射线检测及基础知识总结
射线无损检测重点工作总结
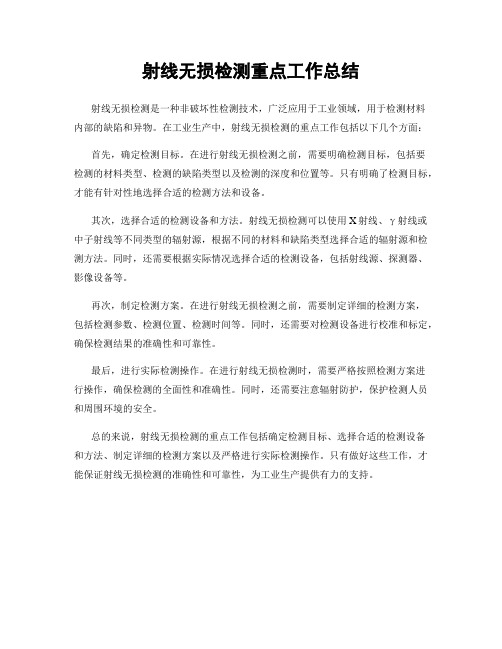
射线无损检测重点工作总结
射线无损检测是一种非破坏性检测技术,广泛应用于工业领域,用于检测材料
内部的缺陷和异物。
在工业生产中,射线无损检测的重点工作包括以下几个方面:首先,确定检测目标。
在进行射线无损检测之前,需要明确检测目标,包括要
检测的材料类型、检测的缺陷类型以及检测的深度和位置等。
只有明确了检测目标,才能有针对性地选择合适的检测方法和设备。
其次,选择合适的检测设备和方法。
射线无损检测可以使用X射线、γ射线或中子射线等不同类型的辐射源,根据不同的材料和缺陷类型选择合适的辐射源和检测方法。
同时,还需要根据实际情况选择合适的检测设备,包括射线源、探测器、影像设备等。
再次,制定检测方案。
在进行射线无损检测之前,需要制定详细的检测方案,
包括检测参数、检测位置、检测时间等。
同时,还需要对检测设备进行校准和标定,确保检测结果的准确性和可靠性。
最后,进行实际检测操作。
在进行射线无损检测时,需要严格按照检测方案进
行操作,确保检测的全面性和准确性。
同时,还需要注意辐射防护,保护检测人员和周围环境的安全。
总的来说,射线无损检测的重点工作包括确定检测目标、选择合适的检测设备
和方法、制定详细的检测方案以及严格进行实际检测操作。
只有做好这些工作,才能保证射线无损检测的准确性和可靠性,为工业生产提供有力的支持。
射线检测培训

二、射线检测设备和器材
18
4、X射线管的焦点:(P34) a、实际焦点—阳极靶上受电子轰击的部分。 b、有效焦点—实际焦点在垂直于管轴线方向上的投影。 c、焦点大,利于散热,管电流可以较大;焦点小,散热 条件差,管电流不能太大。 d、焦点形状和尺寸取决于灯丝形状和尺寸,圆形和正方 形焦点尺寸为 a(a为直径或边长);长方形和椭圆形焦点 尺寸为( a和b为边长或轴长)。
状谱,由一个或几个特定的波长组成。 c、连续X射线的能量(波长)取决于管电压;标识X射线的能
量(波长)取决于靶材,与管电压无关。
一、射线检测物理基础
6、连续X射线的最短波长:
minV1(K2.4V)
0
(A)
4
7、X射线的产生效率:(P6) 0ZV
式中:η0≈1.1~1.4×10-6,
V—管电压(KV)
5
8、X射线和γ射线的相同和不同之处:(习题P20—371)
a、相同之处:X射线和γ射线都是电磁波,它们具有相同 的性质,如不可见、依直线传播、不带电、能穿透物质、 能使物质电离、使胶片感光、能发生生物效应等。
b、不同之处:
⑴、产生机理不同,X射线是高速电子与物质碰撞产生的; 而γ射线是放射性物质原子核衰变时放射出来的。
二、射线检测设备和器材
20
9、X射线机管电压和管电流:(P43—44)
①、管电压调节是通过调节高压变压器初级线圈并联的自耦
变压器的电压来实现的。
管电压越高,电子运动速度越快,产生的X射线能量越高,穿透力越大。
②、管电流是通过调节灯丝变压器电压从而调节灯丝加热电
流来实现的。
管电流越大,产生的X射线强度就越大。
解:设增厚前胶片接受
增厚之后胶片接受的照
