下量的相互作用对铸坯的质量的影响作了系统的实验研究,图6和图7是他们的研究结果.由图6可以看出,在压下量减少时,由于凝固收缩得不到充分补偿,仍有残存V 偏析.随着压下量增加,V 偏析不断减少.液芯厚度越大,所需压下量越大.当压下量大时,发生白亮带负偏析和逆V 偏析.当压下量过大时,将产生裂纹.同时可以看出液芯厚度过大(对应位置的两相区固相率很小或在液相区),压下已不起消除V 偏析作用,反而形成内部裂纹.由图7可知,在压下速率小于0.02m m /s 时,无论怎么增加压下量,也不能防止V 偏析,这是因为压下速率小于凝固收缩速率,来不及充分补充凝固收缩的缘故.同时,由于压下速率的增大导致应变率增加,相应的临界应变变小,从而上临界压下量减少.此外还可以看出,随着压下速率的增加,为防止V 偏析的必要压下量增加,但压下量区间变窄.图6 压下量和液芯厚度对V 偏析的影响(压下速率0.35m m /s)F i g .6 E f f e c t o f r e d u c t i o no nV -s e g r e ga t i o n a t r e d u c t i o n r a t eo f 0.35m m /s图7 压下速率和压下量对V 偏析的影响(液芯厚度32m m )F i g .7 E f f e c t o f r e d u c t i o n r a t eo nV -s e g r e ga t i o n a t I i qu i dc o r e t h i c k n e s s o f 32m m 从实际生产来看,芬兰的R a u t a r u u k k i 钢铁公司[5]在浇铸尺寸为210m m ×(1625~1825)m m 的低合金钢时的最佳压下量为1.5m m ,而且得出在压下率为1.00m m /m 以下,压下不会对铸坯表面质量产生影响.韩国浦项[7](大方坯)发现,随着压下量的增加,中心偏析不断降低,但压下量超过6m m 之后,中心偏析并无进一步改善.铸坯内部裂纹也是随着压下量的增加而增加,但在总压下量低于6m m 时,铸坯内部裂纹极其微小.综合这两方面的因素,合理的总压下量为6m m.具体的压下量和压下速率与钢种、铸坯断面及生产条件有关.462材料与冶金学报 第3卷3存在问题及讨论要很好应用或改进轻压下技术,必须要有相当的技术支持.虽然许多冶金工作者对此已进行了大量研究,但仍需在以下几方面作进一步的研究.3.1宏观偏析形成机理铸坯和钢锭凝固过程中,所有类型的宏观偏析只在固液混合区存在,而不是存在于固液共存区前端.绝大多数情况是因收缩、铸坯的几何形状、固体变形或者重力能引起枝晶间钢液的缓慢流动[2].在某些情况下,它可能是凝固前期固体运动的结果.但是,在实践中仍存在着如何理解宏观偏析和控制宏观偏析的问题.在这方面仍有更深入细致的工作要做.3.2两相区的本构关系钢在固态的应力和应变本构关系研究比较成熟.但对连铸过程中的凝固末端固液共存区(固相率fs从0到1所对应的区域)的应变与应力的关系研究很少.中心裂纹就是在该区域形成的,只有明晰了应力和应变的本构关系,才能精确地计算出凝固前沿的应力和应变,从而有效地控制其在临界范围内,不形成裂纹.3.3临界应力应变测定虽然众多的研究者测定了铸坯的临界应力和应变值,但由于实验方法和条件的差异,结果相差较大.为了能使测得的临界值成为评价裂纹敏感性及预测裂纹的判据,应当统一实验标准.要充分考虑实际连铸工况,尽可能地模拟凝固前沿的组织、温度分布及受力状态,使测得的临界值能够较真实地反映铸坯内裂纹的形成.3.4铸坯内部应力应变计算只有知道铸坯在实际复杂工况下的应力应变值,才能预测裂纹的形成.以前大多用经验或半经验公式进行计算,对铸坯断面和材料性质作了很多假设,这往往会忽略某些特殊而且很关键的局部应力与应变,这就需要用更准确的计算方法.有限元法在这方面有明显优势,以后须用该方法进行数值模拟,得出更准确的铸坯内部应力应变分布.4结语在改善产品中心疏松和偏析的诸多方法之中,动态轻压下技术将会占据重要地位.为了更好地应用和改进该技术,需对如下几个方面作进一步研究:宏观偏析形成的机理;两相区的本构关系;临界应力应变的准确测定;铸坯内部应力应变的计算.参考文献:[1]B y r n e C,T e r c e l l i C.M e c h a n i c a ls o f tr e d u c t i o ni n b i l l e tc a s t i n g[J].S t e e lT i m e sI n t e r n a t i o n a l,2002,26(9):33-35.