车轮径向疲劳试验有限元仿真及疲劳寿命估算
汽车钢圈疲劳强度的有限元分析与寿命预测
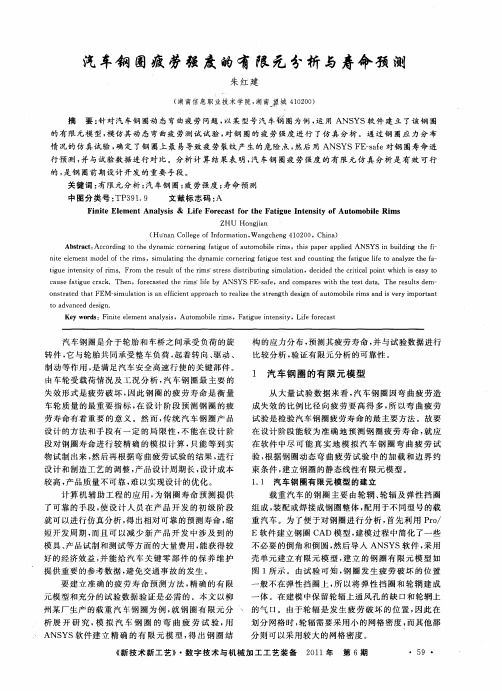
t u n e s t frms i e i t n iy o i .Fr m h e u to h i " te s d s rb tn i lt n,d cd d t e c i c l o n ih i a y t g o t e r s l ft e rms s r s it i u i g smu a i o e i e h rt a itwh c se s o i p
汽 车钢 圈是 介于 轮胎 和 车桥 之 间承受 负荷 的旋
构 的应 力分 布 , 预测 其疲 劳 寿命 , 并与 试验 数据 进行
比较分 析 , 验证 有 限元分 析 的可靠 性 。
转 件 , 与轮 胎共 同承受 整车 负荷 , 着转 向、 它 起 驱动 、 制动 等作 用 , 是满 足汽 车 安全 高速 行使 的关 键部 件 。
c u ef tg e c a k a s a i u r c .Th n o e a t d t e rms l e b e ,f r c s e h i " i y ANS E s f ,a d c mp r s wi h e td t .Th e u t e f YS F - a e n o a e t t et s a a h e r s l d m— s o s r t d t a n ta e h t FEM — i lto sa fi in p r a h t e l et e s r n t e i n o u o b l i sa d i v r p ra t smu a in i n e fce t p o c o r a i h t e g h d sg fa t mo i r n e y i o t n a z e m s m
由 车轮受 载 荷情 况及 工 况分 析 , 车 钢 圈最 主要 的 汽 失 效 形式 是疲 劳破 坏 , 此 钢 圈 的疲 劳 寿命 是 衡 量 因
基于有限元分析的铝合金车轮弯曲疲劳寿命的预测

第 l 2期
机 械 设计 与制 造
—
鱼 ±.
—=——— —— : =
8 一 5
文 章 编 号 :0 1 9 7 2 0 )2— 0 5一O 10 —3 9 (0 6 1 0 8 2
基 童 水光 闫胜 暂 张 响 徐 立 ( 浙江 大学 化 工机 械研 究所 C AD室 , 州 30 2 ) 杭 10 7
^
:
5
【 要】 摘 研究I DA 软 铝合 — ES 件下 金车 轮弯曲 试 疲劳 验力学 析模型的 立 数值 拟, 2 分 建 及其 模 结
合铝合金材料特性运用名义应力法预测车轮的弯曲疲劳寿命, 并与试验数据进行分析比较, 证明了 2 j 预测寿命与试验寿命基本一致, 也验证了 预测方法的可行性和有效性。 2 5 关键词: 车轮; 弯曲试验; 疲劳寿命; 有限元 2
