矿热炉的基本原理
电石炉(矿热炉)生产工艺原理与电极入炉深度分析与控制方法
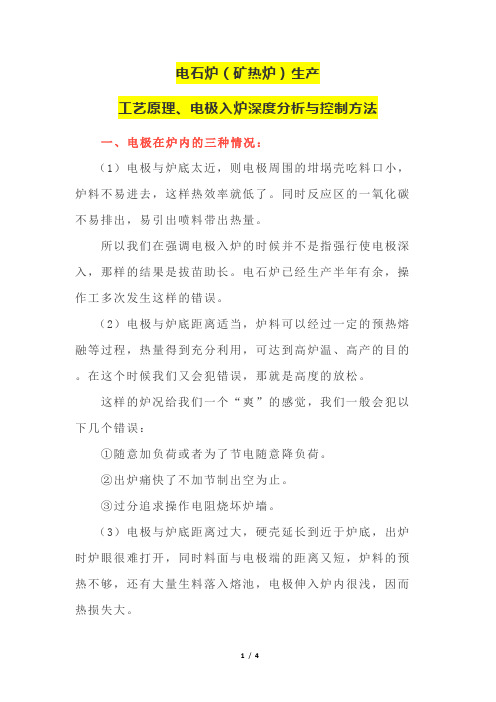
电石炉(矿热炉)生产工艺原理、电极入炉深度分析与控制方法一、电极在炉内的三种情况:(1)电极与炉底太近,则电极周围的坩埚壳吃料口小,炉料不易进去,这样热效率就低了。
同时反应区的一氧化碳不易排出,易引出喷料带出热量。
所以我们在强调电极入炉的时候并不是指强行使电极深入,那样的结果是拔苗助长。
电石炉已经生产半年有余,操作工多次发生这样的错误。
(2)电极与炉底距离适当,炉料可以经过一定的预热熔融等过程,热量得到充分利用,可达到高炉温、高产的目的。
在这个时候我们又会犯错误,那就是高度的放松。
这样的炉况给我们一个“爽”的感觉,我们一般会犯以下几个错误:①随意加负荷或者为了节电随意降负荷。
②出炉痛快了不加节制出空为止。
③过分追求操作电阻烧坏炉墙。
(3)电极与炉底距离过大,硬壳延长到近于炉底,出炉时炉眼很难打开,同时料面与电极端的距离又短,炉料的预热不够,还有大量生料落入熔池,电极伸入炉内很浅,因而热损失大。
此时,我们要检查原料、出炉量,在很多时候需要将炉眼内生料带出甚至干烧。
如果发生这种情况说明炉子工况已经很坏。
从上面三种情况可以看出,电极控制在适当的位置是十分重要的。
平时操作时,若发现电极位置高了,就要设法让电极插下去。
又若发现电极位置过深了,也要设法把电极位置纠正。
当炉内的电石生成过多时,电石液位上升,其电石液体的沸腾必使电流波动,使电极位置难以稳定。
如果出炉时,把电石全部掏空,就会使炉温降低,此时电极钻得很深。
炉温低的电石炉,电极的波动频繁而剧烈,造成操作上的困难,有时往往下一炉出不来或三相不通。
此刻,电极的位置则比原来的还要高得多。
如果电极位置经常插得过深,出来的电石质量不好,我们可以适当增加一些配比,提高炉温,使电极保持适当的位置。
连续反应的电炉的料层结构大致分四个方面:1冷料和热料;2沾结料;3半成品;4液体电石。
当多加了石灰,出现出炉过多的现象以后,料层结构则被破坏了,炉温亦下降,因此,副石灰必须控制。
矿热炉冶金原理
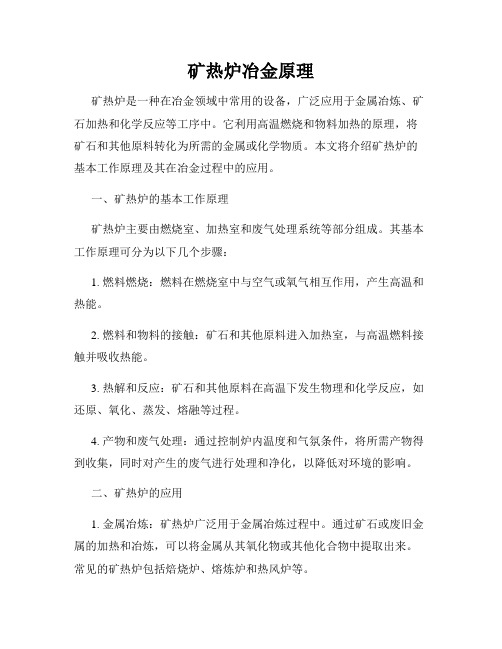
矿热炉冶金原理矿热炉是一种在冶金领域中常用的设备,广泛应用于金属冶炼、矿石加热和化学反应等工序中。
它利用高温燃烧和物料加热的原理,将矿石和其他原料转化为所需的金属或化学物质。
本文将介绍矿热炉的基本工作原理及其在冶金过程中的应用。
一、矿热炉的基本工作原理矿热炉主要由燃烧室、加热室和废气处理系统等部分组成。