射线检测及基础知识总结

第一部分金属材料及热处理基本知识一,材料性能:通常所指的金属材料性能包括两个方面:使用性能即为了保证机械零件、设备、结构件等能够正常工作,材料所应具备的性能,主要有力学性能(强度、硬度、刚度、塑性、韧性等),物理性能(密度、熔点、导热性、热膨胀性等)。
化学性能(耐腐蚀性)使用性能决定了材料的应用范围,使用安全可靠性和寿命。
工艺性能即材料被制造成为零件、设备、结构件的过程中适应的各种冷、热加工的性能,如铸造、焊接、热处理、压力加工、切削加工等方面的性能。
工艺性能对制造成本、生产效率、产品质量有重要影响。
二,材料力学基本知识承压类特种设备材料的力学性能指标主要有强度、硬度、塑性、韧性等。
可以通过力学性能试验测定。
1,强度金属的强度是指金属抵抗永久变形和断裂的能力。
材料强度指标可以通过拉伸试验测出。
抗拉强度σb和屈服强度σs是评价材料强度性能的两个主要指标。
一般金属材料构件都是在弹性状态下工作的。
是不允许发生塑性变形,所以机械设计中一般采用屈服强度σs作为强度指标,并加安全系数。
2,塑性材料在载荷作用下断裂前发生不可逆永久变形的能力。
评定材料塑性的指标通常用伸长率和断面收缩率。
对必须承受强烈变形的材料,塑性优良的材料冷压成型的性能好。
3,硬度金属的硬度是材料抵抗局部塑性变形或表面损伤的能力。
硬度与强度有一定的关系,一般情况下,硬度较高的材料其强度也较高,所以可以通过测试硬度来估算材料强度。
另外,硬度较高的材料耐磨性也较好。
工程中常用的硬度测试方法有以下四种1、布氏硬度HB (2)洛氏硬度HRc(3)维氏硬度HV(4)里氏硬度HL4,冲击韧性指材料在外加冲击载荷作用下断裂时消耗的能量大小的特性。
材料的冲击韧性通常是在摆锤式冲击试验机是测定的,摆锤冲断试样所作的功称为冲击吸收功。
以Ak表示,Sn为断口处的截面积,则冲击韧性ak=Ak/Sn。
在承压类特种设备材料的冲击试验中应用较多。
5、弯曲试验是焊接接头力学性能试验的主要项目。
射线检测基础知识课件

公共安全
射线检测技术可用于公 共安全检查,如地铁站 、体育馆等场所的安全 检查。
环境监测领域应用
1 2
空气质量监测
射线检测技术可用于监测空气质量,如PM2.5、 气态污染物等。
水质监测
射线检测技术可用于监测水质,如总大肠菌群、 重金属等。
01
中子射线是一种粒子流 ,其质量约为氢原子质 量的1.14倍。
02
中子射线具有很强的穿 透性,能够穿透一定厚 度的重金属和混凝土等 物质。
03
中子射线具有很强的诱 变作用,能够使DNA发 生变异,导致生物体发 生突变。
04
中子射线还具有热效应 和辐射损伤等作用。
电子射线的性质
电子射线是一种带负电的粒子流,其能量范围在几兆电 子伏特到几百千电子伏特之间。
类型
X射线探伤机可分为固定 式、移动式和便携式。
应用
广泛应用于航空、航天、 汽车、电子等领域。
γ射线探伤机
工作原理
γ射线探伤机利用γ射线穿 透金属材料,检测其内部 缺陷。
类型
γ射线探伤机可分为放射性 同位素源和加速器源两种 。
应用
广泛应用于石油、化工、 电力等领域。
中子射线探伤机