有着 重要 的意义 。计算机辅助工程 的应用 ,为结构寿命 预测提 供了可靠 的手段 ,使设计人员在产品开发的初级阶段就可以进
行 仿 真分 析 。 出相 对 可 靠 的预 测 寿命 。 短 开 发 周 期 , 省 费 得 缩 节
用。要建 立准确 的疲劳寿命预测方法 ,精确的有限元模 型和充 分 的试验数据验证是必需的 ,国 内这方 面的研究仍有 限。本 文 就有 限元模型方面展开研究 , 以汽车车轮的弯曲疲劳试验为例 , 用 I E S软件建立精确 的有限元模型 , —D A 得出车轮结构 的应 力 分布 , 结合 名义应力 法预测其疲劳 寿命 , 与大量试验数 据进行 并 比较分析 , 验证该模 型的可靠性 。
{ aa s n o £ r li,w i r e a t a fa b n e i. n l i oe c s t k a l ys s i l eo e e hc po dt th w ys es la e cv f h v h e i ie d f te 5
铝合金车轮的有限元分析与疲劳寿命预测
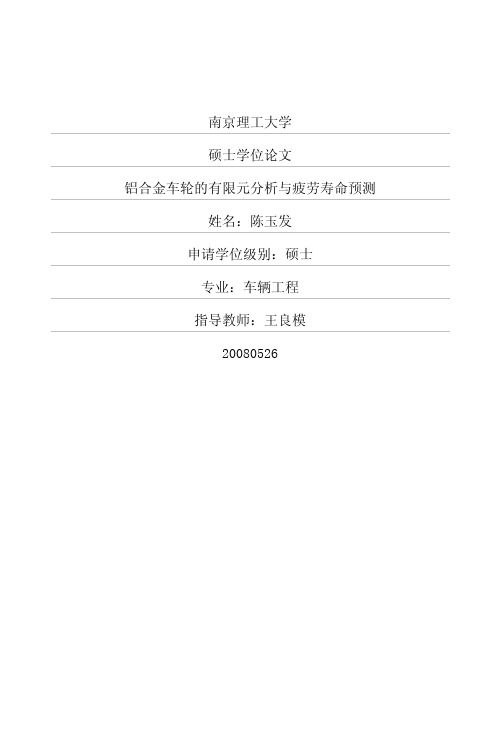
有限元分析软件的使用,将使铝轮产品的设计周期大大缩短,同时提高产品设计的精确程度,有限元的优化设计将推动整个铝轮行业的迅速发展,它彻底抑制了不合理、错误的结构设计,使铝轮的运转更加安全和迅捷.
6.学位论文周堃汽车用铝合金车轮低压铸造过程的数值模拟及其疲劳性能分析2009
铸造过程计算机模拟与仿真同结构有限元分析技术是信息科学、材料科学、工程力学及计算机图形学等各种学科的交叉科学,是先进制造科学的重要前沿领域。针对传统凭借经验设计制造车轮的过程中存在设计造型盲目性大、铸件成品率低、检测周期长的问题,本论文采用了计算机辅助造型技术及有限元分析方法,研究了车轮从初始造型设计到铸件生产过程数值模拟,最后到产品结构疲劳性能分析的全过程,这样能够迅速发现产品设计和生产中存在的问题,通过优化设计,提高产品成品率同时改善结构薄弱环节以缩短开发周期、降低成本,主要研究内容如下:
然而,车轮结构的弯曲疲劳试验和冲击试验均为动态试验,因此,有必要对其建立动态有限元分析模型,从而更准确地得到车轮结构在试验条件下的响应情况。首先,对车轮结构进行了弯曲疲劳试验和冲击试验条件下的模态分析,分析了车轮结构的模态振型和特点;然后,对车轮结构进行了旋转弯矩动态分析,发现在弯曲疲劳试验中车轮结构中的应力是非对称循环应力。针对两种弯曲疲劳试验装置工作原理的不同,对车轮结构进行了离心力分析,通过分析表明两种试验装置的试验结果是一致的。
能的有限元分析-机械设计与制造2009,""(5)
利用三维建模软件ug和有限元分析软件Ansys建立某款轿车铝合金车轮的弯曲疲劳试验力学分析模型.结合铝合金的材料特性,通过Ansys的结构分析模块研究螺栓预紧力、旋转离心力和试验弯矩对车轮结构强度的影响以及车轮结构的应力应变分布规律,找出应力集中区域.通过与实际试验结果的比较,验证了有限元分析结果的准确性.
