数控机床误差过大故障的分析与处理.
数控机床跟踪误差大故障分析与排除

F 耋
Pr
图 2 指 令 与 实际 速度 曲 线对 比 图 4 跟踪误差大故 障成 因分析 数控机床 中跟踪误差大是一个较为复杂的问题 , 其故障原因多种多 样, 看似毫无规律可循。 但从 跟踪误差大报警机理出发, 可以知道跟踪误 差 大报警 条件可 以简单描 述为 :控制 指令值 一实 际反馈值 l I >允许 误 差, 确定排除此类 故障的三条主线 : 指令值过 大 、 实际反馈值过小或允许 误差过小。 1是 否为允许误差过/ ) b?
科技 论坛
2 1 年第 1 期 01 2
民 科技 营
数控机床跟踪误差 大故障分析 与排除
张 勇 吕家 将 z
(、 1 九江职业技术 学院继续教 育部 , 江西 九江 32 0 2 九江职业技 术学院机械工程学院, 300 、 江西 九江 3 20 ) 3 0 7
摘 要: 现从跟踪误差概念入手 , 深入 浅出地 阐述 了跟踪误差产生机理 , 并据此进行跟踪误差 大故 障成 因分析 , 最后 用“ 排故五 步法” 示范跟 踪 误 差大故障排除过程 。 关键词 : 跟踪误 差; 位置环 ; 故障诊 断; 步法 五 数控机床加工 时 , 经常会出现跟踪误差过 大的报警 , 探究其故 障机 所 以, 我们需要人 为的确定一个极 限值作 为最大跟踪误差 , 超过此 极限 理 ,找到快速有效 的排除此故障的方法与思路就 是本 文所要讨论 的内 值 , 机床就报警 , 避免产 品的成批报废 , 最大跟踪 误差 的设定 与加工 零件 容。 的位置与形状 的精度有密切关系。
1 什 么是 跟 踪 误 差 ?
为了保பைடு நூலகம்加工精度 , 目前的数控机床一般采取 了三环结构的伺服系 统, 系统实际位移值被反馈 到数控 装置或伺服驱动 中, 直接 与输 入的指 令位移值进行 比较 , 用误差进行 控制 , 最终实现移动部件 的精 确运动和 定位。所谓跟随误差 , 是指伺服系统发 出的指令位置与系统输出的实际 位置之 间的动态误差 , 其大小反映 的是当前采样周期 , C指令位置值与 N 坐标轴实 际运行值之间的差值 。 到底 , 说 跟踪误差与位置有关 , 了 究 为 研 跟踪误差 , 就少不得理解位置环 的工作原理。 位置环 的结构简图如图 1 所示 , 其核心为位置偏差计数器。P 来 自 z 于N 。 C 这是 N C根据输入数据经过插补计算及刀补计算 , 速度的均化等 处理 , 向各轴发出的脉 冲, 个数代表距 离 , 频率代表速度 , 于位 置偏差 对 计算器而言, 是加计数。 f 自于脉 冲编码器的反馈脉冲, P来 个数代表工作 台运行 的实际距离 , 频率代表电机旋转速度。 它通过同步, 四分频等控制 和转换 后送到偏差计算器中去 , 是减计数。 在每个采样周期 内, 置偏差 计数器得到一个数 , 位 这个数就 是跟踪 误差 , 表示 N C要求这个轴运行的距 离还有 多少 没有走 出去 。数 大表 明 实际运行距离与 N C要求 运行 距离差得远 , 望坐标轴 走快 点 , 以这 希 所 个数经过 DA转换 , / 转换为模拟量去控制 电机速度。数小 表明 目前距离 目 标近 , 就要慢慢接近 目 , 标 最后准确停车。
数控机床跟踪误差过大的故障诊断

任务2 跟踪误差过大的故障诊断【任务目标】1、掌握伺服进给系统的位置控制原理;2、掌握跟踪误差过大的原因;3、掌握跟踪误差过大故障的诊断思路;4、能够排除跟踪误差过大的故障。
