硫腐蚀
基于高酸性条件下元素硫对碳钢腐蚀的影响分析

Management & Technology of SME
基于高酸性条件下元素硫对碳钢腐蚀的影响分析
Analysis of the Influence of Elemental Sulfur on the Corrosion of Carbon Steel
Under High Acid Conditions
【作者简介】唐江(1986-),男,重庆人,助理工程师,从事硫及其化 合物对不同材料的腐蚀研究。
172
供良好环境,并且还能为腐蚀监测提供技术支撑。在实验过 程中主要使用了 L245 低碳钢,电化学反应和失衡条件分别 为 1.4MPa 和 1.6MPa,元素硫主要通过传统的方式进行保留, 试验温度可能在 60益之上,试验周期可以确定为 3D。在具体 的实验开展过程中需要参考相关数据资料,这样才能确保电 化学腐蚀实验条件满足水溶液需求,另外还需要针对元素硫 涂覆方式进行重新选择。
唐江
(重庆民丰化工有限责任公司,重庆 402660)
TANG Jiang (Chongqing Minfeng Chemical Co., Ltd., Chongqing 402660, China)
揖摘 要铱天然气中,在硫含量压力条件和温度超标的情况下,都会形成硫沉积现象,在元素硫大量沉积的背景下,会直接造成流体通 道堵塞问题,会直接发生采输系统严重腐蚀现象。为解决这种问题,需要通过电化学极化测试方法,全面开展碳钢腐蚀性能实验,对
3 结果与讨论
干的硫本身没有腐蚀性 (高温或超高温硫腐蚀除外),但 是一旦遇到 H2O、H2S 和 Fe2S3,它将作为催化剂,所引起的材 料腐蚀速率高达 55mm/a,这被认为是元素硫诱导腐蚀的典 型特性。1953 年元素硫的腐蚀性首次被发现,Farrer 将硫的 悬浊液作为钢和铁的浸蚀剂,发现 30益时含 20%悬浮硫的溶 液与含 3%盐酸溶液具有相同的腐蚀性,而且金属的腐蚀速 率随悬浮的硫含量的增加而增大。1978 年,MacDonald 进一 步对碳钢在湿硫条件下的腐蚀行为开展系统研究,发现灾难 性的元素硫腐蚀需要一定的孕育期,其腐蚀行为受元素硫的 粒径和溶液初始 pH 值的影响。20 世纪 80 年代,Hyne 研究发 现在 Cl-存在的条件下,元素硫的腐蚀特征对 pH 值的变化非 常敏感,并认为元素硫在中性 pH 值条件下的腐蚀速率较大, 且腐蚀速率随着 Cl-浓度的增大而线性增大。Kuster 发现材料 的腐蚀速率在含元素硫的无氧环境中随 Cl-浓度的增大,呈
硫对金属的腐蚀机理

硫对金属的腐蚀机理
硫对金属的腐蚀机理主要有以下几种:
1. 硫化物形成:硫化物是硫元素与金属形成的化合物,可以导致金属腐蚀。
硫化物会降低金属的电解质能,并在金属表面形成薄膜,防止金属继续被氧化,从而减缓腐蚀速度。
2. 氧化:硫与氧反应产生硫酸,硫酸是一种强酸,可以对金属产生腐蚀作用。
硫酸会与金属表面的氧发生反应,形成金属氧化物,从而导致金属腐蚀。
