反应注射成型技术
高分子材料加工技术——注射成型.ppt
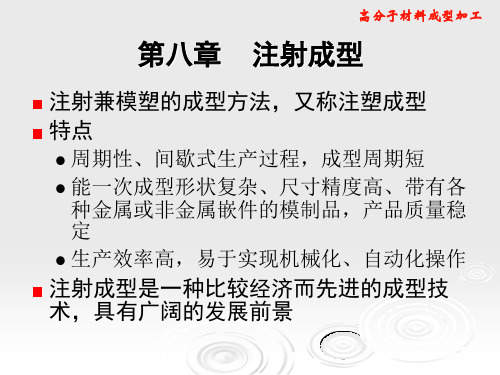
高分子材料成型加工
高分子材料成型加工
第三节 注射成型工艺及工艺条件
一. 注射成型工艺流程P294
1、成型前的准备
原料预处理 料筒清洗 嵌件预热 脱模剂选用
2、注射成型过程
合模与锁紧 注射装置前移 塑化 注射充模 保压 制品冷却 注射装置后退和开模顶出制品
高分子材料成型加工
注射成型用于热塑性塑料的成型加工最普 遍,本章主要讨论热塑性塑料注射成型原 理及工艺
高分子材料成型加工
第一节 注射机的结构与作用
一. 注射机分类: 1. 按结构特点分类 (1) 柱塞式注射机
(2) 双阶柱塞式注射机
高分子材料成型加工
高分子材料成型加工
(3) 螺杆预塑化柱塞式注射机
压力,会有流涎现象。 背压高,螺杆扭矩高,对塑化电机的负荷大。
高分子材料成型加工
注射压力:指在注射过程中注射机螺杆对塑料熔 体所施加的压力。
作用: ①克服塑料熔体由料筒流向型腔的流动阻力。 ②压实熔体,使注射制品密实(提供保压压力)。 注射压力的选择
• 熔体粘度大、玻璃化温度高的物料,采用较 高注射压力;
2、热固性塑料熔体在充模过程中的流动
热固性塑料熔体注满模腔
3、热固性塑料在模腔内的固化
高分子材料成型加工
二、注射原料要求
热固性塑料注射成型工艺性能的基本要求 是:在低温料筒内塑化产物能较长时间保 持良好流动性,而在高温的模腔内能快速 反应固化。
酚醛塑料最适合 不饱和聚酯塑料和三聚氰胺塑料 环氧树脂注射成型时技术难度较大
注射压力。
高分子材料成型加工
[工学]反应注射成型技术在聚氨酯材料合成中的研究与应用
![[工学]反应注射成型技术在聚氨酯材料合成中的研究与应用](https://img.taocdn.com/s3/m/cff1c521f90f76c661371af3.png)
反应注射成型技术在聚氨酯材料合成中的研究与应用摘要:主要介绍反应型注射技术,以及在聚氨酯合成中的研究与应用,并对几种不同的类型的RIM-PU注射成型技术进行介绍关键词:反应型注射聚氨酯自增强1. 前言:反应注射成型,简称RIM( Reaction Injection Molding),是将两种或两种以上具有反应性的液体组分在一定温度下注入模具型腔内,在其中直接生成聚合物的成型技术。
即将聚合与成型加工一体化,或者说,直接从单体得到制品的“ 一步法注射技术”。
和传统的热塑性注射成型 (TIM)不同,RIM是单体在模具中聚合而形成固体聚合物,而TIM是聚合物在模具中冷却才成型。
其它反应成型加工方法,如单体浇铸成型、热固性塑料的注射成型,虽然也是在形成部件的形状后完成聚合反应。
而在RIM中,单体和模具的温度没有很大的不同,而是靠基体激烈撞击混合来活化反应。
和各种聚合物加工方法相比RIM制品最节能,RIM 是目前聚合物加工领域中引人注目的新方向。
RIM技术可用于聚氨酯、硅橡胶、环氧树脂和尼龙的成型加工。
RIM聚氨酯发展尤为迅速,现已用于制造汽车内饰件、机器外壳和家具等。
汽车行业为了获得高模量的聚氨酯制品,又发展了增强反应注射成型(RRIM)。