【任务描述】有一台YL559数控车床,配备FANUC 0i TD数控系统,采用半闭环控制,在手动移动X 轴的时候,出现“SV0411 (X)移动时误差太大”报警,故障现象见图6-2-1。
本次任务的工作是找出故障原因并能排除故障。
图6-2-1 故障现象【资讯计划】一、资料准备要完成本任务中的故障诊断及排除工作,需要配备以下资料:1、FANUC 0i D数控系统硬件连接说明书;2、FANUC 0i D数控系统维修说明书;3、YL559数控机床电气原理图;4、FANUC PMC梯形图语言说明书;5、故障记录单。
二、工具、材料准备要完成本任务中的故障诊断及排除工作,需要配备以下工具和材料,具体见表6-2-1。
表6-2-1 工具和材料清单三、知识准备伺服进给系统的任务是尽可能使系统的输出准确地跟踪给定输入,位置控制的实质是位置的随动控制。
位置控制包含两部分:位置比较和速度控制指令的实现,如图6-2-2所示。
图6-2-2 位置控制原理1、位置控制原理下面以脉冲比较法实现位置的比较为例,说明伺服系统位置控制的原理。
脉冲比较法是将CNC 插补输出脉冲P C 与位置检测装置输出脉冲P f 相比较,得到脉冲偏差信号P e ,如图6-2-3所示。
12323432323232321212121指令信号Pc 反馈信号Pf 误差量图6-2-3 脉冲比较示意图当数控系统控制工作台向一个方向(比如X 轴)进给时,经插补运算得到一系列脉冲作为指令脉冲,该脉冲的数量代表了工作台的移动量,脉冲的频率代表了工作台的进给速度,方向代表了工作台的进给方向。
以增量型光电编码器为例,当光电编码器与伺服电动机和滚珠丝杠直连时,随着伺服电动机的转动,产生序列脉冲输出,脉冲的频率将随着转速的快慢而升降。
数控机床孔加工的常见问题与解决方式

数控机床孔加工的常见问题与解决方式数控机床是一种高精度、高效率的机械加工设备,广泛应用于各个制造行业。
在数控机床的孔加工过程中,常常会遇到一些问题,如孔径误差过大、孔底质量差等。
本文将针对数控机床孔加工的常见问题进行分析,并提供相应的解决方式。
首先,孔径误差过大是孔加工中常见的问题之一。
造成孔径误差过大的原因有很多,如机床热变形、刀具磨损等。
解决这个问题的方法是进行机床的温度补偿,通过监测机床温度的变化来控制机床的加工过程,以保证孔径的精度。
其次,孔底质量差也是常见的问题之一。
孔底质量差主要是由于切削过程中产生的毛刺和残留物导致的。
解决这个问题的方法是合理选择切削参数,并使用合适的润滑剂来降低摩擦力,减少残留物的产生。
此外,还可以采用后处理的方式进行除毛刺,如采用锉刀或砂纸进行修整。
此外,孔壁粗糙度高也是数控机床孔加工中常见的问题之一。
孔壁粗糙度高主要是由于切削刀具损耗和润滑不良导致的。
解决这个问题的方法是定期更换切削刀具,保证切削刀具的锋利度;同时,加强切削润滑,使用合适的润滑剂来降低摩擦力,以提高加工效果。
另外,孔位误差是孔加工中常见的问题之一。
孔位误差主要是由于机床定位不准确或刀具位置不稳定导致的。
解决这个问题的方法是定期检查和校准机床定位装置,确保机床的精度;同时,采用稳定的刀具固定方式,如采用刀具夹紧器固定刀具等,以保证刀具位置的稳定性。
此外,孔加工过程中还可能遇到其他一些问题,如微抖动、断屑等。
微抖动主要是由于机床刚性不足导致的,解决方法是增加机床的刚性,例如加装稳定支撑或调整刀具切入角度。
断屑主要是由于切削刀具切削力过大或润滑不良导致的,解决方法包括降低切削刀具的切削力、增加润滑剂的使用量等。
综上所述,数控机床孔加工中常见的问题包括孔径误差过大、孔底质量差、孔壁粗糙度高、孔位误差等。