其基本工作原理可分为以下几个步骤:1. 燃料燃烧:燃料在燃烧室中与空气或氧气相互作用,产生高温和热能。
2. 燃料和物料的接触:矿石和其他原料进入加热室,与高温燃料接触并吸收热能。
3. 热解和反应:矿石和其他原料在高温下发生物理和化学反应,如还原、氧化、蒸发、熔融等过程。
4. 产物和废气处理:通过控制炉内温度和气氛条件,将所需产物得到收集,同时对产生的废气进行处理和净化,以降低对环境的影响。
二、矿热炉的应用1. 金属冶炼:矿热炉广泛用于金属冶炼过程中。
通过矿石或废旧金属的加热和冶炼,可以将金属从其氧化物或其他化合物中提取出来。
常见的矿热炉包括焙烧炉、熔炼炉和热风炉等。
2. 矿石提纯:在矿石提纯过程中,矿热炉可以通过物质的加热和分解,将其中的杂质或有害成分去除,得到纯净的金属或化学物质。
3. 化学反应:矿热炉也被广泛应用于化学工业中。
通过高温条件下的热解反应,可以使化学反应更加快速和高效。
例如,矿热炉可用于生产硝酸、硫酸等化学品。
4. 热处理:在金属加工中,矿热炉常用于热处理工序,通过控制炉内温度和气氛,改变金属的物理和化学性质,提高其机械强度、耐腐蚀性等。
三、矿热炉的优势和挑战1. 优势:矿热炉具有加热速度快、效率高、操作灵活等优势。
它可以适应不同物料和工艺要求,能够高效完成加热和反应过程。
2. 挑战:矿热炉的使用也存在一些挑战,如高温下设备的耐久性、废气处理的环保问题以及能源消耗等。
随着环保意识的增强,矿热炉也在不断改进和优化,以减少能源消耗和废气排放。
总结:矿热炉作为一种常用的冶金设备,在金属冶炼和化学反应等领域中发挥着重要作用。
矿热炉的原理

矿热炉的原理矿热炉是一种用于高温矿石加热和冶炼的设备。
它基本上是由炉膛、燃烧器、排烟管和温度控制系统等部分组成。
其工作原理涉及到燃烧、传热和矿石冶炼等多个方面。
首先,矿热炉采用的燃烧器是关键组成部分。
一般来说,矿热炉中所使用的燃烧器会将燃料和空气混合并着火。
燃料可以是天然气、重油、煤等,而空气则是为燃烧提供所需的氧气。
在燃烧过程中,燃料被氧气氧化,产生的热能被释放出来,并且化学反应的产物如二氧化碳、二氧化硫等将会通过排烟管排出。
因此,燃烧器的设计和操作对矿热炉的高效工作至关重要。
其次,燃烧释放的热能将通过传热的方式传递到炉膛和矿石上。
炉膛通常由耐火材料构成,它们能够承受高温和化学腐蚀,在矿石冶炼过程中起到保护作用。
同时,炉膛的结构也有利于加热的均匀分布,确保矿石得到均匀的加热。
在矿热炉内部,通常会放置一种被称为“铁护板”的耐火材料,它不仅能够稳定矿石料床的形状,还能阻止煤气对矿石的直接接触,降低燃烧产生的有害元素对矿石的污染。
这样,矿石料床得以在合适的温度下进行冶炼反应。
另外,矿石冶炼是矿热炉的核心功能之一。
