现代船舶建造技术
船舶建造与维护的技术

船舶建造与维护的技术船舶是人类交通运输和海上经济中不可缺少的组成部分。
在古代,船只的建造和维护是非常简单的,只有木头和绳索的工具。
但是现代船舶的建造和维护是一个完整的系统工程,涉及各种多学科知识,包括机械工程、电气工程、材料工程以及环保工程。
在本文中,我们将介绍现代船舶建造和维护的关键技术。
一、船舶的设计和建造现代船舶的设计始于从计算机辅助设计(CAD)开始,通过对船型的分析和优化来确定船舶的外形和内部空间,包括舱室、生活区、甲板等。
经过审查和确认后,设计师通过计算机模拟来执行船舶结构,以确保船舶的强度和浮力。
这是现代建造船舶的重要步骤。
船舶建造的材料也随着科技的进步而不断变化。
在古代,船只的建造只有木头和铁件,但是现代船只的建造则需要使用各种金属、塑料、玻璃纤维等材料,以满足船舶对不同性能和强度的要求。
例如,抗风险和磨损的船舶龙骨等,就需要使用高强度钢材。
二、船舶设备和系统的选择和维护现代船舶需要各种复杂的设备和系统来支撑其正常运行,如船舶控制系统、船用机械设备、电气设备等。
这些设备一旦出现故障,可能导致严重的安全风险。
因此,船舶设备和系统的选择和维护显得格外重要。
船舶控制系统通常包括主机控制、动力定位、自航导航、交通控制等。
现代船舶控制系统使用高科技电子产品,如先进的计算机、雷达、电视监控技术、GPS定位系统等。
在使用这些电子设备时,需要注意防潮、防震等特殊条件下的使用。
船用机械设备,如主机、发电机、空调、泵等,是现代船舶不可或缺的一部分。
这些设备可能会随设备老化、损坏或在极端环境下使用而出现故障。
因此,维护这些设备的日常保养和维修养护显得尤为重要。
三、船舶安全工程技术船舶作为一种运输工具,在运输过程中需要考虑安全因素。
因此,船舶安全工程技术是现代船舶建造和维护中不可忽略的技术。
首先,需要为船舶安装声纳和雷达等设备,以便在极端天气下减少船舶的碰撞风险。
其次,需要防范火灾和爆炸风险,通过冷却系统、火焰检测器和喷水系统等设备来降低这些风险。
现代船舶建造工艺流程-壳舾涂一体化造船模式
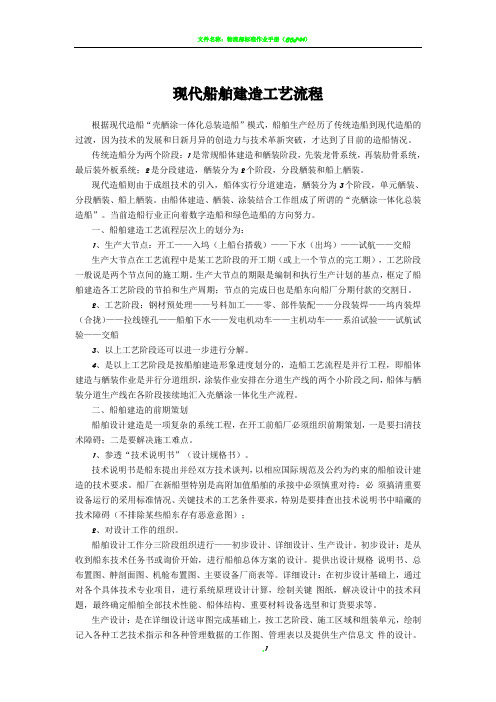
现代船舶建造工艺流程根据现代造船“壳舾涂一体化总装造船”模式,船舶生产经历了传统造船到现代造船的过渡,因为技术的发展和日新月异的创造力与技术革新突破,才达到了目前的造船情况。
传统造船分为两个阶段:1是常规船体建造和舾装阶段,先装龙骨系统,再装肋骨系统,最后装外板系统;2是分段建造,舾装分为2个阶段,分段舾装和船上舾装。
现代造船则由于成组技术的引入,船体实行分道建造,舾装分为3个阶段,单元舾装、分段舾装、船上舾装。
由船体建造、舾装、涂装结合工作组成了所谓的“壳舾涂一体化总装造船”。