针对这些问题,我们可以采取相应的解决方式,如温度补偿、合理选择切削参数、定期更换切削刀具、加强切削润滑、检查和校准机床定位装置等。
数控车床常见故障及解决对策

数控车床常见故障及解决对策近年来,随着数控技术的迅猛发展,数控车床在工件加工中表现出来的优点越来越多,如加工质量稳定、生产率高、适应性好等,因此许多的工厂企业都将数控车床作为重要的机械加工设备;大部分的技工院校也都面向社会需求,把数控车床的教学作为一项常规的教学任务,而非见习性教学任务。
数控车床在使用过程中不可避免地会发生一些故障,笔者结合自己在实习教学工作中遇到的一些实际问题作以下几点分析。
一、出现“数据位数过多”的报警信息数控车床在多次进行图形模拟、验证确保程序基本正确后再对刀,准备进行工件加工时,却发现总是提示“数据位数过多”的报警信息。
这一现象比较多地发生在数控车床的检测反馈元件采用的是增量式编码器机床上,其原因在于:在图形显示空运行程序时,都是在机床锁定的状态下,此时机床面板上显示的坐标位置是按照程序当中的设定进行变化,但是实际上机床位置不动。
这样程序运行结束后,面板上所显示的坐标位置和运行前就存在一定的偏差,如此所述情况,在进行了多次的图形显示(机床锁定空运行)后,机床面板上显示的坐标值就会对所有的偏差进行累加,最终导致坐标值超出机床的行程范围。
这样在对刀时(目的是设定工件坐标系在机床坐标系下的相对位置),机床的运算就会出现问题,从而产生报警。
此时,复位、机床回零并不能解决问题,必须对系统断电,然后重新开机,报警才能解除,机床才能够正常使用。
二、“急停报警”或“变频器报警”数控车床在发生撞车事件时,都会下意识地拍下急停,可是松开急停后,会出现“急停报警”或“变频器报警”。
这一现象一般发生在采用变频器进行无级调速的数控机床上,其原因在于,由于撞车,对电动机的输出功率(扭矩)产生很大需求,可是电动机的输出功率又是有一定的极限的,当超出此极限后,电机产生过载现象,为了防止事故的进一步扩大,系统都有过载保护措施。
机床就处于这种状态时,需要断电,重新开机,让数控系统重新初始化一下,就可以正常使用。
数控机床伺服系统常见故障的诊断及其处理

数控机床伺服系统常见故障的诊断及其处理数控机床伺服系统是机床的重要组成部分,其故障会严重影响机床的生产效率和质量。
本文将对数控机床伺服系统常见故障进行分析,提供相应的诊断和处理方法,帮助机床维修工程师进行有效的故障排查。
一、伺服电机输出不稳定或不工作的故障1. 伺服电机电气连接故障。
在伺服电机输出不稳定或不工作的情况下,首先要检查电气连接是否良好,包括伺服电机与伺服主轴电机之间的电气连接是否正常、伺服驱动器电气与伺服电机之间的连接是否正确、接地是否合格等,排除电气连接问题。
2. 伺服电机本身故障。
伺服电机的故障如轴承磨损、线圈断路、电机转子故障等都会导致输出不稳定或不工作的情况,需要进行检测和维修。
常见的检测方法如用万用表测量电机的电阻,检查电机转动是否灵活、轴承是否正常等。
3. 伺服驱动器故障。
伺服驱动器的故障如防护电路故障、电源故障、接口板连接不良等都会导致伺服电机输出不稳定或不工作,需要检查相应的部件进行排查。
常见的检测方法如检查驱动器是否有报警信号、电源是否正常、接口板是否正确插接等。
二、伺服系统位置偏移或误差过大的故障1. 导轨故障。
导轨质量差、磨损严重或进刀太大等都会导致伺服系统位置偏移或误差过大,需要检查导轨表面是否有磨损痕迹以及导向面是否平整。
2. 动态中的机械振动、系统震动或机床本身质量不好。
