耗差分析系统在电厂中的应用.
基于Web混合模式的火电机组耗差分析系统设计与实现1

基于Web混合模式的火电机组耗差分析系统设计与实现发表时间:2003-10-9作者:陈鸿伟[1],甄志[1],陈宇[2],杨中其[1],李永华[1]摘要:在市场经济条件下,安全运行、降低成本成为电厂提高经济效益,在竞争中立于不败之地的根本措施。
因此,应对机组热力系统进行优化管理。
火电机组耗差分析系统就是以降低及控制机组煤耗为最终目的动态管理方法。
1 系统总体结构随着火电厂自动化水平的不断提高,电力企业内部局域网建设更加健全。
目前实时信息管理系统通常采用2种体系结构:C/S(Client/Server)计算模式和B/S(Browser/Server)网络计算模式。
1.1 C/S体系结构在C/S结构系统中(图1),服务器部分负责数据的管理与派送、客户端请求的响应、系统共享资源的分配;客户端部分负责将从服务器端请求得到的数据和资源进行组织,按用户的要求将结果返回给用户。
C/S 结构采用请求与响应的应答模式,大部分数据的处理工作放在客户端进行,服务器端只作相应的数据应答。
1.2 B/S体系结构B/S模式是1种以Web技术为基础的新型模式,把传统C/S模式中的服务器部分分解成1个数据库服务器与1个或多个应用服务器(Web服务器),从而构成1个3层结构的体系(图2)。
用户可通过浏览具有一定交互功能的网页获取、发送信息,客户端将用户的处理请求提交给第2层的Web服务器。
第2层Web服务器启动相应进程响应用户的请求,动态生成代码,将处理结果嵌入其中,返回客户端;若用户请求中包括数据存取,Web服务器需与数据库服务器协同完成该处理工作。
第3层数据库服务器的任务类似C/S结构,负责管理数据库,协调不同Web服务器发出的SQL请求。
通过以上对C/S结构和B/S结构的分析和比较,可以得出以下结论:C/S结构具有交互性强、安全性高的特点;B/S结构具有安装简便,易于维护,扩展性好,信息共享度高的优点,所以在系统设计的过程中要考虑如下2条原则:(1)在安全性要求高,交互性强,处理数据量大,且地点固定、计算机分布范围小的情况下,应选用C/S模式;(2)在安全性和交互性要求不高,计算机分布范围广的情况下,可选用B/S模式。
耗差分析简介

机组煤耗的大小取决于机组热耗率、锅炉 效率、机组厂用电率三部分的数值。在火 电机组整个热力系统中影响机组热经济性 的因素虽然有很多,但都是通过引起以上 三个部分的变化来影响机组的煤耗。
• 锅炉风烟系统中排烟温度、排烟氧量、飞灰含碳量、炉 渣含碳量、燃煤灰分、燃煤发热量等参数的变化会引起 锅炉排烟损失q2、机械未燃尽损失q4、灰渣物理热损失 q6、入炉总热量Qr的变化,锅炉效率也随之变动,从而 造成机组煤耗的变化。 • 机组整个汽水系统(包括锅炉、汽轮机两部分)中主蒸 汽压力、主蒸汽温度、再热汽温度、再热汽压损、锅炉 减温水量、排汽压力、高压缸效率、中压缸效率、低压 缸效率、加热器上端差、加热器下端差、加热器旁路阀 泄漏量等参数的变化及高压加热器切除运行方式能够引 起机组作功的变化及热力循环吸热量的变化,机组热耗 率也随之变动,从而造成机组煤耗的变化。 • 机组内各辅机的效率变化及辅机运行方式不同,都会使 辅机总耗电量发生变化而使供电量变化,进一步使机组 煤耗发生变化。
b
×( − 1
∑
δη
i
)=
ηb
∑ (∆ q ( ) ) × b × (1 − δη ) ∑ + ∑ (∆ q ( ) )
i i i
谢谢大家!
