5S推动实战过程通用版
现场5S实战技能精编版
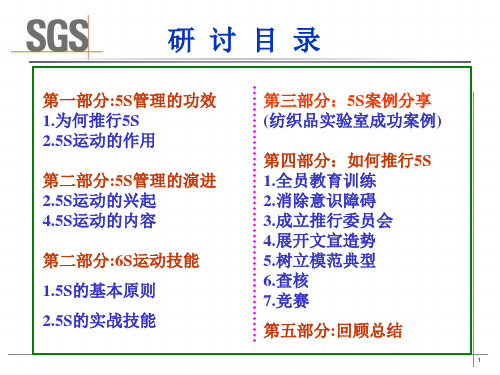
研 讨 目 录
第一部分:5S管理的功效1.为何推行5S2.5S运动的作用第二部分:5S管理的演进2.5S运动的兴起4.5S运动的内容第二部分:6S运动技能1.5S的基本原则2.5S的实战技能
第三部分:5S案例分享(纺织品实验室成功案例)第四部分:如何推行5S1.全员教育训练2.消除意识障碍3.成立推行委员会4.展开文宣造势5.树立模范典型6.查核7.竞赛第五部分:回顾总结
注意:猴子并不是剔光了毛就变成了人
5S运动的内容
安全(SAFETY)对使用,维修和与此有关的操作人员可能造成的危害或不安全状况,用行动消除隐患的不良安全因素发生。目的:◇操作协及安全者,防止不良事故发生; ◇“预防为主,防消结合” 保障公司机制人身安全; ◇居安要思危,安全工作要不懈的抓紧防火工作,做 到人人有责任的观念,认真对待落实安全防火工作 ◇保证防火设施完好无损,《谁主管,谁负责》。
成立委员会案例
上海纺织品实验室委员会
每周稽查两次,一次例会,每月由USD综合稽查一次并协助制定下阶段工作计划
如何推行5S
C.宣传培训
如何推行5S
D.制定查核表
查检表的使用有两种,一种是点检用,只记入好与不好的符号;另一种是记录用评鉴的数据。在推行7S活动的过程中,对于每一个要逐项均要定期检查,加以控制,透过查检表之定期检核,能得到进展情况,若有偏差,即可亮相随时纠正不良问题点。整理:通道状况,工作场所的设备、材料、办公桌(作业台)、物料架状况、仓库;整顿:设备、机器、仪器、工具、零件、图纸、作业标示书、文具档案清扫:通道、作业场所、办公桌(作业台)、窗、墙板、天花板、设备、工具、仪器;清洁:通道和作业区、地面、办公桌、会议室、洗手台、储物室;教养:日常“7S”活动、服装、仪表、行为规范、时间观念、作业标准、标准作业;安全:安全点检表、安全区域、专管制度职责;
5s现场管理推行的步骤

5s现场管理推行的步骤
5S现场管理可让工作环境大变样呢。
整理这一步呀,就像是给东西们来个大筛选。
把工作场所里的东西都翻出来瞅瞅,区分哪些是要用的,哪些是不要用的。
不要用的东西就别让它们在那占地方啦,该扔的扔,该送人的送人。
这就好比给屋子大扫除,把没用的杂物都清理掉,只留下有用的宝贝。
整顿紧随其后。
这就像是给留下来的有用东西安排个合适的家。
给每个东西都找个固定的位置,贴上小标签啥的,让大家一眼就能看到。
工具放哪儿,材料放哪儿,都清清楚楚的。
就像我们把衣服都整齐地放在衣柜里,不同的衣服有不同的格子,找的时候多方便呀。
清扫可不能马虎。
把工作场所里的脏东西都打扫干净,设备呀、地面呀都要亮晶晶的。
这不仅是为了好看,也是为了能及时发现设备有没有小毛病。
就像我们每天洗脸刷牙一样,把自己收拾得干干净净的,工作场所也得这样。
清洁是把前面三个S维持下去呢。
不能今天整理、整顿、清扫了,明天就又乱成一团。
要制定一些规则,大家都按照规则来做。
这就像是我们养成好习惯一样,不能三天打鱼两天晒网。
素养是5S的灵魂哦。
就是让每个员工都养成遵守前面4S的习惯,从心里就重视起来。
大家都自觉地去做,整个团队就变得超有秩序。
这就像是大家都有礼貌,都懂得爱护环境一样,整个氛围就特别好。
推行5S现场管理,一步一步来,每个环节都做到位,工作场所就会变得整洁又高效,大家工作起来也会更舒心呢。
5S推动实战过程

