简子纱染色需要注意几个问题
筒子纱染色技术
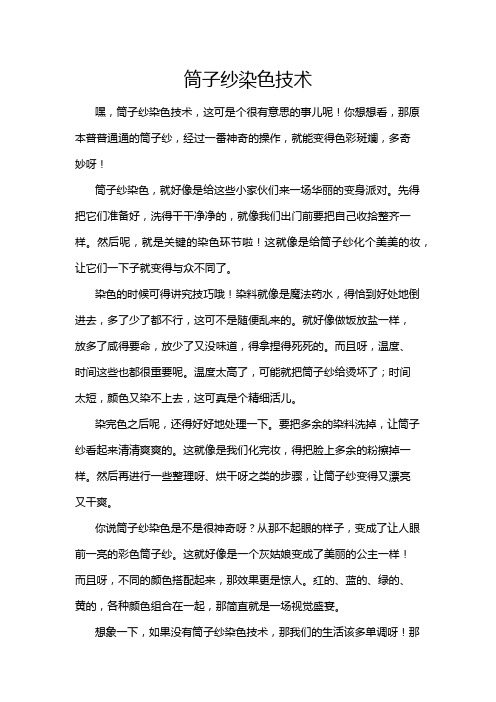
筒子纱染色技术嘿,筒子纱染色技术,这可是个很有意思的事儿呢!你想想看,那原本普普通通的筒子纱,经过一番神奇的操作,就能变得色彩斑斓,多奇妙呀!筒子纱染色,就好像是给这些小家伙们来一场华丽的变身派对。
先得把它们准备好,洗得干干净净的,就像我们出门前要把自己收拾整齐一样。
然后呢,就是关键的染色环节啦!这就像是给筒子纱化个美美的妆,让它们一下子就变得与众不同了。
染色的时候可得讲究技巧哦!染料就像是魔法药水,得恰到好处地倒进去,多了少了都不行,这可不是随便乱来的。
就好像做饭放盐一样,放多了咸得要命,放少了又没味道,得拿捏得死死的。
而且呀,温度、时间这些也都很重要呢。
温度太高了,可能就把筒子纱给烫坏了;时间太短,颜色又染不上去,这可真是个精细活儿。
染完色之后呢,还得好好地处理一下。
要把多余的染料洗掉,让筒子纱看起来清清爽爽的。
这就像是我们化完妆,得把脸上多余的粉擦掉一样。
然后再进行一些整理呀、烘干呀之类的步骤,让筒子纱变得又漂亮又干爽。
你说筒子纱染色是不是很神奇呀?从那不起眼的样子,变成了让人眼前一亮的彩色筒子纱。
这就好像是一个灰姑娘变成了美丽的公主一样!而且呀,不同的颜色搭配起来,那效果更是惊人。
红的、蓝的、绿的、黄的,各种颜色组合在一起,那简直就是一场视觉盛宴。
想象一下,如果没有筒子纱染色技术,那我们的生活该多单调呀!那些漂亮的衣服、五彩的纺织品从哪里来呢?所以说呀,筒子纱染色技术可真是太重要啦!它让我们的生活变得更加丰富多彩,更加有滋有味。
筒子纱染色技术也不是一成不变的哦!它也在不断地发展和进步呢。
新的染料、新的工艺不断涌现,让筒子纱的染色效果越来越好。
这就像我们的科技一样,总是在不停地向前推进,给我们带来更多的惊喜和便利。
筒子纱染色,看似简单,实则蕴含着无数的奥秘和技巧。
它需要我们用心去对待,去钻研,才能真正掌握其中的精髓。
这可不是随随便便就能做好的事情呢!所以呀,那些从事筒子纱染色工作的人,可真是了不起呀!他们用自己的双手和智慧,创造出了那么多美丽的色彩。
筒子纱染色加工注意事项
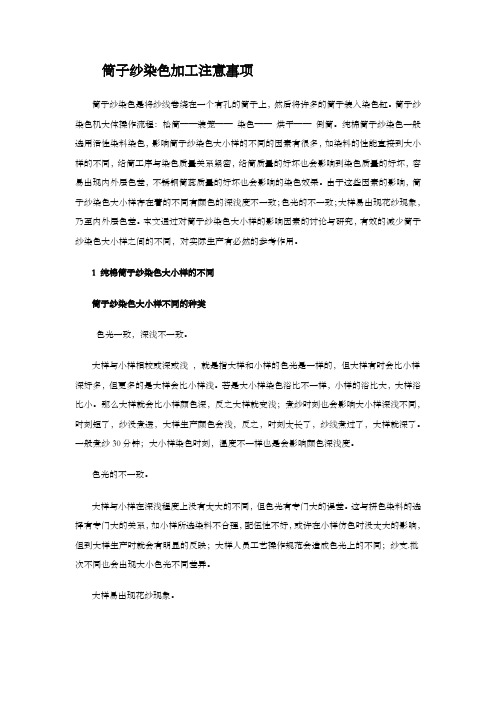
筒子纱染色加工注意事项筒子纱染色是将纱线卷绕在一个有孔的筒子上,然后将许多的筒子装入染色缸。
筒子纱染色机大体操作流程:松筒——装笼——染色——烘干——倒筒。
纯棉筒子纱染色一般选用活性染料染色,影响筒子纱染色大小样的不同的因素有很多,如染料的性能直接到大小样的不同,络筒工序与染色质量关系紧密,络筒质量的好坏也会影响到染色质量的好坏,容易出现内外层色差,不锈钢筒蕊质量的好坏也会影响的染色效果。