工作原理
中子射线探伤机利用中子射线穿 透金属材料,检测其内部缺陷。
工业领域应用
零部件检测
射线检测技术可用于检测工业生产中的零部件,如铸件、焊接件 等,检测是否存在气孔、裂纹等缺陷。
设备维护
射线检测可对设备内部结构进行检测,提前发现设备潜在的故障和 问题,为设备维护和修理提供帮助。
产品质量控制
射线检测可对生产过程中的产品进行实时监测,确保产品质量符合 标准。
射线检测专业知识点
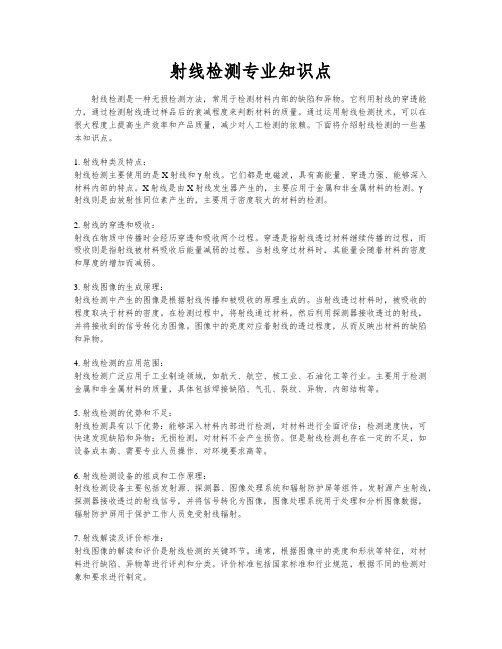
射线检测专业知识点射线检测是一种无损检测方法,常用于检测材料内部的缺陷和异物。
它利用射线的穿透能力,通过检测射线透过样品后的衰减程度来判断材料的质量。
通过运用射线检测技术,可以在很大程度上提高生产效率和产品质量,减少对人工检测的依赖。
下面将介绍射线检测的一些基本知识点。
1. 射线种类及特点:射线检测主要使用的是X射线和γ射线。
它们都是电磁波,具有高能量、穿透力强、能够深入材料内部的特点。
X射线是由X射线发生器产生的,主要应用于金属和非金属材料的检测。
γ射线则是由放射性同位素产生的,主要用于密度较大的材料的检测。
2. 射线的穿透和吸收:射线在物质中传播时会经历穿透和吸收两个过程。
穿透是指射线透过材料继续传播的过程,而吸收则是指射线被材料吸收后能量减弱的过程。
当射线穿过材料时,其能量会随着材料的密度和厚度的增加而减弱。
3. 射线图像的生成原理:射线检测中产生的图像是根据射线传播和被吸收的原理生成的。
当射线透过材料时,被吸收的程度取决于材料的密度。
在检测过程中,将射线通过材料,然后利用探测器接收透过的射线,并将接收到的信号转化为图像。
图像中的亮度对应着射线的透过程度,从而反映出材料的缺陷和异物。
4. 射线检测的应用范围:射线检测广泛应用于工业制造领域,如航天、航空、核工业、石油化工等行业。
主要用于检测金属和非金属材料的质量,具体包括焊接缺陷、气孔、裂纹、异物、内部结构等。
5. 射线检测的优势和不足:射线检测具有以下优势:能够深入材料内部进行检测,对材料进行全面评估;检测速度快,可快速发现缺陷和异物;无损检测,对材料不会产生损伤。
但是射线检测也存在一定的不足,如设备成本高、需要专业人员操作、对环境要求高等。
6. 射线检测设备的组成和工作原理:射线检测设备主要包括发射源、探测器、图像处理系统和辐射防护屏等组件。
发射源产生射线,探测器接收透过的射线信号,并将信号转化为图像,图像处理系统用于处理和分析图像数据,辐射防护屏用于保护工作人员免受射线辐射。
射线检测—射线检测基础知识(无损检测课件)
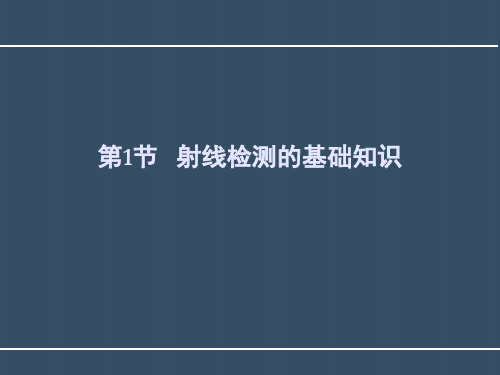
♫ 射线检测主要适用于体积型缺陷,如气孔等的检测;在特 定的条件下,也可检测裂纹、未焊透、未熔合等缺陷。
♫ 工业应用的射线检测技术有三种:X射线检测,γ射线检测、 中子射线检测。
2. 物理基础
♫ 射线分类:
X射线和γ射线都是波长极短的电磁波,从现代物理学波粒 二相性的观点看也可将其视为能量极高的光子束流,两者 基本区别在于X射线是从X射线管中产生的,而γ射线是从 放射性同位素的原子核中放射出来的。