在矿热炉内,矿石与高温煤气接触后,会发生一系列冶金反应。
具体来说,矿石中的金属成分在高温下与煤气中的氧气反应,生成金属氧化物。
随后,金属氧化物会进一步还原成金属,并在矿石的表面沉积下来。
该冶炼过程中涉及到的化学反应相当复杂,但主要原理是将金属与氧气分离,使金属转化为可用于后续加工的形式。
冶炼过程中释放的热量也有助于维持矿石料床的温度,以保证反应的持续进行。
最后,矿热炉通常还配备了温度控制系统。
通过控制燃烧器的燃料供应、空气流量和炉内的温度分布等参数,可以调节矿热炉的工作状态。
例如,可以通过增加或减少燃料供应来调节炉内的温度,从而控制矿石冶炼过程的进行。
同时,温度控制系统还监测炉内的温度分布,以确保矿石得到均匀的加热。
这些控制措施有助于提高矿石的冶炼效果和燃烧效率。
综上所述,矿热炉的工作原理涉及到燃烧、传热和矿石冶炼等多个方面。
矿热炉
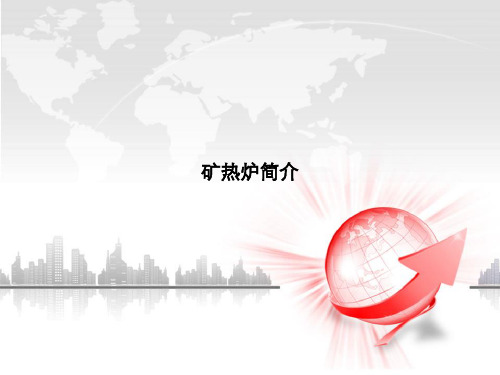
2.2 主要零部件及作用
• 电极把持器 • 电极把持器是矿热炉的核心设备,它是由导电装臵、抱紧 装臵、压放装臵、升降装臵和把持筒、电极壳组成。电极 把持器主要通过抱紧装臵使铜瓦在适宜的压力下贴紧电机 壳,保证从短网传来的大电流过集电环或无极电环的集电 支承器、导电铜管经铜瓦传到电极上。 • 我国目前的矿热炉装备水平差异较大,使用电极把持器类 型较多。目前国内使用的电极把持器如果按照报紧装臵的 类型区分。有径向打螺钉 禁式把持器、大螺栓夹紧式把持 器、锥型环式把持器、组合式或标准组件把持器、波纹管 式把持器等。
铜瓦结构
2.2 主要零部件及作用
• 导电装臵 • 传统的导电装臵一搬包括集电环、导电铜管和铜瓦。 集电 环主要起均压作用,将电流集合起来,然后再分配给导电 铜管,以使每根电极上每块铜瓦的电流基本相等. 铜瓦是 将电能送到电极的主要部件。铜瓦用紫铜铸造,其内部有 冷却水管,铜瓦与电极接触面允许的电流密度在 0.9~2.5A/cm2范围内,铜瓦的高度约等于电极直径,铜瓦 数量可根据每相电极的电流来计算。电极烧结带是整个电 极强度的薄弱环节,铜瓦对电极的抱紧力为0.05~0.15MPa ,接触压力来源于电极把持器。采用组合把持器的电极有 助于改善电极烧结。
2.2 主要零部件及作用
• 烟罩 • 烟罩的作用是封闭炉口,遮挡辐射热,收集冶炼反应过程 中产出的烟气,改善操作环境。烟罩由盖板、侧壁、炉门 、烟罩骨架等组成。烟罩是由钢板和型材焊接成形的,呈 六边形。通过烟罩骨架坐在操作平台上。
2.2 主要零部件及作用
