塑料齿轮的成型缺陷分析与对策
对塑料齿轮的成型及缺陷的探讨
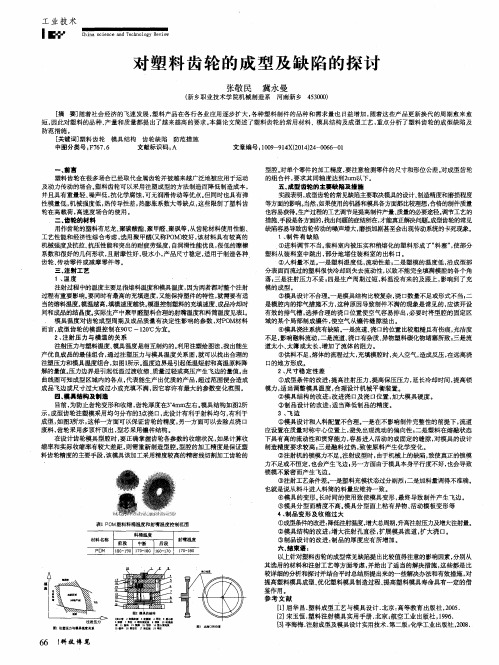
分表面而流过的塑料很快冷却到失去流动性, 以致不能完全填满模腔的各个角 落, 三是 注射压 力不 妥 , 四是 生产周 期过 短 , 料温 没有 来的及 跟上 , 影p i l a u 了充 模 的成型 。 ③模具设计 不合理 。 一是 模具结 构 比较复 杂 , 浇 口数量 不足或形 式不 当 。 二 是模 腔 内的排气 措施 不力 , 这种 原 因导致 制件不 满 的现象 是常见 的 , 应该 开设 有效 的排气 槽 , 选择 合理 的浇 口位置使 空 气容易 排 出, 必 要时将 型腔 的 固定 区 域 的某个 局部 制成镶 件 , 使 空气 从镶 件缝 隙溢 出 。 ④模具浇注系统有缺陷。 一是流道、 浇口的位置比较粗糙且有伤痕, 光洁度 不足, 影响融料流动 , 二是流道、 浇口有杂质、 异物塑料碳化物堵塞所致 , 三是流 道 太小 、 太簿 或太 长 , 增 加 了流 体 的阻力 。 ⑤供料不足 , 熔体的流程过大, 充填模腔时, 夹人空气, 造成反压 , 在远离浇 口的地 方 形成 。
注射过程中的温度主要足指熔料温度和模具温度, 因为两者都对整个注射 过程有重要影响。 要同时有最高的充填速度, 又能保持塑件的特性, 就需要有适 当 的熔 料温度 。 模温越高 , 填 模速 度趱 陕 模 温控制塑料 的充填速度 、 成品冷 却时 间和成品的结晶度。 实际生产 中聚甲醛塑料合理的射嘴温度和料筒温度见表1 。 模具温度对齿轮成型周期及成品质量有决定性影响的参数, 对P O M材料 而言 , 成型 齿轮 的模 温控 制在 9 0 " C~l 2 0 ℃为 宜。 2 、 注射 压 力 与模 温 的关 系 注 射压力与 塑料温度 、 模具 温度是相 互制约 的。 利用注塑绘 图法 , 找 出能 生 产优 良成品的最佳组合, 通过注塑压力与模具温度关系图, 就可以找出合理的 注塑压力和模具温度组合, 如 图1 所示。 温度边界是引起低温短射和高温原料降 解的量值。 压力边界是引起低温过渡收缩、 质量过轻或高压产生飞边的量值。 由 曲线图可知成型区域内的各点, 代表能生产出优质的产品, 超过范围便会造成 成品飞边或尺寸过大或过小或充填不满 , 因它容许有最大的参数变化范围 四, 模 具结 构及 制造 目前, 为防止齿轮变形和收缩 , 齿轮厚度在3 " 4 mm ̄右。 模具结构如图2 所 示, 成型齿 轮 注塑模 采用均 匀分 布的 3 点浇 口, 此 设计 有利于 射料 均匀 , 有 利于 成型, 如 图3 所示 , 这 样一 方面 可 以保 证齿 轮的精 度 , 另一 方面可 以去 除点浇 口 废料, 齿 轮采 用多 顶杆 顶 出 , 型 芯 采用镶 件结 构 。 在设计齿轮模具型腔时, 要正确掌握齿轮各参数的收缩状况, 如果计算收 缩 率和 实 际收缩率 有较 大差 距 , 则需重 新制 造型腔 。 型 腔 的加工精 度是保 证 塑 料齿轮精度的主要手段, 该模具该加工采用精度较高的精密线切割加工齿轮的
