萃取设备中离心萃取机的技术要求
生物制药判断试题+答案

生物制药判断试题+答案一、判断题(共100题,每题1分,共100分)1、蒸发法是借蒸发除去部分溶剂,而使溶液达到过饱和的方法。
( )A、正确B、错误正确答案:A答案解析:蒸发法是借蒸发除去部分溶剂,而使溶液达到过饱和的方法。
2、萃取所选用的萃取剂密度与原溶剂的密度差异要小。
( )A、正确B、错误正确答案:B答案解析:萃取所选用的萃取剂密度与原溶剂的密度差异越大越好。
3、解析干燥阶段,系统的真空度和温度均较高,保持2~3h,除去升华阶段残留的吸附湿分。
( )A、正确B、错误正确答案:A4、洁净室是指需要对尘埃粒子及微生物含量进行控制的厂房A、正确B、错误正确答案:A5、预冻结速度过慢会形成小冰晶,晶格之间的空隙小,在升华时水蒸气不易排出,使升华速率降低,但产品颗粒细腻,具有较大的比表面积,产品的复原性较好。
( )A、正确B、错误正确答案:A答案解析:预冻结速度过快会形成小冰晶,晶格之间的空隙小,在升华时水蒸气不易排出,使升华速率降低,但产品颗粒细腻,具有较大的比表面积,产品的复原性较好。
6、过滤操作中被过滤介质截留的固体物质称为滤饼或滤渣。
A、正确B、错误正确答案:A答案解析:过滤操作中被过滤介质截留的固体物质称为滤饼或滤渣。
7、三角形坐标图,萃取相用字母R表示。
A、正确B、错误正确答案:B答案解析:三角形坐标图,萃取相用字母E表示,萃余相用字母R表示。
8、糖的变旋现象是指糖溶液放置后,旋光方向从右旋变成左旋或从左旋变成右旋A、正确B、错误正确答案:B9、当盐水溶液浓度高于共熔点浓度时,若温度降低至饱和曲线时,溶质结晶析出,而余下溶液的浓度沿饱和曲线下降,结晶温度也沿饱和曲线上升。
( )A、正确B、错误正确答案:B答案解析:当盐水溶液浓度高于共熔点浓度时,若温度降低至饱和曲线时,溶质结晶析出,而余下溶液的浓度沿饱和曲线下降,结晶温度也沿饱和曲线下降。
10、小试样品与中试样品所含结晶水或结晶溶媒具有相一致性。
生物制药设备之萃取及设备—溶剂萃取及设备
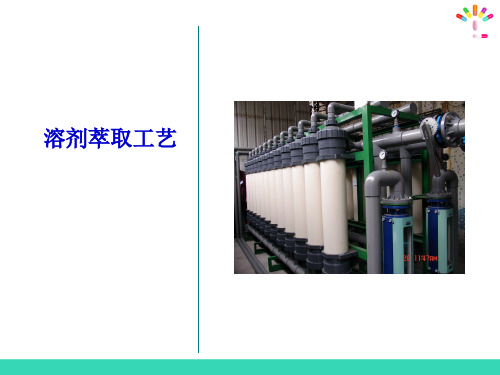
萃取分率
萃取过程完成后,组分在萃余液中的数量与原料液中总 数量的比值.
