永磁铁氧体预烧料的加工工艺及方法
永磁铁氧体生产工艺

永磁铁氧体生产工艺永磁铁氧体是一种具有高磁性和高温稳定性的磁性材料,广泛应用于电机、发电机、传感器等领域。
永磁铁氧体的生产工艺一般包括以下几个步骤:1. 原料准备:永磁铁氧体的主要原料是氧化铁、氧化钡、氧化钴等化合物,需要按照一定的比例进行配料,同时还需要添加一定的助磁剂和其他添加剂。
配料完成后,将原料送入球磨机进行混合研磨,以提高混合度和颗粒粒度的均匀性。
2. 造粒压制:将研磨后的混合粉末送入造粒机进行压制成形。
常用的造粒方法有干压造粒和湿压造粒两种。
干压造粒是将混合粉末在模具中进行压制,形成预定形状的颗粒;湿压造粒则是在添加一定的液体和黏结剂的情况下进行造粒,然后通过干燥将颗粒固化。
3. 烧结和烧结控制:将压制成形的颗粒送入高温炉进行烧结。
在烧结过程中,由于高温作用,颗粒之间的颗粒间结合力增强,形成致密的材料,颗粒内部排列有序。
烧结温度和时间的控制对于材料的性能具有重要影响,需要进行精确控制。
4. 后处理:烧结后的材料还需要通过一些后处理工艺来进一步提高其性能。
常见的后处理方法包括磁化处理、热处理和磁场处理等。
磁化处理是将材料置于强磁场中进行磁化,以提高材料的磁性能;热处理则是利用高温进行退火或淬火等处理,以改变材料的晶体结构和性能;磁场处理则是利用磁场对材料进行预处理,提高材料的磁性能。
5. 检验和包装:经过上述工艺步骤后,对生产出的永磁铁氧体进行质量检验,包括磁性能测试、密度测试、外观检查等。
合格的产销售前,还需要进行包装和存储,以保证产品的质量和使用寿命。
以上是永磁铁氧体的基本生产工艺,不同厂家和产品可能会有所差异,但总体上都是通过原料准备、造粒压制、烧结和后处理等环节来完成材料的制备。
随着技术的不断发展,工艺也在不断改进和优化,以提高材料的性能和生产效率。
铁氧体磁铁制造工艺流程

铁氧体磁铁制造工艺流程铁氧体磁铁制造工艺流程一、概述铁氧体磁铁是一种常见的永磁材料,具有高磁能积、高矫顽力、高稳定性等优点,广泛应用于电机、声学器件、传感器等领域。
本文将介绍铁氧体磁铁的制造工艺流程。
二、原材料准备1. 铁氧体粉末:选择适当的铁氧体粉末是制造高质量铁氧体磁铁的关键。
常用的粉末有SrFe12O19、BaFe12O19等。
2. 粘结剂:粘结剂可以增加粉末之间的黏着力,提高成型后的强度和韧性。
常用的粘结剂有聚乙烯醇(PVA)、聚乙烯(PE)等。
3. 溶剂:溶剂用于稀释粘结剂,使其易于涂覆在粉末表面。
常用的溶剂有水、丙酮等。
4. 添加剂:添加剂可以改善材料性能,如增加导电性能或防腐蚀性能。
常用的添加剂有氧化铁、钛酸酯等。
三、成型1. 压制:将铁氧体粉末和粘结剂混合均匀后,采用压制工艺将其压成所需形状的坯料。
压制时需要控制压力和温度,以确保坯料的致密性和稳定性。
2. 烧结:将压制好的坯料置于高温炉中进行烧结。