• 在实际的热力系统中不可能是单个因素偏离基准值, 通常都是多个因素同时偏离基准值,这些因素对热力 系统的影响有正有负,此时整个热力系统的变化是这 些因素对系统影响的耦合。 • 如果热力系统有n个变化因素(X1,X2,…,Xn),其使新 蒸汽做功变化分别为(ΔHX1, HX2,…, HXn),循环吸 H ,ΔH ,…,ΔH 热量变化分别为(ΔqX1,ΔqX2,…,ΔqXn),经推导可得到 煤耗的变化计算式: n n ∑ ∆H Xj − ∑ ∆q Xj ⋅η i
耗差分析法煤耗计算的介绍

耗差分析法煤耗计算的介绍目前,火电厂计算煤耗主要有以下三种方法:正平衡、反平衡、耗差法。
这些方法各有优缺点:正平衡方法直观,计算简单。
其燃料计量有二种方法:一为入炉称计量,较准确;二为入厂称计量,需煤场盘煤才能计算结果,误差较大。
反平衡方法其计量配备和计算方法较传统,但煤耗计算结果受主蒸汽流量变化影响易起伏。
以上二种方法都只能计算一个最终煤耗,而无法知道每个参数对煤耗的定量影响。
运行中到底哪些因素是影响煤耗的主要矛盾,哪些是次要因素,耗差分析法则为解决这个问题提供了定量依据。
所谓耗差分析法就是研究机、炉每个重要参数由于偏离设计值而引起机组煤耗变化的一种定量分析计算方法。
因此它对日常运行的经济性和节能有较大的分析利用价值。
它是做好节能工作的重要技术基础。
1、选择和确定影响煤耗的参数由机组效率公式可知:η=ηkηgηtηoiηmηd。
影响总效率η的有锅炉效率ηk,管道效率ηg,汽机循环热效率ηt,汽机相对内效率ηoi,汽轮机组机械效率ηm和发电机电气效率ηd。
与上述效率有关的参数很多,但变化和影响煤耗较大的只有十几个主要参数。
包括影响锅炉效率的排烟温度、进风温度、飞灰含碳量、过剩氧量、燃煤发热量;影响汽机循环热效率的主蒸汽、再热汽的压力、温度和减温水量,循环水温、补水率、凝器背压和凝水过冷度,及回热系统的给水温度、端差和供热抽汽量等参数;影响汽机相对内效率的平均负荷、机组塑性和弹性老化损失等。
由于ηg、ηm、ηd效率不太会偏离基值,故在耗差煤耗计算中不作考虑。
2、各参数基准值的确定2.1 应达值的确定方法在当前电厂运行的能损分析系统中,应达值主要由5 种方法确定:(1) 采用制造厂提供的设计值。
如主蒸汽压力、主蒸汽温度、再热蒸汽温度等。
(2) 采用最佳运行试验的方法。