第1节 射线检测机
➢ 产生X射线的基本过程是: 发射电子→电子高速飞向阳极→撞击阳极靶→产生X射线
3. 设备器材
➢ 由X射线管所发出的X射线能谱为连续谱,因其波长分布 是连续的。连续谱的最短波长λmin与管电压千伏值(kVP) 的关系为
λmin=12.4/kVP ➢ 管电压越高,最短波长λmin的值就越小,平均波长越短,X
1. 概述
♫ 射线检测技术特点:
➢ 对被检验工件的材料、形状、表面状态无特殊要求; ➢ 检测结果显示直观; ➢ 检测技术和检测工作质量可以自我检测。
1. 概述
♫ 射线检测是利用射线探测零件内部缺陷的无损探伤方法, 利用X射线、γ射线和中子射线易于穿透物体和穿透物体后 的衰减程度不同,使胶片感光程度的不同来探测物体内部 的缺陷,对缺陷的种类、大小、位置等进行判断。
第1节 射线检测的基础知识
1. 概述
♫ 射线检测技术四部分:射线照相检测技术;射线实时
成像检测技术;层析射线检测技术;辐射测量技术。
♫ 射线检测技术应用类型包括:
➢ 缺陷检验:铸造、焊接等工艺; ➢ 测量:厚度、结构与尺寸、密度等; ➢ 检查:机场、车站、海关安全检查; ➢ 动态研究:爆炸、核技术、铸造工艺等。
RT2理论知识 第1章 射线检测的物理基础
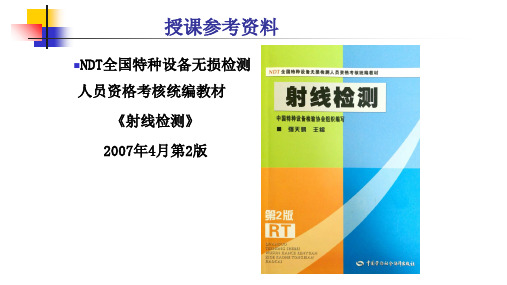
射线向四周辐射。
1.2.2 X射线的产生及其特点
1.2.2 X射线的产生及其特点
1.2.2 X射线的产生及其特点
1.2.2 X射线的产生及其特点
1.2.2 X射线的产生及其特点
1.2.2 X射线的产生及其特点
1. <10KeV
光电效应为主
2. 2. 10~100KeV KeV↑,光电↓
3. >100KeV
康普顿为主
4. 1Mev
康普顿几率最大
5. >1Mev
KeV↑,康普顿↓,电子对↑
6. 10Mev
康普顿几率与电子对几率相同
7. >10Mev
以电子对为主
1.3.5 各种相互作用发生的相互概率
各种不同效应对射线照相量的影响
1.2.3 γ射线的产生及其特点
1.2.3 γ射线的产生及其特点
1.3 射线与物质的相互作用
1.吸收与散射; 2.射线与物质的作用形式; 3.强度衰减规律
1.3 射线与物质的相互作用
1.3.1 光电效应
光电效应的发生概率随光子能量增大而减小,随原子序数Z增大而增大。
1.3.2 康普顿效应
1.3.5 各种相互作用发生的相互概率
三种效应的发生概率与入射光子的能量和原子序数有关:
1.对于低能量射线、高原子序数物质,光电效应占优势; 2.对于中等能量射线、低原子序数物质,康普顿效应占优势; 3.对于高能量射线、高原子序数物质,电子对效应占优势;
1.3.5 各种相互作用发生的相互概率
射线在钢中各种效应的发生几率
原子核的构成 原子核由更小的两种粒子:质子和中子
射线检测知识点
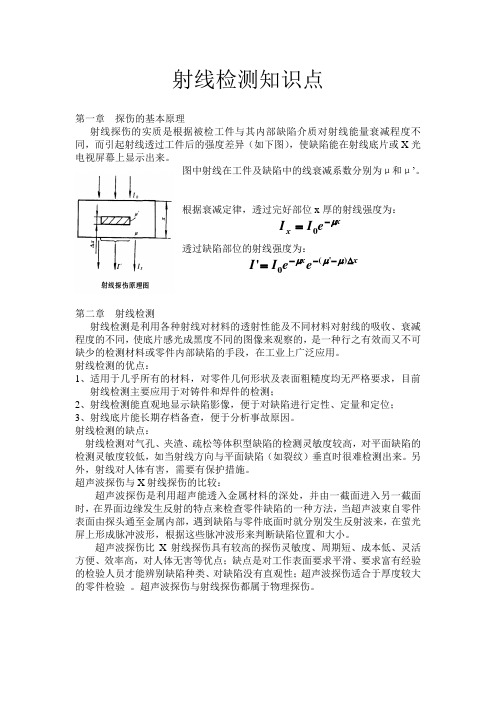
射线检测知识点第一章 探伤的基本原理射线探伤的实质是根据被检工件与其内部缺陷介质对射线能量衰减程度不同,而引起射线透过工件后的强度差异(如下图),使缺陷能在射线底片或X 光电视屏幕上显示出来。
