环氧树脂工艺介绍
环氧树脂的生产工艺

对设备 的腐蚀
产品 质量
苯酚 回收量
反应 周期
劳动 强度
硫酸法
旧工艺 新工艺
简单 更简单
间歇 间歇
很严重 较严重
很差 较差
— —
长 一般
高 较高
盐酸法 氯化氢气体法 三氯化硼法 四氯化硅甲苯法 疏基离子交换 树脂法
复杂 复杂 一般 一般 较简单
间歇 间歇、连续 间歇 间歇、连续 连续
二 环氧树脂的交联固化
固化温度与使用固化剂种类和用量有关,从低温到高温均可。其固化过程一般不放出水或其它低分子,故作胶粘剂、层压制品或浇注灌封的制品均不会有多孔性缺陷。
环氧树脂的固化剂种类繁多,随着科技进步及各部门的需要,新的固化剂还在不断涌现。
双酚A环氧树脂本身很稳定,即使加热到200℃也不变化。由于树脂中含有很多可以反应的活性基团(如环氧基、羟基)所以树脂均能在酸性或碱性固化剂的作用下固化。
弹性模量低、耐温性差、层间剪切强度低、耐老化差
轻质高强
FRP性能特点
性能的 可设计性好
工艺性好
邻苯型、间苯型、双酚A、乙烯基系
FRP生产原料
01
UP
02
树脂
03
生产原料
04
固化剂
EP 填料 助剂
FRP生产工艺
● 手糊成型工艺 ● 喷射成型法 ● 缠绕成型法 ● 注射成型法 ● 模压法 ● 连续挤拉成型法 ● 层压法
NaOH浓度:30%
A 低分子量树脂的生产
配料:双酚A:环氧氯丙烷:NaOH=1:2.75:2.42(摩尔)
除配料比有差别外,操作和温度等基本一致。 中等分子量: 双酚A:环氧氯丙烷:NaOH=1:1.473:1.598(摩尔); NaOH浓度10%。 高分子量: 双酚A:环氧氯丙烷:NaOH=1:1.218:1.185; NaOH浓度10%。
环氧树脂生产工艺

环氧树脂生产工艺环氧树脂是一种重要的聚合物材料,广泛应用于涂料、胶黏剂、复合材料等领域。
环氧树脂的生产工艺主要包括原料处理、环氧树脂合成和产品加工三个步骤。
原料处理是环氧树脂生产的第一步。
环氧树脂的主要原料是环氧化合物和多元酸酐。
环氧化合物一般是含有两个或多个环氧基团的有机化合物,如双酚A、环氧丙烷等。
多元酸酐一般是含有两个或多个羧酸酐基团的化合物,如酞酸酐、脂肪酸酐等。
在原料处理中,首先需要对原料进行筛选和储存,确保原料的质量稳定。
然后进行配比,根据需要调整不同原料的比例,得到目标产品的配方。
最后进行预处理,如加热、混合等,以便后续的环氧树脂合成。
环氧树脂合成是环氧树脂生产的核心步骤。
合成环氧树脂的方法有很多种,常见的是环氧化反应和羧酸酐反应。
环氧化反应是指将环氧化合物与多元酸酐反应,形成环氧树脂的过程。
该反应一般在高温条件下进行,并加入催化剂促进反应的进行。
羧酸酐反应则是指将环氧化合物与酸酐反应,生成环氧树脂。
不同的合成方法有不同的反应条件和催化剂选择,以获得具有特定性能的环氧树脂。
合成完环氧树脂后,还需要进行产品加工。
产品加工一般包括溶剂调配、填充料添加、固化剂调整等过程。
溶剂调配是将环氧树脂与适量的溶剂混合,以调整产品的粘度和流动性。
填充料添加是将适量的填充料加入到环氧树脂中,以增加产品的强度和硬度。
固化剂调整是根据需要调整固化剂的类型和用量,以控制产品的固化速度和性能。
最后,将加工好的环氧树脂产品进行包装和储存,以确保产品的质量和长期保存。
总的来说,环氧树脂的生产工艺包括原料处理、环氧树脂合成和产品加工三个步骤。