在进行设备消缺后,进行若干工况的试验,确定应达值,如排烟温度、烟气含氧量、汽水损失等。
(3) 采用变工况热力计算结果。
如汽机真空、给水温度等。
优化运行管理系统在电厂机组的运用
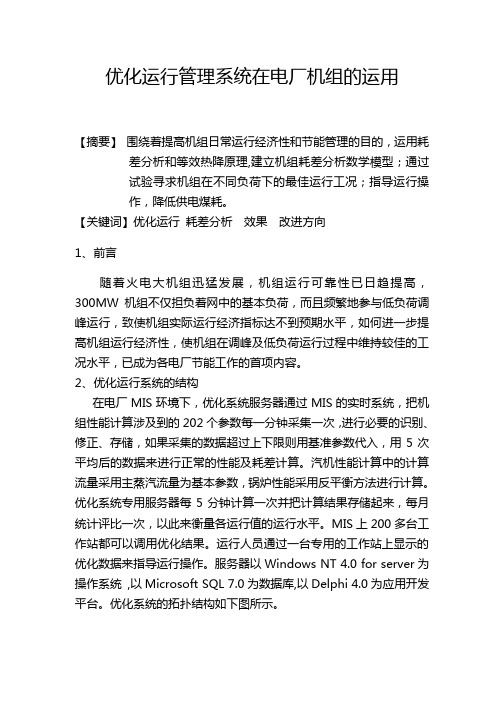
优化运行管理系统在电厂机组的运用【摘要】围绕着提高机组日常运行经济性和节能管理的目的,运用耗差分析和等效热降原理,建立机组耗差分析数学模型;通过试验寻求机组在不同负荷下的最佳运行工况;指导运行操作,降低供电煤耗。
【关键词】优化运行耗差分析效果改进方向1、前言随着火电大机组迅猛发展,机组运行可靠性已日趋提高, 300MW 机组不仅担负着网中的基本负荷,而且频繁地参与低负荷调峰运行,致使机组实际运行经济指标达不到预期水平,如何进一步提高机组运行经济性,使机组在调峰及低负荷运行过程中维持较佳的工况水平,已成为各电厂节能工作的首项内容。
2、优化运行系统的结构在电厂MIS环境下,优化系统服务器通过MIS的实时系统,把机组性能计算涉及到的202个参数每一分钟采集一次,进行必要的识别、修正、存储,如果采集的数据超过上下限则用基准参数代入,用5次平均后的数据来进行正常的性能及耗差计算。
汽机性能计算中的计算流量采用主蒸汽流量为基本参数,锅炉性能采用反平衡方法进行计算。
优化系统专用服务器每5分钟计算一次并把计算结果存储起来,每月统计评比一次,以此来衡量各运行值的运行水平。
MIS上200多台工作站都可以调用优化结果。
运行人员通过一台专用的工作站上显示的优化数据来指导运行操作。
服务器以Windows NT 4.0 for server为操作系统 ,以Microsoft SQL 7.0为数据库,以Delphi 4.0为应用开发平台。
优化系统的拓扑结构如下图所示。
3、优化运行管理系统主要功能3.1热力系统工艺流程图:共4幅(系统概貌、风烟系统、锅炉流程、汽机流程),分别实时地显示有关运行工况主要可控参数的基准值(目标值)与实际值,以及由两者差值所引起的耗差损失,直观地反映运行动态工况的优劣,为运行人员提供工况调整依据。
3.2机组调峰速率控制:提供一幅负荷、温度实际运行速率曲线,为机组参与调峰安全性提供保障。
3.3报警查询:系统中涉及汽机、锅炉性能参数计算的有关数据均取自于DCS系统。
耗差分析系统在电厂中的应用.