当前造船行业正向着数字造船和绿色造船的方向努力。
一、船舶建造工艺流程层次上的划分为:1、生产大节点:开工——入坞(上船台搭载)——下水(出坞)——试航——交船生产大节点在工艺流程中是某工艺阶段的开工期(或上一个节点的完工期),工艺阶段一般说是两个节点间的施工期。
生产大节点的期限是编制和执行生产计划的基点,框定了船舶建造各工艺阶段的节拍和生产周期;节点的完成日也是船东向船厂分期付款的交割日。
2、工艺阶段:钢材预处理——号料加工——零、部件装配——分段装焊——坞内装焊(合拢)——拉线镗孔——船舶下水——发电机动车——主机动车——系泊试验——试航试验——交船3、以上工艺阶段还可以进一步进行分解。
4、是以上工艺阶段是按船舶建造形象进度划分的,造船工艺流程是并行工程,即船体建造与舾装作业是并行分道组织,涂装作业安排在分道生产线的两个小阶段之间,船体与舾装分道生产线在各阶段接续地汇入壳舾涂一体化生产流程。
二、船舶建造的前期策划船舶设计建造是一项复杂的系统工程,在开工前船厂必须组织前期策划,一是要扫清技术障碍;二是要解决施工难点。
1、参透“技术说明书”(设计规格书)。
技术说明书是船东提出并经双方技术谈判,以相应国际规范及公约为约束的船舶设计建造的技术要求。
船厂在新船型特别是高附加值船舶的承接中必须慎重对待:必须搞清重要设备运行的采用标准情况、关键技术的工艺条件要求,特别是要排查出技术说明书中暗藏的技术障碍(不排除某些船东存有恶意意图);2、对设计工作的组织。
现代造船技术
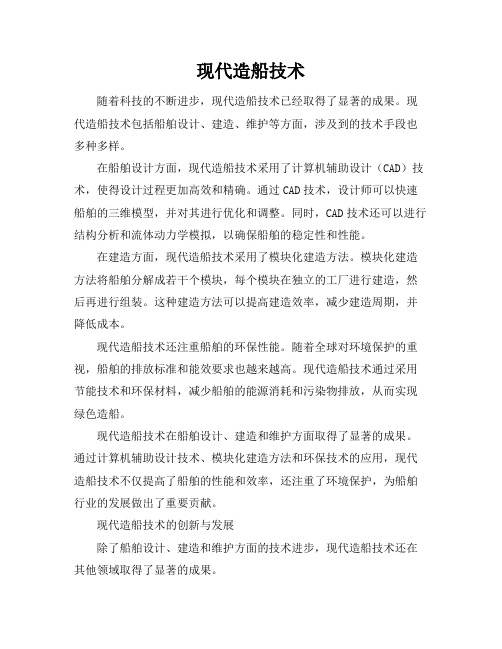
现代造船技术随着科技的不断进步,现代造船技术已经取得了显著的成果。
现代造船技术包括船舶设计、建造、维护等方面,涉及到的技术手段也多种多样。
在船舶设计方面,现代造船技术采用了计算机辅助设计(CAD)技术,使得设计过程更加高效和精确。
通过CAD技术,设计师可以快速船舶的三维模型,并对其进行优化和调整。
同时,CAD技术还可以进行结构分析和流体动力学模拟,以确保船舶的稳定性和性能。
在建造方面,现代造船技术采用了模块化建造方法。
模块化建造方法将船舶分解成若干个模块,每个模块在独立的工厂进行建造,然后再进行组装。
这种建造方法可以提高建造效率,减少建造周期,并降低成本。
现代造船技术还注重船舶的环保性能。
随着全球对环境保护的重视,船舶的排放标准和能效要求也越来越高。
现代造船技术通过采用节能技术和环保材料,减少船舶的能源消耗和污染物排放,从而实现绿色造船。
现代造船技术在船舶设计、建造和维护方面取得了显著的成果。
通过计算机辅助设计技术、模块化建造方法和环保技术的应用,现代造船技术不仅提高了船舶的性能和效率,还注重了环境保护,为船舶行业的发展做出了重要贡献。