5S推动实战过程背景现代工业生产环境下,常常存在着工作场所混乱、生产工具随意堆放等问题,这些问题不仅会降低工作效率,增加生产成本,还会影响工作质量和安全。
如何管理和优化工作场所成为一个非常重要的问题。
在这个背景下,5S管理法应运而生。
5S管理法最初由古田康介在20世纪60年代提出,它是在日本企业中广泛应用的一种方法,意为整理、整顿、清扫、清洁、素养。
简称为5S,它主要是通过规范化管理的方式,使企业在生产中遵循一套标准的管理方式,达到提高效率、降低成本、提高质量、增强安全等目的。
本文将介绍5S推动实战的过程和方法。
步骤5S推动实战分为以下五个步骤:第一步:排序排序的目的是要把不必要的东西从工作区域中清除出去,留下的东西必须是有用的、被管理的、适当的。
在这一步骤中,需要做到以下几点:•按照现有的管理标准对设备、材料、工具等进行分类;•审查无用物资、垃圾和杂物,以便实施清除和清理工作;•对设备进行拍照或者其他的标记,以便随时查看资料。
整顿的主要目的是对设备、控制开关、维护记录簿以及其他员工财产进行标记和标注。
在这一步骤中,需要做到以下几点:•对设备上的图纸、内部抽屉、控制开关、配线等进行标注;•配置状态显示器,为设备进行分类标记,以表明是否工作、停机或者有异常状况;•对维护记录簿进行标记,以便业务员能够读出设备的工作状况。
第三步:清扫清扫是对设备及周围环境进行清洁清理和保养的过程。
清扫是整个5S推动实战的重要步骤,它的目的在于:•建立起清洁的工作环境,提高生产效率;•减少因误操作造成的设备损坏或者停机维修的情况,并延长设备的使用寿命。
第四步:清洁清洁是保持清洁和美化工作环境的过程。
在这一步骤中,需要做到以下几点:•清洁设备、维护处和生产区域;•维持设备周围的原料清洁;•保持设备在平整、美观的水平上。
素养是激励员工自觉遵守5S标准,持续推动工作改进,建立职业道德和自我修养的行为。
在这一步骤中,需要做到以下几点:•激励员工自觉遵守5S标准,保持工作环境的清洁和整洁;•激励员工秉持职业道德,遵守安全环保和人身安全的原则;•激励员工时常检视标准检查表,并向领导提出改进意见。
5S的做法以及推进步骤-实施5S的重要工具与目视管理示范

2. 整 顿
整顿技巧(1):划定场所
定位置、标识
分区划线
良品
通
道
待检品
不良品
2. 整 顿
整顿的技巧(2)—放置方法
定位置、标识
形迹管理
创造容易放 回去的状态
2. 整 顿
整顿的技巧(3)—放置方法
形迹管理
整顿技巧(4)---放置方法
定位置、标识
连接线标识
2. 整 顿
第三个5S:清扫
清扫的定义
对象:主要在通过持续不断的4S 活动中,提升员工道德品质及自身修养。
素养教育的开展方式
基本的礼仪行为规范培训 规定统一的服饰和标识识别系统 开展丰富多彩的文体活动 培养团队协作精神 员工行为准则:提升员工素养的基础 改善提案:参与现场改善,提升自主管理 形成习惯并且持续改善
素养形成的三个阶段: 形式化、行事化、习惯化
4)放置标识;
5)摆放整齐。
整顿的“三要素“ 放置场所:三定:定点、定容、定量 。 物品的放置场所原则上要100%设定。 生产线附近只能放真正需要的物品 。 放置方法: 三易:易见 易取 易还 。 不超出所规定的范围。 在放置方法上多下工夫。 标识方法: 放置场所和物品原则上一对一标识。 现物的表示和放置场所的标识 。 某些标识方法全公司要统一 。 在标识方法上多下工夫 。
急忙订货
糟糕!