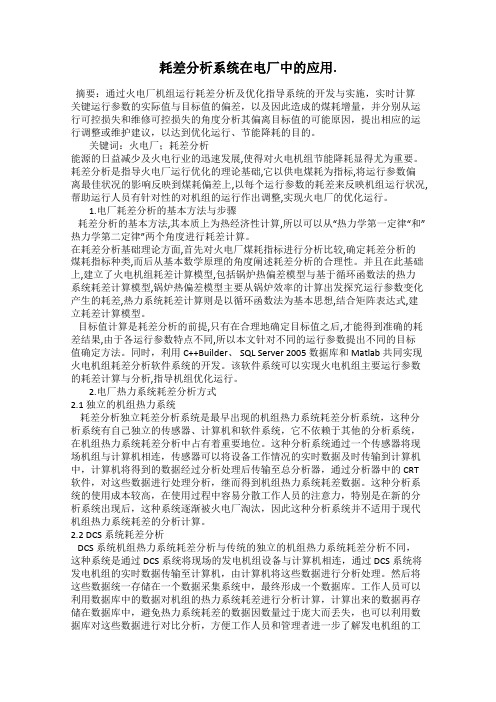
耗差分析系统在电厂中的应用.摘要:通过火电厂机组运行耗差分析及优化指导系统的开发与实施,实时计算关键运行参数的实际值与目标值的偏差,以及因此造成的煤耗增量,并分别从运行可控损失和维修可控损失的角度分析其偏离目标值的可能原因,提出相应的运行调整或维护建议,以达到优化运行、节能降耗的目的。
关键词:火电厂;耗差分析能源的日益减少及火电行业的迅速发展,使得对火电机组节能降耗显得尤为重要。
耗差分析是指导火电厂运行优化的理论基础,它以供电煤耗为指标,将运行参数偏离最佳状况的影响反映到煤耗偏差上,以每个运行参数的耗差来反映机组运行状况,帮助运行人员有针对性的对机组的运行作出调整,实现火电厂的优化运行。
1.电厂耗差分析的基本方法与步骤耗差分析的基本方法,其本质上为热经济性计算,所以可以从“热力学第一定律“和”热力学第二定律”两个角度进行耗差计算。
在耗差分析基础理论方面,首先对火电厂煤耗指标进行分析比较,确定耗差分析的煤耗指标种类,而后从基本数学原理的角度阐述耗差分析的合理性。
并且在此基础上,建立了火电机组耗差计算模型,包括锅炉热偏差模型与基于循环函数法的热力系统耗差计算模型,锅炉热偏差模型主要从锅炉效率的计算出发探究运行参数变化产生的耗差,热力系统耗差计算则是以循环函数法为基本思想,结合矩阵表达式,建立耗差计算模型。
目标值计算是耗差分析的前提,只有在合理地确定目标值之后,才能得到准确的耗差结果,由于各运行参数特点不同,所以本文针对不同的运行参数提出不同的目标值确定方法。
同时,利用C++Builder、 SQL Server 2005 数据库和Matlab 共同实现火电机组耗差分析软件系统的开发。
该软件系统可以实现火电机组主要运行参数的耗差计算与分析,指导机组优化运行。
2.电厂热力系统耗差分析方式2.1 独立的机组热力系统耗差分析独立耗差分析系统是最早出现的机组热力系统耗差分析系统,这种分析系统有自己独立的传感器、计算机和软件系统,它不依赖于其他的分析系统,在机组热力系统耗差分析中占有着重要地位。
耗差分析法在电厂热经济性分析中的应用研究
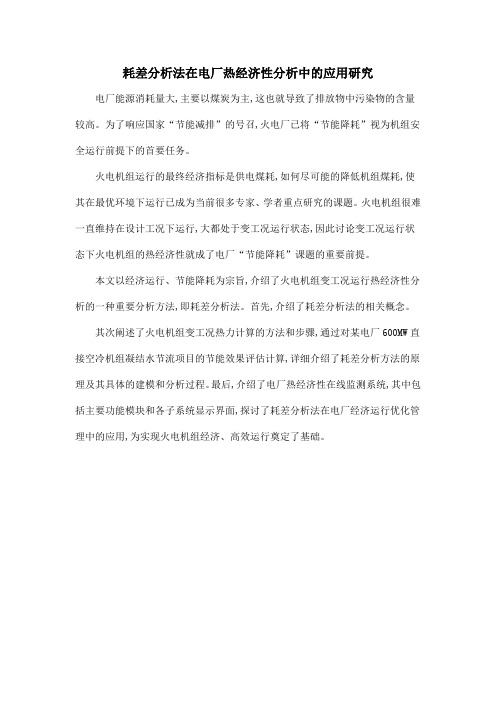
耗差分析法在电厂热经济性分析中的应用研究电厂能源消耗量大,主要以煤炭为主,这也就导致了排放物中污染物的含量较高。
为了响应国家“节能减排”的号召,火电厂已将“节能降耗”视为机组安全运行前提下的首要任务。
火电机组运行的最终经济指标是供电煤耗,如何尽可能的降低机组煤耗,使其在最优环境下运行已成为当前很多专家、学者重点研究的课题。