烧结过程中,粉末颗粒之间会发生化学反应,形成致密的晶体结构。
同时,粘结剂也会被热分解并挥发出去。
烧结温度和时间需要根据具体材料而定。
四、加工1. 切割:将烧结好的铁氧体坯料切割成所需尺寸的小块。
2. 磨削:对切割好的小块进行表面处理和修整,以获得平整光滑的表面。
3. 磁化:通过电流或强磁场对铁氧体磁铁进行磁化处理。
在这个过程中,材料内部会产生一定方向上的自发极化,并形成一个稳定的磁场。
五、检测和质量控制1. 磁性检测:通过磁性测试仪器检测铁氧体磁铁的磁场强度、剩磁、矫顽力等指标。
2. 外观检测:对铁氧体磁铁进行外观检查,检查是否有裂纹、毛刺等缺陷。
3. 包装和贮存:将合格的铁氧体磁铁进行包装,并在干燥、无尘的环境中储存。
同时,要注意避免与其他磁性物品接触,以免影响其性能。
六、结语以上就是铁氧体磁铁制造工艺流程的详细介绍。
在实际生产中,需要根据具体情况进行调整和改进,以确保产品质量和生产效率。
永磁铁氧体的制备工艺
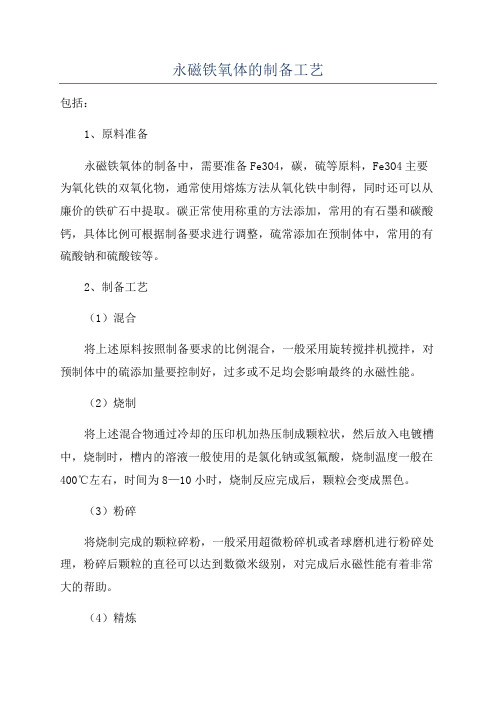
永磁铁氧体的制备工艺
包括:
1、原料准备
永磁铁氧体的制备中,需要准备Fe3O4,碳,硫等原料,Fe3O4主要为氧化铁的双氧化物,通常使用熔炼方法从氧化铁中制得,同时还可以从廉价的铁矿石中提取。
碳正常使用称重的方法添加,常用的有石墨和碳酸钙,具体比例可根据制备要求进行调整,硫常添加在预制体中,常用的有硫酸钠和硫酸铵等。
2、制备工艺
(1)混合
将上述原料按照制备要求的比例混合,一般采用旋转搅拌机搅拌,对预制体中的硫添加量要控制好,过多或不足均会影响最终的永磁性能。
(2)烧制
将上述混合物通过冷却的压印机加热压制成颗粒状,然后放入电镀槽中,烧制时,槽内的溶液一般使用的是氯化钠或氢氟酸,烧制温度一般在400℃左右,时间为8—10小时,烧制反应完成后,颗粒会变成黑色。
(3)粉碎
将烧制完成的颗粒碎粉,一般采用超微粉碎机或者球磨机进行粉碎处理,粉碎后颗粒的直径可以达到数微米级别,对完成后永磁性能有着非常大的帮助。
(4)精炼。
永磁铁氧体的制备工艺

永磁铁氧体的制备工艺一、原料选取1.氧化物原料:通常使用Fe2O3、Fe3O4作为铁源,Co3O4作为钴源。
2.氮化物原料:一般使用氮化铁作为氮源。
3.稀土原料:利用稀土元素的高磁晶各向异性,常使用氧化稀土和相应的稀土钴化合物作为稀土源。
二、配料1.按照化学计量比例将各种原料精细研磨,并通过筛网分选得到均匀的粉末。
2.将各种原料粉末按照一定比例进行混合,通常由铁源、稀土源和钴源组成。
三、烧结1.将混合粉末充分搅拌均匀,并进行压片成坯。
通常采用等静压方法,在模具中施加一定压力,使混合粉末在模具中成型。
2.将坯体进行预烧处理,去除一部分有机物质,并形成初步的金属氧化物。
3.进行烧结处理,将坯体加热至一定温度下,使金属氧化物发生化学反应,形成金属间化合物和磁性颗粒。