• 烟气导出管 • 烟气导出管的作用是靠自然压差或除尘器的风机形成矮烟 罩内的负压,实现向外排烟的。每台电炉设有2个烟道, 烟道是用钢板和型材制作的。烟道由下部水冷段,烟管段 、钟罩阀和烟道吊挂组成。 • 烟道下部水冷段座在矮烟罩的梁圈上,它是通水冷却的。 烟管段分成若干节,直接通到屋顶外。屋顶外的烟道口上 设有钟罩阀,钟罩阀是用来封闭烟道的。钟罩阀是用烟道 油缸来开闭的,当需要接入除尘器时关闭钟罩阀,烟气通 过三通在风机的作用下将烟气送入除尘器。
矿热炉的工作原理

矿热炉的工作原理
矿热炉是一种用于提炼金属矿石的设备,它通过高温加热将金属矿石中的金属元素分离出来。
矿热炉的工作原理主要包括加热、矿石分解和金属提取三个过程。
矿热炉通过加热的方式使矿石达到高温状态。
矿热炉通常采用燃烧器或电加热器作为热源,将燃料或电能转化为热能,然后通过热能传递给矿石,使其升温。
矿石在高温下开始发生热化反应,使其中的结晶水、氢氧化物、碳酸盐等化合物分解,并释放出相应的气体或液体。
矿石在高温下发生分解反应,使金属元素从矿石中分离出来。
在分解过程中,矿石中的金属元素经过一系列的化学反应,与其他元素或化合物发生作用,形成金属氧化物、金属硫化物等化合物。
矿热炉中的高温环境有利于这些反应的进行,促使金属元素从矿石中转化为易于提取的化合物。
矿热炉通过物理或化学方法将金属元素从化合物中提取出来。
常用的提取方法包括冶炼、还原、浸出等。
冶炼是将金属化合物与熔剂一起加热,使金属熔化并分离出来。
还原是通过加入还原剂,使金属化合物中的金属元素还原为金属。
浸出是将金属化合物与溶剂接触,使金属元素溶解到溶液中。
总的来说,矿热炉的工作原理是将金属矿石加热至高温,使其中的
金属元素分解并转化为易于提取的化合物,最后通过提取方法将金属元素从化合物中分离出来。
矿热炉在矿石提炼中发挥着重要的作用,它不仅可以提高金属矿石的利用率,还可以减少对自然资源的消耗,具有重要的经济和环境意义。
矿热炉运行概述总结范文
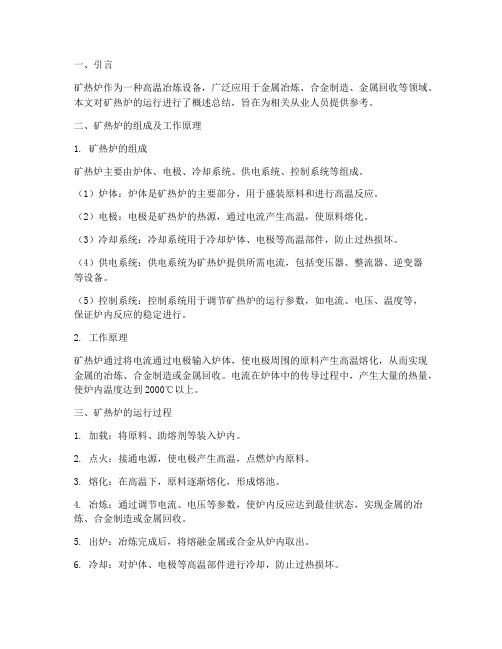
一、引言矿热炉作为一种高温冶炼设备,广泛应用于金属冶炼、合金制造、金属回收等领域。
本文对矿热炉的运行进行了概述总结,旨在为相关从业人员提供参考。
二、矿热炉的组成及工作原理1. 矿热炉的组成矿热炉主要由炉体、电极、冷却系统、供电系统、控制系统等组成。
(1)炉体:炉体是矿热炉的主要部分,用于盛装原料和进行高温反应。
(2)电极:电极是矿热炉的热源,通过电流产生高温,使原料熔化。
(3)冷却系统:冷却系统用于冷却炉体、电极等高温部件,防止过热损坏。
(4)供电系统:供电系统为矿热炉提供所需电流,包括变压器、整流器、逆变器等设备。