火电机组很难一直维持在设计工况下运行,大都处于变工况运行状态,因此讨论变工况运行状态下火电机组的热经济性就成了电厂“节能降耗”课题的重要前提。
本文以经济运行、节能降耗为宗旨,介绍了火电机组变工况运行热经济性分析的一种重要分析方法,即耗差分析法。
首先,介绍了耗差分析法的相关概念。
其次阐述了火电机组变工况热力计算的方法和步骤,通过对某电厂600MW直接空冷机组凝结水节流项目的节能效果评估计算,详细介绍了耗差分析方法的原理及其具体的建模和分析过程。
最后,介绍了电厂热经济性在线监测系统,其中包括主要功能模块和各子系统显示界面,探讨了耗差分析法在电厂经济运行优化管理中的应用,为实现火电机组经济、高效运行奠定了基础。
大唐河北分公司耗差分析系统案例
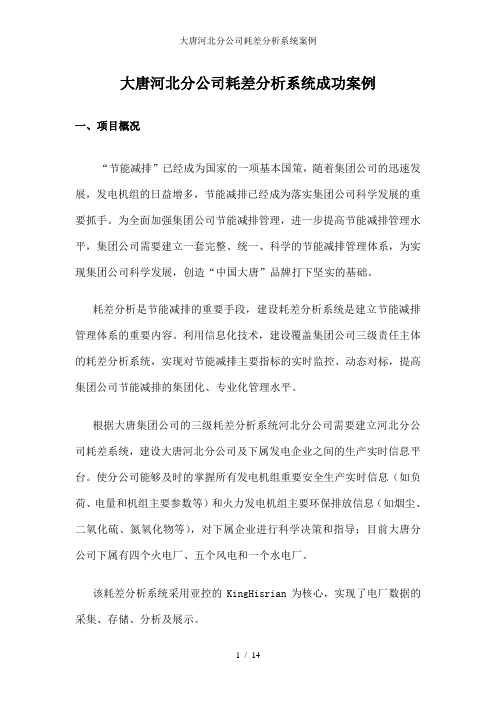
大唐河北分公司耗差分析系统成功案例一、项目概况“节能减排”已经成为国家的一项基本国策,随着集团公司的迅速发展,发电机组的日益增多,节能减排已经成为落实集团公司科学发展的重要抓手。
为全面加强集团公司节能减排管理,进一步提高节能减排管理水平,集团公司需要建立一套完整、统一、科学的节能减排管理体系,为实现集团公司科学发展,创造“中国大唐”品牌打下坚实的基础。
耗差分析是节能减排的重要手段,建设耗差分析系统是建立节能减排管理体系的重要内容。
利用信息化技术,建设覆盖集团公司三级责任主体的耗差分析系统,实现对节能减排主要指标的实时监控、动态对标,提高集团公司节能减排的集团化、专业化管理水平。
根据大唐集团公司的三级耗差分析系统河北分公司需要建立河北分公司耗差系统,建设大唐河北分公司及下属发电企业之间的生产实时信息平台。
使分公司能够及时的掌握所有发电机组重要安全生产实时信息(如负荷、电量和机组主要参数等)和火力发电机组主要环保排放信息(如烟尘、二氧化硫、氮氧化物等),对下属企业进行科学决策和指导;目前大唐分公司下属有四个火电厂、五个风电和一个水电厂。
该耗差分析系统采用亚控的KingHisrian为核心,实现了电厂数据的采集、存储、分析及展示。
二、项目特色●实现公司下属所有电厂的数据共享,远程可以看到电厂的运营情况;●具有压缩能力的历史数据库能保存长期产生的海量数据;●接口丰富方便实现及集团系统的统一连接。
三、系统架构●系统架构图根据系统网络层次和功能不同,将整个系统划分为三个层次,从下到上依次为:系统数据层、数据采集及网络传输层、应用层。
系统结构如图1所示:工工工工工工工工工工工工工工工工工工工工工工工工工工工工工工工工工工工工图1:系统结构图●主要软件产品工业数据库软件—北京亚控工业数据库KingHistorian软件采集、计算、报警、展示软件—大唐先一软件关系数据库-Orccle数据库●通讯方式➢各电厂及河北分公司采用VPN的通讯方式联接。