汽车车轮双轴疲劳试验仿真方法
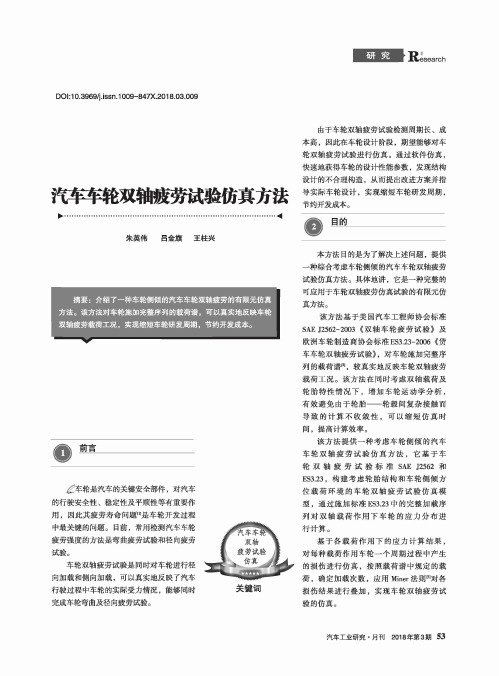
re se a rch D0I:10.3969/j.issn.1009-847X.2018.03.009汽轉轮双轴疲舰验仿真方法由于车轮双轴疲劳试验检测周期长、成 本高,因此在车轮设计阶段,期望能够对车 轮双轴疲劳试验进行仿真。
通过软件仿真,快速地获得车轮的设计性能参数,发现结构 设计的不合理构造,从而提出改进方案并指 导实际车轮设计,实现缩短车轮研发周期,节约开发成本。
►◄朱英伟吕金旗王柱兴®舰摘要:介绍了一种车轮侧倾的汽车车轮双轴疲劳的有限元仿真方法。
该方法对车轮施加完整序列的载荷谱,可以真实地反映车轮双轴疲劳载荷工况,实现缩短车轮研发周期,节约开发成本。
本方法目的是为了解决上述问题,提供 一种综合考虑车轮侧倾的汽车车轮双轴疲劳 试验仿真方法。
具体地讲,它是一种完整的 可应用于车轮双轴疲劳仿真试验的有限元仿 真方法。
该方法基于美国汽车工程师协会标准 S A E J2562-2003《双轴车轮疲劳试验》及 欧洲车轮制造商协会标准E S3.23-2006《货⑬紐车车轮双轴疲劳试验》,对车轮施加完整序 列的载荷谱p],较真实地反映车轮双轴疲劳 载荷工况。
该方法在同时考虑双轴载荷及 轮胎特性情况下,增加车轮运动学分析,有效避免由于轮胎——轮毂间复杂接触而 导致的计算不收敛性,可以缩短仿真时间,提高计算效率。
该方法提供一种考虑车轮侧倾的汽车 车轮双轴疲劳试验仿真方法,它基于车 轮双轴疲劳试验标准S A E J2562和£车轮是汽车的关键安全部件,对汽车的行驶安全性、稳定性及平顺性等有重要作 用,因此其疲劳寿命问题[1]是车轮开发过程 中最关键的问题。
目前,常用检测汽车车轮 疲劳强度的方法是弯曲疲劳试验和径向疲劳 试验。
车轮双轴疲劳试验是同时对车轮进行径 向加载和侧向加载,可以真实地反映了汽车行驶过程中车轮的实际受力情况,能够同时 完成车轮弯曲及径向疲劳试验。
关键词E S3.23,构建考虑轮胎结构和车轮侧倾方位载荷环境的车轮双轴疲劳试验仿真模型,通过施加标准E S3.23中的完整加载序列对双轴载荷作用下车轮的应力分布进行计算。
汽车车轮疲劳试验有限元仿真的研究现状

行业观察
汽车车轮疲劳试验有限元 仿真的研究现状
孙跃
(江苏大学东海机械汽配研究院)
摘要:为了在车轮产品的开发阶段,通过弯曲和径向疲劳试验来检验车轮的疲劳性能,同时节省开发费用和时间,一般采用
有限元仿真分析代替物理试验的方法。该文主要从钢制车轮冷变形、离心力、螺栓预紧力、轮胎与轮辋接触应力、充气压力等
9:%+'&(+; !" #$%&$ '# '&(' ')& *+',-.& /&$*#$0+"1& #* 2)&&3( ')$#.-) 4&"%,"- +"% $+%,+3 *+',-.& '&('( %.$,"- ')& %&5&3#/0&"' #* 2)&&3 /$#%.1'(6 +"% '# (+5& %&5&3#/0&"' 1#(' +"% ',0&6 *,",'& &3&0&"' (,0.3+',#" +"+37(,( ,( -&"&$+337 .