4.控制烧结温度和时间,以保证产生足够的磁晶各向异性和颗粒尺寸的增长。
四、后处理1.针对烧结后的材料进行磨削、超声清洗等处理,以去除表面的污染物和不良颗粒。
2.进行磁化处理,通过外加磁场将材料磁化,使其具有永久磁性。
3.进行磁性能测试,进行磁感强度、矫顽力和剩余磁感应强度等性能测试,并根据需要对材料进行优化。
永磁铁氧体的制备工艺繁多,其中最常用的是传统的陶瓷工艺和后来发展起来的粉末冶金工艺。
陶瓷工艺制备的永磁铁氧体具有较高的矫顽力和剩余磁感应强度,但磁晶各向异性较低;而粉末冶金工艺制备的永磁铁氧体具有较高的磁晶各向异性,但矫顽力和剩余磁感应强度较低。
目前,研究人员正在努力寻找新的制备工艺,以获得更优异的永磁铁氧体性能。
综上所述,永磁铁氧体的制备工艺包括原料选取、配料、烧结和后处理等步骤。
这些工艺在生产过程中需要严格控制参数和条件,以获得理想的微观结构和磁性能。
随着技术的不断发展,相信永磁铁氧体的制备工艺还会不断创新和改进,以满足不同领域对其性能的需求。
永磁铁氧体预烧料的加工工艺及方法

永磁铁氧体预烧料的加工工艺及方法永磁铁氧体(Permanent Magnet Ferrite)是一种常用的磁性材料,具有高磁感应强度、优良的耐腐蚀性和热稳定性等特性。
在制备永磁铁氧体磁体之前,需要首先制备永磁铁氧体预烧料,然后通过烧结等工艺将其转化为磁体材料。
原料选择与准备:永磁铁氧体预烧料的主要成分为铁氧体和结合剂。
铁氧体的主要成分有镍、锌、尤其是氧化铝和钡等。
结合剂可以选择有机物或无机物,如聚乙烯醇(PVA)、羟丙基甲基纤维素醚(HPMC)等。
这些原料需要根据成品永磁铁氧体的性能要求选择,并进行准备。
混合:将原料按照一定比例进行混合。
混合可以采用机械搅拌、称重、喷洒等方法。
通过混合可以保证各种成分得到均匀分布,确保后续工艺的顺利进行。
均化:将混合后的原料进行均化处理。
均化是为了消除原料中的团聚现象,使颗粒得到更好的分散状况。
常用的均化方法有机械研磨、超声波均化等。
湿法制粒:将均化后的原料与添加一定量的水或有机溶剂进行混合,形成可塑性较好的湿混合物。
然后通过制粒机等设备对湿混合物进行制粒。
制粒的目的是使混合物得到更好的成型性和流动性。
干燥:将制粒后的永磁铁氧体预烧料进行干燥,以去除水分或溶剂。
干燥的方法可以有自然干燥、烘箱干燥、真空干燥等。
干燥的温度和时间需要根据具体情况确定。
细粉磁性颗粒制备:将干燥后的永磁铁氧体预烧料粉末进行进一步处理,制备细粉磁性颗粒。
常用的制备方法有磁力分选、水力分选等。
此过程的主要目的是提高预烧料颗粒的磁性能和均匀性。
综上所述,永磁铁氧体预烧料的制备工艺包括原料选择与准备、混合、均化、湿法制粒、干燥、细粉磁性颗粒制备等环节。
这些工艺步骤的顺序和参数需要根据具体情况进行调整和优化,以确保永磁铁氧体预烧料的质量和性能。