塑料件缺陷原因及改进方法
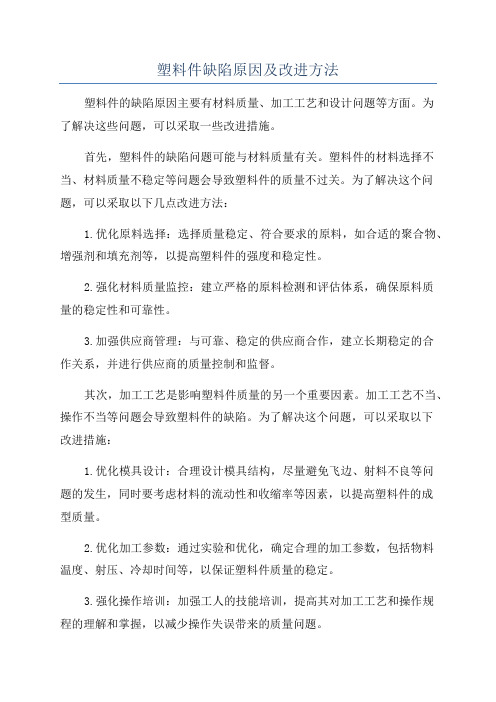
塑料件缺陷原因及改进方法塑料件的缺陷原因主要有材料质量、加工工艺和设计问题等方面。
为了解决这些问题,可以采取一些改进措施。
首先,塑料件的缺陷问题可能与材料质量有关。
塑料件的材料选择不当、材料质量不稳定等问题会导致塑料件的质量不过关。
为了解决这个问题,可以采取以下几点改进方法:1.优化原料选择:选择质量稳定、符合要求的原料,如合适的聚合物、增强剂和填充剂等,以提高塑料件的强度和稳定性。
2.强化材料质量监控:建立严格的原料检测和评估体系,确保原料质量的稳定性和可靠性。
3.加强供应商管理:与可靠、稳定的供应商合作,建立长期稳定的合作关系,并进行供应商的质量控制和监督。
其次,加工工艺是影响塑料件质量的另一个重要因素。
加工工艺不当、操作不当等问题会导致塑料件的缺陷。
为了解决这个问题,可以采取以下改进措施:1.优化模具设计:合理设计模具结构,尽量避免飞边、射料不良等问题的发生,同时要考虑材料的流动性和收缩率等因素,以提高塑料件的成型质量。
2.优化加工参数:通过实验和优化,确定合理的加工参数,包括物料温度、射压、冷却时间等,以保证塑料件质量的稳定。
3.强化操作培训:加强工人的技能培训,提高其对加工工艺和操作规程的理解和掌握,以减少操作失误带来的质量问题。
此外,塑料件的设计问题也会导致质量缺陷。
设计不当、结构不合理等问题会影响塑料件的使用寿命和功能。
1.优化产品设计:在设计阶段就要充分考虑材料特性、工艺要求和使用环境等因素,合理确定塑料件的结构和尺寸,以提高产品的可靠性和使用寿命。
2.强化模拟分析:通过使用CAD、CAE等软件工具进行模拟分析,预测设计在使用过程中的变形、应力分布等问题,在设计阶段就可以进行修正和优化。
3.进行实际测试:在设计验证阶段进行实际测试,包括强度测试、耐久性测试等,以验证设计的合理性和可靠性。
综上所述,塑料件的缺陷问题可能与材料质量、加工工艺和设计问题有关。
通过优化原料选择、加强材料质量监控、优化模具设计、优化加工参数、强化操作培训、优化产品设计、强化模拟分析和进行实际测试等改进方法,可以有效解决这些问题,提高塑料件的质量和可靠性。
塑胶件常见成型缺陷及改善策略
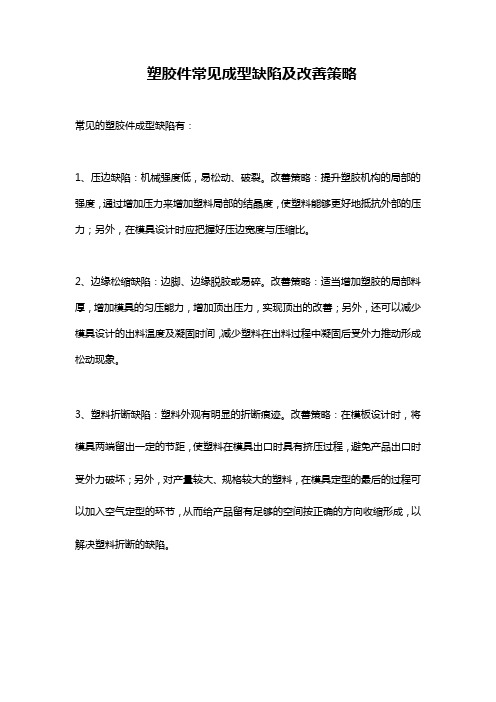
塑胶件常见成型缺陷及改善策略
常见的塑胶件成型缺陷有:
1、压边缺陷:机械强度低,易松动、破裂。
改善策略:提升塑胶机构的局部的强度,通过增加压力来增加塑料局部的结晶度,使塑料能够更好地抵抗外部的压力;另外,在模具设计时应把握好压边宽度与压缩比。
2、边缘松缩缺陷:边脚、边缘脱胶或易碎。
改善策略:适当增加塑胶的局部料厚,增加模具的匀压能力,增加顶出压力,实现顶出的改善;另外,还可以减少模具设计的出料温度及凝固时间,减少塑料在出料过程中凝固后受外力推动形成松动现象。