(&% ,"('&+% #* /)7(,1+3 '&('(8 9),( /+/&$ 0+,"37 ,"'$#%.1&( +"% (.00+$,:&( ')& $&(&+$1) ('+'.( +"% /$#-$&(( #* *,",'& &3&0&"' (,0.3+',#" #* 2)&&3 *+',-.& '&(' *$#0 ')& +(/&1'( #* ('&&3 2)&&3 1#3% %&*#$0+',#"6 1&"'$,*.-+3 *#$1&6 4#3' /$&;',-)'&","- *#$1&6 1#"'+1' ('$&(( 4&'2&&" ',$& +"% $,06 ,"*3+',#" /$&((.$&6 &'18 <&('$,1'&% 47 0#%&3,"- +11.$+176 3#+%,"- +"% 4#."%+$7 1#"%,',#"(6 (,0.3+',#" $&(.3'( +"% /)7(,1+3 '&(' $&(.3'( #*'&" )+5& 1&$'+," %,**&$&"1&(8 =.--&(',#"( +$& /.' *#$2+$% '# (#35& ')& %&*,1,&"1,&(6 2),1) /$#5,%& ,0/#$'+"' $&*&$&"1& *#$ *.$')&$ $&(&+$1)8 <$= >-'?%:5$)0(3$ >)$$3@ /&+07,$ +$%+@ /010+$ $3$4$1+ %04,3&+0-1
全表面车轮径向疲劳试验的数值仿真及疲劳寿命分析
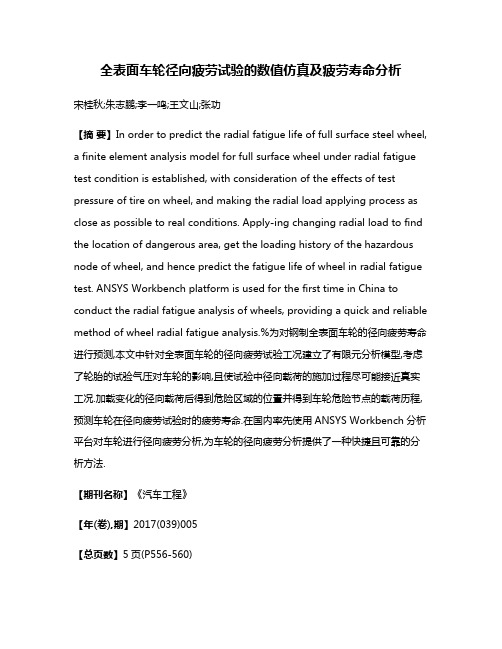
全表面车轮径向疲劳试验的数值仿真及疲劳寿命分析宋桂秋;朱志鹏;李一鸣;王文山;张功【摘要】In order to predict the radial fatigue life of full surface steel wheel, a finite element analysis model for full surface wheel under radial fatigue test condition is established, with consideration of the effects of test pressure of tire on wheel, and making the radial load applying process as close as possible to real conditions. Apply-ing changing radial load to find the location of dangerous area, get the loading history of the hazardous node of wheel, and hence predict the fatigue life of wheel in radial fatigue test. ANSYS Workbench platform is used for the first time in China to conduct the radial fatigue analysis of wheels, providing a quick and reliable method of wheel radial fatigue analysis.