3. 腐蚀介质的酸化:硫化物和硫酸可以使腐蚀介质的PH值降低,导致腐蚀介质具有更强的腐蚀性。
酸性介质会增加金属表面的阳极反应,从而加速金属的腐蚀。
4. 高温腐蚀:在高温下,硫与金属反应速度加快,金属更容易被硫氧化物腐蚀。
此外,高温还可以促进硫氧化物的形成,进一步加剧金属的腐蚀。
需要注意的是,不同金属与硫的腐蚀机理可能有所不同,因为金属的化学性质不同。
同时,腐蚀机理可能还受到其他因素的影响,比如温度、湿度、氧气浓度等。
因此,要深入研究硫对金属的腐蚀机理,需要考虑到多个因素的综合影响。
锅炉的硫腐蚀资料

锅炉的硫腐蚀指烟气中的水蒸气和硫燃烧后生成的三氧化硫结合成的硫酸对锅炉的腐蚀。
最常见的硫腐蚀是发生在锅炉尾部受热面上的低温硫腐蚀。
低温硫腐蚀常发生在空气预热器的冷端及给水温度低的省煤器中。
在受热面的温度低于烟气的露点时,烟气中的水蒸气和硫燃烧后生成的三氧化硫结合成的硫酸会凝结在受热面上,严重地腐蚀受热面并造成“堵灰”。
当烟气中只含水蒸气而不含三氧化硫时,烟气露点实际上指的是烟气中水蒸气霹点,即烟气中水蒸气的结露(凝结)温度。
这个温度与烟气中所含水蒸气的分压有关。
水蒸气分压越高,露点温度也越高。
不同燃料燃烧生成烟气的水蒸气露点大致如下表所示。
烟气的水蒸气露点由上表可以看出,烟气中水蒸气露点温度不超过50℃,比锅炉的排烟温度低得多,因而单纯的水蒸气是很难在受热面上结露的。
烟气中如果有三氧化硫,情况就大不相同了。
燃料中硫燃烧后,生成二氧化硫。
在过量空气系数较大,过量氧气较多而温度又不太高的条件下,少量二氧化硫继续氧化生成三氧化硫:)/(8.19122322mol kJ SO O SO +⇔+ 这个反应是个可逆的放热反应,在温度高、氧量少的情况下很难进行;即使温度不高,供氧充足,生成的三氧化硫也很有限。
国内外实测数据表明,三氧化硫转化率[烟气中SO 3体积/(SO 3+SO 2)体积)对链条炉为1%~2%;对抛煤机炉为0.5%~1.5%;对煤粉炉为0.5%~1%;燃油炉为0.5%~2%。
烟气中的二氧化硫对受热面没有明显的腐蚀作用。
三氧化硫的含量虽然很小,但它能与烟气中的水蒸气结合成硫酸蒸气,会显著地提高烟气的露点温度。
只要有极少量的硫酸蒸气存在,烟气的露点(酸露点)就会提高到100℃以上。
露点温度的提高意味着硫酸蒸气遇到温度较高的壁面就可能结露,酸露不仅腐蚀金属壁面,而且会使烟气中的灰分凝结在金属壁面上,灰分越积越多,最后堵塞烟气通道。
为了避免低温硫腐蚀,可采用下列技术措施:(1)用热空气或蒸汽加热冷空气,提高空气预热器入口的空气温度,从而提高预热器壁面温度使之高于露点温度。
高温硫腐蚀
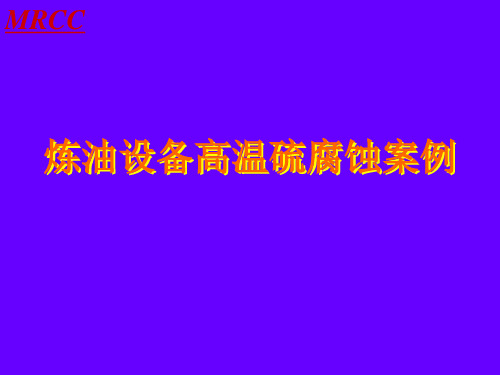
设备材质
➢ 铬含量越高,耐蚀性能越强。Cr含量大于5% 的合金钢具有较好的耐高温硫腐蚀性能。
➢ 一般选用Cr5MO、Cr9MO、Cr13、18-8等材料, ➢ 12CrMO、15CrMO、1.25Cr0.5MO、2.25Cr-1MO是
常用的耐热临氢用钢,不宜用在以高温硫腐蚀 为主的场合.