寻找后没 有找到
订货
后来又找到
寻
好不容易
下班了
太多了!
找
找到了
不良品不能使用
数量不够
可惜!
立即找到 (寻找时间
为30S)
立即能使用
数量太多 合适
我最好!
第二个5S:整顿
办公室5S管理实战参考
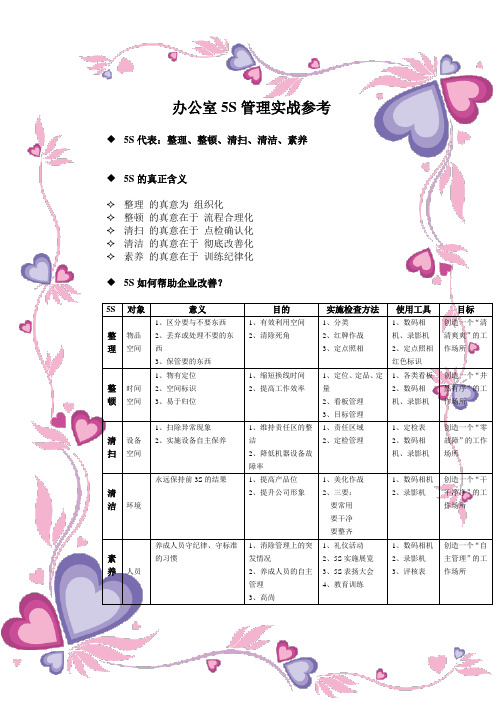
办公室5S管理实战参考◆5S代表:整理、整顿、清扫、清洁、素养◆5S的真正含义✧整理的真意为组织化✧整顿的真意在于流程合理化✧清扫的真意在于点检确认化✧清洁的真意在于彻底改善化✧素养的真意在于训练纪律化◆5S如何帮助企业改善?5S 对象意义目的实施检查方法使用工具目标整理物品空间1、区分要与不要东西2、丢弃或处理不要的东西3、保管要的东西1、有效利用空间2、清除死角1、分类2、红牌作战3、定点照相1、数码相机、录影机2、定点照相红色标识创造一个“清清爽爽”的工作场所整顿时间空间1、物有定位2、空间标识3、易于归位1、缩短换线时间2、提高工作效率1、定位、定品、定量2、看板管理3、目标管理1、各类看板2、数码相机、录影机创造一个“井然有序”的工作场所清扫设备空间1、扫除异常现象2、实施设备自主保养1、维持责任区的整洁2、降低机器设备故障率1、责任区域2、定检管理1、定检表2、数码相机、录影机创造一个“零故障”的工作场所清洁环境永远保持前3S的结果1、提高产品位2、提升公司形象1、美化作战2、三要:要常用要干净要整齐1、数码相机2、录影机创造一个“干干净净”的工作场所素养人员养成人员守纪律、守标准的习惯1、消除管理上的突发情况2、养成人员的自主管理3、高尚1、礼仪活动2、5S实施展览3、5S表扬大会4、教育训练1、数码相机2、录影机3、评核表创造一个“自主管理”的工作场所◆员工和管理人员在5S活动中的责任✧员工在5S活动中的责任1、自己的工作环境不断地整理、整顿,物品、物料及资料不可乱放2、不用的东西立即处理,不可使其占用作业空间3、通路必须经常维持清洁和畅通4、物品、工具及文具要放置于规定场所5、灭火器、开关箱、电动车机器设备等周围要时刻保持清洁6、物品、设备要仔细放、正确放、安全地放、较大较重的堆在下层7、保管的工具、设备及所负责的责任区要整理8、纸屑、材料屑等要集中于规定场所9、不断清扫,保持清洁10、注意上级的指示,并加以配合✧管理人员在5S重的责任1、配合公司政策全力支持与推行5S;2、参加有关5S的教育训练,吸收5S技巧;3、研读5S相关书籍,搜集广泛资料;4、部门内5S的宣导及参与公司5S文宣活动;5、规划部门内工作区域的整理、定位工作;6、依公司的5S进度表,全面做好整理、定位、划线标示的作业;7、协助部署克服5S的障碍与困难点;8、熟读“5S推行手册”并向部署解释;9、必要时,参与公司评分工作;10、5S评分缺点的改善和申述;11、督促所属执行定期的清扫点检;12、上班后的签到与服装仪容清查,下班前的安全巡查与确保。