%为对钢制全表面车轮的径向疲劳寿命进行预测,本文中针对全表面车轮的径向疲劳试验工况建立了有限元分析模型,考虑了轮胎的试验气压对车轮的影响,且使试验中径向载荷的施加过程尽可能接近真实工况.加载变化的径向载荷后得到危险区域的位置并得到车轮危险节点的载荷历程,预测车轮在径向疲劳试验时的疲劳寿命.在国内率先使用ANSYS Workbench分析平台对车轮进行径向疲劳分析,为车轮的径向疲劳分析提供了一种快捷且可靠的分析方法.【期刊名称】《汽车工程》【年(卷),期】2017(039)005【总页数】5页(P556-560)【关键词】全表面车轮;径向疲劳;ANSYSWorkbench【作者】宋桂秋;朱志鹏;李一鸣;王文山;张功【作者单位】东北大学机械工程与自动化学院,沈阳 110004;东北大学机械工程与自动化学院,沈阳 110004;东北大学机械工程与自动化学院,沈阳 110004;山东通力车轮有限公司,诸城 262200;中国人民解放军65066部队二大队,沈阳 110004【正文语种】中文全表面车轮是一款新型的钢制车轮,较传统的钢制车轮具有外形美观、通风孔大等优点,本文中将针对某型号的全表面车轮进行研究。
大尺寸重载车用铝合金轮毂径向疲劳寿命预测
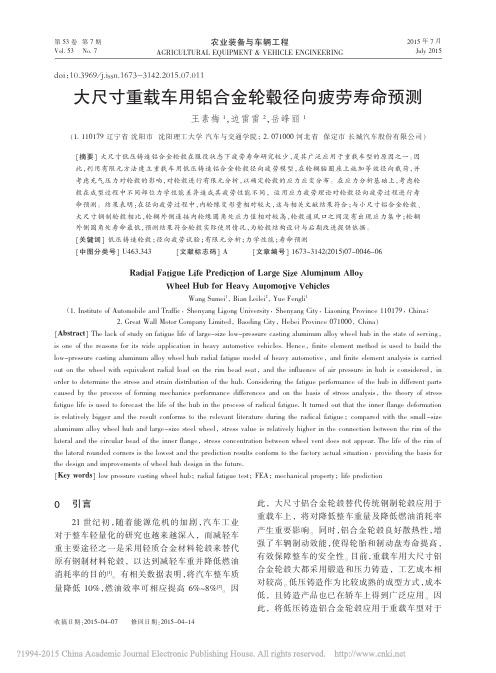
农业装备与车辆工程2015年0引言21世纪初,随着能源危机的加剧,汽车工业对于整车轻量化的研究也越来越深入,而减轻车重主要途径之一是采用轻质合金材料轮毂来替代原有钢制材料轮毂,以达到减轻车重并降低燃油消耗率的目的[1]。
有相关数据表明,将汽车整车质量降低10%,燃油效率可相应提高6%~8%[2]。
因此,大尺寸铝合金轮毂替代传统钢制轮毂应用于重载车上,将对降低整车重量及降低燃油消耗率产生重要影响。
同时,铝合金轮毂良好散热性,增强了车辆制动效能,使得轮胎和制动盘寿命提高,有效保障整车的安全性。
目前,重载车用大尺寸铝合金轮毂大都采用锻造和压力铸造,工艺成本相对较高。
低压铸造作为比较成熟的成型方式,成本低,且铸造产品也已在轿车上得到广泛应用。
因此,将低压铸造铝合金轮毂应用于重载车型对于收稿日期:2015-04-07修回日期:2015-04-14doi :10.3969/j.issn.1673-3142.2015.07.011大尺寸重载车用铝合金轮毂径向疲劳寿命预测王素梅1,边雷雷2,岳峰丽1(1.110179辽宁省沈阳市沈阳理工大学汽车与交通学院;2.071000河北省保定市长城汽车股份有限公司)[摘要]大尺寸低压铸造铝合金轮毂在服役状态下疲劳寿命研究较少,是其广泛应用于重载车型的原因之一。
因此,利用有限元方法建立重载车用低压铸造铝合金轮毂径向疲劳模型,在轮辋胎圈座上施加等效径向载荷,并考虑充气压力对轮毂的影响,对轮毂进行有限元分析,以确定轮毂的应力应变分布。