聚氨酯(PU) 反应注射成型(RIM) 近年来发展十分迅速,其主要原料有 A料和B料。
A料通常为低分子量聚酯或聚醚,有时也加入其他添加剂。
B料为各种异氰酸酯,目前国内外常用二苯甲烷二异氰酸酯(MDI )或液化改性MDI (L—MDI)。
反应注射成型聚氨醋( RIM—PU) 是70年代初聚合物加工领域中研制开发的一门新型交叉成型技术,它是由低粘度高活性的异氰酸酯和多元醇经高压碰撞混合,通过化学、物理等变化而成型的。
它具有成型温度和压力低、能耗少、材料性能优良等优点,近年来发展和应用极为迅速。
2. RIM在聚氨酯方面的发展聚氨酯RIM聚氨酯制品(RIM—PUR) 是世界上开发最早且首先达到实用化的品种:通过配方的调整.利用RIM可生产出不同密度的软、硬制品,由低密度的发泡材料到高密度的结构泡沫材料,低或高模量的弹性体等。
反应注射成型技术

反应注射成型技术反应注射成型起源于聚氨酯塑料。
随着工艺技术的进步,该工艺也扩展到了多种材料的加工中。
与此同时,为了拓宽 RIM 技术的应用领域,特别是在汽车行业中的应用,该工艺还引入了纤维增强技术。
RIM 简介反应注射成型(简称“ RIM”是指将具有高化学活性、相对分子质量低的双组分材料经撞击混合后,在常温低压下注入密闭的模具内,完成聚合、交联和固化等化学反应并形成制品的工艺过程。
这种将聚合反应与注射成型相结合的新工艺,具有物料混合效率高、流动性好、原料配制灵活、生产周期短及成本低的特点,适用于大型厚壁制品生产,故而受到了世界各国的重视。
RIM 最早仅用于聚氨酯材料,随着工艺技术的进步, RIM 也可应用于多种材料(如环氧、尼龙、聚脲及聚环戊二烯等)的加工。
用于橡胶与金属成型的RIM 工艺是当前研究的热点。
为了拓宽 RIM 的应用领域,提高 RIM 制品的刚性与强度,使之成为结构制品, RIM 技术得到了进一步的发展,出现了专门用于增强型制品成型的增强反应注射成型( RRIM)和专门用于结构制件成型的结构反应注射成型(SRIM)技术等。
RRIM和SRIM成型工艺原理与 RIM相同,不同之处主要在于纤维增强复合材料制品的制备。
目前,典型的RIM 制品有汽车保险杠、挡泥板、车体板、卡车货箱、卡车中门和后门组件等大型制品。
它们的产品质量比SMC产品好,生产速度更快,所需二次加工量更小。
RIM 成型工艺1.工艺过程RIM 工艺过程为:单体或预聚物以液体状态经计量泵以一定的配比进入混合头进行混合。
混合物注入模具后,在模具内快速反应并交联固化,脱模后即为RIM 制品。
这一过程可简化为:贮存T计量T混合T充模T固化T顶出T后处理。
2.工艺控制(1)贮存。
RIM 工艺所用的两组分原液通常在一定温度下分别贮存在 2 个贮存器中,贮存器一般为压力容器。
在不成型时,原液通常在 0.2~0.3 MPa 的低压下,在贮存器、换热器和混合头中不停地循环。
反应注射成型工艺
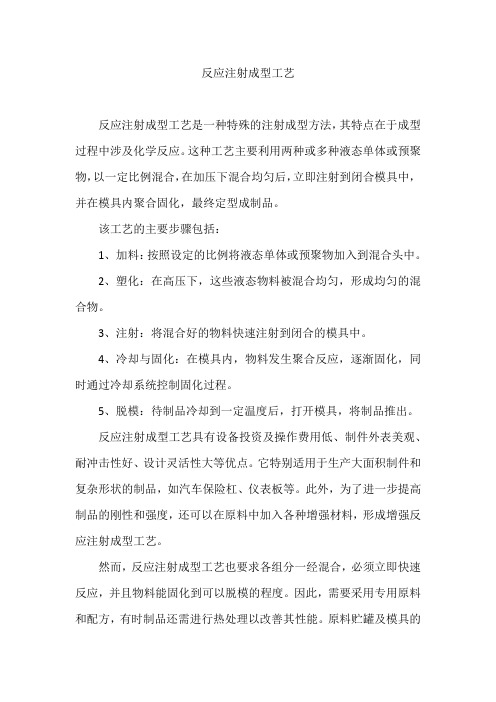
反应注射成型工艺
反应注射成型工艺是一种特殊的注射成型方法,其特点在于成型过程中涉及化学反应。