这些因素在机床运行中都会产生影响,导致伺服系统位置偏移或误差过大,需要进行检查和调整。
调整方法可采用优化机床支撑结构、调整伺服参数等。
3. 伺服系统参数设置错误。
如伺服系统的比例系数、积分系数和微分系数未能正确设置,将导致位置偏移或误差过大。
此时需要检查和调整伺服系统的参数设置。
三、伺服系统温度过高或过低的故障伺服系统的温度过高或过低都会导致数控机床性能下降,进而影响机床的精度和稳定性。
常见的故障原因包括:1. 冷却系统故障。
如冷却水温度过高或过低、冷却系统中水泵或水管路堵塞、扇叶损坏等都会导致伺服系统温度异常。
数控机床误差过大故障的分析与处理(精)

措施 延长加/减速时间设定 减小位置环增益或提高机 床的刚性 若正确,见第2项,否则 第3项 调整机床机械传动系统
提高位置环、速度环增益
若正确,见第2项,否则 第3项 调整机床机械传动系统
更换不良板 更换不良位置检测期间 (编码器、光栅) 维修、更换不良板 若轴向变形,则见第2项, 若45°方向上成椭圆,则 见第3项 调整机床,进行定位精度、 反向间隙的补偿 调整位置环增益以消除各 轴间的增益差
排除措施 依照参数说明书, 正确设置个参数
数控机床误差过大故障分析与处理
一加工误差过大故障的分析与处理
项目 超调 1
2
单脉 1 冲精 度差 2
3
定位 1 精 不良 2
3 4
5 圆弧 1 插补 加工 的圆 2 度差
3
4 5
6
故障原因 加/减速时间设定过小 与机床的连接部分刚性差或连接不牢固
需要根据不同情况进行故障分析
检测位置检测器件(编码器、光 栅)
测量不圆度,检查周向上是否变 形,45°方向上是否成椭圆
机床反向间隙大、定位精度差
测量各轴的定位精度与反向间隙
位置环增益设定不当
各插补轴的检测增益设定不良 感应同步器或旋转变压器的接口板调整不 良 丝杠间隙或传动系统间隙
调整控制单元,使同样的进给速 度下各插补轴的位置跟随误差的 差值在±1%以内 在项目3调整后,在45°上成椭圆 检查接口板的调整
一 数控机床振荡故障分析与处理 案例分析
分析及处理过程:进一步观察、测量机床Y 轴移动情况, 发现该机床 Y 轴伺服在移动到某一固定角度时,都有一冲 击过程:在无冲击的区域,测量实际移动距离与指令值相符, 根据以上现象,初步判定,故障原因与位置检测系统有关。
数控机床加工误差原因及对策分析

数控机床加工误差原因及对策分析数控车床为零件加工的主要方式,对于零件加工具有较高的自动化水平,但是就实际情况来看,零件加工经常会因为设备自身或者操作不当等因素限制,而造成工件精度达不到专业要求,存在一定误差。
零件加工精度最终由机床刀具与零件间相对位移误差决定,因此需要确定加工误差存在的原因,以降低误差为面对,采取措施进行优化。
本文选择经济性数控机床为对象,就其加工误差与优化对策进行了简要分析。
标签:数控机床;加工误差;补偿0 引言数控机床零件加工经常会因为各项因素的影响而出现误差,即加工后零件实际几何参数与设计几何参数间存在一定偏差,导致零件精确度不能满足设计要求,最终只能作为不合格或者废品处理。
以提高数控机床加工精确度为的目的,需要对各类加工误差原因进行分析,有针对性的采取措施进行处理,对存在的误差进行有效补偿。
1 数控机床加工误差分析经济性数控车床对零件的加工,应用为步进电机开环伺服系统或者半闭环伺服系统来驱动刀具,在这个过程中就会因为受各项因素的影响而存在加工误差。
一方面,数控机床自身因素。
主要是因为数控机床所用构件精确度较低,以及机床装配过程中存在误差,导致零件加工后精确度达不到设计要求。