在应力分析基础上,考虑轮毂在成型过程中不同部位力学性能差异造成其疲劳性能不同,运用应力疲劳理论对轮毂径向疲劳过程进行寿命预测。
结果表明:在径向疲劳过程中,内轮缘变形量相对较大,这与相关文献结果符合;与小尺寸铝合金轮毂、大尺寸钢制轮毂相比,轮辋外侧连接内轮缘圆角处应力值相对较高,轮毂通风口之间没有出现应力集中;轮辋外侧圆角处寿命最低,预测结果符合轮毂实际使用情况,为轮毂结构设计与后期改进提供依据。
《2024年铝合金车轮双轴疲劳试验数值模拟研究》范文

《铝合金车轮双轴疲劳试验数值模拟研究》篇一一、引言随着汽车工业的快速发展,铝合金车轮因其轻量化、高强度、耐腐蚀等优点,正逐渐成为汽车制造行业的主流选择。
然而,在车辆使用过程中,车轮需承受来自双轴的复杂应力与疲劳载荷,因此对铝合金车轮的疲劳性能进行准确评估显得尤为重要。
本文将通过数值模拟的方法,对铝合金车轮双轴疲劳试验进行研究,以期为车轮的设计与制造提供理论支持。
二、铝合金车轮材料与结构特性铝合金车轮因其轻量化、高强度等优点,在汽车制造领域得到广泛应用。
其材料特性包括良好的塑形、较低的密度以及较高的抗腐蚀性。
此外,铝合金车轮的结构设计也需考虑其承受双轴应力与疲劳载荷的能力。
因此,在模拟研究过程中,应充分了解并考虑铝合金车轮的材料与结构特性。
三、双轴疲劳试验数值模拟方法为了研究铝合金车轮的双轴疲劳性能,本文采用数值模拟的方法。
首先,建立铝合金车轮的三维有限元模型,并利用材料力学性能参数对模型进行校准。
其次,根据实际双轴疲劳试验的工况,设定模拟试验的边界条件与载荷。
最后,通过有限元分析软件进行数值模拟,得出铝合金车轮在双轴疲劳试验过程中的应力分布、变形及疲劳寿命等情况。
四、模拟结果分析通过对铝合金车轮双轴疲劳试验的数值模拟,我们得到了以下结果:1. 应力分布:在双轴疲劳试验过程中,铝合金车轮的应力分布呈现出明显的非均匀性。
其中,轮辐与轮盘连接处、轮盘边缘等部位的应力较大。
这些部位在长期承受双轴应力与疲劳载荷的过程中,容易出现裂纹、断裂等损伤。
2. 变形情况:在双轴疲劳试验过程中,铝合金车轮的变形主要表现为弹性变形和塑性变形。
其中,弹性变形在加载过程中可恢复,而塑性变形则会导致车轮永久性的形状变化。
在设计中应考虑这些变形对车轮性能的影响。
3. 疲劳寿命:通过数值模拟,我们可以得出铝合金车轮在不同工况下的疲劳寿命。
结果表明,铝合金车轮的疲劳寿命受多种因素影响,如材料性能、结构设计、载荷大小及频率等。
在实际设计和制造过程中,应综合考虑这些因素以提高车轮的疲劳寿命。
- 1、下载文档前请自行甄别文档内容的完整性,平台不提供额外的编辑、内容补充、找答案等附加服务。
- 2、"仅部分预览"的文档,不可在线预览部分如存在完整性等问题,可反馈申请退款(可完整预览的文档不适用该条件!)。
- 3、如文档侵犯您的权益,请联系客服反馈,我们会尽快为您处理(人工客服工作时间:9:00-18:30)。
, LJ
针对 目前双摆角数控铣头研究现状中亟待解决的精度和扭
rlfrae hes utr ipoe n oeo r elt cue m rymet l w r t .