图中射线在工件及缺陷中的线衰减系数分别为μ和μ’。
根据衰减定律,透过完好部位x 厚的射线强度为:透过缺陷部位的射线强度为:第二章 射线检测射线检测是利用各种射线对材料的透射性能及不同材料对射线的吸收、衰减程度的不同,使底片感光成黑度不同的图像来观察的,是一种行之有效而又不可缺少的检测材料或零件内部缺陷的手段,在工业上广泛应用。
射线检测的优点:1、适用于几乎所有的材料,对零件几何形状及表面粗糙度均无严格要求,目前射线检测主要应用于对铸件和焊件的检测;2、射线检测能直观地显示缺陷影像,便于对缺陷进行定性、定量和定位;3、射线底片能长期存档备查,便于分析事故原因。
射线检测的缺点:射线检测对气孔、夹渣、疏松等体积型缺陷的检测灵敏度较高,对平面缺陷的检测灵敏度较低,如当射线方向与平面缺陷(如裂纹)垂直时很难检测出来。
另外,射线对人体有害,需要有保护措施。
超声波探伤与X 射线探伤的比较:超声波探伤是利用超声能透入金属材料的深处,并由一截面进入另一截面时,在界面边缘发生反射的特点来检查零件缺陷的一种方法,当超声波束自零件表面由探头通至金属内部,遇到缺陷与零件底面时就分别发生反射波来,在萤光屏上形成脉冲波形,根据这些脉冲波形来判断缺陷位置和大小。
超声波探伤比X 射线探伤具有较高的探伤灵敏度、周期短、成本低、灵活方便、效率高,对人体无害等优点;缺点是对工作表面要求平滑、要求富有经验的检验人员才能辨别缺陷种类、对缺陷没有直观性;超声波探伤适合于厚度较大的零件检验 。
超声波探伤与射线探伤都属于物理探伤。
xx e I I μ-=0x x ee I I ∆---=)'(0'μμμ第一节射线检测的物理基础一、射线的种类和频谱波长较短的电磁波叫射线。
- 1、下载文档前请自行甄别文档内容的完整性,平台不提供额外的编辑、内容补充、找答案等附加服务。
- 2、"仅部分预览"的文档,不可在线预览部分如存在完整性等问题,可反馈申请退款(可完整预览的文档不适用该条件!)。
- 3、如文档侵犯您的权益,请联系客服反馈,我们会尽快为您处理(人工客服工作时间:9:00-18:30)。
基础知识力学性能指标有:强度、硬度、塑性、韧性应力腐蚀脆性断裂;由于拉应力与介质腐蚀联合作用引起的低应力脆性断裂叫做应力腐蚀。
应力腐蚀产生的必要条件:1元件承受拉应力的作用2具有与材料种类相匹配的特定腐蚀介质环境3材料对应力腐蚀的敏感程度。
对钢材而言应力腐蚀的敏感性与的成分、组织及热处理情况有关。
热处理是将固态金属及合金按预定要求进行加热,保温和冷却,以改变其内部组织,从而获得所要求性能的一种工艺过程。
热处理的基本工艺过程加热,保温和冷却三个阶段构成的,温度和时间是影响热处理的主要因素处理工艺分:退火、正火、淬火、回火、化学热处理退火目的:均匀组织、降低硬度、消除内应力、改善切削加工性能。
消除应力退火目的消除焊接过程中产生的内应力、扩散焊缝的氢,提高焊缝抗裂性和韧性,改善焊缝和热影响区的组织,稳定结构形状。
正火主要目的细化晶粒,均匀组织,降低内应力承压类特种设备常用材料应具有的特点1足够的强度2良好的韧性 3良好的加工工艺性能 4良好的低倍组织和表面质量5良好的耐高温性6良好的抗腐蚀性能。