由于这些因素的影响,筒子纱染色大小样存在着的不同有颜色的深浅度不一致;色光的不一致;大样易出现花纱现象,乃至内外层色差。
本文通过对筒子纱染色大小样的影响因素的讨论与研究,有效的减少筒子纱染色大小样之间的不同,对实际生产有必然的参考作用。
1 纯棉筒子纱染色大小样的不同筒子纱染色大小样不同的种类色光一致,深浅不一致。
大样与小样相较或深或浅,就是指大样和小样的色光是一样的,但大样有时会比小样深好多,但更多的是大样会比小样浅。
若是大小样染色浴比不一样,小样的浴比大,大样浴比小。
那么大样就会比小样颜色深,反之大样就变浅;煮纱时刻也会影响大小样深浅不同,时刻短了,纱没煮透,大样生产颜色会浅,反之,时刻太长了,纱线煮过了,大样就深了。
一般煮纱30分钟;大小样染色时刻,温度不一样也是会影响颜色深浅度。
色光的不一致。
大样与小样在深浅程度上没有太大的不同,但色光有专门大的误差。
这与拼色染料的选择有专门大的关系,如小样所选染料不合理,配伍性不好,或许在小样仿色时没太大的影响,但到大样生产时就会有明显的反映;大样人员工艺操作规范会造成色光上的不同;纱支.批次不同也会出现大小色光不同差异。
大样易出现花纱现象。
小样染色没有明显的色花,而大样染出来后却出现花纱现象。
有内外层色差;筒子两头与中间的色差。
散纤维的装笼既要均匀,还要紧密。
紧密度与均匀度不一,会使这缸大样出现花纱,筒子与筒子间出现色光不同;倒筒卷绕密度有的松有的紧,就会出现内外层色差。
筒子纱染色调色技术控制要点

0170 00 80 .6 . 7 OO 02 .0 H 0O 45 .1
清 洗 成 本 ( )( ・ ) o0 08 00 05 水 /元 t .0 . 0 抗 污 剂 成 本/元 ・ ( t ) 04 00 02 O0 .5 .1
滤 袋 更 换 成 本/元 ・ ) 00 50 00 30 ( t .2 .l 片 碱 成 本/元 ・ f t 1
4 调 色 方 法
00 30 . 4
05 36 04 11 .3 .2
膜 = 换 成 本 /元 ・ 0370 03 70 芷更 f t ) . .7 7
设 备 及 安装 折 旧/元 ・ . 30 02 30 ( t 02 .9 ) 9
房 屋及 基础 设 施 折 I/ H
电/ 元 ・ f t 、
文 章 编 号 :0 0 4 3 (0 0 0 — 0 3 O 10 — 0 3 2 1 )2 0 3 一 l 筒 子纱 染 色 由于 损耗 小 、 质 量 高 、 货 快 、 益好 . 交 效 已经 被 广 大 纱 线染 整 厂 所 采 用 了达 到一 次 为 准 确率 和按 时 交 货 . 控 制 影 响车 应 间 调 色准 确 率 的 关键 因 素 1 调 色 灯 箱 首 先 必 须 在 标 准 灯 箱 里 进 行 调 色 . 准 灯 箱 是 指标 准 光 源 和标 标 准灯 箱 内壁 通 常所 用标 准 光 源为 D 光 源 .特 殊 要 求 则 用 其 他 特 殊 标 准光 源 , U 如 V光 源 、W F光源 。 C 因 不 同灯 箱 内壁 颜 色 对 光 有 不 同 会 偏 浅 . 拉 得 太 松 . 看 起 来 偏 若 则 深. 尤其是弹力纱