这种工艺主要利用两种或多种液态单体或预聚物,以一定比例混合,在加压下混合均匀后,立即注射到闭合模具中,并在模具内聚合固化,最终定型成制品。
该工艺的主要步骤包括:
1、加料:按照设定的比例将液态单体或预聚物加入到混合头中。
2、塑化:在高压下,这些液态物料被混合均匀,形成均匀的混合物。
3、注射:将混合好的物料快速注射到闭合的模具中。
4、冷却与固化:在模具内,物料发生聚合反应,逐渐固化,同时通过冷却系统控制固化过程。
5、脱模:待制品冷却到一定温度后,打开模具,将制品推出。
反应注射成型工艺具有设备投资及操作费用低、制件外表美观、耐冲击性好、设计灵活性大等优点。
它特别适用于生产大面积制件和复杂形状的制品,如汽车保险杠、仪表板等。
此外,为了进一步提高制品的刚性和强度,还可以在原料中加入各种增强材料,形成增强反应注射成型工艺。
然而,反应注射成型工艺也要求各组分一经混合,必须立即快速反应,并且物料能固化到可以脱模的程度。
因此,需要采用专用原料和配方,有时制品还需进行热处理以改善其性能。
原料贮罐及模具的
温度控制也是非常重要的。
总的来说,反应注射成型工艺是一种高效、灵活的塑料加工方法,广泛应用于汽车、电子、家电等领域。
随着技术的进步和工艺的完善,该工艺将在更多领域得到应用。
反应注射成型技术概述 4.

(1)RIM微孔弹性 体:主要用于制作保 险杠、挡泥板、侧防 护条、扰流板、格栅、 内饰件、仪表板、方 向盘、大灯壳、后灯 和汽车窗包边等零件。
(2)RRIM微孔弹性体:用于保险杠、缓冲件、车内转角 立柱、车门扶手、散热器格栅、前阻流板、挡泥板、发动 机罩、行李箱底板及盖、车门外板及卡车承载地板等零件
(3)自结皮泡沫塑料:该材料具有柔软的泡沫芯层和坚固 的表面皮层,并可进行涂装加工处理。用于方向盘、变速 杆手柄、线束护套、按钮开关、空气滤清器垫圈、扶手、 头枕、衬及止推块、门窗立柱、仪表板及喇叭盖等零件。
(4)半硬质泡沫塑料:它与各种表皮和骨架材料粘结性很 强,具有较高承压负荷及突出的防震抗冲击性能,且能消 除振动噪音,非常适合制造汽车仪表板、扶手芯、头枕、 遮阳板、变速箱顶盖、杂物箱盖、喇叭盖、车顶内衬、门 内饰板、膝部防撞板、衣帽架、车体梁柱装饰板、保险杠 内芯、止推垫和柱状物等零件。
(5)硬质泡沫塑料:用于制作车门内衬、内装板、座椅靠 背盖壳/垫、顶棚内衬及加工内饰件等零件。
RIM除在汽车领域广泛应用之外,还在办公设备、医疗 设备、工业用品、日用品、体育娱乐器材、建筑装饰等行 业应用广泛。
反应注射成型(RIM)聚氨酯特性与应用

在RIM-PU的生产中,供选择的聚醚 多元醇大致有三类:
1、以氧化乙烯封端的聚氧化丙烯-聚氧化 丙烯基聚醚多元醇
它们主要是采用传统方式合成的端羟基聚醚, 然后再用环氧乙烷反应进行封端,使端部的仲羟基 转化为伯羟基,以达到它与异氰酸酯反应速度提高 3~4倍的目的。
反应注射成型(RIM)聚氨酯的特性和 应用
RIM机具有以下优点:
⑴混合室小,无任何机械搅拌混合装置,液体物料依 靠高压输送和小口径喷嘴产生高能量冲击,达到充 分混合的目的。
⑵具有自清洁功能,没有低压机那种溶剂清洗,压缩
空气冲刷,劣化工作环境的缺点。
⑶采用高精度、高压力计量装置。并具备高压注射混