同时,制备过程中需要严格控制工艺参数,确保原料的均匀分布和颗粒的一致性。
最终,制备出的永磁铁氧体预烧料可以通过烧结等工艺转化为磁体材料,用于生产各种永磁铁氧体磁体产品。
永磁铁氧体材料大生产工艺控制技术
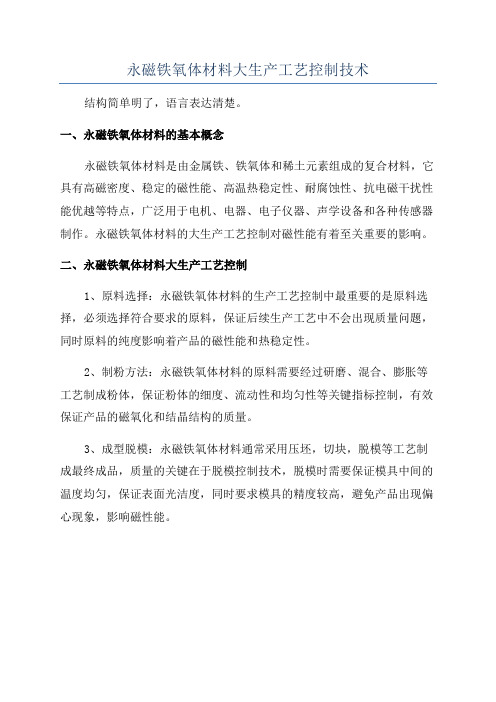
永磁铁氧体材料大生产工艺控制技术结构简单明了,语言表达清楚。
一、永磁铁氧体材料的基本概念
永磁铁氧体材料是由金属铁、铁氧体和稀土元素组成的复合材料,它具有高磁密度、稳定的磁性能、高温热稳定性、耐腐蚀性、抗电磁干扰性能优越等特点,广泛用于电机、电器、电子仪器、声学设备和各种传感器制作。
永磁铁氧体材料的大生产工艺控制对磁性能有着至关重要的影响。
二、永磁铁氧体材料大生产工艺控制
1、原料选择:永磁铁氧体材料的生产工艺控制中最重要的是原料选择,必须选择符合要求的原料,保证后续生产工艺中不会出现质量问题,同时原料的纯度影响着产品的磁性能和热稳定性。
2、制粉方法:永磁铁氧体材料的原料需要经过研磨、混合、膨胀等工艺制成粉体,保证粉体的细度、流动性和均匀性等关键指标控制,有效保证产品的磁氧化和结晶结构的质量。
3、成型脱模:永磁铁氧体材料通常采用压坯,切块,脱模等工艺制成最终成品,质量的关键在于脱模控制技术,脱模时需要保证模具中间的温度均匀,保证表面光洁度,同时要求模具的精度较高,避免产品出现偏心现象,影响磁性能。
永磁铁氧体预烧料的生产工艺是怎样的
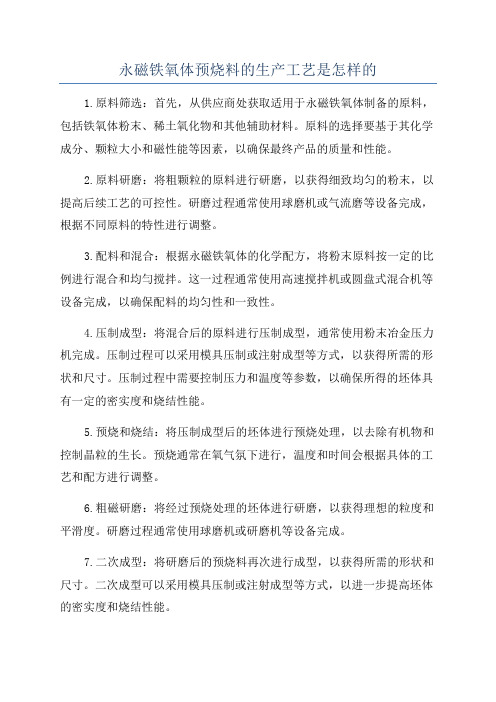
永磁铁氧体预烧料的生产工艺是怎样的1.原料筛选:首先,从供应商处获取适用于永磁铁氧体制备的原料,包括铁氧体粉末、稀土氧化物和其他辅助材料。
原料的选择要基于其化学成分、颗粒大小和磁性能等因素,以确保最终产品的质量和性能。
2.原料研磨:将粗颗粒的原料进行研磨,以获得细致均匀的粉末,以提高后续工艺的可控性。
研磨过程通常使用球磨机或气流磨等设备完成,根据不同原料的特性进行调整。
3.配料和混合:根据永磁铁氧体的化学配方,将粉末原料按一定的比例进行混合和均勻搅拌。
这一过程通常使用高速搅拌机或圆盘式混合机等设备完成,以确保配料的均匀性和一致性。
4.压制成型:将混合后的原料进行压制成型,通常使用粉末冶金压力机完成。
压制过程可以采用模具压制或注射成型等方式,以获得所需的形状和尺寸。
压制过程中需要控制压力和温度等参数,以确保所得的坯体具有一定的密实度和烧结性能。
5.预烧和烧结:将压制成型后的坯体进行预烧处理,以去除有机物和控制晶粒的生长。
预烧通常在氧气氛下进行,温度和时间会根据具体的工艺和配方进行调整。
6.粗磁研磨:将经过预烧处理的坯体进行研磨,以获得理想的粒度和平滑度。
研磨过程通常使用球磨机或研磨机等设备完成。
7.二次成型:将研磨后的预烧料再次进行成型,以获得所需的形状和尺寸。
二次成型可以采用模具压制或注射成型等方式,以进一步提高坯体的密实度和烧结性能。