(5)控制系统:控制系统用于调节矿热炉的运行参数,如电流、电压、温度等,保证炉内反应的稳定进行。
2. 工作原理矿热炉通过将电流通过电极输入炉体,使电极周围的原料产生高温熔化,从而实现金属的冶炼、合金制造或金属回收。
电流在炉体中的传导过程中,产生大量的热量,使炉内温度达到2000℃以上。
三、矿热炉的运行过程1. 加载:将原料、助熔剂等装入炉内。
2. 点火:接通电源,使电极产生高温,点燃炉内原料。
3. 熔化:在高温下,原料逐渐熔化,形成熔池。
4. 冶炼:通过调节电流、电压等参数,使炉内反应达到最佳状态,实现金属的冶炼、合金制造或金属回收。
5. 出炉:冶炼完成后,将熔融金属或合金从炉内取出。
6. 冷却:对炉体、电极等高温部件进行冷却,防止过热损坏。
7. 维护:定期对矿热炉进行检查、维修,确保设备正常运行。
四、矿热炉运行注意事项1. 严格按照操作规程进行操作,确保安全。
2. 定期检查设备,发现问题及时处理。
3. 保持炉内温度稳定,避免过热或温度过低。
4. 优化原料配比,提高冶炼效率。
5. 注意环境保护,降低有害气体排放。
五、总结矿热炉作为一种高温冶炼设备,在金属冶炼、合金制造、金属回收等领域具有广泛的应用。
通过对矿热炉的组成、工作原理、运行过程及注意事项进行概述总结,有助于提高矿热炉的运行效率,确保设备安全稳定运行。
矿热炉的基本原理
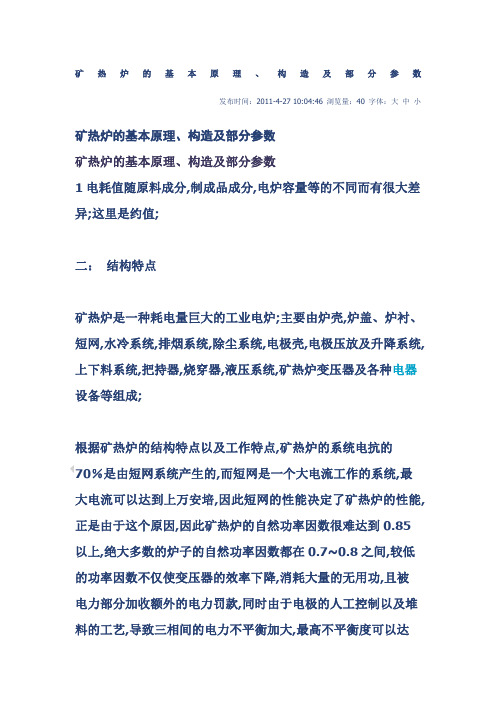
炉膛直径mm
6200
6400
炉膛深度mm
2200
1900
极心圆直径mm
2800±100
2800-3000
电极直径mm
1050
1100
电极电流密度A/cm2
5.95
6.15
因此目前也有部分单位在新建炉子上采取了高低压同时进行无功补偿的措施,来解决以上的问题,在短网端进行补偿能够大幅提高短网端的功率因数,降低电耗,针对炉变低压侧短网的大量无功消耗和不平衡性,兼顾有效提高功率因数而实施无功就地补偿技术改造,从技术上来讲是可靠、成熟的,从经济上来讲,投入和产出是成正比的;在矿热炉低压侧针对短网无功消耗和其布置长度不一致导致的三相不平衡现象而实施的无功就地补偿,无论在提高功率因数、吸收谐波,还是在增产、降耗上,都有着高压补偿无法比拟的优势;但是由于成本较高,同时由于工作环境恶劣,因此寿命受到极大的影响,同时短网低压端无功补偿也带来了谐波增加,因此又必须采取措施来抑制3~7次谐波,从而使投入加大,投资回收周期加长,同时后续维护费用高,综合效益不佳;一般仅适用于新建炉子
矿热炉炼硅的原理
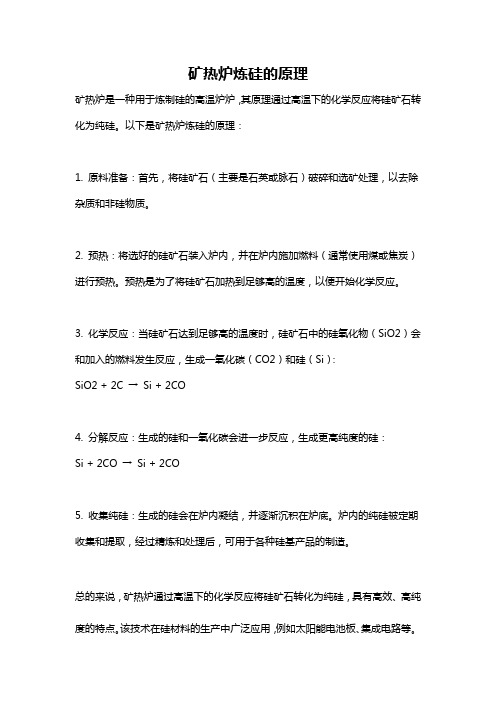
矿热炉炼硅的原理
矿热炉是一种用于炼制硅的高温炉炉,其原理通过高温下的化学反应将硅矿石转化为纯硅。
