工业控制系统
工业控制系统

03
无线网络技术
• 优点:无需布线,安装维护方便,适用于远距离通信。
• 缺点:受环境因素影响较大,传输速度不稳定,网络安
全性较差。
工业控制系统通信与网络技术的应用
数据采集与传输
• 通过通信技术实现现场设备与中央控制器之间的数据传输。
• 采用网络技术实现远程监控和数据交换。
具,提高漏洞扫描效率。
高安全防护性能。
理机制,实现访问控制。
密钥管理策略,保证加密数
据的安全性。
工业控制系统的安全检测与监控
安全检测
安全监控
• 对工业控制系统进行定期安全检测,评估系统安全性。
• 对工业控制系统进行实时安全监控,发现异常情况并进
• 采用专业的安全检测工具和风险评估方法,提高安全检
行处理。
• 提高生产过程中的效率和产品质量。
无人化与远程操作
• 实现工业控制系统的无人化操作和远程监控。
• 降低生产成本,提高生产效率。
工业控制系统的绿色与可持续发展
节能减排
可持续发展
• 应用节能减排技术,降低工业控制系统的能耗。
• 遵循绿色和可持续发展理念,实现工业控制系统的环保
• 提高生产过程中的能源利用效率。
• 工业控制系统主要由硬件、软件和通信网络三部分组成,具有实时性、可靠性和稳定性等特点。
• 工业控制系统的功能
• 数据采集与处理:实时采集生产过程中各种设备的状态参数,进行处理和分析,为生产决策提供依据。
• 控制与调节:根据生产过程中的实际需求,对设备进行自动控制和调节,以保证生产过程的稳定和高效。
中期阶段(20世纪70年代至90年代)
• 工业控制系统开始采用微处理器和数字电路等先进技术,实现复杂的自动化控制。
工业控制中的控制系统和自动化流程
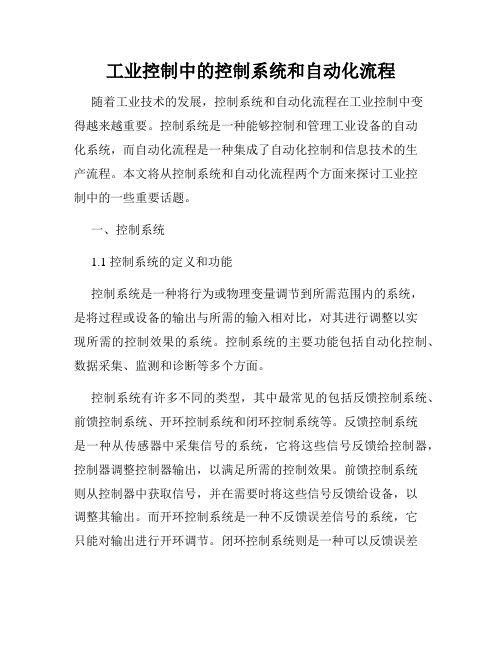
工业控制中的控制系统和自动化流程随着工业技术的发展,控制系统和自动化流程在工业控制中变得越来越重要。
控制系统是一种能够控制和管理工业设备的自动化系统,而自动化流程是一种集成了自动化控制和信息技术的生产流程。
本文将从控制系统和自动化流程两个方面来探讨工业控制中的一些重要话题。
一、控制系统1.1 控制系统的定义和功能控制系统是一种将行为或物理变量调节到所需范围内的系统,是将过程或设备的输出与所需的输入相对比,对其进行调整以实现所需的控制效果的系统。
控制系统的主要功能包括自动化控制、数据采集、监测和诊断等多个方面。
控制系统有许多不同的类型,其中最常见的包括反馈控制系统、前馈控制系统、开环控制系统和闭环控制系统等。
反馈控制系统是一种从传感器中采集信号的系统,它将这些信号反馈给控制器,控制器调整控制器输出,以满足所需的控制效果。
前馈控制系统则从控制器中获取信号,并在需要时将这些信号反馈给设备,以调整其输出。
而开环控制系统是一种不反馈误差信号的系统,它只能对输出进行开环调节。