设备材质
渣油加氢装置:2003“4、19”事故
高温腐蚀主要部位
蒸馏装置: 240℃以上的管线 、设备。
重点监控部位:减 三、减四、减五、 减渣240℃以上的 管线、设备,尤其 注意280℃以上的 管线、设备。
高温腐蚀主要部位
焦化装置: 焦化装置是将减压渣油转化 为石油焦和油气的工艺装置 ,装置原料含硫量大,温度 高,主要腐蚀为典型的高温 硫腐蚀,主要有分馏塔250℃ 以上的侧线、循环线、从分 馏塔经进料泵、加热炉至焦 碳塔的高温渣油线及焦碳塔 底拿油线。
➢ 表现为腐蚀减薄为主。
高温硫腐蚀的几点规律
➢ (1)硫化物含量越高,腐蚀越高。 ➢ (2)温度越高,腐蚀速率越大; ➢ (3)管内介质流速越大,腐蚀越严重;(4)
弯头、大小头、三通、设备进出口接管等易产 生湍流、涡流部位,腐蚀速率高;直管段腐蚀 速率较小; ➢ (5)高温下碳钢腐蚀速率较大。 ➢ 设备材质是目前提高防腐性能的主要手段
•C、 三蒸馏装置:
•换13/1C壳程进口短管(20#钢)2000年2月18日因高温硫腐蚀 减薄穿孔,测厚为1.5mm。
•2000年8月2日减压渣油与减四连通线(20#)腐蚀减薄穿孔。
•2000年3月10日,渣油泵预热线(20#钢)腐蚀穿孔。
•1998年8月测厚发现减四泵(泵22、泵23)出口至一次换热器 (换12/1AB)弯头最薄处为1.3mm,更换为Cr5Mo。
硫腐蚀措施

硫腐蚀措施1. 简介硫腐蚀是指金属在含硫介质中发生化学反应而受到破坏的现象。
由于硫化物的形成,金属表面可能会出现腐蚀、渗透和脆化等现象,严重影响设备和结构的安全运行。
针对硫腐蚀问题,有一些常用的措施能有效地减少或防止腐蚀的发生,本文将介绍一些常见的硫腐蚀措施。
2. 硫腐蚀措施2.1 选用合适的材料选用抗硫化物腐蚀的材料是预防硫腐蚀的首要措施。
一些材料在含硫环境中具有较好的耐蚀性,如不锈钢、镍基合金等。
这些材料能够有效地防止硫腐蚀的发生,延长设备和结构的使用寿命。
2.2 表面涂层保护通过对金属表面进行表面涂层处理,能够有效地防止硫腐蚀的发生。
一些特殊的涂层材料,如聚合物涂层、铬化物涂层等,能够形成一层抗腐蚀的保护膜,防止硫化物与金属直接接触,减少硫腐蚀的风险。
2.3 设备与结构防腐层对于设备和结构来说,防腐层是防止硫腐蚀的重要手段之一。
通过给设备和结构表面涂上抗硫化物腐蚀的防腐涂层,能够有效地隔绝硫化物与金属的接触,减少腐蚀的风险。
常见的防腐涂层材料有环氧树脂、聚氨酯等。
2.4 控制硫腐蚀环境条件控制硫腐蚀环境条件是预防硫腐蚀的关键措施之一。
根据含硫介质的特性,可以通过控制温度、气氛、压力等因素来减少硫腐蚀的发生。
例如,在高温高压硫化物腐蚀环境中,降低温度和压力可以有效减缓硫腐蚀的速率。
2.5 定期维护和检测定期的维护和检测是确保硫腐蚀措施有效的重要环节。
及时发现腐蚀现象,对设备和结构进行维修和保养,可以有效延长其使用寿命。
此外,定期的腐蚀检测也能够及时掌握设备腐蚀状况,采取相应的防护措施。
3. 总结硫腐蚀是金属在含硫介质中受到化学反应而受损的现象,对设备和结构的安全运行造成严重威胁。
为了减少硫腐蚀带来的风险,我们可以采取一系列措施,如选用合适的材料、表面涂层保护、设备与结构防腐层、控制环境条件以及定期维护和检测等。
通过这些措施的综合应用,能够有效地防止硫腐蚀的发生,延长设备和结构的使用寿命。
硫化反应对金属腐蚀机理的影响研究