以下是矿热炉炼硅的原理:
1. 原料准备:首先,将硅矿石(主要是石英或脉石)破碎和选矿处理,以去除杂质和非硅物质。
2. 预热:将选好的硅矿石装入炉内,并在炉内施加燃料(通常使用煤或焦炭)进行预热。
预热是为了将硅矿石加热到足够高的温度,以便开始化学反应。
3. 化学反应:当硅矿石达到足够高的温度时,硅矿石中的硅氧化物(SiO2)会和加入的燃料发生反应,生成一氧化碳(CO2)和硅(Si):
SiO2 + 2C →Si + 2CO
4. 分解反应:生成的硅和一氧化碳会进一步反应,生成更高纯度的硅:
Si + 2CO →Si + 2CO
5. 收集纯硅:生成的硅会在炉内凝结,并逐渐沉积在炉底。
炉内的纯硅被定期收集和提取,经过精炼和处理后,可用于各种硅基产品的制造。
总的来说,矿热炉通过高温下的化学反应将硅矿石转化为纯硅,具有高效、高纯度的特点。
该技术在硅材料的生产中广泛应用,例如太阳能电池板、集成电路等。
- 1、下载文档前请自行甄别文档内容的完整性,平台不提供额外的编辑、内容补充、找答案等附加服务。
- 2、"仅部分预览"的文档,不可在线预览部分如存在完整性等问题,可反馈申请退款(可完整预览的文档不适用该条件!)。
- 3、如文档侵犯您的权益,请联系客服反馈,我们会尽快为您处理(人工客服工作时间:9:00-18:30)。
引用矿热炉的基本原理、构造及部分参数
引用
ycmsol 的矿热炉的基本原理、构造及部分参数
摘要:
本文就矿热炉短网实施无功就地补偿的增产及降耗从理论上作出了阐述,指出了实施短网无功就地补偿应注意的相关技术问题,阐明了中国冶金设备总公司矿热
炉短网无功就地补偿设备的特点。
关键词:
矿热炉短网无功就地补偿
一原理用途
矿热炉又称电弧电炉或电阻电炉。
它主要用于还原冶炼矿石,碳质还原剂及溶剂等原料。
主要生产硅铁,锰铁,铬铁、钨铁、硅锰合金等铁合金,是冶金工业中重要工业原料及电石等化工原料。
其工作特点是采用碳质或镁质耐火材料作炉衬,使用自培电极。
电极插入炉料进行埋弧操作,利用电弧的能量及电流通过炉料的,因炉料的电阻而产生能量来熔炼金属,陆续加料,间歇式出铁渣,连续作用的一种工业电炉。
矿热炉主要类别、用途
工业余热是指钢铁、石化、建材、有色金属的工业生产线中产生的大量余热。
而余热发电技术就是指利用企业的高品位热量进行回收,并集中转化为电力供企业自用的技术。
我国一直将利用余热发电作为节能降耗、实现循环发展的重要措施之一,给予了大力支持,目前我国的余热发电技术应用领域不断扩大,但在铁合金、电石里领域中,烟气余热以及其他余热综合回收发电技术仍比较欠缺。