闭环控制系统则是一种可以反馈误差信号的系统,它可以快速地校正误差,并保证在大多数情况下获得稳定的效果。
1.2 控制系统的基本组成部分控制系统通常由传感器、执行器、控制器、信号处理器和数据保存器等多个模块组成。
其中,传感器将控制器所需的输入信号转换为电信号,执行器将控制器的输出信号转换为机械或电信号,并改变所控制设备的运动或状态。
控制器是系统中最重要的部分,它负责计算和调整输入和输出信号。
此外,信号处理器和数据保存器也是控制系统中不可或缺的部分,它们可以帮助系统维护和存储需要的信息。
1.3 控制系统中的建模和仿真控制系统中,建模和仿真是非常重要的方法。
建模是利用数学模型来描述控制系统的动态过程,通过这种方式可以帮助系统分析和预测系统的行为。
而仿真则是通过仿真软件来模拟系统的运行过程,以检验控制算法的正确性和有效性。
这些方法不仅可以提高系统控制的精度和稳定性,还可以帮助工程师快速发现任何可能存在的问题。
工业控制系统的技术发展和趋势
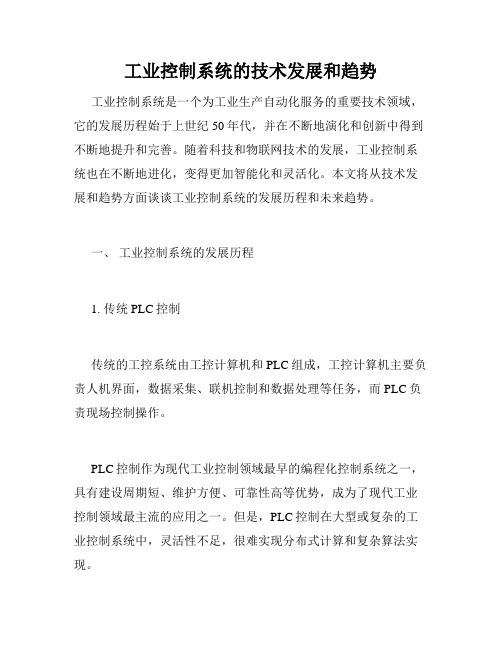
工业控制系统的技术发展和趋势工业控制系统是一个为工业生产自动化服务的重要技术领域,它的发展历程始于上世纪50年代,并在不断地演化和创新中得到不断地提升和完善。
随着科技和物联网技术的发展,工业控制系统也在不断地进化,变得更加智能化和灵活化。
本文将从技术发展和趋势方面谈谈工业控制系统的发展历程和未来趋势。
一、工业控制系统的发展历程1. 传统PLC控制传统的工控系统由工控计算机和PLC组成,工控计算机主要负责人机界面,数据采集、联机控制和数据处理等任务,而PLC负责现场控制操作。
PLC控制作为现代工业控制领域最早的编程化控制系统之一,具有建设周期短、维护方便、可靠性高等优势,成为了现代工业控制领域最主流的应用之一。
但是,PLC控制在大型或复杂的工业控制系统中,灵活性不足,很难实现分布式计算和复杂算法实现。
2. DCS随后,随着工业控制领域的不断发展和智能化趋势,DCS(分布式控制系统)等控制策略应运而生。
DCS控制针对大型复杂工业系统,其主要优点在于强大的控制能力、多点测量、多点操作,其相对于PLC控制而言为一种灵活高效的分布式控制方法,而且DCS可以方便的实现大规模的集群控制,是工业控制系统的发展之一。
3. PC控制现代工业控制系统中,随着工控技术的不断进步和计算机性能的不断提高,基于PC控制的技术应运而生。
它基于通用计算机平台,摆脱了传统的特殊硬件和编程方式,使得整个系统的开发成本大大降低,同时也提高了整个系统的可定制性和可升级性。
4. 大数据大数据技术的发展给现代工业控制系统带来了重要影响。
在控制系统中,消息传递和大数据分析应用价值非常高,可以利用大数据技术来分析工业控制中的各种问题,包括控制精度、稳定性、系统故障等,有效提高工业生产的效率和质量。
二、工业控制系统的未来趋势1. 智能化化、网络化、集成化现代工业控制要实现智能化,那么工业控制系统就需要更加智能。
