铸钢件粘冷铁机理浅析及防止措施
铸钢件质量分析及质量改进措施
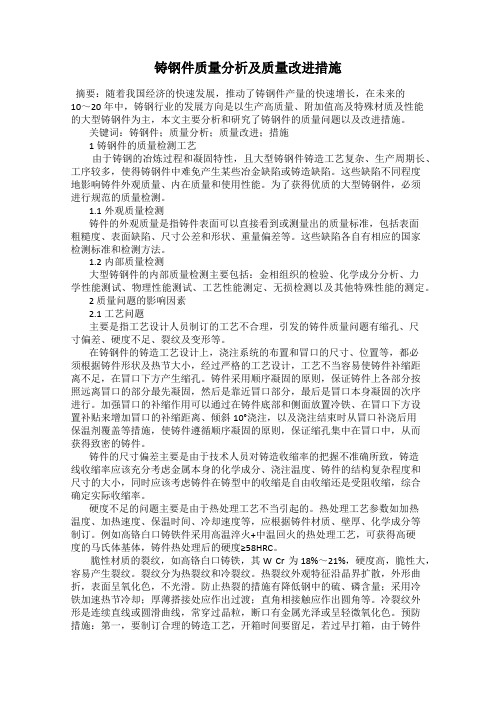
铸钢件质量分析及质量改进措施摘要:随着我国经济的快速发展,推动了铸钢件产量的快速增长,在未来的10~20年中,铸钢行业的发展方向是以生产高质量、附加值高及特殊材质及性能的大型铸钢件为主,本文主要分析和研究了铸钢件的质量问题以及改进措施。
关键词:铸钢件;质量分析;质量改进;措施1铸钢件的质量检测工艺由于铸钢的冶炼过程和凝固特性,且大型铸钢件铸造工艺复杂、生产周期长、工序较多,使得铸钢件中难免产生某些冶金缺陷或铸造缺陷。
这些缺陷不同程度地影响铸件外观质量、内在质量和使用性能。
为了获得优质的大型铸钢件,必须进行规范的质量检测。
1.1外观质量检测铸件的外观质量是指铸件表面可以直接看到或测量出的质量标准,包括表面粗糙度、表面缺陷、尺寸公差和形状、重量偏差等。
这些缺陷各自有相应的国家检测标准和检测方法。
1.2内部质量检测大型铸钢件的内部质量检测主要包括:金相组织的检验、化学成分分析、力学性能测试、物理性能测试、工艺性能测定、无损检测以及其他特殊性能的测定。
2 质量问题的影响因素2.1工艺问题主要是指工艺设计人员制订的工艺不合理,引发的铸件质量问题有缩孔、尺寸偏差、硬度不足、裂纹及变形等。
在铸钢件的铸造工艺设计上,浇注系统的布置和冒口的尺寸、位置等,都必须根据铸件形状及热节大小,经过严格的工艺设计,工艺不当容易使铸件补缩距离不足,在冒口下方产生缩孔。
铸件采用顺序凝固的原则,保证铸件上各部分按照远离冒口的部分最先凝固,然后是靠近冒口部分,最后是冒口本身凝固的次序进行。
加强冒口的补缩作用可以通过在铸件底部和侧面放置冷铁、在冒口下方设置补贴来增加冒口的补缩距离、倾斜10°浇注,以及浇注结束时从冒口补浇后用保温剂覆盖等措施,使铸件遵循顺序凝固的原则,保证缩孔集中在冒口中,从而获得致密的铸件。
铸件的尺寸偏差主要是由于技术人员对铸造收缩率的把握不准确所致,铸造线收缩率应该充分考虑金属本身的化学成分、浇注温度、铸件的结构复杂程度和尺寸的大小,同时应该考虑铸件在铸型中的收缩是自由收缩还是受阻收缩,综合确定实际收缩率。
球墨铸铁件浇注冷隔

球墨铸铁件浇注冷隔球墨铸铁件是一种常见的铁合金制品,在工业生产中广泛应用。
为了保证球墨铸铁件的质量和性能,冷隔是一项必要的工艺措施。
本文将从球墨铸铁件的特点、冷隔的作用、冷隔的实施步骤以及注意事项等方面进行详细介绍,旨在为相关人员提供指导意义。
首先,我们来了解一下球墨铸铁件的特点。
球墨铸铁件具有高强度、良好的韧性和可加工性,广泛应用于机械制造、汽车工业等领域。
相较于普通铸铁件,球墨铸铁件通过球化处理使铸铁中的石墨变为球状,改善了其力学性能,提高了其抗拉强度和断裂韧度。
然而,球墨铸铁件在生产过程中仍然存在一些问题,例如热裂纹、气孔等缺陷,这会降低其质量和性能,影响使用寿命。
为了解决这些问题,冷隔被引入到球墨铸铁件的浇注过程中。
那么,冷隔在球墨铸铁件生产中起到什么作用呢?冷隔主要能够有效地控制铁水浇注的速度和流向,防止过热现象的发生,减少铁水中的气体和杂质含量,从而减少缺陷的产生。
冷隔还能够协助铸造工人掌握铁水的凝固时间,保证球墨铸铁件的组织均匀,提高产品质量。