的吸收和反射 . 因此灯箱 内壁必须 是标准银灰色 . 否则 对 标 准 光 源 反 射 光 颜 色 造成 负 面影 响 . 要 是 影 主 响对颜 色 色光 的判 断 2 调 色 标 准 调 色依 据 是对 色 标 准样 . 首 先 需 要 确 保 对 色 标 准 样 是 标 准 的 .即确保调 色依据 的对 色标 准 样是 技术部指 定对色标 准 .确保 对 色标 准 样 的状 态是 标 准 的 . 正 常 情 况 下 不 能用 手 去 摸 对 色 标 准 样 补 做 或 加 缸 的 对 色 标 准 样 通 常 是 穿 在 多孔 卡 里 的 Q C纱 样 . 通 常 这 样 的标 准 状 态 不 太 稳 定 . 建 议 先 用 透 明胶 将 对 色 标 准 样 固定 在 卡 上 . 后 再 进 行 对 色 然
筒子纱染色如何避免染色上色不匀、白节白点、色渍色斑
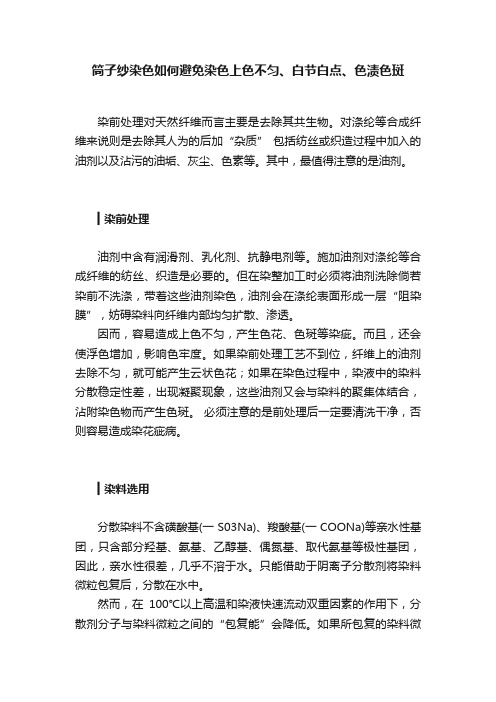
筒子纱染色如何避免染色上色不匀、白节白点、色渍色斑染前处理对天然纤维而言主要是去除其共生物。
对涤纶等合成纤维来说则是去除其人为的后加“杂质” 包括纺丝或织造过程中加入的油剂以及沾污的油垢、灰尘、色素等。
其中,最值得注意的是油剂。
▎染前处理油剂中含有润滑剂、乳化剂、抗静电剂等。
施加油剂对涤纶等合成纤维的纺丝、织造是必要的。
但在染整加工时必须将油剂洗除倘若染前不洗涤,带着这些油剂染色,油剂会在涤纶表面形成一层“阻染膜”,妨碍染料向纤维内部均匀扩散、渗透。
因而,容易造成上色不匀,产生色花、色斑等染疵。
而且,还会使浮色增加,影响色牢度。
如果染前处理工艺不到位,纤维上的油剂去除不匀,就可能产生云状色花;如果在染色过程中,染液中的染料分散稳定性差,出现凝聚现象,这些油剂又会与染料的聚集体结合,沾附染色物而产生色斑。
必须注意的是前处理后一定要清洗干净,否则容易造成染花疵病。
▎染料选用分散染料不含磺酸基(一S03Na)、羧酸基(一COONa)等亲水性基团,只含部分羟基、氨基、乙醇基、偶氮基、取代氨基等极性基团,因此,亲水性很差,几乎不溶于水。
只能借助于阴离子分散剂将染料微粒包复后,分散在水中。
然而,在100℃以上高温和染液快速流动双重因素的作用下,分散剂分子与染料微粒之间的“包复能”会降低。
如果所包复的染料微粒游离出来,就会重新聚集成更大的染料颗粒。
这种现象即为分散染料的“高温凝聚性”不同结构的分散染料,其热凝聚现象不同。