随着制造业的深入开展,自动化成为未来产业中一项不可或缺的技术,未来工业控制系统将向网络化、智能化、集成化的方向发展,将很多机器和设备的信息通过物联网或其他技术进行互联,以实现更加丰富、精准、可靠的处理和控制,以达到更好的结果。
工业控制系统的概念和发展历程
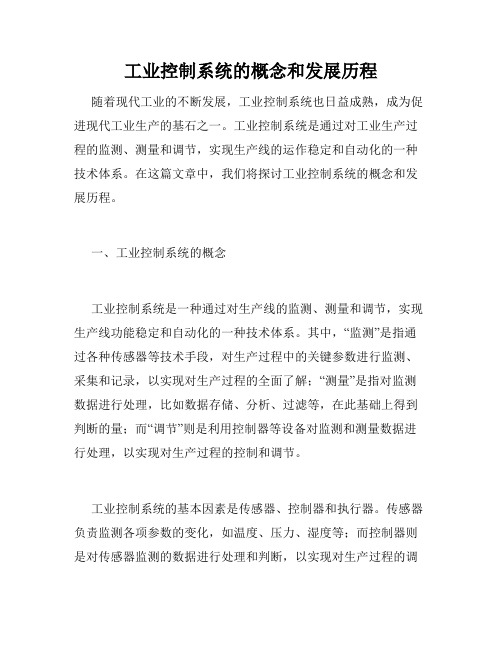
工业控制系统的概念和发展历程随着现代工业的不断发展,工业控制系统也日益成熟,成为促进现代工业生产的基石之一。
工业控制系统是通过对工业生产过程的监测、测量和调节,实现生产线的运作稳定和自动化的一种技术体系。
在这篇文章中,我们将探讨工业控制系统的概念和发展历程。
一、工业控制系统的概念工业控制系统是一种通过对生产线的监测、测量和调节,实现生产线功能稳定和自动化的一种技术体系。
其中,“监测”是指通过各种传感器等技术手段,对生产过程中的关键参数进行监测、采集和记录,以实现对生产过程的全面了解;“测量”是指对监测数据进行处理,比如数据存储、分析、过滤等,在此基础上得到判断的量;而“调节”则是利用控制器等设备对监测和测量数据进行处理,以实现对生产过程的控制和调节。
工业控制系统的基本因素是传感器、控制器和执行器。
传感器负责监测各项参数的变化,如温度、压力、湿度等;而控制器则是对传感器监测的数据进行处理和判断,以实现对生产过程的调节和控制,最终以执行机构的形式改变生产过程中的各种因素,以达到预定目标。
二、工业控制系统的历史发展工业控制系统的发展可以追溯到19世纪末期。
当时发明了一种叫做“沙尔顿水银控制器”的装置,它通过调节蒸汽压力控制溶液的温度和浓度,实现工业生产过程的稳定。
这一技术的出现标志着现代工业控制系统的起点。
20世纪初,随着电气技术的进步和应用,电气控制系统开始普及。
电气控制系统利用串、并联电路和继电器等元器件,实现对电气信号的监测和控制,为现代工业控制系统的发展奠定了基础。
20世纪60年代至70年代期间,数字技术应用的兴起进一步推动了工业控制系统的发展。
自动控制系统中的传感器和执行器也随之改变,焦点从机械式的改变为电子式的,即触发器和逻辑门,这使得控制器变成一台可以以电子数字信号为输入和输出的计算机系统。
一些特定行业,如航空航天和核能,需要高度抗干扰和安全性的控制系统。
进入21世纪后,工业控制系统的发展进入了数字化、网络化和智能化的时代。
工业控制系统概念
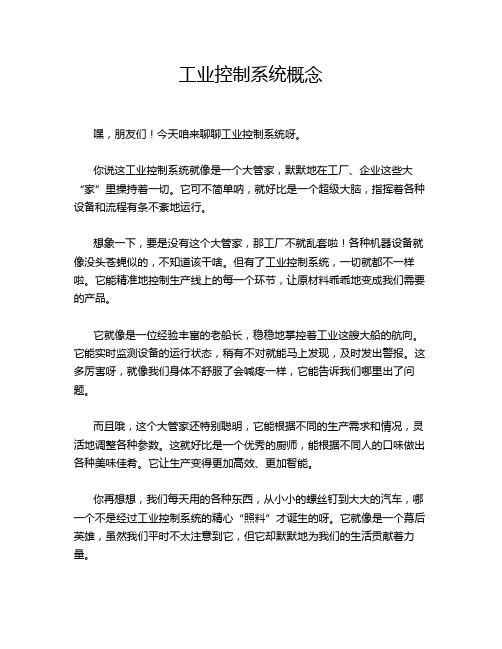
工业控制系统概念嘿,朋友们!今天咱来聊聊工业控制系统呀。
你说这工业控制系统就像是一个大管家,默默地在工厂、企业这些大“家”里操持着一切。
它可不简单呐,就好比是一个超级大脑,指挥着各种设备和流程有条不紊地运行。
想象一下,要是没有这个大管家,那工厂不就乱套啦!各种机器设备就像没头苍蝇似的,不知道该干啥。