接下来,我们来了解一下冷隔的实施步骤。
首先,要选择合适的冷隔材料,常见的有陶质、聚苯乙烯、氧化镁等。
其次,在浇注前,要将冷隔材料切割成合适尺寸,将其安装在铸型的合适位置,并确保与铸型接触紧密。
然后,进行预热处理,避免冷隔材料吸湿。
最后,在浇注时要控制好铁水的浇注速度和温度,以保证冷隔的作用正常发挥。
最后,我们来总结一下冷隔实施中需要注意的事项。
首先,要选择适当的冷隔材料,根据不同的浇注条件进行选择。
其次,要保证冷隔的安装质量,确保与铸型接触紧密,避免铁水的漏浇。
同时,要注意控制好铁水的浇注速度和温度,避免过热现象和缺陷的产生。
最后,要及时清理冷隔材料,防止其残留在铸件内部,影响产品的质量。
总之,冷隔是球墨铸铁件生产中不可或缺的工艺措施,对于提高产品质量、避免缺陷的产生具有重要作用。
在实施冷隔时,要选择适当的材料,注意安装质量和浇注控制,同时及时清理冷隔材料,以保证球墨铸铁件的质量和性能。
影响球墨铸铁过冷度因素及控制方法

影响球墨铸铁过冷度因素及控制方法球墨铸铁作为一种常用的铸造材料,在机械制造、汽车制造、航空航天等领域有着广泛的应用。
而球墨铸铁的性能又受到很多因素的影响,其中过冷度是影响球墨铸铁性能的重要因素之一。
本文将介绍影响球墨铸铁过冷度的因素及控制方法。
一、过冷度的概念过冷度是指铸造中铁水在凝固前的温度低于其凝固温度的程度。
在铸造中,铁水凝固时会释放出一定的热量,使得铁水温度逐渐下降,直到达到凝固温度时才开始凝固。
而如果铁水的温度在凝固前就已经降低到了凝固温度以下,就会出现过冷现象。
二、影响过冷度的因素1. 铁水温度铁水温度是影响过冷度的主要因素之一。
铁水温度越低,过冷度就越大。
因此,在铸造过程中,需要控制好铁水的温度,避免出现过低的温度。
2. 浇注速度浇注速度也会影响过冷度。
浇注速度越快,铁水的热量就越容易散失,过冷度就越大。
因此,在铸造过程中,需要控制好浇注速度,避免过快的浇注速度。
3. 浇注方式浇注方式也会影响过冷度。
对于复杂的铸件,采用自由浇注容易造成过冷现象,而采用压力浇注则可以减少过冷现象的发生。
4. 铸型温度铸型温度也会影响过冷度。
铸型温度越低,过冷度就越大。
因此,在铸造过程中,需要控制好铸型的温度,避免过低的温度。
5. 涂料涂料也会影响过冷度。
一些涂料的热传导性能较差,容易造成过冷现象。
因此,在铸造过程中,需要选择合适的涂料,避免过冷现象的发生。
三、控制过冷度的方法1. 提高铁水温度提高铁水温度是控制过冷度的主要方法之一。
可以通过加热设备对铁水进行加热,提高铁水温度,减少过冷现象的发生。
2. 控制浇注速度控制浇注速度也是控制过冷度的重要方法之一。
可以通过调整浇注速度,使铁水的热量散失得更加均匀,减少过冷现象的发生。
3. 采用压力浇注采用压力浇注是减少过冷现象的有效方法之一。
通过增加浇注压力,可以使铁水更加均匀地填充到铸型中,减少铁水的热量散失,从而减少过冷现象的发生。
4. 提高铸型温度提高铸型温度也是控制过冷度的方法之一。
知识篇——铸钢件产生缺陷的原因及分析与防范
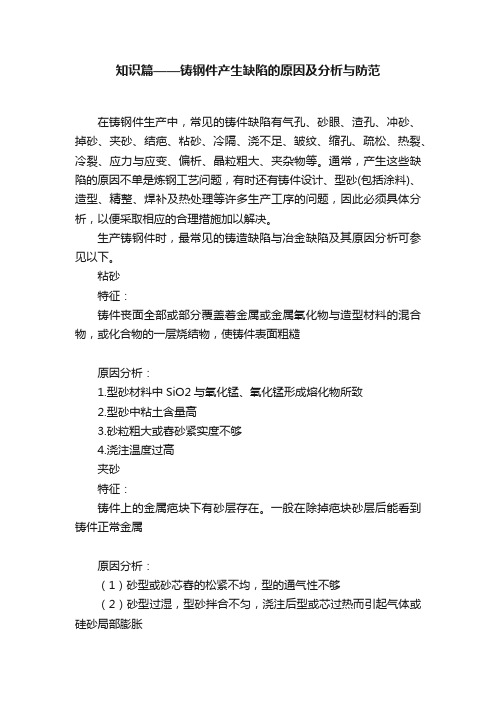
知识篇——铸钢件产生缺陷的原因及分析与防范在铸钢件生产中,常见的铸件缺陷有气孔、砂眼、渣孔、冲砂、掉砂、夹砂、结疤、粘砂、冷隔、浇不足、皱纹、缩孔、疏松、热裂、冷裂、应力与应变、偏析、晶粒粗大、夹杂物等。