大体可分三种:一为不易发生热凝聚。
这类染料不会因升温、降温或相互碰撞而凝聚。
使用这样的染料染色一般不会造成染色不匀或色斑色渍。
二为容易发生热凝聚但随着染料分子向纤维内部扩散,染料的聚集体会再度解聚,只要染料在纤维表面吸附均匀,一般就不会造成色花、色渍。
三为容易发生热凝聚,而且在染色过程中,又难以解聚。
使用这类染料染色时,特别是当使用的分散剂或匀染剂高温分散能力较差时,就很容易由于染料的热凝聚而造成色泽不匀。
筒子染色时内外色差原因及预防措施
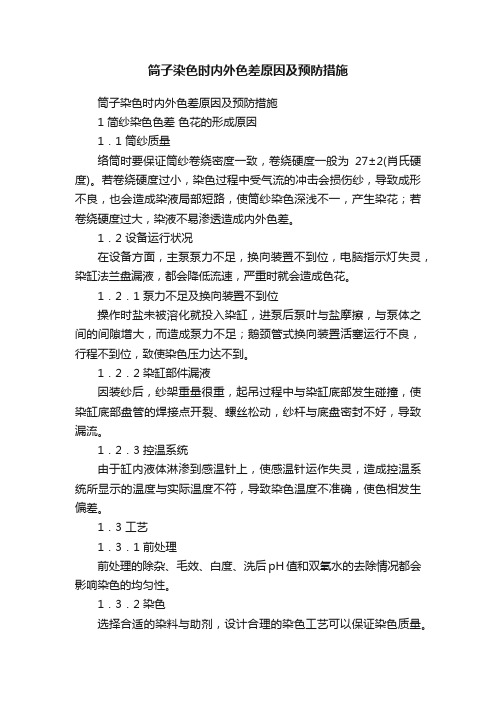
筒子染色时内外色差原因及预防措施筒子染色时内外色差原因及预防措施1 简纱染色色差色花的形成原因1.1 筒纱质量络筒时要保证筒纱卷绕密度一致,卷绕硬度一般为27±2(肖氏硬度)。
若卷绕硬度过小,染色过程中受气流的冲击会损伤纱,导致成形不良,也会造成染液局部短路,使筒纱染色深浅不一,产生染花;若卷绕硬度过大,染液不易渗透造成内外色差。
1.2 设备运行状况在设备方面,主泵泵力不足,换向装置不到位,电脑指示灯失灵,染缸法兰盘漏液,都会降低流速,严重时就会造成色花。
1.2.1 泵力不足及换向装置不到位操作时盐未被溶化就投入染缸,进泵后泵叶与盐摩擦,与泵体之间的间隙增大,而造成泵力不足;鹅颈管式换向装置活塞运行不良,行程不到位,致使染色压力达不到。
1.2.2 染缸部件漏液因装纱后,纱架重量很重,起吊过程中与染缸底部发生碰撞,使染缸底部盘管的焊接点开裂、螺丝松动,纱杆与底盘密封不好,导致漏流。
1.2.3 控温系统由于缸内液体淋渗到感温针上,使感温针运作失灵,造成控温系统所显示的温度与实际温度不符,导致染色温度不准确,使色相发生偏差。
1.3 工艺1.3.1 前处理前处理的除杂、毛效、白度、洗后pH值和双氧水的去除情况都会影响染色的均匀性。
1.3.2 染色选择合适的染料与助剂,设计合理的染色工艺可以保证染色质量。
工艺设计不好,选择三原色的配伍性差,也会造成色花。
2 防止色差色花的措施2.1 筒纱质量筒纱成形要严格把关,杜绝哑铃纱、喇叭纱、重叠纱、漏眼纱及硬边纱,卷绕密度要控制在要求范围之内,过硬过松的`要挑出,筒纱大小一致。
2.2 设备维修为保证设备正常运行,对上述所存在的问题要定期检查,这样才能保证设备运转良好和染色质量稳定。
定期对水、汽阀门进行检查,看有无开启不灵活和关闭不严现象,加强设备维护。
2.3 前处理工艺选择前处理工艺要煮透、煮匀,以便于染色。
为缩短时间,采用煮练漂白同浴法。
工艺处方(g/L)3O%氢氧化钠 4精练剂 2渗透剂 2双氧水 6稳定剂 3前处理工艺曲线(见图1)。
染筒子纱规章制度

染筒子纱规章制度1. 目的本文档旨在确立和规范染筒子纱的使用和管理制度,以提高纱线染色工作的效率和质量,并保证生产过程的安全和可持续发展。