通过合理的配比和反应条件,可以制备出具有特定性能的环氧树脂产品。
环氧树脂的生产工艺也在不断发展中,新的工艺和技术的应用将进一步提高产品的质量和性能,推动环氧树脂产业的发展。
简述环氧树脂封装工艺

简述环氧树脂封装工艺
环氧树脂封装工艺是一种常见的电子元器件封装技术,其主要原理是将电子元器件放入环氧树脂中进行封装,以保护元器件不受外界环境的影响。
下面将从材料选择、工艺流程、特点等方面进行详细介绍。
一、材料选择
1. 环氧树脂:环氧树脂是一种高分子化合物,具有优异的绝缘性能和机械强度,常用于电子元器件的封装。
2. 硬化剂:硬化剂是环氧树脂的重要组成部分,能够使环氧树脂快速固化,并提高其机械性能。
3. 填充物:填充物可以增加环氧树脂的强度和硬度,常用的填充物有石墨、玻璃纤维等。
二、工艺流程
1. 准备工作:首先需要准备好所需材料和设备,并对电子元器件进行清洗和干燥处理。
2. 混合材料:将环氧树脂、硬化剂和填充物按比例混合均匀。
3. 封装:将电子元器件放入封装模具中,倒入混合好的环氧树脂,待固化后取出即可。
4. 固化:环氧树脂需要一定时间进行固化,通常需要在恒温恒湿条件下进行。
三、特点
1. 绝缘性能好:环氧树脂具有优异的绝缘性能,可以有效保护电子元
器件不受外界环境的影响。
2. 机械强度高:环氧树脂可以增加电子元器件的机械强度和硬度,提
高其抗震动和抗振动能力。
3. 耐温性好:环氧树脂具有较高的耐温性能,在高温环境下也能保持
稳定性能。
4. 工艺简单:环氧树脂封装工艺相对简单,不需要复杂的设备和技术,容易掌握。
综上所述,环氧树脂封装工艺是一种常见的电子元器件封装技术,具
有绝缘性能好、机械强度高、耐温性好等特点。
在实际应用中,需要
注意材料选择和工艺流程,以保证封装质量和稳定性。
环氧树脂的生产工艺

环氧树脂的生产工艺1. 简介环氧树脂是一种具有广泛应用领域的重要合成树脂。
它具有优良的耐腐蚀性、机械强度高、绝缘性能好等特点,因此在涂料、粘合剂、复合材料等领域得到了广泛应用。
本文将介绍环氧树脂的生产工艺。
2. 原料准备环氧树脂的生产过程需要准备以下原料: - 环氧化合物:一般选择环氧氯丙烷或环氧环己烷作为主要原料。
- 硬化剂:常用的硬化剂有聚酰胺、酸酐和环氧值较低的酚醛树脂等。
- 催化剂:通常使用类似胺类的催化剂。
3. 反应槽设备环氧树脂的生产通常需要一个反应槽设备。
反应槽应具备耐腐蚀性和耐高温性能,以确保生产过程中不发生意外事故。
同时,反应槽还需要具备良好的密封性能,以控制反应条件。
4. 生产工艺步骤4.1 反应槽预处理首先,需要对反应槽进行清洗和干燥处理,以确保反应槽内部的洁净度和干燥度。
4.2 原料配制将准备好的环氧化合物、硬化剂和催化剂按照一定的配比加入反应槽中。
配比的选择应根据所需产品的性能要求进行调整。
4.3 混合反应将反应槽密封,控制好温度和压力条件,开始进行混合反应。
混合反应的时间和温度取决于所选的催化剂和反应体系的性质。
4.4 出料和后处理反应结束后,将反应产物从反应槽中排出,并对其进行后处理。
这包括冷却、固化、研磨等步骤,以获得最终的环氧树脂产品。
5. 质量控制生产过程中的质量控制非常重要,可以通过以下方式进行: - 严格控制原料的质量,并配合合理的配比。