现代造船技术的创新与发展除了船舶设计、建造和维护方面的技术进步,现代造船技术还在其他领域取得了显著的成果。
在船舶材料方面,现代造船技术采用了先进的材料,如高强度钢、复合材料和轻质合金等。
这些材料不仅提高了船舶的强度和耐用性,还减轻了船舶的重量,提高了船舶的航行性能和燃油效率。
在船舶动力系统方面,现代造船技术采用了高效的发动机和推进系统。
通过采用先进的燃烧技术和能效优化,现代造船技术使得船舶的燃油消耗更低,排放更少,同时也提高了船舶的动力性能和可靠性。
在船舶自动化和智能化方面,现代造船技术采用了先进的控制系统和传感器技术。
通过自动化和智能化技术,船舶可以实现自动导航、自动避障和远程监控等功能,提高了船舶的安全性和运营效率。
现代造船技术的创新与发展除了船舶设计、建造和维护方面的技术进步,现代造船技术还在其他领域取得了显著的成果。
船舶制造工艺探索现代船舶建造的先进技术
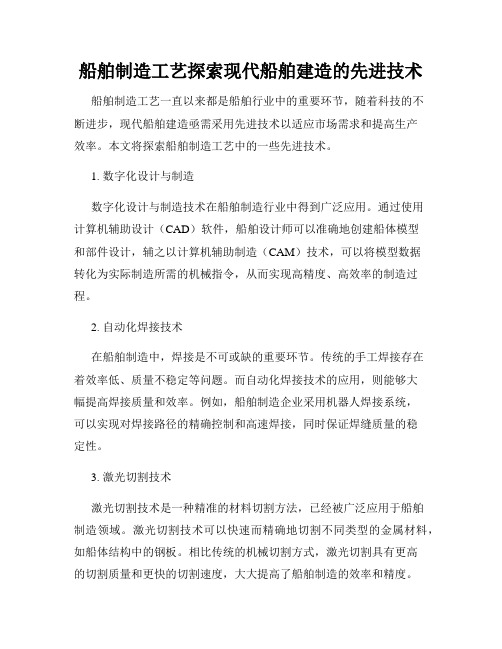
船舶制造工艺探索现代船舶建造的先进技术船舶制造工艺一直以来都是船舶行业中的重要环节,随着科技的不断进步,现代船舶建造亟需采用先进技术以适应市场需求和提高生产效率。
本文将探索船舶制造工艺中的一些先进技术。
1. 数字化设计与制造数字化设计与制造技术在船舶制造行业中得到广泛应用。
通过使用计算机辅助设计(CAD)软件,船舶设计师可以准确地创建船体模型和部件设计,辅之以计算机辅助制造(CAM)技术,可以将模型数据转化为实际制造所需的机械指令,从而实现高精度、高效率的制造过程。
2. 自动化焊接技术在船舶制造中,焊接是不可或缺的重要环节。
传统的手工焊接存在着效率低、质量不稳定等问题。
而自动化焊接技术的应用,则能够大幅提高焊接质量和效率。
例如,船舶制造企业采用机器人焊接系统,可以实现对焊接路径的精确控制和高速焊接,同时保证焊缝质量的稳定性。
3. 激光切割技术激光切割技术是一种精准的材料切割方法,已经被广泛应用于船舶制造领域。
激光切割技术可以快速而精确地切割不同类型的金属材料,如船体结构中的钢板。
相比传统的机械切割方式,激光切割具有更高的切割质量和更快的切割速度,大大提高了船舶制造的效率和精度。
4. 三维打印技术三维打印技术作为一项新兴的先进制造技术,也在船舶制造中得到了尝试。
船舶制造企业可以使用三维打印技术制造船舶组件,通过将材料逐层堆叠来实现船舶部件的快速制造。
利用三维打印技术,不仅可以减少制造成本和时间,而且可以实现更复杂和个性化的设计。
5. 船舶智能制造技术船舶智能制造技术涵盖了多个方面,如物联网、传感器技术、云计算等。
通过将多个智能设备和传感器应用于船舶制造过程中,可以实现生产数据、设备状态等的实时监控和分析。
这有助于船舶制造企业优化生产流程,提高生产效率和产品质量。
综上所述,船舶制造工艺中的先进技术对现代船舶建造具有重要意义。