药皮的作用:稳弧作用、保护作用、冶金作用、掺合金作用、改善焊接工艺性能。
手工电弧焊的焊接规范:焊接电流、电弧电压、焊条直径、焊接速度、焊接层数。
坡口的形式的选择要考虑以下因素:①.保证焊透②.充填焊缝部位的金属要尽量少③.便于施焊,改善劳动条件④、应尽量减少焊接变形量。
焊接变形和应力的形成: 1、焊件上的温度分布不均匀2、熔敷金属的收缩3、金属组织的转变4、焊件的刚性拘束焊接应力的控制措施:1.合理的装配与焊接顺序 2.焊前预热消除焊接应力的方法:1、热处理法 2、机械法 3、振动法控制焊接质量的工艺措施1预热 2焊接能量参数 3多层焊多道焊4紧急后热 5焊条烘烤和坡口清洁焊后热处理有利作用1减轻残余应力2改善组织,降低淬硬性3减少扩散氢低合金钢的焊接特点1热影响区的淬硬倾向比较大2容易出现冷裂纹产生冷裂纹的主要原因;1氢的聚集 2淬硬组织 3 焊接应力大奥氏体不锈钢的焊接时,防止或减少晶间腐蚀的主要措施1使焊缝形成双相组织 2严格控制含碳量 3添加稳定剂4焊后热处理 5采用正确的焊接工艺奥氏体不锈钢的焊接时,防止产生热裂纹的主要措施;1在焊缝中加入形成铁素体的元素 2减少母材和焊缝的含碳量3严格控制焊接规范锅炉定义:利用各种燃料、电或其它能源,将所盛装的液体加热到一定参数,并承载一定压力的密闭设备,其范围规定为容积大于或等于30L的承压蒸汽锅炉;出口水压大于或等于(表压),且额定功率大于或等于的承压热水锅炉;有机热载体锅炉。
2,锅炉的特点1连续工作;2高压、高温、工作条件恶劣;3具有爆炸危险性;4破坏性极大。
锅炉的主要参数容量、压力、温度锅炉的三大附件安全阀、压力表、水位计压力容器的含义:盛装气体或液体。
承受一定压力的密闭设备,其范围规定为最高工作压力Pw≥,且压力与容积的乘积≥ Mpa·L的气体,液化气体或最高温度≥标准沸点的液体的固定式容器和移动式容器;盛装公称工作压力≥,且压力与容积的乘积≥·L的气体,液化气体和标准沸点≤60度的液体的气瓶,医用氧舱等,可以认为这个规定是对压力容器作出的最权威的定义。
影响压力容器设计的主要工艺参数 1压力2温度 3直径压力管道的定义:指利用一定的压力,用于输送气体或液体的管状设备,其范围规定为最高工作压力大于或等于(表压)的气体,液化气体,蒸汽介质或可燃,易燃,有毒,有腐蚀性,最高工作温度高于或等于标准沸点的液体介质,且公称直径大于25mm的管道。
无损检测的定义在不损坏工件的前提下,以物理或化学方法为手段,借助先进的技术和设备器材,对工件的内部及表面的结构,性质,状态进行检查和测试的方法称为无损检测。
无损检测的目的1保证产品质量2保障使用安全3改进制造工艺4降低生产成本无损检测的应用特点1无损检测要与破坏性检测相结合2正确选用实施无损检测的时机3选用最恰当的无损检测方法4综合应用各种无损检测方法射线照相应用了射线的那些性质 1在真空中以光速直线传播;2不带电,不受电场和磁场的影响;3不可见,具有极大的能量,能穿透可见光不能穿透的物体;4在穿透物质的过程中,会与物质发生复杂的物理和化学作用,射线检测知识X射线和γ射线的相同点:1、都是电磁波,本质相同;2、都具有反射,折射等光学性质;3都能使胶片感光;4都是电离辐射能对人和生物造成危害; 