8.最后烧结:将经过二次成型的坯体进行最后的烧结处理,以实现晶粒的长大和晶界的固相扩散,得到具有优良磁性能和物理性能的成品。
烧结过程通常在氧气氛下进行,温度和时间也会根据具体需求进行调整。
9.检测和包装:对最后烧结的永磁铁氧体进行物性和磁性能的检测,以确保产品符合要求。
合格的产品将经过清洗、包装和标识等工艺,最终通过质检合格后进入市场。
总结:永磁铁氧体预烧料的生产工艺包括原料筛选、原料研磨、配料和混合、压制成型、预烧和烧结、粗磁研磨、二次成型、最后烧结、检测和包装等多个步骤。
铁氧体磁瓦生产工艺
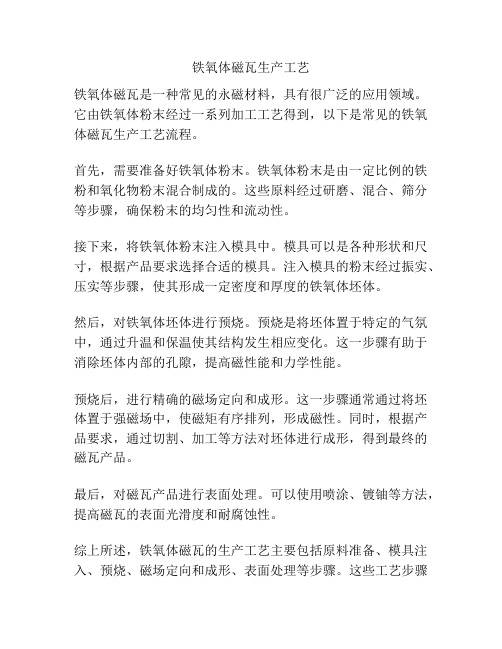
铁氧体磁瓦生产工艺
铁氧体磁瓦是一种常见的永磁材料,具有很广泛的应用领域。
它由铁氧体粉末经过一系列加工工艺得到,以下是常见的铁氧体磁瓦生产工艺流程。
首先,需要准备好铁氧体粉末。
铁氧体粉末是由一定比例的铁粉和氧化物粉末混合制成的。
这些原料经过研磨、混合、筛分等步骤,确保粉末的均匀性和流动性。
接下来,将铁氧体粉末注入模具中。
模具可以是各种形状和尺寸,根据产品要求选择合适的模具。
注入模具的粉末经过振实、压实等步骤,使其形成一定密度和厚度的铁氧体坯体。
然后,对铁氧体坯体进行预烧。
预烧是将坯体置于特定的气氛中,通过升温和保温使其结构发生相应变化。
这一步骤有助于消除坯体内部的孔隙,提高磁性能和力学性能。
预烧后,进行精确的磁场定向和成形。
这一步骤通常通过将坯体置于强磁场中,使磁矩有序排列,形成磁性。
同时,根据产品要求,通过切割、加工等方法对坯体进行成形,得到最终的磁瓦产品。
最后,对磁瓦产品进行表面处理。
可以使用喷涂、镀铀等方法,提高磁瓦的表面光滑度和耐腐蚀性。
综上所述,铁氧体磁瓦的生产工艺主要包括原料准备、模具注入、预烧、磁场定向和成形、表面处理等步骤。
这些工艺步骤
相互衔接,通过精确控制各工艺参数和参数,确保最终产品的质量和性能。
- 1、下载文档前请自行甄别文档内容的完整性,平台不提供额外的编辑、内容补充、找答案等附加服务。
- 2、"仅部分预览"的文档,不可在线预览部分如存在完整性等问题,可反馈申请退款(可完整预览的文档不适用该条件!)。
- 3、如文档侵犯您的权益,请联系客服反馈,我们会尽快为您处理(人工客服工作时间:9:00-18:30)。
永磁铁氧体预烧料的加工工艺及方法永磁铁氧体预烧料的加工过程实际上是碳酸钡(BaCO3)或碳酸锶(SrCO3)与铁红(Fe2O3)经过高温下的固相反应充分生成六角形的铁氧体晶粒的过程。
固相反应是否完善、充分,晶粒形状是否完整,对材料的质量有很大影响。
同时预烧料的优劣在铁氧体磁铁的生产中至关重要,质量差的预烧料是无法生产出高性能铁氧体磁铁。
目前我们公司生产的铁氧体预烧料有:异方性锶料、等方性普通粒料、自动车料三种。