通常,产生这些缺陷的原因不单是炼钢工艺问题,有时还有铸件设计、型砂(包括涂料)、造型、精整、焊补及热处理等许多生产工序的问题,因此必须具体分析,以便采取相应的合理措施加以解决。
生产铸钢件时,最常见的铸造缺陷与冶金缺陷及其原因分析可参见以下。
粘砂特征:铸件丧面全部或部分覆盖着金属或金属氧化物与造型材料的混合物,或化合物的一层烧结物,使铸件表面粗糙原因分析:1.型砂材料中SiO2与氧化锰、氧化锰形成熔化物所致2.型砂中粘土含量高3.砂粒粗大或舂砂紧实度不够4.浇注温度过高夹砂特征:铸件上的金属疤块下有砂层存在。
一般在除掉疤块砂层后能看到铸件正常金属原因分析:(1)砂型或砂芯舂的松紧不均,型的通气性不够(2)砂型过湿,型砂拌合不匀,浇注后型或芯过热而引起气体或硅砂局部膨胀(3)钢液进人型腔过慢,使型或芯表面局部过热裂纹特征:铸件裂纹可分为热裂纹、冷裂纹。
它们都是由于液态钢在高温下收缩变形受阻而形成的。
铸件冷却收缩受阻后产生应力,应力超过了钢液在该温度下的强度或塑性极限,便生成裂纹原因分析:1.硫、磷等有害元索含量偏高易形成热裂纹2.钢中的夹杂物与偏析容易形成应力集中3.钢液的线收缩越大,热裂纹倾向越大4.铸件设计的结构不良易产生局部应力集中,也会导致热裂纹5.钢液浇注温度偏高,易于产生热裂纹6.铸件浇、冒口排列位置不当,导致收缩受阻而产生热裂纹7.砂型舂得过紧,退让性不良,阻碍收缩,增加热裂倾向8.铸件冷却速度过快,或打箱过早都会造成更大的冷却应力,增加热裂倾向9.铸件切割浇冒口不当或清理不当,热处理后冷却过快或不匀等也会导致热裂10.铸件冷却至温度较低范围,铸件的残余应力或外界条件而形成冷裂纹缩孔与缩松特征:铸件缩孔与缩松均产生于铸钢件表面(切割冒口即发现孔洞)或铸件内部(经加工或无损检测发现)其形状不规则,呈海绵状洞穴或小孔原因分析:由于铸件凝固收缩,又得不到足够的钢液补给所致,其原因是:1.冒口位置安排不合理2.冒口补贴能力不足3.冒口补贴设计不当4.钢液浇注温度过高,收缩量过大夹杂物特征:夹杂物按其原始形成可分为“内生”与“外来”夹杂物,这里指外来夹杂物,它包括金属与非金属夹杂物,来自出钢、浇注过程中设备或浇注系统中剥落混入铸件形成,大多是耐火材料及型砂材料的熔渣原因分析:1.原材料、炼钢过程控材不当2.浇注过程、钢包中钢液与气体、砂型的相互作用气孔特征:是指“外生”式气孔,这类气孔呈梨形,细颈方向指向气体来源,发生在铸件表面或皮下,热处理后或加工后可发现原因分析:1.型砂中的水分过高,冷铁涂料处理不当2.砂型透气不良3.浇注系统和型腔在浇注过程中卷入气体而不能排除夹杂物特征:是指“内在”夹杂物,即所有的氧化物、硫化物聚集颗粒的非金属氧化物形态,还有氯化物、硅酸盐等,其结构为FeS、FeO、MnS、MnO-Al2O3及FeO-FeS等形状呈球状、网状、沿晶界及枝晶轴间分布原因分析:1.来自钢的冶炼过程中的氧和硫及脱氧剂,在冷却凝固过程中,残余的氧化物与硫化物相以不连续的相沉淀出脱氧产物Si+O2=SiO2,4Al+3O2=2Al2O32.浇注过程中的二次氧化也产生夹杂,称二次氧化夹杂气孔特征:是指“内生”式气孔,钢液中气体随温度下降其溶解度急剧减少,气体向较高温度扩散至壁较厚部位,严重时遍布冒口下部部位原因分析:炼钢过程中脱氧不良偏析特征:1.