5穿过物体时具有相同的衰减规律. X射线和γ射线的不同点 1产生方式不同;2能量不同:X--可控,可调,取决于管电压;γ--不可控,不可调,取决于源的性质; 3强度不同: X--可控,可调,取决于U,i, Z;γ--随时间变化; 4波谱形式不同射线检测的优点1可直接得到缺陷的直观图象,检测结果缺陷形象直观,定性,定量,定位准确;2检测结果可以长期保存;3检测灵敏度高;4工业TV可实现自动检测,效率高射线检测的局限性; 1不能检出与射线方向垂直的面状缺陷;如钢板的分层;2不适用于钎焊,摩擦焊,爆炸焊,锻件,轧制等方法加工的构件;3检测周期长,成本高4对人体有害,需要采取防护措施。
影响缺陷检出率的因素:1底片像质计灵敏度2工艺参数选择的正确性(透照方向、焦距等)3良好的观片条件4评片人员的判断能力如何提高照片灵敏度:1选择低能射线 2降低散射线 3选择合适的透照角度 4选择适合的胶片 5选择适合的显影条件 6增大底片黑度 7选择适合的焦距 8屏与片贴紧些 9选择合适的曝光量影响射线照片灵敏度的主要因素:1射线能量 2焦距 3增感屏 4胶片类型 5控制散射线 6暗室处理影响射线照相灵敏度的三大要素射线照相对比度(缺陷影像与其周围背景的黑度差);射线照相不清晰度(影像轮廓边缘黑度过渡区的宽度)射线照相颗粒度(影像黑度的不均匀程度)主因对比度影响因素:射线能量μ、透照方向上的缺陷ΔT、散射比n胶片对比度影响因素:胶片种类、显影条件、底片黑度几何不清晰度影响因素; 源的大小df、源到工件表面的距离L1、工件表面到胶片的距离L2固有不清晰度的影响因素:射线能量μ、增感屏种类、屏一片贴紧程度颗粒度的影响因素:胶片系统、射线能量μ、曝光量、底片黑度能量的提高对射线照相灵敏度有不利影响:随着管电压的升高,衰减系数μ减小,对比度△D降低,固有不清晰度Ui增大,底片颗粒度也将增大,其结果是射线照相灵敏度下降。
因此,从灵敏度角度考虑X射线能量的选择的原则是:在保证穿透力的前提下,选择能量较低的X射线。
胶片系统是指包括射线胶片、增感屏(材质和厚度)、和冲洗条件(方式、配方、时间、温度)的组合。
焦距的选择主要考虑的因素是:1、几何不清晰度Ug、透照方式、工件的几何形状选择透照方式时应综合考虑各方面的因素, 1.照相灵敏度2.缺陷检出特点3.透照厚度差和横向裂纹检出角4.一次透照长度5.操作方便性6.试件及探伤设备具体情况曝光曲线的使用条件:1、所使用的X射线探伤机2、一定的焦距3、一定的胶片类型4、一定的增感方式5、所使用的冲洗条件⑹基准黑度散射线是如何产生的:射线在穿透物质过程中与物质相互作用会产生吸收和散射主要是由康普顿效应造成的,最大的散射线源往往是试件本身,散射线可分前散射、背散射、边蚀散射。
散射线的控制措施:1.选择合适的射线能量2.使用铅箔增感屏3、背防护铅板4.铅罩和光阑 5.厚度补偿物 6.滤板7.遮蔽物8.修磨试件焊缝透照的基本操作过程1.试件检查及清理2.划线3.像质计和标记摆放4.贴片5.对焦6.散射线防护7.曝光大厚度比试件的透照技术1.适当提高管电压技术2.双胶片技术3.补偿技术暗室处理程序主要有:显影、停显、定影、水洗和干燥五个过程。