日前,矿热炉余热回收利用发电技术方案研讨会在京召开,来自国家能源办、钢铁研究总院、国家发改委以及各行业协会的领导和专家共同讨论了由西安瑞驰能源工程技术有限公司开发,针对铁合金、电石等领域的余热发电技术。
铁合金、电石等领域的余热回收发电由于量大面广,一直不为大家重视,该技术填补了这一空缺,提高了余热回收率,降低了成本。
当前,节能减排已成为我国的基本国策,而铁合金行业又正是典型的高能耗行业,在这一行业里推广余热回收发电技术有利于降低企业能耗,提高能源利用效率。
不久前国家三部委发文取消了高耗能企业的优惠电价,对铁合金行业的电价优惠,自2007年10月20日起全部取消。
在用电成本增加的情况下,铁合金企业余热回收发电项目的投资回收期将进一步缩短,该项技术将会有更好的发展前景。
铁合金电炉的烟气收尘和余热回收
冶炼铁合金的主要设备。
铁合金电炉分为还原电炉和精炼电炉两类。
还原电炉又称埋弧电炉或矿热电炉,采取电极插入炉料的埋弧*作,还原电炉有敞口、封闭(或半封闭),炉体有固定、旋转等各种形式。
50年代以前普遍采用敞口固定式电炉(图1a铁合金还原电炉),随着环境保护要求的提高和余热利用技术的进展,对不同产品分别采用封闭式电炉(图1b铁合金还原电炉)或矮烟罩、半封闭式电炉(图1c铁合金还原电炉)。
炉体旋转可以消除悬料、减少结壳“刺火”使布料均匀、反应区扩大,以利炉况顺行。
电炉容量(在铁合金生产中指电炉变压器容量,按千伏安计,用以标志电炉能力)在50年代以前一般从几百至一万千伏安左右,后来逐渐向大型化发展。
70年代新建电炉一般为20000~40000千伏安,最大的封闭式电炉达75000千伏安,最大的半封闭炉达96000千伏安。
现代铁合金电炉一般为圆形炉体,配备三根电极。
大型锰铁电炉有采用矩形多电极的。
大型硅铁电炉有些装备旋转机构,炉体以30~180小时旋转360°的速度沿水平方向旋转或往复摆动。
封闭电炉设置密封的炉盖,半封闭电炉在烟罩下设有可调节开启度的*作门,以控制抽入空气量和烟气温度。
电极系统广泛采用连续自焙电极,最大的直径可达2000毫米,有的还做成中空式。
连续自焙电极由薄钢板电极壳和电极糊组成,在运行中电极糊利用电流通过时产生的热量和炉热的传导辐射自行焙烧。
随着电极的消耗,电极壳要相应逐节焊接,并向壳内充填电极糊。
电极把持器由接触颊板(导电铜瓦)、铜管和把持环等构件组成,它的作用是将电流输向电极,并将电极夹持在一定的高度上,还可以调节电极糊的烧结状态。
电极升降和压放装置吊挂着整根电极,用以调整电极插入深度。
从变压器低压侧到电极把持器的馈电线路通称短网,是一段大截面的导体,用以输送大电流至炉内。
大型电炉变压器的二次绕组多数通过短网在电极上完成三角形接线。