5S推动实战过程_1
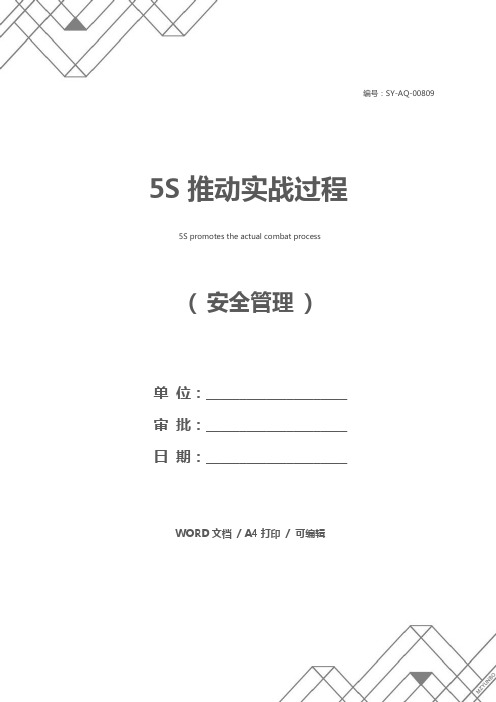
编号:SY-AQ-00809( 安全管理)单位:_____________________审批:_____________________日期:_____________________WORD文档/ A4打印/ 可编辑5S推动实战过程5S promotes the actual combat process5S推动实战过程导语:进行安全管理的目的是预防、消灭事故,防止或消除事故伤害,保护劳动者的安全与健康。
在安全管理的四项主要内容中,虽然都是为了达到安全管理的目的,但是对生产因素状态的控制,与安全管理目的关系更直接,显得更为突出。
日本的工厂向以整齐、清洁闻名于世,这都得感谢所谓5S的管理技巧,可以用来培养现场工人的良好工作习惯,5S运动背后所蕴含的理念是:整齐、清洁与纪律化的工作现场乃是制造高品质产品、杜绝量费,以及维持高生产能力的必要条件。
5S代表五个日本单字:SEIRI(整理)、SEITON(整顿)、SEISO (清扫)、SEIKETSU(标准)、以及SHITSUKE(教养),以下就是按步推行5S运动的简介。
推行中的5S在推行5S运动前,第一件事情就是先到工厂现场周围环境拍照存证,将来推行5S运动后,在拍照比较,可以立即看出推行的成效。
整理环境(Clearupthearea)。
在任何工厂里都有废弃或不需要的物品,这些物品目前生产用不着,应以红色标签区别,任何人见到都知道应予搬移或抛弃,不过,厂区应先确定不需要之标准以避免争端,然后指派第三者(通常为管理部门)着手上标签。
整理储藏所(Organizestorageplaces)。
环境清洁后,应再整理储藏所,并以文字或数字、颜色等明显标示各项物品存放位置,整理储藏所时,应牢记三个关键因素:何地(Where)、何物(What)、以及多少数量(HowMany),标示应清楚明白并易于识别,应采开放式储藏系统,否则各项工具不易保持整齐。
全面清扫(Consolidateclearingprocedure)。
5S活动的推进方法3精编版

改善後
在此場合、這是C-2
3.演練(3)QC検査(異混防止)
右邊是QC檢査工程的照片.從5S的觀點來看,應如何改善?