[2]F l e m i n g sM C.O u r u n d e r s t a n d i n g o fm a c r o s e g r e g a t i o n:p a s ta n d p r e s e n t[J].I S I J i n t e r n a t i o n a l,2000,40(9):833-841.[3]S u z u k i K,T a k a h a s h i K.M e c h a n i c a l p r o p e r t i e s o f t h es l a b b i n g m i l l r o l l m a t e r i a l s a t r o o m a n d e l e v a t e d t e m p e r a t u r e s[J].T r a n s.I r o na n dS t e e l I n s t i t u t eo f J a p a n, 1975,61(3):371-387.[4]赵培建,韩洪龙.轻压下技术在济钢新板坯连铸机上的应用[J].工艺技术,2002,6:11-12.[5]武金波译.板坯动态软压下的最新成果[J].世界钢铁,2001,6:5-7,18.[6]董珍编译.关于高碳大方坯中心偏析的改善[J].冶金译丛,1998,1:44-48.[7]K u y n g S h i k O h.D e v e l o p m e n to f S o f t R e d u c t i o nf o rt h eB l o o mC a s t e ra tP o h a n g W o r k so fP o s c o[J].S t e e l m a k i n gC o n f e r e n c eP r o c e e d i n g,1995:301-308.[8]K e l l y J E,M i c h a l e k K P,O'c o n n o r T G,e ta l.I n i t i a ld e v e l o p m e n t o f t h e r m a l a n d s t r e s s f i e l d s i n c o n t i n u o u s l y c a s ts t e e l b i l l e t s[J].M e t a l l u r g i c a lT r a n s a c t i o n sA,1988,19A: 2589-2602.[9]闫小林.连铸过程原理及数值模拟[M].石家庄:河北科学技术出版社,2001.152-153.[10]H a n H N,L e e Y G,O h K H,e ta l.A n a l y s i so fh o tf o rg i n g o f p o r o u s m e t a l s[J].M a t e r i a l s S c i e n c e&E n g i n e e r i n g A,1996,206:81-89.[11]Y a m a n a k a A,N a k a j i m a K,Y a s u m o t o K,e ta l.N e we v a l u a t i o no fc r i t i c a l s t r a i nf o r i n t e r n a l c r a c kf o r m a t i o ni nc o n t i n u o u s c a s t i n g[J].L aR e v u ed eMe t a l l u r g i e,1992,89(7-8):627-633.[12]Y a m a n a k a A,N a k a j i m a K,O k a m u r a K,e ta l.C r i t i c a ls t r a i nf o ri n t e r n a lc r a c kf o r m a t i o ni n c o n t i n u o u sc a s t i n g [J].I r o n m a k i n g a n d S t e e l m a k i n g,1995,22(6):508-512.