3、塑料折断缺陷:塑料外观有明显的折断痕迹。
改善策略:在模板设计时,将模具两端留出一定的节距,使塑料在模具出口时具有挤压过程,避免产品出口时受外力破坏;另外,对产量较大、规格较大的塑料,在模具定型的最后的过程可以加入空气定型的环节,从而给产品留有足够的空间按正确的方向收缩形成,以解决塑料折断的缺陷。
塑料齿轮变形解决方案

塑料齿轮变形解决方案
塑料齿轮变形是指在使用过程中,由于受到力的作用,齿轮的形状发生改变而造成的问题。
塑料齿轮变形的原因有很多,比如长时间受力、工作温度过高、挤压变形等。
针对这些问题,可以采取以下解决方案:
1. 选择合适的材料:选择适合工作环境的塑料材料,比如耐高温的尼龙材料或者耐腐蚀的聚四氟乙烯材料。
这样可以减少塑料齿轮受热或受化学物质侵蚀而变形的风险。
2. 加强结构设计:在齿轮的结构设计时要考虑到承受的力的大小和方向,合理设计齿轮的齿形和齿向,以提高其承载能力和抗变形能力。
同时,在齿轮的中心部位加强加固,以增加其稳定性。
3. 增加冷却系统:对于高温环境下的塑料齿轮,可以设置冷却系统,通过循环冷却水或者风扇等方式,将齿轮表面的温度降低,以减少塑料材料膨胀和变形的可能性。
4. 控制生产工艺:在生产过程中,对于塑料齿轮的成型温度和冷却时间等参数进行严格控制,以保证齿轮的尺寸和形状的稳定性。
同时,进行质量检测,对于变形严重的齿轮进行淘汰,以减少在使用过程中的问题。
5. 使用补强材料:在塑料齿轮的设计和生产过程中,可以添加一定量的增强材料,如玻璃纤维,以提高齿轮的强度和抗变形能力。
6. 修复和更换:对于已经变形的塑料齿轮,可以尝试进行修复,采用热塑性方法使其恢复原状。
但对于严重变形的齿轮,需要及时更换,以避免影响机械设备的正常运行。
总之,针对塑料齿轮变形问题,需要从材料选择、结构设计、生产工艺和维护等多个方面进行综合考虑和解决。
通过合理的设计和控制,可以降低塑料齿轮变形的发生率,提高其使用寿命和稳定性。
塑件缺陷原因及改善方法

塑件缺陷原因及改善方法塑件是一种常见的工程材料,广泛应用于汽车、家电、电子、医疗设备等领域。
然而,在塑件生产过程中,常常会出现一些缺陷,如气泡、毛刺、热缩、变形等问题,这些缺陷会影响塑件的质量和性能。
因此,了解塑件缺陷的原因,并采取相应的改善方法,对于提高塑件质量和性能具有重要意义。
首先,塑件缺陷的原因有多种,下面是一些常见的原因及相应的改善方法:1.气泡:气泡是塑件生产过程中常见的缺陷,通常是由于原料中含有挥发性成分,或者模具中有气体积聚引起的。
改善方法包括:使用质量稳定的原料,避免使用含有挥发性成分的原料;在塑件生产过程中提高注塑压力,减少气泡的生成;对模具进行定期维护,清除模具中的积聚气体。
2.毛刺:毛刺是塑件表面出现的细小突起,通常是由于模具不平整或模具开合不良引起的。
改善方法包括:对模具进行定期检修和研磨,保持模具的平整度;调整模具开合速度和压力,使开合动作更加平稳;在设计模具时考虑减少毛刺的生成。