成分偏析:凝固过程中,由于固相和液相成分不同,先凝固都分含有高熔点组元,后凝固部分含有低熔点组元,而产生成分偏析2.树枝状偏析;铸件基本上存在成分上和组织上的不均称树枝状偏析3.晶间偏析:存在于树枝状晶体之间的后凝固的低熔点组成物,它与晶体本身成分不同4.岩石状断口:断口呈岩石状或片状.多产生于铝、硼和碳较高的铸件原因分析:1.浇注温度不当2.浇注速度不当3.某些低合金钢的脱氧剂用铝量多,氮含量高,硼的含量未控制好。
机车车辆铸钢铁失效分析与预防措施

83玻璃固化和化学稳定化等,其中的自胶结固化主要用于处置无机危险固体废物。
此技术在应用过程中具有原材料易于获取、价格低廉、适宜大体积和大规模危险废物的处理和处置。
本技术的缺点在于,处置之后的固体废物会增加废物的体积和重量,后续处理依然使用填埋方式,占用土地资源,难以对含有有机物的废物进行固化处理,对操作工作人员的技术水平要求较高,此外还有处理设备价格昂贵、易在处置过程中出现操作不当而造成二次污染等问题。
(二)快速碳酸化技术本技术应用于上世纪90年代,主要原理为:经碳酸化处理后,在高浓度的二氧化碳环境中加速危险固废的反应,应用此种方法有助于加速工业热反应之后的废弃物与二氧化碳反应,有效降低其中的重金属浓度,在钢铁渣、电石渣、废石灰、煤飞尘和废弃物的焚化炉灰、废弃的建筑材料以及某些金属冶炼尾矿的处理中应用比较广泛。
我国金属冶炼行业发展迅速,冶炼废渣产生量巨大,因此该技术在国内得到了较为深入的研究与应用。
目前该技术已经能够实现对包括铅、钡、锡等在内的17种工业危险固废进行处理,并且能够有效降低其中铅、钡等重金属的浸出。
通过此技术的应用,可以有效降低废弃物中重金属的流动性,缺点在于其处理工艺比较复杂,处理设备投入较大,难以在更大的行业范围内大规模推广应用。
(三)等离子气化技术本技术采用等离子火炬或电弧来将危险固废加热到6000℃左右,极大地增加基本粒子的内能与活化能,此时以原子热运动为主的有毒有害物质就会由于其原有原子状态被打破而失去化学活性,将危险固废成功转换为化学结构简单的无害物质。
在上述过程中,危险固废中的有机物转化分解为可燃气体,无机物液态渣经过转换、冷却之后,变为可用于建筑施工的工程材料。
此技术最大的优势就是在废弃物处理之后基本不会产生二噁英,设备体积小、节省占地面积、设备工艺、结构和操作比较简单,运行安全性和可靠性较高。
但是此技术应用前期的设备资金投入比较高且资金回收时间长,可以通过技术长期稳定运行,以期尽快收回前期投入成本。
灰铸铁件损伤、冷裂、温裂、变形、金相不合格、过硬六大缺陷的防止方法

灰铸铁件损伤、冷裂、温裂、变形、金相不合格、过硬六大缺陷的防止方法灰铸铁件由于落砂清理、热处理时造成的主要缺陷及其原因分析与防止方法(1)损伤特征及发现方法:损坏了铸件的完整性用外观检查可以发现原因分析:1.在开箱、搬运或清理时不注意2.打浇、冒口的方向不对或冒口颈过大,造成带肉缺陷防止方法:1.认真按照工艺规程和要求操作2.正确掌握打浇、冒口的方向(2)冷裂特征及发现方法:1.薄壳零件落砂时被振裂,并违反操作规程2.采用水爆清砂时,热应力较大,当应力超过铸件某部分的抗拉强度时,应生冷裂防止方法:1.