但有了工业控制系统,一切就都不一样啦。
它能精准地控制生产线上的每一个环节,让原材料乖乖地变成我们需要的产品。
它就像是一位经验丰富的老船长,稳稳地掌控着工业这艘大船的航向。
它能实时监测设备的运行状态,稍有不对就能马上发现,及时发出警报。
这多厉害呀,就像我们身体不舒服了会喊疼一样,它能告诉我们哪里出了问题。
而且哦,这个大管家还特别聪明,它能根据不同的生产需求和情况,灵活地调整各种参数。
这就好比是一个优秀的厨师,能根据不同人的口味做出各种美味佳肴。
它让生产变得更加高效、更加智能。
你再想想,我们每天用的各种东西,从小小的螺丝钉到大大的汽车,哪一个不是经过工业控制系统的精心“照料”才诞生的呀。
它就像是一个幕后英雄,虽然我们平时不太注意到它,但它却默默地为我们的生活贡献着力量。
那工业控制系统是怎么做到这么厉害的呢?这可离不开先进的技术和复杂的算法呀。
它要处理大量的数据,要快速做出决策,这可不是一般人能做到的哟!它得不断学习、不断进步,才能跟上时代的步伐。
咱国家现在的工业发展得多快呀,这可少不了工业控制系统的功劳。
它让我们的工业变得越来越强大,越来越有竞争力。
我们的生活也因为它变得更加美好,更加便利。
所以啊,可别小瞧了这工业控制系统,它可是工业领域的中流砥柱呢!它让我们的工业生产如虎添翼,为我们创造了无数的价值。
咱得好好感谢它,也得不断支持它的发展,让它为我们的生活带来更多的惊喜和改变,不是吗?。
工业控制系统
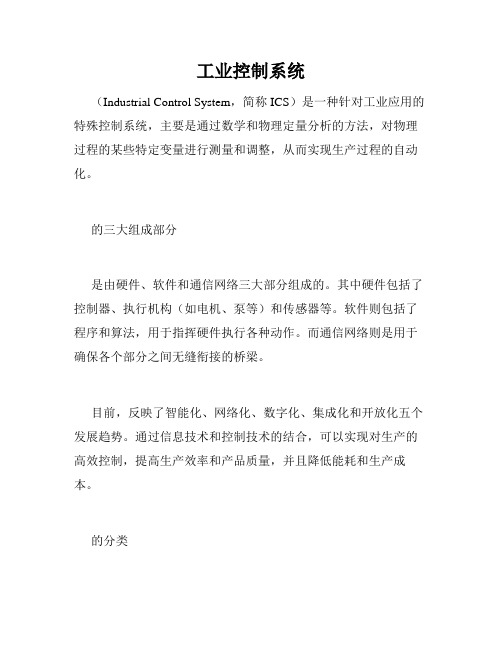
工业控制系统(Industrial Control System,简称ICS)是一种针对工业应用的特殊控制系统,主要是通过数学和物理定量分析的方法,对物理过程的某些特定变量进行测量和调整,从而实现生产过程的自动化。
的三大组成部分是由硬件、软件和通信网络三大部分组成的。
其中硬件包括了控制器、执行机构(如电机、泵等)和传感器等。
软件则包括了程序和算法,用于指挥硬件执行各种动作。
而通信网络则是用于确保各个部分之间无缝衔接的桥梁。
目前,反映了智能化、网络化、数字化、集成化和开放化五个发展趋势。
通过信息技术和控制技术的结合,可以实现对生产的高效控制,提高生产效率和产品质量,并且降低能耗和生产成本。
的分类根据控制对象的不同,可以分为过程控制系统和机器控制系统两种。
过程控制系统主要应用于化工、石油、电力、冶金、水泥、钢铁等行业,其控制对象通常是工业的物理过程,如温度、压力、流量、含量等。
过程控制系统主要分为单参数控制和多参数控制两大类。
单参数控制一般适用于控制单个物理量,如温度、压力等;而多参数控制则是将多个物理量联系在一起进行调控,如化工过程中的反应速度、温度、流量等因素的综合控制。
机器控制系统也称为离散控制系统,主要应用于机械加工、自动化装配、机器人控制等领域。