3.热缩:塑件在冷却后会发生热缩现象,导致尺寸变小。
这是由于塑料在冷却过程中会收缩引起的。
改善方法包括:在设计模具时考虑塑件的热缩率,合理设置模具尺寸,使得塑件在冷却后能得到正确的尺寸;控制注塑过程中的冷却时间和温度,避免过快或过慢的冷却导致过大的热缩。
4.变形:塑件在注塑过程中可能会发生变形,导致尺寸不准确或形状失真。
这是由于塑料在注塑过程中由于内应力不平衡引起的。
改善方法包括:优化模具设计,使模具在注塑过程中能够充分填充塑料,并保持良好的冷却效果;控制注塑过程的温度、压力和速度,减少内应力的释放。
此外,还有一些其他常见的塑件缺陷,如熔流线、白斑、开裂等。
这些缺陷的原因和改善方法也各不相同,需要具体问题具体分析。
总的来说,塑件缺陷的原因多种多样,通过针对不同的原因采取相应的改善方法,能够有效地提高塑件的质量和性能。
对于塑件生产企业来说,建立完善的质量控制体系,加强原材料的筛选和控制,定期维护和检修模具,改进注塑工艺,都是改善塑件质量和性能的重要措施。
塑胶产品成型常见的品质缺陷产生的原因及改善的办法

塑膠產品成型常見的品質缺陷產生的原因及改善的辦法:缺陷定義產生的原因改善辦法縮水產品成型硬化,在產品表面形成保壓,保壓時間不夠,射出壓力小,溫度加大保壓和射出壓力,延長保凹現象過高,冷卻時產短,模具本身設計上的缺壓和冷卻的時間,增加膠量,降陷,(產品骨位較厚),膠量不夠.低模溫,改善模具.披鋒又稱毛邊,產品成型後在產品的射出壓;力過大,模溫過高,膠量過多,鎖減少射出壓力,降低模溫,減少分型面,PL面多出的部分.模壓力夠,材料的流通強,模具質量差或膠量,重設鎖模壓力,改善模具.老化.頂白/產品成型時在產品頂針對應面頂高上的發白,凸起的現象.產品脫模不順,射壓,保壓過大,頂針過修正棋具,減少射出和保壓,調長,頂針頂出壓力大,冷卻時間不夠,模校頂針頂出的壓力和長度,降低溫高,模溫.氣紋產品的表面,水口處形成与產品射膠速度過大,模具存在著排气不良的降低射膠速度,改善模具排氣結顏色,光澤不一致的現象(非混色).波紋產品表面波浪狀品質不良射膠速度小,模溫度低,材料的流通性差,電熱壞,或是有個別水品堵死.衝花/產品表面水口處或其它部位銀料花色放射狀,起泡狀的白色不良現象.夾水線又叫結合線,熔接線,塑膠成型跡.光影產品表面閃亮發白不良缺陷.混色產品表面局部顏色與其整體產品顏色異常.缺膠產品成型時填充不足材質不良,模溫過高,壓力過大,模具結改善材質,降低模溫,減小壓力.構(膠位較薄).混有其它材料,電熱溫度失控,使材質發檢查電熱溫度,清洗炮筒.生變化,料筒清洗不徹底.射膠時間,壓力不夠,膠量不夠,模溫低,延長射膠地間,增加射出壓力,模設計上存在缺陷,水口堵塞,材料流動加大射出膠量,升高模溫,改善性產.氣泡產品成型後,產品內有氣體存在材料未干燥,射出速度過快.未排出(多發生透明鉸片)燒燋產品骨位或邊緣有燒黑,發白,模具排氣不良,射膠速度過快.模具,.調整焗料溫度,焗料時間調整射出速度.改善模具排氣結構,降低射出速度.