显影液的组成:显影剂、保护剂、促进剂、和抑制剂显影剂的作用是将已感光的卤化银还原成金属银。
有米吐尔、菲尼酮、对苯二酚保护剂的作用是阻止显影剂与进入显影液的氧发生作用,使其不被氧化。
最常用的保护剂是亚硫酸钠。
促进剂的作用是增强显影剂的显影能力和速度。
硼砂为软性促进剂,碳酸钠为中性促进剂,氢氧化钠为硬性促进剂。
抑制剂的作用是抑制灰雾,常用的抑制剂包括溴化钾、苯丙三氮唑等。
影响显影的因素;1、配方2、显影时间、3、温度、4、搅动情况5、显影液老化程度定影液有四种组分:定影剂、保护剂、坚膜剂、酸性剂定影液常用的定影剂为硫代硫酸钠,又称大苏打或海波。
保护剂的作用保护硫代硫酸钠在酸性溶液中易发生分解析出硫而失效,常用的保护剂为无水亚硫酸钠,坚膜剂的作用在定影过程中,胶片乳剂层吸水膨胀,易造成划伤和药膜脱落,降低胶片的吸水性,干燥起来更容易。
常用的坚膜剂有硫酸铝钾酸性剂的作用为中和停显阶段未除净的显影液碱性物质,通常是醋酸和硼酸。
影响定影的因素主要有:定影时间,定影温度,定影液老化程度,定影液的搅动。
评片工作的基本要求 1底片质量要求2设备环境条件要求和人员条件要求底片质量检查1像质计灵敏度检查2.黑度检查3.标记检查4、伪缺陷识别检查5背散射防护检查6、搭接情况检查评片工作条件: 1、环境 2、观片灯3、放大镜4、遮光板5、直尺 6、记号笔7、手套评片的基本操作 1通览底片2影像细节观察影像细节观察采用方法:1.调节观片灯亮度,寻找最适合观察的透过光强;2.用纸框等物体遮挡住细节部位邻近区域的透过光线; 3.使用放大镜进行观察;4.移动底片,不断改变观察距离和角度焊接定义:两个分离的物体通过原子或分子之间的结合和扩散造成永久性连接的工艺过程焊缝的外部缺陷焊瘤、咬边、焊穿、凹陷、填充未满、偏焊、错口焊缝的内部缺陷,裂纹、未熔合、未焊透、夹渣和气孔焊接缺陷对锅炉压力容器安全的影响主要表现在三个方面 1由于缺陷的存在,减少了焊缝的承载截面积,削弱了静力拉仲强度。
2是由于缺陷形成缺口,缺口尖端会发生应力集中和脆化现象,容易产生裂纹并扩展。
3是缺陷可能穿透筒壁,发生泄漏,影响致密性冷裂纹产生原因拘束应力、淬硬组织、扩散氢常见伪缺陷影像 1划痕 2 压痕 3折痕 4水迹 5静电感光 6 显影斑纹 7显影液沾染 8 定影液沾染 9 增感屏伪缺陷常用的焊接方法:手工电弧焊、手工钨极氩弧焊、埋弧自动焊、自动钨极氩弧焊等。
常见的焊接位置:板分为平焊、立焊、横焊和仰焊。
管子的焊接分管轴线水平固定焊、管轴线垂直固定焊和管轴线水平转动焊。
管轴线水平固定焊有称为全位置焊。
辐射防护的目的: 1防止有害的确定性效应;2限制随机性效应的发生率使之达到被认为可以接受的水平。
辐射防护的基本原则:1辐射实践的正当化; 2辐射防护的最优化;3个人剂量限值。
影响辐射损伤的因素: 1辐射性质:2剂量大小:3剂量率大小:4照射方法:5照射部位: 6照射面积辐射防护的基本方法 1. 时间防护:缩短人体接触射线的时间。