合、低压循环物料的自动切换功能,能量消耗较为
反应注射成型(RIM)聚氨酯的特性和 应用
(7)可以使用模内涂装(IMC-Inmold Coating)技术,减少制 品后涂装工序。降低加工成本。 目前聚氨酯RIM一般指两类材料,一类为密度 较高从800到1200千克每立方米以上的外皮密实、内 芯气泡较少或基本无泡孔的聚氨酯材料;另一类是 密度在200千克每立方米以上的软质或硬质自结皮聚 氨酯泡沫塑料。
反应注射成型(RIM)聚氨酯的特性和 应用
表现出的反应特点如下所述:
(1)剧烈的放热效应。
(2)合成反应的速度与原料品种体系有直接关系。即在 异氰酸酯品种决定的前提下,不同的含活泼氢化合 物将有不同的反应速度,其反应速度顺序大体为: 胺>醇>水>脲>氨基甲酸酯。
(3)除了第4代RIM聚氨酯以外,其它RIM-聚氨酯 加工中。催化剂是必不可少的。主要使用以三亚乙 基二胺为代表的叔胺类催化剂和以二月桂酸二丁基 锡为代表的有机锡类催化剂。
塑料先进成型技术第7章 反应注射成型技术
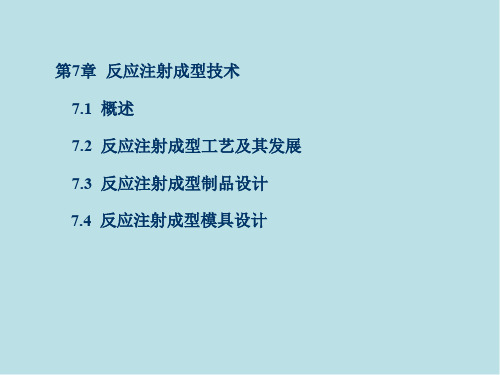
早期应用:聚氨酯弹性体和聚氨酯泡沫塑料,用于大型 厚壁制品生产。
一、反应注射成型的原理及特点
增强反应注射成型(RRIM): 1979年出现,用玻璃纤 维增强的聚氨酯RIM生产工艺,可拓宽应用领域,提高制 品刚性与强度;用于汽车挡泥板和车体板的生产。
7)具有设备投资及生产成本低、制件外表美观,耐冲击 性好,设计灵活性大等优点,特别适用于汽车覆盖件等大 型塑件的成型加工。
二、反应注射成型工艺流程
工艺过程:包含原料准备—贮存—计量—混合—充模— 固化—顶出—后处理等工序。
(1)原料准备:配制成A(异氰酸酯)、B(多元醇)两 种组分,B组分常含扩链剂、催化剂及其它助剂。
一、反应注射成型的原理及特点
应用拓展:不再局限于聚氨酯体系,已广泛应用于不饱 和聚酯、环氧树脂等快速固化类树脂和触媒,以及尼龙、 聚脲及聚环戊二烯、有机硅树脂和互穿聚合物网络等多种 材料;将RIM工艺用于橡胶与金属成型已成为高分子材料 加工领域的研究热点。
我国上世纪80年代初已引进RIM设备和原料,生产汽车 方向盘、聚氨酯泡沫塑料,但目前仍主要用于聚氨酯材料, 对其它种类材料的研究特别是工业应用还不广泛,RIM技 术普及更是任重道远。
一、反应注射成型的原理及特点
RIM与其它塑料成型技术比较,具有以下特点: 1)RIM是能耗最低的工艺之一。因液态原料所需注射压
力和锁模力仅为普通注射成型的1/100~1/40,耗能少。 2)RIM模腔压力小,约为0.3~1.0MPa,设备和模具所需
的投资少。
3)RIM所用体系多种多样,如聚氨酯、聚脲、尼龙、双 环戊二烯等。
反应注射成型PDCPD的合成与应用
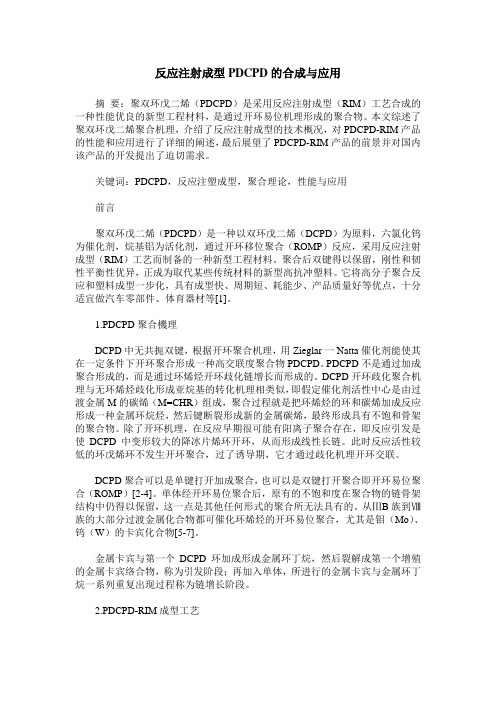
反应注射成型PDCPD的合成与应用摘要:聚双环戊二烯(PDCPD)是采用反应注射成型(RIM)工艺合成的一种性能优良的新型工程材料,是通过开环易位机理形成的聚合物。