膠渣,吸附在模腔內.的擠壓.具進行異物清除,.後使產品平放冷卻後包裝,使合理包裝方式.射壓射速低,模具溫度低,材質流通性增加射出壓力,射出速度,提高模具溫度,改善模具進水結構.在型腔內流通結合的,熔接的痕差,模具設計存在缺陷.材料未干燥,射膠速度大.調整焗料溫度和時間,增大射膠速度.改變射膠速度,模溫,改善材質.缺陷.構.困氣發亮甚至碳化的現象.在產品表面.曲等形變.冷膠又稱膠屎,產品成型時羿物包含模腔內有異物,一般是產品拖出的膠粉,修正模具,增設風槍開模時對模變形指產品與原有形狀發生彎曲,扭冷卻時間,壓力,保壓有關,或其機械性調整冷卻時間,壓力,保壓,啤塑。
塑料制品缺陷及改善措施
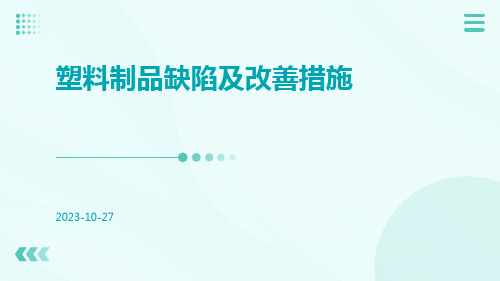
产生原因与危害
产生原因
塑料制品缺陷的产生原因很多,包括原材料质量不好、配方不合理、加工工 艺不当、设备故障、操作失误等。
危害
塑料制品缺陷会严重影响产品的质量、性能和外观,降低产品的使用价值和 寿命,甚至会对人体健康和安全造成威胁。
银纹
银纹是由于塑料在填充过程中混入的空气没有及 时排出而形成的,类似于气泡的一种缺陷。
银纹的产生可能是由于注射压力不足、注射速度 过快、模具温度不当等原因造成的。
银纹通常在塑料制品的表面或内部出现,形状为 细小的条状或网状。
改善措施:可以通过调整注射压力、注射速度和 模具温度来减少银纹的产生。在生产过程中,也 可以通过使用真空装置来帮助排出空气,从而避 免银纹的产生
VS
提高模具制造精度
采用高精度的数控机床等加工设备,提高 模具的制造精度,以减少制品缺陷。
调整生产工艺
优化注塑工艺
根据不同的塑料材料和制品要求,调整注 塑温度、压力和时间等工艺参数,以获得 理想的制品质量。
研究生产工艺优化方案
通过对生产工艺的研究和试验,找出最佳 的生产工艺参数,提高制品的质量和稳定 性。
裂纹
裂纹是由于塑料制品在冷却过程中产生的内应力 超过了塑料的抗拉强度而形成的。
裂纹的产生可能是由于注射速度过快、模具温度 过低、塑料的流动性差等原因造成的。
裂纹通常出现在塑料制品的表面或内部,形状为 线形或网状。
改善措施:可以通过降低注射速度、提高模具温 度、改善塑料的流动性来减少裂纹的产生。另外 ,可以通过调整塑料的配方,加入增韧剂等改性 剂来提高塑料的抗拉强度,从而减少裂纹的产生
塑料传动齿轮的成型缺陷分析与对策
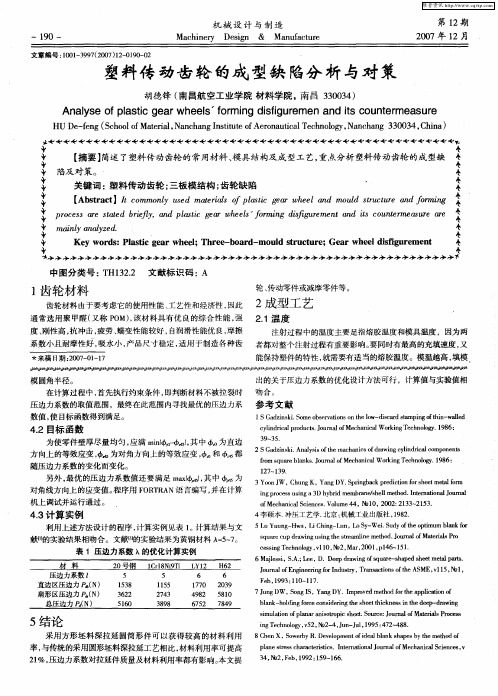
关 键词 : 塑料 传 动齿轮 ; 三板模 结构 ; 齿轮 缺 陷
毒
【 bt c】 o m n sd m t iso l t erw el n o l sut eadfr i A s at h cm ol u a r l fpa i ga he adm u t c r n m n r y e e a sc d r u o g
通 常选 用聚 甲醛 ( 又称 P M)该材料 具有优 良的综 合性 能 , O , 强 21温度 .