- 控制好反应过程中的温度、压力和反应时间,以保证产品的性能。
- 进行产品的抽样检测,包括外观、粘度、固含量等指标。
6. 环境与安全在环氧树脂的生产过程中,还需要关注环境保护和安全生产。
以下是一些常见的措施: - 选择环保的原材料和工艺,减少对环境的污染。
- 加强安全意识培训,严格遵守操作规程,防止事故的发生。
- 定期对生产设备和工艺进行检查和维护,确保设备安全可靠。
7. 结论环氧树脂作为一种重要的合成树脂,在涂料、粘合剂、复合材料等领域具有广泛的应用。
环氧树脂的合成工艺
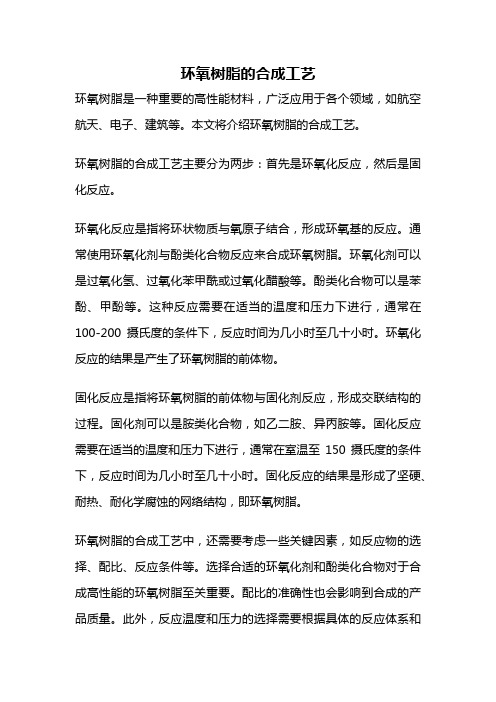
环氧树脂的合成工艺环氧树脂是一种重要的高性能材料,广泛应用于各个领域,如航空航天、电子、建筑等。
本文将介绍环氧树脂的合成工艺。
环氧树脂的合成工艺主要分为两步:首先是环氧化反应,然后是固化反应。
环氧化反应是指将环状物质与氧原子结合,形成环氧基的反应。
通常使用环氧化剂与酚类化合物反应来合成环氧树脂。
环氧化剂可以是过氧化氢、过氧化苯甲酰或过氧化醋酸等。
酚类化合物可以是苯酚、甲酚等。
这种反应需要在适当的温度和压力下进行,通常在100-200摄氏度的条件下,反应时间为几小时至几十小时。
环氧化反应的结果是产生了环氧树脂的前体物。
固化反应是指将环氧树脂的前体物与固化剂反应,形成交联结构的过程。
固化剂可以是胺类化合物,如乙二胺、异丙胺等。
固化反应需要在适当的温度和压力下进行,通常在室温至150摄氏度的条件下,反应时间为几小时至几十小时。
固化反应的结果是形成了坚硬、耐热、耐化学腐蚀的网络结构,即环氧树脂。
环氧树脂的合成工艺中,还需要考虑一些关键因素,如反应物的选择、配比、反应条件等。
选择合适的环氧化剂和酚类化合物对于合成高性能的环氧树脂至关重要。
配比的准确性也会影响到合成的产品质量。
此外,反应温度和压力的选择需要根据具体的反应体系和产品要求进行调整。
在环氧树脂的合成工艺中,还可以通过引入其他功能性单体来改变其性能。
例如,可以添加含有双键的单体,使环氧树脂具有良好的耐冲击性和韧性。
还可以添加含有活性基团的单体,使环氧树脂具有更好的耐化学腐蚀性能。
这些功能性单体的引入可以通过共聚反应实现。
环氧树脂的合成工艺是一个复杂的过程,需要合理选择反应物、配比和反应条件。
通过环氧化反应和固化反应,可以合成出具有良好性能的环氧树脂。
随着科技的进步,环氧树脂的合成工艺也在不断发展,为各个领域提供了更多应用的可能性。
环氧树脂的生产工艺方案

环氧树脂的生产工艺方案环氧树脂是一种重要的合成材料,广泛应用于涂料、粘合剂、电子电气设备和航空航天等领域。
其生产工艺主要分为酚醛法、酚酸法和环氧氯化物法等多种方法。
一、酚醛法:酚醛法是一种传统的环氧树脂生产工艺,主要步骤如下:1.原料准备:准备苯酚、甲醛和碱性催化剂作为主要原料。
2.酚醛缩合反应:将苯酚和甲醛在碱性催化剂的作用下进行缩合反应,生成酚醛树脂。
3.环氧化反应:将酚醛树脂与环氧化剂进行反应,生成环氧树脂。
4.精制和分离:对得到的环氧树脂进行精制和分离,得到所需产品。
酚醛法具有工艺简单、操作方便的优点,但由于该方法对原料的要求较高,容易产生有毒物质,限制了其在环氧树脂生产中的应用。
二、酚酸法:酚酸法是一种改进的环氧树脂生产工艺,其主要特点是采用酚酸酯作为中间产物。