对易裂的薄壳零件,清理时应挑出,另行清理,并认真执行合理的操作规程2.根据铸件结构和性能特点,选用合理的清理方式和清理工其3.严格执行水爆工艺4.在运输和清理过程中,尽量减轻碰撞(3)温裂特征及发现方法:开裂处金属表皮氧化用外观检查,透光法,磁力探伤,打压试验,煤油渗透等方法发现原因分析:由于气割、焊接或热处理不当,温度应力大所引起防止方法:正确制订并认真执行合理的焊接、热处理规范和操作规程(4)变形特征及发现方法:长的或扁平类铸件在靠近壁厚的一方凹入成弯曲形用外观检查,划线等方法发现原因分析:在铸件冷却过程中,产生的铸造应力超过该材质的屈服极限时,则产生塑性变形和挠曲为减少和消除铸件的残留应力,可采用人工时效(即退火热处理),若热处理规范不正确,仍会产生变形和挠曲防止方法:1.改变热处理规范,使其合理,并认真执行2.延长开箱时间或把刚落砂的铸件送入保温炉中保温,并随炉缓慢冷却(5)金相不合格特征及发现方法:铸件断面的粗视组织和显微组织不符合标准或技术条件用断面观察,金相检验可以发现原因分析:1.开箱时间不当2.热处理规范不正确防止方法:1.按技术要求,合理控制铸件的开箱时间2.改变热处理规范,使其合理,并认真执行(6)过硬特征及发现方法:在铸件边缘和薄璧处出现白口铁组织断面观察,硬度试验,机械加工可以发现原因分析:开箱时间过早防止方法:适当延长开箱时间或在退火炉中缓慢降温。
冷焊中铸铁断裂的通病及其预防

冷焊中铸铁断裂的通病及其预防材料为灰口铸铁的冲床,压力机,气缸,变速箱等结构件,断裂和机床导轨的磨损是常见的。
对此,采用焊接工艺修复是最为经济迅速和有效的办法。
灰口铸铁的特点是,组织疏松,含碳量高,性脆,杂质多,偏析情况严重,所以客焊性差。
往往因焊接不当,会发生各种缺陷,最常见的有裂纹、剥离、白口和气孔四种。
一、防止裂纹的措施焊接铸铁件是最容易产生裂纹,因此认为它的可焊性差。
实际上,分析设备损坏的情况,它们的断裂部位往往是机件的最大受力点,或者是应力集中区,或者是金相偏析严重的区域,既设备结构的薄弱点。
因此,对焊接工艺带来的难度比较高。
1、清污在熔接区域里清除垃圾、油脂、水分之类的各类杂质,否则将产生气孔、夹渣和裂纹。
焊接坡口处,可用四氯化碳清洗,在焊接完成前,不能接触任何杂质。
2、均温均温是焊接全过程中的重要一环。
在焊接坡口两侧约300mm范围内,可用氧乙炔火焰将工件加热至100~150℃。
这样,除能达到均温的目的外,还有烧去坡口内的有机物质和蒸发金属内部水分的作用。
焊接过程中应注意,不使焊接面温度超过120℃;并只有保持均温,才能排除因涨缩所引起的裂纹、剥离和白口。
3、定向施焊定向施焊是消除应力、防止裂纹的重要措施。
定哪一个焊缝走向,应视工件断裂的具体部位而定。
就规律而言,是“从内到外”、“从强到弱”。
定向后的焊缝走向始终不能改变。
4、规则性的施焊、通常对冷焊工艺采用不规则的施焊法,即左、右、上、下的分散焊法,它只能达到“均温”而不能使应力分散,不规则施焊的结果,使焊缝产生错综复杂的应力;既有相向应力,又有背向应力。
5、短、窄、厚、小的焊接工艺是否采取分段焊缝,可视被焊机件裂口的长度而确定,如断口长度长达数米,可在同一方向分为多段起点,以创造“均温”条件。
焊程宜短不宜长,焊一次最长不超过35mm,以使它热量不会集中。