数字化设计与制造、自动化焊接技术、激光切割技术、三维打印技术以及船舶智能制造技术,都为船舶制造业的发展提供了新的可能性。
新型船舶建造技术的应用前景
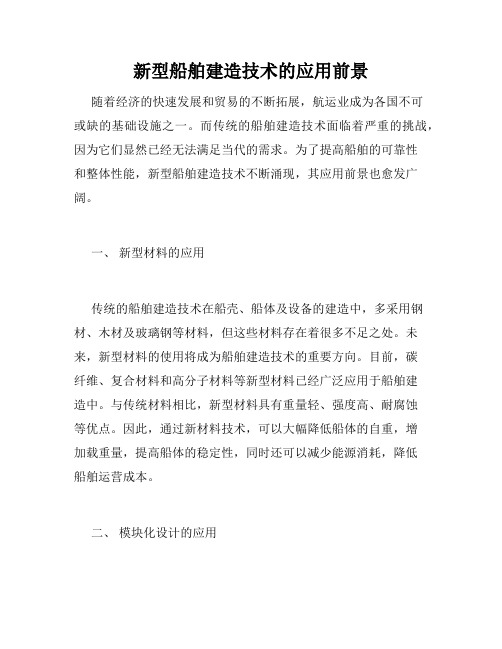
新型船舶建造技术的应用前景随着经济的快速发展和贸易的不断拓展,航运业成为各国不可或缺的基础设施之一。
而传统的船舶建造技术面临着严重的挑战,因为它们显然已经无法满足当代的需求。
为了提高船舶的可靠性和整体性能,新型船舶建造技术不断涌现,其应用前景也愈发广阔。
一、新型材料的应用传统的船舶建造技术在船壳、船体及设备的建造中,多采用钢材、木材及玻璃钢等材料,但这些材料存在着很多不足之处。
未来,新型材料的使用将成为船舶建造技术的重要方向。
目前,碳纤维、复合材料和高分子材料等新型材料已经广泛应用于船舶建造中。
与传统材料相比,新型材料具有重量轻、强度高、耐腐蚀等优点。
因此,通过新材料技术,可以大幅降低船体的自重,增加载重量,提高船体的稳定性,同时还可以减少能源消耗,降低船舶运营成本。
二、模块化设计的应用传统的船舶建造技术通常采用大块船体组装,难以满足对船舶性能和灵活性的快速变化需求。
现在,模块化设计已经成为一种流行的建造技术,它可以提高船舶的设计和建造效率。
模块化设计是将船舶按组件模块化,然后将各部件组装在厂区内,减少了施工现场的工作量,提高了建造速度和效率。
同时,模块化设计可以减少误差和缩短时间,降低生产成本,同时对环境污染的影响也非常小。
三、智能制造的应用随着船舶建造技术的不断发展,智能制造技术逐渐成为船舶建造的新趋势。
智能制造技术是通过光学传感、无线通讯、计算机控制等先进技术,将生产过程与信息技术无缝集成,从而达到减少船舶制造成本,提高生产效率。
因此,在船舶建造生产过程中,智能化设计和生产辅助设备的普及和实施,将促使船舶生产的数字化和网络化,大幅提高船舶建造的精度和质量。
四、智能化航行的应用智能化航行是船舶建造技术的第四大趋势。
根据能源消耗率、驾驶员劳动强度等因素,自动化驾驶系统、船舶智能化控制、智能化导航等技术已经逐步应用于船舶建造中。
智能化航行可以提高船舶的运营效率和安全性。
同时,它也能够减少船舶的耗油量和排放,从而达到保护环境和节能减排的目的。
现代船舶建造工艺流程-壳舾涂一体化造船模式

现代船舶建造工艺流程根据现代造船“壳舾涂一体化总装造船”模式,船舶生产经历了传统造船到现代造船的过渡,因为技术的发展和日新月异的创造力与技术革新突破,才达到了目前的造船情况。
传统造船分为两个阶段:1是常规船体建造和舾装阶段,先装龙骨系统,再装肋骨系统,最后装外板系统;2是分段建造,舾装分为2个阶段,分段舾装和船上舾装。
现代造船则由于成组技术的引入,船体实行分道建造,舾装分为3个阶段,单元舾装、分段舾装、船上舾装。