针对此种误差原因,一般可以就高精度零部件进行更换,以及在装配环节做好控制,争取提高机床自身精确度。
另外,对于部分技术能力可以达到要求的企业,还可以选择对步进电机构成的开环伺服系统进行适当的改造,使其成为闭环伺服系统,来提高零件加工精度[1]。
另一方面,工艺操作因素。
部分零件在加工过程中,会因为机床以及零件本身的热变形,造成切削、振动、装夹、磨损等细节存在误差。
想要对此类误差进行补偿,需要建立补偿模型在CNC系统内补偿,实施难度比较大,对提高数控机床零件加工精确度需要重点研究。
2 数控机床加工误差原因与对策分析2.1 数控机床自身原因2.1.1 控制系统误差(1)开环控制系统。
开环控制系统并未设置反馈装置,数控信号为单向流程,并不能对移动部件实际位移量进行测量与反馈,进而会影响对加工过程中所存误差的调整。
数控机床的加工精度误差分析与校正方法
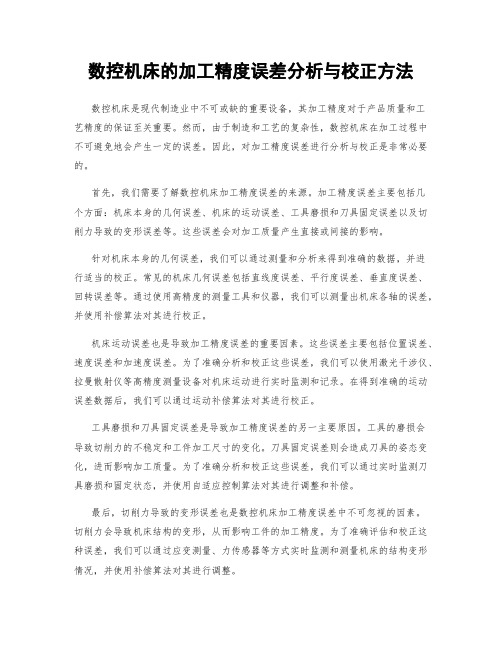
数控机床的加工精度误差分析与校正方法数控机床是现代制造业中不可或缺的重要设备,其加工精度对于产品质量和工艺精度的保证至关重要。
然而,由于制造和工艺的复杂性,数控机床在加工过程中不可避免地会产生一定的误差。
因此,对加工精度误差进行分析与校正是非常必要的。
首先,我们需要了解数控机床加工精度误差的来源。
加工精度误差主要包括几个方面:机床本身的几何误差、机床的运动误差、工具磨损和刀具固定误差以及切削力导致的变形误差等。
这些误差会对加工质量产生直接或间接的影响。
针对机床本身的几何误差,我们可以通过测量和分析来得到准确的数据,并进行适当的校正。
常见的机床几何误差包括直线度误差、平行度误差、垂直度误差、回转误差等。
通过使用高精度的测量工具和仪器,我们可以测量出机床各轴的误差,并使用补偿算法对其进行校正。
机床运动误差也是导致加工精度误差的重要因素。
这些误差主要包括位置误差、速度误差和加速度误差。
为了准确分析和校正这些误差,我们可以使用激光干涉仪、拉曼散射仪等高精度测量设备对机床运动进行实时监测和记录。
在得到准确的运动误差数据后,我们可以通过运动补偿算法对其进行校正。
工具磨损和刀具固定误差是导致加工精度误差的另一主要原因。
工具的磨损会导致切削力的不稳定和工件加工尺寸的变化。
刀具固定误差则会造成刀具的姿态变化,进而影响加工质量。
为了准确分析和校正这些误差,我们可以通过实时监测刀具磨损和固定状态,并使用自适应控制算法对其进行调整和补偿。
最后,切削力导致的变形误差也是数控机床加工精度误差中不可忽视的因素。
切削力会导致机床结构的变形,从而影响工件的加工精度。
为了准确评估和校正这种误差,我们可以通过应变测量、力传感器等方式实时监测和测量机床的结构变形情况,并使用补偿算法对其进行调整。
总结来说,数控机床的加工精度误差分析与校正是确保产品质量和工艺精度的关键步骤。
在这个过程中,我们需要准确地识别和分析加工精度误差的来源,并采取相应的校正措施。
- 1、下载文档前请自行甄别文档内容的完整性,平台不提供额外的编辑、内容补充、找答案等附加服务。
- 2、"仅部分预览"的文档,不可在线预览部分如存在完整性等问题,可反馈申请退款(可完整预览的文档不适用该条件!)。
- 3、如文档侵犯您的权益,请联系客服反馈,我们会尽快为您处理(人工客服工作时间:9:00-18:30)。
机床反向间隙大、定位精度差 位置环增益设定不当
4
5 6
各插补轴的检测增益设定不良
感应同步器或旋转变压器的接口板调整不 良 丝杠间隙或传动系统间隙
调整检测增益
重新调整接口板 调整间隙或改变间隙补偿 值
数控机床振荡故障分析与处理