c2VF 1
c2VF c1VS K 1
组分的回收率
1 K
K m
在多次萃取过程中,每一次萃取都服从分配定律, 且每次萃取过程的分配系数都相同。
K K1 K 2 K n
所以,随着萃取次数的增加,残留在原料体系中的组分 越来越少,但无论进行多少次萃取,都不可能将组分从原 料体系中彻底萃取出来。
在双水相萃取中,PEG的回收采用盐溶蛋白质 和离子交换法,无机盐的回收采用结晶沉淀法进行。
溶剂萃取分离法
一、萃取基本知识 1.萃取过程
萃取: 两互不相溶的溶剂构成的非均相体系中,组分从一 相转移到另一相的过程。
萃取剂:转移组分的溶剂。 萃取液:萃取剂萃取组分后所得溶液。 萃余液:被萃取剂萃取后的溶液。
2.萃取原理 萃取推动力:遵守相似相溶原理,组分在两溶剂中溶解度之 差即为推动力,推动力越大萃取大越容易进行。
二、分配定律 在其他条件不变的情况下,萃取过程达到平衡后,萃
取液中溶质浓度与萃余液中溶质浓度的比值是常数,这个 规律叫分配定律。
萃取相组分浓度 K 萃余相c1VS c2VF
在错流萃取中,随着萃取的级数增加,萃取液中组 分总数量增多,溶剂体积逐级增大,萃取液中组分浓度 逐级降低。溶媒消耗量大,后续蒸发浓缩量大,但萃取 较完全。
三、多级逆流萃取
在多级逆流萃取中,在第一级加入原料液,在第 三级加入新鲜萃取剂。在第三级萃取后所得萃取液 作为萃取剂进入第二级,第一级的萃余液作为原料 液进入第二级,两股流体混合萃取后,所得萃余液 作为原料液进入第三级。而萃取液作为萃取剂进入 第一级,在第一级对原料液萃取后,所得萃取液被 送入贮罐贮存备用。
离心萃取机生产操作规程
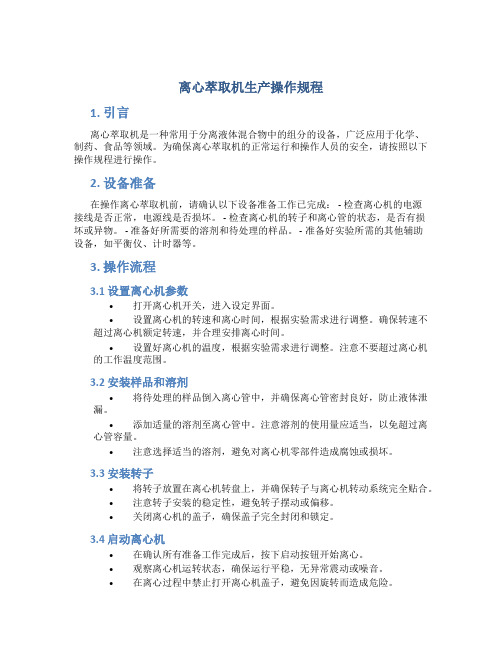
离心萃取机生产操作规程1. 引言离心萃取机是一种常用于分离液体混合物中的组分的设备,广泛应用于化学、制药、食品等领域。
为确保离心萃取机的正常运行和操作人员的安全,请按照以下操作规程进行操作。
2. 设备准备在操作离心萃取机前,请确认以下设备准备工作已完成: - 检查离心机的电源接线是否正常,电源线是否损坏。
- 检查离心机的转子和离心管的状态,是否有损坏或异物。
- 准备好所需要的溶剂和待处理的样品。
- 准备好实验所需的其他辅助设备,如平衡仪、计时器等。
3. 操作流程3.1 设置离心机参数•打开离心机开关,进入设定界面。
•设置离心机的转速和离心时间,根据实验需求进行调整。
确保转速不超过离心机额定转速,并合理安排离心时间。
•设置好离心机的温度,根据实验需求进行调整。
注意不要超过离心机的工作温度范围。
3.2 安装样品和溶剂•将待处理的样品倒入离心管中,并确保离心管密封良好,防止液体泄漏。
•添加适量的溶剂至离心管中。
注意溶剂的使用量应适当,以免超过离心管容量。
•注意选择适当的溶剂,避免对离心机零部件造成腐蚀或损坏。
3.3 安装转子•将转子放置在离心机转盘上,并确保转子与离心机转动系统完全贴合。
•注意转子安装的稳定性,避免转子摆动或偏移。
•关闭离心机的盖子,确保盖子完全封闭和锁定。
3.4 启动离心机•在确认所有准备工作完成后,按下启动按钮开始离心。
•观察离心机运转状态,确保运行平稳,无异常震动或噪音。
•在离心过程中禁止打开离心机盖子,避免因旋转而造成危险。
3.5 停止离心机•离心结束后,按下停止按钮,将离心机停止运转。
•等待离心机完全停止后,方可打开离心机盖子。