整个网路由硬母线束、软母线束和铜管组成。
精炼电炉用于精炼中碳、低碳、微碳铁合金。
电炉容量一般为1500~6000千伏安,采用敞口固定或带盖倾动形式。
前者类似还原电炉,可配备连续自焙电极;后者类似电弧炼钢炉,使用石墨或炭质电极。
铁合金电炉煤气净化铁合金还原电炉生产过程中产生大量煤气。
用敞口电炉生产时,煤气遇空气燃烧成为烟气,量大尘多,既难净化,又不利于能量回收,长期污染环境,形成公害并造成能量损失。
70年代以来,为了保护环境和节约能源,铁合金还原电炉逐渐由敞口电炉改为封闭或半封闭电炉。
冶炼锰铁、铬铁等铁合金用封闭电炉,冶炼需要料面*作的铁合金(硅铁、金属硅等),则用半封闭电炉。
封闭电炉设置密封的炉盖和泄爆装置,产生的煤气于未燃状态引出,导入煤气净化设施净化回收。
煤气发生过程连续稳定,煤气体积只有敞口电炉烟气体积的1~2%。
因此煤气净化设备小,组合简单,净化*作便利。
煤气净化一般采
用湿法工艺。
煤气含CO、H□、CH□等有效燃料成分约占气体体积的80%,主要是CO,发热值为2100~2400千卡/标米□。
为了治理硅铁电炉的烟气,起初将敞口电炉的高烟罩改为矮烟罩,后来发展成为半封闭电炉。
其发展过程见图2敞口铁合金电炉烟气治理发展过程。
能控制烟气量便于净化和回收热能。
装设余热锅炉时,回收的热量可达电炉总耗能量的30%或总耗电量的65%,如用于发电可回收电能约20%。
烟气净化一般采用干法工艺。
东方所提供全套烟气净化及余热回收方案!
(1)电耗值随原料成分,制成品成分,电炉容量等的不同而有很大差异。
这里是约值。
二结构特点
矿热炉是一种耗电量巨大的工业电炉。
主要由炉壳,炉盖、炉衬、短网,水冷系统,排烟系统,除尘系统,电极壳,电极压放及升降系统,上下料系统,把持器,烧穿器,液压系统,矿热炉变压器及各种电器设备等组成。
矿热炉共分三层
第一层为炉壳,炉衬,出铁系统,烧穿器等组成。
第二层
(1)炉盖。
现代人型矿热炉人多数采用密闭式,具有密封炉盖。
采用这样的结构可把生产中产生的废气(主要成分是一氧化碳)收集起来综合利用,并可减少电路的热损失,降低电极上部的温度,改善操作条件。
(2)电极夹持器。
人多数矿热炉都由三相供电,按正三角形对称位置布置在炉膛中间。
大型矿热炉一般采用无烟煤,焦碳和沥青煤油拌合成的电极料,在电炉工作过程中自己培烧成的电极。
(3)短网
(4)铜瓦
(5)电极壳
(6)下料系统
(7)倒炉机
(8)排烟系统
(9)水冷系统
(10)矿热炉变压器
(11)操作系统
第三层
(1)液压系统
(2)电极压放装置
(3)电极升降系统
(4)钢平台
(5)料斗及环行布料车
其他附属;斜桥上料系统,电子配料系统等三各种技术参数。