其控制对象是机器设备本身,如运动轨迹、速度、位置等。
机器控制系统一般采用开环控制或者闭环控制方式,通过感知设备发送的信号,来控制设备的运动轨迹和位置等参数。
的安全问题由于在生产领域中的重要性日益提高,因此对于其安全问题也越来越引起关注。
一旦遭到攻击或者出现故障,不仅会影响生产过程,还有可能对生产系统造成严重的损害。
针对的安全问题,现有的解决方案主要包括以下几点:1、防御攻击。
加密、访问控制和安全检测技术都是有效的安全防御措施。
其中加密技术可以对敏感信息进行加密,不让管道中的任何人来访问和窃取数据。
此外,访问控制和安全检测技术则可以限制未经授权的访问和检测任何异常活动。
《工业控制系统》课件

网络化发展趋势
物联网集成
工业控制系统将与物联网技术深度融合,实现设 备间的互联互通和数据共享。
云计算应用
云计算技术将为工业控制系统提供强大的数据处 理和存储能力,支持远程监控和管理。
无线通信发展
无线通信技术的进步将为工业控制系统的网络化 提供更加便捷和可靠的数据传输方式。
安全性与可靠性提升
安全防护体系
执行器
执行器是工业控制系统中用于执行控制信号的装置。
执行器的种类繁多,常见的有电动执行器、气动执行器和液压执行器等。 执行器的性能指标包括调节精度、响应速度和稳定性等,选择合适的执行 器是实现精确控制的重要环节。
人机界面
人机界面是工业控制系统中用 于实现人与机器交互的设备。
人机界面的种类繁多,常见 的有触摸屏、显示屏和操作
故障诊断与容错技术
故障检测
通过传感器、监控系统等手段实时监测工业 控制系统的运行状态,及时发现异常情况。
故障诊断
利用各种诊断工具和技术,对故障进行定位和原因 分析,以便采取相应的处理措施。
容错技术
采用冗余设计、备件切换等技术,提高工业 控制系统的容错能力,确保系统在部分组件 故障时仍能正常运行。
系统可靠性评估与优化
模糊控制系统的特点
模糊控制系统具有适应性强、鲁棒性好、能够处理不确定性和非线性等优点,但也存在计算量大、精度 不高和稳定性较差等缺点。
04
工业控制系统的设计与实现
系统需求分析
需求调研
深入了解工业控制系统的需求,包括 但不限于控制精度、响应速度、安全 性和稳定性等方面的要求。
需求规格书编写
根据调研结果,编写详细的需求规格 说明书,明确系统的功能、性能和安 全等方面的要求。
工业控制系统架构课件

随着系统规模扩大,集中式架构 可能面临性能瓶颈和安全风险, 中央控制器容易成为攻击的目标 。
分散式架构
优点
分散式架构将系统划分为多个独立的子系统,每个子系统具有一定的自治能力,能够减轻中央控制器的负担。
缺点
分散式架构增加了系统的复杂性,可能面临通信延迟和协同问题。
分布式架构
优点
分布式架构将系统划分为多个独立的节点,每个节点具有完整的自治能力,能 够实现并行处理和负载均衡。
密性。
案例四:智能制造的工业控制应用场景
总结词