由船体建造、舾装、涂装结合工作组成了所谓的“壳舾涂一体化总装造船”。
当前造船行业正向着数字造船和绿色造船的方向努力。
一、船舶建造工艺流程层次上的划分为:1、生产大节点:开工——入坞(上船台搭载)——下水(出坞)——试航——交船生产大节点在工艺流程中是某工艺阶段的开工期(或上一个节点的完工期),工艺阶段一般说是两个节点间的施工期。
生产大节点的期限是编制和执行生产计划的基点,框定了船舶建造各工艺阶段的节拍和生产周期;节点的完成日也是船东向船厂分期付款的交割日。
2、工艺阶段:钢材预处理——号料加工——零、部件装配——分段装焊——坞内装焊(合拢)——拉线镗孔——船舶下水——发电机动车——主机动车——系泊试验——试航试验——交船3、以上工艺阶段还可以进一步进行分解。
4、是以上工艺阶段是按船舶建造形象进度划分的,造船工艺流程是并行工程,即船体建造与舾装作业是并行分道组织,涂装作业安排在分道生产线的两个小阶段之间,船体与舾装分道生产线在各阶段接续地汇入壳舾涂一体化生产流程。
二、船舶建造的前期策划船舶设计建造是一项复杂的系统工程,在开工前船厂必须组织前期策划,一是要扫清技术障碍;二是要解决施工难点。
1、参透“技术说明书”(设计规格书)。
技术说明书是船东提出并经双方技术谈判,以相应国际规范及公约为约束的船舶设计建造的技术要求。
船厂在新船型特别是高附加值船舶的承接中必须慎重对待:必须搞清重要设备运行的采用标准情况、关键技术的工艺条件要求,特别是要排查出技术说明书中暗藏的技术障碍(不排除某些船东存有恶意意图);2、对设计工作的组织。
现代造船模式下的生产布局技术
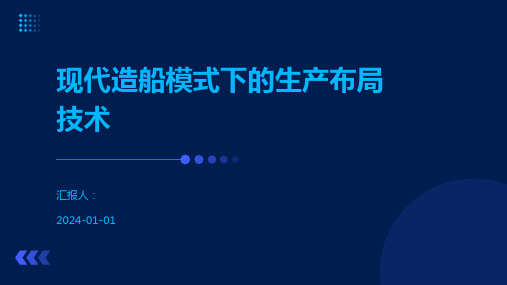
以中间产品为导向,实行区域总 装、壳舾涂一体化作业,实现生 产过程的连续性、均衡性和协调 性。
现代造船模式的重要性
01
02
03
提高生产效率
通过优化生产布局和工艺 流程,减少生产过程中的 等待和重复作业时间,提 高生产效率。
降低生产成本
实现规模化、标准化生产 ,降低原材料和能源消耗 ,减少生产成本。
安全与质量控制问题
在大型复杂的船舶建造过程中,安全与质量 控制管理难度大。
解决方案与实施策略
引入先进的生产布局理念
如模块化、精益生产等,以适应现代造 船的高效需求。
强化信息沟通与协同
利用信息化手段,如物联网、大数据 等,实现各部门之间的信息实时共享
和协同作业。
优化资源配置
通过资源整合、动态调度等手段,实 现资源的最优配置和共享。
技术更新
关注行业内的技术发展动态,及时引入新的技术 和设备,提升生产布局的效率和灵活性。
跨部门协作
加强各部门之间的沟通和协作,共同推动生产布 局的持续改进。
ABCD
员工培训
定期对员工进行培训和教育,提高员工对生产布 局的认识和技术水平。