决定永磁铁氧体预烧料性能优劣主要有以下几个方面:○1材料○2配方○3工艺手段及控制方法一、材料在永磁铁氧体预烧料生产中首先要选择合适的原材料,选择时主要考虑:原料纯度、含杂质情况、原料化学活动性、颗粒度等几个方面。
1、铁红(Fe2O3):永磁铁氧体预烧料的主料,应选择纯度>97%以上,最好在98%以上。
目前我公司使用印度铁红有98.5%、98%、97.5%、96%四种,用量最大为97.5%铁红。
台湾铁红纯度98.5%、比利时铁红纯度99%。
2、碳酸钡(BaCO3)或碳酸锶(SrCO3):永磁铁氧体预烧料的主料,纯度应大于96%。
最好大于98%以上。
目前我公司使用为纯度97%。
3、添加剂:在预烧时增加添加剂主要目的是为了改善材料的结构灵敏度,弥补某一特性。
永磁铁氧体常用的添加剂有:SiO2、CaCO3、SrSO4等,具体作用在配方中再做介绍。
4、含杂质情况:杂质含量中二氧化硅(SiO2)含量应该在0.5%以下,最好在0.1%以下。
氯离子含量最好在0.15%以下(此杂质对铁氧体性能影响很大,直接影响产品收缩率、反应气氛,应在烧结低温部分将其挥发排除)。
5、化学活动性:就铁红、铁磷、铁矿砂三种生产永磁铁氧体原料而言,铁红的化学活动性优于其他两种。
我公司目前全部使用铁红生产,另外纯度大的铁红化学活动性优于纯度小的铁红。
4、颗粒度:原料的粒度最好在1um以下,颗粒度太大往往影响固相反应的充分发生。
5、原料密度:原料的压密程度(密度)同样对预烧料的烧结有较大影响,密度大的铁红在混料过程中更加容易混料均匀、铁红与碳酸锶能充分接触;预烧过程中会增加铁氧体的生成比例。
二、原料配方1、异方性锶料的主配方:碳酸锶(SrCO3)与铁红(Fe2O3),一般按摩尔比1:5.3-5.9之间。
我公司目前使用摩尔比1:6,换算成原料为:154公斤碳酸锶、1000公斤铁红。
2、等方性钡料的主配方:碳酸钡(BaCO3)与铁红(Fe2O3),一般按摩尔比1:5.0-5.3之间,我公司使用摩尔比1:5.0,换算成原料为248公斤碳酸钡、1000公斤铁红。
一次加杂为SiO2,比例为0.8%。
3、加杂及作用:(1)加杂的作用:有促进固相反应、助熔、防止晶粒膨胀、降低需要烧结温度、改善材料性能、增加机械强度、增加韧性等作用。
(2)加杂分一次加杂和二次加杂。
一次加杂为在预烧料烧结前加入,二次加杂是在已烧结加工完成的预烧料二次加工时加入,如异方性锶料球磨工序、自动车料砂磨工序都需要进行二次加杂。
○1二氧化硅(SiO2):等方性钡料中加入SiO2有降低原料需要的烧结温度,使其在较低温度下进行固相反应作用。
异方性锶料中加入少量SiO2有在成型烧结时抑制晶粒膨胀、提高矫顽力的作用。
一般在加入0.3%-0.8%的SiO2时,矫顽力有所增加,而Br(剩磁)有所下降。
○2碳酸钙(CaCO3):碳酸钙在800℃左右开始分解,在产品烧结过程中,较低温度下碳酸钙即成熔融状态,有利于固相反应的进行,降低产品烧结所需要的温度,增加产品致密程度。