6、熔敷通常认为,铸铁焊接也象碳钢焊接一样,穿透越深强度越高,这实际是错误的。
铸造件冷铁基本知识与安放原则及案例
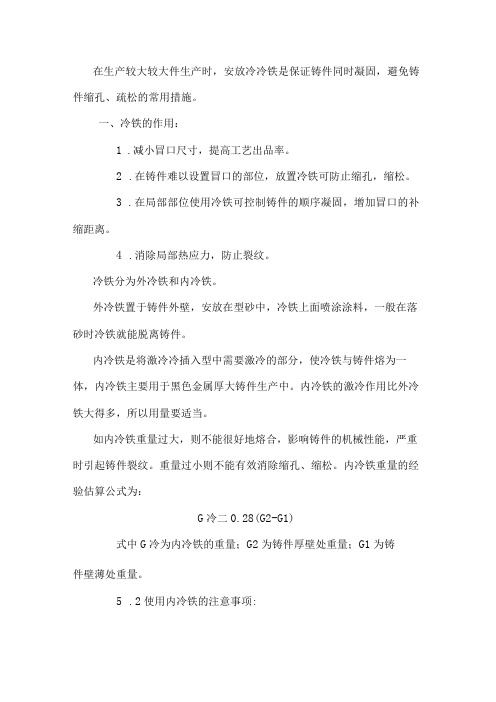
在生产较大较大件生产时,安放冷冷铁是保证铸件同时凝固,避免铸件缩孔、疏松的常用措施。
一、冷铁的作用:1.减小冒口尺寸,提高工艺出品率。
2.在铸件难以设置冒口的部位,放置冷铁可防止缩孔,缩松。
3.在局部部位使用冷铁可控制铸件的顺序凝固,增加冒口的补缩距离。
4.消除局部热应力,防止裂纹。
冷铁分为外冷铁和内冷铁。
外冷铁置于铸件外壁,安放在型砂中,冷铁上面喷涂涂料,一般在落砂时冷铁就能脱离铸件。
内冷铁是将激冷冷插入型中需要激冷的部分,使冷铁与铸件熔为一体,内冷铁主要用于黑色金属厚大铸件生产中。
内冷铁的激冷作用比外冷铁大得多,所以用量要适当。
如内冷铁重量过大,则不能很好地熔合,影响铸件的机械性能,严重时引起铸件裂纹。
重量过小则不能有效消除缩孔、缩松。
内冷铁重量的经验估算公式为:G冷二0.28(G2-G1)式中G冷为内冷铁的重量;G2为铸件厚壁处重量;G1为铸件壁薄处重量。
5.2使用内冷铁的注意事项:使用前"内冷铁要喷丸或喷砂处理,去除表面锈蚀和油污,常镀锌或镀锡防氧化。
砂型内放置内冷铁后及时浇注,防止内冷铁上聚集水分而产生气孔。
时长一般不超过4h°对放置有较多内冷铁的铸型,浇注前最好用喷灯加热,去除内冷铁表面的水分。
承受高温、高压和质量要求很高的铸件,不宜放置内冷铁。
放置内冷铁的铸型上方应有出气孔,如上方是暗冒口,冒口上也应有较大的出气孔。
采用栅状内冷铁时,单根冷铁的直径不大于30mm。
内冷铁在铸件加工后不得暴露,以免影响铸件的力学性能。
2.3外冷铁分直接外冷铁与间接外冷铁。
使用外冷铁的注意事项:外冷铁紧贴铸件表面的部位应光洁,除去锈污等各种脏物,有时要刷涂料。
对于易产生裂纹的铸造合金浇注的铸件,使用外冷铁时应带有一定的斜度以免型砂和冷铁分界处因冷却速度差别过大而形成裂纹。
外冷铁边缘与砂型相接处不宜有尖角砂。
可以选择随形冷铁。
选择恰当的外冷铁厚度。
太薄的外冷铁只在凝固初期发生微弱的激冷作用,甚至会与铸件熔合在一起。
- 1、下载文档前请自行甄别文档内容的完整性,平台不提供额外的编辑、内容补充、找答案等附加服务。
- 2、"仅部分预览"的文档,不可在线预览部分如存在完整性等问题,可反馈申请退款(可完整预览的文档不适用该条件!)。
- 3、如文档侵犯您的权益,请联系客服反馈,我们会尽快为您处理(人工客服工作时间:9:00-18:30)。
铸钢件粘冷铁机理浅析及防止措施
马文治,张旭鹏,苏志东,杨磊,闫新飞
(宁夏共享铸钢有限公司,宁夏银川 750021)
摘要:影响铸钢件表面粘冷铁的因素很多,文章从我公司实际情况出发,对铸钢件的粘冷铁机理作了简单分析,并针对其影响因子,提出了防止铸钢件粘冷铁的控制措施。
关键词:铸钢件粘冷铁机理铸造工艺
Mechanism and Preventing Measures of Chill Adhering to Steel Casting Ma Wenzhi, Zhang Xupeng, Su Zhidong,Yang Lei,Yan Xinfei