具体步骤如下:1.酚酸酯合成:将苯酚与酸酐在酸催化剂的作用下反应,生成酚酸酯。
2.酸酐环氧化:将酸酐酯与环氧化剂进行环氧化反应,生成环氧树脂。
3.精制和分离:对得到的环氧树脂进行精制和分离。
酚酸法相对于酚醛法具有操作简便、原料较为容易获取的优点,同时产生的副产物较少,对环境污染小。
三、环氧氯化物法:环氧氯化物法是目前广泛采用的环氧树脂生产工艺,其主要过程如下:1.原料准备:准备环氧化剂、马来酸盐和溴代调整剂等作为主要原料。
2.环氧化反应:将环氧化剂与马来酸盐在催化剂的作用下反应,生成环氧树脂。
3.分离和精制:对得到的环氧树脂进行分离和精制。
环氧氯化物法具有工艺流程简单、环境友好的优势,同时可根据需要进行不同的调整剂加入,以改变环氧树脂的性能。
总之,环氧树脂的生产工艺方案主要包括酚醛法、酚酸法和环氧氯化物法等多种方法。
每种方法都有其特点和适用范围,企业可以根据自身需求和实际情况选择适合的工艺方案。
环氧树脂漆工艺

环氧树脂漆工艺一、引言环氧树脂漆是一种广泛应用于建筑、工业等领域的涂料材料,具有优异的附着力、耐磨性和耐腐蚀性能。
环氧树脂漆工艺是指在使用环氧树脂漆进行涂装时所采用的一系列操作和步骤。
本文将从环氧树脂漆的特性、涂装前的准备工作、涂装工艺和涂装后的处理等方面进行介绍。
二、环氧树脂漆的特性环氧树脂漆具有以下特性:1. 优异的附着力:环氧树脂漆能够与各种基材形成牢固的结合,使涂层具有良好的附着力。
2. 耐磨性强:环氧树脂漆具有出色的耐磨性,能够承受较大的机械磨损。
3. 耐腐蚀性好:环氧树脂漆对酸、碱、盐等化学品具有较好的耐腐蚀性,能够有效保护基材。
4. 施工性好:环氧树脂漆施工过程简便,可涂刷、喷涂或滚涂,适用于不同形状和材质的基材。
三、涂装前的准备工作在进行环氧树脂漆涂装之前,需要进行以下准备工作:1. 表面清洁:将基材表面的油污、灰尘等杂质清除干净,以保证涂层与基材之间的附着力。
2. 表面处理:对于金属基材,可以采用喷砂、抛光等方式进行表面处理,增加涂层与基材的结合力。
3. 基材修补:对于基材表面的凹陷、裂缝等缺陷,需要进行修补,以保证涂装后的表面平整。
4. 底漆涂装:在涂装之前,可以先进行底漆涂装,增加涂层的附着力和耐久性。
四、涂装工艺环氧树脂漆的涂装工艺一般包括以下步骤:1. 搅拌:将环氧树脂漆搅拌均匀,以保证其成分充分混合。
2. 稀释:根据需要可以将环氧树脂漆适量稀释,以调节涂层的粘度和流动性。
3. 涂刷:使用刷子将环氧树脂漆均匀涂刷在基材表面,注意避免漏刷和堆积。
4. 喷涂:使用喷枪将环氧树脂漆均匀喷涂在基材表面,注意控制好喷涂的厚度和均匀度。
5. 滚涂:使用滚筒将环氧树脂漆均匀滚涂在基材表面,注意避免滚筒滚出气泡和刷痕。
6. 干燥:根据环氧树脂漆的特性和施工环境,进行适当的干燥时间,以保证涂层的质量。
五、涂装后的处理在涂装完成后,还需要进行以下处理:1. 检查:对涂装后的表面进行检查,确保涂层的质量和外观。
环氧树脂工艺流程

环氧树脂工艺流程一、环氧树脂的概述环氧树脂是一种热固性树脂,具有优异的物理性能和化学稳定性,被广泛应用于涂料、粘合剂、电子材料等领域。
其制备过程包括环氧化反应、缩合反应和固化反应。
二、原材料准备1. 环氧树脂:选择适合用途的环氧树脂,可根据不同要求选择不同型号。
2. 固化剂:通常使用胺类固化剂,如乙二胺、三乙烯四胺等。