•注意离心管内可能存在的压力,小心打开离心管,避免喷溅或溢出。
4. 后续处理4.1 取出样品•谨慎取出离心管,并注意离心管外壁是否有液体残留。
如有残留,使用纸巾或棉签轻柔擦拭。
•将样品转移到其他容器中,根据实验需求进行后续处理。
4.2 清理离心机•关闭离心机电源,拔掉电源线。
萃取过程及设备

萃取是利用系统中组分在溶剂中有不同的溶解度来分离混合物的单元操作,利用相似相溶原理,萃取有两种方式:液-液萃取,用选定的溶剂分离液体混合物中某种组分,溶剂必须与被萃取的混合物液体不相溶,具有选择性的溶解能力,而且必须有好的热稳定性和化学稳定性,并有小的毒性和腐蚀性。
如用苯分离煤焦油中的酚;用有机溶剂分离石油馏分中的烯烃;用CCl4萃取水中的Br2.固-液萃取,也叫浸取,用溶剂分离固体混合物中的组分,如用水浸取甜菜中的糖类;用酒精浸取黄豆中的豆油以提高油产量;用水从中药中浸取有效成分以制取流浸膏叫“渗沥”或“浸沥”。
虽然萃取经常被用在化学试验中,但它的操作过程并不造成被萃取物质化学成分的改变(或说化学反应),所以萃取操作是一个物理过程。
萃取是有机化学实验室中用来提纯和纯化化合物的手段之一。
通过萃取,能从固体或液体混合物中提取出所需要的化合物。
用溶剂从液体混合物中提取其中某种组分的操作称为液/液萃取。
萃取是利用溶液中各组分在所选用的溶剂中溶解度的差异,使溶质进行液液传质,以达到分离均相液体混合物的操作。
萃取操作全过程可包括:1.原料液与萃取剂充分混合接触,完成溶质传质过程;2.萃取相和萃余相的分离过程;3.从萃取相和萃余相中回收萃取剂的过程。
通常用蒸馏方法回收。
现以提取含有A、B两组分的混合液中的A组分为例说明萃取操作过程。
选用一种适宜的溶剂S,这种溶剂对欲提取的组分A应有显著的溶解能力,而对其它组分B应是完全不溶或部分互溶(互溶度越小越好)。
所选用的溶剂S称为萃取剂。
待分离的混合液(含A+B)称为原料液,其中被提取的组分A称为溶质,另一组分B(原溶剂)称为稀释剂。
萃取过程的三个步骤:(1)首先将原料液(A+B)与适量的萃取剂S在混合器中充分混合。
由于B与S不互溶,混合器中存在S与(A+B)两个液相。
进行搅拌,造成很大的相界面,使两相充分接触,溶质A由原料液(稀释剂B)中经过相界面向萃取剂S中扩散。
萃取设备(离心萃取机)净化磷酸工业过程

萃取设备(离心萃取机)净化磷酸工业过程
磷酸的生产工艺可分为热法和湿法,热法是在高温下用焦炭还原磷矿石制成黄磷,而后再氧化成五氧化二磷经水吸收成磷酸,此法虽然产品质量好,但耗能高,已经为湿法取代,成为次要的生产方法。
萃取设备(离心萃取机)净化磷酸工业过程是湿法通过硫酸分解磷灰石而得到粗磷酸,粗酸除含20%-30%的P2O5外尚含有其他杂质,必须进一步净化才能满足不同用途的要求,使用沉淀法虽可以去除部分金属杂质,但不易获得高品质的产品。
萃取设备(离心萃取机)净化磷酸工业过程已成为纯化湿法冶金的重要技术。
CWL型萃取设备在磷酸精制中的应用包括两个方面的内容,一是从磷酸中萃取除去金属杂质,二是萃取磷酸与杂质分离,得到所期望纯度的产品。
直观演示7大萃取设备的结构和原理

直观演示7大萃取设备的结构和原理萃取(Extraction)是分离液体混合物的一种单元操作,依据液体混合物中各组分在溶剂中溶解度的差异分离液体混合物,俗称抽提。