Ke y wor ds: he l Ri ; W e ; m Radi a i uet s ; al tg e tFEM i ul to Fa i uel e f sm a i n; tg f i
【 摘
要】 采用有限元分析方法, 建立汽车车轮有限元模型, 模拟车轮径 向疲劳试验施加合理的栽
荷及 边界条 件 。通过 分析 车轮 试验过 程 中的应力 变化 情 况 , 出高应 力集 中区域及其各 主应 力值 , 用 得 运
疲劳寿命计算理论及 A S S N Y 软件估算车轮 的疲劳寿命。 通过与车轮径向疲劳试验结果进行比较 , 结果
验进行仿真模拟及疲劳寿命估算 , 的是得到此车轮在动态径向疲 17 0 目 2 6 个单元和 5 23个节点口如 图 2 09 , 所示 。 不考虑轮辐和轮辋
★ 来稿 日 : 1— 8 0 ★基金项 目: 期 2 0 0—6 0 厦门市科技计划 高校创新项 目(5 2 2 o 3 4 ) 3 O z o 8 0 4
新型双摆角数控铣头。
矩兼顾问题 , 研究精度保证技术和采用提高扭矩 的方案 , 设计 出 参考文 献
() 1进行 了整体结构和传动方 案的分 析和论证 ;2采用力 ()
矩电机与蜗轮蜗杆驱动方式 , 优化传 动链配置 , 达到大传动 比、 高 精度传 动 ;3 建立精度分析数学模型 , () 确定驱动扭矩 算式 , 通过 优化参数配置提高铣头精度和转矩 ;4 分析加工过程铣头精度状 () 况, 进行了铣头体刚度分析并进行结构优化 ;5设计的双摆角数 ()
第 6期
2 1 年 6月 01
文章编号 :0 13 9 (0 10 — 0 7 0 10 — 9 7 2 1 )6 0 2 — 3
机 械 设 计 与 制 造
Ma h n r De i n c iey sg & Ma fc u e nu a t r 2 7
车轮径 向疲劳试验有限元仿真及疲 劳寿命估算 术
节 点 的方 式 。车 轮轮辋 的材料 为 R L 8 C 3 0钢 ; 辐 的材料 为 如 图 4所示 , 轮 通过车轮一圈的旋 转分 析 . 高应力区域 出现在通风
S 0 钢, W4 0 强度极限为 = 9 MP , 5 0 a屈服极 限为  ̄= 6 M a对称 孔边缘 A、 C、 四个位置处 , 中, ,4 0 P , B、 D 其 A点处的应力最高 , 其当量 5 MP 。 B C D四个位 置即为 弯曲疲劳极限 由公式 = 80 3 计算得 = 9 .MP 。 3+. 4 2 1 a 分 应力达到 2 6 a据此预测通风孔边缘 A、 、 、 7 析计算时材料 的弹性模量取 为 E 20 85 a = . e MP ,泊松 比取 为 = 车轮 的危险点 , 6 与车轮径向疲 劳试验结果基本吻合 , 如图 5所示。 03质量密度取 p 78 3  ̄ _, =. k m。 E
2车轮 的有 限元模型建立
该 型无 内胎车 轮钢 圈 的轮辐 与 轮辋厚 度分 别为 7 m和 a r
作用m 随着我国汽车工业整体水平的提高, 。 以及对汽车的行驶速度 21车轮有限元模型 . 与载荷 的大幅度提高 , 对车轮的质量要求也越来越高。一般意义上 m, l 所示。运用有限元分析软件 A S S建立车轮 的实 NY 的车轮包括轮胎和钢圈两部分 ,研究的是某车轮厂生产 的某 型号 1m 如图 1 采用 S l 9 od 5单元对车轮进行 网格划分 , i 分网后模型共有 1。 C无内胎车轮钢圈。采用 A S S 5D N Y 软件对该车轮的径向疲劳试 体模 型,
载荷和汽车负载。 气压载荷分 为 2部分施a : 1作用在整个轮辋 n()
表面的内压;2作用在钢圈两侧沿圆周均布 的侧向载荷[ () 3 1 。 试验 中车轮的汽车负载等效 于地 面对 轮胎的反作用 力 , 通
图 , 疲 劳 试验 中车 轮 裂 纹位 置
4车轮疲劳寿命估算
名义应力法是 以材料或零件的 S N曲线为基础 ,对 照零件 -
ata c in cak, esme oft eleeau i n ew el rele lo teea - culoaos rcsiit a frai i v ao adt he’ t i. l hs p lt f o tsh u g f lt n h S u fA f