3. 添加剂:如增塑剂、填料等。
三、制备工艺流程1. 环氧化反应:将环氧树脂与酚类或酸类进行反应,得到具有活性基团的环氧预聚体。
2. 缩合反应:将环氧预聚体与缩合剂进行反应,形成线型分子结构。
3. 固化反应:将线型分子结构的环氧树脂与固化剂进行混合并加热,使其发生交联反应,形成硬质无机聚合物。
四、具体步骤1. 环氧化反应:(1)将环氧树脂加入反应釜中,加热至一定温度。
(2)将酚类或酸类缓慢滴入反应釜中,控制反应速率。
(3)反应结束后,通过蒸馏等方法去除副产物。
2. 缩合反应:(1)将环氧预聚体和缩合剂混合均匀。
(2)加热至一定温度,控制时间和温度,使其发生缩合反应。
(3)反应结束后,通过过滤等方法去除不溶性物质。
3. 固化反应:(1)将线型分子结构的环氧树脂与固化剂混合均匀。
(2)根据需要添加填料、增塑剂等添加剂,并混合均匀。
(3)加热至一定温度,控制时间和温度,使其发生固化反应。
(4)冷却后即可得到成品。
五、注意事项1. 选择适合用途的环氧树脂和固化剂,并按比例混合使用。
2. 控制好每个步骤的时间、温度和速率,以保证产品质量。
3. 添加剂的使用应根据需要和比例进行,过量使用会影响产品性能。
4. 操作时应注意安全,避免接触皮肤和吸入有害气体。
六、总结环氧树脂制备工艺流程包括环氧化反应、缩合反应和固化反应。
在操作时需要选择适合用途的原材料,并严格控制每个步骤的时间、温度和速率。
同时,添加剂的使用也要按比例进行,以保证产品性能。
操作时要注意安全,避免接触皮肤和吸入有害气体。
- 1、下载文档前请自行甄别文档内容的完整性,平台不提供额外的编辑、内容补充、找答案等附加服务。
- 2、"仅部分预览"的文档,不可在线预览部分如存在完整性等问题,可反馈申请退款(可完整预览的文档不适用该条件!)。
- 3、如文档侵犯您的权益,请联系客服反馈,我们会尽快为您处理(人工客服工作时间:9:00-18:30)。
1、环氧树脂浇注及浇注材料
环氧树脂浇注是将环氧树脂、固化剂和其他配合料浇注到设定的模具内,由热塑性流体交联固化成热卧性制品的过程。
由于环氧树脂浇注产品集优良的电性能和力学性能于一体,因此环氧树脂浇注在电器工业中得到了广泛的应用和决速的发展。
环氧树脂浇注的工艺方法,从不同的工艺条件去理解有不同的区分方法。
从物料进入模具的方式来区分可分为浇注和压注。
浇注指物料自流进入模具。
它又分常压浇注和真空浇注。
压注指物料在外界压力下进入模具,并且为了强制补缩,在物料固化过程中,仍保持着一定的外压,它由过去的简单加压凝胶法发展成现在成熟的自动压力凝胶法。
从物料固化温度来区分可分为常温浇注法和高温浇注法。
选用常温或高温浇注法由浇注材料的本身性质所决定的,其根本区别是浇注材料固化过程中所必需的温度条件。
从物料固化的速度来区分可分为普通固化法和快速固化法。
物料进入模具至拆模所需的时间为初固化时间,普通固化法需几个甚至十几个小时,快速固化法只需十几分钟至几十分钟。
现代浇注工艺中,应用比较成熟的浇注工艺方法主要是真空浇注法和自动压力凝胶法。
(1)真空浇注工艺
真空浇注工艺是目前环氧树脂浇注中应用最为广泛、工艺条件最为成熟的工乙方法。
对于一件环氧树脂浇注的电器绝缘制品,它要求外观完美、尺寸稳定、力学年耍:—电性能合格。