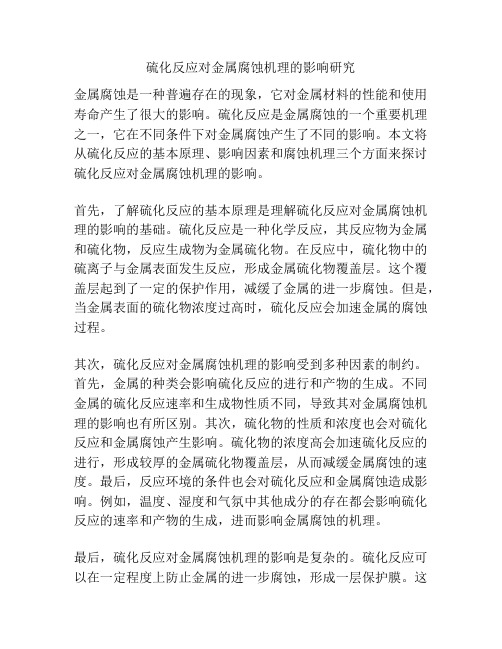
硫化反应对金属腐蚀机理的影响研究金属腐蚀是一种普遍存在的现象,它对金属材料的性能和使用寿命产生了很大的影响。
硫化反应是金属腐蚀的一个重要机理之一,它在不同条件下对金属腐蚀产生了不同的影响。
本文将从硫化反应的基本原理、影响因素和腐蚀机理三个方面来探讨硫化反应对金属腐蚀机理的影响。
首先,了解硫化反应的基本原理是理解硫化反应对金属腐蚀机理的影响的基础。
硫化反应是一种化学反应,其反应物为金属和硫化物,反应生成物为金属硫化物。
在反应中,硫化物中的硫离子与金属表面发生反应,形成金属硫化物覆盖层。
这个覆盖层起到了一定的保护作用,减缓了金属的进一步腐蚀。
但是,当金属表面的硫化物浓度过高时,硫化反应会加速金属的腐蚀过程。
其次,硫化反应对金属腐蚀机理的影响受到多种因素的制约。
首先,金属的种类会影响硫化反应的进行和产物的生成。
不同金属的硫化反应速率和生成物性质不同,导致其对金属腐蚀机理的影响也有所区别。
其次,硫化物的性质和浓度也会对硫化反应和金属腐蚀产生影响。
硫化物的浓度高会加速硫化反应的进行,形成较厚的金属硫化物覆盖层,从而减缓金属腐蚀的速度。
最后,反应环境的条件也会对硫化反应和金属腐蚀造成影响。
例如,温度、湿度和气氛中其他成分的存在都会影响硫化反应的速率和产物的生成,进而影响金属腐蚀的机理。
最后,硫化反应对金属腐蚀机理的影响是复杂的。
硫化反应可以在一定程度上防止金属的进一步腐蚀,形成一层保护膜。
这种保护膜可以减缓金属腐蚀的速率,延长金属材料的使用寿命。
但是,当硫化物的浓度超过一定限度时,硫化反应反而会加速金属的腐蚀过程,使金属材料迅速损失其性能和寿命。
另外,硫化反应还会导致金属材料的脆性增加,从而降低其强度和韧性。
综上所述,硫化反应对金属腐蚀机理有着重要的影响。
它能够在一定程度上减缓金属的腐蚀速率,延长金属材料的使用寿命。
但是,硫化反应的影响受到多种因素的制约,不同的金属、硫化物和环境条件都会对其产生不同的影响。
锅炉水冷壁的高温硫腐蚀原因及对策
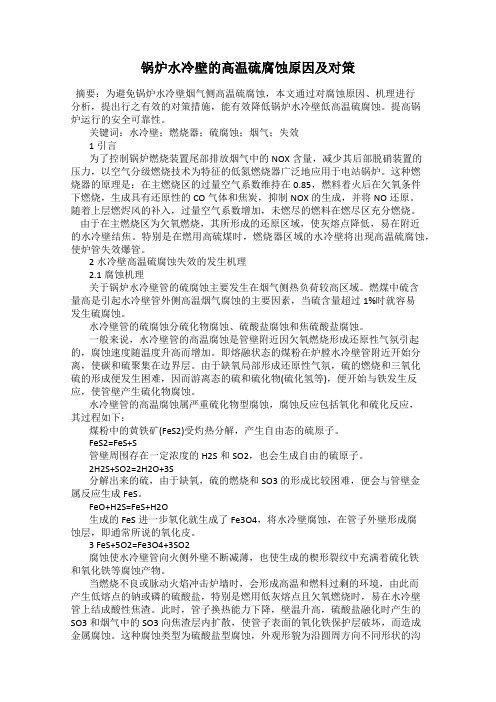
锅炉水冷壁的高温硫腐蚀原因及对策摘要:为避免锅炉水冷壁烟气侧高温硫腐蚀,本文通过对腐蚀原因、机理进行分析,提出行之有效的对策措施,能有效降低锅炉水冷壁低高温硫腐蚀。
提高锅炉运行的安全可靠性。
关键词:水冷壁;燃烧器;硫腐蚀;烟气;失效1引言为了控制锅炉燃烧装置尾部排放烟气中的NOX含量,减少其后部脱硝装置的压力,以空气分级燃烧技术为特征的低氮燃烧器广泛地应用于电站锅炉。
这种燃烧器的原理是:在主燃烧区的过量空气系数维持在0.85,燃料着火后在欠氧条件下燃烧,生成具有还原性的CO气体和焦炭,抑制NOX的生成,并将NO还原。
随着上层燃烬风的补入,过量空气系数增加,未燃尽的燃料在燃尽区充分燃烧。
由于在主燃烧区为欠氧燃烧,其所形成的还原区域,使灰熔点降低,易在附近的水冷壁结焦。
特别是在燃用高硫煤时,燃烧器区域的水冷壁将出现高温硫腐蚀,使炉管失效爆管。
2水冷壁高温硫腐蚀失效的发生机理2.1腐蚀机理关于锅炉水冷壁管的硫腐蚀主要发生在烟气侧热负荷较高区域。
燃煤中硫含量高是引起水冷壁管外侧高温烟气腐蚀的主要因素,当硫含量超过1%时就容易发生硫腐蚀。
水冷壁管的硫腐蚀分硫化物腐蚀、硫酸盐腐蚀和焦硫酸盐腐蚀。