激励机制
建立有效的激励机制,鼓励员工积极参与生产布 局的改进和创新。
定义
生产布局是指根据企业生产需求,对 生产系统各要素进行合理配置和组织 ,以实现高效、低成本、高柔性生产 的过程。
目标
提高生产效率、降低生产成本、优化 资源配置、提升企业竞争力。
生产布局的原则与要素
原则
统一规划、功能分区、物流顺畅、信 息流便捷。
要素
生产线、工作站、设备、工具、物料 、人员等。
生产布局的优化方法
以提高生产效率,降低生产成本,有利于标准化和专业化生产。
总段造船法

总段造船法
总段造船法,也称为“巨型总段造船法”,是一种现代化的船舶建造技术。
它的核心思想是将整个船体分成若干个大型的“总段”(也称为“巨型段”或“船段”),每个总段都是一个自成体系的模块,可以在陆地上进行预制、加工和组装,然后再将它们运输到船厂进行现场组装。
这种方法可以大大缩短船舶的建造周期,提高生产效率,并且可以降低建造成本。
总段造船法的主要优点包括:
1. 提高生产效率:总段造船法可以将整个船体分成若干个大型的模块,这些模块可以在陆地上进行预制、加工和组装,然后再将它们运输到船厂进行现场组装。
这样可以大大缩短船舶的建造周期,提高生产效率。
2. 降低建造成本:总段造船法可以减少现场加工和组装的工作量,降低了人力、材料和设备的使用成本,同时也减少了建造过程中的浪费和损耗。
3. 提高质量和安全性:总段造船法可以在陆地上进行预制、加工和组装,这样可以更好地控制质量和安全性。
此外,由于总段之间可以互相替换,一旦发现质量问题,可以更容易地进行修复和更换。
4. 降低环境影响:总段造船法可以减少现场加工和组装
的工作量,降低了噪音、废气和废水的排放量,从而降低了对环境的影响。
总段造船法是一种现代化的船舶建造技术,具有许多优点,可以提高生产效率、降低建造成本、提高质量和安全性,并且可以降低环境影响。
- 1、下载文档前请自行甄别文档内容的完整性,平台不提供额外的编辑、内容补充、找答案等附加服务。
- 2、"仅部分预览"的文档,不可在线预览部分如存在完整性等问题,可反馈申请退款(可完整预览的文档不适用该条件!)。
- 3、如文档侵犯您的权益,请联系客服反馈,我们会尽快为您处理(人工客服工作时间:9:00-18:30)。
3、内腐蚀控制
• 缓蚀剂、加腐蚀余量、内涂层、采用
耐腐蚀管材或内衬、保持输送介质无
水。
4、混凝土加重层
确保管道在海床上
的稳定性,保护防
腐涂层和管道本身 安装、运行期免受 机械损坏。
5、管中管 输送高粘度、高含蜡、高凝点原油的 海底管道—双层结构的管中管:
两层管之间填充绝热保温材料,减少
输送中的热损失,确保原油的流动性能。
• • •
• • • •
海底管道与平台的连接
海底管道与平台的连接
Thank
you !