[13]M a t s u m i y aT,I t o M,K a j i o k a H,e t a l.A ne v a l u a t i o no fc r i t i c a l s t r a i nf o r i n t e r n a lc r a c kf o r m a t i o ni nc o n t i n u o u s l yc a s t s l a b s[J].T r a n sI r o na nd S te e lI n s t i t u t eo fJ a p a n,1986,26:540-546.[14]Y o u n g M W,T a e-J u n g Y,D o n g J S,e t a l.An e wc r i t e r i o nf o r i n t e r n a l c r a c k f o r m a t i o n i n c o n t i n u o u s l y c a s t s t e e l s[J].M e t a l l u r g i c a l a n dM a t e r i a l sT r a n s a c t i o n s B,2000,31B:779 -794.[15]I t oY,Y a m a n a k aA,W a t a n a b eT,e t a l.I n t e r n a l r e d u c t i o ne f f i c i e n c y o f c o n t i n u o u s l y c a s t s t r a n dw i t h l i q u i dc o r e[J].L aR e v u e d eM e t a l l u r g i e,2000,O c t o b r e:1171-1176.[16]Y o k o y a m aT,U e s h i m a Y,M i z u k a m iY,e t a l.E f f e c to fC r,Pa n dT i o nd e n s i t y a n d s o l i d i f i c a t i o ns h r i n k a g eo f i r o n[J].T e t s u-t o-H a g a n e,1997,83:557-562.[17]Z e z eM,M i s u m iH,N a g a t aS,e t a l.S e g r e g a t i o nb e h a v i o ra n d d e f o r m a t i o nb e h a v i o r d u r i n g s o f t-r e d uc t i o n o fu n s o l i d i f i e ds t e e l i n g o t[J].T e t s u-t o-H a g a n e,2001,87(2):71-76.562第4期林启勇等:连铸坯动态轻压下的压下参数分析。
动态轻压下技术在连铸中的应用
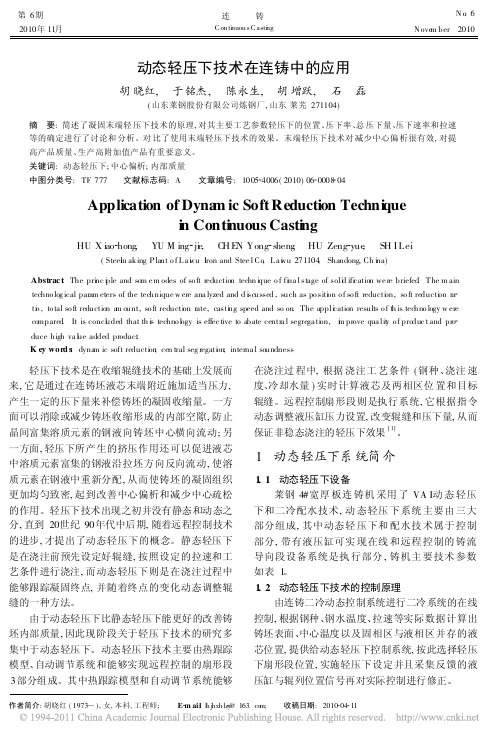
Abstrac t: The princ iple and som e m odes of so ft reduction techn ique o f fina l stage of solid ification we re briefed. T he m ain techno log ical param eters of the technique w ere ana lyzed and d iscussed , such as po sition o f so ft reduction, so ft reduction ra tio , to tal so ft reduction am ount, so ft reduction rate, casting speed and so on. The application results o f th is techno logy w ere compared. It is concluded that th is techno logy is effec tive to abate centra l segrega tion, im prove qua lity o f produc t and pro duce high va lue added product. K ey word s: dynam ic soft reduction; cen tral seg regation; interna l soundness