一般来说,水冷壁管的高温腐蚀是管壁附近因欠氧燃烧形成还原性气氛引起的,腐蚀速度随温度升高而增加。
即熔融状态的煤粉在炉膛水冷壁管附近开始分离,使碳和硫聚集在边界层。
由于缺氧局部形成还原性气氛,硫的燃烧和三氧化硫的形成便发生困难,因而游离态的硫和硫化物(硫化氢等),便开始与铁发生反应,使管壁产生硫化物腐蚀。
水冷壁管的高温腐蚀属严重硫化物型腐蚀,腐蚀反应包括氧化和硫化反应,其过程如下:煤粉中的黄铁矿(FeS2)受灼热分解,产生自由态的硫原子。
FeS2=FeS+S管壁周围存在一定浓度的H2S和SO2,也会生成自由的硫原子。
2H2S+SO2=2H2O+3S分解出来的硫,由于缺氧,硫的燃烧和SO3的形成比较困难,便会与管壁金属反应生成FeS。
锅炉硫腐蚀原理

锅炉的硫腐蚀指烟气中的水蒸气和硫燃烧后生成的三氧化硫结合成的硫酸对锅炉的腐蚀。
最常见的硫腐蚀是发生在锅炉尾部受热面上的低温硫腐蚀。
低温硫腐蚀常发生在空气预热器的冷端及给水温度低的省煤器中。
在受热面的温度低于烟气的露点时,烟气中的水蒸气和硫燃烧后生成的三氧化硫结合成的硫酸会凝结在受热面上,严重地腐蚀受热面并造成“堵灰”。
当烟气中只含水蒸气而不含三氧化硫时,烟气露点实际上指的是烟气中水蒸气霹点,即烟气中水蒸气的结露(凝结)温度。
这个温度与烟气中所含水蒸气的分压有关。
水蒸气分压越高,露点温度也越高。
不同燃料燃烧生成烟气的水蒸气露点大致如下表所示。
烟气的水蒸气露点由上表可以看出,烟气中水蒸气露点温度不超过50℃,比锅炉的排烟温度低得多,因而单纯的水蒸气是很难在受热面上结露的。
烟气中如果有三氧化硫,情况就大不相同了。
燃料中硫燃烧后,生成二氧化硫。
在过量空气系数较大,过量氧气较多而温度又不太高的条件下,少量二氧化硫继续氧化生成三氧化硫:这个反应是个可逆的放热反应,在温度高、氧量少的情况下很难进行;即使温度不高,供氧充足,生成的三氧化硫也很有限。
国内外实测数据表明,三氧化硫转化率[烟气中SO3体积/(SO3+SO2)体积)对链条炉为1%~2%;对抛煤机炉为0.5%~1.5%;对煤粉炉为0.5%~1%;燃油炉为0.5%~2%。
烟气中的二氧化硫对受热面没有明显的腐蚀作用。
三氧化硫的含量虽然很小,但它能与烟气中的水蒸气结合成硫酸蒸气,会显著地提高烟气的露点温度。
只要有极少量的硫酸蒸气存在,烟气的露点(酸露点)就会提高到100℃以上。
露点温度的提高意味着硫酸蒸气遇到温度较高的壁面就可能结露,酸露不仅腐蚀金属壁面,而且会使烟气中的灰分凝结在金属壁面上,灰分越积越多,最后堵塞烟气通道。
为了避免低温硫腐蚀,可采用下列技术措施:(1)用热空气或蒸汽加热冷空气,提高空气预热器入口的空气温度,从而提高预热器壁面温度使之高于露点温度。
- 1、下载文档前请自行甄别文档内容的完整性,平台不提供额外的编辑、内容补充、找答案等附加服务。
- 2、"仅部分预览"的文档,不可在线预览部分如存在完整性等问题,可反馈申请退款(可完整预览的文档不适用该条件!)。
- 3、如文档侵犯您的权益,请联系客服反馈,我们会尽快为您处理(人工客服工作时间:9:00-18:30)。
1硫腐蚀的特点硫腐蚀贯穿于炼油全过程。
原油中的总硫含量与腐蚀性之间并无精确的对应关系,主要取决于含硫化合物的种类、含量和稳定性。
如果原油中的非活性硫易转化为活性硫,即使硫含量很低,也将对设备造成严重的腐蚀。
这就使硫腐蚀发生在炼油装置的各个部位。