me o ,n esn l Zas ad b u d r o dt n r p l d b i uaigte rda f t u et t d a d rao a e od o n ayc n io saea pi ysm l n a il ai e t . h b n i e t h g s T ru ha a zn ec ag rs i e rcs o h e s n ,i t s p s i so ea tm - ho g l igt h eo s es nt o esf w elet g hg s es oio t uo o n y h n ft h p t i h r tn f h bl w e l n r c a s essteotie , e v u e te ai elewt e r n N Y i h e a dp i il t se ; ba d t nea a s h t g i i t oya dA S Ss e n p r l f n h lt f u f hh C m aigw t ter i i ets rsl is o sta te o p r i h a af g et eut t h w t h 劲 s es oio ecni e t i e n h d l au t , h t s p st n a o s tn wt t r i r s s hh
颜 伟泽 郝艳华 黄致 建 蒋万标
( 华侨 大学 机 电及 自动化学 院 , 泉州 322 ) 60 1
F EM i lt n f e l a il a i u s n a iu f v la i n smu a i or o wh e da t e t ta d f t e le e au t r f g e g i o Y N We—e H O Y n h a H A G Z ij n J N n ba A iz , A a - u , U N h-i ,I G Wa— io a A ( o eeo ca i l n ier ga dA tm t n H aioU i ri , u nh u3 2 2 , hn ) C l g f l Meh nc gn ei n uo ai , u qa nv sy Q a zo 6 0 C ia aE n o e t 1
一
结
H
和重复定位精度分别达到 1 5。其大功率 、 0和 ” 大扭矩、 高精度的
特性可极大扩展五轴联动机床加工能力范围。
[] 1 丁雪生. 欧洲双主轴加工中心简介世 界制造技术与装备市场, 0 : ) 2 5( . 0 2 [] 2 赵妙霞 , 郑玉巧 , 胡世军 , 工进花. 机床传动链误差对齿轮加工精度 的 影 响及控制. 工业科技 ,0 5 6 :5 4 . 2 0 ( )4 - 7 [] 3 徐峰 , 李庆祥精密机械设计 京: E 清华大学出版社 , 0 : 22 5 2 5 1 - 1. 0 2 [] 4 成大先. 机械设计手册. : 北京 化学工业 出版社 , 9 (3 :9 . 1 3 1 )2 6 9 [ ] ・a e ・ kba v ・ re f t l et n o eh i ef hm n i 5 DK t , V o r oi S vyi e i n ot l cn u s r ao iM u t c u o n lg c r t q o u d rb t・ unlfnel etn R bt s ytm .0 33 ()1 7 1 1 oos o raoItlgn ad o oi S s s20 .72 :1— 4 . J i c e [] ・u oroi・i dl cm tn ya i ,aitcn oad pl 6 MV kba v Bp al 0 o 0dnmc sbl , t l ap- t c e 0 i st i or n y i
控铣头 A C 、 轴额定进给扭矩均达到 30N , 00 m 驱动系统定位精度
2 8
颜伟泽等 : 车轮径向疲劳试验有限元仿真及疲劳寿命估算
第6 期
装配焊接过程 中产生的初始应力 , 轮辐与轮辋之间的连接采用共 应力状态 , 以以当量应力 ( o ss作 为计算 应力进行研 究。 所 V nMi ) e
. 过轮胎 与轮辋 的接触 面间接 的传递 给轮辋 , 具体加载情况 , 图 41名义应力法估算车轮疲劳寿命 如
3所示。车轮在工作时轮胎与轮辋之间传递力的有效接触范围为
尺寸系数 、 面加工 系数 表 对称于车轮中轴线前后各 的范围内, 的大小为从 中间向两边 或结 构疲 劳危 险部位 的应 力集 中系数 、 力 结合疲劳损伤累积理论 , 计算零件的疲劳寿命 。 按余 弦规律减小 。由于车轮工作时的离心力对车轮强度的影响 及名义应力 , 微忽其微 , 予考虑。 不 为了有效模拟动态径 向试验工况 , 将车轮固 由于轮辐材料 S 0 W4 0为新型材料 , 没有现成 的材料 S N曲 - 所 - 当 0 定外载荷绕 车轮旋转 , 外载荷每转一个小角度写 出一个载荷步 。 线 , 以只能采用简化的方法估算 该材料的 S N曲线 。 Ⅳ 1 09 ; 盯 0时 1 ; (0 0) 由 该车轮的试 验汽 车负载  ̄ 6 6 0 轮胎内压  ̄ I a 轮胎与轮 时 , = . ^当 Ⅳ≥1 , = 一 当 Ⅳ= 13 1 时 , Ⅳ= 5 6 N, MP ,