萃取设备——离心萃取机————混合·沉降萃取器————脉冲筛板萃取塔————筛板萃取塔————填料萃取塔————往复筛板萃取塔————转盘筛板萃取塔——萃取设备简介萃取设备又称萃取器,其作用是实现两液相之间的质量传递。
对萃取设备的基本要求是使萃取系统的两液相之间能够充分混合、紧密接触并伴有较高程度的湍动;同时使传质后的萃取相与萃余相能够较完善的分开。
萃取设备的种类很多,按两相接触方式,可分为逐级接触式和连续接触式;按形成分散相的动力,可分为无外加能量与有外加能量两类,前者只依靠液体送入设备时的压力和两相密度差在重力作用下使液体分散,后者则依靠外加能量用不同的方式使液体分散;此外,根据两相逆流的动力不同,可分为重力作用和离心力作用两类。
常用的萃取塔型①转盘塔在工作段中,等距离安装一组环板,把工作段分隔成一系列小室,每室中心有一旋转的圆盘作为搅拌器。
这些圆盘安装在位于塔中心的主轴上,由塔外的机械装置带动旋转。
转盘塔结构简单,处理能力大,有相当高的分离效能,广泛应用于石油炼制工业和石油化工中。
②脉动塔在工作段中装置成组筛板(无溢流管的)或填料。
由脉动装置产生的脉动液流,通过管道引入塔底,使全塔液体作往复脉动。
脉动液流在筛板或填料间作高速相对运动产生涡流,促使液滴细碎和均布。
脉动塔能达到更高的分离效能,但处理量较小,常用于核燃料及稀有元素工厂。
③振动板塔将筛板连成串,由装于塔顶上方的机械装置带动,在垂直方向作往复运动,借此搅动液流,起着类似于脉动塔中的搅拌作用。
萃取塔设计主要是确定塔的直径和工作段高度。
先从液体流量除以操作速度,得出塔截面,算出塔径。
然后根据塔的特性以及物系性质和分离要求,确定传质单元高度和传质单元数,最后两者相乘即得塔的工作段高度。
萃取实验原理、要求
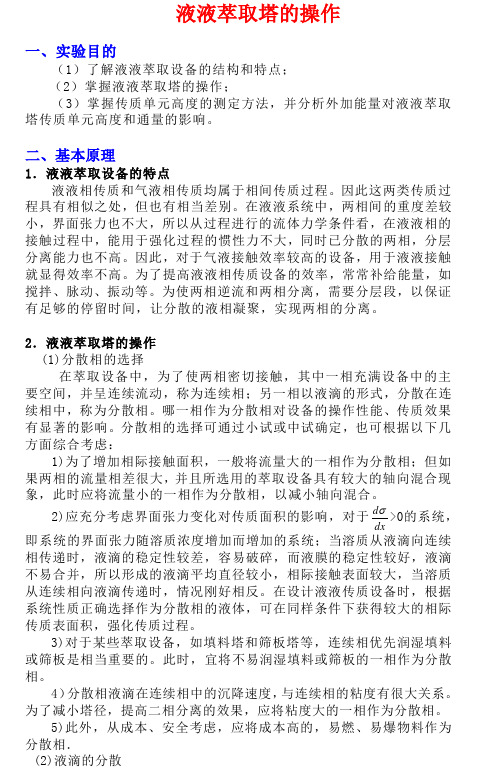
液滴的分散可以通过以下几个途径实现: A 借助喷嘴或孔板,如喷洒塔和筛孔塔。 B 借助塔内的填料,如填料塔。 C 借助外加能量,如转盘塔,振动塔,脉动塔,离心萃取器等。 液滴的尺寸除与物性有关外,主要决定于外加能量的大小。 (3)萃取塔的操作 萃取塔在开车时,应首先将连续相注满塔中,然后开启分散相,分 散相必须经凝聚后才能自塔内排出。因此当轻相作为分散相时,应使分 散相不断在塔顶分层段凝聚,当两相界面维持适当高度后,再开启分散 相 出 口 阀 门 ,并 依 靠 重 相 出 口 的 π 形 管 自 动 调 节 界 面 高 度 。当 重 相 作 为 分散相时,则分散相不断在塔底的分层段凝聚,两相界面应维持在塔底 分层段的某一位置上。
(2)液滴的分散
为了使其中一相作为分散相,必须将其分散为液滴的形式。一相液 体的分散,亦即液滴的形成,必须使液滴有一个适当的大小。因为液滴 的尺寸不仅关系到相际接触面积,而且影响传质系数和塔的流通量。
较小的液滴,固然相际接触面积较大,有利于传质;但是过小的液 滴,其内循环消失,液滴的行为趋于固体球,传质系数下降,对传质不 利。所以,液滴尺寸对传质的影响必须同时考虑这两方面的因素。
往复振动筛板塔外加能量大小的标志是振幅与振动频率的乘积。
5.液泛 在 连 续 逆 流 萃 取 操 作 中 ,萃 取 塔 的 通 量 (又 称 负 荷 )取 决 于 连 续 相 容