(*^__^*)
外钢管具有隔水、保护保温层作用,加大
管道的负浮力,可取代混凝土加重层。
6、柔性管
为了早产油、早见到经济效益,海上许多临
时和早期生产装置上的集油气管道常使用柔性管。
柔性管:钢丝加强筋、多层热塑材料组合而
成,具有非常好的耐腐蚀和保温性能,使用寿命
长,易回收可重复使用。
目前生产的柔性管直径已达16英寸,破裂应 力可达280MPa,可承受2100米水深的水柱压力。
3、卷筒法
• 用于小口径管道 • 日铺管速度快,大大降低铺设费用。
(二)
拖管法
• 用于平台间比较短的集油气管道、注水管道、
装有控制电缆的管束铺设。
• 好处:管串的预制、试压、检验工作可在陆的拖管船。
• 四种托管施工方式:沿海水平面拖管、海水
平面下拖管、海平面以上、沿海床面拖管。
Return
二、海底管道的铺设方法
(一)铺管船法
铺管能力:可铺设60英寸、水深2000米。
1、S型铺管法
• 预制管段在船上进行组对、焊接、涂防腐层和
• •
无损探伤 从托管架下到海床管道为S型 水深一般不超过300米。
2、J型铺管法
• 托管架垂直向下 • 在立式塔架上进行组对、焊接 • 适于深水海域
深海采油平台下的管道铺设
成员:汤佳勇,王小虎,石迎潮
海底管道是通过密闭的管道在海底连续地 输送大量油(气)的管道,是海上油(气)田 开发生产系统的主要组成部分,也是目前最快 捷、最安全和经济可靠的海上油气运输方式。
• 世界上第一条海底管道:1951年美国在墨西哥湾
Cameron气田铺设的16公里的海底管道。
Return
三、海底管道的挖沟方法
海底管道等铺设好以后,裸露 在海床上,这就需要采用开沟犁 等工作,在已铺管线位置进行后 挖沟,然后管线进入沟内保护起 来。
• • • •
水力喷射 液化 机械切割 挖沟犁
Return
四、海底管道的立管连接
1、预先安装在平台上的立管和管 道连接方法: 法兰连接 高压舱焊接 机械接头 2、现场安装的立管和管道的连接 方法: 铺管船上焊接 J型导管内拉管 J型导管内反向拉管 通过平台底部的弯管滑轨弯管法。
• 世界累计铺设海底管道约100000公里,水深已达
1463米,海管径42英寸(1英寸=25.4mm)。
• 我国到1998年底,累计铺设海管约2000公里。南
海的崖城13-1气田到香港的28英寸、778公里高 压输气管道是世界第二长的海底管道。
海底管道铺设
海底管道焊接
海管的保护
海底管道的铺设方法
海底管道的挖沟方法
海底管道的立管连接
一、海管的保护(防腐涂层和加重层)
确保海管在寿命期内能安全运行,管道系
统应防止输送介质和海水引起的内外腐蚀。 1、外涂层:
• 在实际的海水环境中,提供有效的腐蚀保护。 • 煤焦油瓷漆、沥青瓷漆、环氧树脂、聚乙烯
树脂、聚丁橡胶。
2、阴极保护 作为外涂层的补充和加强。以牺牲阳 极为基础,材料可以是铝或锌的合金。 有涂层的海管上,两个阳极之间的间 距一般不超过150米。
1、沿海水平面拖管 施工费用低
2、在海水平面下拖管 极大减小了表面风浪流的影响。
3、在海床面以上拖管
通过铁链悬挂在水中长度的变化, 避免管线与海床接触。
4、沿海床面拖管(底拖法)
优点:作业时管串不受气候条件的影响; 气候条件超出拖船的能力,可安全停 放在海底; 不需要后拉船。 缺点:拖船马力要大;易损坏外涂层; 费用相对高