发电厂电能计量装置综合误差分析及应用
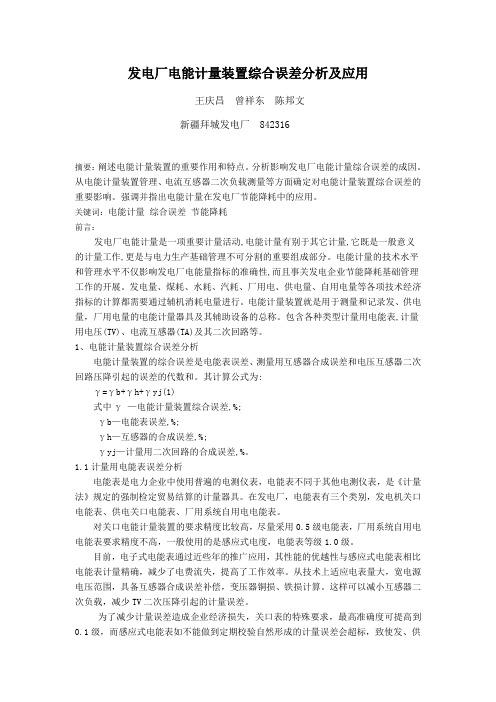
发电厂电能计量装置综合误差分析及应用王庆昌曾祥东陈邦文新疆拜城发电厂 842316摘要:阐述电能计量装置的重要作用和特点。
分析影响发电厂电能计量综合误差的成因。
从电能计量装置管理、电流互感器二次负载测量等方面确定对电能计量装置综合误差的重要影响。
强调并指出电能计量在发电厂节能降耗中的应用。
关键词:电能计量综合误差节能降耗前言:发电厂电能计量是一项重要计量活动,电能计量有别于其它计量,它既是一般意义的计量工作,更是与电力生产基础管理不可分割的重要组成部分。
电能计量的技术水平和管理水平不仅影响发电厂电能量指标的准确性,而且事关发电企业节能降耗基础管理工作的开展。
发电量、煤耗、水耗、汽耗、厂用电、供电量、自用电量等各项技术经济指标的计算都需要通过辅机消耗电量进行。
电能计量装置就是用于测量和记录发、供电量,厂用电量的电能计量器具及其辅助设备的总称。
包含各种类型计量用电能表,计量用电压(TV)、电流互感器(TA)及其二次回路等。
1、电能计量装置综合误差分析电能计量装置的综合误差是电能表误差、测量用互感器合成误差和电压互感器二次回路压降引起的误差的代数和。
其计算公式为:γ=γb+γh+γyj(1)式中γ —电能计量装置综合误差,%;γb—电能表误差,%;γh—互感器的合成误差,%;γyj—计量用二次回路的合成误差,%。
1.1计量用电能表误差分析电能表是电力企业中使用普遍的电测仪表,电能表不同于其他电测仪表,是《计量法》规定的强制检定贸易结算的计量器具。
在发电厂,电能表有三个类别,发电机关口电能表、供电关口电能表、厂用系统自用电电能表。
对关口电能计量装置的要求精度比较高,尽量采用0.5级电能表,厂用系统自用电电能表要求精度不高,一般使用的是感应式电度,电能表等级1.0级。
目前,电子式电能表通过近些年的推广应用,其性能的优越性与感应式电能表相比电能表计量精确,减少了电费流失,提高了工作效率。
从技术上适应电表量大,宽电源电压范围,具备互感器合成误差补偿,变压器铜损、铁损计算。
- 1、下载文档前请自行甄别文档内容的完整性,平台不提供额外的编辑、内容补充、找答案等附加服务。
- 2、"仅部分预览"的文档,不可在线预览部分如存在完整性等问题,可反馈申请退款(可完整预览的文档不适用该条件!)。
- 3、如文档侵犯您的权益,请联系客服反馈,我们会尽快为您处理(人工客服工作时间:9:00-18:30)。
耗差分析系统在电厂中的应用.