智能制造是当前工业控制领域的重要发展方向,其应 用场景非常广泛,包括机器人、智能生产线、智能仓 储等。
详细描述
智能制造的工业控制应用场景非常广泛,包括机器人、 智能生产线、智能仓储等。其中,机器人的应用非常普 遍,其控制方式主要是通过PLC或嵌入式系统进行控制 ,实现自动化操作和精确控制。智能生产线则是由多个 机器人和其他设备组成的生产线,实现生产过程的自动 化和信息化。智能仓储则是利用物联网技术和传感器技 术对仓库进行智能化的管理和控制,提高仓库的管理效 率和物流效率。
案例二:汽车制造厂的分布式控制架构
总结词
汽车制造厂的分布式控制架构是一种基于PLC和工业以 太网的架构,实现生产过程的自动化和信息化。
详细描述
汽车制造厂的分布式控制架构主要由现场控制层、监控 层和信息管理层三个层次组成。现场控制层主要负责生 产现场的自动化控制,包括生产设备的控制和生产过程 的监测等。监控层则负责对生产过程进行监控和管理, 包括生产计划、生产进度、质量检测等。信息管理层则 负责对整个制造过程进行信息化管理,包括生产管理、 库存管理、人员管理等。
01
02
03
- 1、下载文档前请自行甄别文档内容的完整性,平台不提供额外的编辑、内容补充、找答案等附加服务。
- 2、"仅部分预览"的文档,不可在线预览部分如存在完整性等问题,可反馈申请退款(可完整预览的文档不适用该条件!)。
- 3、如文档侵犯您的权益,请联系客服反馈,我们会尽快为您处理(人工客服工作时间:9:00-18:30)。
输入 单元
存储
输入采样阶段
CPU 以固定的周期重复 调度执行下面的过 程
用户程序
用户程序执行阶段
精品课件
存储
数据
输出 单元
接收 ALC 数据
状态 接口
输出刷新阶段
PLC的主要功能
运算功能
目前PLC基本已具有高级数学运算和模拟量的PID运算功能。
控制功能
控制功能包括顺序控制(开关量控制)、过程控制(模拟量控制)、运动控制(脉冲量控制)和信息 控制远程控制,应根据实际需求选用。(详情可参考最后一页‘补充参考资料’)
处理速度
从实时性要求来看,处理速度应越快越好,如果信号持续时间小于扫描时间,则可编程逻辑控制器将 扫描不到该信号,造成信号数据的丢失。
精品课件
5、RTU
• RTU(远程终端单元),全称为远程终端控制系统,负责对现场 信号、工业设备的监测和控制。通常由信号输入/出模块、微处 理器、有线/无线通讯设备、电源及外壳等组成,由微处理器控 制,并支持网络系统。
工业控制系统(ICS)
精品课件
ICS
工业控制系统(ICS)是各式各样控制系统类型的总称。目前常见的有: 1. 监控和数据采集系统(SCADA) 2. 分布式控制系统(DCS) 3. 过程控制系统(PCS)(源于西门子将自家PLC集成做的DCS解决方案) 4. 可编程控制器(PLC) 5. 远程终端单元( RTU )
DCS(分布式控制系统)是从1975年前后从CCS(计算机集中控制系统)发 展出的工业控制系统的架构。