本文综述了聚双环戊二烯聚合机理,介绍了反应注射成型的技术概况,对PDCPD-RIM产品的性能和应用进行了详细的阐述,最后展望了PDCPD-RIM产品的前景并对国内该产品的开发提出了迫切需求。
关键词:PDCPD,反应注塑成型,聚合理论,性能与应用前言聚双环戊二烯(PDCPD)是一种以双环戊二烯(DCPD)为原料,六氯化钨为催化剂,烷基铝为活化剂,通过开环移位聚合(ROMP)反应,采用反应注射成型(RIM)工艺而制备的一种新型工程材料。
聚合后双键得以保留,刚性和韧性平衡性优异,正成为取代某些传统材料的新型高抗冲塑料。
它将高分子聚合反应和塑料成型一步化,具有成型快、周期短、耗能少、产品质量好等优点,十分适宜做汽车零部件、体育器材等[1]。
1.PDCPD聚合機理DCPD中无共扼双键,根据开环聚合机理,用Zieglar一Natta催化剂能使其在一定条件下开环聚合形成一种高交联度聚合物PDCPD。
PDCPD不是通过加成聚合形成的,而是通过环烯烃开环歧化链增长而形成的。
DCPD开环歧化聚合机理与无环烯烃歧化形成亚烷基的转化机理相类似,即假定催化剂活性中心是由过渡金属M的碳烯(M=CHR)组成,聚合过程就是把环烯烃的环和碳烯加成反应形成一种金属环烷烃,然后键断裂形成新的金属碳烯,最终形成具有不饱和骨架的聚合物。
除了开环机理,在反应早期很可能有阳离子聚合存在,即反应引发是使DCPD中变形较大的降冰片烯环开环,从而形成线性长链。
此时反应活性较低的环戊烯环不发生开环聚合,过了诱导期,它才通过歧化机理开环交联。
DCPD聚合可以是单键打开加成聚合,也可以是双键打开聚合即开环易位聚合(ROMP)[2-4]。
单体经开环易位聚合后,原有的不饱和度在聚合物的链骨架结构中仍得以保留,这一点是其他任何形式的聚合所无法具有的。
- 1、下载文档前请自行甄别文档内容的完整性,平台不提供额外的编辑、内容补充、找答案等附加服务。
- 2、"仅部分预览"的文档,不可在线预览部分如存在完整性等问题,可反馈申请退款(可完整预览的文档不适用该条件!)。
- 3、如文档侵犯您的权益,请联系客服反馈,我们会尽快为您处理(人工客服工作时间:9:00-18:30)。
反应注射成型技术反应注射成型起源于聚氨酯塑料。
随着工艺技术的进步,该工艺也扩展到了多种材料的加工中。
与此同时,为了拓宽RIM技术的应用领域,特别是在汽车行业中的应用,该工艺还引入了纤维增强技术。
RIM简介反应注射成型(简称“RIM”)是指将具有高化学活性、相对分子质量低的双组分材料经撞击混合后,在常温低压下注入密闭的模具内,完成聚合、交联和固化等化学反应并形成制品的工艺过程。
这种将聚合反应与注射成型相结合的新工艺,具有物料混合效率高、流动性好、原料配制灵活、生产周期短及成本低的特点,适用于大型厚壁制品生产,故而受到了世界各国的重视。
RIM最早仅用于聚氨酯材料,随着工艺技术的进步,RIM也可应用于多种材料(如环氧、尼龙、聚脲及聚环戊二烯等)的加工。
用于橡胶与金属成型的RIM工艺是当前研究的热点。
为了拓宽RIM的应用领域,提高RIM制品的刚性与强度,使之成为结构制品,RIM技术得到了进一步的发展,出现了专门用于增强型制品成型的增强反应注射成型(RRIM)和专门用于结构制件成型的结构反应注射成型(SRIM)技术等。