当在永磁铁氧体材料中加入0.2%-1.0%的碳酸钙时,Br有一定增加,而矫顽力无明显下降。
○3硫酸锶(SrSO4):分解温度在1400℃以上,在锶铁氧体一次配料时加入少量硫酸锶,其中一部分固溶在铁氧体中,形成自由能,对铁氧体的各向异性取向度有明显提高,不溶于铁氧体中的部分,成为细的分散剂,可抑制晶粒长大,提高矫顽力。
实验发现,加入0.5-1.0%的硫酸锶,锶铁氧体材料的剩磁和矫顽力均有一定提高。
加杂过程对产品的性能影响是多方面的,我们加杂时提高一项性能参数往往会影响其他参数,因此加杂需要注意以下事项:○1要根据不同的性能参数及工艺加工要求选择不同的杂质。
○2加杂应点到为止,过多往往会起到反作用。
○3加杂是应注意杂质纯度及其含量。
三、加工工艺及控制方法在铁氧体生产过程中,配方决定材料性能,但配方的实现取决于生产工艺及控制方法。
配方不同生产工艺也不尽相同,一种配方的最佳体现,必须有一种合适的生产工艺相适应。
我公司经多年实践、大量经验积累,已形成一套行之有效且低成本的原料加工工艺。
目前主要有异方性锶料、等方性普通粒料、自动车料三种加工工艺,下面将从异方性锶料、自动车料来探讨其加工工艺。
1、异方性锶料加工工艺:○1混料工序:混料分为湿混、干混两种加工工艺。
湿混为使用球磨机将一定比例的原料、水进行混和,其优点为混料均匀,有利于铁红与配料的充分接触,预烧时固相反应充分。
缺点是成本较高、工期较长。
干混为将干的配料使用锥形混料器利用搅拌臂搅拌混和,其优点是成本较低、工期短;缺点是混料不均匀,有死角,预烧时铁氧体生成比例略低。
混料工序需注意事项:混料时间要至少40分钟,时间太短混料不均匀、湿混不能加入地下水,需使用自来水,减少杂质。
目前公司异方性锶料、自动车料使用湿混工艺混料,等方性普通粒料使用干混工艺混料。
○2料球成型:此工序使用煤球成型机将已混和的原料成型为直径110毫米左右、高度70-80毫米且中间有通孔的料球,以便于烧结时氧气流通。
料球成型需注意事项:成型密度尽量大、水分含量在10%以下、料球孔必须贯通。
○3料球预烧:使用四孔推板窑炉对成型料球进行预烧,使其充分固相反应生成永磁铁氧体。
烧结温度一般在1290-1320℃(测温表显示温度),推板速度30-40分钟/板。
烧结过程在整个预烧料制备工艺中至关重要,要从以下方面重点控制:(1)温度:温度必须严格控制,在规定温度上下浮动不能超过5℃,预烧温度太低将影响铁氧体晶粒生成比例;温度太高,造成晶格膨胀,一般温度超过1380度以上,部分铁氧体将会分解,生成铁氧体晶体将有重量减轻现象,影响预烧料性能。
(2)氧化气氛:在烧结过程中,800℃时SrCO3开始分解,900℃以上开始逐步生成铁氧体晶体,反应过程要经过2SrO.Fe2O3 →SrO.Fe2O3 →SrO.6Fe2O3几个过程,反应时需要有充分的氧气环境。