202. 00
a 50%
b 95%
10
辊缝值 结晶器上口 结晶器下口 垂直段入口 垂直段出口 矫直一段入口 水平一段入口 水平末段出口 压下量 /mm 出口实际辊缝值 压下位置固相率
连铸
表 3 250mm 厚辊缝及压下参数值 Table 3 Param eters of 250mm th ick roll gap and redu ction
关于连铸板坯轻压下位置的分析与研究

关于连铸板坯轻压下位置的分析与研究王国君,杜家恩(江西新余钢铁集团公司,江西 新余 338001)摘 要:轻压下技术对于提升板坯质量有着重要作用,位置的选择是轻压下技术的关键。
基于此,本文通过分析轻压下技术相关原理,展开了实验分析,通过实验计算和专家系统进行对比,在计算之后得出轻压下的位置。
在该位置上轻压板坯,对连铸坯的质量进行分析,发现板坯质量有明显的提升。
关键词:连铸板坯;轻压下技术;轻压下位置;实验研究中图分类号:TF777 文献标识码:A 文章编号:11-5004(2018)06-0261-2在连铸板坯的生产环节中,板坯出现中心偏析以及中心疏松问题十分常见,将会影响到钢材质量以及性能。
要想保证钢材的质量,必须要采取一些手段对疏松、偏析等问题进行控制和消除,最常使用的技术就是轻压下技术,轻压下技术需要使用在最佳位置上,才能保证技术的使用能够达到良好的效果,让钢材质量得到提升。
1轻压下技术1.1 概述在连续铸钢的过程中,钢坯使用液芯进行矫直的时候,为了能够得到没有缺陷的铸坯,需要使用对铸坯施加一定的压力。
这样能够避免凝固前出现搭桥,避免影响到钢水的输送,从而产生中心偏析的问题。
这项技术最早在二十世纪八十年代,在板坯支撑辊道从上至下收缩辊缝,从而避免板坯出现鼓肚,造成中心偏析问题的出现。
轻压下技术主要包括三种类型,第一种是轻压下技术,主要被应用在板坯以及大方板坯的铸坯液相穴的凝固末端;第二种是液芯压下技术,常被应用在薄板坯的连轧工艺中;第三种是铸轧技术,同样适合在薄板坯中使用。
从位置方面分类,轻压下技术分成全程和局部;从控制方式方面分类,轻压下技术分成动态压下和静态压下。
1.2 轻压下技术原理根据板坯中疏松、偏析以及缩孔的形成原理,在板坯凝固的最末端区域施加一定的压力,使得向下的压量让坯壳出现变形对两相区的凝固收缩量进行补偿。
一方面能够对中心孔隙进行消除,避免溶质液体向着铸坯出现横向的流动。
另一方面在轻压下作用下,积压作用能够破坏掉搭桥,让液相穴和凝固末端可以连通,实现补偿。
连铸板坯轻压下过程压下率参数的理论分析

图 1 铸坯横截面由液相区A、 中, , 两相区A . 2
单位时间的压下量, 等于压下率与拉速的乘积) , 以平均压下率、 平均压下速率来衡量轻压下的大
小和快慢程度。 22 模型求解 由式6 要确定压下率, 可知, 就必须首先确定
固相区A 组成; 〕 横坐标x 表示宽面方向, 纵坐标y 表示厚度方向, 垂直于纸面方向为: 方向, 即拉坯
d/z P p 整理后可得: M d= 汤= 拢+流, 0
J 静 警 d+ 0 o" P )y r .( ,、 J o x鄂Y d .
(z + JP),二 户)x d V,、。 U.、z. s, s一 : ‘ , z一 ( . ‘
() 3
P a` +k) () 。 二k) y“ c g au 。 c xa y> ・ 7 a (x ( T s a
板坯轻压下过程的基础上, 推出了压下 率理论模 型, 并结合实际条件, 研究了拉速和铸坯断面对连
铸板坯压下率的影响。
术 一 ’〕 其 动 轻 下 术, 成 现 之 〔’尤 是 态 压 技 已 为 代 一, 连 机重 铸 要标志之一〔‘ 压 “」 下率( 拉 一。 即 坯方向
单位长度的压下量,m m 是轻压下技术的核心 r/) t a 参数之一, 压下率过大将导致中心裂纹等缺陷, 过 小对改善中心偏析与疏松的效果不明显。目前, 有关压下率的研究主要集中 在工业试验和实验研
和凝固收缩的铸坯轻压下的必要压下率, 即:
液相区A ,
y
图 1 连铸坯 1 横截面内凝固区 / 4 域分布示意图
0} x 0器d ` f d _d, 2 " ( d ( ) H二 2 二 1 o ,y 6 Y
山 山
j }x x Op ,_ . 一d ,