RRIM和SRIM成型工艺原理与RIM 相同,不同之处主要在于纤维增强复合材料制品的制备。
目前,典型的RIM制品有汽车保险杠、挡泥板、车体板、卡车货箱、卡车中门和后门组件等大型制品。
它们的产品质量比SMC产品好,生产速度更快,所需二次加工量更小。
RIM成型工艺1.工艺过程RIM工艺过程为:单体或预聚物以液体状态经计量泵以一定的配比进入混合头进行混合。
混合物注入模具后,在模具内快速反应并交联固化,脱模后即为RIM制品。
这一过程可简化为:贮存→计量→混合→充模→固化→顶出→后处理。
2.工艺控制(1)贮存。
RIM工艺所用的两组分原液通常在一定温度下分别贮存在2个贮存器中,贮存器一般为压力容器。
在不成型时,原液通常在0.2~0.3 MPa的低压下,在贮存器、换热器和混合头中不停地循环。
对聚氨酯而言,原液温度一般为20~40℃,温度控制精度为±1℃。
(2)计量。
两组分原液的计量一般由液压系统来完成,液压系统由泵、阀及辅件(控制液体物料的管路系统与控制分配缸工作的油路系统)所组成。
注射时还需经过高低压转换装置将压力转换为注射所需的压力。
原液用液压定量泵进行计量输出,要求计量精度至少为±1.5%,最好控制在±1%。
(3)混合。
在RIM制品成型中,产品质量的好坏很大程度上取决于混合头的混合质量,生产能力则完全取决于混合头的混合质量。
一般采用的压力为10.34~20.68MPa,在此压力范围内能获得较佳的混合效果。
(4)充模。
反应注射物料充模的特点是料流的速度很高。
为此,要求原液的粘度不能过高,例如,聚氨酯混合料充模时的粘度为0.1Pa.s左右。
当物料体系及模具确定之后。
重要的工艺参数只有2个,即充模时间和原料温度。
聚氨酯物料的初始温度不得超过90℃,型腔内的平均流速一般不应超过0.5m/s。
(5)固化。
聚氨酯双组分混合料在注入模腔后具有很高的反应性,可在很短的时间内完成固化定型。
但由于塑料的导热性差,大量的反应热不能及时散发,故而使成型物内部温度远高于表层温度,致使成型物的固化从内向外进行。
为防止型腔内的温度过高(不能高于树脂的热分解温度),应该充分发挥模具的换热功能来散发热量。
反应注射模内的固化时间,主要由成型物料的配方和制品尺寸决定。
另外,反应注射制品从模内脱出后还需要进行热处理。
热处理有两个作用:一是补充固化,二是涂漆后的烘烤,以便在制品表面形成牢固的保护膜或装饰膜。
(6)成型制品缺陷产生的原因及解决方法。
RIM制品缺陷产生的原因及解决办法见表1。
表1 RIM成型常见制品缺陷和对策RIM模具与制品设计1.模具设计(1)浇注系统。
浇注系统又称“注入系统”,由浇口、流道和排气孔组成。
在进行RIM模具设计时,浇口形状与高度取决于成型制品的壁厚与型腔流量。
大容量的模具通常宜采用直棒状浇口,而小容量模具则宜采用扇形浇口。
主流道的位置应直接设在模具上,但应注意,在确定流道位置时,务必使物料从制品的横截面的最低处进入型腔。
排气孔的位置则应设在物料流动的末端,以便注射时将空气赶出型腔。
(2)模温控制系统。
这里仅以RIM金属模具为例加以说明。
模具温度的控制方法通常是在模内埋设套管,通入水进行加热或冷却。