许的线速度,其上限为最小的分散相液滴处于相对静止状态时的连续相 流率。这时塔刚处于液泛点(即为液泛速度)。在实验操作中,连续相的 流速应在液泛速度以下。为此需要有可靠的液泛数据,一般这是在中试 设备中用实际物料做实验测得的。
萃取分离原理及设备介绍
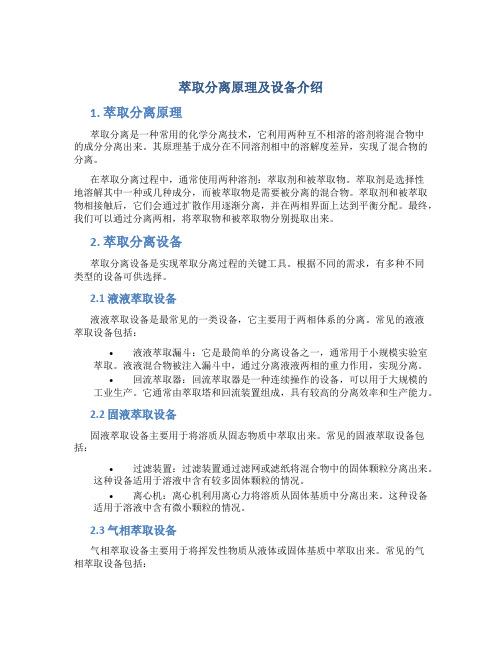
萃取分离原理及设备介绍1. 萃取分离原理萃取分离是一种常用的化学分离技术,它利用两种互不相溶的溶剂将混合物中的成分分离出来。
其原理基于成分在不同溶剂相中的溶解度差异,实现了混合物的分离。
在萃取分离过程中,通常使用两种溶剂:萃取剂和被萃取物。
萃取剂是选择性地溶解其中一种或几种成分,而被萃取物是需要被分离的混合物。
萃取剂和被萃取物相接触后,它们会通过扩散作用逐渐分离,并在两相界面上达到平衡分配。
最终,我们可以通过分离两相,将萃取物和被萃取物分别提取出来。
2. 萃取分离设备萃取分离设备是实现萃取分离过程的关键工具。
根据不同的需求,有多种不同类型的设备可供选择。
2.1 液液萃取设备液液萃取设备是最常见的一类设备,它主要用于两相体系的分离。
常见的液液萃取设备包括:•液液萃取漏斗:它是最简单的分离设备之一,通常用于小规模实验室萃取。
液液混合物被注入漏斗中,通过分离液液两相的重力作用,实现分离。
•回流萃取器:回流萃取器是一种连续操作的设备,可以用于大规模的工业生产。
它通常由萃取塔和回流装置组成,具有较高的分离效率和生产能力。
2.2 固液萃取设备固液萃取设备主要用于将溶质从固态物质中萃取出来。
常见的固液萃取设备包括:•过滤装置:过滤装置通过滤网或滤纸将混合物中的固体颗粒分离出来。
这种设备适用于溶液中含有较多固体颗粒的情况。
•离心机:离心机利用离心力将溶质从固体基质中分离出来。
这种设备适用于溶液中含有微小颗粒的情况。
2.3 气相萃取设备气相萃取设备主要用于将挥发性物质从液体或固体基质中萃取出来。
常见的气相萃取设备包括:•萃取头:萃取头是一种装有吸附材料的小型装置,用于从气体中吸附目标物质。
它常用于分析实验室中进行样品前处理。
•挥发性物质萃取器:这种设备通过加热产生蒸汽,将挥发性物质从基质中蒸馏出来。
蒸馏后的气体再通过冷凝器冷却并收集。
3. 萃取分离的应用萃取分离技术在化工、制药、环境保护等领域有着广泛的应用。
在化工领域,萃取分离常用于提纯化学品、回收溶剂和分离相互溶解的成分等。
- 1、下载文档前请自行甄别文档内容的完整性,平台不提供额外的编辑、内容补充、找答案等附加服务。
- 2、"仅部分预览"的文档,不可在线预览部分如存在完整性等问题,可反馈申请退款(可完整预览的文档不适用该条件!)。
- 3、如文档侵犯您的权益,请联系客服反馈,我们会尽快为您处理(人工客服工作时间:9:00-18:30)。
萃取设备中离心萃取机的技术要求
前言
萃取设备是一类用于萃取操作的传质设备,能够实现料液所含组分的完善分离。
萃取设备可按结构分为混合澄清器、萃取塔和离心萃取机。
下面我们主要从离心萃取
机的简介,性能要求,技术要求及外观质量方面说明离心萃取机的技术要求。
1.离心萃取机的简介
在离心力场中,利用液/液两相密度的不同,在同一机器中完成混合传质过程和分离过程,达到液/液两相萃取分离的连续萃取设备。
(简称“萃取机”)
在离心力场中先进行充分混合,使溶质的转移,再进行两相液体的分离和排出。
轻相液体从靠近转鼓壁处进料,重液相则从转鼓中心进料。
在转鼓内形成两相分散的