3.改善例(3)QC檢査(異混防止)
改善前
改善後
因為沒有做好整頓、物品與現品票有被錯換的可能。因此QC検査時LOT的判定可能會造成改變.又也有可能會造成製品的異混.
改善例(1)桌上只放著1個LOT.(2)其他LOT放入空盒內防止裝箱錯誤.(3)検査前、検査後的放置場所已明確化.
END
改善例:中高圧電容器(廈門)
10、你要做多大的事情,就该承受多大的压力。11、自己要先看得起自己,别人才会看得起你。12、这一秒不放弃,下一秒就会有希望。13、无论才能知识多么卓著,如果缺乏热情,则无异纸上画饼充饥,无补于事。14、我只是自己不放过自己而已,现在我不会再逼自己眷恋了。
谢谢大家
4.5S活動事例(4)
・不僅是作業區域、清掃用具的收藏放置內容及數量亦要明確化・裡面看不到的、櫃子等同樣的內.5S活動事例(6)
4.5S活動事例(7)
結語
5S活動並沒有結束。活動要持續不斷的去實施,且以5S活動為『製造物品』的基本,來進行再構築吧!
附録
如右側照片所顯示的現場。從5S的觀點來看,應如何改善?
3.演練(1)現場環境的改善
改善前
改善後
改善例(1)現場環境的再檢視改善
放置場所明確的規劃並標示設置完成。
沒有台車放置場所而任意放置,無法做好定位管理。.
某日、A君得到B君的指示.
從C-2的地方搬來 1 箱!!
A君可能會犯下什麼錯誤?
又,您認為應該如何改善?
5S活動向來被認為是『製造物品』 基本的要求,這是理所當然的事。但是,把理所當然的事情要理所當然的 去實行,卻是件困難的事。 本課程是要來學習5S活動的推進 方法。
5s现场管理的推行步骤

5S现场管理的推行步骤简介5S现场管理是一种以提高工作场所的整洁度、安全性和效率为目标的管理方法。
它通过整理、整顿、清扫、清洁和素养五个步骤,帮助组织提高生产效率和质量,提升员工的工作环境和工作态度。
本文将详细介绍5S现场管理的推行步骤,帮助读者了解如何有效地实施5S现场管理。
步骤一:整理(Sort)整理是5S现场管理的第一步,它的目标是去除工作场所中的杂物和不必要的物品,使工作环境更加整洁和有序。
以下是整理的具体步骤:1.制定整理计划:确定整理的范围和目标,制定整理的时间表和责任分工。
2.识别和分类:对工作场所进行全面的检查,识别出不必要的物品,并将它们分类为需要保留、需要移动、需要处理或需要丢弃的物品。
3.去除不必要的物品:根据分类结果,将不必要的物品移出工作场所,可以通过捐赠、回收或销售等方式进行处理。
4.整理工作区域:对保留的物品进行整理和归类,为每个物品分配合适的位置,并标识清楚,确保工作区域的整洁和有序。
步骤二:整顿(Set in Order)整顿是5S现场管理的第二步,它的目标是使工作场所的物品摆放整齐,方便使用和查找。
以下是整顿的具体步骤:1.分析工作流程:了解工作流程和操作需求,确定物品的使用频率和使用顺序。
2.制定整顿计划:根据工作流程和使用频率,确定物品的摆放位置和存放方式,并制定整顿的时间表和责任分工。
3.组织工作区域:根据整顿计划,将物品按照使用频率和使用顺序摆放在合适的位置,确保每个物品都有固定的存放位置。
4.标识和标示:为每个存放位置标识清楚,使用标识牌、标签或颜色等方式标示,以便员工能够快速找到所需物品。
步骤三:清扫(Shine)清扫是5S现场管理的第三步,它的目标是保持工作场所的清洁和卫生,提高工作环境的舒适度和安全性。
以下是清扫的具体步骤:1.制定清扫计划:确定清扫的频率和责任分工,制定清扫的时间表和工作内容。
2.清除垃圾和污垢:定期清除工作区域的垃圾和污垢,包括地面、设备、工具等。
- 1、下载文档前请自行甄别文档内容的完整性,平台不提供额外的编辑、内容补充、找答案等附加服务。
- 2、"仅部分预览"的文档,不可在线预览部分如存在完整性等问题,可反馈申请退款(可完整预览的文档不适用该条件!)。
- 3、如文档侵犯您的权益,请联系客服反馈,我们会尽快为您处理(人工客服工作时间:9:00-18:30)。
操作规程编号:YTO-FS-PD192
5S推动实战过程通用版
In Order T o Standardize The Management Of Daily Behavior, The Activities And T asks Are Controlled By The Determined Terms, So As T o Achieve The Effect Of Safe Production And Reduce Hidden Dangers.