(Kocel Steel Foundry Co.,Ltd.,Yinchuan 750021, Ningxia)
Abstract:There are many factors for chill adhering to steel castings. Combined with the actual situation, this paper gives a brief analyze of the mechanism of chill adhering to steel castings, and proposes
some preventing measures for the factors of chill adhering to steel castings.
Keywords:steel castings chill adherence mechanism casting process
1 引言
随着生产的发展,铸钢件冷铁技术在铸造工艺中的地位显得越来越重要,尤其是对铸钢件产量大、产品形状较复杂、产品种类较多的厂家。
经过钢液浇注后,铸件表面容易粘冷铁,轻则导致表面粗糙,重则冷铁与铸件熔为一体,大大增加铸件清理工作量,生产效率低下。
据统计,平均每100 kg铸钢件需使用冷铁5 kg,那么每年生产2000t铸钢件的厂家,需要冷铁100 t,仅冷铁制造费用就达20万元左右[1]。
针对上述问题,本文从我公司实际情况出发,对铸钢件粘冷铁机理进行了浅析,并提出相应的解决措施,达到降低消耗、节约成本的目的。
2 冷铁的作用
铸造工艺中,由于铸钢件的结构复杂,各个部分壁厚不均,壁厚厚的部位冷却得慢,壁厚薄的部位冷却得快,造成同一个铸件各个部位冷却速度不均。
在型腔内部及工作表面安放的金属块称为冷铁,分为内冷铁和外冷铁两大类,其作用是增加铸件局部的冷却速度。
冷铁的作用可总结如下6点[2]:
1)与浇注系统和冒口配合控制铸件的凝固次序。
2)增加铸件的凝固速度,细化晶粒组织,提高铸件的力学性能。
3)减小冒口尺寸,提高工艺出品率。
4)在铸件难以设置冒口的部位,放置以防止缩孔,缩松。
5)在局部使用冷铁,控制铸件的顺序凝固,增加冒口的补缩距离。
6)消局部热应力,防止裂纹。
3 铸件粘冷铁机理
外冷铁被铸件熔接的原理:假设贴冷铁部位
的铸件体积为
v,与这一部位邻接的铸件体积为
r v ,且0v v r >,为了获得致密的铸件,0v 的凝
固时间至少应与r v 的凝固时间相等。
这就要求体积差(重量差)引起的热量差)()(0U L v v r +-ρ应由所设置的冷铁完全吸收,才能保证两者的凝固时间相同或相近。
根据铸件凝固过程的热平衡原理,当冷铁可吸收的热量不能满足钢液凝固所释放出的热量时,冷铁将与铸件熔接。
4 铸件粘冷铁影响因子研究
影响铸钢件表面粘冷铁的因素很多,统计分析我公司在大型铸钢件浇注中的粘冷铁现象,归纳出两项影响因子:第一,冷铁重量偏低,无法吸收钢液凝固释放的热量;第二,冷铁经过多次使用,表层氧化严重,热导率大大降低,比热增加,热传导能力降低,致使冷铁温度升高,与铸件熔接。
4.1 冷铁重量偏低
在铸钢件易粘冷铁处选用规格为φ100x100mm 和φ100x150mm 的两种冷铁,分别放置在同一铸件上下两半相同的位置进行试验。