金属模具厚度应为50mm,而套管间距要因加工树脂不同而有所不同。
通常,聚氨酯RIM的模温为40~80℃,模温控制精度为±4℃,最好为±1℃。
套管间距为80~100mm,冷却孔与模具腔壁之间的距离应为9.5mm。
(3)分型面。
对分型面的位置设置有一总体要求,就是将分型面位置设在加工制件轮廓的附近稍下方,这样可使正在膨胀并充满型腔的物料将型腔内的残留空气排至模外。
2.制品设计(1)制品厚度。
与常规注射制品相同,在进行RIM制品的壁厚设计时,同样应避免壁厚过厚或过薄。
以聚氨酯泡沫塑料RIM制品为例,常规壁厚应控制在6.35~12.7mm,当壁厚大于12.7mm或小于3.17mm时,则应采取适当的补救措施。
(2)加强筋。
使用加强筋的目的是提高制品的刚性与强度。
应选用细而长的加强筋,避免选用粗而短的加强筋。
加强筋的设置应沿物料流动方面为宜,这样不会影响物料流动过程中的气体排放。
(3)脱模斜度。
RIM制品的脱模斜度应选择2°,太大或太小都不利于制品脱模。
(4)圆角。
RIM制品的内部圆角半径不得小于3.175mm,外部圆角半径不得小于1.578mm。
(5)凸台。
凸台应采用2°的脱模斜度并沿制件周边或内筋布置,若凸台的设计高度超过6.57mm,则必须由撑板相辅。
在导入孔中成型,必须准确确定定位螺纹和自攻螺纹的位置。
凸台和导入孔的尺寸对于脱模强度影响很大,应加以注意。
多种多样的RIM技术1.聚氨酯RIM聚氨酯RIM所用原料与通用型聚氨酯原料不同的是:要求液体原料粘度低、流动性好及反应活性高,而且原料应配制成A(多元醇)、B(二异氰酯)两组分。
其工艺过程包括:将A、B两组分原料分别置于注射机的原料罐中,并使它们在N2气氛中、于一定温度下保持适宜的粘度(1Pa·s以下)和反应活性;用定量泵将两组分原料按一定比例压入混合器并注入密封的模具中;混合物在模具内迅速聚合,固化成型。
在这一过程中,从原料压出到充满模腔只需1~4s,而完整的生产周期则为30~120s。
2.聚氨酯RRIM聚氨酯RRIM工艺所用的双组分是多元醇和异氰酸酯。
多元醇为聚醚型,相对分子质量为1?800~2?400,官能度为2~3;异氰酸酯一般为二苯基甲烷二异氰酸酯(MDI)或多异氰酸酯及其异构体的混合物,官能度为2~7。
RRIM的增强材料主要有两种,即短切增强纤维和磨碎增强纤维。
纤维的长度一般为1.5~3.0mm,这种长度既能保证增强效果,又便于通过注射系统。
纤维长度的分散性越大,则增强效果越差。
RRIM制品中的增强纤维含量(质量分数)一般在20%以下,对于特殊要求的高强度制品,增强纤维的含量可达50%。
3.环氧树脂RIM环氧树脂是继聚氨酯之后开发的又一热固性RIM品种。
双组分环氧树脂RIM工艺过程与聚氨酯RIM大致相同。
环氧树脂与固化剂配比及工艺条件见表2。
表2 环氧树脂配方及工艺条件环氧树脂RIM制品的拉伸强度和弯曲模量高,线膨胀系数低,并具有优良的耐化学性和较高的耐热性(与聚氨酯和尼龙相比)。
为了改善环氧树脂的冲击强度,可在原料中添加带有异氰酸酯基、相对分子质量为4?000的聚乙二醇预聚物。