因此,硫腐蚀涉及装置多,腐蚀环境多种多样,含硫化合物的转化关系复杂,给硫腐蚀的动力学和热力学研究、防腐蚀措施的制定以及加工含硫原油的设备选材带来很多困难。
在原油加工过程中,硫腐蚀不是孤立存在的。
硫和无机盐、环烷酸、氮化物、水、氢、氨等其它腐蚀性介质共同作用,形成多种复杂的腐蚀环境。
从腐蚀环境考虑硫腐蚀可分为高温(大于240℃)化学腐蚀、低温硫化氢电化学腐蚀以及两种比较特殊的腐蚀——硫酸露点腐蚀和连多硫酸腐蚀;从腐蚀形态考虑,硫腐蚀又可分为均匀腐蚀、点蚀、缝隙腐蚀、应力腐蚀开裂(SCC)以及由湿硫化氢引起的氢鼓泡(HB)、氢致开裂(HIC)、含硫化合物应力腐蚀开裂(SSCC)和应力导向氢致开裂(SOHIC)等。
2低温轻油部位的腐蚀与防护原油中存在的H2S以及有机含硫化合物在不同条件下逐步分解生成的H2S,与原油加工过程中形成的腐蚀性介质(如HCl,NH3等)和人为加入的腐蚀性(或可引起腐蚀的)介质(如乙醇胺、糠醛、水等)共同形成腐蚀性环境,在装置的低温部位(特别是气液相变部位)造成严重的腐蚀。
典型的有常减压蒸馏装置常、减压塔顶的HCl+H2S+H2O型腐蚀环境;催化裂化装置分馏塔顶的HCN+H2S+H2O型腐蚀环境;加氢裂化和加氢精制装置流出物空冷器的H2S+NH3+H2+H2O型腐蚀环境;干气脱硫装置再生塔、气体吸收塔的RNH2(乙醇胺)+CO2+H2S+H2O型腐蚀环境等。
2.1HCl+H2S+H2O型腐蚀环境这种腐蚀环境主要存在于常减压蒸馏装置塔顶循环系统和温度低于150℃的部位,如常压塔、初馏塔、减压塔顶部的塔体、塔板或填料以及塔顶冷凝冷却系统。
一般气相部位腐蚀较轻,液相部位腐蚀较重,气液相变部位即露点部位最为严重。
2.1.1腐蚀状况HCl和H2S的沸点都非常低(标准沸点分别为-84.95℃和-60.2℃)。
因此,在原油加工过程中形成的HCl和H2S均伴随着油气集聚在常压塔顶。
在110℃以下遇到蒸汽冷凝水会形成pH值达1~1.3的强酸性腐蚀介质,对设备产生腐蚀。
对于碳钢为均匀腐蚀,对于0Cr13钢为点蚀,对于奥氏体不锈钢则为氯化物应力腐蚀开裂。
有资料表明,在无工艺防腐蚀条件下,碳钢的腐蚀速率可达2 mm/a,常压塔碳钢管壳式冷却器管束进口部位腐蚀速率高达6.0~14.5 mm/a,腐蚀形态为均匀腐蚀;常压塔顶的Cr13浮阀出现点蚀,腐蚀速率为1.8~2.0 mm/a。
某炼油厂曾使用Cr18-Ni8钢作常压塔顶衬里,5年后出现大面积氯化物应力腐蚀开裂。
某炼油厂使用1Cr18Ni9Ti钢作常压塔顶空冷器管束,投用90天后管子与管板胀接过渡区全部发生脆断。
采用工艺防腐蚀后,常压塔顶空冷器管束腐蚀速率为0.1~0.3 mm/a,管壳式冷却器碳钢管束腐蚀速率为0.8 mm/a。
某炼油厂常压塔顶管壳式冷却器管束使用1Cr18Ni9Ti钢,在加强工艺防腐蚀措施后,使用5年后发生应力腐蚀开裂。
2.1.2工艺防腐蚀措施对于原油蒸馏塔顶的腐蚀控制技术,除搞好深度电脱盐外,仍然是“三注”,即在系统中注水、注缓蚀剂和注中和剂。
过去注入氨水是产生铵盐垢下腐蚀的主要原因,占设备破坏的80%,其腐蚀速率是均匀腐蚀的20倍。
垢下沉积物中硫化铁占70%~80%,其它是[wiki]焦炭[/wiki]和重质烃。
硫化铁是原油蒸馏塔顶系统中溶解度最小的盐,其溶解性取决于pH值和含硫化合物浓度。
腐蚀机理是由于干净或微覆盖区之间形成电位差电池。
但传统观点认为,中和盐引起了塔顶的许多问题。