结果形成如图1所示的效果,放置规格为φ100x150mm 冷铁的铸件上半没有粘冷铁,而放置规格为φ100x100mm 冷铁的铸件下半大量粘冷铁。
由此得出结论,校核钢液凝固释放的热量,计算所需冷铁重量,选择规格合适的冷铁,对于防止铸钢件表面粘冷铁有很好的效果。
所需冷铁的重量,可根据热平衡的条件进行计算[3]
,
图1 冷铁重量对铸钢件粘冷铁的影响
由于
因此
假设钢液浇注到砂型后的温度(即与冷铁接触时的温度)为1550℃以及凝固结束时冷铁的温度为600℃,则
式中,0v —设置冷铁部位的铸件体积(dm 3);
r v —与设置冷铁部位相邻的铸件体积(dm 3 );
L —凝固潜热(kJ/Kg);
U —过热度所含的热给(kJ/kg); t 冷—凝固结束时冷铁的温度(℃); c —比热容(kJ/Kg ℃); G 冷—所需冷铁的重量(kg)。
4.2 冷铁表面氧化
为节省生产成本,我公司造型工厂的冷铁均为多次重复使用。
但是使用过的冷铁,经过一次高温后,使用面会产生一层氧化层。
随着氧化层的增加,冷铁热导率大大降低、比热增加,而铸件散热缓慢,冷铁温度升高,导致冷铁易与铸钢
件熔接在一起,形成铸件粘冷铁。
造型工厂使用新旧冷铁做试验进行对比:选择同一个模型分别使用新旧冷铁进行浇注,在其他条件都相同的条件下,得到如图2所示的试验结果,使用了新冷铁的铸件没有粘冷铁,而使用了回收的旧冷铁的铸件粘了冷铁。
图2 回收旧冷铁(左)和新冷铁(右)效果对比
由此可得出解决冷铁重复使用过程中使用
面氧化问题的办法。
通过截面金相法[4],可见如
图3所示的循环使用的冷铁使用面的氧化层厚
度。
用显微镜测量,冷铁使用面的氧化层厚度在
0.5~1mm之间,如表1。
由此得出,使用过的冷铁需要重复使用的,
只需使用面加工掉1mm,就可完成氧化层去除,
在校核重量安全的条件下,即可重复使用并有效
避免铸件粘冷铁。
图3 循环使用的冷铁表面氧化
表1 显微镜下冷铁表面氧化层厚度
试样1 试样2 试样3 试样4 试样5 试样6 试样7 试样8 试样9 试样10 最大值0.73 0.657 0.299 0.956 0.886 0.82 0.654 0.822 0.286 0.982
最小值0.4 0.455 0.216 0.722 0.977 0.56 0.471 0.687 0.182 0.846
平均值0.565 0.556 0.257 0.839 0.932 0.69 0.562 0.754 0.234
0.914
5 结论
5.1冷铁激冷能力与铸钢件粘冷铁有密切的联系,工艺设计校核冷铁重量,选择适当规格的冷铁可以有效地防止铸钢件粘冷铁;
5.2 循环使用的冷铁在使用过一次后,表面生成0.5~1mm厚的氧化层,降低了冷铁的激冷能力。
在重复使用之前,将冷铁使用面加工去除1mm 的氧化层,可在一定程度上恢复冷铁的激冷能力,防止铸件粘冷铁。
参考文献
[1]陈家能,任美福.铸钢件外冷铁标准化技术初探[J]. 重庆钢铁高等专科学校
学报.1995年第10期第4卷.
[2]刘炀,王国平.内冷铁在厚大铸钢件生产中的应用[J].铸造技术. 2004. 07. [3]李新亚.铸造手册:铸造工艺第2版[M].
机械工业出版社.2011
[4]金属和氧化覆盖层测试方法截面金相法[S]. 中华人民共和国国家标准.。