标准/ 权威/ 规范/ 实用
Authoritative And Practical Standards
5S推动实战过程通用版
使用提示:本操作规程文件可用于工作中为规范日常行为与作业运行过程的管理,通过对确定的条款对活动和任务实施控制,使活动和任务在受控状态,从而达到安全生产和减少隐患的效果。
文件下载后可定制修改,请根据实际需要进行调整和使用。
日本的工厂向以整齐、清洁闻名于世,这都得感谢所谓5S的管理技巧,可以用来培养现场工人的良好工作习惯,5S运动背后所蕴含的理念是:整齐、清洁与纪律化的工作现场乃是制造高品质产品、杜绝量费,以及维持高生产能力的必要条件。
5S代表五个日本单字:SEIRI(整理)、SEITON(整顿)、SEISO(清扫)、SEIKETSU(标准)、以及SHITSUKE(教养),以下就是按步推行5S运动的简介。
推行中的5S
在推行5S运动前,第一件事情就是先到工厂现场周围环境拍照存证,将来推行5S运动后,在拍照比较,可以立即看出推行的成效。
整理环境(Clear up the area)。
在任何工厂里都有废弃或不需要的物品,这些物品目前生产用不着,应以红色标签区别,任何人见到都知道应予搬移或抛弃,不过,厂区应先确定不需要之标准以避免争端,然后指派第
三者(通常为管理部门)着手上标签。
整理储藏所(Organize storage places)。
环境清洁后,应再整理储藏所,并以文字或数字、颜色等明显标示各项物品存放位置,整理储藏所时,应牢记三个关键因素:何地(Where)、何物(What)、以及多少数量(How Many),标示应清楚明白并易于识别,应采开放式储藏系统,否则各项工具不易保持整齐。
全面清扫(Consolidate clearing procedure)。
厂区清扫涵盖三大范围:仓储区、设备与环境。
应先划分责任区域,并将清扫的责任分派给现场工作人员。
在共同责任区内,可以采用轮班制度。
最好将个人责任归属与清扫项目制表公布于现场,每一个人都看得见的地方,让每一位员工都养成每天清扫五分钟的习惯,五分钟听起来很短,但如果持之以恒,效果是十分惊人的。
把整洁的工作现场当作一项标准来追求(Standardize a spotless workplace)。
只要每人付出一点小小的努力,现场就永远保持整洁,秘诀在于牢记三个没有(No)的原则:没有不需要的物品,没有杂乱,没有肮脏。
在达成这一标准前,应派人定期检查评分。
执行视觉管制(Implement visual control)。
有批评才有进步,5S运动也是一样,理想的工作现场应该是一望即知问题所在,解决问题也就容易的多,经过一段时间
后,现场的外貌也许有了很大的改变,请你再照一些照片,然后根5S运动实施前的照片比较。
最好办一次照片展览,这是对现场员工最好的教育,此外,也不要忘记了对执行5S具有成效的现场单位或员工,给与适当的奖励。
5S的成效
现在你的工厂看起来整洁多了,但这只是5S运动的开始而已,千万不要松懈,下一个目标是潜移默化,把5S变成工厂的习惯。
管制存货水平(Control sock levels),在不影响生产的前提下,应设法逐步降低存货水平,做法很简单:利用红色(红线或标签)表示存货之最高水平,黄色标示最低水平,慢慢降低红色标签的位置,如此即可加强存货管制,减少积压存货。
容易取用,容易归位
(Make it easy to use and return things)。
各种夹具、工具与备品放置之位置,应标示名称和编号,最好画出工具的形状,精确标示位置所在,理想的工具位置,应该临近相关的机器设备,才能随取随用,用后立即归位,还可以利用不同颜色区别不同之工具或原料备品,令使用者更易于识别。