一般要求含氧量>5%,氧气含量低将会影响铁氧体生成比例或产生还原现象,即:Fe2O3还原成Fe3O4,影响预烧料性能。
(3)推进速度:产品推进速度必须经过相关实验来确定最合适的速度,一般来讲有两种推进方式:低温慢推、高温快退。
两种方式各有优劣,低温慢推,产品废气、挥发的要好一些,有利于产品质量稳定和提高,但缺点是产量低一些;高温快推,产品废气有时会挥发不完全,对产品质量有一定影响,好处是产量会高一些。
(4)保温时间:保温时间是指预烧料球在高温区的烧结时间,保温的目的是要尽可能提高铁氧体晶体的生成比例,使其充分反应,一般能生成95%以上的铁氧体已经是较佳的状态。
其烧结时间根据颗粒粒子直径大小而定,颗粒小的原料要求保温时间短,颗粒大的原料要求保温时间长,一般在30-180分钟,目前我公司使用铁红粒度一般在0.5-1.0um,保温时间在90分钟左右。
○4、QC检查工序:从烧结炉口取出已烧结完成的预烧料球,经过破碎、打散、球磨后形成粒度在0.8-0.9um的粉料。
然后经过实验成型机压制成圆饼,在实验烧结炉中经1250℃左右烧结后,使用磁性能测试仪检测预烧料的性能参数。
一般要求:B r(剩磁)≥3650Gs, Hcb(矫顽力)≥2600 Oe, Hcj(內禀矫顽力)≥2800 OeBH(max)(最大磁能积)≥3.0MG Oe○5、振磨工序:将已经烧结并抽查的预烧料球,经鄂式破碎机破碎后经输送带送入振磨机,经西德振磨机粗磨、日本振磨机细磨加工成粒度在3.5-5.0um的异方性锶料粗粉。
经QC检查后即可合格入库。
2、等方性钡料(自动车料)加工工艺○1、混料、料球成型、料球预烧、振磨几个工序与异方性锶料加工工艺基本一致,区别在预烧工序温度控制在1070-1090℃,推进速度在25分钟左右。
等方性钡料烧结注意事项:如在等方性钡料烧结过程中烧结温度高一些,对产品Br(剩磁)、松装比都有好处,造粒工序也容易加工,但振磨工序加工难度加大,粒度往往经过多次振磨都无法达到要求;如烧结温度低一些,振磨工序加工难度小,但造粒产生细粉多,松装比很难达到要求。
因此等方性钡料烧结温度设定要与振磨工序、性能要求配合设定。
○2、砂磨工序:将已振磨完成的等方性料粉和配方一同投入砂磨机加入自来水,使用砂磨机砂磨3-4小时,将原料由1.2um粒度砂磨至0.8-0.9um粒度的过程。
此工序要注意砂磨后粒度必须在0.8-0.9um.○3、烘干、打散工序:使用烘干炉将已砂磨的细粉烘干至水分0.8%以下。
并进入打散机打散至蓬松状态。
此工序要注意杂质、异物的混入。
○4、造粒工序:将已打散的细粉加入捏合机进行搅拌,同时均匀洒入PVA胶水,经捏合机均匀搅拌,使每个PVA胶粒周围沾满等方性磁粉。
后经提升机进入烘干炉,在300℃左右温度下使粘结在一起的料块分散开,形成中间为PVA胶粒、四周为等方性磁粉的单个颗粒的过程,称之为造粒。