这些盐水解使pH值为4,过量使用中和剂提高pH值,会引起硫化铁沉积,最终导致塔顶破坏。
一些研究结果表明,常压塔顶系统最佳pH值范围比过去推荐的范围(5.5~7.0)低,如表1所示。
表1常压塔顶系统推荐的最佳pH值H2S/mg.L-1 pH值20/50 5.1~5.6/4.9~5.4100/200 4.8~5.3/4.6~5.1由于常减压蒸馏装置塔顶腐蚀环境中氯离子的浓度较高,再加上各种应力的影响,极易造成氯离子应力腐蚀开裂,所以低温轻油部位的材质较难升级。
国内绝大部分炼油厂常减压塔顶冷凝冷却系统仍采用碳钢,因此以“一脱四注”为核心内容的传统工艺防腐蚀手段显得异常重要。
考虑到钠离子对二次加工装置加工工艺的影响,炼油厂已将“一脱四注”改为“一脱三注”。
“一脱”是原油深度脱盐,一方面是深度脱除钠盐。
由于钠离子易引起加氢脱硫催化剂的中毒,因此对原料油中的钠离子含量要求很严格。
例如某炼油厂加工进口含硫原油,要求原油经深度脱盐后,其原料油中钠离子含量小于1 mg/L。
另一方面,为减轻塔顶HCl带来的腐蚀,要求电脱盐装置不仅脱钠离子,而且有效脱除钙、镁、铁离子。
尽量降低塔顶冷凝冷却系统HCl的生成量。
目前炼油厂常减压蒸馏装置“三顶”大部分采用注氨,但其中和效果差,必须过量注入。
这样,生成的NH4Cl容易结垢,一方面容易引起堵塞,另一方面产生垢下腐蚀。
加工进口含硫原油后,塔顶冷凝冷却系统中H2S含量增加,结垢和腐蚀的问题更为突出。
有的炼油厂采用注有机胺,取得了很好的中和效果,但有机胺价格昂贵,因此有的炼油厂采用氨和有机胺按一定比例混注的方法,效果也较好。
部分炼油厂在“三顶”注入7019等水溶性缓蚀剂,但其保护面积小,膜完整性差,且膜修复困难。
有的炼油厂采用油溶性缓蚀剂,选择合适的注入位置,取得了较好的缓蚀效果。
国内新开发的中和缓蚀剂,既具有中和作用,又具有缓蚀作用,一剂多用,应用效果也较好。
国内炼油厂常减压蒸馏装置的“三剂”(破乳剂、缓蚀剂和中和剂)一般采用手工注入,很难做到定时定量。
新开发的“三剂”自动注入系统,可根据物流量自动调节药剂的注入量,在部分炼油厂试用,取得了较好的效果,但与信号的自动采集和反馈等智能注入系统相比,仍有很大的差距。
目前,洛阳石油[wiki]化工[/wiki]工程公司设备研究所正在进行这方面的研究工作,并已取得进展。
2.1.3材料防腐蚀原油蒸馏塔顶耐蚀金属材料的选择是过程设备选择的一个关键。
在欧美发达国家,这个部位的材料90年代以前一直选用Monel合金(UNS No.4400),设备壳体材料采用碳钢+Monel合金复合钢材,内件全部为Monel合金。
90年代初期,发现这种合金对湿硫化氢应力腐蚀开裂是敏感的,故在120℃以上不推荐使用。
某国外炼油厂的常减压蒸馏装置原设计为:塔体采用碳钢+Monel合金,内件仍采用Monel合金。
但在详细设计中,耐蚀金属材料壳体改成了碳钢+Hastelloy C-4合金,内件改为Hastelloy C-4合金(UNS No.6455)。
在日本,该部位的耐蚀材料选用SUS 405(0Cr13Al)和Monel等合金。
在常减压蒸馏装置塔顶冷凝冷却系统的选材中,国内在80年代和90年代不断有炼油厂在塔顶冷凝冷却系统尝试使用奥氏体不锈钢和铝镁合金,结果都以设备很快腐蚀穿孔、开裂而告终。
也有的炼油厂尝试使用钛合金换热器,但由于价格昂贵,很难推广。