2. 适用范围本规章制度适用于染筒子纱的相关工作人员和管理人员。
3. 定义•染筒子纱:指将纱线通过染色工艺加工后,成为具有特定颜色的纱线。
•染色工艺:指在染筒子纱的生产过程中采用的染色方法和工艺步骤。
•染色剂:指用于染筒子纱的染色剂料,包括染料和助剂等。
4. 染筒子纱操作规范4.1 染色工艺确定 - 定期根据市场需求和产品要求,确定染色工艺和生产计划。
- 染色工艺应包括染色剂的选用、配方的确定、染色温度和时间等关键参数。
- 经过验证的染色工艺应及时记录并进行归档,以备后续参考和追溯。
4.2 筒子准备 - 筒子应经过清洗、消毒并严格标记,以确保染色过程中的纯净度。
- 不同品种和颜色的纱线应分开存放,并进行分类管理。
4.3 染色操作 - 按照染色工艺要求,精确测量染色剂,确保染色配方的准确性。
- 控制染色温度和时间,保证染色效果的一致性。
- 加入适量的染料分散剂或助剂,并根据染色剂的特点进行搅拌和处理。
4.4 染后操作 - 染色后,及时将染好的筒子取出,并用清水进行充分冲洗,清除残留的染料和助剂。
- 对染色后的纱线进行必要的处理,如漂白、干燥等,以保证染色效果和质量。
4.5 高效施工管理 - 严格按照工艺流程操作,并确保各个环节的协调和衔接。
- 做好生产记录和数据统计,及时发现和解决问题,提高工作效率和质量。
5. 安全管理5.1 使用安全 - 使用染色剂和助剂时,应遵循相关安全操作规范。
- 防止染料和助剂的泄漏和接触,定期检查和维护染色设备和仪器。
5.2 废弃物处理 - 废弃的染料和助剂应分类收集,并依法进行合理的处理和处置,以减少对环境的污染。
5.3 应急预案 - 建立应急预案,针对可能发生的突发事件和事故,进行预防和应对。
在染色过程中,如果发生泄漏、火灾等紧急情况,应立即停止工作并采取相应措施。
筒子纱染色内外层色差产生的原因及防止

维普资讯
染
整
技
术
V 12 o2 o 4N . .
A t2 0 p. 02
筒子纱在染色过程中正反循环时间比, 则应根
据 泵 的扬 程流量 、 纱线类 别 而定 一般 筒纱采 用 反
襄 1 筒 纱的卷绕 密度
循环 ( 外一 内) 时间大于正循环 ( 内一外) 时间。 筒子
注: 筒子 纱 支数 越 南 , 相应 筒 子 纱 卷 绕 密度 应越 小 。
3 43 筒 子纱 染 色工艺 .. () 涤工 艺 ; 1染
分散染料染涤 , 一般采用高温高压染色法 。在 高温高压条件下 , 染料分子产生强烈运动, 从纤维 表面向内部扩散 , 而纤维表面又不断被染料饱和溶
纱颜 色 内层 浅 , 外层深 , 增加染 液 的正 循环 ; 筒子纱
颜色内层深 , 外层浅 , 则增加反循环时间。
3 3 染料 的选 择 .