案例分析
一
故障现象:一台配套 DYNAPATH 20M 系统的二手数 控铣床,加工零件时的Y向加工尺寸与编程尺寸存在较大 的误差,而且误差值与Y轴的移动距离成正比,距离越长, 误差越大。 分析及处理过程:为了进一步确认故障原因,维修时 对机床 Y轴的定位精度进行了仔细测量。测量后发现, 机床Y轴每移动一个螺距,实际移动距离均要相差 0.1mm 左右,而且具有固定的规律。 根据故障现象,机床存在 以上问题的原因似乎与系统的参数设定有关,即:系统 的指令倍率、检测倍率、反馈脉冲数等参数设定错误, 是产生以上故障的常见原因。但在本机床上,由于机床 参数被存储于EPROM上,因此参数出错的可能性较小。
数控机床常见故障诊断与排除
数控机床误差过大故障的分析与处理
数控机床误差过大故障分析与处理
一
定位超调故障的分析与处理
可能原因 加减速时间 设定不当 位置环比例 增益设置不 当
速度环比例 增益设置不 当 速度环积分 时间设置不 当
检查步骤 依次检查数控装置 或伺服驱动器上的 这几个参数的设置 是否与说明书要求 相同
热爱学习,勤于思考,善于发现,敢于实践
THANKS
省级精品在线开放课程
敬请指大故障分析与处理
项目 超调 1 2 单脉 1 冲精 度差 2 故障原因 加/减速时间设定过小 与机床的连接部分刚性差或连接不牢固 需要根据不同情况进行故障分析 机械传动系统存在爬行或松动
一 加工误差过大故障的分析与处理
检查步骤 检测起、制动电流是否已经饱和 检查故障是否可以通过减小位置 环增益改善 检查定位时位置跟随误差是否正 确 检查机械部件的安装精度与定位 精度 调整速度控制单元扮傻姑娘的相 应旋钮,提高速度环增益 检查定位是位置跟随误差是否正 确 检查机械部件的安装精度与定位 精度 更换位置控制单元板(主板) 检测位置检测器件(编码器、光 栅) 测量不圆度,检查周向上是否变 形,45°方向上是否成椭圆 测量各轴的定位精度与反向间隙 调整控制单元,使同样的进给速 度下各插补轴的位置跟随误差的 差值在±1%以内 在项目3调整后,在45°上成椭圆 检查接口板的调整 测量、重新调整间隙 措施 延长加/减速时间设定 减小位置环增益或提高机 床的刚性 若正确,见第2项,否则 第3项 调整机床机械传动系统
数控机床振荡故障分析与处理
案例分析
一
分析及处理过程:进一步观察、测量机床Y 轴移动情况, 发现该机床 Y 轴伺服在移动到某一固定角度时,都有一冲 击过程:在无冲击的区域,测量实际移动距离与指令值相符, 根据以上现象,初步判定,故障原因与位置检测系统有关。 因该机床采用的是半闭环系统,维修时拆下了伺服内装 式编码器检查,经仔细观察发现,在冲击的区域,编码器动 光栅上有一明显的黑斑。 考虑到更换编码器的成本与时间问题,维修时对编码器 进行了仔细的清洗,洗去了由于轴承润滑脂融化产生的黑斑。 重新安装编码器后,机床可以正常工作,Y 轴冲击现象消失, 精度恢复。
3
定位 1 精度 不良 2 3 4 5 圆弧 1 插补 加工 的圆 2 度差 3
伺服系统的增益不足
需根据不同情况进行故障分析 机械传动系统存在爬行或松动 位置控制单元不良 位置检测器件(编码器、光栅)不良 速度控制单元控制板不良 需根据不同情况进行故障分析
提高位置环、速度环增益
若正确,见第2项,否则 第3项 调整机床机械传动系统 更换不良板 更换不良位置检测期间 (编码器、光栅) 维修、更换不良板 若轴向变形,则见第2项, 若45°方向上成椭圆,则 见第3项 调整机床,进行定位精度、 反向间隙的补偿 调整位置环增益以消除各 轴间的增益差