对于塔顶冷凝冷却系统,国内目前比较一致的看法是,设备采用碳钢材质,加强[wiki]涂料[/wiki]的施工管理,严格控制“一脱三注”,基本上可以控制塔顶冷凝冷却系统的腐蚀。
2.2HCN+H2S+H2O型腐蚀环境原油中的含硫化合物在催化裂化的反应条件下形成H2S,同时一些氮化物也以一定的比例存在于裂解产物中,其中1%~2%的氮化物以HCN形式存在,从而在催化裂化装置吸收解吸系统形成HCN+H2S+H2O腐蚀环境。
该部位的温度为40~50℃,压力为1.6 MPa。
HCN的存在对H2S+H2O的腐蚀起了促进作用。
氰化物在碱性的H2S+H2O溶液中起两种作用:①溶解硫化铁保护膜,加速硫化氢的腐蚀,并产生有利于氢向钢中渗透的金属表面;②氰化物能除掉溶液中的缓蚀剂。
在吸收解吸系统,随着CN-浓度的增加,腐蚀性也提高。
当催化裂化原料中氮的总含量大于0.1%时,就会引起设备的严重腐蚀。
当CN-浓度大于500 mg/L时,明显促进腐蚀作用。
对这种腐蚀可采取以下工艺防腐蚀措施:①用水洗将氰化物脱除;②注入多硫化合物缓蚀剂,将氰化物消除。
也可采用材料防腐蚀措施:筒体采用碳钢(镇静钢)+3mm 0Cr13Al钢复合板或0Cr13钢,也可采用铬钼钢(12Cr2AlMoV),配用317焊条焊接,焊后750℃热处理,焊缝及热影响区的硬度应小于HB 200。
填料可采用0Cr13钢或渗铝碳钢。
但在HCN+H2S+H2O环境下,选用不锈钢焊条焊接碳钢或铬钼钢,极易发生硫化氢应力腐蚀开裂,应引起重视。
2.3RNH2+CO2+H2S+H2O型腐蚀环境腐蚀部位在干气及液化石油气脱硫的再生塔底部系统及富液管道系统(温度高于90℃,压力约0.2 MPa)。
在碱性介质下(pH值不小于8),腐蚀形态为由CO2及胺引起的应力腐蚀开裂和均匀减薄。
均匀腐蚀主要是CO2引起的,应力腐蚀开裂是由胺、CO2和H2S以及设备所受的应力引起的。
对操作温度高于90℃的碳钢设备及管道,进行焊后消除应力热处理,防止碱性条件下由碳酸盐引起的应力腐蚀开裂。
3湿硫化氢的腐蚀与防护湿硫化氢腐蚀环境,即H2S+H2O型的腐蚀环境,是指水或含水物流在露点以下与H2S 共存时,在[wiki]压力容器[/wiki]与管道中产生的腐蚀环境。
湿硫化氢环境广泛存在于炼油厂二次加工装置的轻油部位,如流化催化裂化装置的吸收稳定部分,产品精制装置中的干气及液化石油气脱硫部分,酸性水汽提装置的汽提塔,加氢裂化装置和加氢脱硫装置冷却器、高压分离器及其下游的设备。
3.1腐蚀机理在H2S+H2O腐蚀环境中,碳钢设备发生两种腐蚀:均匀腐蚀和湿硫化氢应力腐蚀开裂。
开裂的形式包括氢鼓泡、氢致开裂、硫化物应力腐蚀开裂和应力导向氢致开裂。
氢鼓泡是由于含硫化合物腐蚀过程析出的氢原子向钢中渗透,在钢中的裂纹、夹杂、缺陷等处聚集并形成分子,从而形成很大的膨胀力。
随着氢分子数量的增加,对晶格界面的压力不断增高,最后导致界面开裂,形成氢鼓泡,其分布平行于钢板表面。
氢鼓泡的发生并不需要外加应力。
氢致开裂是由于在钢的内部发生氢鼓泡区域,当氢的压力继续增高时,小的鼓泡裂纹趋向于相互连接,形成阶梯状特征的氢致开裂。
钢中MnS夹杂的带状分布会增加氢致开裂的敏感性。
氢致开裂的发生也无需外加应力。
硫化物应力腐蚀开裂是湿硫化氢环境中产生的氢原子渗透到钢的内部,溶解于晶格中,导致氢脆,在外加应力或残余应力作用下形成开裂。
它通常发生在焊道与热影响区等高硬度区。