另外,为进一步提高力学性能,还可加入各种增强材料,如各种纤维、须状粉末、片状粉末、微珠料及长纤维等,使之成为RRIM制品,它们在汽车工业的应用中极具竞争力。
4.尼龙6 RIM尼龙6 RIM所用的原料包括聚醚多元醇和催化剂制成的预聚物(A组分)及己内酰胺(B组分)。
加工时,先将己内酰胺加入原料罐中,控制温度为74~85℃,再加入催化剂,封闭容器,强力搅拌使催化剂溶于己内酰胺中,混合物在N2下脱气15min。
再将己内酰胺和预聚物混合,混合温度74~85℃,搅拌均匀后脱气。
随后在压力作用下,两种液体组分经过混合器进入模具,固化成型。
由于预聚物和己内酰胺发生了嵌段共聚反应,因而所得制品柔性好,冲击强度高。
添加了增强材料的尼龙6 RRIM制品的刚性更高,线膨胀系数较低。
尼龙6 RIM和RRIM制品用途较广,主要用于汽车工业,如挡泥板、门板、发动机罩和防撞盖等。
5.双环戊二烯(DCPD)RIMDCPD RIM的原料主要包括DCPD、催化剂、活化剂、稳定剂、调节剂、填料、抗氧剂、弹性体、发泡剂、阻燃剂及成核剂等。
在DCPD RIM体系中,一般将各种原料按配方要求分为A、B两组分,其中A组分包括DCPD、催化剂、稳定剂及其他助剂等。
B组分包括DCPD、活化剂、调节剂及其他助剂等。
加工时,经准确计量的A、B两组分在混合头内混合均匀后,被注入密封模具内,在模具中发生快速聚合反应,随之固化成型。
需要特别注意的是,在模具未充满前,由聚合反应时间调节剂来控制化学反应。
充满模具后,大约在10s内完成聚合而成型。
制品一般不需要经过后熟化过程。
6.聚脲RIM聚脲RIM使用的是一种含内脱模剂的自脱模物料体系,成型时由端氨基聚醚、胺扩链剂与端基为异氰酸基的预聚物(MDI)反应制成聚脲。
该工艺具有很多优良特性:由于胺基和异氰酸基的反应活性高,因而不需要催化剂;反应物料注入模腔时粘度大,充模时减少了涡流,因此带入空气少,制品的废品率低;物料入模后1~2s内即发生凝胶,在模具内仅需停留20s;脱模时物料不黏附模腔,选用内脱模剂体系受限制较少;加入增强玻璃纤维制备聚脲RRIM 制品时,对胺与异氰酸酯之间的反应亦无影响。
聚脲生成的整个反应过程中不需要催化剂,使得制品中无残存催化剂,故而聚脲RIM制品在高温下不发生降解,制品稳定性好。
端氨基聚醚、二胺扩链剂与MDI的反应速度很快。
为使反应处于可控制状态,可用部分聚醚多元醇对MDI进行改性以制成半预聚物,从而降低物料之间的反应速度,减缓反应物料的凝胶速度。
同时,通过调节游离异氰酸基含量,还可制得具有不同弯曲弹性模量的聚脲RIM制品。
陶氏化学公司的SPECTRIMTMHT系列聚脲的性能见表3。
表3 聚脲SPECTRIMTMHT系列性能7.毡片模塑RIM将增强纤维制成毡片,预先放置于模具中,然后,两组分低粘度液体经高压撞击混合并注入型腔。
在型腔中,混合液体浸渍纤维毡片并反应形成制品,这种成型方法被称为“毡片模塑RIM(MM/RIM)”。
ARIMA×1000是Ashland公司开发的MM/RIM 产品,其性能见表4。
表4 ARIMA×1000的性能8.可变纤维反应注射成型(VFRIM)MM/RIM技术是先将纤维铺设于模具型腔,然后再注入液态树脂。