系数小且耐摩性好 , 吸水小 , 品尺寸稳定 , 产 适用 于制造各 种齿 者都对整个注射过程有重要影响。 同时有最 高的充填速度 , 要 又
★ 来稿 1 :0 7 0 — 7 3 2 0 — 1 1 期
为使零件壁厚 尽量均匀 , 满 mn S 应 ir ̄ o q l 中 为直边 , 其
c l d cl rd csJ u n f c a c okn c n lg . 9 6: yi r a o u t.o ra o Me h nia W rigTe h ooy 1 8 ni p l l
ma l ay i y a lz n
、 r
Ke r s P a tc g a e l Th e - o r - o l t u t r ; a e ld s g r me t y wo d : l s i e r wh e ; r e b a d m u d sr c u e Ge r wh e if u e n i
能保持塑件的特性 , 就需要有适 当的熔胶温度。模温越高 , 填模 出的关于压边力系数 的优化设计 方法可行 ,计算值与实验值相
模 圆角半径。
在计算 过程 中, 首先执行约束条件 , 即判断材料不被拉裂时 吻合 。
- 1、下载文档前请自行甄别文档内容的完整性,平台不提供额外的编辑、内容补充、找答案等附加服务。
- 2、"仅部分预览"的文档,不可在线预览部分如存在完整性等问题,可反馈申请退款(可完整预览的文档不适用该条件!)。
- 3、如文档侵犯您的权益,请联系客服反馈,我们会尽快为您处理(人工客服工作时间:9:00-18:30)。
塑料齿轮的成型缺陷分析与对策
1 前言
塑料齿轮由于它的质轻、价廉,传动噪声小,不需后加工,生产工序少,又因其强度和刚度接近于金属材料,可以代替有色金属和合金,因此,它在工业上的应用正在逐步扩大,现已广泛应用于机械、仪表,电讯、家用电器、玩具产品和各种记时装置中。
由于成型塑料齿轮的模具有其特殊性,因而塑料齿轮形成了一种特殊类型的注射模。
2 齿轮材料
齿轮材料纤综合考虑使用性能、工艺性能和经济性,选用聚甲醛(又称POM),该材料具有优异的综合性能,强度、刚性高,抗冲击,疲劳、蠕变性能较好,自润滑性能优良,摩擦系数小且耐摩性好,吸水小,产品尺寸稳定,适用于制造各种齿轮、传动零件或减摩零件等。
3 注射工艺
3.1 温度
注射过程中的温度主要足指熔胶温度和模具温度,因为两者都对整个注射过程有重要影响。
要同时有最高的充填速度,又能保持塑件的特性,就需要有适当的熔胶温度。
模温越高,填模速度越快。
模温控制塑料的充填速度、成品冷却时间和成品的结晶度。
实际生产中聚甲醛塑料合理的喷嘴温度和料筒见表1。
模具温度对齿轮成型周期及成品质量(如应力、系数率、尺寸公左、机械性能等)有决定性影响的参数,对POM材料而言,成型齿轮的模温控制范围为90度C~120度C。
3.2 注射压力与模温的关系
注射压力对塑料充填起决定性作用,而注塑压力与塑料温度、模具温度又是相互制约的。
利用注塑绘图法,找出能止产优良成品的最佳参数组合,通过射胶压力与模具温度关系图,就可以找出合理的射胶压力和模具温度组合,如图1所示。
由曲线图可知,ABCD范围内的各点,代表能生产优质产品的压力和棋具温度组合。