发表时间:2019-11-29T16:05:00.963Z 来源:《中国电业》2019年16期作者:伏林[导读] 通过火电厂机组运行耗差分析及优化指导系统的开发与实施摘要:通过火电厂机组运行耗差分析及优化指导系统的开发与实施,实时计算关键运行参数的实际值与目标值的偏差,以及因此造成的煤耗增量,并分别从运行可控损失和维修可控损失的角度分析其偏离目标值的可能原因,提出相应的运行调整或维护建议,以达到优化运行、节能降耗的目的。
关键词:火电厂;耗差分析
能源的日益减少及火电行业的迅速发展,使得对火电机组节能降耗显得尤为重要。
耗差分析是指导火电厂运行优化的理论基础,它以供电煤耗为指标,将运行参数偏离最佳状况的影响反映到煤耗偏差上,以每个运行参数的耗差来反映机组运行状况,帮助运行人员有针对性的对机组的运行作出调整,实现火电厂的优化运行。
1.电厂耗差分析的基本方法与步骤
耗差分析的基本方法,其本质上为热经济性计算,所以可以从“热力学第一定律“和”热力学第二定律”两个角度进行耗差计算。
在耗差分析基础理论方面,首先对火电厂煤耗指标进行分析比较,确定耗差分析的煤耗指标种类,而后从基本数学原理的角度阐述耗差分析的合理性。
并且在此基础上,建立了火电机组耗差计算模型,包括锅炉热偏差模型与基于循环函数法的热力系统耗差计算模型,锅炉热偏差模型主要从锅炉效率的计算出发探究运行参数变化产生的耗差,热力系统耗差计算则是以循环函数法为基本思想,结合矩阵表达式,建立耗差计算模型。
目标值计算是耗差分析的前提,只有在合理地确定目标值之后,才能得到准确的耗差结果,由于各运行参数特点不同,所以本文针对不同的运行参数提出不同的目标值确定方法。
同时,利用C++Builder、 SQL Server 2005 数据库和Matlab 共同实现火电机组耗差分析软件系统的开发。
该软件系统可以实现火电机组主要运行参数的耗差计算与分析,指导机组优化运行。
2.电厂热力系统耗差分析方式
2.1 独立的机组热力系统
耗差分析独立耗差分析系统是最早出现的机组热力系统耗差分析系统,这种分析系统有自己独立的传感器、计算机和软件系统,它不依赖于其他的分析系统,在机组热力系统耗差分析中占有着重要地位。
这种分析系统通过一个传感器将现场机组与计算机相连,传感器可以将设备工作情况的实时数据及时传输到计算机中,计算机将得到的数据经过分析处理后传输至总分析器,通过分析器中的 CRT 软件,对这些数据进行处理分析,继而得到机组热力系统耗差数据。
这种分析系统的使用成本较高,在使用过程中容易分散工作人员的注意力,特别是在新的分析系统出现后,这种系统逐渐被火电厂淘汰,因此这种分析系统并不适用于现代机组热力系统耗差的分析计算。
2.2 DCS 系统耗差分析
DCS 系统机组热力系统耗差分析与传统的独立的机组热力系统耗差分析不同,这种系统是通过 DCS 系统将现场的发电机组设备与计算机相连,通过 DCS 系统将发电机组的实时数据传输至计算机,由计算机将这些数据进行分析处理。
然后将这些数据统一存储在一个数据采集系统中,最终形成一个数据库。