它的这些性能取决于制件本身的设计、模具的质量、浇注用材料的选择、浇注工艺条件的控制等各个方面。
环氧树脂真空浇注的技术要点就是尽可能减少浇注制品中的气隙和气泡。
为了达到这一目的,在原料的预处理、混料、浇注等各个工序都需要控制好真空皮、温度及工序时间。
(2)自动压力凝胶工艺
自动压力凝胶工艺是20世纪70年代初由瑞士CIB入Ctigy公司开发的技术。
因为这种工艺类似于热塑性塑料注射成型的工艺方法,因此也称其为压力注射工艺。
它的最为显著的优点是大大提高了浇注工效。
可以说自动压力凝胶技术的开发成功及在工业上的大量应用,是真空浇注由间歇、手工操作向自动化生产发展的一场革命,它和真空浇注的主要区别在于:
1)浇注材料是在外界压力下通过管道由注入口注入模具。
2)物料的混料处理温度低,模具温度高。
3)物料进人模具后,固化速度快,通常为十几分钟至几十分钟。
4)模具固定在液压机上,模具加热由模具或模具固定板上的电热器提供。
5)模具的合拆由液压机上的模具固定板移动来完成。
自动压力凝胶工艺的特点:模具利用率高,生产周期短,劳动效率高;模具装卸过程中损伤程度低,模具使用寿命长;自动化程度高,操作人员劳动强度轻;制品成型性好,产品质量有所提高。
2、环氧树脂的灌封及灌封材料
(1)灌封料的用途
灌封是环氧树脂的一个重要应用领域。
已广泛地用于电子器件制造业,是电子工业不可缺少的重要绝缘材料。
灌封,就是将液态环氧树脂复合物用机械或手工方式灌入装有电子元件、线路的器件内,在常温或加热条件下固化成为性能优异的热因性高分子绝缘材料。
它的作用是:强化电子器件的整体性,提高对外来冲击、震动的抵抗力;提高内部元件、线路间绝缘,有利于器件小型化、轻量化;避免元件、线路直接暴露,改善器件的防水、防潮性能。
(2)灌封料的分类
环氧灌封料应用范围广,技术要求千差万别,品种繁多。
从固化条件上分,有常温固化和加热固化两类。
从剂型上分,有双组分和单组分两类。
多组分剂型,由于使用不方便,做为商品不多见。
常温固化环氧灌封料一般为双组分,灌封后不需加热即可固化,对设备要求不高,使用方便。
缺点是复合物作业教度大,浸渗性差,适用期短,难以实现自动化生产,且固化物耐热性和电性能不很高。
一般多用于低压电子器件灌封或不宜加热固化的场合使用。
(3)灌封料的术要求
加热固化双组分环氧灌封料,是用量最大、用途最广的品种。
其特点是复合物作业教度小,工艺性好,适用期长,浸渗性好,固化物综合性能优异,适于高压电子器件自动生产线使用。
单组分环氧灌封料,是近年国外发展的新品种,需加热固化。
与双组分加热固化灌封料相比,突出的优点是所需灌封设备简单,使用方便,灌封产品的质量对设备及工艺的依赖性小。
不足之外是成本较高,材料贮存条件要求严格,所用环氧灌封料应满足如下要求:
1)性能好,适用期长,适合大批量自动生产线作业。
2)教度小,浸渗性强,可充满元件和线间。
3)灌封和固化过程中,填充剂等粉体组分沉降小,不分层。
4)固化放热峰低,固化收缩小。
5)固化物电气性能和力学性能优异,耐热性好,对多种材料有良好的粘接性,吸水性和线膨胀系数小。
6)某些场合还要求灌封料具有难燃、耐候、导热、耐高低温交变等性能。
近年,随电子工业迅猛发展,我国已拥有一支优秀的环氧灌封料研究、开发队伍,专业生产厂家规模不断壮大,产品商品化程度明显提高,初步形成了门类品种较为齐全的新兴产业。