在染涤棉混纺纱 、 全棉纱时, 染料选择的好与 坏是影响筒纱 内外色差的最重要因素 , 由于筒子纱
染 色 的特殊性 ,要求 所用 染料 有较好 的渗 透性 、优 良的移 染性 、 和染 色牢 度 。 在染 色 中 , 染物 的色 泽往 往不 是来 自一 个 染料 ,而 是 由几个 染 料拼 色所 得 , 染料 拼色 时应考 虑掌 握 以下 几条 原 则 ._ a 染料 对纤 维 的适应性 ;.染料 一般 采用 同类 型 ;.染 料 的性 b c 能 , 接性 , 散性 , 色牢 度 等尽 可能一致 。 直 扩 染 若所选 用 的染料 它们 的相溶 性 ,同步性 ,重演
对铁 的含 量也应控 制好 ,如 f — F 含 量过
其一织机中产生 , 其二是筒子色纱有 内外层色差。 针对筒子纱 内外层色差问题 , 将从以下各个环节进
涤纶筒纱染色工艺探讨

涤纶筒纱染色工艺探讨摘要:本文主要介绍了涤纶筒子染色时的生产工艺,结合我司生产实际,阐述了纯涤筒纱在染色生产过程中易出现的质量问题,着重分析了造成涤纶筒子色差的原因及影响因素,并提出了一系列改善和解决方案。
关键词:涤纶染色;筒纱;染色工艺;色差;低聚物0 前言随着消费者生活水平的不断提升,人们对色织品的功能风格等需求也在日益增长。
筒子纱染色可以达到独特的色织物风格。
同时,筒子纱染色浴比小,染色损耗小,可降低生产成本;而且质量高、交货快、效益好。
加上筒子纱具有批量小、品种多、开发品种灵活的优势,受到市场的欢迎,市场占有率也越来越高[1]。
然而,涤纶的筒子纱染色工艺流程较复杂,影响因素较多且难以控制,稍有疏忽,易造成色花色差。
从而使得修色、回染、改染、重染问题变得很突出,它所带来的不仅是成本昂贵,而且耗时,影响染色的一次成功率和即时化生产,导致成本居高不下,产品周期延长。
为提高一次命中率和降低生产成本,缩短产品交货周期,必须对涤纶染色的质量影响因素加强控制。
1 松筒质量控制1.1 密度控制筒纱的密度通常是决定色差的最重要因素之一。
若松纱密度太小,易造成纱线松散,导致染色循环过程中筒纱纱线被染液冲散冲乱,成形不良,影响后序倒筒;若松纱密度太大,则染液难以穿透纱层,易造成染色不匀,甚至染不透等问题。
另外,由于涤纶具有热收缩性质和染色中松筒预置张力,在高温染色过程中的密度也会发生一定的变化。
筒子纱在高温130℃染色时外层自由端不受到拉伸,而内层受热收缩和松筒预置张力同一方向共同作用,使纱线明显受到拉伸[2]。
因此,涤纶纱线由于内外层受到的张力不同,而内层受到较大的收缩张力,使得筒子越内层密度越紧。
当筒纱密度大到不足以使染料分子顺利循环渗透时,染料分子便聚集在内层,染色后表现为越里层颜色越深,而最外层纱线由于浸泡在染液中,最终染出的筒子显现为内层颜色最深,中层较浅,而最外层介于两者之间,形成色差。
1.2 外包袜管涤纶纱线外表光滑,若直接使用直筒型松式壳染色,在受到流动染液的冲击下容易产生纱线滑移,形成表面乱纱甚至脱壳问题。
- 1、下载文档前请自行甄别文档内容的完整性,平台不提供额外的编辑、内容补充、找答案等附加服务。
- 2、"仅部分预览"的文档,不可在线预览部分如存在完整性等问题,可反馈申请退款(可完整预览的文档不适用该条件!)。
- 3、如文档侵犯您的权益,请联系客服反馈,我们会尽快为您处理(人工客服工作时间:9:00-18:30)。
简子纱染色需要注意的几个问题
近年来,由于越来越多的客户认识到筒子纱线染色损耗小、质量高、交货快、效益好,因此,筒子纱线染色订单快速增长。
然而涤纶筒子纱线染色工艺复杂,要求很高,且影响因素较多难于控制,稍有疏忽,容易造成色花。
一、染色原理
涤纶筒子纱线染色是采用高温高压染色法在高温高压筒子纱染色机上进行的。
由于聚酯纤维结构紧密,分散染料在低温条件下几乎不上染。
只有将温度提高至90℃以上,染料的上染才逐渐增加。