逆流接触。
最终两相达到转鼓另一端时轻重液相分别浓缩在转鼓中心和内壁处排出。
利用管式、多室式和碟片式离心机结构制成离心萃取机,充分地发挥了管式离心机分
离因数高、轴向长度大,适于处理密度差较小的两相液体,室式和碟片式离心机对两
相液体分散度高,接触面积大,停留时间长等特点,有利于萃取过程先使两相流分散
接触,再使两相流分别浓缩的工艺要求。
分别称为管式、室式和碟片式离心萃取机。
目前市面上最先进的离心萃取机为CWL-M型离心萃取机。
2.性能要求
2. 1 离心萃取机在额定工况下,转速应不低于额定转速的97%。
2. 2 离心萃取机在额定转速运行时,其空运转时振动速度应不大于4.5 mm/s,负荷运转时振动速度应不大于7.1 mm/s。
2. 3 离心萃取机在额定转速下,空运转时噪声(声压级)应不大于80 dB(A);负荷运转时噪声(声压级)应不大于85 dB(A)。
2. 4 离心萃取机主轴承温升:空运转时应不高于40℃;负荷运转时应不高于45℃。
2. 5 离心萃取机主轴承温度:空运转时应不高于75℃;负荷运转时应不高于80℃。
2. 6 离心萃取机最大通量应符合设计要求。
3.结构要求
3.1 离心萃取机应设置适合于整体吊装的起吊装置。
3.2 离心萃取机各密封部位应密封良好。
3.3 离心萃取机在结构上宜设置有调整轻重相界面的装置。
3.4易松动的螺栓连接部位应有防松装置。
3.5 用于制药、食品等行业的离心萃取机,结构上应符合相关规定。
4.外观质量
离心萃取机机壳表面不应有明显的锤痕和划伤,不锈钢机壳内表面应作钝化处理,外表面应光洁、平整。
离心萃取机非加工易锈表面应涂漆,涂漆质量应符合JB/T7217 的规定。
5.材料要求
5.1离心萃取机的材料应符合相关标准的规定,并有材料的质量证明书,如无质量证明书时,须经制造厂质量检验部门检验合格方可使用。
5.2离心萃取机主要零件的材料应符合设计要求,允许以质量相当或较优的材料代用,但须经设计部门同意。
5.3外购件应有供应商提供的合格证。
5.4铸钢件的铸造与验收应符合GB/T 2100 或GB/T 11352 和GB/T 14408 的规定。
5.5锻件的锻制和验收应符合JB/T 4385.1 的规定。
5.6用于食品、制药工业的离心萃取机采用的材料应符合相关行业的有关规定。
6.铸造要求
铸铁件和碳钢铸件需进行消除应力和改善金相组织的处理。
奥氏体不锈钢铸件需
进行固溶处理。
6.1焊接转鼓应符合下列规定:
6.1.1焊接接头的力学性能应不低于母材。
焊接试样的力学性能测定按JB 4744 的规定进行。
6.1.2每个转鼓的纵向焊接接头作100%的无损检测,环向焊接接头作20%的无损检测,并应符合JB/T9095 的规定。
6.1.3转鼓焊接接头的返修应符合GB19815 的规定。
6.2表面包衬或喷涂非金属材料的转鼓,其包衬或喷涂层表面应均匀平滑,不得有凸起、凹陷、气孔及裸露等缺陷。
6.3转鼓装配后,其径向圆跳动量应不大于0.001D(D为转鼓内径)。
6.4每台转鼓部件应先做静平衡,再做动平衡。
精度等级不低于6.3级,其允许剩余不平衡量和配重位置的确定应符合附录A 的规定。
6.5包衬或喷涂非金属材料的转鼓应在包衬或喷涂前后分别做动平衡。
6.6转鼓的平衡,允许做加重或去重处理。
加重或去重位置应在转鼓两端的边缘局部加厚区,衡重不得超过转鼓总重的1/1000。