FCS (现场总线控制系统)是基于网络化、标准化、开放理念发展的最新的 架构。
精品课件
分布式控制系统(DCS)的发展
网 络 化 、 标 准 化
精品课件
DCS和FCS的对比
FCS主要引入了网络,统一了标准,开放了整个控制系统。
PLC和RTU主要用于获取设备状态,PLC也可以用于设备的本地控制;DCS通常用于局域网内生产 过程的整体控制,SCADA主要从PLC和RTU采集监控数据。
精品课件
1、SCADA
• SCADA(Supervisory Control And Data Acquisition)系统,即 数据采集与监视控制系统。
• SCADA可以应用于电力、冶金、石油、化工、燃气、铁路等领域 的数据采集与监视控制以及过程控制等诸多领域。在电力系统中, SCADA系统应用最为广泛,技术发展也最为成熟。
精品课件
2、DCS
控制系统的结构从最初的CCS(计算机集中控制系统),到第二代的DCS(分 布式控制系统),发展到现在流行的FCS(现场总线控制系统)。
通信功能
大中型可编程逻辑控制器系统应支持多种现场总线和标准通信协议(如TCP/IP),同时还应支持的通 信接口应包括串行和并行通信接口、RIO通信口、常用DCS接口等。
编程功能
支持编制用户自定义程序。支持C、Basic等语言。
诊断功能
可编程逻辑控制器的诊断功能包括硬件和软件的诊断。硬件诊断通过硬件的逻辑判断确定硬件的故障 位置,软件诊断分内诊断和外诊断。
精品课件
补充参考资料
• 1、PLC的五大控制功能
精品课件
DCSC实质是一种专用于工业控制的计算机,其硬件结构基本上与 微型计算机相同。
PLC主要组成部分: 1. 电源 2. 中央处理单元(CPU) 3. 存储器 4. 输入输出接口电路 5. 功能模块(如计数、定位等功能模块) 6. 通信模块
精品课件
PLC的工作原理
数据
精品课件
PLC和RTU对比
起源不同 PLC起源于生产线自动化,主要应用于机械设备生产线,以顺序逻辑控制为主。RTU起源于石油天然气生产,生产设备比较分布、且 数量众多、环境恶劣。 功能不同 PLC主要用于室内的生产线或站控制系;RTU主要用于室外生产控制设备。 通讯能力不同 PLC一般是单机使用,或和本系列的产品使用,一般只支持本公司的通讯协议。RTU一般作为SCADA系统的一个部分,随着系统的 增大系统中可能会有不同厂家的RTU,因此RTU具有通用的通讯协议。RTU大多以无线方式与中控室通讯,因此RTU能很好的支持无 线通讯设备(电台、无线以太网、GPRS、CDMA等) 使用场合不同 PLC主要用于:生产线、流水线、部分厂站、配电系统、机床控制等。RTU主要用于:石油天然气生产、管道、城市天然气管网、供 水管网、环境监测等。 目前随着技术的融合,PLC也能做RTU的事情,RTU也可以完成PLC的工作。