达到110℃以上时,涤纶纤维中无定型区高分子链段的运动加剧,增加了微隙,降低了染料分子扩散进入纤维内部的阻力,提高了染料分子扩散速度,使分散染料的上染速
率迅速加大。
至130℃才能获得满意的染色效果,染料利用率达到90%以上,得色丰满,各种染色牢度优良。
涤纶筒子纱线染色就是在一定的温度下,利用染色机上主泵的压力作用使染液穿透卷绕在具多孔筒管上的纱线层,使染料分子与纤维分子接触,溶解了的染料首先被纤维外层吸附,接着再向纤维内部扩散,从而达到上染目的。
二、染色易色花应注意以下问题:
2.1松筒
涤纶筒子纱线染色前需先松筒。
松简首选不锈钢弹簧管,其优点是有效穿透面积特别大,对获得匀染非常有利。
可自由压缩,对不同数量批号的订单有极强的适应能力。
筒纱的卷绕密度大小是很重要的,考虑到染色机械的泵的扬程高度,涤纶筒纱的卷绕密度以
0.33-0.39g/立方厘米为宜。
卷绕太紧,染液难以穿透很厚的纱层,局部因接触染料太少而得色偏浅造成色花或色圈等染疵,卷绕太松,筒纱容易变形脱落,造成乱纱,难于上机。
2.2前处理
前处理的目的是去除涤纶纱线在纺纱和松筒等人缸染色前工序中沾污在纱线上的油剂,通常采用除油灵,加碳酸纳2g/L于80℃条件下处理20min。
必须注意的是前处理后一定要清洗干净,否则容易造成染花疵病。
2.3染料的选择
高温高压染色应尽量选用分子量小、分散性优良的染料,国产分散红E-4B、分散黄
E-3RL、分散蓝E-4R是一组很匹配的低温型染料组合。
能拼出大部分常见的色谱体系。
考
虑到欧共体等关于禁止使用有与且能含有致癌物质的限制,采用分散黄SE-4RL代E-3RL 也能获得满意的染色效果,对于牢度要求特别高的产品需用高温型分散染料,这一组合常选分散红S-5BL、分散橙S-4RL、分散兰S-3BG,可以拼出大部分颜色,成本也相对较低,但需加大分散剂的用量,否则会形成染料聚集,造成染斑,难以去除。
2.4助剂选择
匀染剂的使用在高温高压筒子纱线染色中具有极其重要的意义。
选用的匀染剂要求泡沫小、高温分散性好、移染性强。
筒子染色时对水质要求极高,整合分散剂R-DL对水中的Ca 离子、Mg离子具有很强的整合能力,通常在染液中的用量为0.5g/l,1g/l,既可以降低水的硬度又可以增加染料的分散能力,防止染料聚集在纱线上;形成染斑。
2.5 pH值的要求
高温高压筒子纱线染色要求染浴pH值控制在4.5-5最好。
2.6液流的控制
液流方向的控制是获得匀染的关键因素,控制不好会造成内外色差,织到布面上表现出来的就是色档。
液流方向的控制要通过长期的摸索,它取决于泵的压力大小。
一般情况下采用正循环3min反循环4min方式循环使染色筒纱里表颜色一致。
2.7升温速度的控制
当染色温度在85℃以下时,染料很少上染,可直接升温。
85℃-110℃是上染速度增加最快的温度区域,需要严格控制升温速度在1.5℃/min以下。
115℃-130℃范围内可稍快点,但仍需要将升温速度控制在2℃/min左右。
这里的保温时间是对中等深度的颜色而言,浅色可适当缩短,深色可适当延长.保温时间要适宜,太短会产生环染现象,太长易产生毛丝。
一般应控制在30--60min.
染色完毕后降温要快,因为在缓慢的降温过程中会产生低聚物,其残留在纱线表面呈焦油状难以去除。
2.8还原清洗
还原清洗是涤纶筒子纱线染色后的一个重要工序。
它不仅可以洗掉吸附在纱线表面的分散染料,使染色牢度得到保证,而且可以去除在染色过程中吸附在纱线表面的其它物质,减少染斑的产生。
三、色花后补救办法
筒子纱线染花一般都能得到回修。
回修的方法是在高温条件下借助于匀染剂的移染作用使染料从深色区域向浅色区域转移。
修补剂L是一种低泡型具有高效分散作用、移染能力特强的匀染剂。
用量加大至3g/L-5g/L。
用作回修色花,成功率高达95%以上。
我们曾将不同颜色的色纱混装在一起,用修补剂L 5g/L,加酸调节pH值为5左右,于135℃条件下处理60min。
然后检查各筒纱之间的色差,色差回修很好.难于分辩。