超过CD曲线便会造成成品飞边或尺寸过大;低于AB曲线会造成成品尺寸过小或充填不满,最佳的组合在X点,因它容许有最大的参数变化范围。
4 模具结构及制造
目前,大多数注射成型齿轮的模数在lun以下,为防止齿轮变形和收缩,齿轮厚
度在2~3mm左右。
模具结构如图2所示,成型齿轮注塑模采用均匀分布的3
点浇门如图3所示,这样一方面町以保证齿轮的精度,另一方面可以去除点浇口废料。
齿轮采用顶杆顶出,型芯采用镶件结构。
在设计齿轮模具型腔时,要正确掌握齿轮各参数的收缩状况,如果计算收缩率和实际收缩率有较大差距,则需重新制造型腔。
型腔的加工精度是保证塑判齿轮精度的主要手段,该模具采用加工精度较高的精密线切割加工齿轮的型腔。
对单个零件的加工精度,要注意检测零件的尺寸公左和形位公差。
对成型齿轮的组合件,要求其同轴度达到0.003mm。
5 成型齿轮的主要缺陷及对策
生产实践表明,成型齿轮的缺陷主要在于模具的设计、制造精度和磨损程度等方面,刘于较成熟的塑料工厂,如果使用的注射机和模具在各方面比较理想,容易获得合格的制件质量。
生产过程的工艺调节是提高制件产量、质量的必要途径。
调节工艺的措施、手段是各方面的,找出问题的症结所在,才能真正解决问题。
成型齿轮的缺陷容易导致齿乾传动的噪声、磨损加剧、效率降低甚至传动系统的卡死现象。
下面就成型齿轮注射过程中产生主要缺陷的原因及刘策分述如下:
(1)制件不满。
制件不满就是制品没有完全成型,导致这种缺陷的上要原因有:
a.进料调节不当。
一是汁算装置调节得不正确;二是装料室内被压实和稍熔化的塑料形成了“料塞”,使部分塑料从装料室中跳出,部分地堵住装料室的出料口(柱塞不能椎到最前位置)。
b.射人模具中的料量太少。
一是塑料温度低,塑料流动性差;二是塑模的温度低,沿成型部分左面而流过的塑料很快冷却到失去流动性,以致不能完全填满模腔的各个角落;三是注射压力不妥;四是生产周期过短,料温来不及跟上,影响充模成型。
c.模具设计不合理。
一是模具本身结构复杂,浇口数目不足或形式不当;二是模腔内排气措施不力,这种原因导致制件不满的现象是屡见不鲜的,消除这种缺陷的设计应开设有效的排气孔道,选择合理的浇口位置使空气容易排腺,必要时将型腔的固气区域的某个局部制成镶件,使空气从镶件缝隙逸出。
d.模具浇注系统有缺陷。
一是流道太小、太簿或太长,增加了流体的阻力;二是流道、浇口有杂质、异物塑料炭化物堵塞所致;三足流道、浇口粗糙有伤痕,光洁度不足,影响物料流动。
(2)飞边。
飞边又称溢边、毛刺、披锋等,大多发生在摸具的分合位置上,导致该缺陷的主要原因有:
a.模具分型而精度差。
模具分型面上粘有凸出异物、活动模板变形曲翘等。
b,模具设计和人料配置不合理。
一是在不影响制件完整性前提下,流道应设置在质量对称中心上,避免出现偏向性流动;二是塑料在熔融状态下具有很高的流动性和贯穿能力,容易进入活动的或固定的缝隙,要求模具的设计制造精度较高。
c.注笛机的锁模力不足。
注射成型时,由于机械上的缺陷,致使真正的锁模力不足或不恒定,也会产生飞边;另一方面由于模具本身平行度不好,也会导致锁模不紧密而产生飞边。
d.注射工艺条件差。
一是塑料充模状态过分剧烈;二是加料量调得不准确。
也就是说从料斗进入料筒的料量应维持一致。