工作人员可以利用数据库中的数据对机组的热力系统耗差进行分析计算,计算出来的数据再存储在数据库中,避免热力系统耗差的数据因数量过于庞大而丢失,也可以利用数据库对这些数据进行对比分析,方便工作人员和管理者进一步了解发电机组的工作情况,及时对发电机组的工作状态进行调整。
2.3 MIS 系统耗差分析
单纯使用MIS 系统进行机组热力耗差分析现阶段还比较少见,应用较多的是利用 MIS 技术实现客户/服务器模式的耗差分析。
这种系统将耗差计算模块与耗差显示模块想分离,形成两个相互之间独立的模块,有着各自的模块处理器二者依靠耗差分析数据库进行连接。
在这种情况下,MIS 系统拥有单独的数据库,与单纯使用 MIS 系统进行耗差分析相比,安全性得到了相应的提高。
而且 MIS 系统在读取数据库中的数据时,与原有的 MIS 系统的通信系统并不会产生相互干扰的情况,安全性较高。
随着计算机技术水平的不断提高,将会有越来越多的发电机组采取这样的耗差分析方法。
3.电厂耗差分析系统的应用
3.1 机组经济性能应用
现在运行人员和管理人员町以实时查看到机组的各项性能和经济指标,掌握机组的运行水平. (1)查看煤耗可以知道当前机组的经济状况,结合成本分析,可以给出机组的发电成本.如果煤耗偏高,则应看看是哪些因素引起的,这时结合耗差分析棒图,就可以找到偏差的主要凶索. (2)查看各加热器的端差可以知道各加热器的运行情况.当端差偏人时,可以通过查看加热器运行水位等调节手段来降低端差,同时,可根据加热器的传热情况,指导加热器的检修. (3)查看真空度和凝结水过冷度可以反映真空系统的严密性,如果真空度一直偏低,凝结水过冷度较大,则应检查真空系统的严密性. (4)查看补水率可以知道系统的补水情况,如果补水率偏人,则要看看锅炉排污是否正常,或系统明漏,不明泄漏量过大. (5)查看锅炉各项热损失,能够知道哪些损失大,对于偏大的损失,可以具体分析,如果是排烟损失大,看看排烟温度是否偏高,氧量是否偏大,如果是机械未完全燃烧损失偏大,则看看飞灰含碳量是否偏大. (6)查看空预器性能则能知道空预器的传热效果,如果空预器效率偏低,则考虑空预器积灰严重要进行吹扫或漏风严重。
3.2 运行参数的优化应用
通过耗差分析获取的目标值,来实现运行参数优化,让运行参数尽可能接近目标值来运行. 运行参数优化主要有:主汽温度,主汽压力,再热温度,给水温度,真空,氧量,过减温流量,再减温流量,排烟温度等. 运行人员通过一些手段的调节使以上这些运行参数的实际值尽可能接近目标值,通过查看耗差比较棒图,使红色部分(正耗差)尽可能减少,从而实现运行参数的优化. 由于煤耗比较棒图的煤耗偏差在屏幕上一目了然,因此,运行人员应从影响煤耗最大偏差的参数开始调节,比较容易快速达到减少煤耗。
4.结束语
总而言之,耗差分析系统会应根据实际需求进行相应的改进,工作人员要不断加强耗差分析研究,加强技术人员的素质要求,不断总结经验,完善我国自主的耗差分析系统,进一步完善和积累如何更好的地使用该系统,提升我国电力机组耗差分析的水平,才能使该系统发挥出最佳的经济效益,才能为我国电力事业的发展作出贡献。
参考文献:
[1]王运民,李素真.热力系统节能分析[J].汽轮机技术,2012(10):96.。