随时清理与清点(Always clean and check)在现
场随时清理雨情点,目的是要做到零故障,零错误,以及零中断,每一个与生产流程相关的环节都应该随时清理雨情点,划分责任区域,指派清理雨情点工作予现场人员。
设定前点项目与清理之顺序,并列入日常工作之一环。
工厂的维护应该由现场人员自己来做。
维持整洁的工作现场
(Maintain a spotless workplace)前面提到的三个整理重点--何地、何物、以及多少数量--是否都已做到?是否已经设定标准,杜绝现场及仓储中不需要的物品?假如现场有不需要的物品,由谁来负责搬运?所有的工具是否已经归还原位?如有肮脏是否立即清扫?员工每天清扫是否已经习惯?应该排人定期及不定期检查。
全公司维持相同的水平
(Maintain standards throughout the company)教养应该着手于严格的要求,各级主管应该放宽胸怀,可以批评别人,也要接受批评,所谓\’预防胜于治疗\’,现场的事故防患于未然。
工人缺乏教养,主管应该职责的是领班、组长,而不是工人。
领班、组长应负责教导工人,并创造活泼明朗的工作环境。
预防性的5S
当5S经过潜移默化,逐渐根栖于你的工厂,你的下一个目标就是加入世界一流公司的行列,为了达成此一目
标,还要加倍努力才行。
去处不需要的物品(Avoid unnecessary items)如果不需要的物品在你清理时一再出现,请赶快找出一再出现的原因。
与其事后处理,不如事先防范。
二防范的最佳手段就是维持并降低库存水平。
避免杂乱(Avoid disorganization)关于工具的使用,可能你的工人已经知道用毕归位,并加以整理,但现场还是相当杂乱,为了能解决问题,不能只知道杂乱的现象,却不知道杂乱的原因。
可能原因如下:储藏所并非固定,或未明显的标志放置位置;工人教养或训练不足;堆放之物品超过正常需要量。
清扫后不再肮脏
(Cleaning without getting dirty again)肮脏在被注意到以前,往往已经在工厂散布开来,散布的媒介包括风、水、油、工人制服、鞋底、轮胎(如堆高机)等。
除非消除脏乱之源,否则清不胜清,扫不胜嫂,脏乱永远存在。
想要清扫后不再肮脏,就必须找出原因,对症下药,更应该避免工作本身制造肮脏(例如加油时油洒落地面,或是运货卡车经过,轮胎将大量污泥带进工厂)。
预防环境退化
(Prevent degradation of the environment)整齐与清洁是效率的表征,一个肮脏的工厂要谈品质和效率,
无异于缘木求鱼。
为了防止环境之退化,我们不但要推行5S,还要推行预防性的5S,亦即预防性的清理、整顿与清扫。
你应该十分清楚自己工厂的缺失,掌握5S的要点,致力改进,提高标准,这样你已经朝向5S模范工厂迈进中。
有计划的训练(Systematize training)应让现场工人自动自发、承担责任、解决问题。
建设性批评虽然有效,不过一旦灾害发生,仍然于事无补。
只要不断加强员工教育训练,人为地意外或灾害必可减少。
一家公司在一年中,至少应该拨出几个月来推行5S运动,活动内容包括:5S研讨会、5S竞赛等。
公司高级主管每月至少巡视工厂一次检视5S成效。
另一有效的办法是辑印5S简讯,供员工阅读,这是教育现场工人的有效方法,此外,也可以在晨间上班前,或在晚间下班后安排五分钟的简短会议,检讨5S的成效。
一旦5S在你的工厂里已经根深蒂固、潜移默化,你的工厂就已经登列世界一流工厂的行列。
该位置可输入公司/组织对应的名字地址
The Name Of The Organization Can Be Entered In This Location。